TEST PROCEDURE for FMVSS No. 135 Light Vehicle Brake Systems
Total Page:16
File Type:pdf, Size:1020Kb
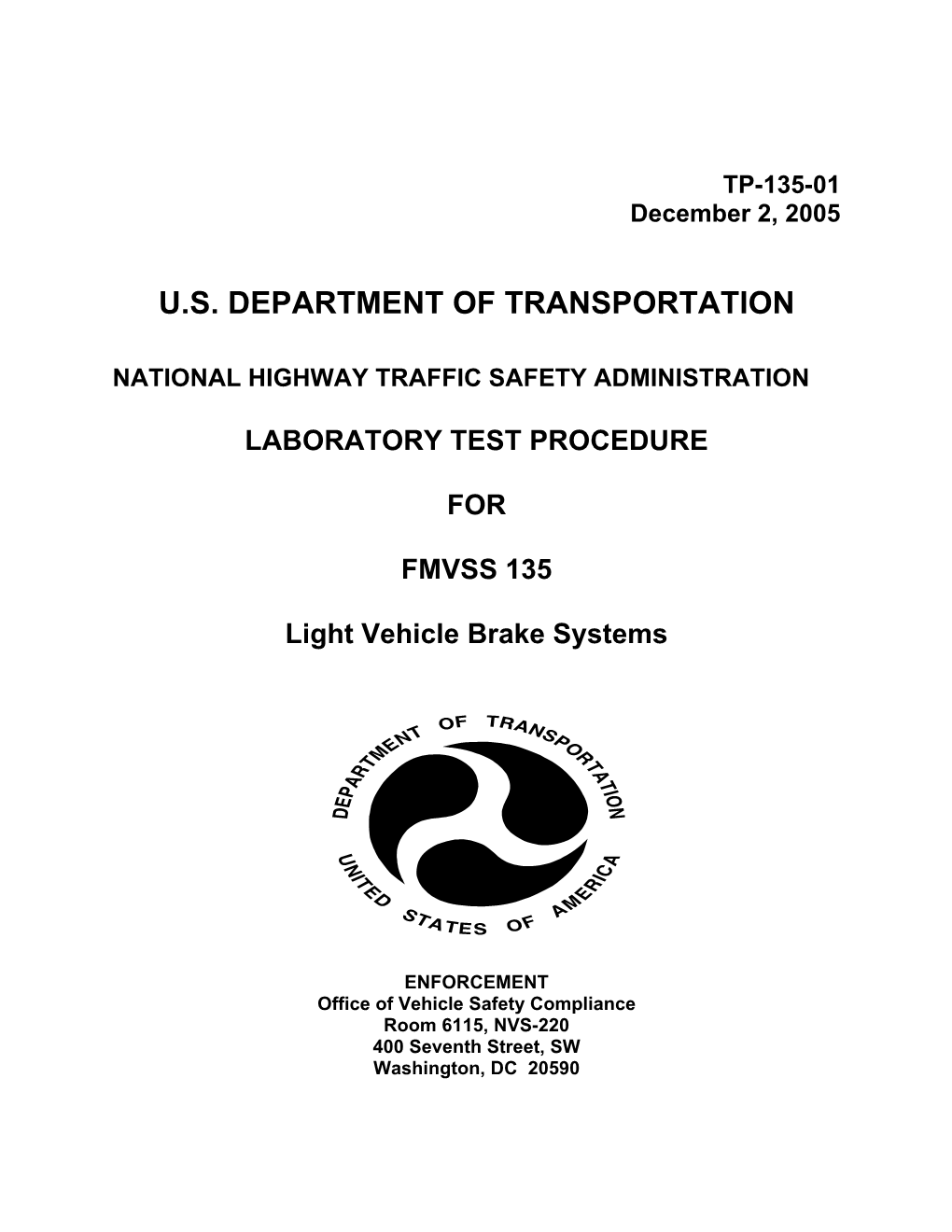
Load more
Recommended publications
-
EP / BP Compact Product Family
EP / BP Compact Product Family Foto Siemens AG“ APPLICATIONS High-Speed Trains | Locomotives | Metros | Regional and Commuter Trains 2 EP / BP COMPACT PRODUCT FAMILY IS A FLEXIBLE AND POWERFUL BRAKE CONTROL SYSTEM providing not only brake cylinder pressure control for central and decentralized systems but also for brake pipe pressure control. Its modular design of electronic and pneumatic modules makes it configurable for all types of high-speed trains, multiple units and metros. With its variety of modules, EP / BP CUSTOMER BENEFITS DIVERSIFICATION Compact can be used for a wide n Lightweight and compact EP Compact offers control of various range of different applications of all n Flexible system layout functions of the braking systems: car builders across different markets. n Maximum economy thanks to n Service brake (direct and indirect) Every electropneumatic module standardized modules n Emergency brake (direct and controls either brake pipe n Discrete, highly integrable indirect) applications, single bogies components n Magnetic track brake separately or several bogies with n Straightforward service and n Parking brake identical braking requirements. maintenance concept n Wheel slide control Different electronic modules allow n For central or decentralized control n Continuous load correction and the use of different communication n Multifunctional for numerous load limitation interfaces: wheel slide protection, system configurations pressure regulation and diagnosis n Innovative use of proven Electronic control functions: functions. Anti-skid valves as well as technology n Blending / brake management different auxiliary control functions n Integrated electronics for n Diagnostics and monitoring can be integrated into the module underfloor or separate electronics n Sanding and other auxiliary systems as an option. -
Real-World Exhaust Emissions of Diesel Locomotives and Motorized Railcars During Scheduled Passenger Train Runs on Czech Railroads
atmosphere Article Real-World Exhaust Emissions of Diesel Locomotives and Motorized Railcars during Scheduled Passenger Train Runs on Czech Railroads Michal Vojtisek-Lom 1,2,* , Jonáš Jirk ˚u 3 and Martin Pechout 4 1 Department of Automobile, Combustion Engine and Railway Engineering, Faculty of Mechanical Engineering, Czech Technical University of Prague, 160 00 Prague, Czech Republic 2 Department of Vehicles and Engines, Technical University of Liberec, 46117 Liberec, Czech Republic 3 Department of Vehicle Technology, Faculty of Transportation Sciences, Czech Technical University in Prague, 110 00 Prague, Czech Republic; [email protected] 4 Department of Vehicles and Ground Transport, Faculty of Engineering, Czech University of Life Sciences, 165 21 Prague, Czech Republic; [email protected] * Correspondence: [email protected] or [email protected]; Tel.: +420-774-262-854 Received: 17 April 2020; Accepted: 28 May 2020; Published: 2 June 2020 Abstract: The paper summarizes exhaust emissions measurements on two diesel-electric locomotives and one diesel-hydraulic railcar, each tested for several days during scheduled passenger service. While real driving emissions of buses decrease with fleet turnaround and have been assessed by many studies, there are virtually no realistic emissions data on diesel rail vehicles, many of which are decades old. The engines were fitted with low-power portable online monitoring instruments, including a portable Fourier Transform Infra Red (FTIR) spectrometer, online particle measurement, and in two cases with proportional particle sampling systems, all installed in engine compartments. Due to space constraints and overhead electric traction lines, exhaust flow was computed from engine operating data. Real-world operation was characterized by relatively fast power level transitions during accelerations and interleaved periods of high load and idle, and varied considerably among service type and routes. -
2018 Avalon Hybrid Product Information
2018 Avalon Hybrid Product Information #Avalon #Hybrid HYBRID POWER SYSTEM Hybrid System Net Horsepower 200 hp ENGINE Type, Materials 2.5-liter, 4-cylinder, aluminum alloy block with aluminum alloy head Valvetrain 16-valve DOHC with VVT-i Displacement 2,494 cc Bore x Stroke 3.54 x 3.86 in. Compression Ratio 12.5:1 Horsepower (SAE Net) 156 hp @ 5,700 rpm Torque 156 lb-ft @ 4,500 rpm Recommended Fuel 87-octane or higher - unleaded Emission Certification LEV3 EPA Estimated Fuel Economy* 40/39/40 (city/highway/combined MPG) ELECTRIC MOTOR Type Permanent Magnet AC Synchronous Motor Electric Motor Power Output 105 kW/4,500 RPM Torque 199 lb-ft @ 0-1,500 RPM HYBRID BATTERY PACK Type Sealed Nickel-Metal Hydride (Ni-MH) Nominal Voltage 244.8 V (204 cells, 1.2V/cells) Capacity 6.5 ampere hour System Voltage 650 volts maximum *2018 EPA estimated MPG - Actual mileage will vary. DRIVETRAIN Transmission Type Electronically Controlled Continuously Variable Transmission Final Drive Ratio 3.54 to 1 CHASSIS AND BODY Suspension - Front MacPherson strut with torsion bar - Rear Dual link Independent MacPherson strut with torsion bar 2018 Avalon Hybrid Product Information #Avalon #Hybrid - Stabilizer Bar 25 mm/ 16 mm (0.98 in. / 0.63 in.) Diameter (front/rear) Steering - Type Electric Power Steering (EPS): rack-and-pinion with electric power-assist - Overall 14.8 to 1 Ratio - Turning 40.0 ft. Circle Diameter (curb-to- curb) Brakes - Type Electronically Controlled Brake system (ECB) - Front Ventilated disc with standard Anti-Lock Brake system (ABS), Brake Assist (BA) and integrated regenerative brake system - Front Diameter 11.7 in. -
TRANSPORTATION NOTICE #2018-045 Effective 0001, Friday, December 14, 2018
THE BELT RAILWAY COMPANY OF CHICAGO TRANSPORTATION NOTICE #2018-045 Effective 0001, Friday, December 14, 2018 To: ALL CONCERNED Subject: Clearing Yard Transportation Work Instructions (Hump Notice) Transportation Notice 2018-034, effective August 21, 2018 is cancelled. The following changes are made to Clearing Yard Transportation Work Instructions (Hump) Addition: • CY 5.20 – Cars on Hump Needing Repairs (NEW) • CY 8.2.1 - Braking During Shove Over Movements (NEW) Transportation Notice 2018-045 Page 1 Clearing Yard Transportation Work Instructions (Hump) The instructions contained within this document are specifically intended for any Transportation Department employees working in Clearing Yard. These instructions provide specific instructions on the operation of the Clearing Yard. Where these instructions may differ from published rules, these instructions will govern operations as they relate to the operation of the Clearing Yard. Transportation Department Employees working in Train, Yard, and Engine Service; including Yardmasters (Humpmasters), Hump Conductors, and all crew members on BRC yard assignments, must have these instructions in their possession while on duty for reference while working in Clearing Yard. These instructions will be published quarterly, with additions made as needed using Transportation Notices, under the direction of the Superintendent-Transportation. CY 1 - Hump Operations: Hump Operations are under the direct control of the Trainmaster-Operations. Reporting to the Trainmaster- Operations are Yardmasters, Hump Conductors, Train Crews, and Transportation-Clerks. CY 2 - Hump Speeds: The Hump Conductor is responsible for regulating hump speeds and communicating this information to Hump Crews. Speed Settings: SPEED SETTING SPEED (MPH) HUMP SLOW 1.4 MPH HUMP 1.7 MPH HUMP FAST 2.2 MPH The default speed for hump operations is Hump. -
Design and Fabrication of Regenerative Braking System and Modifying Vehicle Dynamics
ISSN(Online) : 2319-8753 ISSN (Print) : 2347-6710 International Journal of Innovative Research in Science, Engineering and Technology (An ISO 3297: 2007 Certified Organization) Vol. 5, Special Issue 8, May 2016 Design and Fabrication of Regenerative Braking System and Modifying Vehicle Dynamics D.Kesavaram 1, K.Arunkumar 2, M.Balasubramanian 3, J.Jayaprakash 4, K.Kalaiselvan 5 Assistant Professor, Department of Mechanical Engineering, TRP Engineering College, Tiruchirapalli, India1 UG Scholars, Department of Mechanical Engineering, TRP Engineering College, Tiruchirapalli, India 2,3,4,5 ABSTRACT: A regenerative brake is an energy recovery mechanism which slows a vehicle or object by converting its kinetic energy into a form which can be either used immediately or stored until needed. The conventional brake setup involves many energy loses and hence in our work, the conventional brake setup is replaced by mounting an alternator assembly in the wheel hub. During the forward motion of the vehicle, the alternator’s rotor rotates freely. During the application of brakes, the input supply is given to the alternator and as a result the rotor coils provide a rotational magnetic flux which cuts the stator conductor which is rotating along with the flywheel and hence an induced voltage is obtained from the alternator output which is stored in a battery. By increasing the alternator load the conductor gradually slows down and hence acts as a brake. The time required to stop the vehicle is directly proportional to the load connected to the alternator. Then by increasing the diameter of the front wheel of the vehicle, the stability of the 2 wheeler can be improved as it modifies the rear suspension effect and provides more contact between the wheel and the ground during braking. -
An Optimal Slip Ratio-Based Revised Regenerative Braking Control Strategy of Range-Extended Electric Vehicle
energies Article An Optimal Slip Ratio-Based Revised Regenerative Braking Control Strategy of Range-Extended Electric Vehicle Hanwu Liu , Yulong Lei, Yao Fu * and Xingzhong Li State Key Laboratory of Automotive Simulation and Control, School of Automotive Engineering, Jilin University, Changchun 130022, China; [email protected] (H.L.); [email protected] (Y.L.); [email protected] (X.L.) * Correspondence: [email protected] Received: 2 February 2020; Accepted: 20 March 2020; Published: 24 March 2020 Abstract: The energy recovered with regenerative braking system can greatly improve energy efficiency of range-extended electric vehicle (R-EEV). Nevertheless, maximizing braking energy recovery while maintaining braking performance remains a challenging issue, and it is also difficult to reduce the adverse effects of regenerative current on battery capacity loss rate (Qloss,%) to extend its service life. To solve this problem, a revised regenerative braking control strategy (RRBCS) with the rate and shape of regenerative braking current considerations is proposed. Firstly, the initial regenerative braking control strategy (IRBCS) is researched in this paper. Then, the battery capacity loss model is established by using battery capacity test results. Eventually, RRBCS is obtained based on IRBCS to optimize and modify the allocation logic of braking work-point. The simulation results show that compared with IRBCS, the regenerative braking energy is slightly reduced by 16.6% and Qloss,% is reduced by 79.2%. It means that the RRBCS can reduce Qloss,% at the expense of small braking energy recovery loss. As expected, RRBCS has a positive effect on prolonging the battery service life while ensuring braking safety while maximizing recovery energy. -
Module 11: Regenerative Braking
NPTEL – Electrical Engineering – Introduction to Hybrid and Electric Vehicles Module 11: Regenerative braking Lecture 38: Fundamentals of Regenerative Braking Fundamentals of Regenerative Braking The topics covered in this chapter are as follows: Introduction. Energy Consumption in Braking Braking Power and Energy on Front and Rear Wheels Introduction The electric motors in EVs and HEVs can be controlled to operate as generators to convert the kinetic or potential energy of the vehicle mass into electric energy that can be stored in the energy storage and reused. A successfully designed braking system for a vehicle must always meet two distinct demands: i. In emergency braking, the braking system must bring the vehicle to rest in the shortest possible distance. ii. The braking system must maintain control over the vehicle’s direction, which requires braking force to be distributed equally on all the wheels. Energy Consumption in Braking A significant amount of energy is consumed by braking. Braking a 1500 kg vehicle from 2 100 km/h to zero speed consumes about 0.16 kWh of energy (0.5 Mv V ) in a few tens of meters. If this amount of energy is consumed in coasting by only overcoming the drags (rolling resistance and aerodynamic drag) without braking, the vehicle will travel about 2 km, as shown in Figure 1. When vehicles are driving with a stop-and-go pattern in urban areas, a significant amount of energy is consumed by frequent braking, which results in high fuel consumption. The braking energy in typical urban areas may reach up to more than 25% of the total traction energy. -
ABS 6 Standard Anti-Lock Braking System
Systems for Commercial Vehicles Product Manual ABS 6 Standard Anti-lock Braking System • Basic Principles of Operation of the System • Component Descriptions • Troubleshooting and Fault-Finding • Service Guidance to ensure Safe and Efficient Operation Training Nutzfahrzeug Bremssysteme Contents Contents 3 Disclaimer 4 Safety Checks 5 1. General Information 6 1.1 Service Intervals 6 1.2 Principles of Anti-lock Braking System (ABS) Operation 7 1.2.1 Introduction 7 1.2.2 Operation 9 1.3 General Advice when working with ABS 14 1.3.1 Dos and Don’ts for Drivers / Operators 14 1.3.2 Dos and Don’ts for ABS electrical components and cabling 15 1.3.3 Dos and Don’ts for ABS pneumatic components and pipework 17 1.4 Troubleshooting and Fault-finding 18 1.4.1 Normal Operation 18 1.4.2 Start-up Check 18 1.4.3 Fault Detection 18 1.4.4 Using Blink Codes 18 1.4.5 Configuration Blink Codes 19 1.4.6 Fault Blink Codes 21 1.4.7 Erasing Fault Codes from the ECU memory 26 1.4.8 PC Diagnostics 27 2. System Components 28 2.1 Electronic Control Unit (ECU) 28 2.2 ABS Warning Lamp 29 2.3 Sensing Ring 30 2.4 Wheel Speed Sensor 31 2.5 Sensor Extension Cable 34 2.6 Pressure Modulator Valves 35 2.7 VOSS plug connection system 230 (assembly instructions) 41 3. Wiring Diagrams 43 3 3 Disclaimer The information contained in this document is intended for the exclusive use of trained persons within the commercial vehicle industry, and must not be passed on to any third party. -
Brake Lining Application Guide Marathonbrake.Com
ApplicationGuide_Layout 1 11/24/10 5:03 PM Page 1 The Marathon Advanta ge... Feel the Difference Brake Lining One of the most significant design characteristics of any heavy duty brake lining is its density. When higher quality and heavier Hi-Density Friction raw materials are used in a lining's formulation, it creates a higher ■ Higher density friction materials have the ability to hold Application mass in the block or stated another way, higher density. Truck more heat energy and therefore more efficiently brakes are designed to convert the energy of a moving vehicle into dissipate the heat heat energy. A higher density increases the lining's ability to ■ efficiently handle heat, and is the most critical component in a Higher density linings exhibit significantly better wear Guide friction material's fade, recovery and wear. characteristics, especially at higher temperatures ■ Higher density friction materials are more resistant to brake fade and water fade ■ Higher density friction materials have stronger structural integrity, making them less likely to crack in service, while riveting or due to rust jacking See the difference... higher density Marathon linings tip the scale vs. leading competitor 554 125 Old Mill Road • Cartersville, GA 30120 Call 800.223.5201 or visit CERTIFIED MarathonBrake.com Application Guide AHA 3M 12/10 ©2010 Marathon Brake Systems, Inc. Printed in U.S.A ApplicationGuide_Layout 1 11/24/10 5:03 PM Page 3 Brake Lining Application Guide MarathonBrake.com Severe Medium Light Severe Medium Light Duty Duty Duty Duty -
Adaptive Brake by Wire from Human Factors to Adaptive Implementation
UNIVERSITY OF TRENTO Doctoral School in Engineering Of Civil And Mechanical Structural Systems Adaptive Brake By Wire From Human Factors to Adaptive Implementation Thesis Tutor Doctoral Candidate Prof. Mauro Da Lio Andrea Spadoni Mechanical and Mechatronic Systems December 2013 - XXV Cycle 1 Adaptive Brake By Wire From Human Factors to Adaptive Implementation 2 Adaptive Brake By Wire From Human Factors to Adaptive Implementation Table of contents TABLE OF CONTENTS .............................................................................................................. 3 LIST OF FIGURES .................................................................................................................... 6 LIST OF TABLES ...................................................................................................................... 8 GENERAL OVERVIEW .............................................................................................................. 9 INTRODUCTION ................................................................................................................... 12 1. BRAKING PROCESS FROM THE HUMAN FACTORS POINT OF VIEW .................................... 15 1.1. THE BRAKING PROCESS AND THE USER -RELATED ASPECTS ......................................................................... 15 1.2. BRAKE ACTUATOR AS USER INTERFACE ................................................................................................. 16 1.3. BRAKE FORCE ACTUATION : GENERAL MOVEMENT -FORCE DESCRIPTION ...................................................... -
Altroz.Tatamotors.Com
11189812 TATA-A-OWNER’S MANUAL Cover page 440 mm X 145 mm OWNER’S MANUAL Call us:1-800-209-7979 Mail us: [email protected] Visit us: service.tatamotors.com 5442 5840 9901 Developed by: Technical Literature Cell,ERC. altroz.tatamotors.com OWNER’S MANUAL CUSTOMER ASSISTANCE In our constant endeavour to provide assistance and complete You can also approach nearest TATA MOTORS dealer. A sepa- service backup, TATA MOTORS has established an all India cus- rate Dealer network address booklet is provided with the tomer assistance centre. Owner’s manual. In case you have a query regarding any aspect of your vehicle, TATA MOTORS’ 24X7 Roadside Assistance Program offers tech- our Customer Assistance Centre will be glad to assist you on nical help in the event of a breakdown. Call the toll-free road- our Toll Free no. 1800 209 7979 side assistance helpline number. For additional information, refer to "24X7 Roadside Assis- tance" section in the Owner’s manual. ii Dear Customer, Welcome to the TATA MOTORS family. We congratulate you on the purchase of your new vehicle and we are privileged to have you as our valued customer. We urge you to read this Owner's Manual carefully and familiarize yourself with the equipment descriptions and operating instruc- tions before driving. Always carry out prescribed service/maintenance work as well as any required repairs at an authorized TATA MOTORS Dealers or Authorized Service Centre’s (TASCs). Use only genuine parts for continued reliability, safety and performance of your vehicle. You are welcome to contact our dealer or Customer Assistance toll free no. -
Environmental Product Portfolio 2 KNORR-BREMSE ENVIRONMENTAL PRODUCT PORTFOLIO
1 Environmental product portfolio 2 KNORR-BREMSE ENVIRONMENTAL PRODUCT PORTFOLIO Our contribution towards making mobility more environmentally friendly and energy-efficient In recent years, climate change and environmental Our product portfolio offers solutions that protection have taken on greater relevance for >> minimize energy consumption and enhance the commercial vehicle and rail vehicle sectors. In fuel efficiency, response, Knorr-Bremse has for many years been >> reduce atmospheric emissions, giving top priority to developing fuel-saving, >> minimize noise emissions, emission-reducing technologies with solutions >> protect the environment by using eco-friendly tailored to market needs. materials and manufacturing processes. ENERGY EFFICIENCY PROTECTING RESOURCES AND REDUCING EMISSIONS • CFCB bogie-mounted block brakes • Oil-free compressor with sound insulation • Compact brake calipers • Flexpad Silent brake pad • Lightweight HVAC units, doors, brake discs • LL composite brake block • iCOM Assist (LEADER) driver assistance system • Sanding systems with reduced sand use DIVISION • Driving and training simulators • iCOM Energy Metering • HVAC systems • IFE Generation 4 entrance system RAIL VEHICLE RAIL • Isobar brake pads • Aluminum brake discs • Pneumatic disc brakes • Electronic braking system (EBS) • Electronic air treatment • Engine retarder DIVISION • Aluminum compressor casing • Genuine remanufactured products • Compressor with clutch • Electric screw compressor • Compressor with energy-saving system • Mechatronic transmission