Finite Element Analysis of the Stress and Deformation Fields Around the Blunting Crack Tip
Total Page:16
File Type:pdf, Size:1020Kb
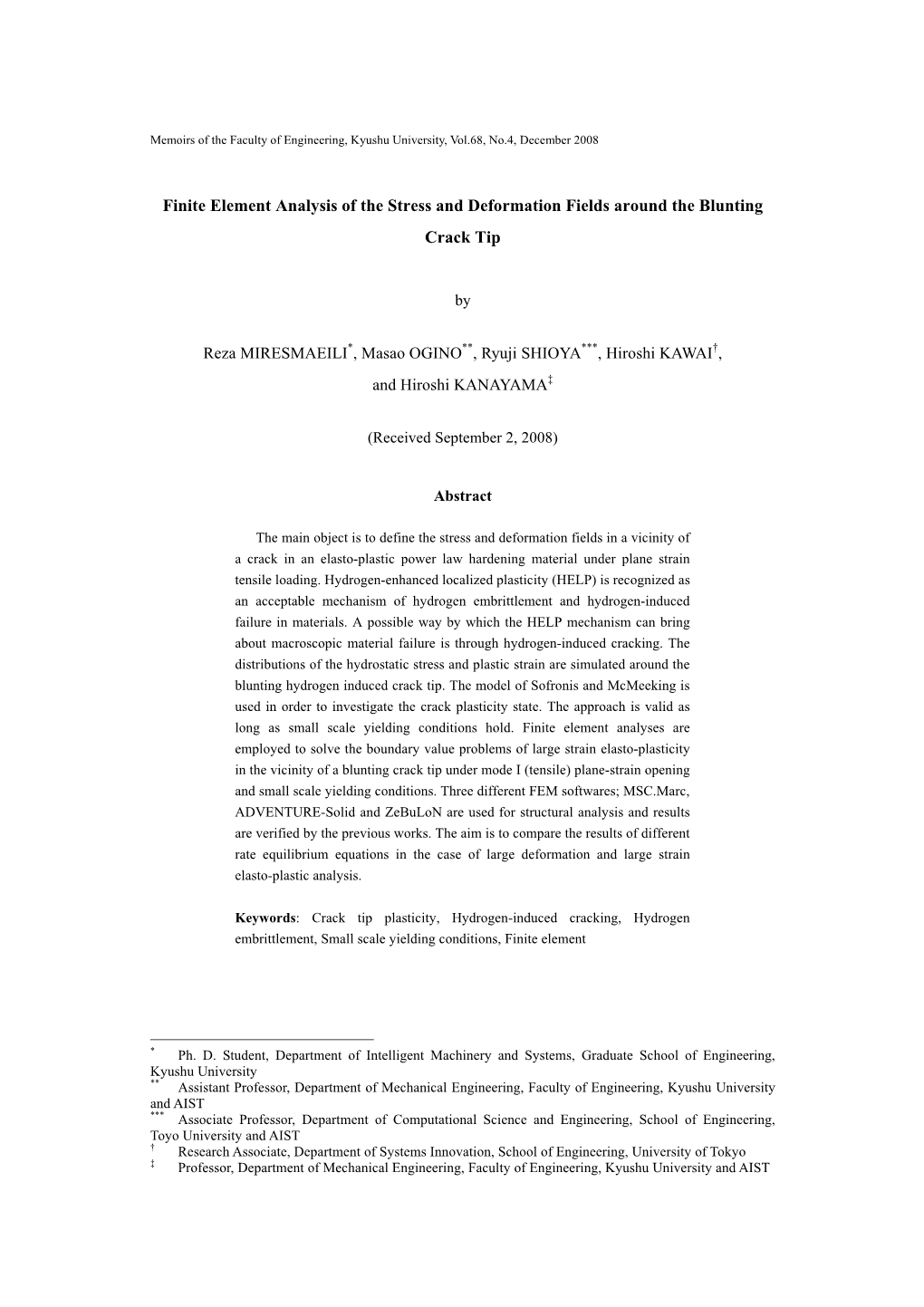
Load more
Recommended publications
-
MSC.Marc and MSC.Marc Mentat
MSC.Marc and MSC.Marc Mentat Release Guide Version 2003 Copyright 2003 MSC.Software Corporation All rights reserved. Printed in U.S.A. Corporate Europe MSC.Software Corporation MSC.Software GmbH 2 MacArthur Place Am Moosfeld Santa Ana, CA 92707 81829 München, GERMANY Telephone: (714) 540-8900 Telephone: (49) (89) 431 987 0 Fax: (714) 784-4056 Fax: (49) (89) 436 1716 Asia Pacific Worldwide Web MSC Japan Ltd. www.mscsoftware.com Entsuji-Gadelius Building 2-39, Akasaka 5-chome Minato-ku, Tokyo 107-0052, JAPAN Telephone: (81) (3) 3505 0266 Fax: (81) (3) 3505 0914 Part Number: MA*V2003*Z*Z*Z*DC-REL Disclaimer THE CONCEPTS, METHODS, AND EXAMPLES PRESENTED IN THE DOCUMENTATION ARE FOR ILLUSTRATIVE AND EDUCATIONAL PURPOSES ONLY, AND ARE NOT INTENDED TO BE EXHAUSTIVE OR TO APPLY TO ANY PARTICULAR ENGINEERING PROBLEM OR DESIGN. USER ASSUMES ALL RISKS AND LIABILITY FOR RESULTS OBTAINED BY THE USE OF THE COMPUTER PROGRAMS DESCRIBED HEREIN. IN NO EVENT SHALL MSC.SOFTWARE CORPORATION BE LIABLE TO ANYONE FOR ANY SPECIAL, COLLATERAL, INCIDENTAL, INDIRECT OR CONSEQUENTIAL DAMAGES ARISING OUT OF, RESULTING FROM, OR IN CONNECTION WITH USE OF THE CONTENTS OR INFORMATION IN THE DOCUMENTATION. MSC.SOFTWARE CORPORATION ASSUMES NO LIABILITY OR RESPONSIBILITY FOR ANY ERRORS THAT MAY APPEAR IN THE DOCUMENTATION. THE DOCUMENTATION IS PROVIDED ON AN “AS-IS” BASIS AND ALL EXPRESS AND IMPLIED CONDITIONS, REPRESENTATIONS AND WARRANTIES, INCLUDING ANY IMPLIED WARRANTY OF MERCHANTABILITY OR FITNESS FOR A PARTICULAR PURPOSE, ARE DISCLAIMED, EXCEPT TO THE EXTENT THAT SUCH DISCLAIMERS ARE HELD TO BE LEGALLY INVALID. MSC.SOFTWARE CORPORATION RESERVES THE RIGHT TO MAKE CHANGES IN SPECIFICATIONS AND OTHER INFORMATION CONTAINED IN THE DOCUMENTATION WITHOUT PRIOR NOTICE. -
MSC.Marc® and MSC.Marc® Mentat®
MSC.Marc® and MSC.Marc® Mentat® Release Guide Version 2005 Copyright 2004 MSC.Software Corporation All rights reserved. Printed in U.S.A. Corporate Europe MSC.Software Corporation MSC.Software GmbH 2 MacArthur Place Am Moosfeld Santa Ana, CA 92707 81829 München, GERMANY Telephone: (714) 540-8900 Telephone: (49) (89) 431 987 0 Fax: (714) 784-4056 Fax: (49) (89) 436 1716 Asia Pacific Worldwide Web MSC Software Japan Ltd. www.mscsoftware.com Shinjuku First West 8F 23-7 Nishi Shinjuku 1-Chome, Shinjuku-Ku Tokyo 160-0023, JAPAN Telephone: (81) (3) 6911 1200 Fax: (81) (3) 6911 1201 Part Number: MA*V2005*Z*Z*Z*DC-REL This document, and the software described in it, are furnished under license and may be used or copied only in accordance with the terms of such license. Any reproduction or distribution of this document, in whole or in part, without the prior written authorization of MSC.Software Corporation is strictly prohibited. MSC.Software Corporation reserves the right to make changes in specifications and other information contained in this document without prior notice. The concepts, methods, and examples presented in this document are for illustrative and educational purposes only and are not intended to be exhaustive or to apply to any particular engineering problem or design. THIS DOCUMENT IS PROVIDED ON AN “AS-IS” BASIS AND ALL EXPRESS AND IMPLIED CONDITIONS, REPRESENTATIONS AND WARRANTIES, INCLUDING ANY IMPLIED WARRANTY OF MERCHANTABILITY OR FITNESS FOR A PARTICULAR PURPOSE, ARE DISCLAIMED, EXCEPT TO THE EXTENT THAT SUCH DISCLAIMERS ARE HELD TO BE LEGALLY INVALID. MSC.Software logo, MSC, MSC., MSC/, MSC.ADAMS, MSC.Dytran, MSC.Marc, MSC.Patran, ADAMS, Dytran, MARC, Mentat, and Patran are trademarks or registered trademarks of MSC.Software Corporation or its subsidiaries in the United States and/or other countries. -
MSC.Marc Volume E
MSC.Marc Volume E Demonstration Problems Version 2001 Copyright 2001 MSC.Software Corporation Printed in U. S. A. This notice shall be marked on any reproduction, in whole or in part, of this data. Corporate Europe MSC.Software Corporation MSC.Software GmbH 2 MacArthur Place Am Moosfeld Santa Ana, CA 92707 81829 München, GERMANY Telephone: (714) 540-8900 Telephone: (49) (89) 431 987 0 Fax: (714) 784-4056 Fax: (49) (89) 436 1716 Asia Pacific Worldwide Web MSC Japan Ltd. www.mscsoftware.com Entsuji-Gadelius Building 2-39, Akasaka 5-chome Minato-ku, Tokyo 107-0052, JAPAN Telephone: (81) (3) 3505 0266 Fax: (81) (3) 3505 0914 Document Title: MSC.Marc Volume E: Demonstration Problems, Version 2001 Part Number: MA*2001*Z*Z*Z*DC-VOL-E-I Revision Date: April, 2001 Proprietary Notice MSC.Software Corporation reserves the right to make changes in specifications and other information contained in this document without prior notice. ALTHOUGH DUE CARE HAS BEEN TAKEN TO PRESENT ACCURATE INFORMATION, MSC.SOFTWARE CORPORATION DISCLAIMS ALL WARRANTIES WITH RESPECT TO THE CONTENTS OF THIS DOCUMENT (INCLUDING, WITHOUT LIMITATION, WARRANTIES OR MERCHANTABILITY AND FITNESS FOR A PARTICULAR PURPOSE) EITHER EXPRESSED OR IMPLIED. MSC.SOFTWARE CORPORATION SHALL NOT BE LIABLE FOR DAMAGES RESULTING FROM ANY ERROR CONTAINED HEREIN, INCLUDING, BUT NOT LIMITED TO, FOR ANY SPECIAL, INCIDENTAL OR CONSEQUENTIAL DAMAGES ARISING OUT OF, OR IN CONNECTION WITH, THE USE OF THIS DOCUMENT. This software documentation set is copyrighted and all rights are reserved by MSC.Software Corporation. Usage of this documentation is only allowed under the terms set forth in the MSC.Software Corporation License Agreement. -
Technical Paper
NONLINEAR FINITE ELEMENT ANALYSIS OF ELASTOMERS Technical Paper P REFACE MSC.Software Corporation, the Appendices describe the physics and worldwide leader in rubber analysis, mechanical properties of rubber, proper would like to share some of our modeling of incompressibility in rubber experiences and expertise in analyzing FEA, and most importantly, testing elastomers with you. methods for determination of material This White Paper introduces you to the properties. Simulation issues and useful nonlinear finite element analysis (FEA) hints are found throughout the text and of rubber-like polymers generally grouped in the Case Studies. under the name “elastomers.” You may Rubber FEA is an extensive subject, which have a nonlinear rubber problem—and involves rubber chemistry, manufacturing not even know it… processes, material characterization, finite element theory, and the latest advances in computational mechanics. A selected list The Paper is primarily intended for two of Suggestions for Further Reading is types of readers: included. These references cite some of ENGINEERING MANAGERS who are the most recent research on FEA of involved in manufacturing of elastomeric elastomers and demonstrate practical components, but do not currently possess applications. They are categorized by nonlinear FEA tools, or who may have an subject for the reader’s convenience. educational/professional background other than mechanical engineering. DESIGN ENGINEERS who are perhaps familiar with linear, or even nonlinear, FEA concepts, but would like to know more about analyzing elastomers. It is assumed that the reader is familiar with basic principles in strength of materials theory. This White Paper is a complement to MSC.Software’s White Paper on Nonlinear FEA, which introduces the reader to nonlinear FEA methods and also includes metal forming applications. -
MSC.Marc Volume A
MSC.Marc Volume A Theory and User Information Version 2003 Copyright 2003 MSC.Software Corporation All rights reserved. Printed in U.S.A. Corporate Europe MSC.Software Corporation MSC.Software GmbH 2 MacArthur Place Am Moosfeld Santa Ana, CA 92707 81829 München, GERMANY Telephone: (714) 540-8900 Telephone: (49) (89) 431 987 0 Fax: (714) 784-4056 Fax: (49) (89) 436 1716 Asia Pacific Worldwide Web MSC Japan Ltd. www.mscsoftware.com Entsuji-Gadelius Building 2-39, Akasaka 5-chome Minato-ku, Tokyo 107-0052, JAPAN Telephone: (81) (3) 3505 0266 Fax: (81) (3) 3505 0914 Part Number: MA*V2003*Z*Z*Z*DC-VOL-A Disclaimer THE CONCEPTS, METHODS, AND EXAMPLES PRESENTED IN THE DOCUMENTATION ARE FOR ILLUSTRATIVE AND EDUCATIONAL PURPOSES ONLY, AND ARE NOT INTENDED TO BE EXHAUSTIVE OR TO APPLY TO ANY PARTICULAR ENGINEERING PROBLEM OR DESIGN. USER ASSUMES ALL RISKS AND LIABILITY FOR RESULTS OBTAINED BY THE USE OF THE COMPUTER PROGRAMS DESCRIBED HEREIN. IN NO EVENT SHALL MSC.SOFTWARE CORPORATION BE LIABLE TO ANYONE FOR ANY SPECIAL, COLLATERAL, INCIDENTAL, INDIRECT OR CONSEQUENTIAL DAMAGES ARISING OUT OF, RESULTING FROM, OR IN CONNECTION WITH USE OF THE CONTENTS OR INFORMATION IN THE DOCUMENTATION. MSC.SOFTWARE CORPORATION ASSUMES NO LIABILITY OR RESPONSIBILITY FOR ANY ERRORS THAT MAY APPEAR IN THE DOCUMENTATION. THE DOCUMENTATION IS PROVIDED ON AN “AS-IS” BASIS AND ALL EXPRESS AND IMPLIED CONDITIONS, REPRESENTATIONS AND WARRANTIES, INCLUDING ANY IMPLIED WARRANTY OF MERCHANTABILITY OR FITNESS FOR A PARTICULAR PURPOSE, ARE DISCLAIMED, EXCEPT TO THE EXTENT THAT SUCH DISCLAIMERS ARE HELD TO BE LEGALLY INVALID. MSC.SOFTWARE CORPORATION RESERVES THE RIGHT TO MAKE CHANGES IN SPECIFICATIONS AND OTHER INFOR- MATION CONTAINED IN THE DOCUMENTATION WITHOUT PRIOR NOTICE. -
Nonlinear Finite Element and Fiber Element Analysis of Concrete Filled Square Steel Tubular (Cfst) Under Static Loading
MATEC Web of Conferences 258, 05025 (2019) https://doi.org/10.1051/matecconf/20192 5805025 SCESCM 20 18 Nonlinear finite element and fiber element analysis of concrete filled square steel tubular (cfst) under static loading Mahmud Kori Effendi1,* Nor Hayati Abdul Hamid2 1 Civil Engineering Departement, Faculty of Engineering, Universitas Negeri Semarang (UNNES), Indonesia 2 Institute for Infrastructure Engineering, Sustainability and Management (IIESM), Universiti Teknologi MARA, 40450 Shah Alam, Selangor, Malaysia Abstract. The combination of thin-walled steel structure with concrete infill can be used as the alternative material properties in the building in Indonesia. This composite material is suitable for seismic- resistant building because it has more ductility than conventional material. In the tsunami event, some tsunami debris strikes the building and induced partial or full collapse of the building. The loading tip shape of tsunami debris which contacts to a tubular surface affects the local deformation or buckling mode of the thin-walled structures. In order to investigate the effects, we conducted three-dimensional nonlinear finite element analyses of concrete filled square steel tubular members subjected to concentrated lateral loads by using the finite element analysis (FEM) program MSC Marc/Mentat. The fiber element analysis is also performed to reduce the analysis time of FEM and simplify the analysis. The accuracy of the FEM and fiber element analysis is verified by the experiment. Being based on the parametric numerical study, it discusses the effect of axial load on the load-deflection relations. It shows that the higher the axial load, the more degradation the ductility of the structure. -
Finite Element Analysis and Simulation Study on Micromachining of Hybrid Composite Stacks Using Micro Ultrasonic Machining Process ______
FINITE ELEMENT ANALYSIS AND SIMULATION STUDY ON MICROMACHINING OF HYBRID COMPOSITE STACKS USING MICRO ULTRASONIC MACHINING PROCESS ____________________________________ A Thesis Presented to the Faculty of California State University, Fullerton ____________________________________ In Partial Fulfillment of the Requirements for the Degree Master of Science in Mechanical Engineering ____________________________________ By Panchal, Sagar Rajendrakumar Thesis Committee Approval: Sagil James, Department of Mechanical Engineering Nina Robson, Department of Mechanical Engineering Darren Banks, Department of Mechanical Engineering Spring, 2018 ABSTRACT Hybrid composites stacks are multi-material laminates which find extensive applications in industries such as aerospace, automobile, and electronics and so on. Most hybrid composites consist of multiple layers of fiber composites and metal sheets stacked together. These composite stacks have excellent physical and mechanical properties including high strength, high hardness, high stiffness, excellent fatigue resistance and low thermal expansion. Micromachining of these materials require particular attention as conventional methods such as micro-drilling is extremely challenging considering the non-homogeneous structure and anisotropic nature of the material layers. Micro Ultrasonic Machining (μUSM) is a manufacturing process capable of machining such difficult-to-machine materials with ultraprecision. Experimental study showed that μUSM process could successfully machine hybrid composite stacks -
Thesis Master’S Degree in Material Engineering Finite Element Analysis of Hot Rolling in the Blooming Mill
Thesis Master’s degree in material engineering Finite element analysis of hot rolling in the blooming mill Author: Petter Persson Mentor at Sandvik: Mattias Gärdsback and Fredrik Sandberg Supervisor at University of Dalarna: Kumar Babu Surreddi Examiner: Lars Karlsson Subject: Materials Engineering Course: MP4001 Credit: 30 hp Date of examination: 2016-06-13 Abstract: During this thesis work a coupled thermo-mechanical finite element model (FEM) was built to simulate hot rolling in the blooming mill at Sandvik Materials Technology (SMT) in Sandviken. The blooming mill is the first in a long line of processes that continuously or ingot cast ingots are subjected to before becoming finished products. The aim of this thesis work was twofold. The first was to create a parameterized finite element (FE) model of the blooming mill. The commercial FE software package MSC Marc/Mentat was used to create this model and the programing language Python was used to parameterize it. Second, two different pass schedules (A and B) were studied and compared using the model. The two pass series were evaluated with focus on their ability to heal centreline porosity, i.e. to close voids in the centre of the ingot. This evaluation was made by studying the hydrostatic stress (σm), the von Mises stress (σeq) and the plastic strain (εp) in the centre of the ingot. From these parameters the stress triaxiality (Tx) and the hydrostatic integration parameter (Gm) were calculated for each pass in both series using two different transportation times (30 and 150 s) from the furnace. The relation between Gm and an analytical parameter (Δ) was also studied. -
Finite Element Analysis of CFRP Composite Material Machining: a Review
International Research Journal of Engineering and Technology (IRJET) e-ISSN: 2395-0056 Volume: 05 Issue: 01 | Jan-2018 www.irjet.net p-ISSN: 2395-0072 Finite element analysis of CFRP composite material machining: A Review Vyavahare S.S1, Pathare Y.S2, Shelke S.V3 1,2 Assistant Professor, Department of Mechanical Engineering, Dr. Vithalrao Vikhe Patil College of Engineering, Ahmednagar, India 3 Assistant Professor, Department of Mechanical Engineering, Pravara Rural Engineering College, Loni, Ahmednagar, India -------------------------------------------------------------------***--------------------------------------------------------------------- Abstract - Rapid increase in utilization carbon fiber Using finite element simulation method, we can observe the composite material (widely used in aviation, aerospace, physical phenomena in the process to simulate actual system defense and automotive, electronic information and high- by physical or mathematical models. Realized the speed machinery and other civilian areas) in these years led to visualization of parameters value, it can also be used to numerical modelling of material behavior & defect formation predict the surface defects in materials processing, guide the while machining. But anisotropic & inhomogeneous nature of tool design and parameters optimization and optimize the material causes challenges while modelling & result cutting process parameters and so on. Therefore the interpretation. Based on the comprehensive literature survey application of finite element techniques to study the cutting from the past few years, it is noticed that limited research has process has a very important significance. been made and published concerning machining modelling of CFRP (Carbon Fiber Reinforced Polymer) composite material. 1.1 Metal Cutting versus Composite cutting This paper gives precise review of current trends in modelling of machining CFRP composites in different solvers in different Shuji Usui et.al.[3] shows an essential difference exists countries. -
Multiscale Simulation of Metal Deformation in Deep Drawing Using Machine Learning Bachelor Integration Project
Multiscale simulation of metal deformation in deep drawing using machine learning Bachelor Integration Project Industrial Engineering & Management University of Groningen Author: F.M. Verwijs s3090345 Supervisors: Prof. dr. A. Vakis (First supervisor) Dr. ir. A.A. Geertsema (Second supervisor) Dr. S. Solhjoo (Daily supervisor) June 19th, 2019 Abstract Crystal plasticity modeling is a powerful and well-established computational materials science tool to investigate mechanical structure{property relations in crystalline materials. The mechanical behavior of crystalline matter is a multiscale problem, whereas the underlying deformation processes such as the slip of dislocations and their reactions and elastic interactions are microscopic problems, and the forming process itself is usually of a macroscopic nature. Information regarding the crystal plasticity of metals in deep drawing processes, can be obtained at microscale. However, for applicability, the larger scale is of importance. To transfer the crystal plasticity information to the larger scale, this information needs to be stored and arranged in a certain way. In this Integration Project, a novel method of integrating the simulations at microscale to larger scale is presented. Crystal plasticity information concerning the material behavior of deep drawing processes is obtained using the DAMASK simulation software, generating representative volume elements, based on various strain rates. An Artificial Neural Network shows the information generated from the crystal plasticity simulations in DAMASK and predicts new data points. The information that is arranged in this machine-learning neural network, will be loaded into a finite element analysis. Based on this information, simulations are performed in MSC.Marc. This ultimately yields the information at larger scale, desired in deep drawing processes. -
Features of MSC.Marc the World Leader in Nonlinear and Coupled Physics Simulation Features of MSC.Marc
MSC.visualNastran enterprise Features of MSC.Marc The World Leader in Nonlinear and Coupled Physics Simulation Features of MSC.Marc MSC.Software Corporation, the world leader in nonlinear and coupled physics simulation, introduces you to MSC.Marc, an integrated member of the MSC.visualNastran Enterprise family. MSC.Marc has been known since 1971 for its versatility in helping market leaders to design better products, and solve simple to complex real-world engineering problems. Today, MSC.Marc has evolved and matured through constant development and worldwide use by thousands of engineers. Please read on to discover how its many capabilities will enable you to solve the most challenging nonlinear and coupled physics problems. Table of Contents Element Technology .......................................................................... 1 Solution Procedures .......................................................................... 2 Parallel Processing .......................................................................... 2 Mesh Adaptivity .......................................................................... 3 Automated Contact Analysis .................................................................... 3 Metallic Materials .......................................................................... 4 Nonmetallic Materials .......................................................................... 5 Cyclic Symmetry .......................................................................... 5 Heat Transfer ......................................................................... -
The Analysis of the Constitutive Model Effect on Convergence of Results
Acta Mechanica Slovaca 16 (1): 66 - 72, 2012 * Corresponding author E-mail address: [email protected] (Dr inż. Stanisław Kut) The analysis of the constitutive model Article information Article history: AMS-Volume16-No.1-00144-12 effect on convergence of results with Received 15 January 2012 Accepted 15 February 2012 the experiment for FEM modeling of 3D issues with high elastic-plastic deformations Stanisław Kut Rzeszów University of Technology, Faculty of Mechanical Engineering and Aeronautics, Poland BIOGRAPHICAL NOTES Stanisław Kut, Dr inż. was born in 1975 in Ropczyce, Poland. He received his MSc. Eng. and PhD. degree at Rzeszow University of Technology. Since 2004 he is an assistant professor at the Department of Materials Forming and Processing, Faculty of Mechani- cal Engineering and Aeronautics, Rzeszow University of Technology. He is autor of 2 monographies, one patent, 6 patent applications and more than 50 publications in scientific journals and conference proceedings. KEY WORDS tension, FEM modeling, constitutive relation, finite elastic-plastic deformation, ductile fracture ABSTRACT This paper presents the results of experimental researches and FEM modeling for ten- sion process of an original plane specimen with notch. The specimen was made of the low carbon steel sheet with thickness of 4 mm. The modeling was performed with three different constitutive relationships, which are available in commercial software for modeling the non-linear issues with high strains. The three-dimensional numerical model was based on the experimental model. The results of individual models were compared with the experimental results. The special attention was paid to conver- gence of force characteristics and modeled specimen shapes in areas of the highest elastic-plastic deformations.