Optical Actuation of a Micromechanical Photodiode Via the Photovoltaic-Piezoelectric Effect A
Total Page:16
File Type:pdf, Size:1020Kb
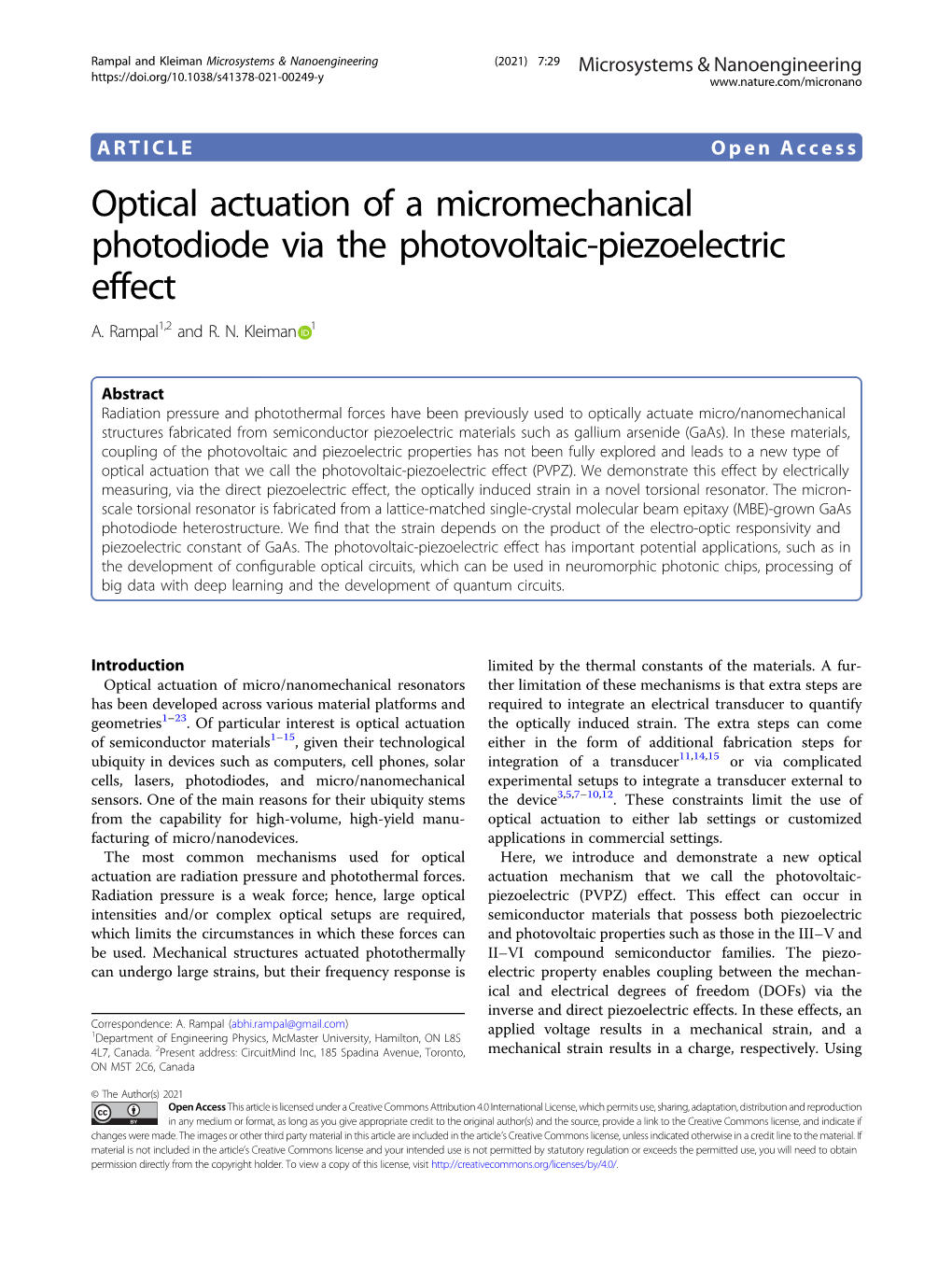
Load more
Recommended publications
-
Important Factors for Performance of Photovoltaic Cell
International Research Journal of Engineering and Technology (IRJET) e-ISSN: 2395-0056 Volume: 07 Issue: 04 | Apr 2020 www.irjet.net p-ISSN: 2395-0072 A Review : Important Factors for Performance of Photovoltaic Cell Pankaj L. Firake1, Pranav R. Mane2, Nagraj S. Dixit3 1,2,3 Assistant Professor, JSPM’s Rajarshi Shahu College of Engineering, Pune ---------------------------------------------------------------------***--------------------------------------------------------------------- Abstract - Energy is one of the requirements for life. There include wind power, solar power, geothermal energy, tidal are two main sources of energy: renewable and non-renewable power and hydroelectric power. The most important feature sources. Renewable energy is the energy which comes from of renewable energy is that it can be harnessed without the natural resources such as sunlight, wind, rain, geothermal release of harmful pollutants [1]. heat etc. The Sun is an extremely powerful energy source, and sunlight is by far the largest source of energy received Solar energy is radiant light and heat from the Sun that is by Earth. Even though, solar power is one of the most harnessed using a range of ever-evolving technologies such promising renewable energy technologies, allowing the as solar heating, photovoltaic, solar thermal energy etc. The generation of electricity from free, inexhaustible sunlight, it still facing a number of hurdles before it can truly replace large magnitude of solar energy available makes it a highly fossil fuels. A solar cell, or photovoltaic cell, is an electrical appealing source of electricity. The potential solar energy device that converts the energy of light directly into electricity that could be used by humans differs from the amount of by the photovoltaic effect. -
Harmonic Analysis of Photovoltaic Generation in Distribution Network and Design of Adaptive Filter
International Journal of Computing and Digital Systems ISSN (2210-142X) Int. J. Com. Dig. Sys. 9, No.1 (Jan-2020) http://dx.doi.org/10.12785/ijcds/090108 Harmonic Analysis of Photovoltaic Generation in Distribution Network and Design of Adaptive Filter Lue Xiong 1, Mutasim Nour 1 and Eyad Radwan2 1 School of Engineering and Physical Sciences Heriot-Watt University Dubai, Dubai, UAE 2 Electrical Engineering, Applied Science University, Amman, Jordan Received 30 Jul. 2019, Revised 21 Oct. 2019, Accepted 18 Dec. 2019, Published 01 Jan. 2020 Abstract: The aim of this paper is to investigate the effect of increased penetration level of Photovoltaic (PV) generation on the distribution network. Harmonic distortion is the main factor studied in this paper and a typical three-bus distribution network is built in MATLAB/Simulink to understand the harmonics problem. The obtained results show that current harmonics are more susceptible to fluctuate compared to voltage harmonics. Based on existing IEEE harmonic standards, total demand distortion of current (TDDi) is evaluated to estimate maximum PV penetration level at Point of Common Coupling (PCC), and the maximum acceptable TDDi at each bus differs according to specific loading and short-circuit levels. Meanwhile, total harmonic distortion of current (THDi) at inverter outputs represents inverter performance. Instead of assessing at standard test conditions (STC), the impact of irradiance variations is studied. Low irradiance results in an increased THDi of the inverter whilst doesn’t explicitly affect TDDi at PCC. A simple and low-cost solution is proposed to dynamically vary the settings of inverter’s filter elements against irradiance, and harmonic distortion at low irradiance of the inverter is successfully mitigated. -
Automation of Home Appliances Using Solar Energy - a Smart Home
International Journal of Future Innovative Science and Engineering Research Volume-1, Issue-I ISSN (Online): 2454- 1966 Research Manuscript Title AUTOMATION OF HOME APPLIANCES USING SOLAR ENERGY - A SMART HOME Website: www.istpublications.com A.ALPHONSA R.SHALINI S.SUDHA PG Students , Communication System, Sona College Of Technology, Salem,Tamilnadu, India. MARCH - 2015 A.ALPHONSA R.SHALINI S.SUDHA, “ AUTOMATION OF HOME APPLIANCES USING SOLAR ENERGY - A SMART HOME”, International Journal of Future Innovative Science and Engineering Research, Vol. -1, Issue – 1 , Page -10 IJFISER International Journal of Future Innovative Science and Engineering Research, Volume-1, Issue-I ISSN (Online): 2454- 1966, AUTOMATION OF HOME APPLIANCES USING SOLAR ENERGY - A SMART HOME ABSTRACT The application design of smart home model system using solar energy here is based on microcontroller. This project mainly focuses on reducing the electricity bill by using solar energy generated from sun for home appliances. Solar panel is made up of PV (photo voltaic) cells, these cells collect sunlight and turn its energy into DC and here DC boost converter is used to boost up the solar energy and the “inverter” converts the DC to AC energy and eventually supplies the current to all appliances, when the solar power is reduced to minimum voltage, then the battery is tripped to EB current immediately and moreover the value (or) range of the current and other related details are transferred to PC using zigbee, so that the current status of the operation can be monitored. Thus the electricity bill is reduced immensively. Keywords : solar panel , inverter , EB current ,ZIGBEE . -
Photovoltaic Effect Produced in Silicon Solar Cells by X- and Gamma Rays
---------~ JO URNAL OF RESEARCH of the National Bureau of Standards-A. Physics a nd Chemistry Vol. 64A, No.4, July- August 1960 Photovoltaic Effect Produced in Silicon Solar Cells by x- and Gamma Rays J Karl Scharf (J anuary 25, 1960) T he open-circuit voltage a nd photocur-rcnt produced in a silicon sola r cell by X- a nd gamma rays we re measured as a function of exposure dose ra te, cell temperature, angle of l incidence of radiation, a nd p hoton energy. This photore ponse was stable a nd propor tional to t he exposure dose rate, which was appli ed up to a maximum of J.8 X lOo roentgen per minute for X -rays a nd 4 X 10 2 roentgen per minute for C060 gamma rays. At a n expo I sure dose rate of 1. roentgen per mi n ute t he response was of the order of 10- 5 vol t for t he open-circuit voltage a nd 10- 8 a mpere for the photocurrent. At high exposure dose rates of Cooo gam ma rays, radiation damage became apparent. The temperature dependence of the photoresponse was controll ed by the te mpera ture dependence of t he cell resistance. The directional dependence of t he photoresponse vari ed wit h t he quality of radiation a nd for Cooo gamma rays was very small for a ngles from 0° to 70 °. The photoresponse decreased with increasin g p hoton energy but cha nged onl y litt le between 200 a nd 1,250 kilo electron vo lts. -
Organic Solar Cell
A MILESTONE IN SOLAR CELLS: ORGANIC SOLAR CELL Prashant Vats1, Prashant Kumar Tayal2, Neeru Goyal3, Rajesh Bhargava4 1,2,4Faculty, Department of Electrical Engineering, L.I.E.T., ALWAR (Raj), (India) 3Faculty, Department of Electrical Engineering, Govt. Polytecnic College, ALWAR (Raj), (India) ABSTRACT Organic solar cells are mostly flexible and lightweight—a good solution to low cost energy production, which can have a manufacturing advantages over inorganic solar cell materials. An organic solar cell uses organic electronics, which deals with conducting polymers or small organic molecules. In 1959, Kallamann and Pope reported a photovoltaic effect in a single crystal of anthracene which was sandwiched between two similar electrodes and illuminated from one side. But they could not explain the phenomenon completely Keywords : Organic Electronics, Photovoltaic Effect, Illuminated etc. I. INTRODUCTION The first organic solar cell was reported by Tang in 1986, with a power conversion efficiency of 1 per -cent (Tang etal.). The simple working principle for photovoltaic devices is that of ‘light in and current out’ which can be analyzed by seven processes: photon absorption, excitation formation and migration, exciton dissociation, charge transport and charge collection at the electrode. The structure of an organic solar cell is very simple. A setup with one photoactive material and electrodes constructed at top and bottom can show a photovoltaic current. In Figure 1, the organic solar cell consists of a photoactive layer composed of two different materials: donor and acceptor. Here the conducting glass acts as an anode and the metal acts as a cathode. The donor and acceptor material has two energy levels one is the Highest Occupied Molecular Orbital (HOMO) and the other is the Lowest Unoccupied Molecular Orbital (LUMO) and the energy gap between these two layers is the band gap. -
The History of Solar
Solar technology isn’t new. Its history spans from the 7th Century B.C. to today. We started out concentrating the sun’s heat with glass and mirrors to light fires. Today, we have everything from solar-powered buildings to solar- powered vehicles. Here you can learn more about the milestones in the Byron Stafford, historical development of solar technology, century by NREL / PIX10730 Byron Stafford, century, and year by year. You can also glimpse the future. NREL / PIX05370 This timeline lists the milestones in the historical development of solar technology from the 7th Century B.C. to the 1200s A.D. 7th Century B.C. Magnifying glass used to concentrate sun’s rays to make fire and to burn ants. 3rd Century B.C. Courtesy of Greeks and Romans use burning mirrors to light torches for religious purposes. New Vision Technologies, Inc./ Images ©2000 NVTech.com 2nd Century B.C. As early as 212 BC, the Greek scientist, Archimedes, used the reflective properties of bronze shields to focus sunlight and to set fire to wooden ships from the Roman Empire which were besieging Syracuse. (Although no proof of such a feat exists, the Greek navy recreated the experiment in 1973 and successfully set fire to a wooden boat at a distance of 50 meters.) 20 A.D. Chinese document use of burning mirrors to light torches for religious purposes. 1st to 4th Century A.D. The famous Roman bathhouses in the first to fourth centuries A.D. had large south facing windows to let in the sun’s warmth. -
A Digital-Twin and Machine-Learning Framework for the Design of Multiobjective Agrophotovoltaic Solar Farms
Computational Mechanics https://doi.org/10.1007/s00466-021-02035-z ORIGINAL PAPER A digital-twin and machine-learning framework for the design of multiobjective agrophotovoltaic solar farms T. I. Zohdi1 Received: 2 March 2021 / Accepted: 10 May 2021 © The Author(s), under exclusive licence to Springer-Verlag GmbH Germany, part of Springer Nature 2021 Abstract This work develops a computational Digital-Twin framework to track and optimize the flow of solar power through complex, multipurpose, solar farm facilities, such as Agrophotovoltaic (APV) systems. APV systems symbiotically cohabitate power- generation facilities and agricultural production systems. In this work, solar power flow is rapidly computed with a reduced order model of Maxwell’s equations, based on a high-frequency decomposition of the irradiance into multiple rays, which are propagated forward in time to ascertain multiple reflections and absorption for various source-system configurations, varying multi-panel inclination, panel refractive indices, sizes, shapes, heights, ground refractive properties, etc. The method allows for a solar installation to be tested from multiple source directions quickly and uses a genomic-based Machine-Learning Algorithm to optimize the system. This is particularly useful for planning of complex next-generation solar farm systems involving bifacial (double-sided) panelling, which are capable of capturing ground albedo reflection, exemplified by APV systems. Numerical examples are provided to illustrate the results, with the overall goal being to provide a computational framework to rapidly design and deploy complex APV systems. Keywords Agrophotovoltaics · Digital-twin · Machine-learning 1 Introduction gies to store heat and redeploy to run steam turbines, (e) artificial photosynthesis (biomimicry of plants), etc. -
The Use of Solar Powered UAV's in Measuring Air Quality
Thesis Milieu- en Natuurwetenschappen The use of solar powered UAV’s in measuring air quality Ronald Muijtjens 3032760 Supervisor: Boudewijn Elsinga MSc 01-07-2013 Summary This thesis discussed the possibility of using solar powered UAV’s as a means of measuring air quality. As Smidl has shown it is possible to use a UAV in case of a single source of pollution in addition to existing ground-stations. Two UAV’s can achieve the same quality measurement data as 30 ground-stations. However those UAV’s cannot stay airborne forever while ground- stations can measure day and night. Geo-stationary satellites can observe the same spot continuously but are inaccurate when clouds are blocking the view. Airborne measurements conducted by weather balloons only create a vertical profile whereas airplanes and zeppelins can give 3d profile of the pollution. This thesis also presented a guideline which can help with designing (and making) a solar powered UAV capable of doing air quality measurements in the boundary layer. It has the advantage to measure everywhere as long as the sun shines. With increasing miniaturization of electronics better sensors can be put on this UAV. Advancements in photovoltaic techniques will ensure that the UAV also flies in the winter or less clear skies. As shown in chapter 3, flight on solar power is only possible around noon for the months April until September and in June it is possible (with the 24.2% cells) to fly solely on solar power from 9am till 3pm.The 30.8% cells can achieve a continuous flight from 8am till 5pm in June. -
Basic Photovoltaic Principles and Methods Page Chapter 5
c Notice This publication was prepared under a contract to the United States Government. Neither the United States nor the United States Department of Energy, nor any of their employees, nor any of their contractors, subcontractors, or their employees, makes any warranty, expressed or implied, or assumes any legal liability or responsibility for the accuracy, completeness or usefulness of any information, apparatus, product or process disclosed, or represents that its use would not infringe privately owned rights. Printed in the United States of America Available in print from: Superintendent of Documents U.S. Government Printing Office Washington, DC 20402 Available in microfiche from: National Technical Information Service U.S. Department of Commerce 5285 Port Royal Road Springfield, VA 22161 Stock Number: SERIISP-290-1448 Information in this publication is current as of September 1981 Basic Photovoltaic Principles and Me1hods SER I/SP-290-1448 Solar Information Module 6213 Published February 1982 This book presents a nonmathematical explanation of the theory and design of PV solar cells and systems. It is written to address several audiences: engineers and scientists who desire an introduction to the field of photovoltaics, students interested in PV science and technology, and end users who require a greater understanding of theory to supplement their applications. The book is effectively sectioned into two main blocks: Chapters 2-5 cover the basic elements of photovoltaics-the individual electricity-producing cell. The reader is told why PV cells work, and how they are made. There is also a chapter on advanced types of silicon cells. Chapters 6-8 cover the designs of systems constructed from individual cells-including possible constructions for putting cells together and the equipment needed for a practioal producer of electrical energy. -
Effect of Soiling on the Performance of Photovoltaic Modules in Kalkbult, South Africa
Master’s Thesis 2016 30 ECTS Department of Mathematical Sciences and Technology Effect of Soiling on the Performance of Photovoltaic Modules in Kalkbult, South Africa Mari Benedikte Øgaard Environmental Physics and Renewable Energy Preface This study is investigating the effect of soiling on the performance of photovoltaic modules in Kalkbult, South Africa, and is based on an initiative promoted by Institute for Energy Technology (IFE), in collaboration with Stellenbosch University and Scatec Solar. Calling the process of writing a master thesis an adventure is overused and a cliché. However, this semester has led me across the world, into the deepest deserts and up medium tall mountains. I have eaten antelope, been defrauded, met incredible nice and interesting people, I got to test my more practical engineering skills by fixing a car with a rope in the middle of nowhere, and I almost died a few times because I never got used to cars driving on the wrong side of the road. And I have learned a lot. So, I will discard my reluctance towards pompous language, and call it an adventure anyway. This adventure would not have been so fun and interesting if it had not been for all the people assisting me along the way. First of all, I want to thank Josefine Selj, my supervisor at IFE, for optimistic support and excellent guidance. I would also like to thank my supervisor at NMBU, Arne Auen Grimenes, for his enthusiasm, invaluable advices and time. I have to thank Armand du Plessis, Carmen Lewis and Tashriq Pandy for interesting discussions, answering all my questions regarding the test station and measuring equipment, and for support during my experiments at the test station in Kalkbult. -
A Study on the Photovoltaic Effect - Solar Cells
A Study on the Photovoltaic Effect - Solar Cells A Group Project by Thaveesakdi Keowsim, Project Coordinator (Thailand) Jean Baptiste Bwanakeye (Rwanda) Htein Lin (Burma) University of Florida Training in Alternative Energy Technologies Program Sponsored by The U.S. Agency For International Development (US AID) 5th Session (22 February - 4 June 1982) Contents Page Acknowledgement ...... ... ......................... i Proposal .... .... ............................ .. Abstract .... .. ... ............................ .. iv I. Theoretical Studies ........ ....................... 1 A Solar Radiation Principles and Properties ............. .. B. Semiconductor Basics .... .... .................... 2 1. Band Theory ...... .. ....................... 2 2. Optical Effects ....... ..................... 4 3. Photovoltaic Junction Properties ..... ........... 6 a. P-N Junction .... .. ... .................. 6 b. Voltage-Current Relationship ..... ........... 6 c. Conversion Efficiency and Materials .... ........ 6 d. Limitations ........ .................... 8 e. Temperature Effects ..... .. ................ 8 C. The Principles Underlying the Photcvoltaic Effect ........10 1. Light Absorption in Semiconductor ... ............ .. 10 2. Charge Separation in the Photovoltaic Cell ... ....... 10 3. Migration of Charge Carriers to the Charge Separation Site ..... ........................ 11 4. Short Circuit Current ....... .................. 12 5. Current Voltage Characteristic and Maximum Efficiency . 13 6. Open Circuit Voltage and Its Dependence on -
Renewable Energy Option. Photovoltaic Solar Power
A RENEWABLE ENERGY OPTION PHOTOVOLTAIC SOLAR POWER 2 A RENEWABLE ENERGY OPTION PHOTOVOLTAIC SOLAR POWER THE ENERGY OF THE SUN CURRENT STATE OF KNOWLEDGE– Photovoltaic systems connected to a power grid represent 95% of the current market, with off-grid systems representing The photovoltaic industry has made considerable progress the remaining 5%. in the last decade. Its installed capacity shot from 1,790 MW to In Québec, centralized photovoltaic solar power genera- 137,000 MW between 2001 and 2013, an average increase of tion is in the experimental stage. While distributed generation PHOTOVOLTAIC 40% per year. In 2013, photovoltaic solar power accounted for does exist, it is still very rare. SOLAR POWER: about 1% of the world’s total electricity output and 4% of the ENERGY FROM available installed capacity. SUNLIGHT, CONVERTED PHOTOVOLTAIC SOLAR POTENTIAL– DIRECTLY INTO The availability of solar energy varies: the amount of sunshine ELECTRICITY BY MEANS depends on the time of day, weather and season, and it can OF A PHOTOVOLTAIC be difficult to predict. Daily sunshine levels in Canada also vary by region. In Québec, solar energy is unavailable during COLLECTOR peak demand periods (mornings and evenings) in the winter. As a result, photovoltaic systems must be adapted to the wide swing in sunlight levels we experience between the summer and winter, especially in northern Québec. This fluctuating availability of solar energy has a number of technical repercussions for photovoltaic systems connected to Québec’s transmission system, especially if the total or local installed capacity becomes significant. Ultimately, these tech- nical constraints will have an impact on the choice of power generation system, in light of the costs involved.