Heat Flux Sensor for Ash Fouling Monitoring
Total Page:16
File Type:pdf, Size:1020Kb
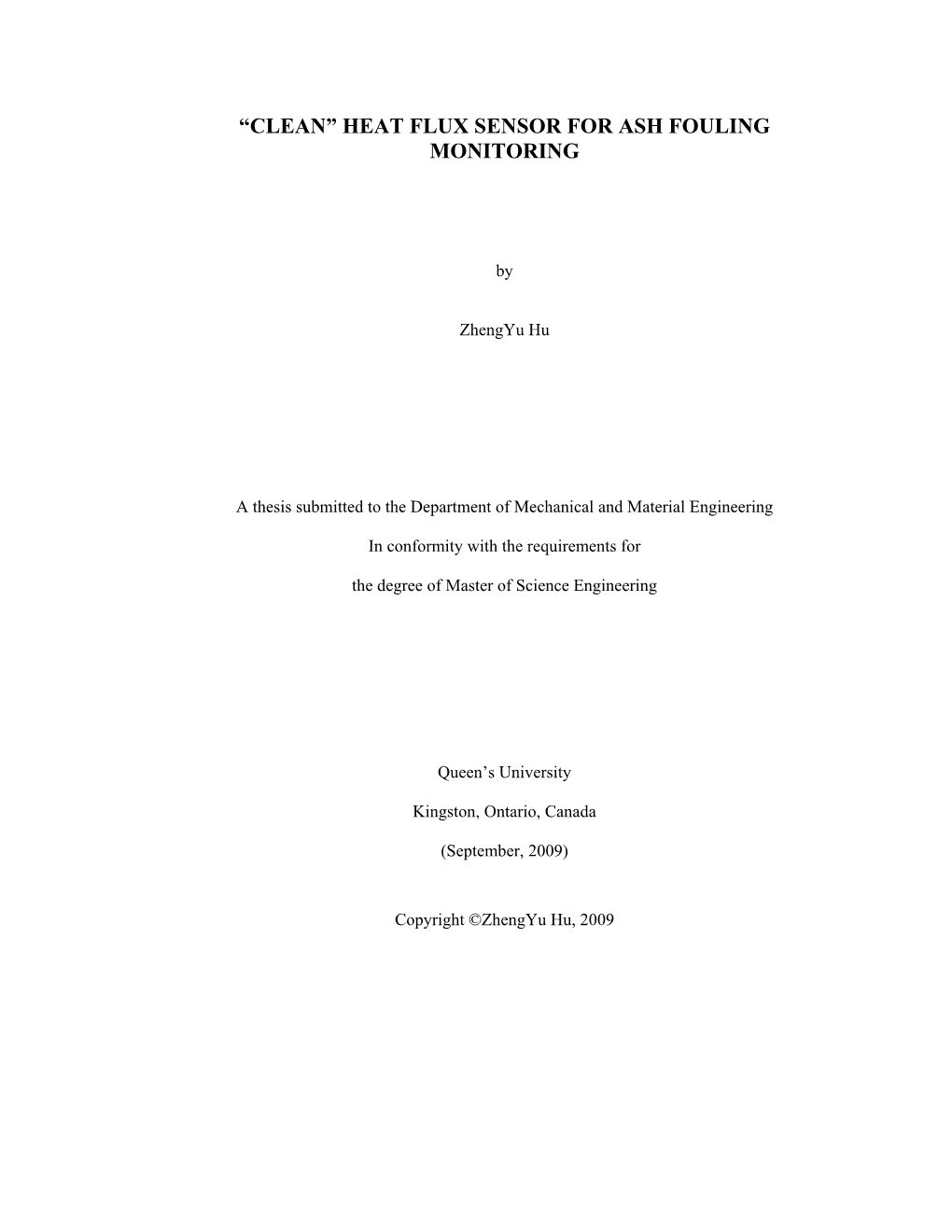
Load more
Recommended publications
-
Heat Flux." Copyright 2000 CRC Press LLC
Thomas E. Diller. "Heat Flux." Copyright 2000 CRC Press LLC. <http://www.engnetbase.com>. Heat Flux 34.1 Heat Transfer Fundamentals Conduction • Convection • Radiation 34.2 Heat Flux Measurement 34.3 Sensors Based on Spatial Temperature Gradient One-Dimensional Planar Sensors • Circular Foil Gages • Research Sensors • Future Developments 34.4 Sensors Based on Temperature Change with Time Semi-Infinite Surface Temperature Methods • Calorimeter Methods 34.5 Measurements Based on Surface Heating Thomas E. Diller 34.6 Calibration and Problems to Avoid Virginia Polytechnic Institute 34.7 Summary Thermal management of materials and processes is becoming a sophisticated science in modern society. It has become accepted that living spaces should be heated and cooled for maximum comfort of the occupants. Many industrial manufacturing processes require tight temperature control of material throughout processing to establish the desired properties and quality control. Examples include control of thermal stresses in ceramics and thin films, plasma deposition, annealing of glass and metals, heat treatment of many materials, fiber spinning of plastics, film drying, growth of electronic films and crystals, and laser surface processing. Temperature control of materials requires that energy be transferred to or from solids and fluids in a known and controlled manner. Consequently, the proper design of equipment such as dryers, heat exchangers, boilers, condensers, and heat pipes becomes crucial. The constant drive toward higher power densities in electronic, propulsion, and electric generation equipment continually pushes the limits of the associated cooling systems. Although the measurement of temperature is common and well accepted, the measurement of heat flux is often given little consideration. -
Model HFP01 Soil Heat Flux Plate 12/07
Model HFP01 Soil Heat Flux Plate 12/07 Copyright © 2002-2007 Campbell Scientific, Inc. Warranty and Assistance The MODEL HFP01 SOIL HEAT FLUX PLATE is warranted by CAMPBELL SCIENTIFIC, INC. to be free from defects in materials and workmanship under normal use and service for twelve (12) months from date of shipment unless specified otherwise. Batteries have no warranty. CAMPBELL SCIENTIFIC, INC.'s obligation under this warranty is limited to repairing or replacing (at CAMPBELL SCIENTIFIC, INC.'s option) defective products. The customer shall assume all costs of removing, reinstalling, and shipping defective products to CAMPBELL SCIENTIFIC, INC. CAMPBELL SCIENTIFIC, INC. will return such products by surface carrier prepaid. This warranty shall not apply to any CAMPBELL SCIENTIFIC, INC. products which have been subjected to modification, misuse, neglect, accidents of nature, or shipping damage. This warranty is in lieu of all other warranties, expressed or implied, including warranties of merchantability or fitness for a particular purpose. CAMPBELL SCIENTIFIC, INC. is not liable for special, indirect, incidental, or consequential damages. Products may not be returned without prior authorization. The following contact information is for US and International customers residing in countries served by Campbell Scientific, Inc. directly. Affiliate companies handle repairs for customers within their territories. Please visit www.campbellsci.com to determine which Campbell Scientific company serves your country. To obtain a Returned Materials Authorization (RMA), contact CAMPBELL SCIENTIFIC, INC., phone (435) 753-2342. After an applications engineer determines the nature of the problem, an RMA number will be issued. Please write this number clearly on the outside of the shipping container. -
FHF02SC Heat Flux Sensor User Manual
Hukseflux Thermal Sensors USER MANUAL FHF02SC Self-calibrating foil heat flux sensor with thermal spreaders and heater Copyright by Hukseflux | manual v1803 | www.hukseflux.com | [email protected] Warning statements Putting more than 24 Volt across the heater wiring can lead to permanent damage to the sensor. Do not use “open circuit detection” when measuring the sensor output. FHF02SC manual v1803 2/41 Contents Warning statements 2 Contents 3 List of symbols 4 Introduction 5 1 Ordering and checking at delivery 8 1.1 Ordering FHF02SC 8 1.2 Included items 8 1.3 Quick instrument check 9 2 Instrument principle and theory 10 2.1 Theory of operation 10 2.2 The self-test 12 2.3 Calibration 12 2.4 Application example: in situ stability check 14 2.5 Application example: non-invasive core temperature measurement 16 3 Specifications of FHF02SC 17 3.1 Specifications of FHF02SC 17 3.2 Dimensions of FHF02SC 20 4 Standards and recommended practices for use 21 4.1 Heat flux measurement in industry 21 5 Installation of FHF02SC 23 5.1 Site selection and installation 23 5.2 Electrical connection 25 5.3 Requirements for data acquisition / amplification 30 6 Maintenance and trouble shooting 31 6.1 Recommended maintenance and quality assurance 31 6.2 Trouble shooting 32 6.3 Calibration and checks in the field 33 7 Appendices 35 7.1 Appendix on wire extension 35 7.2 Appendix on standards for calibration 36 7.3 Appendix on calibration hierarchy 36 7.4 Appendix on correction for temperature dependence 37 7.5 Appendix on measurement range for different temperatures -
Heat Flux Measurement Practical Applications for Electronics
Heat Flux Measurement Practical Applications for Electronics Heat flux sensors are practical measurement tools which are component may be known, as well as the resistance of the useful for determining the amount of thermal energy passed board and solder connections; the resistance at the interface through a specific area per unit of time. Heat flux can be of the component and board to the ambient are not easily thought of as the density of transferred power, similar to known and are dependent on the flow characteristics. While current through a wire or water through a pipe. Measuring analytical or CFD methods can at best predict the heat heat flux can be useful, for example, in determining the transfer coefficient at a particular area, often for complex amount of heat passed through a wall or through a human systems with uneven or sparsely populated components body, or the amount of transferred solar or laser radiant these methods are not accurate and may not be useful. For energy to a given area. In a past article [1] we learned how those components which generate power, but may not need heat flux sensors operate and how they can be calibrated. But the use of a separate heatsink, the heat flux gage can be how can heat flux sensors be used for electronics design? experimentally used to determine the heat transfer coefficient This article highlights several practical uses of the heat flux on the component surface or the compact thermal response sensor in the design of electronics systems. See Figure 1 for on the board (e.g. -
Industrial Heat Flux Sensor Usually Goes Together with a Heat Flux
Hukseflux Thermal Sensors Hukseflux heat flux sensors for industrial use Sensors to improve process control and emergency response Hukseflux is specialised in measurement of heat transfer and thermal quantities. We have designed and supplied sensors for many industrial projects. Our experience includes a variety of environments such as coal fired boilers, fluidised beds, solar concentrators, offshore flare systems and blast furnaces. Relative to conventional monitoring based on temperature, use of heat flux sensors improves insight in processes and often leads to faster response times for process control and emergency response. Introduction Hukseflux Thermal Sensors offers a range of heat flux sensors for use in industrial environments as well as engineering & consultancy services. Our sensors for industrial use are often designed in close cooperation with customers. At Hukseflux, we like having a good technical conversation. Please contact us to discuss your specific application. Process control and emergency response Many industrial systems rely on temperature measurements. Heat flux measurements offer additional information. A change of temperature Figure 2 HF05 industrial heat flux sensor usually goes together with a heat flux. Measuring both quantities offers a better picture of what is happening. Heat flux can often be detected Example applications earlier than a temperature change. This offers • Coal fired boilers: sensors measure heat flux advantages, for example better process control and surface temperature on the furnace wall. and faster response to emergency situations. The heat flux sensors serve as boiler fouling sensors. Surface temperature is used for assessment of expected tube lifetime. • Solar concentrators: sensors measure the concentrated solar radiation on the boiler surface. -
Accuflux – Heat Flux Monitoring in the Freeze Drying Process
AccuFlux – Heat Flux Monitoring in the Freeze Drying Process Tech Note TECH NOTE AccuFlux – Heat Flux Monitoring in the Freeze Drying Process TN Thompson July 2016 AccuFlux, a heat flux sensor, is a thin-film differential thermopile. It acts as a transducer that generates an electrical signal proportional to the total heat applied to the surface of the sensor. The signal is proportional to the difference in temperature and the number of junctions in the thermopiles and is proportional to the heat flow per unit area. Heat flux sensors are simple devices that can be used to measure heat flux in discrete locations. The sensors are unique because they are very thin and provide minimal perturbations to the flow of heat. They require no special wiring, reference junctions or special signal conditioning. The accuracy of the measurement with these devices is optimized by proper installation and the ability to adequately couple the sensor to the materials surrounding it as well as to any prevailing thermal conditions such as convection currents. Bird's Eye View of Heat Flux Sensor The ease of installation makes the use of these sensors in a freeze dryer almost unlimited since the thin and flexible sensors can be attached to either flat or curved surfaces and permanently bonded in place with conventional adhesives or epoxies. The heat flux sensor is most commonly placed on the shelf surface or recessed in the shelf surface to measure the heat flow between the shelf and freeze drying container. Multiple sensors may be placed on one shelf, such as the center and edges. -
On Dew and Micrometeorology in an Arid Coastal Ecosystem
On dew and micrometeorology in an arid coastal ecosystem Bert G. Heusinkveld Promotor: Prof. dr. A.A.M. Holtslag Hoogleraar in de meteorologie Leerstoelgroep Meteorologie en Luchtkwaliteit, Wageningen Universiteit Co-promotor: Dr. ir. A.F.G. Jacobs Universitair hoofddocent Leerstoelgroep Meteorologie en Luchtkwaliteit Wageningen Universiteit Samenstelling promotiecommissie: Prof. dr. A. Kaplan Hebrew University, Jerusalem, Israel Prof. dr. T. Foken University of Bayreuth, Germany Prof. dr. ir. B.J.J.M. v.d. Hurk Universiteit Utrecht, KNMI, De Bilt Prof. dr. ir. S.E.A.T.M. van der Zee Wageningen Universiteit Dit onderzoek is uitgevoerd binnen de onderzoeksschool Productie Ecologie. On dew and micrometeorology in an arid coastal ecosystem Bert G. Heusinkveld Proefschrift ter verkrijging van de graad van doctor op gezag van de rector magnificus van Wageningen Universiteit, Prof. dr. M.J. Kropff, in het openbaar te verdedigen op woensdag 4 juni 2008 des namiddags te vier uur in de Aula CIP-data Koninklijke Bibliotheek, Den Haag On dew and micrometeorology in an arid coastal ecosystem Heusinkveld, B.G., 2008 PhD thesis, Wageningen University, The Netherlands With references – with summaries in English and Dutch ISBN 978-90-8504-932-6 Voorwoord Dankbaar en blij dat het proefschrift klaar is wil ik beginnen met een voorwoord om al die mensen nog eens naar voren te halen die op een of andere manier hebben bijgedragen tot deze mijlpaal. Promotor Bert Holtslag wil ik danken voor de inhoudelijke discussies en de stimulering die daarvan uitging. Mijn co-promotor Adrie Jacobs wil ik bedanken voor zijn toegewijde begeleiding en zijn altijd bijzonder positieve instelling. -
Quantification of Fourth Generation Kapton Heat Flux Gauge Calibration Performance
Quantification of Fourth Generation Kapton Heat Flux Gauge Calibration Performance A THESIS Presented in Partial Fulfillment of the Requirements for the Degree Master of Science in the Graduate School of The Ohio State University By Matthew Paul Hodak B.S. Graduate Program in Mechanical Engineering The Ohio State University 2010 Master’s Examination Committee: Dr. Charles W. Haldeman, Advisor Dr. Michael G. Dunn Copyright by Matthew Paul Hodak 2010 ABSTRACT Double sided Kapton heat flux gauges which are used routinely by the Ohio State University Gas Turbine Laboratory are driven by two main calibrations, the sensors temperature as a function of resistance and the material properties of Kapton. The material properties separate into those that govern the steady-state response of the gauge and those that influence the transient response. The steady-state response, as it forms the key to data processing, will be the topic of this investigation and is based on the thermal conductivity divided by the thickness (k/d). Calibration accuracies for the heat flux gauge sensors reached levels on the order of +-.05 °C and were well within the target accuracy of +- 0.1 °C over a 100 °C calibration range. Time degradation of the gauges did occur and for these cases and a single point calibration method is introduced that maintains the accuracy to ±0.4 °C instead of the ± 3 °C that would have resulted from the resistance shift due to erosion. This method will allow for longer use of the gauges in the turbines. Various calibration methods for k/d were investigated and performed. -
Airbase 2603... [4541Kb]
~ · · ' CI/SfB ' ' I (M2l Research 81 I I R46 1985 UDC Report 699.86:728.3(931 I A SURVEY OF HOUSE INSULATION N.P. lsaacs and H.A. Trethowen /41Vl7 BUILDING RESE/"RCH ASSOCIATIQi\j OF NEW ZEALAND !!• I :f3 I, C_.! Preface This project was carried out by BRANZ as part of its function to evaluate the performance of buildings with respect to building codes. lt was conceived as an exercise to determine how well the building industry as a whole had coped with what was a completely new, though not technically difficult, code requirement. lt also represents one application of the Association's plan to reinforce its laboratory work by surveys of real, functioning buildings. This report is aimed at research workers, code writers, building inspectors, also manufacturers and installers of insulation materials. l . BUILDING RESEARCH ASSOCIATION OF NEW ZEALAND INC. HEAD OFFICE AND LIBRARY, MOONSHINE ROAD, JUDGE FORD. The Building Research Association of New Zealand is an industry-backed, independent research and testing organisation set up to acquire, apply and distribute knowledge about building which will benefit the industry and through it the community at large. Postal Address: BRANZ, Private Bag, Porirua ~~]#51 ;£1) ISSN 0110- 9960 CONTENTS Page INTRODUCTION METHOD OF MEASUREMENT Review of Possible Methods Description of Methods Used Calculation Method Description of Equipment RELIABILITY OF MEASUREMENTS 4 Equipment Calibration 4 Overall System Validation 5 Miscellaneous Errors 5 Operator Training 6 SELECTION OF HOUSING SAMPLE 6 Survey Procedure -
Figure 1 HFP01 Heat Flux Plate Dimensions: (1) Sensor Area
HFP01 HEAT FLUX PLATE / HEAT FLUX SENSOR HFP01 is the world’s most popular sensor for heat flux measurement in the soil as well as through walls and building envelopes. By using a ceramics-plastic composite body the total thermal resistance is kept small. HFP01 serves to measure the heat that flows through the object in which it is incorporated or on which it is mounted. The actual sensor in HFP01 is a thermopile. This thermopile measures the differential temperature across the ceramics- plastic composite body of HFP01. Working completely passive, HFP01 generates a small output voltage proportional to the local heat flux. Using HFP01 is easy. For readout one only needs an accurate voltmeter that works in the millivolt range. To calculate the heat flux, the voltage must be divided by the sensitivity; a constant that is supplied with each individual instrument. HFP01 can be used for in-situ measurement of building envelope thermal resistance (R-value) and thermal transmittance (H-value) according to ISO 9869, ASTM C1046 and ASTM 1155 standards. Traceability of calibration is to the “guarded hot plate” of National Physical Laboratory (NPL) of the UK, according to ISO 8302 and ASTM C177. A typical measurement location is equipped with 2 sensors for good spatial averaging. If necessary two sensors can be put in series, creating a single output signal. If measuring in soil, in case a more accurate measurement is needed the model HFP01SC should be considered. See also models HFP03 and the PU series. HFP01 SPECIFICATIONS Sensitivity (nominal): 50 µV/ W.m-2 Temperature range: -30 to +70 oC Sensor thermal resistance: < 6.25 10 -3 Km2/W Range : +2000 to -2000 W.m-2 Calibration traceability: NPL, ISO 8302 / ASTM C177 Expected typical accuracy: within +5/- 15% Figure 1 HFP01 heat flux plate dimensions: (12hr totals) in most common (1) sensor area, (2) guard of ceramics-plastic soils, composite, (3) cable, standard length is 5 m. -
HFS01 High Heat Flux Sensor User Manual
Hukseflux Thermal Sensors USER MANUAL HFS01 High heat flux sensor for concentrated solar radiation and flames, water cooled Copyright by Hukseflux | manual v1906 | www.hukseflux.com | [email protected] Warning statements Putting more than 12 Volt across the sensor wiring can lead to permanent damage to the sensor. Do not use “open circuit detection” when measuring the sensor output. Using sensors without water cooling may lead to permanent damage to the sensor. Do not apply a point load on the sensor Twisting the metal sheathed cable might damage it Hukseflux performs traceable calibrations and is certified according to ISO 9001, but is not an ISO 17025 accredited calibration laboratory. HFS01 manual v1906 2/33 Contents Warning statements 2 Contents 3 List of symbols 4 Introduction 5 1 Ordering and checking at delivery 8 1.1 Ordering HFS01 8 1.2 Included items 8 1.3 Quick instrument check 9 2 Instrument principle and theory 10 2.1 Instrument principle and theory 10 2.2 Detailed measurement equation 11 3 Specifications of HFS01 13 3.1 Specifications 13 3.2 Dimensions of HFS01 16 4 Recommended practices for use 17 5 Installation of HFS01 18 5.1 Installation 18 5.2 Electrical connection 20 5.3 Requirements for data acquisition / amplification 20 5.4 Cooling 21 6 Maintenance and trouble shooting 22 6.1 Recommended maintenance and quality assurance 22 6.2 Trouble shooting 23 6.3 Recoating / repainting of sensor surfaces 23 6.4 Calibration and checks in the field 24 7 Appendices 26 7.1 Appendix on uncertainty evaluation 26 7.2 Appendix on -
Measurement Techniques for Low Heat Flux Exposures to Fire Fighters Protective Clothing
NISTIR 6750 Measurement Techniques for Low Heat Flux Exposures to Fire Fighters Protective Clothing Robert L. Vettori William H. Twilley David W. Stroup NISTIR 6750 Measurement Techniques for Low Heat Flux Exposures to Fire Fighters Protective Clothing Robert L. Vettori William H. Twilley David W. Stroup Building and Fire Research Laboratory National Institute of Standards and Technology Gaithersburg, MD 20899-8641 June 2001 U.S. Department of Commerce Donald L. Evans, Secretary National Institute of Standards and Technology Karen H. Brown, Acting Director Table of Contents List of Figures................................................................................................................................ iv List of Tables ................................................................................................................................. ix Abstract........................................................................................................................................... 1 1.0 Introduction............................................................................................................................. 2 2.0 Sensor Selection...................................................................................................................... 4 3.0 Experimental Set Up............................................................................................................... 5 4.0 Experimental Procedure and Data Acquisition......................................................................