Carpet Making in India
Total Page:16
File Type:pdf, Size:1020Kb
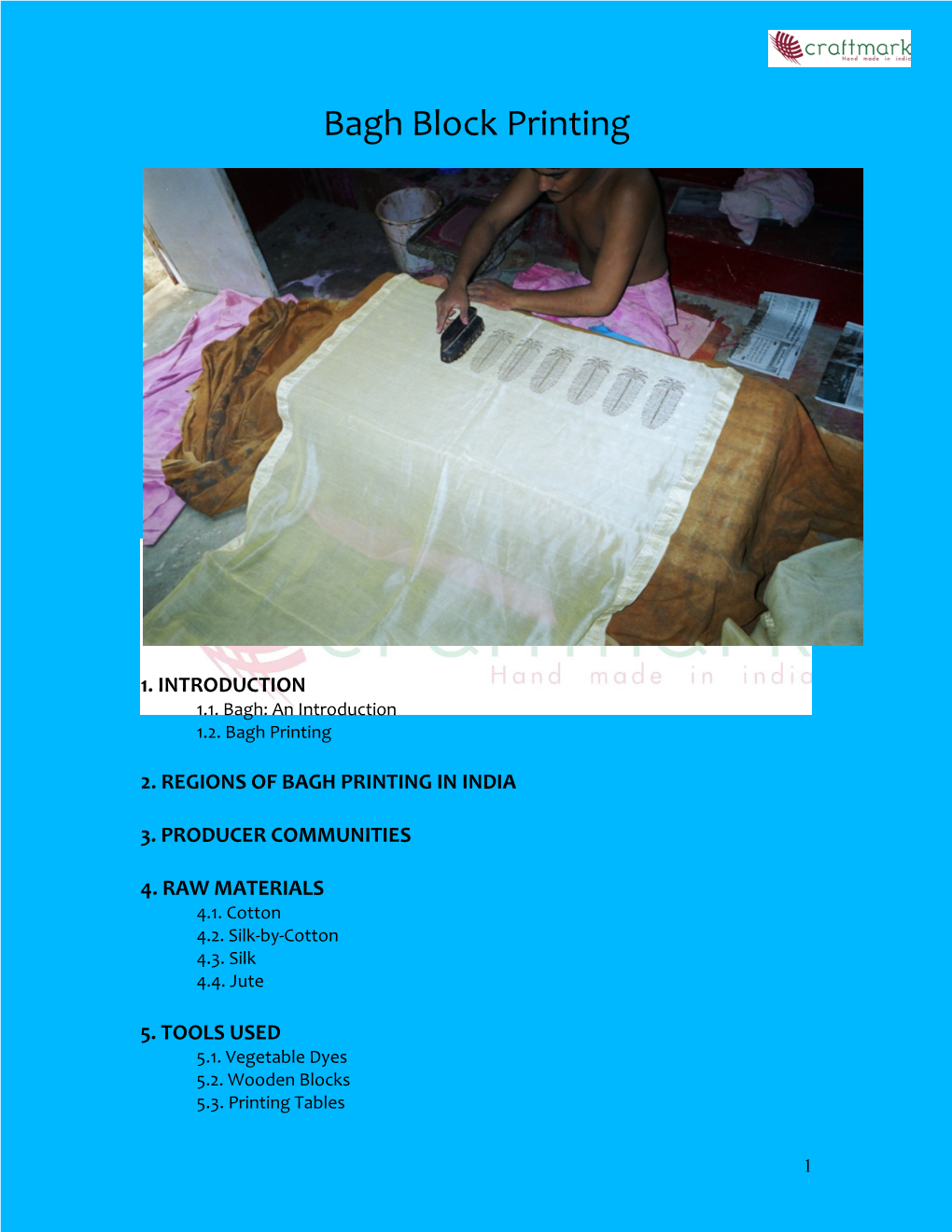
Load more
Recommended publications
-
GI Journal No. 75 1 November 26, 2015
GI Journal No. 75 1 November 26, 2015 GOVERNMENT OF INDIA GEOGRAPHICAL INDICATIONS JOURNAL NO.75 NOVEMBER 26, 2015 / AGRAHAYANA 05, SAKA 1936 GI Journal No. 75 2 November 26, 2015 INDEX S. No. Particulars Page No. 1 Official Notices 4 2 New G.I Application Details 5 3 Public Notice 6 4 GI Applications Bagh Prints of Madhya Pradesh (Logo )- GI Application No.505 7 Sankheda Furniture (Logo) - GI Application No.507 19 Kutch Embroidery (Logo) - GI Application No.509 26 Karnataka Bronzeware (Logo) - GI Application No.510 35 Ganjifa Cards of Mysore (Logo) - GI Application No.511 43 Navalgund Durries (Logo) - GI Application No.512 49 Thanjavur Art Plate (Logo) - GI Application No.513 57 Swamimalai Bronze Icons (Logo) - GI Application No.514 66 Temple Jewellery of Nagercoil (Logo) - GI Application No.515 75 5 GI Authorised User Applications Patan Patola – GI Application No. 232 80 6 General Information 81 7 Registration Process 83 GI Journal No. 75 3 November 26, 2015 OFFICIAL NOTICES Sub: Notice is given under Rule 41(1) of Geographical Indications of Goods (Registration & Protection) Rules, 2002. 1. As per the requirement of Rule 41(1) it is informed that the issue of Journal 75 of the Geographical Indications Journal dated 26th November 2015 / Agrahayana 05th, Saka 1936 has been made available to the public from 26th November 2015. GI Journal No. 75 4 November 26, 2015 NEW G.I APPLICATION DETAILS App.No. Geographical Indications Class Goods 530 Tulaipanji Rice 31 Agricultural 531 Gobindobhog Rice 31 Agricultural 532 Mysore Silk 24, 25 and 26 Handicraft 533 Banglar Rasogolla 30 Food Stuffs 534 Lamphun Brocade Thai Silk 24 Textiles GI Journal No. -
Bhopal, the Govern- Frame
) =0 ) 1 , , , RNI Regn. No. MPENG/2004/13703, Regd. No. L-2/BPLON/41/2006-2008 $%$) *+,- *+*+, /-012 ' -(. 1 A 0';.+&'BA+. 2*/0!&+')'/*!$0*B C/ /&?+!10'+!' )'*!*?-&.( 2.1/*22/&'(/+ +/&?!+/!1+ ?/&)!$/+ .*!'$+''&0.-/)! )/ /$'!+/&!/&!1 (!&A.+1/-!0/& )'+/)& B)'+/2/)!;/B(/)/ >* ? &( 67$$ :3 >/ ' / . # +. /0/*1 */ *(20 '" (( QR However, the needy person, he asked. that because of the shortage of Government’s decision to allow Dr Rajendra Prasad, Spine vaccines and the large popula- vaccination to only 45 years of and Neurosurgeon at tion that needs to be vaccinat- age and above has not gone Indraprastha Apollo Hospital ed there will be delay. But I down well with the health in Sarita Vihar in Delhi, echoed strongly feel that the experts who said that co-mor- similar views saying, “I am dis- Government should spend on bidity, and not age should be appointed that at this point the production of vaccines rather the criteria for vaccination. Government has not opened than spending huge amounts Trying to bring home their up vaccination for all those on elections where there is point, the doctors pointed out above 18 years of age, especially total disregard for social dis- that a large number of the in the wake of the rapid second tancing and I am sure we will below-45 population suffer wave. see a bad effect of this shortly,” from various comorbidity con- “However, I do understand said Dr Prasad. ditions and are more vulnera- ble to the infections than those who are at or above 45. Dr Rahul Bhargava, Director, Department of Clinical Hematology and Bone Marrow Transplant, Fortis Hospital in Gurugram, said ! " # $ &'()'*! economy and is involved in for- that “I believe after covering 60 #% & mal occupation in offices plus people, the Government o speed up the vaccination (Government and private) or should have made comorbidi- ! Tdrive across the country, manufacturing and services. -
To Circulate 1.Xlsx
Selected Artisans for Participation in Surajkund 2020 Nominations received from Regional Offices S.No. Name of Artisan Address Craft I.Card Award Region 1 Shri Mohammad Alimohammad Bhuj Motapur Road, Sanjog Nagar, Kutch Tie & Dye(Bandhani) WRBHC41561 Shilp Guru WR Khatri 2 Shri Mohd. Yusuf Khatri Bagh, Distt. Dhar-454221 Hand Block Printing WRINC214627 Shilp Guru WR 3 Shri Jitendrakumar M. Petigara Surat Wood Carving (Marquetary Inlay WRAHM201802 NA WR Mob.No. 7016778982 4 Shri Deepak Vishwakarma Mortikaron Ka Mohalla, Ganede Wall Stone Carving WRGWC-214823 NA WR Sarak, Lashkar, Gwalior, MP 5 Shri Tijuram Vishwakarma S/o Vill. Kidaichepra, Post-Palari, Distt. Wrought Iron WRJDC01150 NA WR Nanjal Vishwakarma Kondagaon, C.G. Mob.No.9424291825 6 Geetaben Vikram Balasara Ramkrisnu Colony, Dhaneti, Kutch- Embroidered & Crochet WRBHC00674 NA WR 370001 7 Aminaben Ismail Khatri Khatri Chowk, Vora Street, Bhuj, Tie & Dye Craft WRBHC00654 NA WR Kutch. 8 Shri Chitara Kiranbhai Bhulabhai 3- Opp. Jeevan Darshan Society, Kalamkari Mata Ni Pachhedi WRAHM06913 NA WR Mob.No.9427277227 Ravalnagar Na, Zupda, Vasna, Ahmedabad. 9 Smt. Pushpa Harits 101, Shivganj, Yadav Mandi, Neemuch- Bead Jewellery WRINC213229 NA WR 458441 10 Shri Sharif Khan 141, Netaji Subhash Marg, 2nd floor, Flat Leather Toys WRINC02289 NA WR No.4, Indore, MP 11 Shri Udyaram Jhara, S/o Jhadu Vill. Ektal, Post-Netnagar, Raigarh(C.G.) Bell Metal WRJDC00823 NA WR Ram Jhara, Mob.No.8085927566 12 Shri Bhanubhai Chunilal Chitara 1646, Abdulvahab Na Tekro, Khanpu Handprinted Textiles(Kalamkari WRAHM236716 NA WR Mob.No.9898110165 Ahmedabad. Painting 13 Smt Dhanmati Jhorka, W/o Vill. Ektal, Post-Netnagar,Raighar, Bell Metal WRJDC00834 NA WR Dhaniram Jhorka C.G. -
Swati Vyas* Original Research Paper Textile Design Dr. K. D. Joshi Dr
Original Research Paper Volume - 10 | Issue - 6 | June - 2020 | PRINT ISSN No. 2249 - 555X | DOI : 10.36106/ijar Textile Design REVIEW PAPER: PRINTING TECHNIQUES OF MADHYA PRADESH Assistant Professor, Textile Design Department, National Institute of Fashion Swati Vyas* Technology, Bhopal, Madhya Pradesh, India *Corresponding Author Dr. K. D. Joshi Faculty of Design, Professor. (Guide), Banasthali Vidyapeeth, Jaipur, Rajasthan, India Dr. Isha Bhatt Faculty of Design, Professor. (Guide), Banasthali Vidyapeeth, Jaipur, Rajasthan, India ABSTRACT This review was performed involving studies and documentation on the topic of Block Printing of Madhya Pradesh. The study is based on secondary data which was taken from books, journals, e-journals, e-resources, articles and Ph.D. thesis work available. Some keywords were identied to select the documentation. The next was to screen the abstract of the selected papers and exclude the rest which did not meet the selection criteria. Additionally, 9 full-text articles, 10 research papers, 3 Ph. D. and 10 books were assessed for eligibility. The SLR approach was adopted to select the related text from all available literature. Few criteria's were identied for the same and implemented using keywords. After reading and reviewing these research Papers, analysis of data was done to achieve conclusion. The objective of the literature review of block printing techniques of Madhya Pradesh, is to identify printing techniques and clusters which are more renowned and well documented, and further to identify the gap of research. There is no review paper available on this area which makes it necessary to analyse the documentation status of block printing clusters in Madhya Pradesh. -
New Trends in Bagh Prints:A Prospective Study
P: ISSN No. 0976-8602 RNI No.UPENG/2012/426228 VOL.-IV, ISSUE-I, January-2015 E: ISSN No. 2349-9443 Asian Resonance New Trends in Bagh Prints:A Prospective Study Abstract Block printing is an ancient art that has been practiced in India for thousands of years. The earliest documented evidence of this craft is from the times of Alexander the Great in 327 B.C, when he mentions ‗beautiful printed cottons‘ in India. Bagh printing in its current form started in 1962 when a group of Muslim Khatri weavers migrated from the near by Manavar to Bagh. They were originally from Sindh, and had since migrated to Marwad in Rajasthan and then to Manavar, with them they brought the block printing technique, which is now the unique Bagh printing style. In Bagh printing, only vegetable dyes are used, the main colours being black and red. For black colour, a mixture of harada and iron ore is used. For red, a mixture of alum and dhavada flower is used. These dyes are extracted and prepared locally. Wooden blocks are used for making block prints. For raw material cotton, silk and combination clothes are used, due to good absorption power. The whole method goes through a long process of dyeing and printing by different traditional designs. Once the printing is finished the cloth is left to dry in sun. To cover the whole process, survey and interview methods are used, by these methods data‘s are collected randomly. For results, Chi square test is applied and the significant level is checked. -
Andhra Pradesh 1 Sh
List of Craftspersons of Handicrafts for the SurajkundList Crafts of Craftspersons Mela 2001 of Handloom for the Year 2017 Name of Craftperson Father's/Husband Name Discipline Award Work Hut Status Assistant Name Address Confirm/ No. List Number Waiting Rec. Agency Andhra Pradesh 1 Sh. Boga Sh. Lt. Siddaiah Saree dress Assistant Name 12-126, Mallamma Material Venkatagiri Town,Nellore Distt Nellore, Andhra Pradesh 2 Sh. Gowrabathni Sh. Benkata Subbaiah Saree Dress Assistant Name 1-55, Bangarupeta, Venkatagiri Material Nellore(Distt.), Nellore Andhra pradesh 3 Sh. Gunti Venkata Sh. Venkata Narayana Saree Assistant Name 5-188, Weavers Colony Mangalagiri, Guntur(Distt.) Guntur, Andhra Pradesh 4 Sh. Kuna Sh. Venkatasubbaiah Saree dress Assistant Name 1st Ward Bangarupeta Material Nellore Distt Nellore, Andhra Pradesh Monday, January 23, 2017 Page 1 of 29 Name of Craftperson Father's/Husband Name Discipline Award Work Hut Status Assistant Name Address Confirm/ No. List Number Waiting Rec. Agency 5 Sh. Patnam Cheerala Sh. Munaswamy reddy Saree dress Assistant Name 2-91, Kattela Street Material Venkatagiri, Nellore Distt Nellore, Andhra Pradesh 6 Sh. Patnam Muneendra Sh. Krishnaiah Saree Dress Assistant Name 22-108, Kattela Street Material Venkatagiri, Nellore(Distt.), Nellore, Andhra pradesh 7 Sh. Patnam Muni Raja Sh. Muni Ratnam Saree dress Assistant Name 21-93, Kattela Street Material Venkatagiri, Nellore Distt Nellore, Andhra Pradesh Total of Andhra Pradesh 7 Monday, January 23, 2017 Page 2 of 29 Name of Craftperson Father's/Husband Name Discipline Award Work Hut Status Assistant Name Address Confirm/ No. List Number Waiting Rec. Agency Bihar 8 Saree, Stoll Assistant Name MD Monawwarali Badaralampur, Near Pansalla Bhagalpur, Bihar 9 Sh. -
34 a Nnu a L Repo
2019-2020 Printed by : www.censer.in, 9810213218 : www.censer.in, by Printed NATIONAL INSTITUTE REPORT ANNUAL th www.nift.ac.in OF FASHION TECHNOLOGY 34 National Institute of Fashion Technology A Statutory Institute governed by the NIFT Act 2006 Ministry of Textiles, Government of India NIFT Campus, Hauz Khas, Opposite Gulmohar Park, New Delhi - 110016 34th Annual Report 2019-20 CONTENTS 3 Organisational Setup NIFT Campus Report 6 Introduction 60 Bengaluru 8 Foundation Programme 65 Bhopal 10 Fashion Design 70 Bhubaneswar 12 Leather Design 75 Chennai 15 Textile Design 84 Gandhinagar 18 Knitwear Design 94 Hyderabad 20 Fashion & Lifestyle Accessories 99 Jodhpur 22 Fashion Communication 104 Kannur 24 Fashion Management Studies 108 Kangra 26 Fashion Technology 111 Kolkata 29 Design Space 116 Mumbai 31 PhD and Research 123 New Delhi 34 Continuing Education Programmes 129 Panchkula 35 Admissions 130 Patna 36 Student Development Activities 135 Raebareli 38 International and Domestic Linkages 139 Shillong 42 Cluster Development 142 Srinagar 45 National Resource Center 145 Accounts Report 46 Information Technology 203 NIFT Campuses Address 47 Enterprise Resource Planning 48 Campus Placement 52 Convocation 53 Faculty Orentation Training and Development 55 Projects at NIFT 57 Corporate Communications Cell 2 NATIONAL INSTITUTE OF FASHION TECHNOLOGY - ANNUAL REPORT 2019-20 ORGANISATIONAL SETUP BOARD OF GOVERNORS Members as on March 2020 S. No. Name & Designation of BOG Members 1 Mr. Ravi Capoor, IAS Secretary (Textiles), Ministry of Textiles & Chairman, BOG-NIFT 2 Ms. Saroj Pandey Hon’ble Member of Parliament, Rajya Sabha 3 Smt. Raksha Nikhil Khadse Hon’ble Member of Parliament, Lok Sabha 4 Dr. -
Bagh Print: How Khatris Are Keeping the 500- Year Craft Alive Along with MP’S Tribals ANTHROPOLOGY SNIPPET-149
VISHNUIAS.COM Bagh Print: How Khatris are keeping the 500- year craft alive along with MP’s tribals ANTHROPOLOGY SNIPPET-149 (Welcome To Vishnu IAS online ) (Research and Training Institute for the best civil services preparation in India) http://vishnuias.com/ 1 Bagh Print: How Khatris are keeping the 500- year craft alive along with MP’s tribals In the 16th century, when the King of Mewar Maharana Pratap held meetings with his officials, thick cotton jajams (sheets) with colourful floral and geometric patterns were spread on mattresses to seat people. Jajams were also used in marriages and social gatherings, spreading their popularity. They were hand printed using wooden blocks and natural colours by a community of Khatri printers. “Training local tribals, my father felt, was the best way to keep our art alive as the number of 2 Khatri families practicing Bagh print is limited to a few. It was also a good way of increasing income of these families which were solely dependent on agriculture until we started working with them in 1995,” says Mohammed Bilal Khatri, who received an excellence award from the United Nations Educational Scientific and Cultural Organisation (UNESCO) in 2016 for reviving Bagh prints, which received the Geographical Indication (GI) tag in 2008. “Some of our relatives in Rajasthan are Hindus. Our ancestors migrated from there and settled in Rajasthan and Gujarat. Our hand block printing imbibed local influences in both the states,” 33-year-old Bilal says. His great grandfather moved from Rajasthan to Madhya Pradesh in the 1930s. And his grandfather chose to settle down on the banks of the Bagh river from which the village as well as the block printing technique derive their names. -
October 2019 Current Affairs Questions
OCTOBER 2019 CURRENT AFFAIRS QUESTIONS OCTOBER - 2019 MCQs based on Current affairs MENTORS4IAS and Bangalore IAS Academy Hebbal & Vijayanagar, Bangalore 9886151564 / 9886777417 ©www.mentors4ias.com in Association with Bangalore IAS Academy 1 OCTOBER 2019 CURRENT AFFAIRS QUESTIONS 1. Which of the following statements are? 5. Earth Hour is organized by? 1. Asian Development Outlook Report is released (a) UN Environment by the Asia Pacific Economic Cooperation. (b) The World Wide Fund for Nature 2. World Urbanization Prospects report that is (c) Global Footprint Network released by the Department of Economic and (d) Global Environment Facility Social Affairs of the International Monetary Fund. 6. Which of the following statements are? (a) 1 only 1. Sri Lanka is the first country to liberalise its (b) 2 only economy in the South Asian Region. (c) Both 1 and 2 2. The Korean peninsula was divided in to South (d) Neither 1 nor 2 Korea and North Korea at the end of the First World War. 2. Which among the following statements does (a) 1 only not reflect the objectives of Non Alignment (b) 2 only Movement? (c) Both 1 and 2 (a) Enabling newly decolonized countries to (d) Neither 1 nor 2 pursue independent policies (b) Not joining any military alliance 7. Which among the following statements is (c) Focus on elimination of global economic incorrect with respect to National Crisis equalities Management Committee.? (d) None of the above (a) Prime Minister of India is it’s Chairman. (b) Secretaries of all the concerned Ministries 3. Which of the following statements are true? /Departments as well as organizations are the 1. -
Madhya Pradesh
A guide to the heart of Madhya Pradesh Pocket Pocket MADHYA PRADESH MADHYA MADHYA PRADESH TOP SIGHTS • FOOD • SHOPPING All you need to know about Madhya Pradesh • Top 10 attractions of Madhya Pradesh • Options for staying, eating and shopping • Everything you need to know while planning a trip • Packed with travel tips from experts World’s Leading Travel Expert WHY YOU CAN TRUST US... World’s Our job is to make amazing travel Leading experiences happen. We visit the places Travel we write about each and every edition. We Expert never take freebies for positive coverage, so 1ST EDITION Published January 2018 you can always rely on us to tell it like it is. Not for sale Pocket MADHYA PRADESH TOP SIGHTS • FOOD • SHOPPING This guide is researched and written by Supriya Sehgal Contents FOREWORD..........................4 Khajuraho ..............................64 PLAN YOUR TRIP..................6 Bhopal .................................... 78 Need to Know .......................... 8 Sanchi ...................................92 This is Madhya Pradesh ........12 Pachmarhi ...........................100 10 Top Experiences ................16 Ujjain .................................... 108 Madhya Pradesh in a Week .. 24 Indore ....................................116 Getting Around ......................26 Mandu .................................. 126 Eating Out .............................28 Jabalpur ............................... 136 Tribal Culture .........................30 Kanha National Park ........... 140 Shopping Guide ................... -
IJRTSM INTERNATIONAL JOURNAL of RECENT TECHNOLOGY SCIENCE & MANAGEMENT “SIGNIFICANCE the STUDY of BAGH PRINT” Sunita Patil 1, Dr
ISSN : 2455-9679 [Sunita et al, 5(8), Aug 2020] Impact Factor : 3.340 IJRTSM INTERNATIONAL JOURNAL OF RECENT TECHNOLOGY SCIENCE & MANAGEMENT “SIGNIFICANCE THE STUDY OF BAGH PRINT” Sunita Patil 1, Dr. Sadhana Chouhan 2 1 PHD Scholar 2 HOD (Drawing &Painting) ABSTRACT Bagh printing in its current form started in traditionally and old method when a group of Muslim Khatri weavers migrated from the nearby Manavar to Bagh. They were originally from Sindh [now in Pakistan], and had since migrated to Marwad in Rajasthan and then to Manavar. With them they brought the block printing technique, which is now the unique Bagh printing style Keyword: Bagh print, Natural colour. I. INTRODUCTION Natural dyes are known for their use in colouring of food substrate, leather, wood as well as natural fibers like wool, silk, cotton and flax as major areas of application since ancient times. Natural dyes may have a wide range of shades, and can be obtained from various parts of plants including roots, bark, leaves, flowers, and fruit [1]. Since the advent of widely available and cheaper synthetic dyes in 1856 having moderate to excellent colour fastness properties, the use of natural dyes having poor to moderate wash and light fastness has declined to a great extent. However, recently there has been revival of the growing interest on the application of natural dyes on natural fibers due to worldwide environmental consciousness [2]. Although this ancient art of dyeing with natural dyeing with natural dyes withstood the ravages of time, a rapid decline in natural dyeing continued due to the wide available of synthetic dyes at an economical price. -
PRESS STATEMENT 15 October 2018 the Awardees Of
PRESS STATEMENT 15 October 2018 The Awardees of WCC Asia Pacific Region Award of Excellence for Handicrafts 2018 For Five Sub-Regions: West Asia, Central Asia, South Asia, South East Asia and East Asia (South Pacific did not participate) The WCC Award of Excellence for Handicrafts for the year 2018 has been granted to 215 submissions from a total of 510 entries in the Asia Pacific Region from 5 (five) sub- regions. The WCC Award of Excellence for Handicrafts aims to encourage artisans to produce handicrafts that use traditional skills, patterns and themes in an innovative way, to ensure the continuity and sustainability of these traditions and skills so as to set quality standards, raise international awareness and strengthen the promotional potential for handicraft products to enable them to compete in the global market and automatically increase the welfare of the craftsmen. The range of submissions was highly diversified including woven and embroidered textiles, natural fibers, ceramics, wood carvings and inlay, metal work, stone carving, glass and other materials. The total of 510 submitted products originated from the five sub-regions of WCC- Asia Pacific Region, namely : West Asia (Iran, Kuwait, Oman, Saudi Arabia), Central Asia (Kazakhstan, Kyrgyzstan, Tajikistan, Turkmenistan, Uzbekistan), South Asia (Bangladesh, India, Nepal, Pakistan, Sri Lanka), South East Asia (Indonesia, Laos, Malaysia, Philippines, Thailand), and East Asia (China). West Asia Subregion: The jurying committee of experts met in Tehran-Iran between 5-7 August, 2018. The jurying committee comprised of: Ms. Marzieh Torkamanian - Director General of Development and Promotion Bureau in the Department of Handicraft and Traditional Arts of Iranian Cultural Heritage, Handicrafts & Tourism Organization (ICHTO) from Iran, Ms.