Chapter 7: Lead-Based Paint Inspection
Total Page:16
File Type:pdf, Size:1020Kb
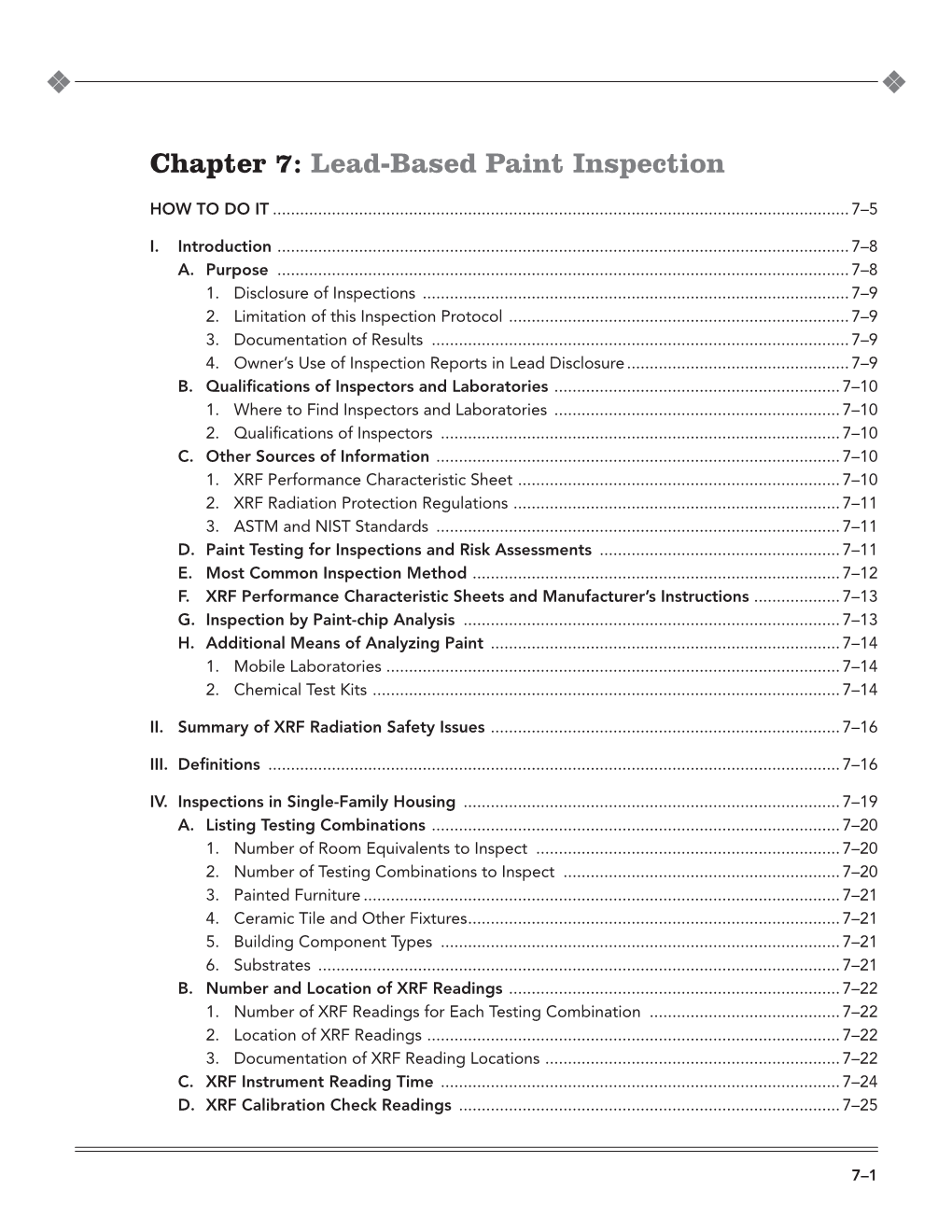
Load more
Recommended publications
-
HISTORY of LEAD POISONING in the WORLD Dr. Herbert L. Needleman Introduction the Center for Disease Control Classified the Cause
HISTORY OF LEAD POISONING IN THE WORLD Dr. Herbert L. Needleman Introduction The Center for Disease Control classified the causes of disease and death as follows: 50 % due to unhealthy life styles 25 % due to environment 25% due to innate biology and 25% due to inadequate health care. Lead poisoning is an environmental disease, but it is also a disease of life style. Lead is one of the best-studied toxic substances, and as a result we know more about the adverse health effects of lead than virtually any other chemical. The health problems caused by lead have been well documented over a wide range of exposures on every continent. The advancements in technology have made it possible to research lead exposure down to very low levels approaching the limits of detection. We clearly know how it gets into the body and the harm it causes once it is ingested, and most importantly, how to prevent it! Using advanced technology, we can trace the evolution of lead into our environment and discover the health damage resulting from its exposure. Early History Lead is a normal constituent of the earth’s crust, with trace amounts found naturally in soil, plants, and water. If left undisturbed, lead is practically immobile. However, once mined and transformed into man-made products, which are dispersed throughout the environment, lead becomes highly toxic. Solely as a result of man’s actions, lead has become the most widely scattered toxic metal in the world. Unfortunately for people, lead has a long environmental persistence and never looses its toxic potential, if ingested. -
Standard Operating Procedure for the Preparation of Lead-Containing Paint Films and Lead-In-Paint Diagnostic Test Materials
EPA/600/R-10/070 August 2009 www.epa.gov/ord Standard Operating Procedure for the Preparation of Lead-Containing Paint Films and Lead-in-Paint Diagnostic Test Materials Prepared by Kristen Sorrell, David Binstock, Curtis Haas, Cynthia Salmons, and William Gutknecht Environmental and Industrial Sciences Division RTI International Research Triangle Park, NC 27709 Disclaimer The information in this document has been funded wholly or in part by the U. S. Environmental Protection Agency (EPA) under EPA Contract No. EP-D-05-065 to Alion Science and Technology, Inc., and RTI Subcontract No. SUB1174861RB. It has been subjected to the Agency’s peer and administrative review. Mention of trade names or commercial products does not constitute endorsement or recommendation for use. ii Acknowledgments This document was prepared under the direction of the Work Assignment Contracting Officer’s Representative, Ms. Sharon L. Harper, National Environmental Research Laboratory, U.S. Environmental Protection Agency, Research Triangle Park, NC. Special acknowledgment is given to Dr. Hunter Daughtrey, Alion Science and Technology, Inc., for his support of this effort and careful review of this document. iii iv Table of Contents List of Figures...............................................................................................................................................vii List of Appendixes........................................................................................................................................vii 1.0 PRINCIPLE AND -
Toxicological Profile for Lead
TOXICOLOGICAL PROFILE FOR LEAD U.S. DEPARTMENT OF HEALTH AND HUMAN SERVICES Public Health Service Agency for Toxic Substances and Disease Registry August 2007 LEAD ii DISCLAIMER The use of company or product name(s) is for identification only and does not imply endorsement by the Agency for Toxic Substances and Disease Registry. LEAD iii UPDATE STATEMENT A Toxicological Profile for Lead, Draft for Public Comment was released in September 2005. This edition supersedes any previously released draft or final profile. Toxicological profiles are revised and republished as necessary. For information regarding the update status of previously released profiles, contact ATSDR at: Agency for Toxic Substances and Disease Registry Division of Toxicology and Environmental Medicine/Applied Toxicology Branch 1600 Clifton Road NE Mailstop F-32 Atlanta, Georgia 30333 LEAD iv This page is intentionally blank. v FOREWORD This toxicological profile is prepared in accordance with guidelines developed by the Agency for Toxic Substances and Disease Registry (ATSDR) and the Environmental Protection Agency (EPA). The original guidelines were published in the Federal Register on April 17, 1987. Each profile will be revised and republished as necessary. The ATSDR toxicological profile succinctly characterizes the toxicologic and adverse health effects information for the hazardous substance described therein. Each peer-reviewed profile identifies and reviews the key literature that describes a hazardous substance's toxicologic properties. Other pertinent literature is also presented, but is described in less detail than the key studies. The profile is not intended to be an exhaustive document; however, more comprehensive sources of specialty information are referenced. The focus of the profiles is on health and toxicologic information; therefore, each toxicological profile begins with a public health statement that describes, in nontechnical language, a substance's relevant toxicological properties. -
A STANDARD of QUALITY for MUSE PAINT January 1949
Ät1001:31TUP,E ROOT 5 A STANDARD Of QUALITY FOR MUSE PAINT January 1949 No. 1)1734 UNITED STATES DEPARTMENT OF AGRICULTURE FOREST SERVICE FORE ST PRODUCTS LABORATORY Madison 5, Wisconsin In Cooperation with the University of Wisconsin A STANDARD OF QUALITY FOR HOUSE PAINT By F. L. BROWNE, Chemist 1 Forest Products Laboratory, – Forest Service U. S. Department of Agriculture You can now buy house paint and barn paints labeled by the maker with both his trade brand and a classification recommended by the U. S. Depart- ment of Agriculture. The classification is a form of quality standard. It tells briefly what kind and grade of paint you are buying. The trade brand tells, as it always has, who made the paint and expects to be held respon- sible for it. Together, classification and trade brand supply all that is needed to buy from reputable sources with an eye to quality as well as to price. The USDA classification plan was suggested by the Forest Products Laboratory after more than 20 years of research in the painting of wood. Under the plan there is a classification for every kind of house or barn paint for wood buildings. Any maker or dealer in paint is free to use the classification on his labels. No law requires it, however, and no agency of government need be consulted about it. But when the classification is used, the paint must conform in fact to the classification claimed for it. Mis- branded paint is unlawful. The law in some States requires the composition, or formula, of paint to be printed on the label. -
Omaha Lead Omaha, Douglas County, Nebraska Epa Facility Id: Nesfn0703481 April 28, 2005 the Atsdr Public Health Assessment: a Note of Explanation
OMAHA LEAD OMAHA, DOUGLAS COUNTY, NEBRASKA EPA FACILITY ID: NESFN0703481 APRIL 28, 2005 THE ATSDR PUBLIC HEALTH ASSESSMENT: A NOTE OF EXPLANATION This Public Health Assessment was prepared by ATSDR pursuant to the Comprehensive Environmental Response, Compensation, and Liability Act (CERCLA or Superfund) section 104 (i)(6) (42 U.S.C. 9604 (i)(6)), and in accordance with our implementing regulations (42 C.F.R. Part 90). In preparing this document, ATSDR has collected relevant health data, environmental data, and community health concerns from the Environmental Protection Agency (EPA), state and local health and environmental agencies, the community, and potentially responsible parties, where appropriate. In addition, this document has previously been provided to EPA and the affected states in an initial release, as required by CERCLA section 104 (i)(6)(H) for their information and review. The revised document was released for a 30-day public comment period. Subsequent to the public comment period, ATSDR addressed all public comments and revised or appended the document as appropriate. The public health assessment has now been reissued. This concludes the public health assessment process for this site, unless additional information is obtained by ATSDR which, in the agency’s opinion, indicates a need to revise or append the conclusions previously issued. Agency for Toxic Substances & Disease Registry.................................................... Julie L. Gerberding, M.D., M.P.H., Administrator Thomas Sinks, Ph.D., M.S., Acting Director -
The White Lead Industry in Omaha, Nebraska
Nebraska History posts materials online for your personal use. Please remember that the contents of Nebraska History are copyrighted by the Nebraska State Historical Society (except for materials credited to other institutions). The NSHS retains its copyrights even to materials it posts on the web. For permission to re-use materials or for photo ordering information, please see: http://www.nebraskahistory.org/magazine/permission.htm Nebraska State Historical Society members receive four issues of Nebraska History and four issues of Nebraska History News annually. For membership information, see: http://nebraskahistory.org/admin/members/index.htm Article Title: The White Lead Industry in Omaha, Nebraska Full Citation: Mark D Budka, "The White Lead Industry in Omaha, Nebraska," Nebraska History 73 (1992): 91-97. URL of article: http://www.nebraskahistory.org/publish/publicat/history/full-text/NH1992White_Lead.pdf Date: 4/3/2013 Article Summary: The Omaha White Lead Company was founded in 1877 to produce paint bases and lead protective coatings to sell in the urban-industrial Northeast. Lead was the standard base in paints and other coatings used to protect structures from wear and weather. The company continued as the Carter White Lead Company and manufactured white lead products until 1936, under the trade name Dutch Boy. Cataloging Information: Names: Charles W Mead, Charles B Rustin, Levi Carter, William A Paxton, Nathaniel Shelton, J P Gardner, A W Phelps, Edward J Cornish, David K Tuttle, James A McCreary, Frank Barker, H C Haskins, -
Lead Poisoning Prevention: a Guide for Legislators
LEAD POISONING PREVENTION: A GUIDE FOR LEGISLATORS by Doug Farquhar Senior Policy Specialist State Issues and Policy Analysis Program National Conference of State Legislatures in cooperation with the U.S. Environmental Protection Agency National Conference of State Legislatures William T. Pound, Executive Director 1560 Broadway, Suite 700 Denver, Colorado 80202-5140 303/830-2200 444 North Capitol Street, N.W., Suite 515 Washington, D.C. 20001 202/624-5400 August 1994 Lead Poisoning Prevention: A Guide for Legislators i CONTENTS LIST OF TABLES AND FIGURES .............................................................................................. v ACKNOWLEDGMENTS............................................................................................................. vi EXECUTIVE SUMMARY ........................................................................................................... vii 1. NATURE AND EXTENT OF LEAD POISONING ......................................................... 1 Characteristics of the Metal .................................................................................................................... 1 Effects on Children and Pregnant Women ...................................................................................... 2 Sources and Reduction of Exposure ................................................................................................... 2 Lead-based paint ................................................................................................................................2 -
Environmental and Sustainable Technology Evaluations Report ESCA Tech, Inc. D-Lead Paint Test
EPA Contract EP-W-09-024 Work Assignment 1-06 December 2010 Environmental Technology Verification Program Environmental and Sustainable Technology Evaluations Report ESCA TECH, INC. ® D-LEAD PAINT TEST KIT QUALITATIVE SPOT TEST KIT FOR LEAD IN PAINT Prepared by Battelle for U.S. Environmental Protection Agency EPA Contract EP-W-09-024 Work Assignment 1-06 December 2010 Environmental Technology Verification Program Environmental and Sustainable Technology Evaluations Report ESCA TECH, INC. ® D-LEAD PAINT TEST KIT QUALITATIVE SPOT TEST KIT FOR LEAD IN PAINT By Stephanie Buehler, Dale Rhoda, and Bruce Buxton, Battelle Julius Enriquez and Evelyn Hartzell, U.S. EPA Battelle Columbus, Ohio 43201 Notice Funding for this verification test was provided under Contract No. EP-W-09-024, Work Assignments 4-16, 0-06, and 1-06, Office of Pollution Prevention, and Toxics, US EPA. The U.S. Environmental Protection Agency, through its Office of Research and Development, managed the research described herein. It has been subjected to the Agency’s peer and administrative review and has been approved for publication. Any opinions expressed in this report are those of the author(s) and do not necessarily reflect the views of the Agency, therefore, no official endorsement should be inferred. Any mention of trade names or commercial products does not constitute endorsement or recommendation for use. ii Foreword The U.S. Environmental Protection Agency (EPA) is charged by Congress with protecting the Nation’s land, air, and water resources. Under a mandate of national environmental laws, the Agency strives to formulate and implement actions leading to a compatible balance between human activities and the ability of natural systems to support and nurture life. -
Lead-Based Paint: Planning Your Paint Removal Project Bob Beckley and James “Scott” Groenier, Project Leaders
Facilities United States Department of Agriculture Forest Service Technology & Development Program December 2007 7300/2100 0773–2330–MTDC Lead-Based Paint: Planning Your Paint Removal Project Bob Beckley and James “Scott” Groenier, Project Leaders ead-based paint was used on steel bridges, towers, storage tanks, buildings, and other facilities through LLthe 1980s, and in some cases into the 1990s. Lead- based paint may have to be removed during facility mainte- nance (figure 1) or when historic buildings are being re- stored. Lead is a serious health hazard if it is inhaled or ingested. Scraping or sanding lead-based paint creates paint particles that are a hazardous waste and can be a health hazard if proper safety precautions are not taken. Before beginning a maintenance or restoration project, conduct a risk analysis to determine if any of the material you’ll be disturbing has lead-based paint. • Paint on older buildings, towers, and bridges—even some built as late as the early 199 0s—may contain lead or other heavy metals. • Lead and other heavy metals can cause se rious problems for human health and the environment. • Any project that disturbs lead-based pain t requires planning to ensure that Figure 1—Steel towers may be coated with lead-based paint. Special the proj ect complies with precautions for climbing won’t be needed when taking samples from a envi ronmental and safety regulations. tower’s lower steps, but samples elsewhere may need to be taken by a • Thi certified climber following all appropriate safety guidelines. The same s tech tip provides information for precautions apply to persons taking samples in precarious spots under planning proj ects that involve bridges. -
The Sherwin-Williams Company
January 21, 2015 Michael J. Solecki Jones Day [email protected] Re: The Sherwin-Williams Company Dear Mr. Solecki: This is in regard to your letter dated January 21, 2015 concerning the shareholder proposal submitted by CHE Trinity Health, Everence Financial, on behalf of the Praxis Growth Index Fund, and Friends Fiduciary Corporation for inclusion in Sherwin- Williams’ proxy materials for its upcoming annual meeting of security holders. Your letter indicates that the proponents have withdrawn the proposal and that Sherwin- Williams therefore withdraws its December 11, 2014 request for a no-action letter from the Division. Because the matter is now moot, we will have no further comment. Copies of all of the correspondence related to this matter will be made available on our website at http://www.sec.gov/divisions/corpfin/cf-noaction/14a-8.shtml. For your reference, a brief discussion of the Division’s informal procedures regarding shareholder proposals is also available at the same website address. Sincerely, Adam F. Turk Attorney-Adviser Enclosure cc: Sanford Lewis [email protected] JONES DAY NORTHPOINT • 901 LAKESIDEAVENUE • CLEVELAND,OHIO 44114.1190 TELEPHONE: + 1.216.586.3939 • FACSIMILE: + 1 .216.579.0212 January 21,2015 VIAE-MAIL shareholderoroposals@sec. gov U.S. Securities and Exchange Commission Division of Corporation Finance Office of Chief Counsel 100 F Street, N.E. Washington, DC 20549 Re: The Sherwin-Williams Company- Omission of Shareholder Proposal Securities Exchange Act of 1934 - Rule 14a-8 Dear -
Lead Paint Reformulation Technical Guidelines
LEAD PAINT REFORMULATION TECHNICAL GUIDELINES Beijing, 2019.10.17. Vojislavka Satric CONTENT 1. Technical Guidelines Content; 2. Colours and Paint Function; 3. Paint Raw Materials; 4. Lead Compounds in Paints; 5. Substitution Process; 6. Substitution of Lead Pigments; 7. Substitution of Lead Driers 1. Technical Guidelines Content • Information on hazardous properties of lead compounds; • Substitution process; • Colour theory and colour index; • Dispersion process; • Alternative pigments and additives; • Assessments of alternative pigments and additives; • General information about reformulation processes; • The Technical Guidelines are developed to help address both capacity constraints and technical barriers to the substitution of lead compounds in paints • Focus is on SMEs needs for the effective and efficient reformulation of paint. 2. COLOURS AND FUNCTIONS OF PAINT COLOURS Colour Theory This Section provides tips for tinting Colour Index • Colour Index (CI) is universally accepted standard coding system for pigments; • Colour Index identifies each colorant by giving the compound a unique Colour Index name (CI) and a Colour Index number. Abbrevi- Abbrevi- Pigment Pigment ation ation Chemical class CI numbers PB Pigment Blue PBk Pigment Black Nitrosol 100000–102999 PBr Pigment Brown PG PG Pigment Green Nitro 103000–109999 PM Pigment Metal PO Pigment Orange Monoazo 110000–199999 PV Pigment Violet PR Pigment Red Diazo 200000–299999 PW Pigment White PY Pigment Yellow Paint Functions – Protection (1) Paint – Signal/Camouflage Function (2) Paint Functions (3) • Decorative, • Insulation, • Conductivity, • Antibacterial, • Fire retardant Paint Functions (4) • Paint is also formulated to adapt to a variety of substrates and methods of application. • Since there are many different initial lead-containing formulations for colour and other paint properties, Technical Guidelines may provide only general information about reformulation processes. -
The Need to Eliminate Lead Paint Globally
FORESIGHT SCIENCE DIVISION1 Brief FORESIGHT December 2020 Brief 021 Early Warning, Emerging Issues and Futures The Need to Eliminate Lead Paint Globally Background The Foresight Briefs are published by the United Nations Environment Programme to highlight a hotspot of environmental change, feature an emerging science topic, or discuss a contemporary environmental issue. The public is provided with the opportunity to find out what is happening to their changing environment and the consequences of everyday choices, and to think about future directions for policy. The 21st edition of UNEP’s Foresight Brief highlights the harmful effects of Lead in Paint. Photo credit: Nils Z / Shutterstock.com Introduction 2020a). While it was once necessary to add lead for color serious, especially in children under six years of age and its anti-corrosive and drying properties, non-toxic (UNICEF and Pure Earth 2020). Lead poisoning can Lead has wide-ranging effects on health, with substitutes for the lead compounds have existed for reduce IQ and learning abilities, and increase behavioral concomitant personal, societal and economic impacts, decades and are available at a comparable cost (Brosché problems, including increased violence and incarceration and thus, it was identified as one of the 10 chemicals et al. 2014; International Pollutants Elimination Network in early adulthood (Aizer and Currie 2019; ATSDR 2020; of major public health concern globally (World Health [IPEN] 2018; UNEP 2019a). Poisoning from lead paint is Mielke and Zahran 2012; UNICEF and Pure Earth 2020; Organization [WHO] 2019). Lead poisoning remains completely avoidable, and we call on all governments Reyes 2007; Wright et al.