Open Jeffkim MS Thesis.Pdf
Total Page:16
File Type:pdf, Size:1020Kb
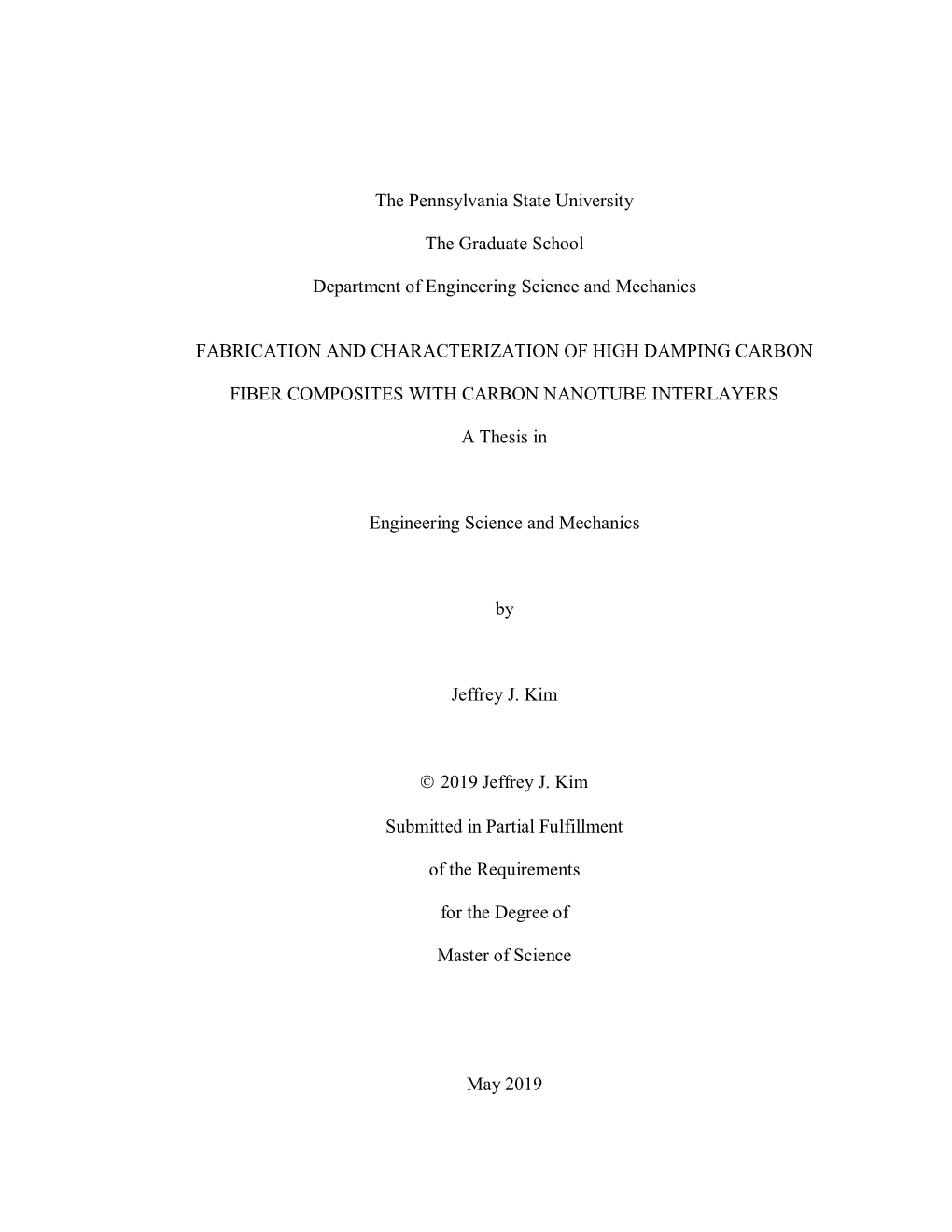
Load more
Recommended publications
-
A Study of Nanostructure and Properties of Mixed Nanotube Buckypaper Materials: Fabrication, Process Modeling Characterization, and Property Modeling Cherng-Shii Yeh
Florida State University Libraries Electronic Theses, Treatises and Dissertations The Graduate School 2007 A Study of Nanostructure and Properties of Mixed Nanotube Buckypaper Materials: Fabrication, Process Modeling Characterization, and Property Modeling Cherng-Shii Yeh Follow this and additional works at the FSU Digital Library. For more information, please contact [email protected] THE FLORIDA STATE UNIVERSITY COLLEGE OF ENGINEERING A STUDY OF NANOSTRUCTURE AND PROPERTIES OF MIXED NANOTUBE BUCKYPAPER MATERIALS: FABRICATION, PROCESS MODELING CHARACTERIZATION, AND PROPERTY MODELING By CHERNG-SHII YEH A Dissertation submitted to the Department of Industrial and Manufacturing Engineering in partial fulfillment of the requirements for the degree of Doctor of Philosophy Degree Awarded: Fall Semester, 2007 The members of the Committee approve the dissertation of Cherng-Shii Yeh defended on November 14. ______________________________ Zhiyong Liang Professor Directing Dissertation ______________________________ Jim P. Zheng Outside Committee Member __________________________________ Ben Wang Committee Member ______________________________ Chuck Zhang Committee Member ______________________________ David Jack Committee Member Approved: _____________________________________________ Chuck Zhang, Chair, Department of Industrial & Manufacturing Engineering _____________________________________________ Ching-Jen Chen, Dean, FAMU-FSU College of Engineering The Office of Graduate Studies has verified and approved the above named committee members. ii -
Nanotube Buckypaper Electrodes for PEM Fuel Cell Applications Chung-Lin Ku
Florida State University Libraries Electronic Theses, Treatises and Dissertations The Graduate School 2007 Nanotube Buckypaper Electrodes for PEM Fuel Cell Applications Chung-Lin Ku Follow this and additional works at the FSU Digital Library. For more information, please contact [email protected] THE FLORIDA STATE UNIVERSITY COLLEGE OF ENGINEERING NANOTUBE BUCKYPAPER ELECTRODES FOR PEM FUEL CELL APPLICATIONS By CHUNG-LIN KU A Thesis submitted to the Department of Industrial and Manufacturing Engineering in partial fulfillment of the requirements for the degree of Master of Science Degree Awarded: Fall Semester, 2007 The members of the committee approve the thesis of Chung-Lin Ku defended on November 06, 2007. ______________________________ Zhiyong Liang Professor Directing Thesis ______________________________ Jim P. Zheng Outside Committee Member __________________________________ Ben Wang Committee Member ______________________________ Chuck Zhang Committee Member Approved: __________________________________________________________ Chuck Zhang, Chair, Department of Industrial and Manufacturing Engineering __________________________________________________________ Ching-Jen Chen, Dean, FAMU-FSU College of Engineering The Office of Graduate Studies has verified and approved the above named committee members. ii BIOGRAPHICAL SKETCH Chung-Lin (Daphne) Ku is currently a master’s student in Industrial Engineering at FAMU-FSU College of Engineering and expecting graduation in December, 2007. She was born in October of 1982. She received her Bachelor’s of Engineering in Industrial Engineering in June 2005 from Tung-Hai University at Tai-Chuang, Taiwan. Her research interests include nanotube technologies, design of experiments, supply chain management, quality control, reliability, and applied optimization. Her favorite hobbies include badminton, music and movies. She is looking forward to pursue a career in the field of Industrial Engineering. -
Mechanical and Electrical Characterization of Hybrid Carbon Nanotube Sheet-Graphene Nanocomposites for Sensing Applications
Dissertations and Theses 5-2016 Mechanical and Electrical Characterization of Hybrid Carbon Nanotube Sheet-Graphene Nanocomposites for Sensing Applications Jiukun Li Follow this and additional works at: https://commons.erau.edu/edt Part of the Aerospace Engineering Commons, and the Structural Materials Commons Scholarly Commons Citation Li, Jiukun, "Mechanical and Electrical Characterization of Hybrid Carbon Nanotube Sheet-Graphene Nanocomposites for Sensing Applications" (2016). Dissertations and Theses. 223. https://commons.erau.edu/edt/223 This Thesis - Open Access is brought to you for free and open access by Scholarly Commons. It has been accepted for inclusion in Dissertations and Theses by an authorized administrator of Scholarly Commons. For more information, please contact [email protected]. i MECHANICAL AND ELECTRICAL CHARACTERIZATION OF HYBRID CARBON NANOTUBE SHEET - GRAPHENE NANOCOMPOSITES FOR SENSING APPLICATIONS A Thesis Submitted to the Faculty of Embry-Riddle Aeronautical University by Jiukun Li In Partial Fulfillment of the Requirements for the Degree of Master of Science in Aerospace Engineering May 2016 Embry-Riddle Aeronautical University Daytona Beach, Florida iii ACKNOWLEDGMENTS I would like to thank my family, Yongjin Li and Xiaoli Zhang and my sister Yahui Li, for their love, support and encouragement throughout so many years and specially my girlfriend, Ruojun Dai, for her support and soul company, though we are in different hemispheres with a 12-hour-difference. I would like to thank Aerospace Engineering Department of Embry-Riddle Aeronautical University and its entire staff for educating, research support, especially Dr. Virginie Rollin, Dr. Daewon Kim, Dr. David J Sypeck, Dr. Marwan Al-Haik, Mr. Michael Potash, and Mr. -
Carbon and Boron Nitride Nanotube Fabricated Supercapacitors
Old Dominion University ODU Digital Commons Electrical & Computer Engineering Theses & Dissertations Electrical & Computer Engineering Spring 2016 Carbon and Boron Nitride Nanotube Fabricated Supercapacitors Derek Christian Demuth Old Dominion University, [email protected] Follow this and additional works at: https://digitalcommons.odu.edu/ece_etds Part of the Electrical and Computer Engineering Commons Recommended Citation Demuth, Derek C.. "Carbon and Boron Nitride Nanotube Fabricated Supercapacitors" (2016). Master of Science (MS), Thesis, Electrical & Computer Engineering, Old Dominion University, DOI: 10.25777/ 59m8-r065 https://digitalcommons.odu.edu/ece_etds/6 This Thesis is brought to you for free and open access by the Electrical & Computer Engineering at ODU Digital Commons. It has been accepted for inclusion in Electrical & Computer Engineering Theses & Dissertations by an authorized administrator of ODU Digital Commons. For more information, please contact [email protected]. CARBON AND BORON NITRIDE NANOTUBE FABRICATED SUPERCAPACITORS by Derek Christian Demuth B.A. May 2007, Virginia Polytechnic and State Institute B.S. December 2014, Old Dominion University A Thesis Submitted to the Faculty of Old Dominion University in Partial Fulfillment of the Requirements for the Degree of MASTER OF SCIENCE ELECTRICAL AND COMPUTER ENGINEERING OLD DOMINION UNIVERSITY May 2016 Approved by: Gon Namkoong (Director) Helmut Baumgart (Member) Abdelmageed Elmustafa (Member) ABSTRACT CARBON AND BORON NITRIDE NANOTUBE FABRICATED SUPERCAPACITORS Derek Christian Demuth Old Dominion University, 2016 Director: Dr. Gon Namkoong The fabrication of supercapacitor devices consisting of boron nitride nanotubes (BNNTs) and carbon nanotubes (CNTs) has great theoretical capabilities of high specific capacitance, energy density, and power density. Various methods of dispersion and deposition are utilized to optimize such supercapacitors with BNNTs and CNTs, and also to produce devices with only CNTs to use as a benchmark. -
Composites Part a 113 (2018) 132–140
Composites Part A 113 (2018) 132–140 Contents lists available at ScienceDirect Composites Part A journal homepage: www.elsevier.com/locate/compositesa Research on high electromagnetic interference shielding effectiveness of a foldable buckypaper/polyacrylonitrile composite film via interface T reinforcing ⁎ Qianshan Xiaa, Zhichun Zhanga, Hetao Chua, Yanju Liub, Jinsong Lenga, a Center for Composite Materials and Structures, No. 2 YiKuang Street, Science Park of Harbin Institute of Technology (HIT), Harbin 150080, PR China b Department of Aerospace Science and Mechanics, No. 92 West DaZhi Street, Harbin Institute of Technology (HIT), Harbin 150001, PR China ARTICLE INFO ABSTRACT Keywords: Herein, a series of foldable buckypaper/polyacrylonitrile (BP/PAN) composite films were developed in a facile Buckypaper strategy. This strategy was based on electrospun and vacuum pressurized filtration methods. The composite film Polymer-matrix composites had better mechanical properties than pristine BP via interface reinforcing, but not deprived of excellent con- Electromagnetic interference shielding ductivity. The maximum tensile strength and elongation at break of BP/PAN films were 1.45 and 11.65 times than pristine BP, respectively. Moreover, BP/PAN film had higher electromagnetic interference (EMI) shielding effectiveness (63.7–65 dB) in the Ku band (12–18 GHz) than pristine BP (34.3–42.9 dB), due to interfaces forming between PAN fibers and CNTs. The BP/PAN composite as a promising EMI shielding material could be utilized in military and civil applications, such as flexible antenna, EMI shielding clothes and soft portable electronic products. 1. Introduction In recent decades, carbon materials [11–15] and their composites [16,17], owing to their low density, anti-corrosion, excellent electrical With the rapid development of information and communications and thermal properties [18], play important roles in development of technology, advanced electrical and electronic devices have played shielding materials. -
Multi-Functional Properties of MWCNT/PVA Buckypapers Fabricated by Vacuum Filtration Combined with Hot Press: Thermal, Electrical and Electromagnetic Shielding
nanomaterials Article Multi-Functional Properties of MWCNT/PVA Buckypapers Fabricated by Vacuum Filtration Combined with Hot Press: Thermal, Electrical and Electromagnetic Shielding Liyang Cao 1, Yongsheng Liu 1,2,*, Jing Wang 1,2, Yu Pan 3,*, Yunhai Zhang 1, Ning Wang 3 and Jie Chen 1 1 Science and Technology on Thermostructural Composites Materials Laboratory, Northwestern Polytechnical University, Xi’an 710072, China; [email protected] (L.C.); [email protected] (J.W.); [email protected] (Y.Z.); [email protected] (J.C.) 2 NPU-SAS Joint Research Center of Advanced Ceramics, Northwestern Polytechnical University, Xi’an 710072, China 3 Science and Technology on Scramjet Laboratory, College of Aerospace Science and Engineering, National University of Defense Technology, Changsha 410073, China; [email protected] * Correspondence: [email protected] (Y.L.); [email protected] (Y.P.); Tel.: +86-29-88495179 (Y.L.); Fax: +86-29-88494620 (Y.L.) Received: 18 November 2020; Accepted: 4 December 2020; Published: 14 December 2020 Abstract: The applications of pure multi-walled carbon nanotubes (MWCNTs) buckypapers are still limited due to their unavoidable micro/nano-sized pores structures. In this work, polyvinyl alcohol (PVA) was added to a uniform MWCNTs suspension to form MWCNT/PVA buckypapers by vacuum infiltration combined with a hot press method. The results showed an improvement in the thermal, electrical, and electromagnetic interference (EMI) shielding properties due to the formation of dense MWCNTs networks. The thermal and electrical properties rose from 1.394 W/m k to 2.473 W/m k · · and 463.5 S/m to 714.3 S/m, respectively. -
Nanotechnology in Transportation Vehicles: an Overview of Its Applications, Environmental, Health and Safety Concerns
materials Review Nanotechnology in Transportation Vehicles: An Overview of Its Applications, Environmental, Health and Safety Concerns Muhammad Shafique 1,2 and Xiaowei Luo 1,2,* 1 Department of Architecture and Civil Engineering, City University of Hong Kong, Hong Kong 2 Architecture and Civil Engineering Research Center, Shenzhen Research Institute of City University of Hong Kong, Shenzhen 518057, China * Correspondence: [email protected] Received: 4 July 2019; Accepted: 1 August 2019; Published: 6 August 2019 Abstract: Nanotechnology has received increasing attention and is being applied in the transportation vehicle field. With their unique physical and chemical characteristics, nanomaterials can significantly enhance the safety and durability of transportation vehicles. This paper reviews the state-of-the-art of nanotechnology and how this technology can be applied in improving the comfort, safety, and speed of transportation vehicles. Moreover, this paper systematically examines the recent developments and applications of nanotechnology in the transportation vehicle industry, including nano-coatings, nano filters, carbon black for tires, nanoparticles for engine performance enchantment and fuel consumption reduction. Also, it introduces the main challenges for broader applications, such as environmental, health and safety concerns. Since several nanomaterials have shown tremendous performance and have been theoretically researched, they can be potential candidates for applications in future environmental friendly transportation -
ABSTRACT KIM, HYUNGJOO. Functionalized Buckypapers For
ABSTRACT KIM, HYUNGJOO. Functionalized Buckypapers for Supercapacitor Electrodes: Effect of Intrinsic Chemical Interactions on Electrochemical Performance. (Under the direction of Dr. Philip D Bradford). Carbon nanotubes (CNTs) and their composites have been widely applied to many fields due to their unique electrical and mechanical properties. In the field of energy storage devices, they have been recognized as promising materials to develop supercapacitor electrodes with outstanding electrochemical performance such as high power density, fast charge/discharge time, low level of heating, safety and long cycle life. Ternary composites, consisting of CNT, conductive polymer (CP) and metal (oxide), have been actively studied to develop supercapacitor electrodes because improved electrochemical performance can be achieved as compared to binary composite or pristine forms. Many researches demonstrated that this improved performance was induced by synergistic effects among the three components in the composite. However, in most of reported researches, all three materials were simply mixed to induce this synergistic effect. To further improve electrochemical performance of ternary composite- based supercapacitors, three different strategies to further improve and understand these synergistic effects were utilized in this study. The first method studied was the introduction of epoxide functional groups on the buckypaper. Raman, XPS and FT-IR were used to analyze the structure of functionalized buckypaper, indicating that epoxide functional groups were well formed on the surface of buckypaper. In addition, to further investigate advantages of epoxide functionalized buckypaper (EBP) as a supercapacitor electrode, key factors affecting electrochemical performance were also studied. According to the result, EBP exhibited wider surface area, higher surface energy and enhanced electrical conductivity when compared with purified pristine buckypaper (PPBP). -
And Double-Walled Boron Nitride Nanotubes
www.nature.com/scientificreports OPEN Single- and double-walled boron nitride nanotubes: Controlled synthesis and application for water purifcation Hyunjin Cho1,6,8, Jun Hee Kim1,2,8, Jae Hun Hwang1,3, Cheol Sang Kim2,3, Se Gyu Jang1, Cheol Park4, Hunsu Lee5 ✉ & Myung Jong Kim7 ✉ Research interest in boron nitride nanotubes (BNNTs) has increased after the recent success of large- scale BNNT syntheses using high-temperature-pressure laser ablation or high-temperature plasma methods. Nonetheless, there are limits to the application and commercialization of these materials because of the difculties associated with their fne structural control. Herein, the growth kinetics of BNNTs were systemically studied for this purpose. The growth pressure of the nitrogen feed gas was varied while the growth temperature remained constant, which was confrmed by black body radiation measurements and calculations based on a heat loss model. Changing from the difusion-limited regime to the supply-limited regime of growth kinetics based on the optimized BNNT synthesis condition aforded the control of the number of BNNT walls. The total amount of BNNTs possessing single and double walls was over 70%, and the BNNT surface area increased to 278.2 m2/g corresponding to small wall numbers and diameters. Taking advantage of the large surface area and high-temperature durability of the material, BNNTs utilized as a recyclable adsorbent for water purifcation. The efciency of the BNNTs for capturing methylene blue particles in water was approximately 94%, even after three repetition cycles, showing the potential of the material for application in the flter industry. Newly discovered materials such as fullerene, carbon nanotubes (CNTs), graphene, transition metal dichalco- genides, hexagonal boron nitride (h-BN), and boron nitride nanotubes (BNNTs) have provided great opportu- nities for scientifc and technical improvements in various application industries in the past several decades1–6. -
Buckypaper Bioelectrodes: Emerging Materials for Implantable and Wearable Biofuel Cells A
Buckypaper bioelectrodes: emerging materials for implantable and wearable biofuel cells A. Gross, M. Holzinger, S. Cosnier To cite this version: A. Gross, M. Holzinger, S. Cosnier. Buckypaper bioelectrodes: emerging materials for implantable and wearable biofuel cells. Energy & Environmental Science, Royal Society of Chemistry, 2018, 11 (7), pp.1670 - 1687. 10.1039/c8ee00330k. hal-03014545 HAL Id: hal-03014545 https://hal.archives-ouvertes.fr/hal-03014545 Submitted on 19 Nov 2020 HAL is a multi-disciplinary open access L’archive ouverte pluridisciplinaire HAL, est archive for the deposit and dissemination of sci- destinée au dépôt et à la diffusion de documents entific research documents, whether they are pub- scientifiques de niveau recherche, publiés ou non, lished or not. The documents may come from émanant des établissements d’enseignement et de teaching and research institutions in France or recherche français ou étrangers, des laboratoires abroad, or from public or private research centers. publics ou privés. Please do not adjust margins ARTICLE Journal Name Buckypaper bioelectrodes: Emerging materials for implantable and wearable biofuel cells Received 00th January 20xx, a a a, Accepted 00th January 20xx A. J. Gross, M. Holzinger and S. Cosnier * DOI: 10.1039/x0xx00000x Carbon nanotubes (CNTs) have been widely exploited for the development of enzymatic biofuel cells with sufficient power densities in the μW to mW range for operating low-power bioelectronics devices from renewable substrates. Buckypaper www.rsc.org/ is a randomly oriented self-supporting film of carbon nanotubes, resembling an electronic paper, with excellent prospects for the construction of high performance enzymatic electrodes for use in biofuel cells. -
From Carbon to Buckypaper
GENERAL ARTICLE From Carbon to Buckypaper Surabhi Potnis This article aims to highlight the amazing properties and po- tential uses of the more recently developed allotropes of car- bon such as carbon nanotubes, graphene, fullerene, and buck- ypaper. This is an area offering wide opportunity for re- search, especially due to the multidisciplinary nature of ap- plications. Carbon has always been acknowledged as an element essential to Surabhi Potnis – formerly life as we know it. It exists in a variety of physical forms or al- Head of Chemistry Department in St. Xavier’s lotropes that have been known for a long time – from the precious College, Mumbai has been diamond and lubricant graphite, to the lowly soot, lampblack, teaching at the coke, and charcoal. The more recently discovered and thereafter undergraduate and post artificially developed forms such as fullerene, carbon nanotubes, graduate levels in Mumbai University, and has also been and graphene are major landmarks in the field of material science, involved with various science and hold out much promise for the future. education platforms for ff school children. She is The di erence in properties of the various forms of carbon orig- actively involved with the inates primarily from their structural peculiarities. In a diamond, Junior Science Olympiad (Figure 1a) the carbon atoms have sp3 hybridization and are tetra- program conducted by the hedral, connected by covalent bonds, and forms a 3-dimensional Homi Bhabha Centre for Science Education (TIFR) network. The rigid structure thus formed is responsible for the Mumbai. extreme hardness of diamond. Graphite (Figure 1b), on the other hand, has carbon atoms in sp2 hybrid state, and the hexagonal planar structure thus formed exists in a large number of paral- lel layers. -
An Overview of the Recent Progress in the Synthesis and Applications of Carbon Nanotubes
Journal of C Carbon Research Review An Overview of the Recent Progress in the Synthesis and Applications of Carbon Nanotubes Gul Rahman 1,* , Zainab Najaf 1, Asad Mehmood 2, Salma Bilal 3, Anwar ul Haq Ali Shah 1, Shabeer Ahmad Mian 4 and Ghulam Ali 5 1 Institute of Chemical Sciences, University of Peshawar, Peshawar 25120, Pakistan; [email protected] (Z.N.); [email protected] (A.u.H.A.S.) 2 Department of Energy and Materials Engineering, Dongguk University-Seoul, Seoul 04620, Korea; [email protected] 3 National Center of Excellence in Physical Chemistry, University of Peshawar, Peshawar 25120, Pakistan; [email protected] 4 Department of Physics, University of Peshawar, Peshawar 25120, Pakistan; [email protected] 5 Center for Energy Convergence Research, Korea Institute of Science and Technology (KIST), Hwarang-ro 14-gil 5, Seongbuk-gu, Seoul 02792, Korea; [email protected] * Correspondence: [email protected]; Tel.: +92-91-911-6652 Received: 13 October 2018; Accepted: 27 December 2018; Published: 3 January 2019 Abstract: Carbon nanotubes (CNTs) are known as nano-architectured allotropes of carbon, having graphene sheets that are wrapped forming a cylindrical shape. Rolling of graphene sheets in different ways makes CNTs either metals or narrow-band semiconductors. Over the years, researchers have devoted much attention to understanding the intriguing properties CNTs. They exhibit some unusual properties like a high degree of stiffness, a large length-to-diameter ratio, and exceptional resilience, and for this reason, they are used in a variety of applications. These properties can be manipulated by controlling the diameter, chirality, wall nature, and length of CNTs which are in turn, synthesis procedure-dependent.