An Experimental Comparison of Galvanically Isolated DC-DC Converters: Isolation Technology and Integration Approach
Total Page:16
File Type:pdf, Size:1020Kb
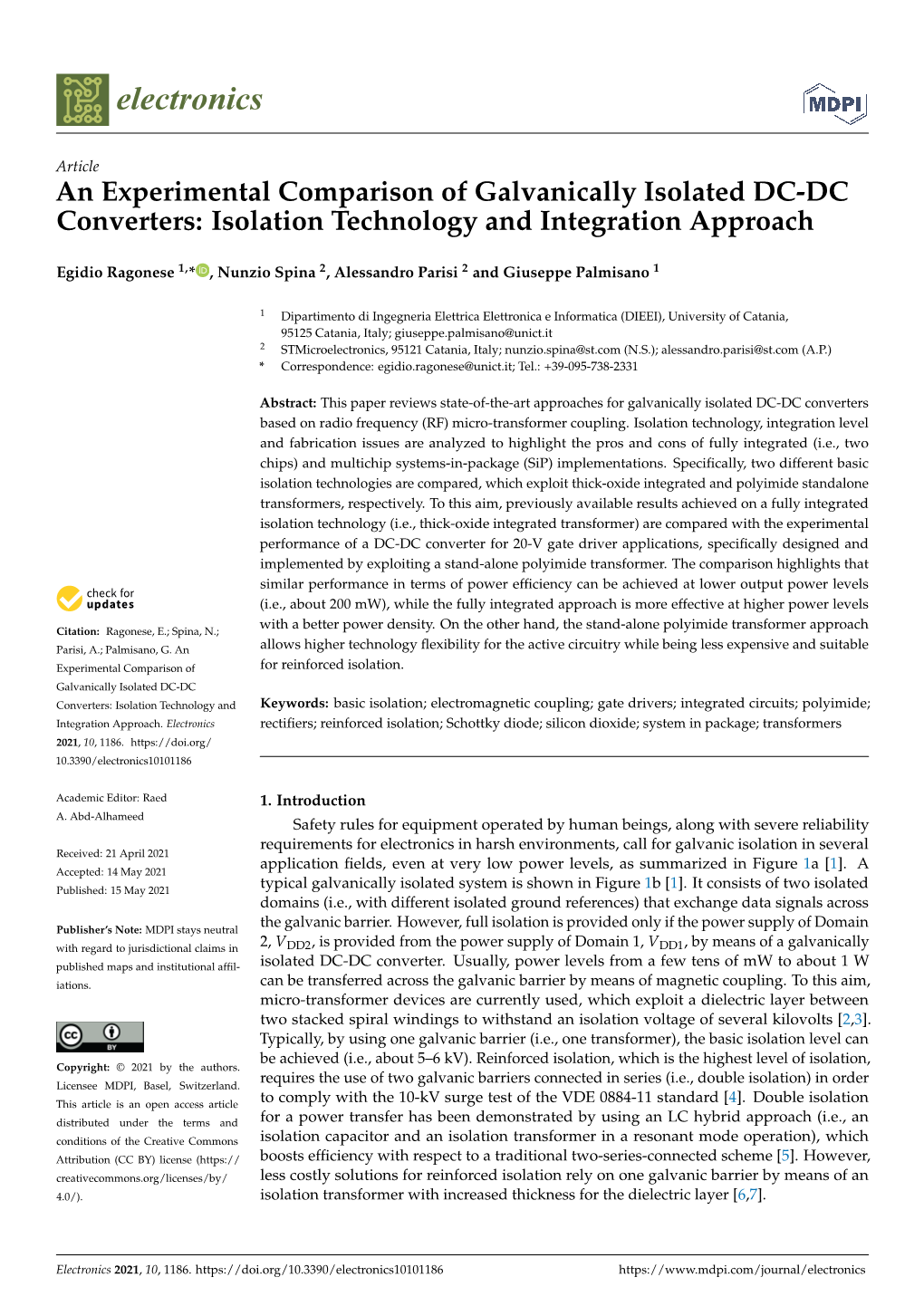
Load more
Recommended publications
-
Designing Linear Amplifiers Using the IL300 Optocoupler Application Note
Application Note 50 Vishay Semiconductors Designing Linear Amplifiers Using the IL300 Optocoupler INTRODUCTION linearizes the LED’s output flux and eliminates the LED’s This application note presents isolation amplifier circuit time and temperature. The galvanic isolation between the designs useful in industrial, instrumentation, medical, and input and the output is provided by a second PIN photodiode communication systems. It covers the IL300’s coupling (pins 5, 6) located on the output side of the coupler. The specifications, and circuit topologies for photovoltaic and output current, IP2, from this photodiode accurately tracks the photoconductive amplifier design. Specific designs include photocurrent generated by the servo photodiode. unipolar and bipolar responding amplifiers. Both single Figure 1 shows the package footprint and electrical ended and differential amplifier configurations are discussed. schematic of the IL300. The following sections discuss the Also included is a brief tutorial on the operation of key operating characteristics of the IL300. The IL300 photodetectors and their characteristics. performance characteristics are specified with the Galvanic isolation is desirable and often essential in many photodiodes operating in the photoconductive mode. measurement systems. Applications requiring galvanic isolation include industrial sensors, medical transducers, and IL300 mains powered switchmode power supplies. Operator safety 1 8 and signal quality are insured with isolated interconnections. These isolated interconnections commonly use isolation 2 K2 7 amplifiers. K1 Industrial sensors include thermocouples, strain gauges, and pressure transducers. They provide monitoring signals to a 3 6 process control system. Their low level DC and AC signal must be accurately measured in the presence of high 4 5 common-mode noise. -
Galvanic Isolation
Galvanic Isolation Stephen Mazich What is it? ● The prevention of current flow between sections of electrical systems ● Energy and/or information can still be exchanged ● Methods to exchange information include: ○ capacitance ○ induction ○ light ○ electromagnetic waves Image courtesy of Analog.com : http://www.analog.com/library/analogdialogue/archives/43-11/imgC_bb.gif Examples ● Transformer ○ Utilizes induction ● Opto-isolator ○ Utilizes light ● Capacitor(class Y) ○ Utilizes capacitance ● Hall effect ○ Utilizes electromagnetic waves Image courtesy of AYA Instruments : http://www.ayainstruments.com/images/theory001.jpg How does it apply to the project? The Formula Hybrid rules ● EV 1.2.4 The tractive and GLV system must be galvanically isolated from one another. ● EV 3.6.5 Any GLV connection to the AMS must be galvanically isolated from the TSV. ● EV 4.5.4 All controls, indicators, and data acquisition connections or similar must be galvanically isolated from the tractive system. ● EV 8.2.11 All chargers must be UL (Underwriters Laboratories) listed. Any waivers of this requirement require approval in advance, based on documentation of the safe design and construction of the system, including galvanic isolation between the input and output of the charger. Picture courtesy of the Formula SAE Rulebook : http://students.sae.org/cds/formulaseries/rules/2015-16_fsae_rules.pdf How are we using it? GLV ● DC-DC Converter ● Relay TSV ● Opto-isolator ● Isolated CAN transceiver ● Relay Dyno ● Opto-isolator ● Isolated CAN transceiver Images courtesy -
Galvanically Isolated on Chip Communication by Resonant
Galvanically Isolated on Chip Communication by Resonant Coupling by Mahdi Javidahmadabadi A Thesis Presented in Partial Fulfillment of the Requirements for the Degree Master of Science Approved July 2015 by the Graduate Supervisory Committee: Jennifer Kitchen, Chair Bertan Bakkaloglu James Aberle ARIZONA STATE UNIVERSITY August 2015 ABSTRACT Galvanic isolation is used in various applications such as power management circuits and medical equipment. In applications where high voltage DC transients are involved, it is necessary to isolate the high voltage portion of the system from the low voltage side to maintain reliability and/or safety requirements. But, most applications require communication between the low voltage and high voltage circuits, thus presenting a challenge to pass information through an isolation barrier. A concern in high-voltage gate drivers is when the middle point of the half-bridge falls below ground during a low-side switching occurrence. The negative voltage causes minority carrier injected to the substrate that travels into low voltage circuitry, such as the control circuit, and causes voltage shift or latch-up. Isolating the high side driver from the low voltage circuits can prevent the injected carriers from traveling to low side circuits. But, the control circuits must communicate to the high-side circuits, making it necessary to provide coupling to transmit the signal over the galvanically isolated barrier. In this research, a novel galvanic isolation method using magnetic coupled on- chip resonators has been proposed. Utilizing adjacently placed magnetically coupled resonators provides 1) high voltage galvanic isolation using the gaps between resonators filled with oxide and 2) magnetic coupling for signal transfer over these gaps. -
Signal Isolation
Signal Isolators, Converters and Interfaces: The “Ins” and “Outs” February 2019 By using the right signal interface instruments, in the right ways, potential problems can be easily avoided well before they boil over... quite literally in some cases. Whether you call them signal isolators, signal converters or signal interfaces, these useful process instruments solve important ground loop and signal conversion challenges everyday. Just as important, they are called upon to do a whole lot more. They can be used to share, split, boost, protect, step down, linearize and even digitize process signals. This guide will tell you many of the important ways signal isolators, converters and interfaces can be used, and what to look for when specifying one. In addition to simple signal isolation and conversion, signal interface instruments can be used to share, split, boost, protect, step down, Signal Isolation linearize and even digitize process signals. The need for signal isolation began to flourish in the To remove the ground loop, any one of these three 1960s and continues today. Electronic transmitters were conditions must be eliminated. The challenge is, the first quickly replacing their pneumatic predecessors because and second conditions are not plausible candidates for of cost, installation, maintenance and performance elimination. Why? Because you cannot always control advantages. However, it was soon discovered that when the number of grounds, and it is often impossible to just 4-20mA (or other DC) signal wires have paths to ground “lift” a ground. at both ends of the loop, problems are likely to occur. The ground may be required for the safe operation of The loop in question may be as simple as a differential an electronic device. -
Design and Implementation of High Frequency Isolated AC-DC Converter for Switched Mode Power Supplies
Design and Implementation of High Frequency Isolated AC-DC Converter for Switched Mode Power Supplies Dr. R. Kalpana, Prof. G. Bhuvaneswari, Prof. Bhim Singh and Saravana Prakash P Abstract—In this paper the design and implementation of DC- DC converter based SMPS for a telecommunication system is presented. A high frequency transformer is used to provide the galvanic isolation between the input and output. A complete design methodology of high frequency transformer used for full- bridge buck derived topology is presented. The operating modes, analysis, and design considerations are explained for the proposed converter. Simulation and experimental results are also presented to demonstrate the performance of the proposed converter. Fig. 1 Schematic diagram of the HF isolated dc-dc converter Keywords—High frequency isolation; Single-stage converter; converter module which is used for the steady state analysis Power factor correction (PFC); Full-bridge buck converter; SMPS and design purpose. It has a dc voltage source from the diode- bridge rectifier with a series inductor feeding to the full-bridge I. INTRODUCTION dc-dc converter. The use of three-phase ac-dc converters for The full-bridge buck converter has four IGBT switches telecommunication power supply system [1] have led to an (S1, S2, S3 and S4) and it is feeding to the high frequency increased harmonic content being injected into the utility mains transformer for providing galvanic isolation. The switches are and low power factor, both caused by the non-linear load ON alternatively in each half of PWM period with the behavior of conventional diode-rectifiers. controlled width of pulse decided by duty ratio from the PI controller. -
Improving EV-HEV Safety, Performance and Reliability with Galvanic Isolation Introduction Learn How
Improving EV-HEV Safety, Performance and Reliability with Galvanic Isolation Introduction Learn How New advances in electric vehicle (EV) and hybrid electric • Emerging requirements to vehicle (HEV) technology are propelling EV and HEV sales improve performance, safety, to new heights and accelerating the pace of innovation and reliability in EV/HEVs for this emerging automotive market. Electric and hybrid vehicles promise greater efficiency and reduced emissions influence car manufactures and are rapidly approaching price and performance parity to select digital isolation with gas-powered vehicles. To be competitive with existing over traditional optocoupler vehicles, the batteries used in EV/HEVs must possess very technology. high energy storage density, near-zero self-leakage current, and the ability to charge in minutes instead of hours. In • Higher-operating voltages addition, the battery management and associated power and currents and dissimilar conversion system must be of minimal size and weight and be able to deliver large amounts of power to the electric voltages in electric vehicles motor efficiently. Finally, the system driving the electric systems emphasize the motors, the traction inverter, needs to leverage cutting- importance of electrical edge semiconductor devices and control techniques to isolation for safety reasons. deliver maximum efficiency and torque from the motors. www.silabs.com/isolation/automotive-isolation 2 EV/HEV Systems Typically Include Six Key System Components Onboard Charger Energy storage is provided by 800 V and greater lithium-ion battery packs charged by an onboard charger (OBC) consisting of an ac-to-dc converter with power factor correction (PFC) and supervised by a battery management system (BMS). -
Design and Experimental Verification of Voltage Measurement Circuits
Article Design and Experimental Verification of Voltage Measurement Circuits Based on Linear Optocouplers with Galvanic Isolation for Battery Management Systems Borislav Dimitrov 1,*, Gordana Collier 1 and Andrew Cruden 2 1 School of Engineering, Computing and Mathematics, Oxford Brookes University, Wheatley campus, Oxford OX33 1HX, UK; [email protected] 2 Faculty of Engineering and the Environment, University of Southampton, University Road, SO17 1BJ Southampton, UK; [email protected] * Correspondence: [email protected]; Tel.: +44-(0)-1865-482962 Received: 20 July 2019; Accepted: 18 September 2019; Published: 23 September 2019 Abstract: A battery management system (BMS) design, based on linear optocouplers for Lithium-ion battery cells for automotive and stationary applications is proposed. The critical parts of a BMS are the input voltages and currents measurement circuits. In this design, they include linear optocouplers for galvanic isolation between the battery pack and the BMS. Optocouplers based on AlGaAs light emitted diodes (LED) and PIN photodiode with external operational amplifiers are used. The design features linear characteristics, to ensure the accuracy of the measurements. The suggested approach is based on graphical data digitalizing, which gives the precise values for the most sensitive parameters: photocurrent, normalized and transferred servo gain and helps the calculation procedure to be automated with MATLAB scripts. Several mathematical methods in the analysis are used in order for the necessary equations to be derived. The results are experimentally verified with prototypes. Keywords: battery management system; linear optocouplers; design; experimental verification; automotive applications 1. Introduction The battery management systems (BMS) are a central part of the on-board vehicles battery packs and battery packs for stationary applications. -
Advantages of a Transformer-Based UPS White Paper.Indd
ADVANTAGES OF A TRANSFORMER-BASED UPS SYSTEM No. 1 - March 2019 Introduction Recent Whitepapers have point out the advantages of transformerless UPS: less weight, fl exible installation, energy effi ciency, money savings. However, transformerless UPS are better suited for large energy effi cient applications where the tolerance for downtime is acceptable under certain circumstances and where there is a transformer installed somewhere else in the electric path. This literature has made it sound like transformer-based technology in UPSs is obsolete and should be avoided. Nonetheless, there are still critical applications requiring With an AC power supply present (I1), the power a nine nines rate which in turn need a transformer-based supply to the load comes from the Static Switch UPS. from the secondary winding of the Output Isolation For that reason, we are listing below the advantages of Transformer. The Rectifi er/PFC Converter is transformer-based UPS: connected to the AC power source (I1) and is used to generate the direct current (DC), which in turn • Galvanic isolation charges the Battery and powers the Inverter. • Independent mains power supplies When the primary AC power supply fails (I1), the • Dual load protection from DC voltage Inverter receives the power supply directly from the • Providing galvanic isolation and recreation of a fi xed TN-S Battery. If a fault occurs the load is automatically System (grounding system) without reducing operating transferred to the Bypass (I2), if available, through effi ciency the Static Switch. With Galvanic isolation between • Providing a higher phase-neutral inverter short circuit the two AC power sources (I1 and I2) – the Rectifi er current than a phase-phase short circuit current and the Bypass – the load is protected from • Superior power protection when presented with power electrical faults (or fault migration) on either AC quality problems power source and receives a continuous AC supply. -
Solutions for High Voltage Drives
Solutions for High Voltage Drives Identifying proper Gate Drivers for Power Switching and Differentiating Isolation techniques December 2020 Content and Presenters Introduction Powers Switches differences and why Gate Drivers are need it: Differences & Similarities between IGBT’s, MOSFET’s, SiC MOSFET’s & GaN MOSFET’s Gate Drive requirements for Power Switches needs Gate Drivers tech features overview Top Key Parameters for Gate Drivers Gate Drivers selection process Gate Drivers Categories/Types High Side, Low Side, Dual… etc… Non-isolated Gate Drivers & relationship to Power Switches Isolated Gate Driver and their Applications Types of Isolation and PROS/CONS of each Why Isolate, how to Isolate and Apps Isolation Standards 2 Gate Drivers Tech/Market & Applications Executive Summary Gate drivers technologies have had certain evolutions during the last decade With the arrival of on-chip integrated isolation technologies, isolated driver ICs have been developed by main driver IC manufacturers. These digital isolators are replacing the OPTO-coupler technology little bylittle So far, microtransformers (coreless transformers) are the preferred digitalisolation In the next 5 years, evolving industry needs will have a considerable impact on gate drivers as well: The emerging market of 48V mild hybrid will require isolated half-bridge drivers. Until now, there was no need for isolation in such low voltages. The cost of microtransformers manufactured today will decrease considerably. SiC MOSFETs will also have an impact on the gate driver market in two ways: Plug-and-Play market will enjoy a short term growth as some clients may choose to integrate SiC in their new generation converters. Customers encountering difficulties with the development of adequate drivers will prefer to purchase plug & play ones to accelerate the integration of SiC. -
Internal Faraday Shield and Small Ci-O Enhance Broadcom Optocoupler Galvanic Isolation Performance
White Paper Internal Faraday Shield and Small Ci-o Enhance Broadcom Optocoupler Galvanic Isolation Performance High-voltage isolation in today’s context involves integrating subsystems with large voltage differences and systems ground potentials. This enables isolation applications ranging from power supply, motor control circuit of servo automation systems and industrial robots, battery management systems, photovoltaic (PV) inverters, electric vehicle (eV) inverters, ultra-fast charging and wireless-charging stations to data communication and digital logic interface circuits. Basically, the most important components, isolators (couplers), provide electrical isolation that allows integration of different subsystems by breaking direct conduction paths. Integrated circuits (ICs) can be combined into the isolators for various electrical functions, such as driving power electronic devices, high accuracy current and voltage measurements, analog and digital communications and logic interfaces, and isolated power supply conversions. Isolation Technology Three types of isolator technologies are available: optocoupler, magnetic coupler, and capacitive coupler. Table 1 shows the key differences between the different isolation techniques, component safety certifications, and lifetime reliability failure mechanisms. Table 1: Key Differences between Different Isolation Techniques, Component Safety Certifications, and Lifetime Reliability Failure Mechanisms Isolator/Coupler Types Broadcom Optocoupler Magnetic Coupler Capacitive Coupler Isolation Construction -
Topologies for Switch Mode Power Supplies
APPLICATION NOTE TOPOLOGIES FOR SWITCHED MODE POWER SUPPLIES by L. Wuidart I INTRODUCTION This paper presents an overview of the most the rectifier, different types of voltage important DC-DC converter topologies. The converters can be made: main object is to guide the designer in selecting the topology with its associated power - Step down “Buck” regulator semiconductor devices. - Step up “Boost” regulator The DC-DC converter topologies can be divided in two major parts, depending on - Step up / Step down “Buck - Boost” regulator whether or not they have galvanic isolation between the input supply and the output II - 1 The “Buck” converter: Step down circuitry. voltage regulator II NON - ISOLATED SWITCHING REGULATORS The circuit diagram, often referred to as a “chopper” circuit, and its principal waveforms According to the position of the switch and are represented in figure 1: AN513/0393 1/18 APPLICATION NOTE Figure 1: The step down “Buck” regulator ∆ The power device is switched at a ≥ * Rectifier: VRRM Vin max frequency f = 1/T with a conduction duty δ I ≥ I (1-δ) cycle, = ton/T. The output voltage can also F(AV) out δ be expressed as: Vout = Vin . Device selection: * Power switch: Vcev or VDSS > Vin max ∆I I or I > I + cmax D max out 2 2/18 APPLICATION NOTE II.2 The “Boost” converter: Step up voltage regulator Figure 2 : The step up “Boost” regulator ton δ = T ∆ In normal operation, the energy is fed from Device selection: the inductor to the load, and then stored in the * Power switch: output capacitor. For this reason, the output Vcev or VDSS > Vout capacitor is stressed a lot more than in the I ∆I Buck converter. -
Galvanic Isolation in Regards to the LFEV 2015
Galvanic Isolation In Regards to the LFEV 2015 Stephen Mazich Department of Electrical & Computer Engineering Lafayette College Easton, Pa [email protected] Abstract— This paper is to explain the topic of galvanic isolation and explain its relevance to the course ECE 492 Senior C. Light Design. Light is used to galvanically isolate systems due Keywords- Galvanic Isolation; relay; optocoupler; induction; to the nature of light being unable to let current capacitance; CAN; flow. A LED is often coupled with a photo detector of some type to complete the transfer of information I. INTRODUCTION using light. The concept of galvanic isolation is the prevention of current flow between sections of electrical systems. While current cannot flow III. HOW IT APPLIES TO THE PROJECT between the sections, energy and/or information can The Formula Hybrid rules are set forth by the still be exchanged between the sections. Several IEEE and the SAE International organizations. different methods are used to exchange this These rules govern what is and isn’t allowed for the information. This paper will discuss capacitance, induction, light and electromagnetic waves as a way competition. These rules are set forth to provide for of transferring information between galvanically safety in the competition. isolated systems as they will be used in the project. There are four rules in the Formula Hybrid rule book that apply to galvanic isolation and therefore II. METHODS OF ISOLATION that part of our project. A. EV 1.2.4 A. Capacitance The tractive and GLV systems must be Capacitance can be used as a method of galvanic galvanically isolated from one another.