A Parametric Investigation and Optimization of a Cylindrical Explosive Charge Logan Ellsworth Beaver Marquette University
Total Page:16
File Type:pdf, Size:1020Kb
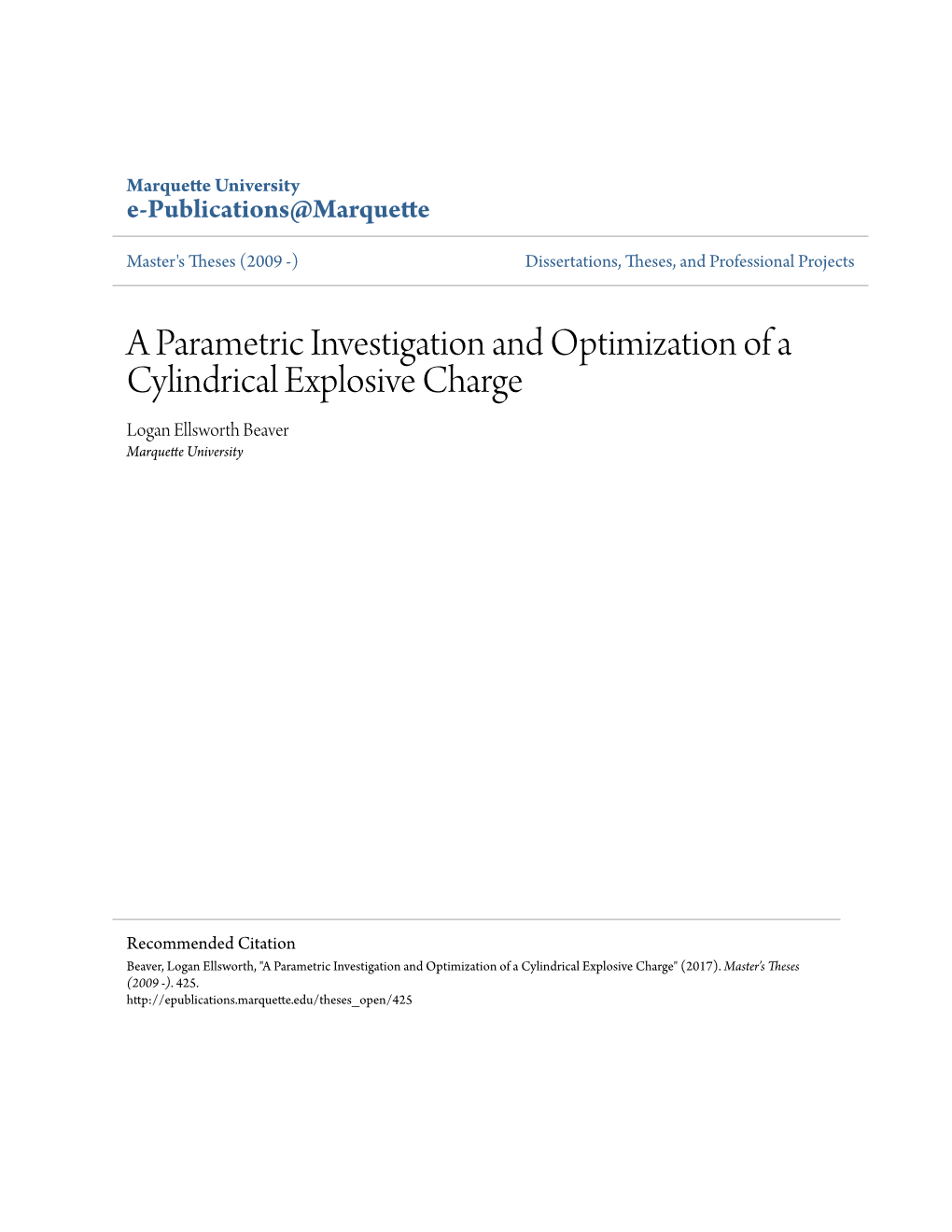
Load more
Recommended publications
-
3.1 the Dambusters Revisited
The Dambusters Revisited J.L. HINKS, Halcrow Group Ltd. C. HEITEFUSS, Ruhr River Association M. CHRIMES, Institution of Civil Engineers SYNOPSIS. The British raid on the Möhne, Eder and Sorpe dams on the night of 16/17 May, 1943 caused the breaching of the 40m high Möhne and 48m high Eder dams and serious damage to the 69m high Sorpe dam. This paper considers the planning for the raid, model testing, the raid itself, the effects of the breaches and the subsequent rehabilitation of the dams. Whilst the subject is of considerable historical interest it also has significant contemporary relevance. Events following the breaching of the dams have been used for the calibration of dambreak studies and emphasise the vulnerability of road and railway bridges which is not always acknowledged in contemporary studies. INTRODUCTION In researching this paper the authors have been very struck by the human interest in the story of English, German and Ukrainian people, whether civilian or in uniform, who participated in some aspect of the raid or who lost their lives or homes. As befits a paper for the British Dam Society, this paper, however, concentrates on the technical questions that arise, leaving the human story to others. This paper was prompted by the BDS sponsored visit, in April 2009, to the Derwent Reservoir by 43 members of the Association of Friends of the Hubert-Engels Institute of Hydraulic Engineering and Applied Hydromechanics at Dresden University of Technology. There is a small museum at the dam run by Vic Hallam, an employee of Severn Trent Water. -
The Development of Military Nuclear Strategy And
The Development of Military Nuclear Strategy and Anglo-American Relations, 1939 – 1958 Submitted by: Geoffrey Charles Mallett Skinner to the University of Exeter as a thesis for the degree of Doctor of Philosophy in History, July 2018 This thesis is available for Library use on the understanding that it is copyright material and that no quotation from the thesis may be published without proper acknowledgement. I certify that all material in this thesis which is not my own work has been identified and that no material has previously been submitted and approved for the award of a degree by this or any other University. (Signature) ……………………………………………………………………………… 1 Abstract There was no special governmental partnership between Britain and America during the Second World War in atomic affairs. A recalibration is required that updates and amends the existing historiography in this respect. The wartime atomic relations of those countries were cooperative at the level of science and resources, but rarely that of the state. As soon as it became apparent that fission weaponry would be the main basis of future military power, America decided to gain exclusive control over the weapon. Britain could not replicate American resources and no assistance was offered to it by its conventional ally. America then created its own, closed, nuclear system and well before the 1946 Atomic Energy Act, the event which is typically seen by historians as the explanation of the fracturing of wartime atomic relations. Immediately after 1945 there was insufficient systemic force to create change in the consistent American policy of atomic monopoly. As fusion bombs introduced a new magnitude of risk, and as the nuclear world expanded and deepened, the systemic pressures grew. -
A Tribute to Bomber Command Cranwellians
RAF COLLEGE CRANWELL “The Cranwellian Many” A Tribute to Bomber Command Cranwellians Version 1.0 dated 9 November 2020 IBM Steward 6GE In its electronic form, this document contains underlined, hypertext links to additional material, including alternative source data and archived video/audio clips. [To open these links in a separate browser tab and thus not lose your place in this e-document, press control+click (Windows) or command+click (Apple Mac) on the underlined word or image] Bomber Command - the Cranwellian Contribution RAF Bomber Command was formed in 1936 when the RAF was restructured into four Commands, the other three being Fighter, Coastal and Training Commands. At that time, it was a commonly held view that the “bomber will always get through” and without the assistance of radar, yet to be developed, fighters would have insufficient time to assemble a counter attack against bomber raids. In certain quarters, it was postulated that strategic bombing could determine the outcome of a war. The reality was to prove different as reflected by Air Chief Marshal Sir Arthur Harris - interviewed here by Air Vice-Marshal Professor Tony Mason - at a tremendous cost to Bomber Command aircrew. Bomber Command suffered nearly 57,000 losses during World War II. Of those, our research suggests that 490 Cranwellians (75 flight cadets and 415 SFTS aircrew) were killed in action on Bomber Command ops; their squadron badges are depicted on the last page of this tribute. The totals are based on a thorough analysis of a Roll of Honour issued in the RAF College Journal of 2006, archived flight cadet and SFTS trainee records, the definitive International Bomber Command Centre (IBCC) database and inputs from IBCC historian Dr Robert Owen in “Our Story, Your History”, and the data contained in WR Chorley’s “Bomber Command Losses of the Second World War, Volume 9”. -
No. 138 Squadron Arrived Flying Whitleys, Halifaxes and Lysanders Joined the Following Month by No
Life Of Colin Frederick Chambers. Son of Frederick John And Mary Maud Chambers, Of 66 Pretoria Road Edmonton London N18. Born 11 April 1917. Occupation Process Engraver Printing Block Maker. ( A protected occupation) Married 9th July 1938 To Frances Eileen Macbeath. And RAFVR SERVICE CAREER OF Sergeant 656382 Colin Frederick Chambers Navigator / Bomb Aimer Died Monday 15th March 1943 Buried FJELIE CEMETERY Sweden Also Remembered With Crew of Halifax DT620-NF-T On A Memorial Stone At Bygaden 37, Hojerup. 4660 Store Heddinge Denmark Father Of Michael John Chambers Grandfather Of Nathan Tristan Chambers Abigail Esther Chambers Matheu Gidion Chambers MJC 2012/13 Part 1 1 Dad as a young boy with Mother and Grandmother Dad at school age outside 66 Pretoria Road Edmonton London N18 His Father and Mothers House MJC 2012/13 Part 1 2 Dad with his dad as a working man. Mum and Dad’s Wedding 9th July 1938 MJC 2012/13 Part 1 3 The full Wedding Group Dad (top right) with Mum (sitting centre) at 49 Pembroke Road Palmers Green London N13 where they lived. MJC 2012/13 Part 1 4 After Volunteering Basic Training Some Bits From Dads Training And Operational Scrapbook TRAINING MJC 2012/13 Part 1 5 Dad second from left, no names for rest of people in photograph OPERATIONS MJC 2012/13 Part 1 6 The Plane is a Bristol Blenheim On leave from operations MJC 2012/13 Part 1 7 The plane is a Wellington Colin, Ken, Johnny, Wally. Before being posted to Tempsford Navigators had to served on at least 30 operations. -
The Dams Raid
The Dams Raid An Air Ministry Press Release, dated Monday, 17th May 1943, read as follows: In the early hours of this (Monday) morning a force of Lancasters of Bomber Command led by Wing Commander G. P. Gibson, D.S.O, D.F.C., attacked with mines the dams at the Möhne and Sorpe reservoirs. These control two-thirds of the water storage capacity of the Ruhr basin. Reconnaissance later established that the Möhne Dam had been breached over a length of 100 yards and that the power station below had been swept away by the resulting floods. The Eder Dam, which controls head waters of the Weser and Fulda valleys and operates several power stations, was also attached and was reported as breached. Photographs show the river below the dam in full flood. The attacks were pressed home from a very low level with great determination and coolness in the face of fierce resistance. Eight of the Lancasters are missing. That short statement lacked some of the secret details and the full human story behind one of the most famous raids in the history of the Royal Air Force. It is the real story of the Dambusters. The story of the “bouncing bomb” designer Barnes Wallis and 617 Squadron is heavily associated with the film, starring Michael Redgrave as Dr Barnes Wallis and Richard Todd as Wing Commander Guy Gibson – and featuring the Dambusters March, the enormously popular and evocative theme by Eric Coates. The film opened in London almost exactly twelve years after the events portrayed. The main detail of the raid which was not fully disclosed until much later was the true specification of the bomb, details which were still secret when the film was made. -
Program and Course Catalog 2015-2016 2
1 Program and Course Catalog 2015-2016 2 Table of Contents Fine Arts ............................................................................................ 77 Health & Wellness ............................................................................ 78 General Information about Course Descriptions Accreditation ...................................................................................... 3 General Studies ................................................................................ 33 Course Numbers ................................................................................ 4 Information Technology .................................................................. 79 Credit Hours ...................................................................................... 4 Management ..................................................................................... 84 Prerequisites and Corequisites ........................................................ 4 Accounting ....................................................................... 86 Cross-Listing ...................................................................................... 4 Business Computing Systems ........................................ 87 Electives .............................................................................................. 4 Economics ......................................................................... 87 Degree Requirements ........................................................................ 5 Finance ............................................................................. -
550 Squadron North Killingholme. BQ-B the Phantom of the Ruhr
550 Squadron North Killingholme. BQ-B The Phantom of the ruhr. BQ-B The Phantom of the Ruhr was one of only three Lancaster’s of 550 Squadron to have completed more than 100 operational sorties. 550 SquadRon Insignia. Through Fire We Conquer. RAF 550 Squadron Flying Echelon, North Killingholme, Lincolnshire. RAF 550 Squadron was formed at Waltham in Nov 1943 and moved to North Killingholme on the 3rd Jan 1944. Its first sortie was to Brunswick on the 14th Jan 1944. The Squadron completed 144 sorties comprising some 4,270 night flying hours and 4,988 daylight hrs. A total 9,250 hrs flown. The squadron dropped 16,195 tons of bombs. 56 aircraft and crews were reported missing and 14 others crashed. Nearly 500 airmen were lost. An informal crew photograph taken sometime in 1944. We flew in Lancaster BQ-Z,Zebra. Z.Zebra crashed in France on our 18th bombing sortie following a mid-air collision while returning from a mission over Ludwigshafen in Germany on the 1st February 1945. Vic Bill Aubrey Norman Eddie Andy Alan Cassapi Anderson Lohrey Tinsley Westhorpe James Jarnell F/E B/A Pilot W/O Nav Mu/G R/G 550 Sqd Flight Engineers 1943-1945. The majority of Flight Engineers on 550 Squadron where fully trained pilots. Though not qualified to fly Lancaster’s, even so all Engineers where trained to fly a straight and level Course in an emergency. I am pictured here on the top row extreme right. Me in the drivers seat. I take a turn in flying Z.Zebra during a cross-country navigation exercise. -
Bouncing-Bomb Man
r Iain Murray is a lecturer in arnes Wallis is best known as the the School of Computing at the ‘boffin’ behind the famous bouncing D Bouncing B University of Dundee, where his bomb used by 617 Squadron to breach research interests include emotion the Ruhr dams in 1943, but his work in synthesised speech. He is Chair covers a far wider canvas. It ranges of the Tayside & Fife Branch of the from airships, through novel aircraft British Science Association and acted structures and special weapons to as a consultant for an episode of the long-range supersonic aircraft, and an ITV drama series Foyle’s War, which extensive patent portfolio. featured a group working on the So how did Wallis’s engineering ‘bouncing bomb’. He lives in Dundee. brilliance take ideas from airships and push them forward to create aircraft - faster than Concorde? Dr Iain Murray Bomb Man Bomb describes the huge breadth of Wallis’s work, showing why his genius brought totally new ideas into these fields, and From giant airships, hypersonic passenger aircraft and a better cricket ball reveals the science and engineering to the legendary bouncing bomb, this fascinating book examines the work expertise that he deployed to make them work. of British engineering genius Sir Barnes Wallis. Dr Iain Murray analyses This is the first book to describe Wallis’s ideas as he did himself – like an experiment, to be invented, built the entire life’s work of Wallis in detail, viewed through the prism of his and tested in operation. He looks at the huge range of Wallis’s inventions technical achievements. -
Gallantry in the Air
Cranwell Aviation Heritage Museum Gallantry in the Air 0 This is the property of Cranwell Aviation Heritage Centre, a North Kesteven District Council service. The contents are not to be reproduced or further disseminated in any format without written permission from NKDC. Introduction This file contains material and images which are intended to complement the displays and presentations in Cranwell Aviation Heritage Museum’s exhibition areas. This file is intended to let you discover more about the heroism of aircrew whose acts of bravery during World War 2 resulted in them receiving gallantry awards. Where possible all dates regarding medal awards and promotions have been verified with entries published in the London Gazette. This file is the property of Cranwell Aviation Heritage Museum, a North Kesteven District Council service. The contents are not to be reproduced or further disseminated in any format, without written permission from North Kesteven District Council. 1 This is the property of Cranwell Aviation Heritage Centre, a North Kesteven District Council service. The contents are not to be reproduced or further disseminated in any format without written permission from NKDC. Contents Page Wg Cdr Roderick Learoyd 3 FO Leslie Manser 5 WO Norman Jackson 7 Sqn Ldr Arthur Scarf 9 Sqn Ldr James Lacey 11 Wg Cdr Hugh Malcolm 13 Wg Cdr Guy Gibson 15 Gp Capt Douglas Bader 17 Wg Cdr Leonard Cheshire 19 Gp Capt Francis Beamish 21 FS John Hannah 24 Flt Lt Pat Pattle 26 FS George Thompson 28 Flt Lt William Reid 30 FO Kenneth Campbell 32 Gp Capt James Tait 34 Gp Capt John Braham 36 Sqn Ldr John Nettleton 38 Wg Cdr Adrian Warburton 40 Wg Cdr Brendan Finucane 42 Flt Lt Eric Lock 44 AVM James Johnson 46 Sqn Ldr Johnny Johnson 48 FS Leslie Chapman 50 2 This is the property of Cranwell Aviation Heritage Centre, a North Kesteven District Council service. -
Ph.D. in Mechanical Engineering with Dissertation in Intelligent Energetic Systems Program
A proposal for the Doctor of Philosophy Degree in Mechanical Engineering with Dissertation in Intelligent Energetic Systems at the New Mexico Institute of Mining and Technology October 2015 1 Executive Summary ............................................................................................................... 4 A Purpose of the Program ................................................................................................... 5 A.1 The Primary Purpose of the Proposed Program ....................................................... 5 A.2 Consistency of the Proposed Program with the Role and Scope of the Institution .. 6 A.3 Priority of the Institution for the Proposed Program ................................................ 7 A.4 Curriculum ............................................................................................................... 8 B Justification for the Program ......................................................................................... 11 B.1 State and Regional Need ........................................................................................ 11 B.2 Duplication ............................................................................................................. 13 B.3 Inter-Institutional Collaboration and Cooperation ................................................. 16 C Clientele and Projected Enrollment............................................................................... 21 C.1 Clientele ................................................................................................................ -
Klein S4900 Supports Vessel and WWII Ordnance Survey in Scotland
NEWS Klein S4900 Supports Vessel and WWII Ordnance Survey in Scotland Klein Marine Systems has supported a successful survey and WWII ordnance recovery project off the west coast of Scotland on a sea inlet once referred to as the “Secret Loch”. The Klein System 4900 sidescan sonar was deployed from the Aspect Surveys vessel ‘Vigilance’ and operated by personnel from Unique Systems - GSE Rentals who provided the winch, cable and ancillary support for the project. Arriving at the target area it quickly became apparent that there was a more dense scattering of “Highballs” in and around sections of anchor chain that had been cut and discarded with their anchors still in place as the French target vessel was towed away for scrap after the war. Survey operators were able to take full advantage of the Klein System 4900’s capability to provide high definition images for classification to 75m per side at 900kHz. An initial pass through the centre channel of the Loch revealed the seafloor was made up of a relatively featureless areas with the exception of extensive trench-marks and scarring presumably caused by the anchor chains used by large cargo container traffic that at one time used the loch as a safe haven during poor weather. Highball Bomb In World War II, British engineer Sir Barnes Wallis invented the bouncing bomb that was designed to skip over the surface of a stretch of water, avoiding anti-torpedo nets, before sinking directly next to a dam wall or battleship target. The initial bombs code-named “Upkeep” were used successfully against the Ruhr dams in Northern Germany. -
Airpower and the Environment
Airpower and the Environment e Ecological Implications of Modern Air Warfare E J H Air University Press Air Force Research Institute Maxwell Air Force Base, Alabama July 2013 Airpower and the Environment e Ecological Implications of Modern Air Warfare E J H Air University Press Air Force Research Institute Maxwell Air Force Base, Alabama July 2013 Library of Congress Cataloging-in-Publication Data Airpower and the environment : the ecological implications of modern air warfare / edited by Joel Hayward. p. cm. Includes bibliographical references and index. ISBN 978-1-58566-223-4 1. Air power—Environmental aspects. 2. Air warfare—Environmental aspects. 3. Air warfare—Case studies. I. Hayward, Joel S. A. UG630.A3845 2012 363.739’2—dc23 2012038356 Disclaimer Opinions, conclusions, and recommendations expressed or implied within are solely those of the author and do not necessarily represent the views of Air University, the United States Air Force, the Department of Defense, or any other US government agency. Cleared for public release; distribution unlimited. AFRI Air Force Research Institute Air University Press Air Force Research Institute 155 North Twining Street Maxwell AFB, AL 36112-6026 http://aupress.au.af.mil ii Contents About the Authors v Introduction: War, Airpower, and the Environment: Some Preliminary Thoughts Joel Hayward ix 1 The mpactI of War on the Environment, Public Health, and Natural Resources 1 Victor W. Sidel 2 “Very Large Secondary Effects”: Environmental Considerations in the Planning of the British Strategic Bombing Offensive against Germany, 1939–1945 9 Toby Thacker 3 The Environmental Impact of the US Army Air Forces’ Production and Training Infrastructure on the Great Plains 25 Christopher M.