F-Band (90-140 Ghz) Uni-Traveling-Carrier Photodiode Module for a Photonic Local Oscillator
Total Page:16
File Type:pdf, Size:1020Kb
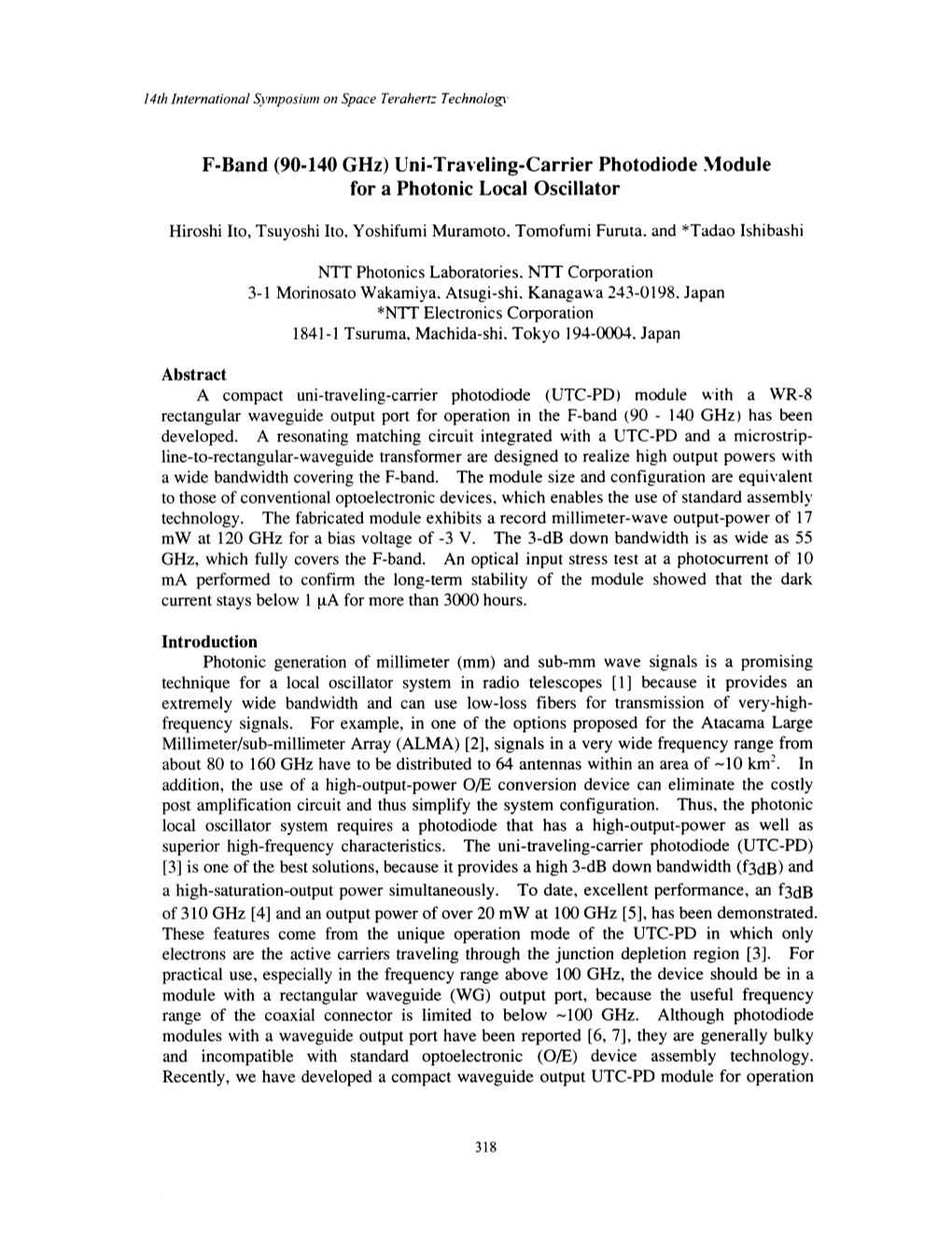
Load more
Recommended publications
-
Qatar National Frequency Allocation Plan and Specific
Communications Regulatory Authority 2 Table of Contents Qatar National Frequency Allocation Plan and Specific Assignments Table of Contents Part 01. GENERAL INFORMATION .............................................................................................................. 1. Introduction ...................................................................................................................................................5 2. Principals of Spectrum Management .................................................................................................5 3. Definition of terms used ..........................................................................................................................7 4. How to read the frequency allocation table .................................................................................. 11 5. Radio Wave Spectrum ............................................................................................................................ 12 Part 02. FREQUENCY ALLOCATION PLAN ............................................................................................... Qatar Frequency Allocation Plan ............................................................................................................ 15 Part 03. QATAR’S FOOTNOTES ................................................................................................................... Footnotes Relevant to Qatar................................................................................................................. -
Color Centers in Additively Colored Csbr David W
Physics and Astronomy Publications Physics and Astronomy 9-1962 Color Centers in Additively Colored CsBr David W. Lynch Iowa State University, [email protected] Follow this and additional works at: http://lib.dr.iastate.edu/physastro_pubs Part of the Atomic, Molecular and Optical Physics Commons, and the Optics Commons The ompc lete bibliographic information for this item can be found at http://lib.dr.iastate.edu/physastro_pubs/8. For information on how to cite this item, please visit http://lib.dr.iastate.edu/howtocite.html. This Article is brought to you for free and open access by the Physics and Astronomy at Iowa State University Digital Repository. It has been accepted for inclusion in Physics and Astronomy Publications by an authorized administrator of Iowa State University Digital Repository. For more information, please contact [email protected]. Color Centers in Additively Colored CsBr Abstract Color centers have been studied in CsBr single crystals additively colored with potassium or cesium. More than ten absorption bands were produced, most of which had previously been found in crystals colored by ionizing radiation. All bands produced by irradiation at or above liquid nitrogen temperature appear to arise from trapped electrons. The most prominent bands in the additively colored crystals are the F band at 642 mμ (liquid nitrogen temperature) and a band at 243 mμ which appears to be due to an impurity. Optically bleaching the F band at 200°K produces bands analogous to the M and R bands in other alkali halides while bleaching at liquid nitrogen temperature yields a broad band identified as the F′ band. -
Far Infrared Vibration-Rotation-Tunneling Spectroscopy and Internal Dynamics of Methane-Water: a Prototypical Hydrophobic System L
Far infrared vibration-rotation-tunneling spectroscopy and internal dynamics of methane-water: A prototypical hydrophobic system L. Dore,a) R. C. Cohen,b) C. A. Schmuttenmaer,c) K. L. Busarow, M. J. Elrod, J. G. Loeser, and R. J. Saykally Department of Chemistry, University of California, Berkeley, California 94720 (Received 26 March 1993; accepted 1 October 1993) Thirteen vibration-rotation-tunneling (VRT) bands of the CH4-H,O complex have been mea- sured in the range from 18 to 35.5 cm-’ using tunable far infrared laser spectroscopy. The ground state has an average center of mass separation of 3.70 A and a stretching force constant of 1.52 N/m, indicating that this complex is more strongly bound than Ar-H,O. The eigenvalue spectrum has been calculated with a variational procedure using a spherical expansion of a site-site ab i&o intermolecular potential energy surface [J. Chem. Phys. 93, 7808 ( 1991)]. The computed eigenvalues exhibit a similar pattern to the observed spectra but are not in quantita- tive agreement. These observations suggest that both monomers undergo nearly free internal rotation within the complex. I. INTRODUCTION order terms in the IPS, whereas they are usually neglected when the more typical low order terms are present. Water-hydrophobe interactions govern essential fea- This study and the accompanying microwave (MW) tures of many chemical and biochemical processes. Con- work’ constitute the first spectroscopic studies of this clus- siderable controversy exists in the literature concerning the ter; in fact it is only within the last 3 years that any high correct molecular description of the macroscopic phenom- resolution spectra for methane containing complexes have ena commonly associated with hydrophobic interactions been reported. -
Recent Progress on Extended Wavelength and Split-Off Band
micromachines Review Recent Progress on Extended Wavelength and Split-Off Band Heterostructure Infrared Detectors Hemendra Ghimire 1, P. V. V. Jayaweera 2 , Divya Somvanshi 3, Yanfeng Lao 4 and A. G. Unil Perera 1,* 1 Center for Nano-Optics (CeNo), Department of Physics and Astronomy, Georgia State University, Atlanta, GA 30033, USA; [email protected] 2 SPD Laboratory, Inc., Hamamatsu 432-8011, Japan; [email protected] 3 Department of Electronics and Tele-Communication Engineering, Jadavpur University, Kolkata 700032, India; [email protected] 4 Hisense Photonics, Inc., 5000 Hadley Road, South Plainfield, NJ 07080, USA; [email protected] * Correspondence: [email protected] Received: 21 April 2020; Accepted: 20 May 2020; Published: 28 May 2020 Abstract: The use of multilayer semiconductor heterojunction structures has shown promise in infrared detector applications. Several heterostructures with innovative compositional and architectural designs have been displayed on emerging infrared technologies. In this review, we aim to illustrate the principles of heterostructure detectors for infrared detection and explore the recent progress on the development of detectors with the split-off band and threshold wavelength extension mechanism. This review article includes an understanding of the compositional and the architectural design of split-off band detectors and to prepare a database of their performances for the wavelength extension mechanism. Preparing a unique database of the compositional or architectural design of structures, their performance, and penetrating the basics of infrared detection mechanisms can lead to significant improvements in the quality of research. The brief outlook of the fundamentals of the infrared detection technique with its appropriateness and limitations for better performance is also provided. -
THE ULTRAVIOLET, OPTICAL, and INFRARED PROPERTIES of SLOAN DIGITAL SKY SURVEY SOURCES DETECTED by GALEX Marcel A
View metadata, citation and similar papers at core.ac.uk brought to you by CORE provided by Columbia University Academic Commons The Astronomical Journal, 130:1022–1036, 2005 September A # 2005. The American Astronomical Society. All rights reserved. Printed in U.S.A. THE ULTRAVIOLET, OPTICAL, AND INFRARED PROPERTIES OF SLOAN DIGITAL SKY SURVEY SOURCES DETECTED BY GALEX Marcel A. Agu¨eros,1,2 Zˇ eljko Ivezic´,1 Kevin R. Covey,1 Mirela Obric´,3 Lei Hao,4 Lucianne M. Walkowicz,1 Andrew A. West,1 Daniel E. Vanden Berk,5 Robert H. Lupton,6 Gillian R. Knapp,6 James E. Gunn,6 Gordon T. Richards,6 John Bochanski, Jr.,1 Alyson Brooks,1 Mark Claire,1 Daryl Haggard,1 Nathan Kaib,1 Amy Kimball,1 Stephanie M. Gogarten,1 Anil Seth,1 and Michael Solontoi1 Received 2004 December 6; accepted 2005 May 16 ABSTRACT We discuss the ultraviolet, optical, and infrared properties of the Sloan Digital Sky Survey (SDSS) sources detected by the Galaxy Evolution Explorer (GALEX ) as part of its All-sky Imaging Survey Early Release Ob- servations. Virtually all (>99%) the GALEX sources in the overlap region are detected by SDSS; those without an SDSS counterpart within our 600 search radius are mostly unflagged GALEX artifacts. GALEX sources represent 2.5% of all SDSS sources within these fields, and about half are optically unresolved. Most unresolved GALEX- SDSS sources are bright (r < 18 mag), blue, turnoff, thick-disk stars and are typically detected only in the GALEX near-ultraviolet (NUV) band. The remaining unresolved sources include low-redshift quasars (z < 2:2), white dwarfs, and white dwarf–M dwarf pairs, and these dominate the optically unresolved sources detected in both GALEX bands. -
Research Article Special Issue
Journal of Fundamental and Applied Sciences Research Article ISSN 1112-9867 Special Issue Available online at http://www.jfas.info WIND SPEED ON ULTRA HIGH FREQUENCY (UHF) OF RADIO SIGNAL S. N. A. Syed Zafar1, S. N. Hazmin2, R. Mat2, M. S. Marhamah1 and R. Umar1,* 1East Coast Environmental Research Institute (ESERI), Universiti Sultan Zainal Abidin, Gong Badak Campus, 21300 Kuala Nerus, Terengganu, Malaysia 2School of Fundamental Science, Universiti Malaysia Terengganu, 21030 Kuala Terengganu, Terengganu, Malaysia Published online: 15 January 2018 ABSTRACT East coast of Peninsular Malaysia has received average wind speed up to 55km/h which equivalent to 15.4m per second and 30 knot, especially during monsoon. These circumstances had affected the radio signal by degrading its strength and quality. This study observe the relationship of wind speed and radio signal in Ultra High Frequency band. The statistical spearman correlation were applied and graph relationship of two variables were plotted in order to investigate these two variables. The measurement were done at 24 hour in February and July 2016 at Kusza Observatory. Analysis of result shown that high correlation strength (r = 0.555) was indicated in first of observation (1-O) at frequency of 382.5MHz. No high correlation were quantified in second of observation (2-O). These findings related to the observed high wind speed which is brought high of water vapor, hence attenuating the radio signal. Keywords: radio signal strength; wind speed; correlation. Author Correspondence, e-mail: [email protected] doi: http://dx.doi.org/10.4314/jfas.v10i1s.18 1. INTRODUCTION Wind is occurring due to the differences in the atmospheric pressure. -
Continuously Tunable, Phase-Locked, Continuous-Wave Terahertz
JOURNAL OF APPLIED PHYSICS 107, 033111 ͑2010͒ Continuously tunable, phase-locked, continuous-wave terahertz generator based on photomixing of two continuous-wave lasers locked to two independent optical combs ͒ Takeshi Yasui,1,a Hisanari Takahashi,2,3 Yutaka Iwamoto,2,3 Hajime Inaba,2 and Kaoru Minoshima2,3 1Graduate School of Engineering Science, Osaka University, 1-3 Machikaneyama-cho, Toyonaka, Osaka 560- 8531, Japan 2National Metrology Institute of Japan, National Institute of Advanced Industrial Science and Technology, 1- 1-1 Umezono, Tsukuba, Ibaraki 305-8563, Japan 3Faculty of Science and Technology, Tokyo University of Science, 2641 Yamasaki, Noda, Chiba 278-8510, Japan ͑Received 16 November 2009; accepted 29 December 2009; published online 9 February 2010͒ A continuously tunable, phase-locked, single-frequency, continuous-wave ͑cw͒ terahertz generator has been demonstrated around 120 GHz, corresponding to the spectral bandwidth of the F-band unitraveling-carrier photodiode ͑UTC-PD͒ used as a photomixer in this study. This cw-terahertz generator is based on photomixing of an accurately tunable cw laser and a tightly fixed cw laser in the optical frequency region, phase locked to two independent optical combs. The continuous tuning range of the presented method was three orders of magnitude around 0.1 THz and two orders around 1 THz broader than that of a previous photomixing method in which two cw lasers are phase locked to a single optical comb, and fully covered the available spectral bandwidth of the F-band UTC-PD. The spectral behavior of the tight locking and continuous tuning of 120 GHz cw-terahertz radiation was confirmed in real time by use of a terahertz-comb-referenced spectrum analyzer. -
Unlicensed, Wireless, Transport SMPTE292M, Video Using V-Band MMW
Unlicensed, Wireless, Transport SMPTE292M, Video using V-Band MMW by Dave Russell, MMW Radio Product-Line Manager HXI, LLC. Contact HXI at 978-521-7300 ext. 7304 for more information. Forward Once the exclusive realm of scientific research and military use, wireless systems operating in the upper millimeter wave (MMW) regions are now providing cost-effective solutions for high-capacity commercial data transport needs. While MMW technology is nothing new, the growing volume of commercial use with associated economies of scale has significantly reduced system costs, making MMW systems more attractive to the general consumer. The unique attributes of MMW signal propagation, combined with the scarcity of RF spectrum at lower frequencies, assures that the proliferation of MMW systems and their effect on daily life will continue. This article examines the unique attributes of signal propagation in the MMW region. The goal of this analysis is to provide the reader with a general, working knowledge to make informed decisions when considering MMW solutions. A dual channel SMPTE292M wireless transport system is used as a characteristic example of a commercial MMW application. This system demonstrates the capacity benefits of MMW techniques by providing roughly 3Gbps of raw HDTV production video throughput in an unlicensed band. The Upper MMW Spectrum The millimeter wave spectrum is defined as that region above microwave where the signal wavelength falls within the range of 1 to 0.1mm. Because of the direct relationship between signal frequency and signal wavelength, signal frequencies from 30-300GHz are defined as millimeter wave frequencies. The millimeter wave spectrum is also identified by IEEE established letter designations. -
Terahertz Photovoltaic Detection of Cyclotron Resonance in the Regime of Radiation-Induced Magnetoresistance Oscillations
PHYSICAL REVIEW B 87, 245308 (2013) Terahertz photovoltaic detection of cyclotron resonance in the regime of radiation-induced magnetoresistance oscillations R. G. Mani, A. N. Ramanayaka, and Tianyu Ye Department of Physics and Astronomy, Georgia State University, Atlanta, Georgia 30303, USA M. S. Heimbeck Aviation & Missile Research, Development, and Engineering Center (AMRDEC), Redstone Arsenal, Huntsville, Alabama 35898, USA H. O. Everitt Aviation & Missile Research, Development, and Engineering Center (AMRDEC), Redstone Arsenal, Huntsville, Alabama 35898, USA and Department of Physics & Departments of Electrical and Computer Engineering, Duke University, Durham, North Carolina 27708-0305, USA W. Wegscheider Laboratorium fur¨ Festkorperphysik,¨ ETH Zurich,¨ 8093 Zurich,¨ Switzerland (Received 6 January 2013; revised manuscript received 19 May 2013; published 17 June 2013) We examine and compare the diagonal magnetoresistance, Rxx, and the photovoltage induced by microwave (42 f<300 GHz) and terahertz (f 300 GHz) photoexcitation in the high mobility quasi-two-dimensional GaAs/AlGaAs system. The data demonstrate strong radiation-induced magnetoresistance oscillations in Rxx to 360 GHz. In addition, cyclotron resonance is observed in the photovoltage to 725 GHz. These results show that our high-mobility GaAs/AlGaAs two-dimensional electron system (2DES) specimens remain photoactive in magnetotransport into the terahertz band. DOI: 10.1103/PhysRevB.87.245308 PACS number(s): 72.20.My, 72.20.Fr, 72.80.Ey, 73.43.Fj I. INTRODUCTION Here, Ref. 15 exhibited radiation-induced magnetoresistance oscillations to 254 GHz. Reference 18 is especially remarkable Microwave photoexcited transport studies of the because it reported that the radiation-induced magnetoresis- GaAs/AlGaAs two-dimensional electron system (2DES) at tance oscillations begin to quench at 120 GHz and disappear high filling factors or low magnetic fields, B, have revealed completely above 230 GHz. -
Sub-Terahertz Radiation from DARC with Laser Created Filament
Sub-Terahertz radiation from DARC with laser created filament Takeharu Hommyo, Yusuke Hyuga, Takamitsu Otsuka and Noboru Yugami Department of Engineering, Utsunomiya University 7-1-2 Yoto, Utsunomiya, Tochi 321-8585 JAPAN ABSTRACT We present the results on generating sub-terahertz radiation by using the dc to ac radiation converter. A relativistic ionization front which is created by the laser filament of loose focus of Ti:sapphire laser pass through a capacitor array of period d= 0.5 cm with a gas pressure between 1 and 200 Pa. The maximum frequency of the generated emission is determined to be in the range of 0.1 to 0.3 THz by several diodes. Keywords Laser created plasma, sub-Terahertz wave, DARC 1. Introduction electrostatic field and an ionization front. In the Generation of the electromagnetic wave by laboratory frame, the generated wave in the plasma laser-plasma interaction is one of the most attractive behind the ionization front is directly observed as the topics in order to realize powerfull radiation sources EM wave radiation pulse18. The observed frequency, with tunable frequency. Not only the theoretical however, is upshifed from zero-frequency, that is, works but also experimental ones have been studied this scheme can directly convert the DC field energy for plasma application of a short, tunable radiation to the EM wave radiation. Therefore, this scheme was sources. As the recent interests, the generation of referred to as a dc to ac radiation converter (DARC terahertz radiation has been extensively investigated source). This means a direct electromagnetic wave in experiments of the laser-plasma interaction and generation from the static electric field and this formation of filaments by intense laser propagating in mechanism is expected to be efficient and to generate air or gas. -
Polycyclic Aromatic Hydrocarbons in Protoplanetary Disks: Emission and X-Ray Destruction
A&A 543, A25 (2012) Astronomy DOI: 10.1051/0004-6361/201219039 & c ESO 2012 Astrophysics Polycyclic aromatic hydrocarbons in protoplanetary disks: emission and X-ray destruction R. Siebenmorgen1 and F. Heymann2 1 European Southern Observatory, Karl-Schwarzschild-Str. 2, 85748 Garching b. München, Germany e-mail: [email protected] 2 Department of Physics and Astronomy, University of Kentucky, Lexington, KY 40506-0055, USA Received 14 February 2012 / Accepted 13 April 2012 ABSTRACT We study the polycyclic aromatic hydrocarbon (PAH) emission from protoplanetary disks. First, we discuss the dependence of the PAH band ratios on the hardness of the absorbed photons and the temperature of the stars. We show that the photon energy together with a varying degree of the PAH hydrogenation accounts for most of the observed PAH band ratios without the need to change the ionization degree of the molecules. We present an accurate treatment of stochastic heated grains in a vectorized three dimensional Monte Carlo dust radiative transfer code. The program is verified against results using ray tracing techniques. Disk models are presented for T Tauri and Herbig Ae stars. Particular attention is given to the photo-dissociation of the molecules. We consider beside PAH destruction also the survival of the molecules by vertical mixing within the disk. By applying typical X-ray luminosities the model accounts for the low PAH detection probability observed in T Tauri and the high PAH detection statistics found in Herbig Ae disks. Spherical halos above the disks are considered. We show that halos reduce the observed PAH band-to-continuum ratios when observed at high inclination. -
Managing Space-Based Resources August 2020
SSI ISSUE GUIDE MANAGING SPACE-BASED RESOURCES AUGUST 2020 ABOUT The ability to operate a satellite in outer space requires access to radiofrequencies and orbital positions, both scarce resources. As the number of spacefaring states, commercial operators, and satellite applications grows, demand for these resources increases. Efficient and equitable managing of these resources to ensure long-term availability requires international cooperation and coordination. THE RADIOFREQUENCY (RF) SPECTRUM Part of the electromagnetic spectrum that can pass through Earth’s atmosphere, the RF spectrum is used for communication between satellites and ground stations. That is, the spectrum is used not only by space-based users, but terrestrial users. It is divided into frequency bands. Frequency is generally measured in hertz, defined as cycles per second. Radio signals can also be characterized by their wavelength, which is the inverse of frequency. Higher frequencies (shorter wavelengths) can transmit more information than lower frequencies (longer wavelengths), but are more susceptible to degradation when travelling through the atmosphere. SSISPACE SECURITY INDEX RADIOFREQUENCY BANDS* BAND NAME FREQUENCY COMMON USES (ITU) ITU NATO** IEEE*** Space Ground Very High A Band (0-250 MHz) VHF 30-300 MHz Satellite uplinks Analog TV Frequency (FHV) UHF (300-1000 MHz) Analog TV, 2-way radio, Ultra High B Band (250-500 MHz) C Mobile satellite services, L Band (1-2 GHz) 300-3,000 MHz cordless phones, Wi-Fi, Frequency (UHF) Band (500-1,000 MHz) satellite navigation