Correlating Tensile Strength & Peak Temperatures for Magnesium Alloy
Total Page:16
File Type:pdf, Size:1020Kb
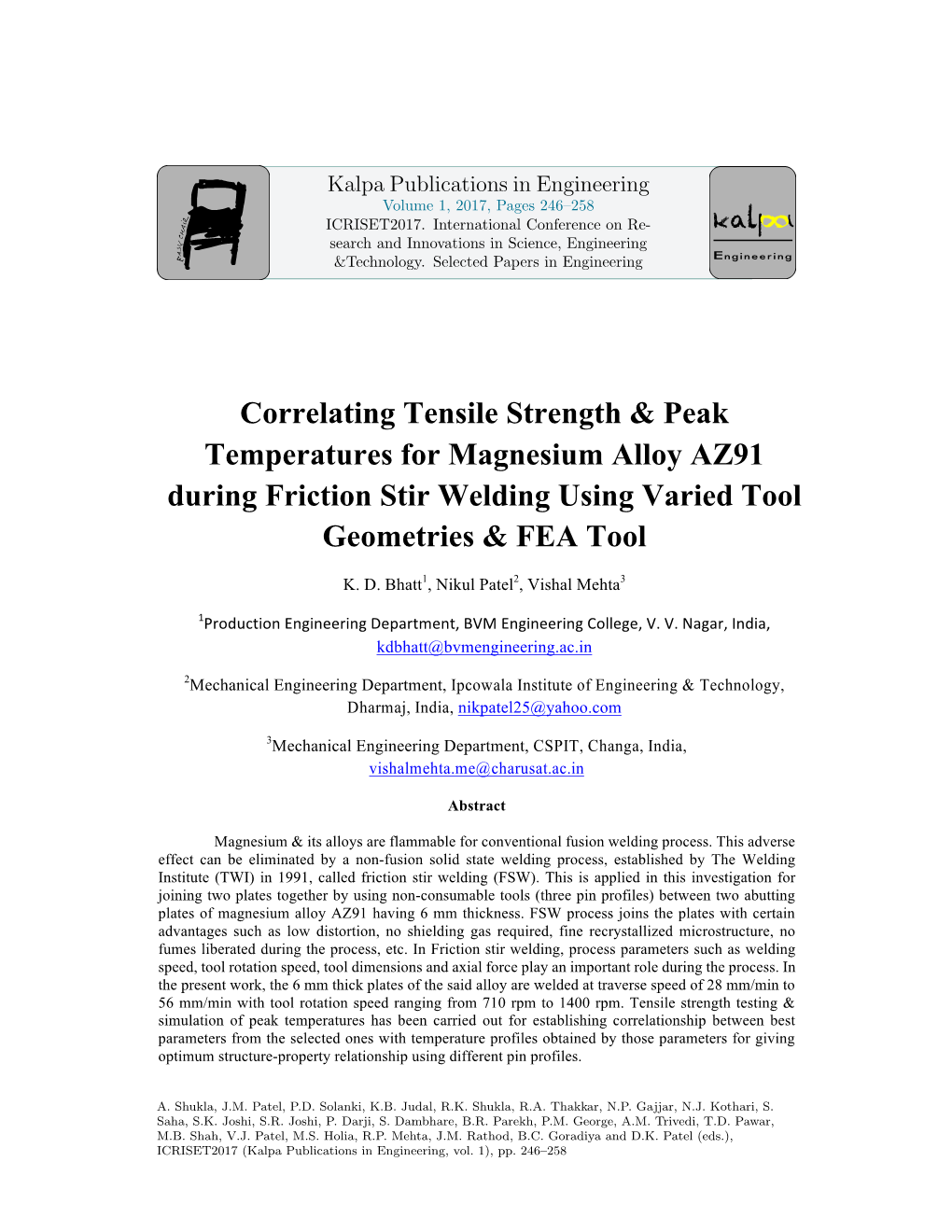
Load more
Recommended publications
-
Investigation of Mg and Zr Addition on the Mechanical Properties of Commercially Pure Al Samiul Kaiser, M
World Academy of Science, Engineering and Technology International Journal of Mechanical and Materials Engineering Vol:13, No:9, 2019 Investigation of Mg and Zr Addition on the Mechanical Properties of Commercially Pure Al Samiul Kaiser, M. S. Kaiser stable against particle coarsening. It causes additional Abstract—The influence of Mg and Zr addition on mechanical distribution of dislocations which pin grain boundaries and properties such as hardness, tensile strength and impact energy of inhibit recrystallization. The Al3Zr particles form from the commercially pure Al are investigated. The microstructure and melt as a primary phase during rapid solidification, act as fracture behavior are also studied by using Optical and Scanning nuclei for the solidification of Al, and Zr can thus operate as Electron Microscopy. It is observed that magnesium addition improves the mechanical properties of commercially pure Al at the grain refiner of Al [13]-[15]. Based on the above point of view, Mg is added to expense of ductility due to formation of β″ (Al3Mg) and β′ (Al3Mg2) phase into the alloy. Zr addition also plays a positive role through commercially pure Al used in this study to form the binary grain refinement effect and the formation of metastable alloy. The other element Zr is subsequently added with Mg to L12 Al3Zr precipitates. In addition, it is observed that the fractured study their mutual effect on the mechanical properties of cast surface of Mg added alloy is brittle and higher numbers of dimples Al at room temperatures. are observed in case of Zr added alloy. II. EXPERIMENTAL PROCEDURE Keywords—Al-alloys, hardness, tensile strength, impact energy, microstructure. -
X-Ray Diffraction Studies of 145 Mev Proton-Irradiated Albemet 162
X-Ray Diffraction Studies of 145 MeV proton-irradiated AlBeMet 162 Mohamed Elbakhshwan1, Kirk T. McDonald2, Sanjit Ghose3, Zhong Zhong3, Nikolaos Simos1,3* 1Nuclear Science and Technology Department, Brookhaven National Laboratory, Upton, NY 11973 2Joseph Henry Laboratories, Princeton University, Princeton, NJ 08544 3National Synchrotron Light Source II, Brookhaven National Laboratory, Upton, NY 11973 Abstract AlBeMet 162 (Materion Co., formerly Brush Wellman) has been irradiated with 145 MeV protons up to 1.2x1020 cm-2 fluence, with irradiation temperatures in the range of 100-220oC. Macroscopic post- irradiation evaluation on the evolution of mechanical and thermal properties was integrated with a comprehensive x-ray- diffraction study using high-energy monochromatic and polychromatic x-ray beams, which offered a microscopic view of the irradiation damage effects on AlBeMet. The study confirmed the stability of the metal-matrix composite, its resistance to proton damage, and the continuing separation of the two distinct phases, fcc aluminum and hcp beryllium, following irradiation. Furthermore, based on the absence of inter-planar distance change during proton irradiation, it was confirmed that the stacking faults and clusters on the Al (111) planes are stable, and thus can migrate from the cascade region and be absorbed at various sinks. XRD analysis of the unirradiated AlBeMet 162 showed clear change in the texture of the fcc phase with orientation especially in the Al (111) reflection which exhibits a “non-perfect” six-fold symmetry, implying lack of isotropy in the composite. * Corresponding author Tel.: +1 631 344 7229 E-mail address: [email protected] 1. Introduction AlBeMet, an aluminum-beryllium compound with high Be content, is better described as a metal-matrix composite rather than an alloy, since the two metals remain as separate phases. -
A Survey of Al7075 Aluminium Metal Matrix Composites
International Journal of Science and Research (IJSR) ISSN (Online): 2319-7064 Index Copernicus Value (2013): 6.14 | Impact Factor (2013): 4.438 A Survey of Al7075 Aluminium Metal Matrix Composites Rajendra .S .K1, Ramesha .C .M2 1Research Scholar, Jain University, Bengaluru, Department of Industrial Engineering and Management, Dr. Ambedkar Institute of Technology, Bengaluru 2Department of Mechanical Engineering, M S Ramaiah Institute of Technology, Bengaluru Abstract:A composite material is a combination of two or more chemically distinct and insoluble phases; its properties and structural performance are superior to those of the constituents acting independently. Metals and ceramics, as well, can be embedded with particles or fibers, to improve their properties; these combinations are known as Metal-Matrix composites. Aluminum 7075 alloy constitutes a very important engineering material widely employed in the aircraft and aerospace industry for the manufacturing of different parts and components. It is due to its high strength to density ratio that it a sought after metal matrix composite. In this paper we present a survey of Al 7075 Metal Matrix Composites. Keywords: Metal Matrix Composites (MMC’s), Aluminium Metal Matrix, Beryl, Al7075, Aluminium alloy 1. Introduction Aluminium alloy 7075 is an aluminium alloy, with zinc as the primary alloying element. It is strong, with a strength The effects of research in Aluminium based Metal Matrix comparable to many steels, and has good fatigue strength and Composites (MMC’s) are far reaching these days. These average machinability, but has less resistance to corrosion composites find various applications in the automobile than many other Al alloys. Its relatively high cost limits its industry, the aerospace industry and in defence and marine use to applications where cheaper alloys are not suitable. -
Turbulent Heat Transfer and Pressure Drop
DESIGN OPTIMIZATION OFMAGNETIC ALLOYS AND NICKEL-BASED SUPERALLOYS FOR HIGH TEMPERATURE APPLICATIONS Rajesh Jha George S. Dulikravich Department of Mechanical and Materials Engineering, MAIDROC Lab. Florida International University 10555 West Flagler Street, Miami, Florida 33174, U.S.A. [email protected], [email protected] Marcelo J. Colaço Department of Mechanical Engineering –POLI/COPPE Federal University of Rio de Janeiro - UFRJ Cidade Universitaria, Cx. Postal: 68503, Rio de Janeiro, RJ, 21941-972, Brazil [email protected] Abstract. Developing a new material or even improving properties of an existing material is a complex and time- consuming task. In recent years, materials scientists around the globe proposed a number of ways to speed up the alloy development process by using various computational tools. In this work, we made an attempt to demonstrate the efficacy of using computational tools in design optimization of materials, especially for high-temperature applications. We addressed two different material systems: Alnico alloys (magnetic) and Nickel-based superalloys. Alnico type alloys are hard magnetic alloys and well known for high-temperature applications. In this work, we defined the variable range of various elements and generated an initial set of alloys by a quasi-random sequence generation algorithm. These alloys were synthesized and tested for determining various material properties. We used a response surface methodology approach to develop surrogate models (meta-models) that approximately linked alloy chemistry with desired properties for these multi-component systems while being computationally affordable. These models were further used for multi-objective optimization of desired (conflicting) properties by using a number of algorithms based on evolutionary approaches, as well as our hybrid optimizer. -
Evolution of Microstructure During Recrystallization in As-Cast Aluminium - Magnesium Alloys with Ternary Titanium/ Zirconium Addition
ISSN(Online) : 2319 -8753 ISSN (Print) : 2347 -6710 International Journal of Innovative Research in Science, Engineering and Technology (An ISO 3297: 2007 Certified Organization) Vol. 4, Issue 10, October 2015 Evolution of Microstructure during Recrystallization in As-cast Aluminium - Magnesium Alloys with Ternary Titanium/ Zirconium Addition Abdullah Al Shafea, Sanjidah Akter Urmib, A. H. M. Azadur Rahmanb, Fahmida Gulshanc, ASW Kurnyd Research Engineer, Foundry Section, Department of Metallurgy, Walton Hi-Tech Industries Ltd, Chandra, Kaliakoir, Gazipur- 1750, Bangladesha Student, Department of Materials and Metallurgical Engineering, Bangladesh University of Engineering and Technology, Dhaka-1000, Bangladeshb Assistant Professor, Department of Materials and Metallurgical Engienering, Bangladesh University of Engineering and Technology, Dhaka-1000, Bangladeshc Professor, Department of Materials and Metallurgical Engineering, Bangladesh University of Engineering and Technology, Dhaka-1000, Bangladeshd ABSTRACT: The purpose of this research was to investigate the influence of Zirconium and Titanium on Al-5Mg alloy. Zirconium and Titanium in the range of 1.5-2wt% individually and combined have been added to Al-5Mg alloy by melt processing technique. The cast alloys were then subjected to investigation for their microstructure and mechanical properties.The evolution of microstructures during as cast condition was studied extensively using optical microscope (OM) which identifies the refining action of both Zr and Ti. Use of different kinds of etching reagent in the microstructural analysis showed different perspective results. The morphology of the intermetallic formed- Al3Zr and Al3Ti, the presence of dendrite structures and the relation of tensile strength on secondary dendritic arm spacing were studied. Use of Zr as third party material provides greater mechanical properties compared to Ti addition but Zr does not influence hardness as does the Ti alone. -
Read Journal
Online ISSN : 2249-4596 Print ISSN : 0975-5861 Land Observation Satellites An Algorithm for Integration Industrial Augmented Reality Properties of Recycled Materials VOLUME 14 ISSUE 7 VERSION 1.0 Global Journal of Researches in Engineering: J General Engineering Global Journal of Researches in Engineering: J General Engineering Volume 14 Issue 7 (Ver. 1.0) Open Association of Research Society © Global Journal of Global Journals Inc. Researches in Engineering. (A Delaware USA Incorporation with “Good Standing”; Reg. Number: 0423089) Sponsors: Open Association of Research Society 2014. Open Scientific Standards All rights reserved. Publisher’s Headquarters office This is a special issue published in version 1.0 of “Global Journal of Researches in Global Journals Headquarters Engineering.” By Global Journals Inc. All articles are open access articles distributed 301st Edgewater Place Suite, 100 Edgewater Dr.-Pl, under “Global Journal of Researches in Wakefield MASSACHUSETTS, Pin: 01880, Engineering” United States of America Reading License, which permits restricted use. Entire contents are copyright by of “Global USA Toll Free: +001-888-839-7392 Journal of Researches in Engineering” unless USA Toll Free Fax: +001-888-839-7392 otherwise noted on specific articles. No part of this publication may be reproduced Offset Typesetting or transmitted in any form or by any means, electronic or mechanical, including Global Journals Incorporated photocopy, recording, or any information storage and retrieval system, without written 2nd, Lansdowne, Lansdowne Rd., Croydon-Surrey, permission. Pin: CR9 2ER, United Kingdom The opinions and statements made in this book are those of the authors concerned. Packaging & Continental Dispatching Ultraculture has not verified and neither confirms nor denies any of the foregoing and Global Journals no warranty or fitness is implied. -
A Review on Effect of Tool Geometry on Mechanical Properties of Friction Stir Welding of AA 6082-T6 Mr
Vol-1 Issue-5 2015 IJARIIE-ISSN(O)-2395-4396 A Review On Effect of Tool Geometry on Mechanical Properties of Friction Stir Welding of AA 6082-T6 Mr. K.S Bhagwat1, Prof. Hredeya Mishra 2 1 PG Student, Mechanical Engineering Department, JCEI’SJaihind College of Engineering, Kuran- 410511 [MS], India. 2 Assistant Professor, Mechanical Engineering Department, JCEI’S Jaihind College of Engineering, Kuran- 410511 [MS], India. ABSTRACT Friction stir welding (FSW) is a novel solid state welding process for joining metallic alloys and has been employed in several industries such as aerospace and automotive for joining aluminum, magnesium and copper alloys. The various parameters such as rotational speed, welding speed, axial force and attack angle play vital role in FSW process in order to analyze the weld quality. The aim of this study is to investigate the effect of rotational speed, welding speed and tool pin profile on weld quality. Friction stir welds find use for structural and other fabrication industries. This report provides details of FSW equipment used and explains the effect of welding speed and rotational speed on the mechanical properties of butt joints in AA6082-T6 material of 5mm thickness for different tool profiles. Weld tensile strength was measured and influence of process parameters was assessed. The weld’s microstructure in various zones was analyzed using optical microscope. Microhardness measurements were performed on the weld’s cross-sections. As tool profile is vital, Special Design (SD) profiled pins were designed and manufactured for trials. The appearance of the weld was studied for surface defects and found to be small in weld nugget. -
Thermomechanical Ageing (TMA) of 2014 Aluminium Alloy for Aerospace Applications
Bull. Mater. Sci., Vol. 14, No. 1, February 1991, pp. 35-41. © Printed in India. Thermomechanical ageing (TMA) of 2014 aluminium alloy for aerospace applications S SINGH and D B GOEL Department of Metallurgical Engineering, University of Roorkee, Roorkee 247 667, India MS received 4 June 1990; revised 13 February 1991 Abstract. Various thermomechanical ageing (TMAJ treatments for 2014 Al-alloy have been developed which include partial peak ageing, warm rolling and further ageing to peak hardness at 160°C. Electron microscopic studies reveal that the TMA treatments affect substantially the ageing characteristics. The TMA-Ib treatment yields finest O' needles having longitudinal dimensions of ~400A,. TMA treatment leads to precipitate- dislocation network of different magnitudes. Among the TMA treatments, the TMA lib treatment results in thickest precipitate-dislocation tangles. In addition to 0', two types of dispersoids A14CuMgsSi,, and AI12(Fe, Mn)3Si have been observed. The density or concentration of these dispersoids is drastically reduced due to TMA treatments. Thus an optimum TMA treatment i.e. TMA-IIb has been developed which results in a significant improvement in the mechanical properties of 2014 Al-alloy. Keywords. Thermomechanical ageing; 2014 aluminium alloy. 1. Introduction The 2014 Al-alloy has a nominal composition: 4.40 Cu, 0-40 Mg, 0.80 Mn, 0.80 Si (Wt.%) and Fe as impurity element. Although this alloy has its own importance in the aircraft industry due to high hardness and high strength at room temperature, its effective application is significantly hampered because of the poor dynamic properties like fatigue strength and fracture toughness and tensile properties at elevated temperatures. -
Couplant Effect and Evaluation of FSW AA6061-T6 Butt Welded Joint
COPYRIGHT AND CITATION CONSIDERATIONS FOR THIS THESIS/ DISSERTATION o Attribution — You must give appropriate credit, provide a link to the license, and indicate if changes were made. You may do so in any reasonable manner, but not in any way that suggests the licensor endorses you or your use. o NonCommercial — You may not use the material for commercial purposes. o ShareAlike — If you remix, transform, or build upon the material, you must distribute your contributions under the same license as the original. How to cite this thesis Surname, Initial(s). (2012) Title of the thesis or dissertation. PhD. (Chemistry)/ M.Sc. (Physics)/ M.A. (Philosophy)/M.Com. (Finance) etc. [Unpublished]: University of Johannesburg. Retrieved from: https://ujcontent.uj.ac.za/vital/access/manager/Index?site_name=Research%20Output (Accessed: Date). Couplant Effect and Evaluation of FSW AA6061-T6 Butt Welded Joint By Itai Mumvenge 217093863 Submitted in partial fulfilment of the requirements for the degree of Master of Engineering in Mechanical Engineering In the Department of Mechanical Engineering Science Of the Faculty of Engineering and the Built Environment At the University of Johannesburg, South Africa Supervisor: Dr Stephen A. Akinlabi Co-Supervisor: Dr Peter M. Mashinini November, 2017 i 1. DEDICATION This dissertation is dedicated to my late grandmother Esnath Mvenge ii 2. COPYRIGHT STATEMENT The copyright of this dissertation is owned by the University of Johannesburg, South Africa. No information derived from this publication may be published without the author’s prior consent, unless correctly referenced. ………………………………….. 25 November 2017 Author’s Signature Date: iii 3. AUTHOR DECLARATION I, Mumvenge Itai hereby declare that the research work documented in this dissertation is my own, and no portion of the work has been submitted in support of an application for another degree or qualification at this or any other university or institute of learning. -
Guide to High Performance Alloys
Table of Contents Alloy Guide 3 The Alloys of Materion Brush Performance Alloys 4 Chemical Composition 6 Alloy Products 6 Physical Properties 8 Product Guide 10 Strip and Wire Temper Designations 11 Strip 12 Strip Product Specifications 13 Spring Bend Limits of Strip Alloys 19 Wire 20 Rod, Bar, Tube and Plate Temper Designations 22 Rod and Bar 22 Tube 26 Plate and Rolled Bar 29 MoldMAX® and PROtherm™ Plastic Tooling Alloys 31 ToughMet® and Alloy 25 Oilfield Products 32 Alloy 25 Drill String Temper (25 DST) 33 BrushCAST® Casting Ingot & Master Alloys 34 Forged and Extruded Finished Components 36 Cast Shapes 37 Recommended Replacements for Discontinued Alloys 38 Materion Brush Performance Alloys Value-Added Services 39 Custom Fabrication Capabilities 40 Customer Technical Service 40 Other Services 42 Processing and Fabrication Guide 43 Heat Treating Fundamentals 44 Forming of Strip 47 Cleaning and Finishing 50 Joining 51 Machining 53 Hardness 56 Microstructures 57 Other Attributes and Application Engineering Data 59 Fatigue Strength 60 Stress Relaxation Resistance 62 Corrosion Resistance 64 Magnetic Properties 67 Galling Resistance 68 Bearing Properties 69 Friction & Wear Properties 69 Resilience and Toughness 70 Elevated Temperature Properties 71 Cryogenic Properties 72 Other Attributes 72 Your Supplier 73 Company and Corporate History 74 Materion Corporate Profile 75 Brush Performance Alloys Mining & Manufacturing 77 Product Distribution 78 Customer Service 79 Quality 80 Health and Safety, Environment and Recycling 81 Alloy Guide The copper and nickel alloys commonly supplied in wrought product form are highlighted in this section. Wrought products are those in which final shape is achieved by working rather than by casting. -
The Development of Process Technology for the Friction Stir Welding of Thick Section Aluminium Alloys
U ìo The Development of Process Technology for the Friction Stir Welding of Thick Section Aluminium Alloys Rudolf Zetller School of Mechanical Engineering Faculty of Engineering, Computer and Mathematical Sciences University of Adelaide July 2006 CONTENTS Abstract 4 Statement of Originality. 6 Acknowledgements ....... 7 1.1 Background... .8 1.2 Significance.. 10 1.3 Objectives..... 10 2. Literature Review ..,12 2.1 Classification For Wrought Aluminium Alloys........ .12 2.2 Strengthening Mechanisms ln Heat-Treatable Aluminium Alloys ....... .13 2.3 Strengthening Mechanisms I n Non-Heat-Treatable Aluminium Alloys 16 2.3.1 Annealing 17 2.3.2 Recovery 1B 2.3.3 Recrystallization 18 2.3.4 Grain Growth 20 2.3.5 Solid-Solution Strengthening 20 2.4 Friction Welding (FW): A Process Overview 21 2.5 FW: Weld Structure And Weld Formation 23 2.6 Fusion Welding Aluminium 30 2.7 Friction Stir Welding (FSW): A Process Overview.. 34 2.8 FSW: Weld Structure And Weld Formation 3B 2.9 The Origins Of The FSW Tool For Joining Aluminium And lts Alloys 46 2.10 FSW And Tool Rubbing Velocity Relationships........... 48 2.11 Limitations Found To Exist For The Original FSW Tool Design........ 53 2.12 Modifications To The Original FSW Tool Pin Design 55 2.13 Forces Encountered When FSW 69 2.14 FSW: Process Modelling With Reference To Flow Visualisation...... 72 2.15 Summary Of Key Points From The Literature Review............ B6 3. Materials, Plant And Equipment 88 3.1 Wrought Aluminum Alloys - Composition and Temper 88 3.2 lnvestigated Wrought Al Alloys - Properties............... -
Elevated Temperature Properties of Extruded Aluminium Matrix
Research & Reviews: Journal of Material Sciences e-ISSN: 2321-6212 p-ISSN: 2347-2278 DOI: 10.4172/2321-6212.1000161 Elevated Temperature Properties of Extruded Aluminium Matrix Composites Reinforced with Nickel Coated Silicon Carbide Particles Dhanalakshmi S1*, Sundaram KS2, Balasubramanian M3, Sivakumar P1 1CVRDE, Ministry of Defence, DRDO, AVADI, Chennai, Tamil Nadu, India 2Department of Mechanical Engineering, College of Engineering Guindy, Anna University, Chennai, Tamil Nadu, India 3Department of Metallurgical and Materials Engineering, IIT Madras, Chennai, Tamil Nadu, India Research Article Received: 02/01/2017 ABSTRACT Accepted: 07/02/2017 The superior mechanical properties of Aluminium Matrix Published: 18/02/2017 Composites (AMC) together with the weight saving makes them attractive for a variety of engineering applications. They also have *For Correspondence improved mechanical properties at the operating conditions, such as high temperature, corrosive or wear environment, etc. This paper deals Dhanalakshmi S, CVRDE, Ministry of Defence, with the study of high temperature tensile properties of Al 2014-10 wt.% DRDO, AVADI, Chennai, Tamil Nadu, India, Tel: 040 SiC composites prepared using stir casting method. The cast billets were 26385112. extruded at 450°C with ram speed of 2 mm/s and extrusion ratio of 8:1. The optical microscopy and scanning electron microscopy analysis were Email: [email protected] carried out on the as-cast and extruded base alloy and the composites. The room temperature and high temperature tensile properties were evaluated. The results of this study show that the extrusion process Keywords: Aluminium matrix composite; Stir improves both the room temperature and high temperature strength of casting; Extrusion; High temperature tensile the base alloy and composites.