Design and Test of a Student Hybrid Rocket Engine with an External Carbon fiber Composite Structure
Total Page:16
File Type:pdf, Size:1020Kb
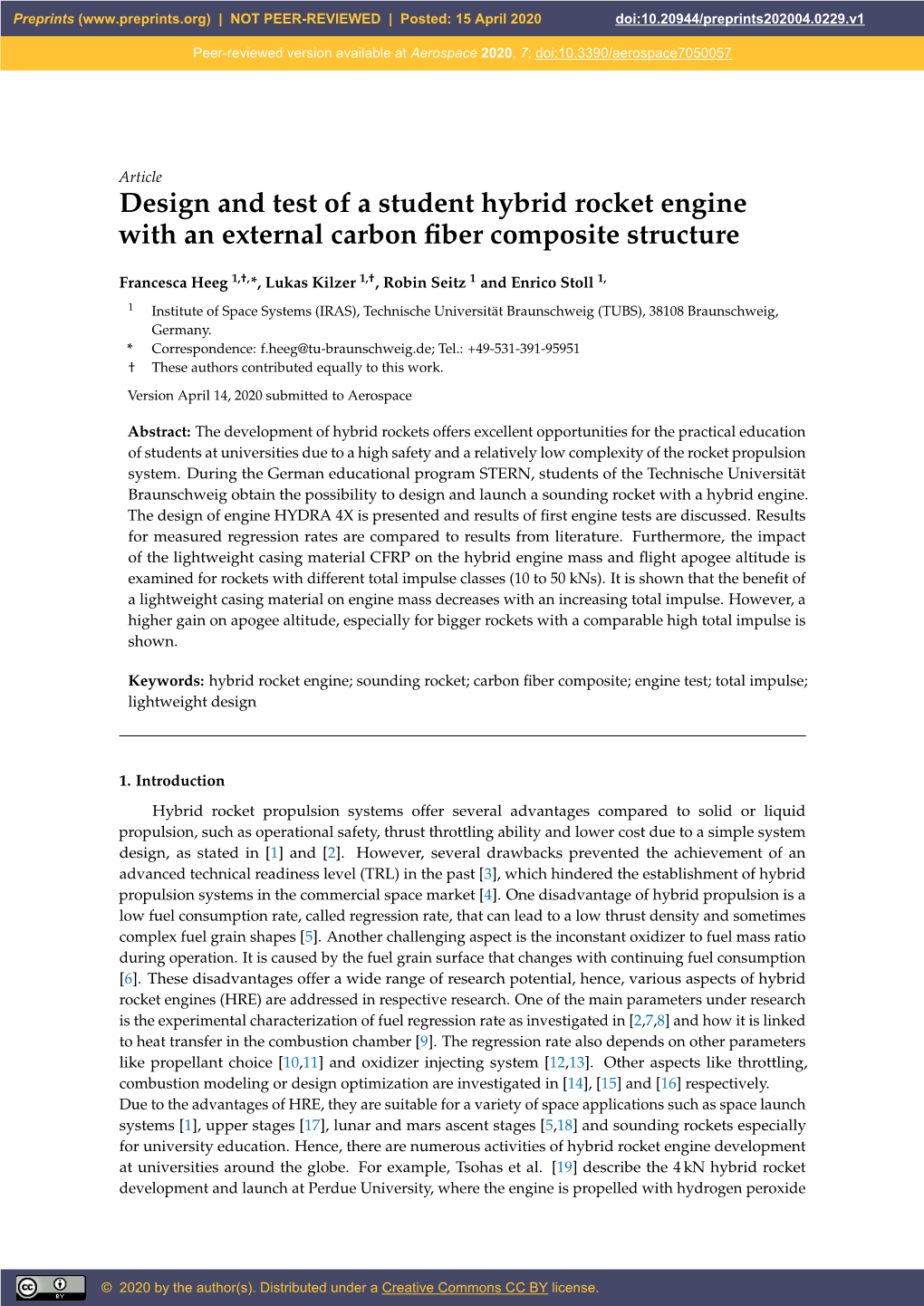
Load more
Recommended publications
-
Einicke Diplom.Pdf
Zum Erlangen des akademischen Grades DIPLOMINGENIEUR (Dipl.-Ing.) Betreuer: Dr. Christian Bach Verantwortlicher Hochschullehrer: Prof. Dr. techn. Martin Tajmar Tag der Einreichung: 20.04.2021 Erster Gutachter: Prof. Dr. techn. Martin Tajmar Zweiter Gutachter: Dr. Christian Bach Hiermit erkläre ich, dass ich die von mir dem Institut für Luft-und Raumfahrttechnik der Fakultät Maschinenwesen eingereichte Diplomarbeit zum Thema Mischungsverhältnis- und Brennkammerdruckregelung eines Expander-Bleed Raketentriebwerks mit Reinforcement Learning (Mixture Ratio and Combustion Chamber Pressure Control of an Expander-Bleed Rocket Engine with Reinforcement Learning) selbstständig verfasst und keine anderen als die angegebenen Quellen und Hilfsmittel benutzt sowie Zitate kenntlich gemacht habe. Berlin, 20.04.2021 Karina Einicke Contents Nomenclature iv Acronyms vii 1. Introduction 1 1.1. Motivation . .1 1.2. Objectives and Approach . .2 2. Fundamentals of Liquid Rocket Engines 3 2.1. Control Loops . .5 2.1.1. Open-Loop Control . .5 2.1.2. Closed-Loop Control . .5 2.1.3. Reusable Liquid Rocket Engine Control . .6 2.2. Control Valves . .8 2.2.1. Flow Characteristics . .9 2.2.2. Valve Types . .9 2.3. Liquid Rocket Engine Control: Historical Background . 11 2.4. Summary . 13 3. LUMEN 15 3.1. LUMEN Components . 15 3.2. Operating Points . 17 3.3. EcosimPro/ESPSS Model . 18 3.3.1. LUMEN System Analysis . 21 3.3.2. LUMEN System Validation . 26 3.4. Summary . 27 4. Reinforcement Learning 28 4.1. Fundamentals of Reinforcement Learning . 28 4.2. Reinforcement Learning Algorithms . 31 4.2.1. Model-based and Model-free Reinforcement Learning . 31 4.2.2. Policy Optimization . -
Design of a 500 Lbf Liquid Oxygen and Liquid Methane Rocket Engine for Suborbital Flight Jesus Eduardo Trillo University of Texas at El Paso, [email protected]
University of Texas at El Paso DigitalCommons@UTEP Open Access Theses & Dissertations 2016-01-01 Design Of A 500 Lbf Liquid Oxygen And Liquid Methane Rocket Engine For Suborbital Flight Jesus Eduardo Trillo University of Texas at El Paso, [email protected] Follow this and additional works at: https://digitalcommons.utep.edu/open_etd Part of the Aerospace Engineering Commons, and the Mechanical Engineering Commons Recommended Citation Trillo, Jesus Eduardo, "Design Of A 500 Lbf Liquid Oxygen And Liquid Methane Rocket Engine For Suborbital Flight" (2016). Open Access Theses & Dissertations. 767. https://digitalcommons.utep.edu/open_etd/767 This is brought to you for free and open access by DigitalCommons@UTEP. It has been accepted for inclusion in Open Access Theses & Dissertations by an authorized administrator of DigitalCommons@UTEP. For more information, please contact [email protected]. DESIGN OF A 500 LBF LIQUID OXYGEN AND LIQUID METHANE ROCKET ENGINE FOR SUBORBITAL FLIGHT JESUS EDUARDO TRILLO Master’s Program in Mechanical Engineering APPROVED: Ahsan Choudhuri, Ph.D., Chair Norman Love, Ph.D. Luis Rene Contreras, Ph.D. Charles H. Ambler, Ph.D. Dean of the Graduate School Copyright © by Jesus Eduardo Trillo 2016 DESIGN OF A 500 LBF LIQUID OXYGEN AND LIQUID METHANE ROCKET ENGINE FOR SUBORBITAL FLIGHT by JESUS EDUARDO TRILLO, B.S.ME THESIS Presented to the Faculty of the Graduate School of The University of Texas at El Paso in Partial Fulfillment of the Requirements for the Degree of MASTER OF SCIENCE Department of Mechanical Engineering THE UNIVERSITY OF TEXAS AT EL PASO December 2016 Acknowledgements Foremost, I would like to express my sincere gratitude to my advisor Dr. -
UCLA Electronic Theses and Dissertations
UCLA UCLA Electronic Theses and Dissertations Title Minimizing hydraulic losses in additively-manufactured swirl coaxial rocket injectors via analysis-driven design methods Permalink https://escholarship.org/uc/item/7n51c078 Author Morrow, David Publication Date 2020 Peer reviewed|Thesis/dissertation eScholarship.org Powered by the California Digital Library University of California UNIVERSITY OF CALIFORNIA Los Angeles Minimizing hydraulic losses in additively-manufactured swirl coaxial rocket injectors via analysis-driven design methods A thesis submitted in partial satisfaction of the requirements for the degree Master of Science in Aerospace Engineering by David Morrow 2020 c Copyright by David Morrow 2020 ABSTRACT OF THE THESIS Minimizing hydraulic losses in additively-manufactured swirl coaxial rocket injectors via analysis-driven design methods by David Morrow Master of Science in Aerospace Engineering University of California, Los Angeles, 2020 Professor Raymond M. Spearrin, Chair Additive manufacturing (AM) has matured significantly over the past decade and become a highly attractive tool for reducing manufacturing complexity and removing traditional de- sign constraints. This is particularly desirable for rocket combustion devices which often feature hundreds of individual parts with precise tolerances. The degree to which AM can be used to improve combustion device performance, however, has been less rigorously ex- plored. In this work, hydraulic performance impacts associated with and enabled by AM are assessed for a liquid bi-propellant swirl coaxial injector. Specifically, a single-element liquid oxygen/kerosene injector based on a canonical design was manufactured from inconel using Direct Metal Laser Sintering at two different coaxial recess depths. Cold-flow testing for the as-manufactured baseline injector found a reduction in the designed discharge coefficients, which is primarily attributed to increased surface roughness inherent in the AM process. -
Ideas Into Hardware: a History of the Rocket Engine Test Facility
Ideas Into Hardware IDEAS INTO HARDWARE A History of the Rocket Engine Test Facility at the NASA Glenn Research Center Virginia P. Dawson National Aeronautics and Space Administration NASA Glen Research Center Cleveland, Ohio 2004 This document was generated for the NASA Glenn Research Center, in accor- dance with a Memorandum of Agreement among the Federal Aviation Administration, National Aeronautics and Space Administration (NASA), The Ohio State Historic Preservation Officer, and the Advisory Council on Historic Preservation. The City of Cleveland’s goal to expand the Cleveland Hopkins International Airport required the NASA Glenn Research Center’s Rocket Engine Test Facility, located adjacent to the airport, to be removed before this expansion could be realized. To mitigate the removal of this registered National Historic Landmark, the National Park Service stipulated that the Rocket Engine Test Facility be documented to Level I standards of the Historic American Engineering Record (HAER). This history project was initiated to fulfill and supplement that requirement. Produced by History Enterprises, Inc. Cover and text design by Diana Dickson. Library of Congress Cataloging-in-Publication Data Dawson, Virginia P. (Virginia Parker) —Ideas into hardware : a history of NASA’s Rocket Engine Test Facility / by Virginia P. Dawson. ——p.——cm. —Includes bibliographical references. —1. Rocket engines—Research—United States—History.—2.—United States. National Aeronautics and Space Administration—History.—I. Title. TL781.8.U5D38 2004 621.43'56'072077132—dc22 2004024041 Table of Contents Introduction / v 1. Carving Out a Niche / 1 2. RETF: Complex, Versatile, Unique / 37 3. Combustion Instability and Other Apollo Era Challenges, 1960s / 64 4. -
Extensions to the Time Lag Models for Practical Application to Rocket
The Pennsylvania State University The Graduate School College of Engineering EXTENSIONS TO THE TIME LAG MODELS FOR PRACTICAL APPLICATION TO ROCKET ENGINE STABILITY DESIGN A Dissertation in Mechanical Engineering by Matthew J. Casiano © 2010 Matthew J. Casiano Submitted in Partial Fulfillment of the Requirements for the Degree of Doctor of Philosophy August 2010 The dissertation of Matthew J. Casiano was reviewed and approved* by the following: Domenic A. Santavicca Professor of Mechanical Engineering Co-chair of Committee Vigor Yang Adjunct Professor of Mechanical Engineering Dissertation Advisor Co-chair of Committee Richard A. Yetter Professor of Mechanical Engineering André L. Boehman Professor of Fuel Science and Materials Science and Engineering Tomas E. Nesman Aerospace Engineer at NASA Marshall Space Flight Center Special Member Karen A. Thole Professor of Aerospace Engineering Head of the Department of Mechanical and Nuclear Engineering *Signatures are on file in the Graduate School iii ABSTRACT The combustion instability problem in liquid-propellant rocket engines (LREs) has remained a tremendous challenge since their discovery in the 1930s. Improvements are usually made in solving the combustion instability problem primarily using computational fluid dynamics (CFD) and also by testing demonstrator engines. Another approach is to use analytical models. Analytical models can be used such that design, redesign, or improvement of an engine system is feasible in a relatively short period of time. Improvements to the analytical models can greatly aid in design efforts. A thorough literature review is first conducted on liquid-propellant rocket engine (LRE) throttling. Throttling is usually studied in terms of vehicle descent or ballistic missile control however there are many other cases where throttling is important. -
Propulsion Engineering Research Center
https://ntrs.nasa.gov/search.jsp?R=19940018555 2020-06-16T15:54:43+00:00Z PROPULSION ENGINEERING RESEARCH CENTER [! - -- - - n I [I 1993 ANNUAL REPORT VOLUME II 0 NOVEMBER, 1993 [I oio P4 m3mm 50 - - R - - -- A UNIVERSITY SPACE ENGINEERING RESEARCH CENTER FIFTH AMNUAL SYMPOSIUM SEPTEMBER 8-9: 1993 106 RESEARCH BUILDING EAST rloweu rn kZX m *w3- UNIVERSITY PARK, PENNSYLVANIA 16801 OI AC 4zom NASA PROPULSION ENGINEERING RESEARCH CENTER ANNUAL REPORT 1993 VOLUME II FIFIH ANNUAL SYMPOSIUM SEPTEMBER &9,1993 THE PENNSYLVANIA STATE UNIVERSITY UNIVERSITY PARK, PA THE PENNSYLVANIA STATE UNIVERSITY UNIVERSITY PARK, PA WBLE OF CONTENTS Sumary.. ......................................................................................................................... Technical Program............................................................................................................ by Image Deconvolution .................................................................................................. Small Rocket Flowfield Diagnostic Chambers................................................................. A Theoretical Evaluation of Aluminum Gel Propellant Two-Phase Flow Losses on Vehicle Performance................................................................................................... Laser Diagnostics for Small Rockets................................................................................ CFD Analyses of Combustor and Nozzle Flowfields....................................................... LOX Droplet Vaporization -
Three Phases of Low-Cost Rocket Engine Demonstration Program
Three Phases of Low-Cost Rocket Engine Demonstration Program Completed The NASA Lewis Research Center and the TRW Space & Technology Group have successfully completed three phases of testing on the Low-Cost Rocket Engine Demonstration Program. TRW and the McDonnell Douglas Corporation are working, in a joint effort, to quickly develop and produce a highly stable, inexpensive, simple, yet reliable, expendable launch vehicle. Studies have shown that this launch system is required to maintain U.S. viability to space access in the face of growing foreign competition. For the U.S. commercial launch industry to remain competitive, a low-cost launch vehicle must be developed to place payloads into low-Earth orbit. Trade studies performed by McDonnell Douglas and TRW have shown that a low-cost, commercial, expendable launch vehicle could be designed that uses low-pressure turbopumps and rocket combustors. These studies show that expensive high-performance technology can be sacrificed for inexpensive lower performance technology and still meet mission requirements. Because the propulsion system is more than half of a launch vehicle's cost, TRW proposed the pintle injector engine design used in the Apollo Program--the lunar module descent engine. TRW's pintle injector engine, which runs on liquid hydrogen or RP-1 fuels and liquid oxygen oxidizer, uses modified low-pressure turbopumps to supply the propellants. The engine consists of a centrally located, coaxial injector; an ablative liner for insulating the metal surfaces of the combustion chamber and nozzle; and annular sleeves to throttle the propellant feeds. Lewis and TRW entered into a Space Act Agreement to demonstrate that the pintle injector can operate at acceptable stable performance levels and to demonstrate the life of a low-cost, combustion chamber with an ablative lining. -
딥 스로틀링 가변 슬리브 인젝터의 추력제어 성능예측 Prediction On
韓國航空宇宙學會誌 487 論文 J. of The Korean Society for Aeronautical and Space Sciences 46(6), 487-495(2018) DOI:https://doi.org/10.5139/JKSAS.2018.46.6.487 ISSN 1225-1348(print), 2287-6871(online) 딥 스로틀링 가변 슬리브 인젝터의 추력제어 성능예측 박선정*, 남정수*, 이건웅*, 구자예**, 황용석*** Prediction on Throttling Performance of a Movable Sleeve Injector for Deep Throttling Sunjung Park*, Jeongsoo Nam*, Keonwoong Lee*, Jaye Koo** and Yongsok Hwang*** Department of Aerospace Mechanical Engineering, Korea Aerospace University* School of Aerospace Mechanical Engineering, Korea Aerospace University** Agency of Defense Development*** ABSTRACT Experimental analysis of the spray characteristics of the movable sleeve injector, which can simultaneously control the area of the annular gap and the pintle gap, has been studied and a method for controlling the uniform performance over a wide thrust range has been studied. It is confirmed that the design flow rate is not satisfied when the constant pressure difference is set regardless of the opening distance of the sleeve. In order to improve this, the differential pressure in the annular gap and the pintle gap was applied differently according to the opening distance. It was confirmed that the design flow rate was satisfied within the operating range and thrust control was linear from 25% to 100% in linear sleeve area. 초 록 환형 갭과 핀틀갭의 면적을 동시에 제어할 수 있는 가변 슬리브 인젝터의 분무특성을 실 험적으로 분석하고, 넓은 추력범위에서 일정한 성능으로 제어할 수 있는 방안을 연구하였 다. 슬리브의 개도에 관계없이 일정한 차압을 설정한 경우 설계유량을 만족하지 못하는 것 을 확인하였다. 이를 개선하기 위해 개도에 따라 환형 갭과 핀틀 갭에서의 차압을 개도에 따라 다르게 적용하였다. -
Electric Feed Systems for Liquid-Propellant Rockets
Research Report. ELECTRIC FEED SYSTEMS FOR LIQUID PROPELLANT ROCKET ENGINES. Pablo Rachov, Hernán Tacca y Diego Lentini. Cita: Pablo Rachov, Hernán Tacca y Diego Lentini (2010). ELECTRIC FEED SYSTEMS FOR LIQUID PROPELLANT ROCKET ENGINES. Research Report. Dirección estable: https://www.aacademica.org/hernan.emilio.tacca/9 Esta obra está bajo una licencia de Creative Commons. Para ver una copia de esta licencia, visite http://creativecommons.org/licenses/by-nc-nd/4.0/deed.es. Acta Académica es un proyecto académico sin fines de lucro enmarcado en la iniciativa de acceso abierto. Acta Académica fue creado para facilitar a investigadores de todo el mundo el compartir su producción académica. Para crear un perfil gratuitamente o acceder a otros trabajos visite: http://www.aacademica.org. RESEARCH REPORTS ELECTRIC FEED SYSTEMS FOR LIQUID PROPELLANT ROCKET ENGINES Pablo RACHOV LABORATORIO DE CONTROL DE ACCIONAMIENTOS, TRACCIÓN Y POTENCIA (LABCATYP) Departamento de Electrónica Facultad de Ingeniería UNIVERSIDAD DE BUENOS AIRES Directors: Prof. Hernán TACCA, University of Buenos Aires, Argentina Prof. Diego LENTINI, University of Roma “La Sapienza”, Italy Buenos Aires, December 6th, 2010. DOI: 10.13140/2.1.4431.9042 Comparison of Liquid Propellant Rocket Engine Feed Systems - 1 - 1 REPORT N o 1 COMPARISON OF LIQUID PROPELLANT ROCKET ENGINE FEED SYSTEMS Pablo RACHOV LABORATORIO DE CONTROL DE ACCIONAMIENTOS, TRACCIÓN Y POTENCIA (LABCATYP) Departamento de Electrónica Facultad de Ingeniería UNIVERSIDAD DE BUENOS AIRES Directors: Prof. Hernán TACCA, University of Buenos Aires, Argentine Prof. Diego LENTINI, University of Roma “La Sapienza”, Italy Buenos Aires, December 6th, 2010. Comparison of Liquid Propellant Rocket Engine Feed Systems - 1 - 2 CONTENTS I. -
Generative Adversarial Networks with Physical Evaluators for Spray Simulation of Pintle Injector
Generative Adversarial Networks with Physical Evaluators for Spray Simulation of Pintle Injector Hao Maa, Botao Zhangb, Chi Zhangc, Oskar J. Haidna,∗ aDepartment of Aerospace and Geodesy, Technical University of Munich, 85748 Garching, Germany bKey Laboratory for Liquid Rocket Engine Technology, Xi'an Aerospace Propulsion Institute, 710100 Xi'an, China cDepartment of Mechanical Engineering, Technical University of Munich, 85748 Garching, Germany Abstract Due to the adjustable geometry, pintle injectors are specially suitable for the liq- uid rocket engines which require a widely throttleable range. While applying the conventional computational fluid dynamics approaches to simulate the complex spray phenomena in the whole range still remains to be a great challenge. In this paper, a novel deep learning approach used to simulate instantaneous spray fields under continuous operating conditions is explored. Based on one specific type of neural networks and the idea of physics constraint, a Generative Ad- versarial Networks with Physics Evaluators (GAN-PE) framework is proposed. The geometry design and mass flux information are embedded as the inputs. After the adversarial training between the generator and discriminator, the gen- erated field solutions are fed into the two physics evaluators. In this framework, mass conversation evaluator is designed to improve the training robustness and convergence. And the spray angle evaluator, which is composed of a down- sampling CNN and theoretical model, guides the networks generating the spray solutions more according with the injection conditions. The characterization of the simulated spray, including the spray morphology, droplet distribution and arXiv:2101.01217v1 [physics.flu-dyn] 27 Dec 2020 spray angle, is well predicted. The work suggests a great potential of the prior ∗Corresponding author. -
Disrupting Launch Systems
DISRUPTING LAUNCH SYSTEMS THE RISE OF SPACEX AND EUROPEAN ACCESS TO SPACE Thesis submitted to the International Space University in partial fulfillment of the requirements of the M. Sc. Degree in Space Studies August 2017 Thesis author: Paul Wohrer Thesis supervisor: Prof. Jean-Jacques Favier International Space University 1 Abstract The rise of SpaceX as a major launch provider has been the most surprising evolution of the launch sector during the past decade. It forced incumbent industrial actors to adapt their business model to face this new competitor. European actors are particularly threatened today, since European Autonomous Access to Space highly depends on the competitive edge of the Ariane launcher family. This study argues that the framework of analysis which best describes the events leading to the current situation is the theory of disruptive innovation. The study uses this framework to analyse the reusability technology promoted by new actors of the launch industry. The study argues that, while concurring with most analysis that the price advantage of reused launchers remains questionable, the most important advantage of this technology is the convenience it could confer to launch systems customers. The study offers two recommendations to European actors willing to maintain European Autonomous Access to Space. The first one aims at allocating resources toward a commercial exploitation of the Vega small launch system, to disrupt the growing market of small satellites and strengthen ties with Italian partners in the launcher program. The second aims at increasing the perception of European launchers as strategic assets, to avoid their commoditization. The recommendation entails developing an autonomous European capacity to launch astronauts into space, which could strengthen the ties between France and Germany as well as lead to a rationalization of the geo-return principle. -
Overview of Combustion Instabilities in Liquid-Propellant Rocket Engines
Chapter 1 Overview of Combustion Instabilities in Liquid-Propellant Rocket Engines Fred E. C. Culick* California Institute of Technology, Pasadena, California 91125 and Vigor Yangt Pennsylvania State University, University Park, Pennsylvania 16802 I. Introduction OMBUSTION instabilities were discovered in solid- and liquid-propellant C rocket engines at about the same time in the late 1930s. Since then, unsta ble oscillations have occurred in most, if not practically all, new development programs. Indeed, because of the high density of energy release in a volume hav ing relatively low losses, conditions normally favor excitation and sustenance of oscillations in any combustion chamber intended for a propulsion system. Figure 1 is an abbreviated chronology of some major events and features of the subject during the past 50 years. In one form or another, combustion instabilities have been under continuous study during all of that period. In time, however, the emphasis naturally has shifted, depending on what sort of full-scale systems experienced difficulties. During World War II in the United States, it seems that virtually all work in this subject was concerned with elimination of high-frequency resonant burning (the term used at the time) in small tactical solid rocket motors. The common treatment was usually a form of passive control, involving installation of baffles, resonance rods, or some other modification of geometry. Since then, the need to solve problems of instabilities in solid rockets has continued for motors of all sizes. Much of the basic understanding that has been gained is applicable to liquid rockets, despite the obvious differences in the systems.