Simulation Tools Used in the Analysis of Aircraft Handling Systems for Safe Embarked Operation
Total Page:16
File Type:pdf, Size:1020Kb
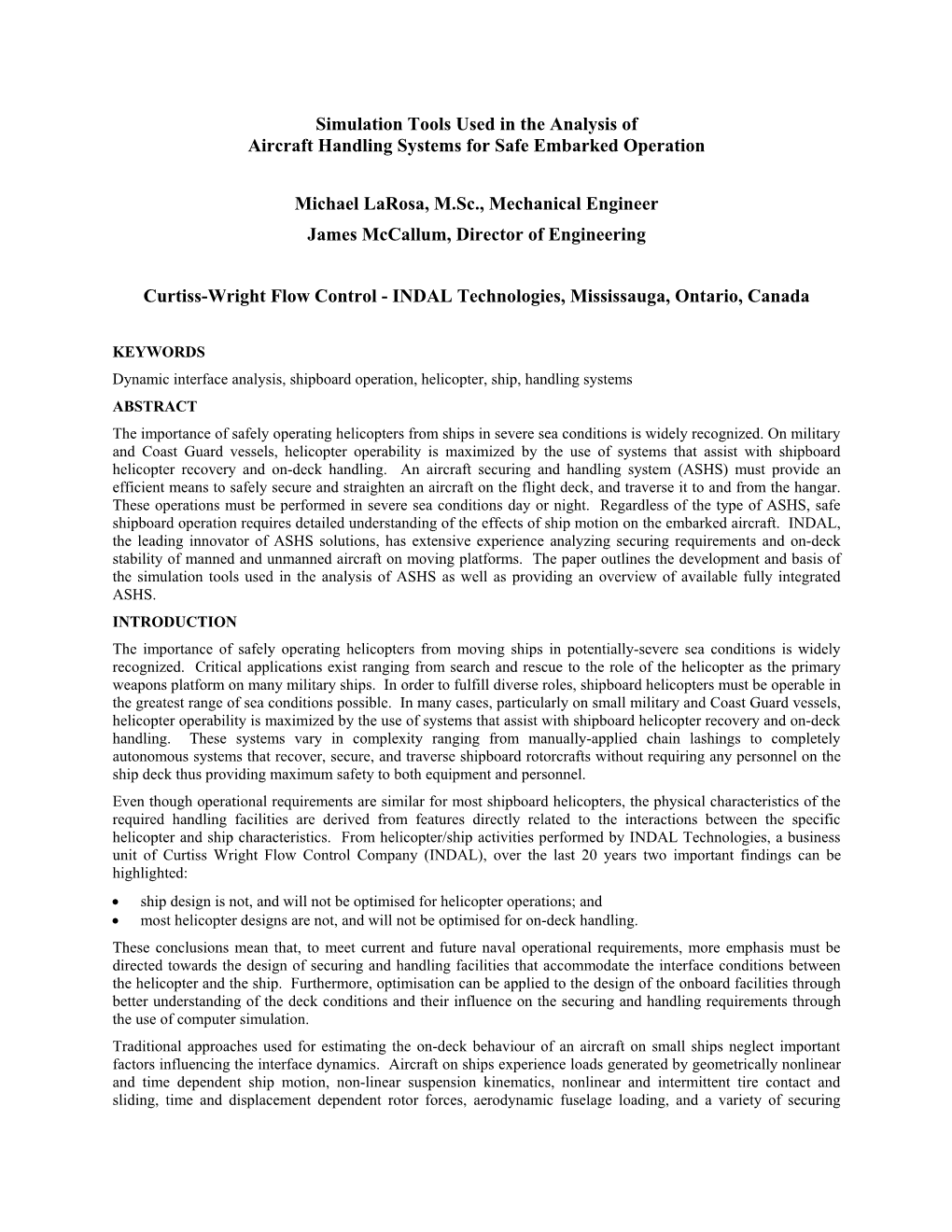
Load more
Recommended publications
-
Helicopter Dynamics Concerning Retreating Blade Stall on a Coaxial Helicopter
Helicopter Dynamics Concerning Retreating Blade Stall on a Coaxial Helicopter A project presented to The Faculty of the Department of Aerospace Engineering San José State University In partial fulfillment of the requirements for the degree Master of Science in Aerospace Engineering by Aaron Ford May 2019 approved by Prof. Jeanine Hunter Faculty Advisor © 2019 Aaron Ford ALL RIGHTS RESERVED ABSTRACT Helicopter Dynamics Concerning Retreating Blade Stall on a Coaxial Helicopter by Aaron Ford A model of helicopter blade flapping dynamics is created to determine the occurrence of retreating blade stall on a coaxial helicopter with pusher-propeller in straight and level flight. Equations of motion are developed, and blade element theory is utilized to evaluate the appropriate aerodynamics. Modelling of the blade flapping behavior is verified against benchmark data and then used to determine the angle of attack distribution about the rotor disk for standard helicopter configurations utilizing both hinged and hingeless rotor blades. Modelling of the coaxial configuration with the pusher-prop in straight and level flight is then considered. An approach was taken that minimizes the angle of attack and generation of lift on the advancing side while minimizing them on the retreating side of the rotor disk. The resulting asymmetric lift distribution is compensated for by using both counter-rotating rotor disks to maximize lift on their respective advancing sides and reduce drag on their respective retreating sides. The result is an elimination of retreating blade stall in the coaxial and pusher-propeller configuration. Finally, an assessment of the lift capability of the configuration at both sea level and at “high and hot” conditions were made. -
Micro Coaxial Helicopter Controller Design
Micro Coaxial Helicopter Controller Design A Thesis Submitted to the Faculty of Drexel University by Zelimir Husnic in partial fulfillment of the requirements for the degree of Doctor of Philosophy December 2014 c Copyright 2014 Zelimir Husnic. All Rights Reserved. ii Dedications To my parents and family. iii Acknowledgments There are many people who need to be acknowledged for their involvement in this research and their support for many years. I would like to dedicate my thankfulness to Dr. Bor-Chin Chang, without whom this work would not have started. As an excellent academic advisor, he has always been a helpful and inspiring mentor. Dr. B. C. Chang provided me with guidance and direction. Special thanks goes to Dr. Mishah Salman and Dr. Humayun Kabir for their mentorship and help. I would like to convey thanks to my entire thesis committee: Dr. Chang, Dr. Kwatny, Dr. Yousuff, Dr. Zhou and Dr. Kabir. Above all, I express my sincere thanks to my family for their unconditional love and support. iv v Table of Contents List of Tables ........................................... viii List of Figures .......................................... ix Abstract .............................................. xiii 1. Introduction .......................................... 1 1.1 Vehicles to be Discussed................................... 1 1.2 Coaxial Benefits ....................................... 2 1.3 Motivation .......................................... 3 2. Helicopter Flight Dynamics ................................ 4 2.1 Introduction ........................................ -
Development of a Helicopter Vortex Ring State Warning System Through a Moving Map Display Computer
Calhoun: The NPS Institutional Archive Theses and Dissertations Thesis Collection 1999-09 Development of a helicopter vortex ring state warning system through a moving map display computer Varnes, David J. Monterey, California. Naval Postgraduate School http://hdl.handle.net/10945/26475 DUDLEY KNOX LIBRARY NAVAL POSTGRADUATE SCHOOL MONTEREY CA 93943-5101 NAVAL POSTGRADUATE SCHOOL Monterey, California THESIS DEVELOPMENT OF A HELICOPTER VORTEX RING STATE WARNING SYSTEM THROUGH A MOVING MAP DISPLAY COMPUTER by David J. Varnes September 1999 Thesis Advisor: Russell W. Duren Approved for public release; distribution is unlimited. Public reporting burden for this collection of information is estimated to average 1 hour per response, including the time for reviewing instruction, searching existing data sources, gathering and maintaining the data needed, and completing and reviewing the collection of information. Send comments regarding this burden estimate or any other aspect of this collection of information, including suggestions for reducing this burden, to Washington headquarters Services, Directorate for Information Operations and Reports, 1215 Jefferson Davis Highway, Suite 1204, Arlington. VA 22202-4302, and to the Office of Management and Budget. Paperwork Reduction Project (0704-0188) Washington DC 20503. REPORT DOCUMENTATION PAGE Form Approved OMB No. 0704-0188 2. REPORT DATE 3. REPORT TYPE AND DATES COVERED 1. agency use only (Leave blank) September 1999 Master's Thesis 4. TITLE AND SUBTITLE 5. FUNDING NUMBERS DEVELOPMENT OF A HELICOPTER VORTEX RING STATE WARNING SYSTEM THROUGH A MOVING MAP DISPLAY COMPUTER 6. AUTHOR(S) Varnes, David, J. 7. PERFORMING ORGANIZATION NAME(S) AND ADDRESS(ES) PERFORMING ORGANIZATION Naval Postgraduate School REPORT NUMBER Monterey, CA 93943-5000 10. -
Robot Dynamics Rotary Wing UAS: Introduction Design and Aerodynamics
Robot Dynamics Rotary Wing UAS: Introduction Design and Aerodynamics 151-0851-00 V Marco Hutter, Roland Siegwart and Thomas Stastny Autonomous Systems Lab Robot Dynamics - Rotary Wing UAS: Propeller Analysis and Dynamic Modeling| 27.10.2015 | 1 Contents | Rotary Wing UAS 1. Introduction - Design and Propeller Aerodynamics 2. Propeller Analysis and Dynamic Modeling 3. Control of a Quadrotor 4. Rotor Craft Case Study Autonomous Systems Lab Robot Dynamics - Rotary Wing UAS: Propeller Analysis and Dynamic Modeling| 27.10.2015 | 2 Introduction Rotary Wing UAS: Introduction Design and Aerodynamics Autonomous Systems Lab Robot Dynamics - Rotary Wing UAS: Propeller Analysis and Dynamic Modeling| 27.10.2015 | 3 Rotorcraft: Definition . Rotorcraft: Aircraft which produces lift from a rotary wing turning in a plane close to horizontal “A helicopter is a collection of vibrations held together by differential equations” John Watkinson Advantage Disadvantage Ability to hover High maintenance costs Power efficiency during hover Poor efficiency in forward flight “If you are in trouble anywhere, an airplane can fly over and drop flowers, but a helicopter can land and save your life” Igor Sikorsky Autonomous Systems Lab Robot Dynamics: Rotary Wing UAS| 07.11.2016 | 4 Rotorcraft | Overview on Types of Rotorcraft Helicopter Autogyro Gyrodyne Power driven main rotor Un-driven main rotor, tilted Power driven main propeller away The air flows from TOP to The air flows from BOTTOM The air flows from TOP to BOTTOM to TOP BOTTOM Tilts its main rotor to fly Forward -
The Pennsylvania State University
The Pennsylvania State University The Graduate School Department of Aerospace Engineering REAL-TIME PATH PLANNING AND AUTONOMOUS CONTROL FOR HELICOPTER AUTOROTATION A Dissertation in Aerospace Engineering by Thanan Yomchinda 2013 Thanan Yomchinda Submitted in Partial Fulfillment of the Requirements for the Degree of Doctor of Philosophy May 2013 The dissertation of Thanan Yomchinda was reviewed and approved* by the following: Joseph F. Horn Associate Professor of Aerospace Engineering Dissertation Co-Advisor Co-Chair of Committee Jacob W. Langelaan Associate Professor of Aerospace Engineering Dissertation Co-Advisor Co-Chair of Committee Edward C. Smith Professor of Aerospace Engineering Christopher D. Rahn Professor of Mechanical Engineering George A. Lesieutre Professor of Aerospace Engineering Head of the Department of Aerospace Engineering *Signatures are on file in the Graduate School iii ABSTRACT Autorotation is a descending maneuver that can be used to recover helicopters in the event of total loss of engine power; however it is an extremely difficult and complex maneuver. The objective of this work is to develop a real-time system which provides full autonomous control for autorotation landing of helicopters. The work includes the development of an autorotation path planning method and integration of the path planner with a primary flight control system. The trajectory is divided into three parts: entry, descent and flare. Three different optimization algorithms are used to generate trajectories for each of these segments. The primary flight control is designed using a linear dynamic inversion control scheme, and a path following control law is developed to track the autorotation trajectories. Details of the path planning algorithm, trajectory following control law, and autonomous autorotation system implementation are presented. -
Helicopter Controllability. Reference 2 Presents a Comprehensive History and References 1 and 3 Present Summarized Histories of Helicopter Development
Calhoun: The NPS Institutional Archive Theses and Dissertations Thesis Collection 1989-09 Helicopter controllability Carico, Dean Monterey, California. Naval Postgraduate School http://hdl.handle.net/10945/27077 DTfltttf NAVAL POSTGRADUATE SCHOOL Monterey , California THESIS C2D L/5~ HELICOPTER CONTROLLABILITY by Dean Carico September 1989 Thesis Advisor: George J. Thaler Approved for public release; distribution unlimited lclassified V CLASSi^'CATiON QF THIS PAGE REPORT DOCUMENTATION PAGE ORT SECURITY CLASSIFICATION 1b RESTRICTIVE MARKINGS assif ied IURITY CLASSIFICATION AUTHORITY 3 DISTRIBUTION /AVAILABILITY OF REPORT Approved for public release :lassification t DOWNGRADING SCHEDULE Distribution is unlimited ORMING ORGANIZATION REPORT NUMBER(S) 5 MONITORING ORGANIZATION REPORT NUMBER(S) ME OF PERFORMING ORGANIZATION 6b OFFICE SYMBOL 7a. NAME OF MONITORING ORGANIZATION il Postgraduate School (If applicable) 62 Naval Postgraduate School DRESS {City, State, and ZIP Code) 7b ADDRESS (C/fy, State, and ZIP Code) :erey, California 93943-5000 Monterey, California 93943-5000 9 PROCUREMENT INSTRUMENT IDENTIFICATION NUMBER DRESS (City, State, and ZIP Code) 10 SOURCE OF FUNDING NUMBERS IE (include Security Claudication) HELICOPTER CONTROLLABILITY RSONAL AUTHOR(S) ICO, G. Dean YPE OF REPORT 4 DATE OF REPORT (Year, Month. Day) ter ' s Thesis 1989, September ipplementary notation T h e views expressed in this thesis are thos e of the hor and do not reflect the official policy or position of the Department r,nyprninpnf npfpnsp nr ___ , COSATi CODES 18 SUBJECT TERMS {Continue on reverse if pecessary and identify Helicopter Controllability, Helicop Flight Control Systems, Helicopter Flying Qualities and Flying Qualities Spec if ications i 3STRACT {Continue I reverse if necessary and identify by block number) 'he concept of helicopter controllability is explained. -
Download (6MB)
Trchalik, Josef (2009) Aeroelastic modelling of gyroplane rotors. PhD thesis. http://theses.gla.ac.uk/1232/ Copyright and moral rights for this thesis are retained by the author A copy can be downloaded for personal non-commercial research or study, without prior permission or charge This thesis cannot be reproduced or quoted extensively from without first obtaining permission in writing from the Author The content must not be changed in any way or sold commercially in any format or medium without the formal permission of the Author When referring to this work, full bibliographic details including the author, title, awarding institution and date of the thesis must be given Glasgow Theses Service http://theses.gla.ac.uk/ [email protected] Aeroelastic Modelling of Gyroplane Rotors Josef Trchalík, Dipl.Ing. Ph. D. Thesis Department of Aerospace Engineering University of Glasgow July 2009 Thesis submitted to the Faculty of Engineering in fulfillment of the requirements for the degree of Doctor of Philosophy c J. Trchalík, 2009 Abstract The gyroplane represents the first successful rotorcraft design and it paved the way for the development of the helicopter during the 1940s. Gyroplane rotors are not powered in flight and work in autorotative regime and hence the characteristics of a helicopter rotor during powered flight and a rotor in autorotation differ sig- nificantly. Gyroplanes in the UK have been involved in number of fatal accidents during the last two decades. Despite several research projects focused on gyroplane flight dynamics, the cause of some of gyroplane accidents still remains unclear. The aeroelastic behaviour of autorotating rotors is a relatively unexplored problem and it has not yet been investigated as possible cause of the accidents. -
Nonlinear Dynamics and Robust Control of a Gyroplane Rotor ?
NONLINEAR DYNAMICS AND ROBUST CONTROL OF A GYROPLANE ROTOR ? Yevgeny I. Somov ∗,† and Oleg Ye. Polyntsev ‡ ∗ Stability and Nonlinear Dynamics Research Center, Mechanical Engineering Research Institute (IMASH), the Russian Academy of Sciences (RAS) 5 Dm. Ul’yanov Str. Moscow 119333 Russia † Research Institute of Mechanical Systems Reliability 244 Molodogvardeyeskaya Str. Samara 443100 Russia [email protected] e−[email protected] ‡ JSC Scientific & Production Corporation IRKUT 3 Novatorov Str. Irkutsk 664020 Russia [email protected] Abstract: Mathematical models of a gyroplane rotor have been carried out. Their approximate analytical solutions have been obtained. Software allowing one to simulate and study a rotor dynamics has been created. Major physical features on the forced flexible oscillations of the rotor have been investigated. The results obtained have successfully been applied to design the A-002 gyroplane rotor. Copyright c 2005 IFAC Keywords: gyroplane rotor, nonlinear dynamics, robust control 1. INTRODUCTION Some assumptions of the analytical models of auto- rotation applied earlier do not allow one to investigate At present due to new advanced technologies gy- entirely a GP rotor. The problem posed can effectively roplanes (GPs) are being created across the world. be solved due to computers having great capacities. Therefore, in order to predict operational features of a The purpose of the paper are modeling and research wind-milling rotor it is of significance to advance the of nonlinear dynamics and robust stabilization by a theory of auto-rotation. As against helicopter main gyroplane rotor, see Fig. 1. The rotor consists of two rotor an auto-rotating rotor is revolved under the blades attached to a hub by means of teeter hinge influence of an air stream rush. -
Flight Dynamics Investigation of Compound Helicopter Configurations
Ferguson, Kevin, and Thomson, Douglas (2014) Flight dynamics investigation of compound helicopter configurations. Journal of Aircraft. ISSN 1533-3868 Copyright © 2014 American Institute of Aeronautics and Astronautics, Inc. A copy can be downloaded for personal non-commercial research or study, without prior permission or charge Content must not be changed in any way or reproduced in any format or medium without the formal permission of the copyright holder(s) When referring to this work, full bibliographic details must be given http://eprints.gla.ac.uk/92870 Deposited on: 29 May 2014 Enlighten – Research publications by members of the University of Glasgow http://eprints.gla.ac.uk Flight Dynamics Investigation of Compound Helicopter Configurations Kevin M. Ferguson∗, Douglas G. Thomsony, University of Glasgow, Glasgow, United Kingdom, G12 8QQ Compounding has often been proposed as a method to increase the maximum speed of the helicopter. There are two common types of compounding known as wing and thrust compounding. Wing compounding offloads the rotor at high speeds delaying the onset of retreating blade stall, hence increasing the maximum achievable speed, whereas with thrust compounding, axial thrust provides additional propulsive force. There has been a resurgence of interest in the configuration due to the emergence of new requirements for speeds greater than those of con- ventional helicopters. The aim of this paper is to investigate the dynamic stability characteristics of compound helicopters and compare the results with a conventional helicopter. The paper discusses the modeling of two com- pound helicopters, which are named the coaxial compound and hybrid compound helicopters. Their respective trim results are contrasted with a conventional helicopter model. -
Measurements of Aerodynamic Interference of a Hybrid
sensors Article Measurements of Aerodynamic Interference of a y Hybrid Aircraft with Multirotor Propulsion Zbigniew Czy˙z 1,* and Mirosław Wendeker 2 1 Aeronautics Faculty, Military University of Aviation, 35 Dywizjonu 303 St., 08-521 D˛eblin,Poland 2 Department of Thermodynamics, Fluid Mechanics and Aviation Propulsion Systems, Faculty of Mechanical Engineering, Lublin University of Technology, 36 Nadbystrzycka St., 20-618 Lublin, Poland; [email protected] * Correspondence: [email protected] This paper is an extended version of our paper published in Zbigniew Czy˙z,Ksenia Siadkowska. y Measurement of Air Flow Velocity around the Unmanned Rotorcraft. In Proceedings of the 2020 IEEE International Workshop on Metrology for AeroSpace, Pisa, Italy, 22–24 June 2020. Received: 10 May 2020; Accepted: 11 June 2020; Published: 13 June 2020 Abstract: This article deals with the phenomenon of aerodynamic interference occurring in the innovative hybrid system of multirotor aircraft propulsion. The approach to aerodynamics requires a determination of the impact of active sources of lift and thrust upon the aircraft aerodynamic characteristics. The hybrid propulsion unit, composed of a conventional multirotor source of thrust as well as lift in the form of the main rotor and a pusher, was equipped with an additional propeller drive unit. The tests were conducted in a continuous-flow low speed wind tunnel with an open measuring space, 1.5 m in diameter and 2.0 m long. Force testing made it possible to develop aerodynamic characteristics as well as defining aerodynamic characteristics and defining the field of speed for the considered design configurations. Our investigations enabled us to analyze the results in terms of a mutual impact of particular components of the research object and the area of impact of active elements present in a common flow. -
Measurement of In-Flight Rotor Blade Loads of an Autogyro
Measurement of In-Flight Rotor Blade Loads of an Autogyro Helmut Rapp, Peter Wedemeyer Institut für Aerospace-Technologie, Hochschule Bremen, Bremen, Germany Christian Teuber STN Atlas Elektronik GmbH, Bremen, Germany Abstract go ahead in gyroplane development until there was Autogyros, or gyroplanes, are rotary wing aircraft extensive pressure due to military requirements. with no driven main rotor. The rotor keeps rotating In later stages their gyroplane was able to take only by the airflow resulting from the plane’s forward off vertically, to proceed the so-called "Direct Take- speed. Since WW2 there has been only a few investi- Off" over a 10 m obstacle and a vertical landing, if gations concerning the flying characteristics and per- required. Several gyroplanes were obtained by the formance of autogyros including blade loading. US-Military and a thorough research programme was This work covers both the theoretical and exper- undertaken at NACA-Laboratories compared to the imental investigations of rotor blade loading. The small research programmes done by the British, Ger- main parameters for the flapping moment are rotor man and French military. However, due to different speed and mass distribution of the rotor blades. For design the later developed Gyrocopter does not reflect the experimental investigations, a small telemetric the NACA results. In some short term research this system was developed. Up to four strains in the ro- type of aircraft was covered, even as a solution for a tor blades can be measured by using strain gauges. Mars-Landing-Vehicle and Pilot-Recovery-Systems. Wireless transmission of the strain data from the ro- Major design effort was put into gyroplanes for the tating rotor to a computer inside the fuselage is ac- civil market, reflected in the McCulloch J-2 and Um- complished by 433 MHz transceivers. -
Bramwell's Helicopter Dynamics
Bramwell’s Helicopter Dynamics Bramwell’s Helicopter Dynamics Second edition A. R. S. Bramwell George Done David Balmford Oxford Auckland Boston Johannesburg Melbourne New Delhi Butterworth-Heinemann Linacre House, Jordan Hill, Oxford OX2 8DP 225 Wildwood Avenue, Woburn, MA 01801-2041 A division of Reed Educational and Professional Publishing Ltd A member of the Reed Elsevier plc group First published by Edward Arnold (Publishers) Ltd 1976 Second edition published by Butterworth-Heinemann 2001 © A. R. S. Bramwell, George Done and David Balmford 2001 All rights reserved. No part of this publication may be reproduced in any material form (including photocopying or storing in any medium by electronic means and whether or not transiently or incidentally to some other use of this publication) without the written permission of the copyright holder except in accordance with the provisions of the Copyright, Designs and Patents Act 1988 or under the terms of a licence issued by the Copyright Licensing Agency Ltd, 90 Tottenham Court Road, London, England W1P OLP. Applications for the copyright holder’s written permission to reproduce any part of this publication should be addressed to the publishers British Library Cataloguing in Publication Data Bramwell, A.R.S. Bramwell’s helicopter dynamics. – 2nd ed. 1 Helicopters – Aerodynamics I Title II Done, George III Balmford, David IV Helicopter dynamics 629.1′33352 Library of Congress Cataloguing in Publication Data Bramwell, A.R.S. Bramwell’s helicopter dynamics / A.R.S. Bramwell, George Done, David Balmford. –2nd ed. p. cm. Rev. ed. of: Helicopter dynamics. c1976 Includes index ISBN 0 7506 5075 3 1 Helicopter–Dynamics 2 Helicopters–Aerodynamics I Done, George Taylor Sutton II Balmford, David III Bramwell, A.R.S.