Minimum Operating Standards for Rolling Stock - Common Interface Requirements
Total Page:16
File Type:pdf, Size:1020Kb
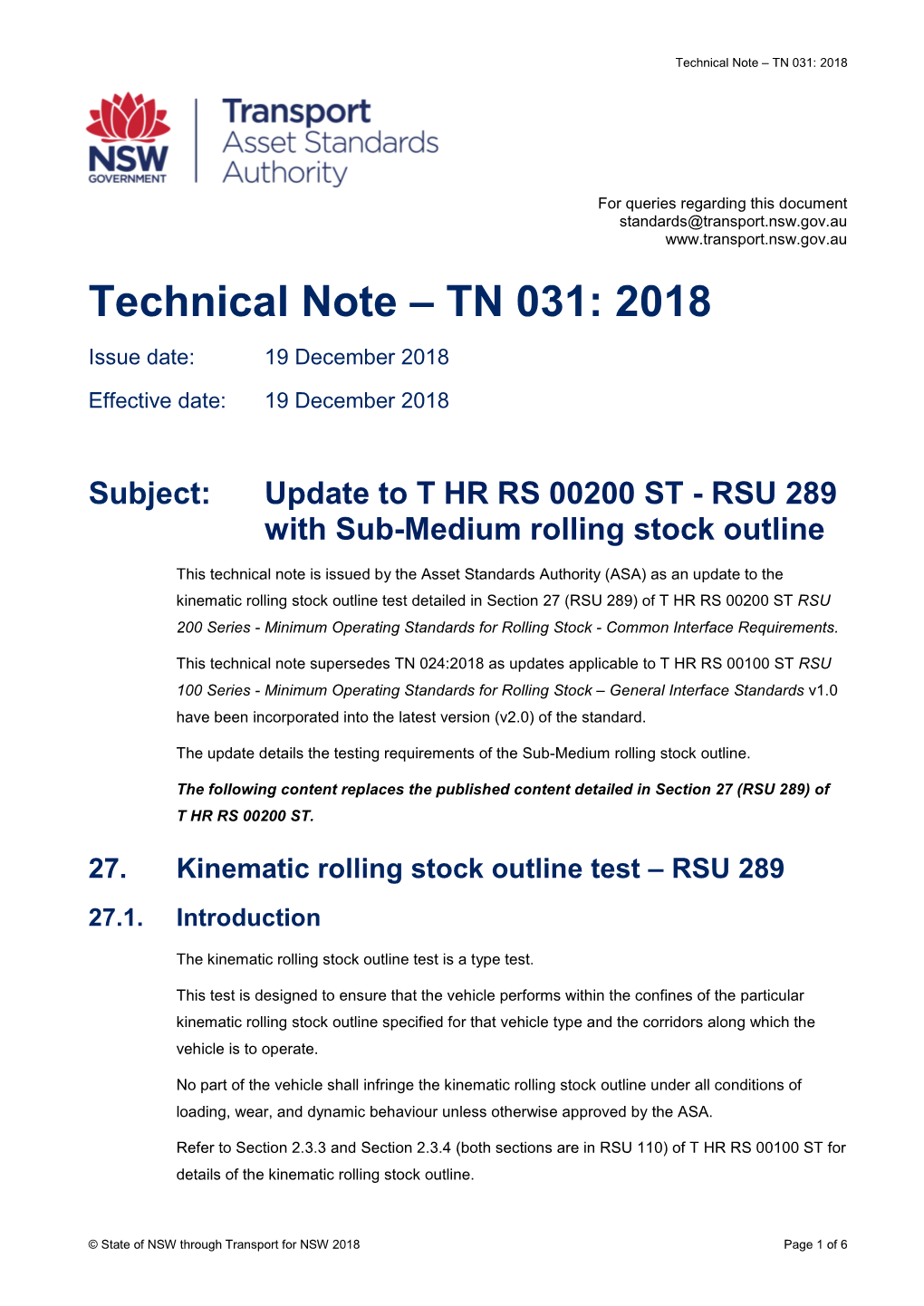
Load more
Recommended publications
-
BNSF Issues Part 240 Submission
Part 240 Submission April 20, 2008 BNSF Railway - Certification Program Revised April 20, 2008 Table of Contents Page Section 1: General Information and Elections. 2 A. Election to train 2 B. Classes of Service 2 1. Train Service Engineer 2 2. Student Engineer 2 3. Remote Control Operator 2 4. Student Remote Control Operator 3 5. Locomotive Servicing Engineer 3 Section 2: Selection of Supervisors of Certified Employees. 4 A. Designating Supervisors 4 Section 3: Training Persons Previously Certified. 5 A. Continuing Education 5 1. Train Service Engineers 5 2. Remote Control Operator-Previously Certified Engineer 7 2a. Remote Control Operator 7 3. Locomotive Servicing Engineers 8 4. Dual Certified 8 B. Territory Qualification 8 C. Addressing Changes 9 Section 4: Testing and Evaluating Persons Previously Certified. 11 A. Written Knowledge Examination 11 B. Skills Performance Examination 12 1. Train Ride 13 2. Simulator 13 C. Vision and Hearing Acuity 14 Section 5: Training, Testing and Evaluating Persons Not Previously Certified. 15 A. Train Service Engineers 15 B. Remote Control Operators 17 C. Locomotive Servicing Engineers 18 Section 6: Monitoring Operational Performance of Certified Employees 19 A. Monitoring Operational Performance 19 1. Annual Observation 19 a. Train Ride 19 b. Simulator 20 c. Event Recorder 20 2. Unannounced Operations Rules Compliance Test 20 Section 7: Procedures for Routine Administration of the Engineer Certification Program. 21 A. General criteria for eligibility based on prior safety conduct 21 1. Motor vehicle Operator 21 2. Operating Rules Compliance 21 3. Substance Abuse Disorders 21 B. Determinations required as a prerequisite to certification 21 C. -
A Resource Book on High Speed Rail Technology
A resource book on High Speed Rail Technology A Resource Book On High Speed Rail Technology Important: The contents of this book are a work of compilation from various international journals, publications, books, data/information available on the e-world etc. No part of this book is an expression of the views of any individual, organisation etc. Neither the Government of India nor the Railway Board and Research Designs and Standards Organisation are responsible for the opinion or statements made therein. The book is meant as a resource material and a ready reckoner information on the work done so far and also the future strategies, by various railways world-over in the field of High Speed Railways. There is no copyright violation in preparation of this book. Published on: May, 2011 Compiled by: Gaurav Agarwal, Director(Efficiency &Research)/Mech Engg. Ministry of Railways, Govt. of India Government of India Ministry of Railways (Research, Design & Standards Organisation, Lucknow) FOREWORD High‐speed rail (HSR) brings clear and significant economic benefits to the communities they serve not only in terms of rise in GDP, but also in terms of its environmental impact. HSR uses much less energy per mile than auto or air travel. HSR transit is thus quickly gaining popularity as a key alternative in transportation policy planning. HSR also presents significant technological challenges as it requires synergy amongst a number of engineering disciplines. It is heartening to see the book “High Speed Rail Technology” by Mr. Gaurav Agarwal, Director(E&R)/ME, Railway Board which is a sincere effort towards collating all the relevant information relating to HSR at one place. -
1.3. Freight Traffic
ORGANISATION FOR CO-OPERATION BETWEEN RAILWAYS (OSJD) 1956-2021 Организация сотрудничества железных дорог (ОСЖД) 铁 路 合 作 组 织 (铁 组) Organisation für die Zusammenarbeit der Eisenbahnen (OSShD) R E P O R T ON THE ACTIVITIES OF THE ORGANISATION FOR CO-OPERATION BETWEEN RAILWAYS FOR 2020 Members of OSJD As of 1 August 2021 The Countries and Railways - Members of OSJD Countries Railways/Authorities Republic of Azerbaijan AZD - Azerbaijani Railways CJSC Republic of Albania Islamic Republic of Afghanistan ARA - Afghanistan Railway Authority (ARA) Republic of Belarus BC - Byelorussian Railway Republic of Bulgaria BDZ - Holding “Bulgarian State Railways” Hungary MAV - CJSC “Hungarian State Railways” Socialist Republic of Vietnam VZD - Vietnamese Railway State Company Georgia GR - “Georgian Railway” JSC Islamic Republic of Iran RAI - Railway of the Islamic Republic of Iran Republic of Kazakhstan KZH - JSC “Kazakhstan Temir Zholy National Company” (Railway of Kazakhstan) People’s Republic of China KZD - State Department for Railways / China State Railway Group Со., Ltd. Democratic People’s Republic of Korea (DPRK) ZC - Railways of the People's Democratic Republic of Korea Republic of Korea KORAIL - Korea Railroad Corporation Republic of Cuba Kyrgyz Republic KRG - “Kyrgyz Temir Zholy National Enterprise” State Company (Kyrgyz Railway) Republic of Latvia LDz - State JSC “Latvian Railway” (Latvijas dzelzceļš) Republic of Lithuania LTG - JSC “Lithuanian Railways” (AB “Lietuvos geležinkeliai“) Republic of Moldova CFM - State Enterprise “Railway of Moldova” -
KKK-R-2800 November 22, 1993 ------SUPERSEDING MIL-R-23314F 8 August 1986
Downloaded from http://www.everyspec.com *------------* * INCH-POUND * *------------* KKK-R-2800 November 22, 1993 ----------------- SUPERSEDING MIL-R-23314F 8 August 1986 FEDERAL SPECIFICATION RAILWAY CAR SPOTTER, SELF-PROPELLED, GED OR DED This specification is approved by the Commissioner, Federal Supply Service, General Services Administration, for the use of all Federal agencies. 1. SCOPE 1.1 Scope. This specification covers a gasoline or diesel-engine-driven vehicle, with railway car couplers or a vehicle towing clevis, designed for operation on rails or on paved surfaces. 1.2 Classification. The railway car spotter shall be of the following type and class as specified (see 6.2.1). Type I - Locomotive rail car Type II - Truck-tractor Class 1 - Gasoline engine driven Class 2 - Diesel engine driven Class 3 - Diesel engine driven, 30,000 pounds (lb) (13 608 kilograms (kg)), draw bar pull 2. APPLICABLE DOCUMENTS 2.1 Government documents. *----------------------------------------------------------------------------* *Beneficial comments (recommendations, additions, deletions) and any * *pertinent data which may be of use in improving this document should be * *addressed to: Commanding Officer (Code 156), Naval Construction Battalion * *Center, 1000 23rd Avenue, Port Hueneme, CA 93043-4301, by using the * *Standardization Document Improvement Proposal (DD Form 1426) appearing at * *the end of this document or by letter. * *----------------------------------------------------------------------------* FSC 2210 DISTRIBUTION STATEMENT A. Approved for public release; distribution is unlimited. Downloaded from http://www.everyspec.com KKK-R-2800 2.1.1 Specifications, standards, and handbooks. The following specifications, standards, and handbooks form a part of this specification to the extent specified herein. Unless otherwise specified, the issues of these documents shall be those listed in the issue of the Department of Defense Index of Specifications and Standards (DODISS) and supplement thereto, cited in the solicitation. -
Copyright and Citation Considerations for This Thesis/ Dissertation
COPYRIGHT AND CITATION CONSIDERATIONS FOR THIS THESIS/ DISSERTATION o Attribution — You must give appropriate credit, provide a link to the license, and indicate if changes were made. You may do so in any reasonable manner, but not in any way that suggests the licensor endorses you or your use. o NonCommercial — You may not use the material for commercial purposes. o ShareAlike — If you remix, transform, or build upon the material, you must distribute your contributions under the same license as the original. How to cite this thesis Surname, Initial(s). (2012). Title of the thesis or dissertation (Doctoral Thesis / Master’s Dissertation). Johannesburg: University of Johannesburg. Available from: http://hdl.handle.net/102000/0002 (Accessed: 22 August 2017). University of Johannesburg 2019 The effectiveness of a new electro-pneumatic braking system introduced on Transnet high capacity coal trains Mini Dissertation By Phumzile Yeni Submitted in Partial Fulfilment of the requirements for the MASTERS OF PHILOSOPHY In ENGINEERING MANAGEMENT In the FACULTY of ENGINEERING and BUILT ENVIRONMENT SUPERVISOR: DR. ANTON MANESCHIJN CO-SUPERVISOR: PROF. J.H.C. PRETORIUS 10-January-2019 Declaration Page I, “Phumzile Prudence Yeni”, student number “201464354”, hereby declare that this mini- dissertation is wholly my own work and has not been submitted anywhere else for academic credit either by myself or another person. I understand what plagiarism implies and declares that this mini-dissertation contains my own ideas, words, phrases, arguments, graphics, figures, results, organization, except where reference is explicitly made to another’s work. I understand further that any unethical academic behaviour, which includes plagiarism, is seen in a serious light by the University and is punishable by disciplinary action. -
Souvenir -International Conference on Green Initiatives & Railway
International Conference on Green Initiatives & Railway Electrification October 27-28, 2017 • New Delhi MESSAGE 51 Message CRB International Conference on Green Initiatives & Railway Electrification October 27-28, 2017 • New Delhi From the General Secretary's Desk 1.0 Introduction The Institution of Railway Electrical Engineers (IREE) is a professional body of Railway Electrical Engineers. It is a technical body under the auspices of Ministry of Railways sharing knowledge and experience of various Railway Engineers and others connected with Electrical Engineering. The Institution was registered at Nasik on 29th July, 1995 with registration no. Maharashtra/3920/ Nasik/95 and was inaugurated by the then Member Electrical, Railway Board Shri V. Santhanam on 26th August, 1995 at Nasik. The Institution was recognized by Railway Board in the year 1998. IREE is exempted under Section 80G of Income Tax Act as referred to U/s 80G(5)(vi). 2.0 Administration The Institution is administered by a Governing Council which works under the overall guidance of the President of the Institution. Member Traction, Railway Board is the Patron of the Institution and Addl. Member Electrical, Railway Board is the President. Principal Chief Electrical Engineer, Northern Railway, is the Hony. General Secretary of the Institution. The administrative work of the Institution is controlled by Hony. General Secretary. 3.0 Aim of the Institution The aim of the Institution is to disseminate and share the technical knowledge among the Railwaymen and industry regarding the available and new technology related to design, construction and maintenance of electrical assets. It is the plaza for adopting new emerging technology to serve the need of Railway Electrical Engineering. -
1418881285399-WDG-3A (ENGLISH).Pdf
Lesson No. 1 HEAT ENGINE Heat engine - Heat engine is the machine which converts heat energy into mechanical energy. Heat engine are of two types. a. External combustion engine - In External combustion engine fuel is burnt or ignited outside the engine cylinder. So it is called as external combustion engine e.g. Steam engine. b. Internal combustion engine - In internal combustion engine fuel is burnt or ignited inside the engine cylinder so it is called internal combustion engine e.g. Petrol engine, diesel engine. They are of two types a. Spark ignition engine - In this type of engine fuel is injected along with air in the cylinder and after compression this mixture is given electric spark due to which fuel starts burning and produces power. e.g. Petrol engine b. Compression ignition engine - It is an engine in which the fuel is ignited in to charge of compressed air and ignited spontaneously by the high temperature of the air induced by the heat of compression. e.g. Diesel engine. Combustion - Burning of fuel with air is called combustion. Piston stroke - The movement of piston from top dead centre to bottom dead center is called the piston stroke. Dead centre - The place beyond which the piston cannot move further in a cylinder is called dead center. Top dead centre - The end towards the head of the cylinder is called top dead center. Bottom dead centre - The end towards the base of the cylinder is called top dead center. Total Volume - The area between piston and cylinder head when the piston is at BDC is called total volume. -
Railway Investigation Report R06v0183 Runaway and Derailment White Pass and Yukon Route Work Train 114 Mile 36.5, Canadian Subdi
RAILWAY INVESTIGATION REPORT R06V0183 RUNAWAY AND DERAILMENT WHITE PASS AND YUKON ROUTE WORK TRAIN 114 MILE 36.5, CANADIAN SUBDIVISION LOG CABIN, BRITISH COLUMBIA 03 SEPTEMBER 2006 The Transportation Safety Board of Canada (TSB) investigated this occurrence for the purpose of advancing transportation safety. It is not the function of the Board to assign fault or determine civil or criminal liability. Railway Investigation Report Runaway and Derailment White Pass and Yukon Route Work Train 114 Mile 36.5, Canadian Subdivision Log Cabin, British Columbia 03 September 2006 Report Number R06V0183 Synopsis On 03 September 2006, at about 1300 Pacific daylight time, northbound White Pass and Yukon Route work train 114, comprising one locomotive and eight loaded ballast cars, ran uncontrolled down a steep grade and derailed the locomotive and the first six ballast cars at Mile 36.5 on the Canadian Subdivision. One person was fatally injured and three others sustained serious injuries. The six derailed ballast cars were destroyed. Ce rapport est également disponible en français. TABLE OF CONTENTS 1.0 Factual Information ........................................................................ 1 1.1 The Accident................................................................................................................ 1 1.2 Post Occurrence........................................................................................................... 3 1.3 Emergency Response................................................................................................. -
Minimum Operating Requirements for Rail-Bound Infrastructure Maintenance Vehicles
Country Regional Network Engineering Standard Rolling Stock and Plant CRN RS 005 MINIMUM OPERATING REQUIREMENTS FOR RAIL-BOUND INFRASTRUCTURE MAINTENANCE VEHICLES Version: 2.1 Issued: July 2019 Owner: Principal Rolling Stock and Plant Engineer Approved by: Drew Palmer Authorised by: James Zeaiter Disclaimer. This document was prepared for use on the CRN Network only. John Holland Rail Pty Ltd makes no warranties, express or implied, that compliance with the contents of this document shall be sufficient to ensure safe systems or work or operation. It is the document user’s sole responsibility to ensure that the copy of the document it is viewing is the current version of the document as in use by JHR. JHR accepts no liability whatsoever in relation to the use of this document by any party, and JHR excludes any liability which arises in any manner by the use of this document. Copyright. The information in this document is protected by Copyright and no part of this document may be reproduced, altered, stored or transmitted by any person without the prior consent of JHG. UNCONTROLLED WHEN PRINTED Page 1 of 44 CRN Engineering Standard - Rolling Stock and Plant CRN RS 005 Minimum Operating Requirements for Rail-Bound Infrastructure Maintenance Vehicles Document control Revision Date of Approval Summary of change 1.1 8/11/11 For publication 2.0 7/12/16 General review, corrections and update 2.1 16/7/19 Periodic Review Summary of changes from previous version Section Summary of change © JHR UNCONTROLLED WHEN PRINTED Page 2 of 44 Issued: July 2019 Version: 2.1 CRN Engineering Standard - Rolling Stock and Plant CRN RS 005 Minimum Operating Requirements for Rail-Bound Infrastructure Maintenance Vehicles Contents 1 Introduction .............................................................................................................................................. -
Railway Investigation Report R08v0270 Non-Main-Track
RAILWAY INVESTIGATION REPORT R08V0270 NON-MAIN-TRACK TRAIN RUNAWAY AND COLLISION KETTLE FALLS INTERNATIONAL RAILWAY WANETA TURN ASSIGNMENT MILE 141.20, KETTLE FALLS SUBDIVISION WANETA, BRITISH COLUMBIA 29 DECEMBER 2008 The Transportation Safety Board of Canada (TSB) investigated this occurrence for the purpose of advancing transportation safety. It is not the function of the Board to assign fault or determine civil or criminal liability. Railway Investigation Report Non-Main-Track Train Runaway and Collision Kettle Falls International Railway Waneta Turn Assignment Mile 141.20, Kettle Falls Subdivision Waneta, British Columbia 29 December 2008 Report Number R08V0270 Summary On 29 December 2008 at 1448 Pacific Standard Time, the Waneta Turn Assignment of the Kettle Falls International Railway ran uncontrolled down a steep grade near Waneta, British Columbia and collided with a cut of 25 stationary cars. Two locomotives and 12 cars derailed. The locomotive engineer received minor injuries. About 3000 gallons of fuel were spilled. Highway 22A was obstructed by the derailment for two days. Ce rapport est également disponible en français. - 2 - Other Factual Information The Accident On 29 December 2008, at about 0700, 1 the crew of the Waneta turn assignment (the assignment), a locomotive engineer, a conductor, and a trainman, reported for duty at Kettle Falls, Washington, United States (U.S.), Mile 95.6 on the Kettle Falls Subdivision. The assignment proceeded northward from Kettle Falls to Mile 141.2, Waneta, British Columbia (see Figure 1), where twenty five cars comprising 10 loads and 15 empties were left on level track at the bottom of the steep grade up to Columbia Gardens, British Columbia, Mile 144.01. -
ABBREVIATION - (MECHANICAL) Hindi and English 1 Full Form of AAC ‡.‡.¬¸Ú
ABBREVIATION - (MECHANICAL) Hindi and English 1 Full form of AAC ‡.‡.¬¸ú. ˆÅ¸ ¢¨¸¬÷¸¼÷¸ ²Åœ¸ Æ¡¸¸ í¾- a. Average Annual Consumption b. Average Accountable Consumption ‡½¨¸£½]¸ ‡›¸º‚¥¸ ˆ¿Å]¸Ÿœ¸©¸›¸ ‡½¨¸£½]¸ ‡ˆÅ¸„›’½¤¸¥¸ ˆ¿Å]¸Ÿœ¸©¸›¸ c. Approximate Annual Consumption d. Average Annual Comparison ‡œÏ¸½¢¬¸Ÿ¸½’ ‡›¸º‚¥¸ ˆ¿Å]¸Ÿœ¸©¸›¸ ‡½¨¸£½]¸ ‡›¸º‚]¸ ˆÅŸœ¸½¢£]¸›¸ Answer: a. Average Annual Consumption ‡½¨¸£½]¸ ‡›¸º‚¥¸ ˆ¿Å]¸Ÿœ¸©¸›¸ 2 Full form of AESS ‡.ƒÄ.‡¬¸.‡¬¸. ˆÅ¸ ¢¨¸¬÷¸¼÷¸ ²Åœ¸ Æ¡¸¸ í¾- a. Auto Engine Start Switch b. Auto Engine Start/Stop Switch ‚¸Á’¸½ ƒ¿¢]¸›¸ ¬’¸’Ä ¢¬¨¸\¸ ‚¸Á’¸½ ƒ¿¢]¸›¸ ¬’¸’Ä/¬’¸Áœ¸ ¢¬¨¸\¸ c. Auto Equipment Start Stop d. Auto Engine Shutdown Stop ‚¸Á’¸½ ƒˆ»Åœ¸Ÿ¸½›’ ¬’¸’Ä ¬’¸Áœ¸ ‚¸Á’¸½ ƒ¿¢]¸›¸ ©¸’”¸„›¸ ¬’¸Áœ¸ Answer: b. Auto Engine Start/stop Switch ‚¸Á’¸½ ƒ¿¢]¸›¸ ¬’¸’Ä/¬’¸Áœ¸ ¢¬¨¸\¸ 3 Full form of AIRF ‡.‚¸ƒÄ.‚¸£.‡œ¸€. ˆÅ¸ ¢¨¸¬÷¸¼÷¸ ²Åœ¸ Æ¡¸¸ í¾- a. All India Regulatory Federation b. All India Railwaymens Firm ‚¸Á¥¸ ƒ¿¢”¡¸¸ £½Š¸º¥¸½’£ú œ¸½€”£½©¸›¸ ‚¸Á¥¸ ƒ¿¢”¡¸¸ £½¥¸¨¸½Ÿ¸½›¬¸ œ¸€Ÿ¸Ä c. All India Railwaymens Federation d. All Included Railwaymens Federation ‚¸Á¥¸ ƒ¿¢”¡¸¸ £½¥¸¨¸½ Ÿ¸½›¬¸ œ¸½€”£½©¸›¸ ‚¸Á¥¸ ƒ›¸Æ¥¸º¢”” £½¥¸¨¸½Ÿ¸½›¬¸ œ¸½€”£½©¸›¸ Answer: c. All India Railwaymens Federation ‚¸Á¥¸ ƒ¿¢”¡¸¸ £½¥¸¨¸½Ÿ¸½›¬¸ œ¸½€”£½©¸›¸ 4 Full form of AITUC ‡.‚¸ƒÄ.’ú.¡¸».¬¸ú. ˆÅ¸ ¢¨¸¬÷¸¼÷¸ ²Åœ¸ Æ¡¸¸ í¾- a. All India Traffic Union Congress b. All India Trade Union Committee ‚¸Á¥¸ ƒ¿¢”¡¸¸ ’ï½¢œ¸€ˆÅ ¡¸»¢›¸¡¸›¸ ˆÅ¸¿ŠÏ½¬¸ ‚¸Á¥¸ ƒ¿¢”¡¸¸ ’ï½” ¡¸»¢›¸¡¸›¸ ˆÅŸ¸½’ú c. All India Trade Uniform Congress d. All India Trade Union Congress ‚¸Á¥¸ ƒ¿¢”¡¸¸ ’ï½” ¡¸»¢›¸œ¸€¸Ÿ¸Ä ˆÅ¸¿ŠÏ½¬¸ ‚¸Á¥¸ ƒ¿¢”¡¸¸ ’ï½” ¡¸»¢›¸¡¸›¸ ˆÅ¸¿ŠÏ½¬¸ Answer: d. All India Trade Union Congress ‚¸Á¥¸ ƒ¿¢”¡¸¸ ’ï½” ¡¸»¢›¸¡¸›¸ ˆÅ¸¿ŠÏ½¬¸ 5 Full form of AR ‡ ‚¸£ ˆÅ¸ ¢¨¸¬÷¸¼÷¸ ²Åœ¸ Æ¡¸¸ í¾- a. -
Design and Analysis of Train Brake T.S.S.Santhosh Kumar
Design and Analysis of Train Brake T.S.S.Santhosh Kumar Mrs.N.Venkata Lakshmi, M.Tech, Ph.D M.Tech, Machine Design, Assistant Professor, Department Mechanical Engineering, Department Mechanical Engineering, Kakinada Institute of Engineering and Technology. Kakinada Institute of Engineering and Technology. ABSTRACT: Most brakes commonly use friction between two Brakes are used on the cars of railway trains to enable surfaces pressed together to convert the kinetic deceleration, control acceleration (downhill) or to keep energy of the moving object into heat, though other them standing when parked. While the basic principle methods of energy conversion may be employed. For is familiar from road vehicle usage, operational example, braking converts much of the energy features are more complex because of the need to to electrical energy, which may be stored for later use. control multiple linked carriages and to be effective on Other methods convert energy into potential energy in vehicles left without a prime mover. Clasp brakes are such stored forms as pressurized air or pressurized one type of brakes historically used on trains. The oil. Eddy current brakes use magnetic fields to convert present work is directed towards the modeling of Train kinetic energy into electric current in the brake disc, brake pad in 3D CAD software called fin, or rail, which is converted into heat. Still other SOLIDWORKS. According to the existing air brake braking methods even transform kinetic energy into system of Railway coach the brake force applied per different forms, for example by transferring the energy one brake block is 2, 2.5 & 3TON.