Chapter 3 Piston Engines Lubrication
Total Page:16
File Type:pdf, Size:1020Kb
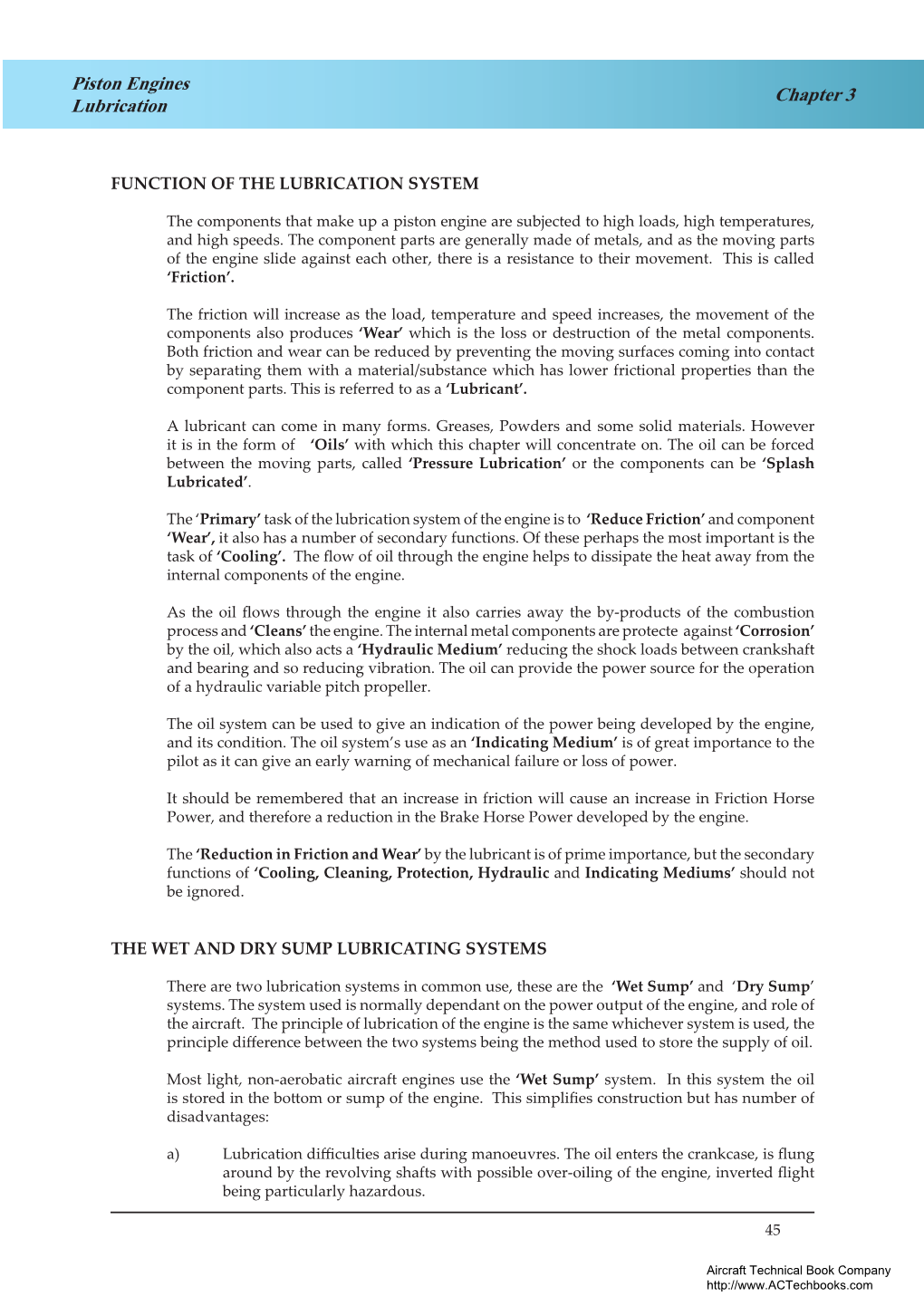
Load more
Recommended publications
-
1. the Future for Automotive Two-Stroke Engines – Part 2
N0.21 THE FUTURE FOR AUTOMOTIVE TWO-STROKE ENGINES (Part 2) CURRENT DEVELOPMENTS Synthetic-based formulation likely to be the preferred option. In the previous issue of Lube, the origins and initial development of the 2T Tendency for combustion chamber deposit formation would have required a engine were described. The earlier engines, characterised by smoky exhausts low ash or ash less lubricant. and poor specific fuel economy, will be remembered by many of the older High temperatures require strong anti-oxidancy. fraternity, as they provided motive power for many commuter lightweight motorcycles, mopeds and scooters in the prewar and postwar years. Many WET SUMP vehicle manufacturers in the UK used proprietary power units manufactured Again, no valve train therefore no requirement for e.g. ZDDP anti-wear by specialist engine manufacturers such as Villiers, who dominated the agent. market, although smaller engine suppliers included companies such as British Diluent unnecessary/undesirable. Anzani. A number of other companies, including Scott, Associated Conventional base oil plus viscosity index-improver is possible (SAE 10/30?). Motorcycles, Excelsior and latterly Ariel also designed their own engines, use Polymer deposits may favour synthetic approach. of which was restricted in the main to vehicles of their own manufacture. However, with the demise of the UK motorcycle industry, 2T engine Tendency for combustion chamber deposits requires a low ash approach. developments, which have progressed steadily during subsequent years, The conclusion was that, in spite of the substantial differences between the have been largely attributable to overseas manufacturers with assistance types of the Orbital engines described above, it may well have been possible from some UK specialist consultancy organizations such as Ricardos at to meet the requirements of both types of engine with a single lubricant, Shoreham. -
Wärtsilä 32 PRODUCT GUIDE © Copyright by WÄRTSILÄ FINLAND OY
Wärtsilä 32 PRODUCT GUIDE © Copyright by WÄRTSILÄ FINLAND OY COPYRIGHT © 2021 by WÄRTSILÄ FINLAND OY All rights reserved. No part of this booklet may be reproduced or copied in any form or by any means (electronic, mechanical, graphic, photocopying, recording, taping or other information retrieval systems) without the prior written permission of the copyright owner. THIS PUBLICATION IS DESIGNED TO PROVIDE AN ACCURATE AND AUTHORITATIVE INFORMATION WITH REGARD TO THE SUBJECT-MATTER COVERED AS WAS AVAILABLE AT THE TIME OF PRINTING. HOWEVER, THE PUBLICATION DEALS WITH COMPLICATED TECHNICAL MATTERS SUITED ONLY FOR SPECIALISTS IN THE AREA, AND THE DESIGN OF THE SUBJECT-PRODUCTS IS SUBJECT TO REGULAR IMPROVEMENTS, MODIFICATIONS AND CHANGES. CONSEQUENTLY, THE PUBLISHER AND COPYRIGHT OWNER OF THIS PUBLICATION CAN NOT ACCEPT ANY RESPONSIBILITY OR LIABILITY FOR ANY EVENTUAL ERRORS OR OMISSIONS IN THIS BOOKLET OR FOR DISCREPANCIES ARISING FROM THE FEATURES OF ANY ACTUAL ITEM IN THE RESPECTIVE PRODUCT BEING DIFFERENT FROM THOSE SHOWN IN THIS PUBLICATION. THE PUBLISHER AND COPYRIGHT OWNER SHALL UNDER NO CIRCUMSTANCES BE HELD LIABLE FOR ANY FINANCIAL CONSEQUENTIAL DAMAGES OR OTHER LOSS, OR ANY OTHER DAMAGE OR INJURY, SUFFERED BY ANY PARTY MAKING USE OF THIS PUBLICATION OR THE INFORMATION CONTAINED HEREIN. Wärtsilä 32 Product Guide Introduction Introduction This Product Guide provides data and system proposals for the early design phase of marine engine installations. For contracted projects specific instructions for planning the installation are always delivered. Any data and information herein is subject to revision without notice. This 1/2021 issue replaces all previous issues of the Wärtsilä 32 Project Guides. Issue Published Updates 1/2021 15.03.2021 Technical data updated. -
Mitsubishi Evolution 4 to 9 4G63 DOHC Engine Dry Sump Installation Guide
Mitsubishi Evolution 4 to 9 4G63 DOHC Engine Dry Sump Installation Guide Mitsubishi Evo 4G63 DOHC Dry Sump Kit Installation Guide Thank you for purchasing the Pace Products dry sump kit for the Mitsubishi Evo. The kit is designed for the 4G63 engine as fitted to the Mitsubishi Evo 4 through to 9, from standard tune engines to high power special installations. It features a high strength cast aluminium sump, machined billet aluminium front cover and our well proven BG 3 stage oil pump. The pump is mounted externally to the engine and is bolted to the exhaust side of the engine block via a mounting bracket and is powered by a toothed rubber belt. Our kit is a bolt on solution requiring no modifications of standard engine components. The kit has been tested and developed using Automotive Performance Tuning’s 700hp Mitsubishi Evo time attack car. If you have any comments on this kit or would like additional information on the Pace Products range of kits and components please call 01440 760960 or email [email protected] - 2 - Pace Products Ltd. Issue D, 05th April 2011. Disclaimer No warranty is offered or inferred on this product. Fitment of this product may invalidate the manufactures’ warranty, please check before. Please note there are some minor differences on later 4G63 engines, primarily effecting sump fitment. Whilst every effort has been made to accommodate these, some modifications may be required to ensure correct fitment to your engine. These depend on your engine variant and specification, particularly if using an aftermarket crankshaft cradle and con rod stud kit. -
BOSE , CUTTACK 1. Mist Lubrication System
BOSE , CUTTACK CHAPTER-06 LUBRICATION SYSTEM IN AUTOMOBILE Functions of lubricating oil: A good lubricating oil should perform the following function. · It reduces the friction between the moving parts. · It cools the piston so it also acts as a cooling medium. · It also prevents the leakage of gas between the piston and cylinder because it makes a film of lubricant between them. · It also reduces the noise between the rubbing surfaces. The various lubrication systems used for lubricating the various parts of engine are classified as 1. Mist lubrication system 2. Wet sump lubrication system, and 3. Dry sump lubrication system. 1. Mist lubrication system: Mist lubrication system is a very simple type of lubrication. In this system, the small quantity of lubricating oil (usually 2 to 3%) is mixed with the fuel (preferably gasoline). The oil and fuel mixture is introduced through the carburetor. The gasoline vaporized and oil in the form of mist enters the cylinder via the crank base. The droplets of oil strike the crank base. The droplets of oil strike the crank base, lubricate the main and connecting rod bearings and the rest of the oil lubricates the piston, piston rings and cylinder. The system is preferred in two stroke engines where crank base lubrication is not required. In a two-stroke engine, the charge is partially compressed in a crank base, so it is not possible to have the oil in the crank base. This system is simple, low cost and maintenance free because it does not require any oil pump, filter, etc. However, it has certain serious disadvantages. -
Eaton Aeroquip E-Z Drain Sump Valve
Aeroquip® E-Z Drain® Sump Valve www.herberaircraft.com Eaton’s Aeroquip E-Z Drain Sump Valve makes aircraft oil changes easy. The hand-actuated valve, when attached to the oil drain port, permits aircraft engine oil changes from the ground without removal of the engine cowling. The spring-loaded E-Z Drain Valve is safe for all piston engine applcations because it canot be accidentally opened. Actuation of FEATURES the valve requires a combination push- • Reduces oil changing time twist motion. It also contains a dual seal arrangement which combines • No need to remove engine cowl both an O-ring and a metal-to-metal to change oil seal to prevent accidental leakage of • Easy manual operation – oil through the valve. The seal used on requires no tools the internal valve is replaceable with a • Eliminates messy oil spills standard AS O-ring. The accompanying • Built-in hose line directs old oil hose is furnished in standard 12-inch to container lengths*. • Spring-loaded sleeve prevents accidental oil drainage The FAA has issued a Parts • Dual seal feature guards against Manufacturing Approval to Eaton for O-ring failure use of the E-Z Drain Sump Valve on all of the aircraft engines listed in the • Safety wire holes provided below table. INSTALLATION 1. Simply remove the plug from 2. Take hold of the knurled nut 4. To close, twist the knurled nut. the bottom of the oil sump and and with a combination push- The spring-loaded valve will install the drain valve in the twist motion, open the valve. -
Compliance-Packet-1.Pdf
D All-wheel drive la"Restrictor plate D Adjustable engine management D Dry sump oil system D Mechanically-adjustable throttle stop D Electronically-adjustable throttle • Accusump or other in-car system capable of adding or removing engine oil D Any form of wireless connection to the ECU or engine management system Adjustable engine management declaration If this car has "adjustable engine management system", including multiple maps, either engaged manually or triggered automatically by wheel speed sensors, acceleration, etc. as defined by section 5.2 of the GTS rules, please complete this section. System name/type Nl f\ Description--~------------------------ Method of adjustment ________________________ Settings used for this dyno run and how to verify at the track ___________ Variable boost declaration If this car has variable boost capabilities, please complete this section. Means of adjustment /J Ifr Settings used for this dyno run and how to verify at the track ___________ Restrictor plate declaration If this car requires a restrictor plate or other intake-restricting device of any kind to produce the figures from this dyno run, please complete this section. Detailed description of the restricting device, including pertinent dimensions ~ YY1 ro \J ~ koo P:immQt:½2odd ~ G"=&-l u.r(;od&C 'R~c:bzc :Pl~ Instructions on how to verify this at the track TI- Ls ]0 oJeJ be-beQ,V\.~ %0?\U:e, \»Ly d,JV\cl'\be I v11J;.e, rro¥11~ fd 1 Throttle stop declaration If this vehicle requires the use of either a mechanical throttle stop or an electronic throttle limit to achieve the numbers shown on this dyno sheet, please complete this section. -
PICTURE DESCRIPTION REPLACEMENT MANUFACTURER & P/N Power Steering Bracket Assembly 97-253BK
REPLACEMENT PICTURE DESCRIPTION MANUFACTURER & P/N 97-253BK (Black - LT4 for Add-On P/ S to Dry Sump ONLY) Power Steering Bracket Assembly 97-251BK (Black Dry Sump) Manifold Assembly, Water Pump Alternator Bracket Holley 97-254 Alternator Bracket Spacer Holley 97-255 (Wet Sump) 97-262BK (Black Wet Sump) Spacer, P/S Bracket Assembly Gaskets, Water Pump GM 12657430 Water Pump Drive Assembly -Clockwise Rotation- Holley 97-245 (not included with wet sump applications) Water Pump Assembly Gasket GM 12619770 REPLACEMENT PICTURE DESCRIPTION MANUFACTURER & P/N Bando 6PK1780 (20-220, Belt (6-Rib), Accessories 20-221, 20-230 & BK versions) Bando 6PK1500 (20-224 & 20-224) Gates FleetRunner® K080820HD Belt (8-Rib), Supercharger (20-220, 20-221, 20-222 & BK ver.) Bando 8PK2130 (20-223 & BK ver.) Bando 11PK2185 (20-233 & BK ver.) Belt (11-Rib), Supercharger Bando Aramid 11PK2137A (20-230 & BK ver.) Holley 97-247 / Thermostat 190° & Housing GM 12674634 LT4 - Holley 97-243 / GM 12663624 Supercharger Tensioner Holley 97-244 / Accessory Tensioner GM 12669076 LT4 - Holley 97-242 / GM 12642706 Supercharger Smooth Idler, Lower LT4 - Holley 97-241 / GM 12665845 Supercharger Smooth Idler, Center LT4 - Holley 97-240 / GM 12678245 Supercharger Ribbed Idler, Center Holley 97-249 / Accessories Smooth Idler Gates 36101 Alternator Harness Pigtail Holley 197-400 197-303 (Black) Alternator REPLACEMENT PICTURE DESCRIPTION MANUFACTURER & P/N Adapter Manifold for A/C Compressor & Holley 199-201 / 199-201BK Hardware (Long Option) Adapter Manifold for A/C Compressor & Holley -
Mike Mavrigian Dry Sump Oil Systems Offer a Number of Advantages Over
Performance Perspectives Dry sump oil systems offer a number of advantages over conventional oiling systems. They also are finding their way into more and more high-end performance engine builds. riginal equipment engines, as A dry sump oil system (so-called because well as a large number of race the oil pan does not store the oil) provides a engines, feature what’s called more efficient and direct approach. An exter- a wet sump oil system that de- nally mounted oil pump takes advantage of ex- livers pressurized oil to the ternal plumbing to directly deliver oil to the Mike main oil gallery. Oil is stored engine. The dry sump pan serves only as a Mavrigian in the oil pan sump and is picked up by a me- containment cover and as a location from Ochanically driven oil pump. The pump fea- which oil can be returned to the reservoir. The [email protected] tures a screened pickup that’s submerged in oil reservoir (the oil supply) is a remote con- the sump’s oil reservoir. The pump is mechan- tainer that can be mounted in the cockpit, en- ically driven by either the camshaft-driven dis- gine bay or other convenient location in a race tributor, by the cam itself or by the crank vehicle. In basic terms, the external pump snout, depending on the engine type. The pulls oil from the remote reservoir, then push- pump pressurizes the oil, sending it through es it (under pressure) to wherever directed by the main gallery, and subsequently to all bear- the plumbing. -
Technical Data Sheet
TECHNICAL DATA SHEET TDS No.: 06-01 Date Issued: 03/28/2006 2100 Mannix | San Antonio, TX 78217 t: 210.820.2450 | f: 210.820.2451 | e: [email protected] Revision: 4 (07/30/2010) AEC is recognized for Quality Management System Compliance to ISO 9001:2000. Page: 1 of 8 Cold Induction System weight and balance could cause instability of the 1.0 Subject: Airmotive Engineering (AE) Cold aircraft. Induction System 5.0 Engine Applications: Call for information 2.0 Availability: The AE Cold Induction Systems regarding other applications are sold through Engine Components Inc. (ECi®) under the TITAN® EXP™ brand. • ECi TITAN® EXP™ IOX-340S (Stroker) Series • ECi TITAN® EXP™ IOX-360 Series 3.0 Part Numbers and Description: AE111-1 (Finned sump) and AE111-2 (Unfinned sump) 6.0 Cold Induction System Schematic: The Cold Induction System components and their 4.0 General Description: An EXPERIMENTAL assembly are shown in Figures 1, 2 and 3 cold induction system for 4 cylinder opposed which are included in Section 13.0 below. engines which are based on the Lycoming 320/360 cu. in. design. The AE Cold Induction System consists of an oil sump assembly with 7.0 Safety Information: The following special “wings” on each side to minimize depth, an attention notices are used in this Technical induction housing with a forward facing Data Sheet to notify and advise the installer mounting pad for the throttle body/servo and and user of the product that certain actions or intake pipe assemblies which together procedures may be dangerous to the user or increase engine horsepower with no weight result in damage to the product. -
Vacuum Pumps Add Easy Horsepower to Any Engine. Here's
The three core components of any vacuum pump system are the pump, drive pulleys, and breather tank. Aerospace Components' billet hardware is too pretty to hide under the hood. The company offers turnkey kits for both small- and big-block Fords. TECH Vacuum Pumps Add Easy Horsepower to Any Engine. BY STEPHEN KIM PHOTOS Here's a Closer Look and How they Work COURTESY OF THE MANUFACTURERS hen a bazillion PSI of cylinder pressure pushes down on the pistons, some of it’s going to leak past the rings and into the crankcase. That’s why old cars have breathers, and newer cars have W PCV systems. While a wee bit of blow-by is completely normal— even in a 100-percent healthy motor—if an engine’s crankcase isn’t ventilated, that wee bit of blow-by is enough to pop oil seals and gaskets in no time. No bueno, homie. So what’s a racer to do? Valve cover breathers are an easy fix for non-emissions engines, but zip-tying rags onto the breathers and using them as disposable “catch cans” is downright ghetto. Instead of venting crankcase fumes into the atmosphere, late-model motors circulate them back into the intake manifold by utilizing a PCV valve. While these closed-loop systems are great for tree-huggers, they also re-circulate tiny oil droplets into the induction tract, which reduces knock resistance and can lead to detonation. Still no bueno, homie. So what’s a racer to do? The ultimate solution is sucking the fumes out of the crankcase with a vacuum pump. -
LUBRICATION SYSTEM in IC ENGINES Definition of Lubrication
LUBRICATION SYSTEM IN IC ENGINES Definition of lubrication Lubrication is the action of applying a substance such as oil or grease to an engine or component so as to minimize friction and allow smooth movement. Lubrication System Lubricating system is a mechanical system of lubricating internal combustion engines in which a pump forces oil into the engine bearings. PURPOSE OF LUBRICATION ➢ To reduce the friction between moving parts ➢ To increase the efficiency ➢ To minimize the vibrations ➢ To reduce the corrosion and carbon deposits ➢ To reduce the heat of moving parts ➢ To minimize power loss due to friction ➢ To reduce the noise created by moving parts ➢ To provide cooling to the engine TYPES OF LUBRICANTS ➢SOLID LUBRICANTS ❑ e.g. graphite ,molybdenum ,mica ➢ SEMI-SOLID LUBRICANTS ❑ e.g. heavy greases ➢ LIQUID LUBRICANTS ❑ e.g. mineral oil obtained by refining petroleum. PROPERTIES OF LUBRICANTS ➢ Viscosity ❑ It is a measure of the resistance to flow of an oil ❑ It is measured in saybolt universal seconds (SUS) ❑ It is expressed in centistokes ,centipoises and redwood seconds ➢ Viscosity Index ❑ viscosity of oil decreases with increase in temperature ➢ Cloud point ❑ If an oil is cooled , it will start solidifying at some time . ❑ Temperature at which oil starts solidifying , is called cloud point PROPERTIES OF LUBRICANTS ➢Pour point ❑ It is temperature just above which the oil sample will not flow under certain prescribed conditions ❑ this property is important for operation of engines and substances at low temperature conditions ➢ Flash point and Fire point ❑ The temperature at which vapour of an oil flash when subjected to a naked flame is called flash point ❑ Fire point is the temperature at which the oil ,it once lit with flame ,will burnt steadily at least for 5 seconds ➢ Specific Gravity ❑ It varies between 0.85 to 0.96 SAE Number • Society of Automotive Engineer has recommended SAE viscosity number for lubricating oils. -
Disadvantages of Dry Sump Lubrication System
DISADVANTAGES OF DRY SUMP LUBRICATION SYSTEM ➢ Dry-sump systems add cost, complexity, and weight ➢ The extra pumps and lines in dry-sump engines require additional oil and maintenance ➢ The large external reservoir and pumps can be tricky to position around the engine and within the engine bay due to their size ➢ Inadequate upper valvetrain lubrication can also become an issue if too much oil vapor is being pulled out from the area, especially with multi-staged pumps Cooling System NECESSITY OF COOLING SYSTEM The cooling system is provided in the IC engine for the following reasons: • The temperature of the burning gases in the engine cylinder reaches up to 1500 to 2000°C, which is above the melting point of the material of the cylinder body and head of the engine. • Therefore, if the heat is not dissipated, it would result in the failure of the cylinder material. • Due to very high temperatures, the film of the lubricating oil will get oxidized, thus producing carbon deposits on the surface. This will result in piston seizure. • Due to overheating, large temperature differences may lead to a distortion of the engine components due to the thermal stresses set up. • This makes it necessary for, the temperature variation to be kept to a minimum. Cooling System REQUIREMENTS OF EFFICIENT COOLING SYSTEM The two main requirements of an efficient cooling system are: • It must be capable of removing only about 30% of the heat generated in the combustion chamber. • Too much removal of heat lowers the thermal efficiency of the engine. • It should remove heat at a fast rate when the engine is hot.