Frequency Measurement of Musical Instrument Strings Using Piezoelectric Transducers
Total Page:16
File Type:pdf, Size:1020Kb
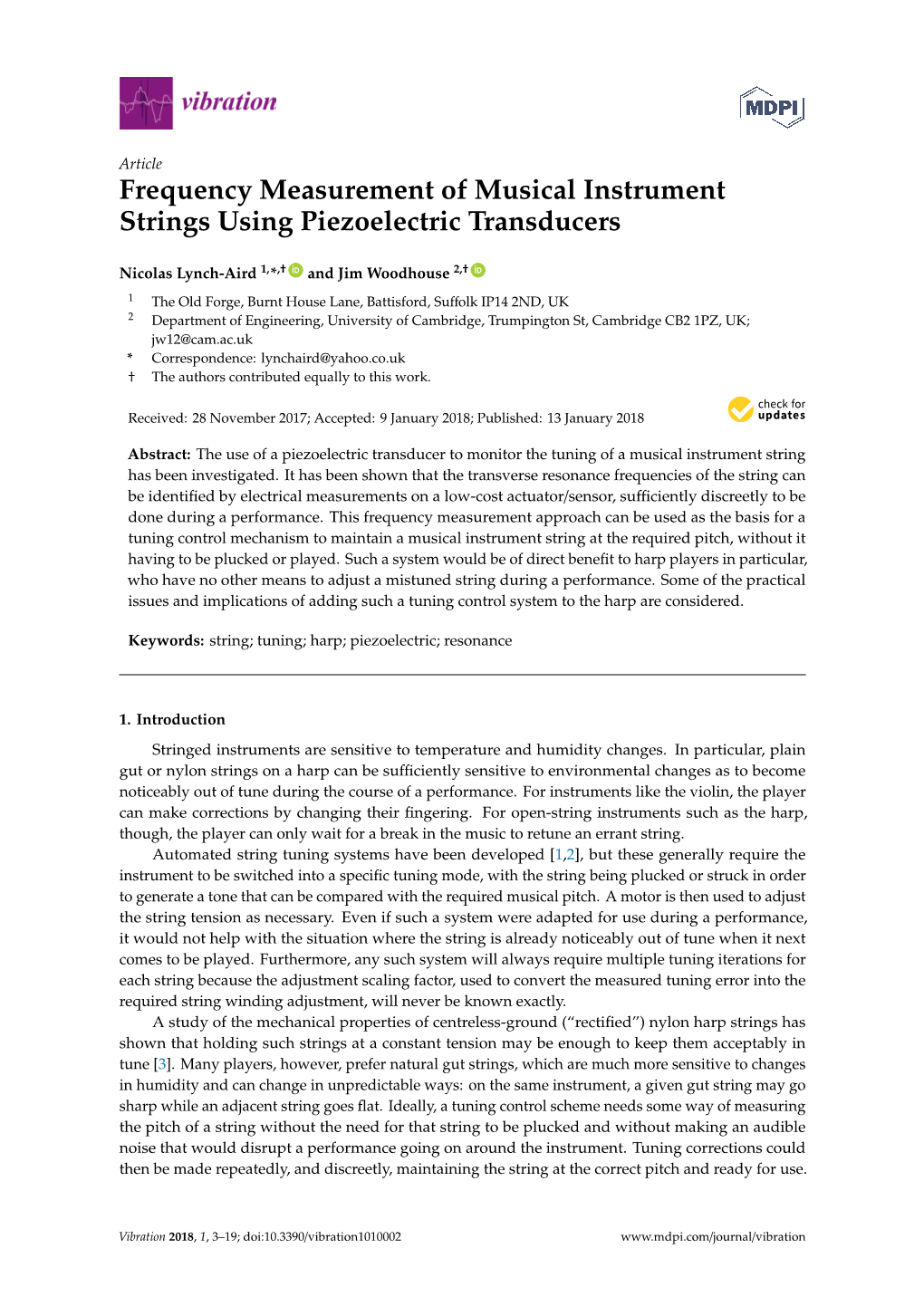
Load more
Recommended publications
-
African Music Vol 6 No 2(Seb).Cdr
94 JOURNAL OF INTERNATIONAL LIBRARY OF AFRICAN MUSIC THE GORA AND THE GRAND’ GOM-GOM: by ERICA MUGGLESTONE 1 INTRODUCTION For three centuries the interest of travellers and scholars alike has been aroused by the gora, an unbraced mouth-resonated musical bow peculiar to South Africa, because it is organologically unusual in that it is a blown chordophone.2 A split quill is attached to the bowstring at one end of the instrument. The string is passed through a hole in one end of the quill and secured; the other end of the quill is then bound or pegged to the stave. The string is lashed to the other end of the stave so that it may be tightened or loosened at will. The player holds the quill lightly bet ween his parted lips, and, by inhaling and exhaling forcefully, causes the quill (and with it the string) to vibrate. Of all the early descriptions of the gora, that of Peter Kolb,3 a German astronom er who resided at the Cape of Good Hope from 1705 to 1713, has been the most contentious. Not only did his character and his publication in general come under attack, but also his account of Khoikhoi4 musical bows in particular. Kolb’s text indicates that two types of musical bow were observed, to both of which he applied the name gom-gom. The use of the same name for both types of bow and the order in which these are described in the text, seems to imply that the second type is a variant of the first. -
Lab 12. Vibrating Strings
Lab 12. Vibrating Strings Goals • To experimentally determine the relationships between the fundamental resonant frequency of a vibrating string and its length, its mass per unit length, and the tension in the string. • To introduce a useful graphical method for testing whether the quantities x and y are related by a “simple power function” of the form y = axn. If so, the constants a and n can be determined from the graph. • To experimentally determine the relationship between resonant frequencies and higher order “mode” numbers. • To develop one general relationship/equation that relates the resonant frequency of a string to the four parameters: length, mass per unit length, tension, and mode number. Introduction Vibrating strings are part of our common experience. Which as you may have learned by now means that you have built up explanations in your subconscious about how they work, and that those explanations are sometimes self-contradictory, and rarely entirely correct. Musical instruments from all around the world employ vibrating strings to make musical sounds. Anyone who plays such an instrument knows that changing the tension in the string changes the pitch, which in physics terms means changing the resonant frequency of vibration. Similarly, changing the thickness (and thus the mass) of the string also affects its sound (frequency). String length must also have some effect, since a bass violin is much bigger than a normal violin and sounds much different. The interplay between these factors is explored in this laboratory experi- ment. You do not need to know physics to understand how instruments work. In fact, in the course of this lab alone you will engage with material which entire PhDs in music theory have been written. -
The Science of String Instruments
The Science of String Instruments Thomas D. Rossing Editor The Science of String Instruments Editor Thomas D. Rossing Stanford University Center for Computer Research in Music and Acoustics (CCRMA) Stanford, CA 94302-8180, USA [email protected] ISBN 978-1-4419-7109-8 e-ISBN 978-1-4419-7110-4 DOI 10.1007/978-1-4419-7110-4 Springer New York Dordrecht Heidelberg London # Springer Science+Business Media, LLC 2010 All rights reserved. This work may not be translated or copied in whole or in part without the written permission of the publisher (Springer Science+Business Media, LLC, 233 Spring Street, New York, NY 10013, USA), except for brief excerpts in connection with reviews or scholarly analysis. Use in connection with any form of information storage and retrieval, electronic adaptation, computer software, or by similar or dissimilar methodology now known or hereafter developed is forbidden. The use in this publication of trade names, trademarks, service marks, and similar terms, even if they are not identified as such, is not to be taken as an expression of opinion as to whether or not they are subject to proprietary rights. Printed on acid-free paper Springer is part of Springer ScienceþBusiness Media (www.springer.com) Contents 1 Introduction............................................................... 1 Thomas D. Rossing 2 Plucked Strings ........................................................... 11 Thomas D. Rossing 3 Guitars and Lutes ........................................................ 19 Thomas D. Rossing and Graham Caldersmith 4 Portuguese Guitar ........................................................ 47 Octavio Inacio 5 Banjo ...................................................................... 59 James Rae 6 Mandolin Family Instruments........................................... 77 David J. Cohen and Thomas D. Rossing 7 Psalteries and Zithers .................................................... 99 Andres Peekna and Thomas D. -
Resonance and Resonators
Dept of Speech, Music and Hearing ACOUSTICS FOR VIOLIN AND GUITAR MAKERS Erik Jansson Chapter II: Resonance and Resonators Fourth edition 2002 http://www.speech.kth.se/music/acviguit4/part2.pdf Index of chapters Preface/Chapter I Sound and hearing Chapter II Resonance and resonators Chapter III Sound and the room Chapter IV Properties of the violin and guitar string Chapter V Vibration properties of the wood and tuning of violin plates Chapter VI The function, tone, and tonal quality of the guitar Chapter VII The function of the violin Chapter VIII The tone and tonal quality of the violin Chapter IX Sound examples and simple experimental material – under preparation Webpage: http://www.speech.kth.se/music/acviguit4/index.html ACOUSTICS FOR VIOLIN AND GUITAR MAKERS Chapter 2 – Fundamentals of Acoustics RESONANCE AND RESONATORS Part 1: RESONANCE 2.1. Resonance 2.2. Vibration sensitivity 2.3. The mechanical and acoustical measures of the resonator 2.4. Summary 2.5. Key words Part 2: RESONATORS 2.6. The hole-volume resonator 2.7. Complex resonators 2.8. Mesurements of resonances in bars, plates and shells 2.9. Summary 2.10. Key words Jansson: Acoustics for violin and guitar makers 2.2 Chapter 2. FUNDAMENTALS OF ACOUSTICS - RESONANCE AND RESONATORS First part: RESONANCE INTRODUCTION In chapter 1, I presented the fundamental properties of sound and how these properties can be measured. Fundamental hearing sensations were connected to measurable sound properties. In this, the second chapter the concept of RESONANCE and of RESONATORS will be introduced. Resonators are fundamental building blocks of the sound generating systems such as the violin and the guitar. -
The Musical Kinetic Shape: a Variable Tension String Instrument
The Musical Kinetic Shape: AVariableTensionStringInstrument Ismet Handˇzi´c, Kyle B. Reed University of South Florida, Department of Mechanical Engineering, Tampa, Florida Abstract In this article we present a novel variable tension string instrument which relies on a kinetic shape to actively alter the tension of a fixed length taut string. We derived a mathematical model that relates the two-dimensional kinetic shape equation to the string’s physical and dynamic parameters. With this model we designed and constructed an automated instrument that is able to play frequencies within predicted and recognizable frequencies. This prototype instrument is also able to play programmed melodies. Keywords: musical instrument, variable tension, kinetic shape, string vibration 1. Introduction It is possible to vary the fundamental natural oscillation frequency of a taut and uniform string by either changing the string’s length, linear density, or tension. Most string musical instruments produce di↵erent tones by either altering string length (fretting) or playing preset and di↵erent string gages and string tensions. Although tension can be used to adjust the frequency of a string, it is typically only used in this way for fine tuning the preset tension needed to generate a specific note frequency. In this article, we present a novel string instrument concept that is able to continuously change the fundamental oscillation frequency of a plucked (or bowed) string by altering string tension in a controlled and predicted Email addresses: [email protected] (Ismet Handˇzi´c), [email protected] (Kyle B. Reed) URL: http://reedlab.eng.usf.edu/ () Preprint submitted to Applied Acoustics April 19, 2014 Figure 1: The musical kinetic shape variable tension string instrument prototype. -
A Comparison of Viola Strings with Harmonic Frequency Analysis
University of Nebraska - Lincoln DigitalCommons@University of Nebraska - Lincoln Student Research, Creative Activity, and Performance - School of Music Music, School of 5-2011 A Comparison of Viola Strings with Harmonic Frequency Analysis Jonathan Paul Crosmer University of Nebraska-Lincoln, [email protected] Follow this and additional works at: https://digitalcommons.unl.edu/musicstudent Part of the Music Commons Crosmer, Jonathan Paul, "A Comparison of Viola Strings with Harmonic Frequency Analysis" (2011). Student Research, Creative Activity, and Performance - School of Music. 33. https://digitalcommons.unl.edu/musicstudent/33 This Article is brought to you for free and open access by the Music, School of at DigitalCommons@University of Nebraska - Lincoln. It has been accepted for inclusion in Student Research, Creative Activity, and Performance - School of Music by an authorized administrator of DigitalCommons@University of Nebraska - Lincoln. A COMPARISON OF VIOLA STRINGS WITH HARMONIC FREQUENCY ANALYSIS by Jonathan P. Crosmer A DOCTORAL DOCUMENT Presented to the Faculty of The Graduate College at the University of Nebraska In Partial Fulfillment of Requirements For the Degree of Doctor of Musical Arts Major: Music Under the Supervision of Professor Clark E. Potter Lincoln, Nebraska May, 2011 A COMPARISON OF VIOLA STRINGS WITH HARMONIC FREQUENCY ANALYSIS Jonathan P. Crosmer, D.M.A. University of Nebraska, 2011 Adviser: Clark E. Potter Many brands of viola strings are available today. Different materials used result in varying timbres. This study compares 12 popular brands of strings. Each set of strings was tested and recorded on four violas. We allowed two weeks after installation for each string set to settle, and we were careful to control as many factors as possible in the recording process. -
Experiment 12
Experiment 12 Velocity and Propagation of Waves 12.1 Objective To use the phenomenon of resonance to determine the velocity of the propagation of waves in taut strings and wires. 12.2 Discussion Any medium under tension or stress has the following property: disturbances, motions of the matter of which the medium consists, are propagated through the medium. When the disturbances are periodic, they are called waves, and when the disturbances are simple harmonic, the waves are sinusoidal and are characterized by a common wavelength and frequency. The velocity of propagation of a disturbance, whether or not it is periodic, depends generally upon the tension or stress in the medium and on the density of the medium. The greater the stress: the greater the velocity; and the greater the density: the smaller the velocity. In the case of a taut string or wire, the velocity v depends upon the tension T in the string or wire and the mass per unit length µ of the string or wire. Theory predicts that the relation should be T v2 = (12.1) µ Most disturbances travel so rapidly that a direct determination of their velocity is not possible. However, when the disturbance is simple harmonic, the sinusoidal character of the waves provides a simple method by which the velocity of the waves can be indirectly determined. This determination involves the frequency f and wavelength λ of the wave. Here f is the frequency of the simple harmonic motion of the medium and λ is from any point of the wave to the next point of the same phase. -
Musical Acoustics - Wikipedia, the Free Encyclopedia 11/07/13 17:28 Musical Acoustics from Wikipedia, the Free Encyclopedia
Musical acoustics - Wikipedia, the free encyclopedia 11/07/13 17:28 Musical acoustics From Wikipedia, the free encyclopedia Musical acoustics or music acoustics is the branch of acoustics concerned with researching and describing the physics of music – how sounds employed as music work. Examples of areas of study are the function of musical instruments, the human voice (the physics of speech and singing), computer analysis of melody, and in the clinical use of music in music therapy. Contents 1 Methods and fields of study 2 Physical aspects 3 Subjective aspects 4 Pitch ranges of musical instruments 5 Harmonics, partials, and overtones 6 Harmonics and non-linearities 7 Harmony 8 Scales 9 See also 10 External links Methods and fields of study Frequency range of music Frequency analysis Computer analysis of musical structure Synthesis of musical sounds Music cognition, based on physics (also known as psychoacoustics) Physical aspects Whenever two different pitches are played at the same time, their sound waves interact with each other – the highs and lows in the air pressure reinforce each other to produce a different sound wave. As a result, any given sound wave which is more complicated than a sine wave can be modelled by many different sine waves of the appropriate frequencies and amplitudes (a frequency spectrum). In humans the hearing apparatus (composed of the ears and brain) can usually isolate these tones and hear them distinctly. When two or more tones are played at once, a variation of air pressure at the ear "contains" the pitches of each, and the ear and/or brain isolate and decode them into distinct tones. -
Science and the Stradivarius
FEATURES Stradivarius violins are among the most sought-after musical instruments in the world. But is there a secret that makes a Stradivarius sound so good, and can modern violins match the wonderful tonal quality of this great Italian instrument? Science and the Stradivarius Colin Gough IS TH ERE really a lost secret that sets Stradivarius 1 violin basics violins apart from the best instruments made today? After more than a hundred years of vigor- force rocks bridge ous debate, this question remains highly con- bowing tentious, provoking strongly held but divergent direction views among players, violin makers and scientists alike. All of the greatest violinists of modern times certainly believe it to be true, and invariably per- form on violins by Stradivari or Guarneri in pref- erence to modern instruments. Violins by the great Italian makers are, of course, beautiful works of art in their own right, and are coveted by collectors as well as players. Particularly outstanding violins have reputedly changed hands for over a million pounds. In con- (a) A copy of a Guarnerius violin made by the trast, fine modern instruments typically cost about 19th-century French violin maker Vuillaume, shown from the player's perspective. £ 10 000, while factory-made violins for beginners (b) A schematic cross-section of the violin at the can be bought for under £100. Do such prices bridge, with the acoustically important really reflect such large differences in quality? components labelled - including the "f-hole" The violin is the most highly developed and Helmholtz air resonance. most sophisticated of all stringed instruments. -
The Simulation of Piano String Vibration
The simulation of piano string vibration: From physical models to finite difference schemes and digital waveguides Julien Bensa, Stefan Bilbao, Richard Kronland-Martinet, Julius Smith Iii To cite this version: Julien Bensa, Stefan Bilbao, Richard Kronland-Martinet, Julius Smith Iii. The simulation of piano string vibration: From physical models to finite difference schemes and digital waveguides. Journal of the Acoustical Society of America, Acoustical Society of America, 2003, 114 (2), pp.1095-1107. 10.1121/1.1587146. hal-00088329 HAL Id: hal-00088329 https://hal.archives-ouvertes.fr/hal-00088329 Submitted on 1 Aug 2006 HAL is a multi-disciplinary open access L’archive ouverte pluridisciplinaire HAL, est archive for the deposit and dissemination of sci- destinée au dépôt et à la diffusion de documents entific research documents, whether they are pub- scientifiques de niveau recherche, publiés ou non, lished or not. The documents may come from émanant des établissements d’enseignement et de teaching and research institutions in France or recherche français ou étrangers, des laboratoires abroad, or from public or private research centers. publics ou privés. Distributed under a Creative Commons Attribution| 4.0 International License The simulation of piano string vibration: From physical models to finite difference schemes and digital waveguides Julien Bensa, Stefan Bilbao, Richard Kronland-Martinet, and Julius O. Smith III Center for Computer Research in Music and Acoustics (CCRMA), Department of Music, Stanford University, Stanford, California 94305-8180 A model of transverse piano string vibration, second order in time, which models frequency-dependent loss and dispersion effects is presented here. This model has many desirable properties, in particular that it can be written as a well-posed initial-boundary value problem ͑permitting stable finite difference schemes͒ and that it may be directly related to a digital waveguide model, a digital filter-based algorithm which can be used for musical sound synthesis. -
A Guide to Extended Techniques for the Violoncello - By
Where will it END? -Or- A guide to extended techniques for the Violoncello - By Dylan Messina 1 Table of Contents Part I. Techniques 1. Harmonics……………………………………………………….....6 “Artificial” or “false” harmonics Harmonic trills 2. Bowing Techniques………………………………………………..16 Ricochet Bowing beyond the bridge Bowing the tailpiece Two-handed bowing Bowing on string wrapping “Ugubu” or “point-tap” effect Bowing underneath the bridge Scratch tone Two-bow technique 3. Col Legno............................................................................................................21 Col legno battuto Col legno tratto 4. Pizzicato...............................................................................................................22 “Bartok” Dead Thumb-Stopped Tremolo Fingernail Quasi chitarra Beyond bridge 5. Percussion………………………………………………………….25 Fingerschlag Body percussion 6. Scordatura…………………………………………………….….28 2 Part II. Documentation Bibliography………………………………………………………..29 3 Introduction My intent in creating this project was to provide composers of today with a new resource; a technical yet pragmatic guide to writing with extended techniques on the cello. The cello has a wondrously broad spectrum of sonic possibility, yet must be approached in a different way than other string instruments, owing to its construction, playing orientation, and physical mass. Throughout the history of the cello, many resources regarding the core technique of the cello have been published; this book makes no attempt to expand on those sources. Divers resources are also available regarding the cello’s role in orchestration; these books, however, revolve mostly around the use of the instrument as part of a sonically traditional sensibility. The techniques discussed in this book, rather, are the so-called “extended” techniques; those that are comparatively rare in music of the common practice, and usually not involved within the elemental skills of cello playing, save as fringe oddities or practice techniques. -
LCC for Guitar - Introduction
LCC for Guitar - Introduction In order for guitarists to understand the significance of the Lydian Chromatic Concept of Tonal Organization and the concept of Tonal Gravity, one must first look at the nature of string vibration and what happens when a string vibrates. The Lydian Chromatic concept is based in the science of natural acoustics, so it is important to understand exactly what happens acoustically to a note and the harmonic overtones that nature creates. A guitar string (or any string from any stringed instrument) vibrates when plucked or struck, producing a tone. The vibrating string creates a natural resonant series of vibration patterns which are called Harmonics. When you strike the string by itself, it vibrates back and forth and moves air molecules, producing sound. This is called a FUNDAMENTAL. (See fig 1.01a) Fig 1.01a – FUNADAMENTAL/OPEN STRING = A 440hz/440cps The fundamental vibration pattern on a single string. This is the FUNDAMENTAL vibration or tone and can be equated to a fixed amount of vibrations or cycles per second (cps) For example, consider this to be the open ‘A’ string producing the note A which in turn a universally considered to vibrate at 440cps or the equivalent of 440hz. If you loosen a guitar string you can visually see the result of the vibrations; the string makes a wide arc near the center and it narrows towards each end. When you touch the string exactly in the center (exactly between both ends or on the guitar the physical location is at the 12 th fret) it divides the vibration exactly in half and produces a note or tone exactly one octave higher in pitch.