A Three-Stage Approach for Solving Location-Routing Problem in Hazardous Materials Transportation
Total Page:16
File Type:pdf, Size:1020Kb
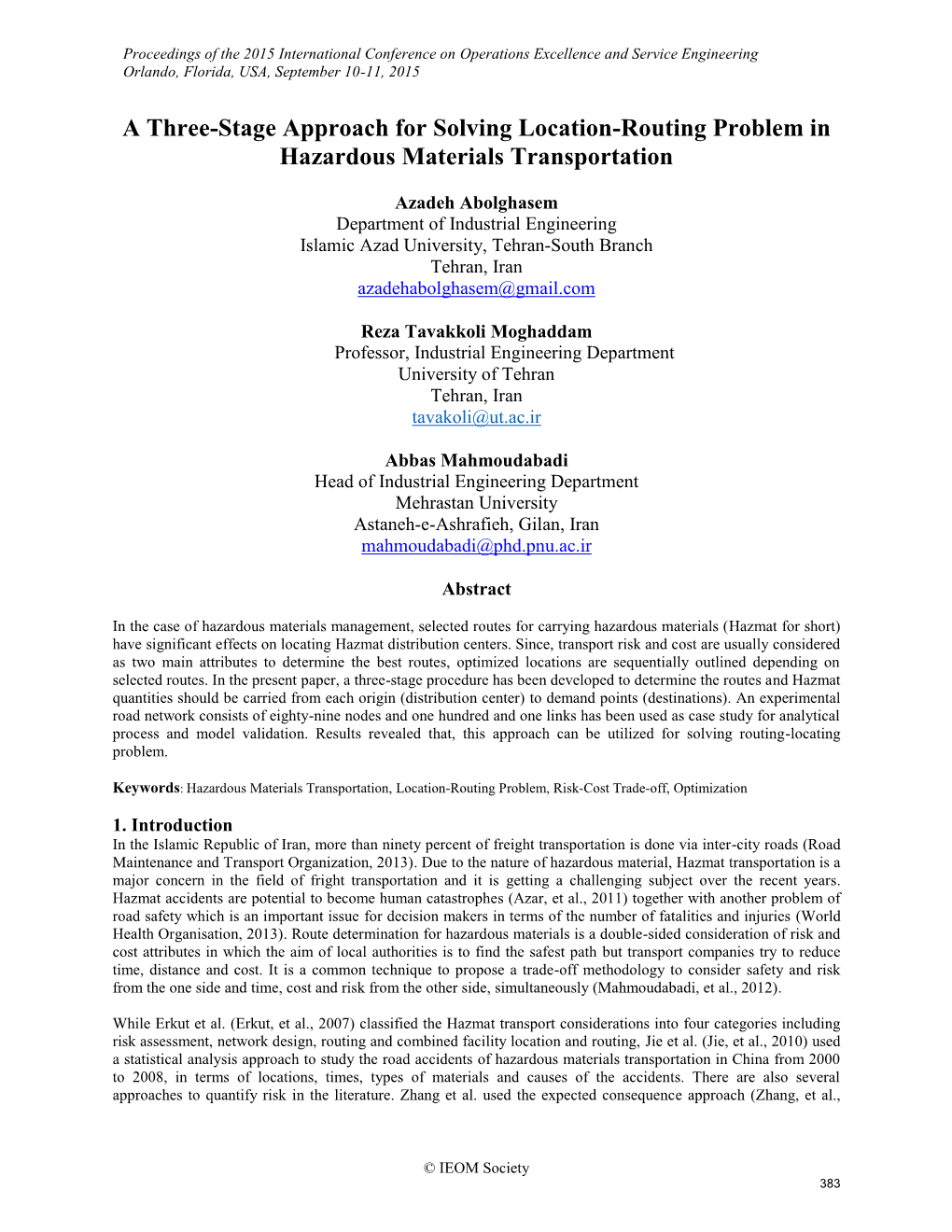
Load more
Recommended publications
-
And “Climate”. Qarah Dagh in Khorasan Ostan on the East of Iran 1
IRAN STATISTICAL YEARBOOK 1397 1. LAND AND CLIMATE Introduction T he statistical information that appeared in this of Tehran and south of Mazandaran and Gilan chapter includes “geographical characteristics and Ostans, Ala Dagh, Binalud, Hezar Masjed and administrative divisions” ,and “climate”. Qarah Dagh in Khorasan Ostan on the east of Iran 1. Geographical characteristics and aministrative and joins Hindu Kush mountains in Afghanistan. divisions The mountain ranges in the west, which have Iran comprises a land area of over 1.6 million extended from Ararat mountain to the north west square kilometers. It lies down on the southern half and the south east of the country, cover Sari Dash, of the northern temperate zone, between latitudes Chehel Cheshmeh, Panjeh Ali, Alvand, Bakhtiyari 25º 04' and 39º 46' north, and longitudes 44º 02' and mountains, Pish Kuh, Posht Kuh, Oshtoran Kuh and 63º 19' east. The land’s average height is over 1200 Zard Kuh which totally form Zagros ranges. The meters above seas level. The lowest place, located highest peak of this range is “Dena” with a 4409 m in Chaleh-ye-Loot, is only 56 meters high, while the height. highest point, Damavand peak in Alborz The southern mountain range stretches from Mountains, rises as high as 5610 meters. The land Khouzestan Ostan to Sistan & Baluchestan Ostan height at the southern coastal strip of the Caspian and joins Soleyman Mountains in Pakistan. The Sea is 28 meters lower than the open seas. mountain range includes Sepidar, Meymand, Iran is bounded by Turkmenistan, the Caspian Sea, Bashagard and Bam Posht Mountains. -
One Hundred New Species of Lichenized Fungi: a Signature of Undiscovered Global Diversity
Phytotaxa 18: 1–127 (2011) ISSN 1179-3155 (print edition) www.mapress.com/phytotaxa/ Monograph PHYTOTAXA Copyright © 2011 Magnolia Press ISSN 1179-3163 (online edition) PHYTOTAXA 18 One hundred new species of lichenized fungi: a signature of undiscovered global diversity H. THORSTEN LUMBSCH1*, TEUVO AHTI2, SUSANNE ALTERMANN3, GUILLERMO AMO DE PAZ4, ANDRÉ APTROOT5, ULF ARUP6, ALEJANDRINA BÁRCENAS PEÑA7, PAULINA A. BAWINGAN8, MICHEL N. BENATTI9, LUISA BETANCOURT10, CURTIS R. BJÖRK11, KANSRI BOONPRAGOB12, MAARTEN BRAND13, FRANK BUNGARTZ14, MARCELA E. S. CÁCERES15, MEHTMET CANDAN16, JOSÉ LUIS CHAVES17, PHILIPPE CLERC18, RALPH COMMON19, BRIAN J. COPPINS20, ANA CRESPO4, MANUELA DAL-FORNO21, PRADEEP K. DIVAKAR4, MELIZAR V. DUYA22, JOHN A. ELIX23, ARVE ELVEBAKK24, JOHNATHON D. FANKHAUSER25, EDIT FARKAS26, LIDIA ITATÍ FERRARO27, EBERHARD FISCHER28, DAVID J. GALLOWAY29, ESTER GAYA30, MIREIA GIRALT31, TREVOR GOWARD32, MARTIN GRUBE33, JOSEF HAFELLNER33, JESÚS E. HERNÁNDEZ M.34, MARÍA DE LOS ANGELES HERRERA CAMPOS7, KLAUS KALB35, INGVAR KÄRNEFELT6, GINTARAS KANTVILAS36, DOROTHEE KILLMANN28, PAUL KIRIKA37, KERRY KNUDSEN38, HARALD KOMPOSCH39, SERGEY KONDRATYUK40, JAMES D. LAWREY21, ARMIN MANGOLD41, MARCELO P. MARCELLI9, BRUCE MCCUNE42, MARIA INES MESSUTI43, ANDREA MICHLIG27, RICARDO MIRANDA GONZÁLEZ7, BIBIANA MONCADA10, ALIFERETI NAIKATINI44, MATTHEW P. NELSEN1, 45, DAG O. ØVSTEDAL46, ZDENEK PALICE47, KHWANRUAN PAPONG48, SITTIPORN PARNMEN12, SERGIO PÉREZ-ORTEGA4, CHRISTIAN PRINTZEN49, VÍCTOR J. RICO4, EIMY RIVAS PLATA1, 50, JAVIER ROBAYO51, DANIA ROSABAL52, ULRIKE RUPRECHT53, NORIS SALAZAR ALLEN54, LEOPOLDO SANCHO4, LUCIANA SANTOS DE JESUS15, TAMIRES SANTOS VIEIRA15, MATTHIAS SCHULTZ55, MARK R. D. SEAWARD56, EMMANUËL SÉRUSIAUX57, IMKE SCHMITT58, HARRIE J. M. SIPMAN59, MOHAMMAD SOHRABI 2, 60, ULRIK SØCHTING61, MAJBRIT ZEUTHEN SØGAARD61, LAURENS B. SPARRIUS62, ADRIANO SPIELMANN63, TOBY SPRIBILLE33, JUTARAT SUTJARITTURAKAN64, ACHRA THAMMATHAWORN65, ARNE THELL6, GÖRAN THOR66, HOLGER THÜS67, EINAR TIMDAL68, CAMILLE TRUONG18, ROMAN TÜRK69, LOENGRIN UMAÑA TENORIO17, DALIP K. -
Investigating the Factors Affecting the Selection of Grapevine Top-Wire Method in the Malekan - East Azerbaijan Gardens: Economic Growth
INTERNATIONAL JOURNAL OF SCIENTIFIC & TECHNOLOGY RESEARCH VOLUME 8, ISSUE 12, DECEMBER 2019 ISSN 2277-8616 Investigating The Factors Affecting The Selection Of Grapevine Top-Wire Method In The Malekan - East Azerbaijan Gardens: Economic Growth Sedigheh Asghari Baighout, Alireza Abdpour, Sandeep Kumar Gupta Serdar Vural UYGUN, Rabi Kuma5 Abstract: Grapes are one of the most important crops in Iran and the rest of the world. East Azerbaijan Province is one of the central provinces of grapevine production in Iran. In the province's Grape is a significant garden product in Malekan, so that the city has 65 % of the province production of the area and 7.2% of the country's grape production. Despite the advantages of the top wire method in grape production, the process of the top wire method in vineyards is prolonged. Therefore, in this research which is applied descriptive - correlation method for the study of the economic, social factors, individual and professional characteristics. Keywords: Logistic Regression, Effective Factors, Grapes, Malekan ———————————————————— 1. INTRODUCTION gardens. It is happening not only to the difference in Grapes are one of the most important crops in the world performance but also to the high quality of the and Iran. The world's grape cultivar is 7 million and 408 manufactured product in the top wire method than the thousand hectares, among the top 10 producing countries traditional method. As a result, the difference in the average of Spain's grapevine with a million and 200 thousand net income in the top wire method is significant compared hectares, France with 813 thousand hectares, Italy with 770 to the traditional one. -
Article a Catalog of Iranian Prostigmatic Mites of Superfamilies
Persian Journal of Acarology, Vol. 2, No. 3, pp. 389–474. Article A catalog of Iranian prostigmatic mites of superfamilies Raphignathoidea & Tetranychoidea (Acari) Gholamreza Beyzavi1*, Edward A. Ueckermann2 & 3, Farid Faraji4 & Hadi Ostovan1 1 Department of Entomology, Science and Research Branch, Islamic Azad University, Fars, Iran; E-mail: [email protected] 2 ARC-Plant Protection Research Institute, Private bag X123, Queenswood, Pretoria, 0121, South Africa; E-mail: [email protected] 3 School of Environmental Sciences and Development, Zoology, North-West University- Potchefstroom Campus, Potchefstroom, 2520, South Africa 4 MITOX Consultants, P. O. Box 92260, 1090 AG Amsterdam, The Netherlands * Corresponding author Abstract This catalog comprises 56 genera and 266 species of mite names of superfamilies Raphignathoidea and Tetranychoidea recorded from Iran at the end of January, 2013. Data on the mite distributions and habitats based on the published information are included. Remarks about the incorrect reports and nomen nudum species are also presented. Key words: Checklist, mite, habitat, distribution, Iran. Introduction Apparently the first checklist about mites of Iran was that of Farahbakhsh in 1961. Subsequently the following lists were published: “The 20 years researches of Acarology in Iran, List of agricultural pests and their natural enemies in Iran, A catalog of mites and ticks (Acari) of Iran and Injurious mites of agricultural crops in Iran” are four main works (Sepasgosarian 1977; Modarres Awal 1997; Kamali et al. 2001; Khanjani & Haddad Irani-Nejad 2006). Prostigmatic mites consist of parasitic, plant feeding and beneficial predatory species and is the major group of Acari in the world. Untill 2011, 26205 species were described in this suborder, of which 4728 species belong to the cohort Raphignathina and tetranychoid and raphignathoid mites include 2211 and 877 species respectively (Zhang et al. -
Mayors for Peace Member Cities 2021/10/01 平和首長会議 加盟都市リスト
Mayors for Peace Member Cities 2021/10/01 平和首長会議 加盟都市リスト ● Asia 4 Bangladesh 7 China アジア バングラデシュ 中国 1 Afghanistan 9 Khulna 6 Hangzhou アフガニスタン クルナ 杭州(ハンチォウ) 1 Herat 10 Kotwalipara 7 Wuhan ヘラート コタリパラ 武漢(ウハン) 2 Kabul 11 Meherpur 8 Cyprus カブール メヘルプール キプロス 3 Nili 12 Moulvibazar 1 Aglantzia ニリ モウロビバザール アグランツィア 2 Armenia 13 Narayanganj 2 Ammochostos (Famagusta) アルメニア ナラヤンガンジ アモコストス(ファマグスタ) 1 Yerevan 14 Narsingdi 3 Kyrenia エレバン ナールシンジ キレニア 3 Azerbaijan 15 Noapara 4 Kythrea アゼルバイジャン ノアパラ キシレア 1 Agdam 16 Patuakhali 5 Morphou アグダム(県) パトゥアカリ モルフー 2 Fuzuli 17 Rajshahi 9 Georgia フュズリ(県) ラージシャヒ ジョージア 3 Gubadli 18 Rangpur 1 Kutaisi クバドリ(県) ラングプール クタイシ 4 Jabrail Region 19 Swarupkati 2 Tbilisi ジャブライル(県) サルプカティ トビリシ 5 Kalbajar 20 Sylhet 10 India カルバジャル(県) シルヘット インド 6 Khocali 21 Tangail 1 Ahmedabad ホジャリ(県) タンガイル アーメダバード 7 Khojavend 22 Tongi 2 Bhopal ホジャヴェンド(県) トンギ ボパール 8 Lachin 5 Bhutan 3 Chandernagore ラチン(県) ブータン チャンダルナゴール 9 Shusha Region 1 Thimphu 4 Chandigarh シュシャ(県) ティンプー チャンディーガル 10 Zangilan Region 6 Cambodia 5 Chennai ザンギラン(県) カンボジア チェンナイ 4 Bangladesh 1 Ba Phnom 6 Cochin バングラデシュ バプノム コーチ(コーチン) 1 Bera 2 Phnom Penh 7 Delhi ベラ プノンペン デリー 2 Chapai Nawabganj 3 Siem Reap Province 8 Imphal チャパイ・ナワブガンジ シェムリアップ州 インパール 3 Chittagong 7 China 9 Kolkata チッタゴン 中国 コルカタ 4 Comilla 1 Beijing 10 Lucknow コミラ 北京(ペイチン) ラクノウ 5 Cox's Bazar 2 Chengdu 11 Mallappuzhassery コックスバザール 成都(チォントゥ) マラパザーサリー 6 Dhaka 3 Chongqing 12 Meerut ダッカ 重慶(チョンチン) メーラト 7 Gazipur 4 Dalian 13 Mumbai (Bombay) ガジプール 大連(タァリィェン) ムンバイ(旧ボンベイ) 8 Gopalpur 5 Fuzhou 14 Nagpur ゴパルプール 福州(フゥチォウ) ナーグプル 1/108 Pages -
Mohammad Mosaferi
CV Mohammad Mosaferi Professor of Environmental Health Tabriz University of Medical Sciences May, 2019 Mohammad Mosaferi Professor of Environmental Health Faculty: Health, Tabriz University of Medical Sciences Department: Environmental Health Engineering Location: Tabriz Areas of Expertise: Environmental Health Engineering ORCID ID:orcid.org/0000-0001-6251-147X ISI Research ID: L-6032-2017 Scopus Author ID: 23018932300 https://scholar.google.com/citations?user=X0WeEEEAAAAJ&hl=en H-index: 10(Scopus), 16(Google scholar) Contact Information: [email protected] , [email protected] Tel: +98 (41) 33355952, +989144148984 Fax: +98 (41) 33340634 Address: Department of Environmental Health Engineering, Health Faculty, Attar-e-Neyshaboori St. Tabriz, Iran Background and Education: B.Sc Environmental Health Engineering, College of Abureyhan, University of Tehran, Tehran, Iran(1996) M.Sc Environmental Health Engineering, University of Medical Science, Tehran, Iran (1999) Ph.D Environmental Health Engineering, University of Medical Science, Tehran, Iran (2005) Sabbatical leave London Arsenic Group, Research School of Earth Sciences at UCL-BIRKBECK, London, England, Sep 2004- Jan 2005 (Supervisor: Prof. Karen Hudson-Edwards) Research Interest: - Water Quality and Treatment - Arsenic in the Environment, Health Effects, Remediation - Environmental Epidemiology and geomedicine - Wastewater Treatment - Environmental and Health Impact Assessment - Waste Management - Passive defense Teaching: - Advanced and New Methods of Water Treatment, Processes -
Using Tolerated Risk for Solving Hazardous Material Routing Problem by Preemptive Goal Programming Approach
Proceedings of the 2016 International Conference on Industrial Engineering and Operations Management Kuala Lumpur, Malaysia, March 8-10, 2016 Using Tolerated Risk for Solving Hazardous Material Routing Problem by Preemptive Goal Programming Approach Abbas Mahmoudabadi Director, Master Program in Industrial Engineering MehrAstan University Astaneh-Ashrafieh, Gilan, Iran [email protected] Hassan Abdoos Deputy of Traffic Safety Department Road Maintenance and Transport Organization Tehran, Iran [email protected] Roozbeh Azizmohammadi Department of Industrial Engineering, Payame Noor University, Iran [email protected] Abstract— Route determination for hazardous material (Hazmat for short) transportation is a main concern in Hazmat management in which transport risk and cost are considered as the main attributes. The pre-defined priorities for risk and cost cause different mathematical models developed to determine the best routes which are not necessarily the shortest paths. In this paper, a tolerated risk usage is utilized to develop mathematical model for selecting the best route for carrying hazardous materials according to risk and path distance. Mathematical model has been developed using preemptive goal programming approach in which transport risk is considered more important than distance at the first step for developing model and route distance is minimized subject to pre-defined risk tolerance at the second stage. Experimental data including eighty-nine nodes and one- hundred and one links in a real network has been selected for numerical analysis and results have been discussed. Results revealed that there are some alternative routes when risk tolerance is getting to be increased or long distance paths used for hazardous materials transportation. In addition, using tolerated risk can satisfy both national/local authorities in hazmat management and transport companies as well. -
An Empirical Study on Empowering Private Bank Workers Using EFQM
Management Science Letters 2 (2012) 321–328 Contents lists available at GrowingScience Management Science Letters homepage: www.GrowingScience.com/msl An empirical study on empowering private bank workers using EFQM Jafar Beikzad, Yousef Majnooni Totakhaneh and Saeid Ghorbannejad Maleki* Department of Public Management, Islamic Azad University, Bonab branch, Bonab, Iran A R T I C L E I N F O A B S T R A C T Article history: Empowering workers play an essential role on increasing productivity in any organization. The Received June 15, 2011 service industries such as insurance companies or banks mostly rely on their own people to Received in Revised form retain their customers and incomes. The recent increasing trend on the number of private banks August, 10, 2011 in Iran has increased competition among existing banks. The banking industry strives to Accepted 12 August 2011 Available online empower its employees as much as possible in an attempt to maintain market share by not 16 August 2011 losing its customers. In this paper, we present an empirical study to detect the most important factors empowering bank employees. The study is implemented for a recently established Keywords: EFQM private bank with 228 people with 32 questions where 15 questions are focused on empowering Enabling employee employees. The results are analyzed using statistical tests and descriptive methods. The results Efficiency indicate that leadership, academic qualification, appropriate policy and strategy, cooperation Competition and processes play important role on empowering and enabling bank's employee. Organizational excellence © 2012 Growing Science Ltd. All rights reserved. 1. Introduction During the past few decades, there have been tremendous efforts on developing various quality based techniques on increasing productivity of organizations such as the Deming prize in Japan, the Malcolm Baldrige national quality award model in the USA, and the European quality award or EFQM excellence model in Europe (2003). -
20 New Candidates (For Evaluation in 2020)
20 New candidates (for evaluation in 2020) Bolivia: -Torotoro Brazil: -Caminhos dos Cânions do Sul -Serido China: -Longyan -Xingyi DPR Korea: -Mount Paektu Ecuador: -Napo Sumaco -Tungurahua France: -Armorique -Normandie-Maine Germany: -Ries Iran: -Aras Jordan: -Mujib Mexico : -Huasteca Potosina New Zealand: -Waitaki Whitestone Poland : -Land of Extinct Volcanoes Sweden: -Platåbergen Thailand: -Khorat UK: -Mourne Gullion Strangford Vietnam: -Ly Son-Sa Huynh 3 Extension requests < 10 %: Czech Republic : -Boheminan Paradise Germany: -Thuringia Inselsberg – Drei Gleichen -Vulkaneifel Disclaimer The Secretariat of UNESCO does not represent or endorse the accuracy of reliability of any advice, opinion, statement or other information or documentation provided by the States Parties to the Secretariat of UNESCO. The publication of any such advice, opinion, statement or other information documentation on the website and/or on working documents also does not imply the expression of any opinion whatsoever on the part of the Secretariat of UNESCO concerning the legal status of any country, territory, city or area or of its boundaries. Applicant UNESCO Global Geopark Torotoro, Bolivia Geographical and geological summary Location of the Torotoro Andean Geopark, Aspiring Unesco, in Central Bolivia, South America. Location of the Torotoro Andean Geopark, Aspiring Unesco, in Potosí Department, Bolivia. 1. Physical and human geography Aspiring Torotoro Andean Geopark, located in the Province Charcas, North of Potosí Department, Bolivia, has the same limits of the Municipality of Torotoro. The most used access occurs through the city of Cochabamba, whose distance is 134 km. From Potosí city, the distance is 552 km. The Torotoro's coordinates are 18°08'01"S and 65°45'47"W, and the area is 118,218 km². -
CV of Bakhtiar Feizizadeh
C V & Research output list P a g e | 1 C V & Research output list P a g e | 1 Curriculum Vitae of Bakhtiar Feizizadeh, born September 21rd 1981 in Malekan, Iran - Name: Bakhtiar Feizizadeh - Academic degree: Associated professor - ORCID: 0000-0002-3367-2925 - Number of publication up to 30. 06.2020: > 150 scientific papers - H-index: 14, Citation < 1730; - Phone, +98 09143058630, - E-Mail: [email protected], [email protected] - Languages: Turkish/Azerbaijani, Persian, English, basic skills in German and Arabic Education /Qualifications - 1.10. 2010- 28.5. 2014: PhD study in Applied Geoinformatics, Department of Geoinformatics, University of Salzburg, Austria. Supervised by Prof.Dr. Thomas Blaschke, PhD thesis topic: “Uncertainty, Sensitivity and Fuzzy Sets in GIS Multi- Criteria Decision Analysis” - 1.10.2012- 30.5. 2013: Scholar researcher and visiting PhD student, Center of GIS in Department of Geography, Supervised by Prof. Dr. Piotr Jankowski, San Diego State University (SDSU), California, USA. - 1.10. 2005-30.12. 2007: Master’s Degree in: Remote sensing and GIS, Department of Remote Sensing and GIS, University of Tabriz, Iran - 1.10. 2001-30.01. 2005: Bachelor’s Degree: Physical Geography (with honors), Department of Physical Geography, University of Tabriz, Iran. Awards - 2020. National Prize as top researcher of Iran, Ministry of Science, Research and Technology of Iran - 2019. Alexander Von Humboldt fellowship for experienced researchers. Germany, University of Humboldt Zu Berlin - 2019. National Prize as honored researcher of East Azerbaijan Provinces, Iran, Governance of East Azerbaijan Provinces - 2018. Prize of University of Tabriz as honoured researcher in 2018 - 2015. -
Outcomes of Community-Based Suicide Prevention Program In
Azizi et al. Int J Ment Health Syst (2021) 15:67 https://doi.org/10.1186/s13033-021-00492-w International Journal of Mental Health Systems RESEARCH Open Access Outcomes of community-based suicide prevention program in primary health care of Iran Hosein Azizi1,2,3* , Ali Fakhari2,4, Mostafa Farahbakhsh2, Elham Davtalab Esmaeili5 and Mohammad Mirzapour6 Abstract Background: Suicidal management and prevention in communities, especially in its frst stages, is an efective inter- vention for the health systems. However, in numerous societies most cases go undetected. Primary Health Care (PHC) is an efective place for the management of Suicide Prevention Programs (SPP). In Malekan County, a health com- munity assessment found suicide as the most important health problem. A regional SPP was performed for suicide prevention during 2014–2017. Methods: This study was carried out in six steps: (1) Establishing a research team, (2) Improving a registry for suicidal behaviors (SBs), (3) Identifying local determinants of SBs, (4) Training healthcare providers, (5) Follow-up and moni- toring of SBs, and (6) Public awareness campaigns. Our ultimate goal was to lower the rates of suicide, and suicide attempt (SA) by 15 and 20 %, respectively. Multiple logistic regression was used to estimate the adjusted odds ratios and the 95% confdence intervals. Results: A total of 821 SAs and 32 suicides were identifed. The gender distribution for suicides was 70% males whereas SAs were 64% among females. The majority of suicides occurred in spring 18 (56.25%) while summer was the most common season among SAs 288 (35.8%). Almost 62 and 75% of suicides and SAs have used hanging and poi- soning methods, respectively. -
Geomorphology of Jolfa-Hadishahr Plain
Islamic Azad University-Ahar Branch Geographic Space An Approved Scientific, Research-based Quarterly Davood Mokhtari1 Geomorphology of Jolfa-Hadishahr Plain Date received: 30 September 2013 Date accepted: 17 October 2013 Abstract To improve our understanding of geomorphological features, morphodynamic systems, Downloaded from geographical-space.iau-ahar.ac.ir at 7:53 IRST on Friday October 1st 2021 process-form relationships analysis, and in an aplication view: protection of biological capabilities of Jolfa-Hadishahr tectonic depression, we performed ergodic method and Facies Architecture Analysis in diverse spatial period. The plain has located between southern Aras river caostline and a part of Ghareh-Dagh mountain chain along Aras river. We forced our evolution reconstruction of landscape with field studies and 1 -Associate Professor, Marand Islamic Azad University and The Department of Geomorphology University of Tabriz. followed of strata surfaces of Quaternary sediments. The role of tectonic activities in plain construction and structure, resulting from tentional movements, plain landscape, and Quaternary alluvial fans structures and accomodation spaces are imparative. Results showed that tectonic activities and lithological properties are more effective factors on morphometric charactristics of geomorphologic units. The plain is a pedimont and the Dara-Diz alluvial fan is the main geomorphological unit on it. The deletion of Quaternary unconsolidated conglomerate cap deposits on marly Miocene formations is the main problem on the plain. The type of geomorphic response to human impacts on earth surface processes described here may represent a manifestation of geomorphic change. Keywords: Plain Geomorphology, Geomorphological Evolution, Fluvial Systems, Jolfa- Hadishahr Plain, Northwest of Iran. Downloaded from geographical-space.iau-ahar.ac.ir at 7:53 IRST on Friday October 1st 2021.