Exomars 2016 Mission Electrical Power System
Total Page:16
File Type:pdf, Size:1020Kb
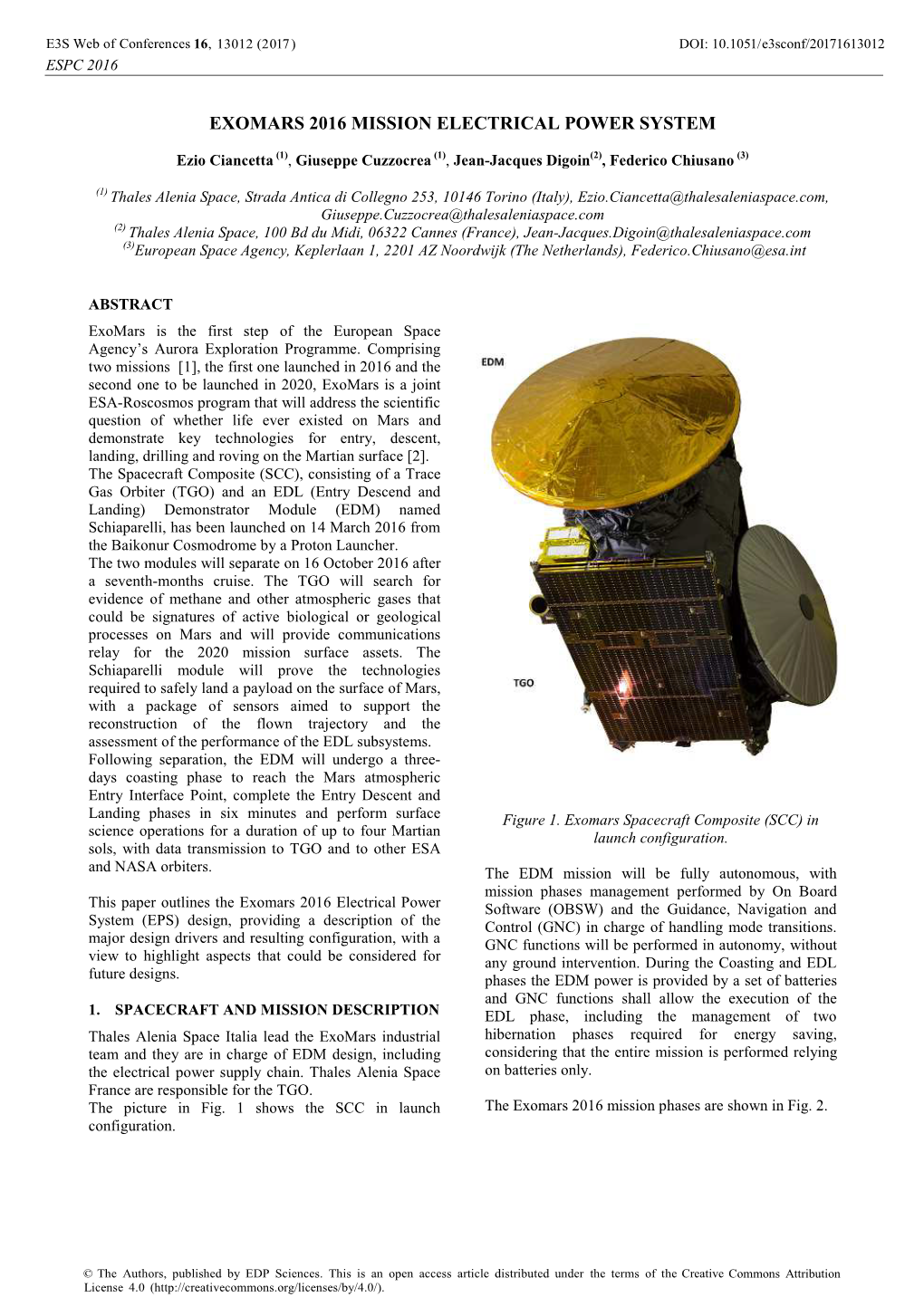
Load more
Recommended publications
-
Planetary Science Division Status Report
Planetary Science Division Status Report Jim Green NASA, Planetary Science Division January 26, 2017 Astronomy and Astrophysics Advisory CommiBee Outline • Planetary Science ObjecFves • Missions and Events Overview • Flight Programs: – Discovery – New FronFers – Mars Programs – Outer Planets • Planetary Defense AcFviFes • R&A Overview • Educaon and Outreach AcFviFes • PSD Budget Overview New Horizons exploresPlanetary Science Pluto and the Kuiper Belt Ascertain the content, origin, and evoluFon of the Solar System and the potenFal for life elsewhere! 01/08/2016 As the highest resolution images continue to beam back from New Horizons, the mission is onto exploring Kuiper Belt Objects with the Long Range Reconnaissance Imager (LORRI) camera from unique viewing angles not visible from Earth. New Horizons is also beginning maneuvers to be able to swing close by a Kuiper Belt Object in the next year. Giant IcebergsObjecve 1.5.1 (water blocks) floatingObjecve 1.5.2 in glaciers of Objecve 1.5.3 Objecve 1.5.4 Objecve 1.5.5 hydrogen, mDemonstrate ethane, and other frozenDemonstrate progress gasses on the Demonstrate Sublimation pitsDemonstrate from the surface ofDemonstrate progress Pluto, potentially surface of Pluto.progress in in exploring and progress in showing a geologicallyprogress in improving active surface.in idenFfying and advancing the observing the objects exploring and understanding of the characterizing objects The Newunderstanding of Horizons missionin the Solar System to and the finding locaons origin and evoluFon in the Solar System explorationhow the chemical of Pluto wereunderstand how they voted the where life could of life on Earth to that pose threats to and physical formed and evolve have existed or guide the search for Earth or offer People’sprocesses in the Choice for Breakthrough of thecould exist today life elsewhere resources for human Year forSolar System 2015 by Science Magazine as exploraon operate, interact well as theand evolve top story of 2015 by Discover Magazine. -
Exomars Schiaparelli Direct-To-Earth Observation Using GMRT
TECHNICAL ExoMars Schiaparelli Direct-to-Earth Observation REPORTS: METHODS 10.1029/2018RS006707 using GMRT S. Esterhuizen1, S. W. Asmar1 ,K.De2, Y. Gupta3, S. N. Katore3, and B. Ajithkumar3 Key Point: • During ExoMars Landing, GMRT 1Jet Propulsion Laboratory, California Institute of Technology, Pasadena, CA, USA, 2Cahill Center for Astrophysics, observed UHF transmissions and California Institute of Technology, Pasadena, CA, USA, 3National Centre for Radio Astrophysics, Pune, India Doppler shift used to identify key events as only real-time aliveness indicator Abstract During the ExoMars Schiaparelli separation event on 16 October 2016 and Entry, Descent, and Landing (EDL) events 3 days later, the Giant Metrewave Radio Telescope (GMRT) near Pune, India, Correspondence to: S. W. Asmar, was used to directly observe UHF transmissions from the Schiaparelli lander as they arrive at Earth. The [email protected] Doppler shift of the carrier frequency was measured and used as a diagnostic to identify key events during EDL. This signal detection at GMRT was the only real-time aliveness indicator to European Space Agency Citation: mission operations during the critical EDL stage of the mission. Esterhuizen, S., Asmar, S. W., De, K., Gupta, Y., Katore, S. N., & Plain Language Summary When planetary missions, such as landers on the surface of Mars, Ajithkumar, B. (2019). ExoMars undergo critical and risky events, communications to ground controllers is very important as close to real Schiaparelli Direct-to-Earth observation using GMRT. time as possible. The Schiaparelli spacecraft attempted landing in 2016 was supported in an innovative way. Radio Science, 54, 314–325. A large radio telescope on Earth was able to eavesdrop on information being sent from the lander to other https://doi.org/10.1029/2018RS006707 spacecraft in orbit around Mars. -
Mars Express Going Gyroless - Impact on Science Operations Systems
EPSC Abstracts Vol. 12, EPSC2018-1048, 2018 European Planetary Science Congress 2018 EEuropeaPn PlanetarSy Science CCongress c Author(s) 2018 Mars Express going Gyroless - Impact on science operations systems C.Muñiz Solaz (1), A.Cardesin (1), J.Marin-Yaseli de la Parra (1), M.Costa i Sitjà (1), D.Merritt (1), M.Castillo (1), M.G.Breitfellner (1), E.Grotheer (1), P.Martin(1), F. Nespoli (1), M.Kueppers(1), G.Buenadicha(1), B. Geiger (1), D.Titov(2) (1) ESA European Space Astronomy Centre (ESAC), Camino bajo del Castillo s/n, Urb. Villafranca del Castillo, P.O. Box 78, 28691 Villanueva de la Cañada, Madrid, Spain ([email protected] / T: +34-91-8131349) (2) European Space Research and Technology Centre (ESTEC), Keplerlaan 1, 2201 AZ Noordwijk ZH, Netherlands Abstract tions of its gyroscopes, thereby extending the mission lifetime. MEX was never designed to fly without its Mars Express was originally designed to explore Mars gyros continuously available, therefore an AOCS up- for a period of 1 Martian year. The mission has been grade was necessary to avoid an end of mission fore- very successful and has been extended in several oc- cast in early 2019. This software update not only af- casions and today it has been flying for more than fects the spacecraft operations but also the science op- 15 years. Due to its long lifetime in space the gy- erations, including procedures and planning processes. ros had started to degrade, and a decision was made The Science Ground Segment (SGS) team, located to extend the spacecraft lifetime by developing a new at the European Space Astronomy Centre (ESAC) near AOCS software to allow for switching off the gyros Madrid (Spain), is responsible for the generation, co- during an extended part of the operations, thereby re- ordination and maintenance of the overall scientific ducing the duty cycle of the IMUs. -
Exomars Trace Gas Orbiter Operations ESOC
Training Opportunity for Swiss Trainees Reference Title Duty Station CH-2019-OPS-OPE Exomars Trace Gas Orbiter operations ESOC Overview of the unit’s mission: OPS-OP is responsible for mission preparation and flight operations for the ESA fleet of solar and interplanetary spacecraft. The division currently operates four missions (Cluster, Mars Express, ExoMars TGO, Bepi Colombo) and prepares for the launch of three others (Solar Orbiter, ExoMars Rover and Surface Platform, JUICE). Within OPS-OP, the ExoMars TGO unit (OPS-OPE) is responsible for the operations of the Trace Gas Orbiter (TGO) in-orbit around Mars. This includes monitoring, control and mission planning of the satellite as well as the mission responsibility for the required data systems and related interfaces. Overview of the field of activity proposed: The ExoMars TGO is the first in a series of Mars missions undertaken jointly by ESA and Roscosmos. From its 400-km- altitude science orbit TGO shall gain a better understanding of methane and other atmospheric gases present in small concentrations (less than 1% of the atmosphere) which could be evidence for possible biological or geological activity. The Orbiter is also an invaluable Mars telecommunications asset, currently providing communication services to NASA rovers (or landers) on the Mars Surface: it acts as a data relay hub for sending commands to the rovers and downloading rover data to Earth using ESA, NASA and Russian space communication networks. This relay function will serve the ExoMars 2020 mission, combining a European Rover and a Russian science Surface Platform, planned to land on Mars in March 2021. -
Exomars 2016 TGO and Schiaparelli
ESA UNCLASSIFIED – For Official Use estec European Space Research and Technology Centre Keplerlaan 1 2201 AZ Noordwijk The Netherlands T +31 (0)71 565 6565 F +31 (0)71 565 6040 www.esa.int ExoMars 2016 Mission Brief description of TGO and Schiaparelli Prepared by H. Svedhem (SCI-S), K. O’Flaherty (SCI-S) Reference EXM-MS-REP-RSSD-001_TGO-EDM-Description_Iss.1 Issue 1 Revision 0 Date of Issue 28/01/2016 Status 1 Document Type RP Distribution ESA UNCLASSIFIED – For Official Use Reason for change Issue Revision Date Original issue 1 0 4/02/2016 Issue 1 Revision 0 Reason for change Date Pages Paragraph(s) Page 2/20 ExoMars 2016 Mission - Brief description of TGO and Schiaparelli Date: 4/02/2016 Issue 1 Revision 0 ESA UNCLASSIFIED – For Official Use Table of contents: 1 INTRODUCTION ....................................................................................... 4 2 EXOMARS TRACE GAS ORBITER AND SCHIAPARELLI MISSION (2016) . 5 3 EXOMARS TRACE GAS ORBITER (TGO) .................................................. 9 4 EXOMARS TRACE GAS ORBITER INSTRUMENTS .................................. 10 5 SCHIAPARELLI: THE EXOMARS ENTRY, DESCENT AND LANDING DEMONSTRATOR MODULE ........................................................................ 12 6 SCHIAPARELLI SCIENCE PACKAGE AND SCIENCE INVESTIGATIONS17 Page 3/20 ExoMars 2016 Mission - Brief description of TGO and Schiaparelli Date: 4/02/2016 Issue 1 Revision 0 ESA UNCLASSIFIED – For Official Use 1 INTRODUCTION This document presents a brief summary of the ExoMars 2016 mission and its two major elements, the Trace Gas Orbiter, TGO, and the Entry descent and landing Demonstrator Model, EDM, - Schiaparelli. It also gives an overview of the TGO and Schiaparelli scientific investigations and the corresponding instruments. The text is derived from information available on the ESA Exploration web-site, http://exploration.esa.int/mars/. -
Exploration of Mars by the European Space Agency 1
Exploration of Mars by the European Space Agency Alejandro Cardesín ESA Science Operations Mars Express, ExoMars 2016 IAC Winter School, November 20161 Credit: MEX/HRSC History of Missions to Mars Mars Exploration nowadays… 2000‐2010 2011 2013/14 2016 2018 2020 future … Mars Express MAVEN (ESA) TGO Future ESA (ESA- Studies… RUSSIA) Odyssey MRO Mars Phobos- Sample Grunt Return? (RUSSIA) MOM Schiaparelli ExoMars 2020 Phoenix (ESA-RUSSIA) Opportunity MSL Curiosity Mars Insight 2020 Spirit The data/information contained herein has been reviewed and approved for release by JPL Export Administration on the basis that this document contains no export‐controlled information. Mars Express 2003-2016 … First European Mission to orbit another Planet! First mission of the “Rosetta family” Up and running since 2003 Credit: MEX/HRSC First European Mission to orbit another Planet First European attempt to land on another Planet Original mission concept Credit: MEX/HRSC December 2003: Mars Express Lander Release and Orbit Insertion Collission trajectory Bye bye Beagle 2! Last picture Lander after release, release taken by VMC camera Insertion 19/12/2003 8:33 trajectory Credit: MEX/HRSC Beagle 2 was found in January 2015 ! Only 6km away from landing site OK Open petals indicate soft landing OK Antenna remained covered Lessons learned: comms at all time! Credit: MEX/HRSC Mars Express: so many missions at once Mars Mission Phobos Mission Relay Mission Credit: MEX/HRSC Mars Express science investigations Martian Moons: Phobos & Deimos: Ionosphere, surface, -
The Pancam Instrument for the Exomars Rover
ASTROBIOLOGY ExoMars Rover Mission Volume 17, Numbers 6 and 7, 2017 Mary Ann Liebert, Inc. DOI: 10.1089/ast.2016.1548 The PanCam Instrument for the ExoMars Rover A.J. Coates,1,2 R. Jaumann,3 A.D. Griffiths,1,2 C.E. Leff,1,2 N. Schmitz,3 J.-L. Josset,4 G. Paar,5 M. Gunn,6 E. Hauber,3 C.R. Cousins,7 R.E. Cross,6 P. Grindrod,2,8 J.C. Bridges,9 M. Balme,10 S. Gupta,11 I.A. Crawford,2,8 P. Irwin,12 R. Stabbins,1,2 D. Tirsch,3 J.L. Vago,13 T. Theodorou,1,2 M. Caballo-Perucha,5 G.R. Osinski,14 and the PanCam Team Abstract The scientific objectives of the ExoMars rover are designed to answer several key questions in the search for life on Mars. In particular, the unique subsurface drill will address some of these, such as the possible existence and stability of subsurface organics. PanCam will establish the surface geological and morphological context for the mission, working in collaboration with other context instruments. Here, we describe the PanCam scientific objectives in geology, atmospheric science, and 3-D vision. We discuss the design of PanCam, which includes a stereo pair of Wide Angle Cameras (WACs), each of which has an 11-position filter wheel and a High Resolution Camera (HRC) for high-resolution investigations of rock texture at a distance. The cameras and electronics are housed in an optical bench that provides the mechanical interface to the rover mast and a planetary protection barrier. -
Investigating Mars' Atmosphere Using the NOMAD Instrument on The
Investigating Mars’ atmosphere using the NOMAD instrument on the ExoMars Trace Gas Orbiter Supervision team: Dr Manish Patel, Dr Stephen Lewis, Dr Jonathon Mason External supervisor: N/A Lead contact: [email protected] Description: This project provides the opportunity to be directly involved in an active space mission and play a key role in the preparation and exploitation of results from a spaceflight instrument on the ESA ExoMars Trace Gas Orbiter mission, which is currently in orbit around Mars. The project will involve supporting work on: - Continued development of a radiative transfer model of the martian atmosphere in preparation for ExoMars - Characterisation of Flight Spare instrumentation and data interpretation from mid-cruise checkouts - Preparation of new techniques for retrieval of atmospheric species - Exploitation of data returned from the NOMAD-UVIS instrument This mission is aimed at furthering our understanding of the composition and dynamics of the martian environment, through the measurement of trace gases such as ozone and methane in the martian atmosphere from orbit. The project relates to the UVIS channel of the NOMAD instrument; UVIS is an optical spectrometer led by the Open University to measure solar radiation travelling through the martian atmosphere at UV and visible wavelengths, in order to detect and map the presence of ozone, dust and ice clouds in the atmosphere of Mars in unprecedented detail. This project will involve scope for a wide range of potential research from instrument testing through to exploitation of real spaceflight instrument data. The focus of the project is on the retrieval of ozone and aerosol abundance and properties from spectra that will be returned from the UVIS instrument. -
Soyuz Launch Brochure
Incredible Adventures is excited to offer a unique opportunity – a chance to visit the famous Baikonur Cosmodrome and observe a manned launch of a Russian Soyuz spacecraft. You’ll be completely immersed in the electric atmosphere surrounding a launch. You’ll explore Baikonur’s launch sites, museums and most historic places. Join IA for an Incredible Space Adventure. Highlights of Your Incredible Baikonur Adventure 800-644-7382 or 941-346-2603 www.incredible-adventures.com Observe roll-out and installation of the Soyuz rocket at launch pad. Attend international press conference of main and back- up crews. See the farewell of the crew at the cosmonaut hotel. Hear crew's ready-to-go official report. See launch of the Soyuz rocket, something you’ll never forget. Incredible Baikonur Adventure Day 1 Meet IA representative at the airport. Flight from Moscow to Baikonur .Transfer to the hotel. Time to relax. Day 2 Breakfast in the hotel Transfer to Baikonur Cosmodrome Roll-out of the Soyuz Rocket. (Follow the Soyuz to its launch site.) Observe installation of the rocket on the launch pad. Visit to the integration building of Soyuz and Progress spaceships. Transfer back to town. Visit to the International Space School. 9 Day 3 Breakfast in the hotel. Visit Museum of History Cosmodrome Baikonur. Enjoy general sightseeing in the town of Baikonur (learn history of the town, visit memorials and monuments). Transfer to Cosmonaut hotel. International press conference with the main and backup crews of Soyuz-TMA vehicle. Walk along the historical alley of Cosmonauts where personalized trees are planted. -
ESA's Planetary Science Archive
EPSC Abstracts Vol. 8, EPSC2013-626, 2013 European Planetary Science Congress 2013 EEuropeaPn PlanetarSy Science CCongress c Author(s) 2013 ESA’s Planetary Science Archive: Status, Activities and Plans. D. J. Heather, M. Barthelemy, N. Manaud, S. Martinez, M. Szumlas, J.L. Vazquez, P. Osuna and the PSA Development Team. European Space Agency, ESAC, Villafranca del Castillo, 28080 Madrid, Spain ([email protected]) 1. Introduction this project, using the upcoming BepiColombo mission to develop our first PDS4 data models. The The European Space Agency’s Planetary Science PDS4 Data Standards aim to provide a framework for Archive (PSA) is the central repository for all capturing planetary science data results in scientific and engineering data returned by ESA’s international archives based on a homogeneous set of planetary missions, making them accessible to the standards that can be extended as needed for world-wide scientific community. The PSA international usage. currently holds data from Mars Express, Venus Express, SMART-1, Huygens, Rosetta and Giotto, as 3. Ensuring long term preservation well as several ground-based cometary observations. It will be used for archiving on ExoMars, The long-term preservation of data and knowledge BepiColombo and for the European contributions to from all of ESA’s planetary missions is a core focus. Chandrayaan-1. This presentation will outline the All data provided within the Planetary Science current status of the PSA, activities underway to Archive are therefore passed through a set of improve our services and plans for the future. rigorous procedures designed to ensure the usability of the data not only at the time of ingestion, but also 2. -
First Year of Coordinated Science Observations by Mars Express and Exomars 2016 Trace Gas Orbiter
MANUSCRIPT PRE-PRINT Icarus Special Issue “From Mars Express to ExoMars” https://doi.org/10.1016/j.icarus.2020.113707 First year of coordinated science observations by Mars Express and ExoMars 2016 Trace Gas Orbiter A. Cardesín-Moinelo1, B. Geiger1, G. Lacombe2, B. Ristic3, M. Costa1, D. Titov4, H. Svedhem4, J. Marín-Yaseli1, D. Merritt1, P. Martin1, M.A. López-Valverde5, P. Wolkenberg6, B. Gondet7 and Mars Express and ExoMars 2016 Science Ground Segment teams 1 European Space Astronomy Centre, Madrid, Spain 2 Laboratoire Atmosphères, Milieux, Observations Spatiales, Guyancourt, France 3 Royal Belgian Institute for Space Aeronomy, Brussels, Belgium 4 European Space Research and Technology Centre, Noordwijk, The Netherlands 5 Instituto de Astrofísica de Andalucía, Granada, Spain 6 Istituto Nazionale Astrofisica, Roma, Italy 7 Institut d'Astrophysique Spatiale, Orsay, Paris, France Abstract Two spacecraft launched and operated by the European Space Agency are currently performing observations in Mars orbit. For more than 15 years Mars Express has been conducting global surveys of the surface, the atmosphere and the plasma environment of the Red Planet. The Trace Gas Orbiter, the first element of the ExoMars programme, began its science phase in 2018 focusing on investigations of the atmospheric composition with unprecedented sensitivity as well as surface and subsurface studies. The coordination of observation programmes of both spacecraft aims at cross calibration of the instruments and exploitation of new opportunities provided by the presence of two spacecraft whose science operations are performed by two closely collaborating teams at the European Space Astronomy Centre (ESAC). In this paper we describe the first combined observations executed by the Mars Express and Trace Gas Orbiter missions since the start of the TGO operational phase in April 2018 until June 2019. -
Mars Insight Launch Press Kit
Introduction National Aeronautics and Space Administration Mars InSight Launch Press Kit MAY 2018 www.nasa.gov 1 2 Table of Contents Table of Contents Introduction 4 Media Services 8 Quick Facts: Launch Facts 12 Quick Facts: Mars at a Glance 16 Mission: Overview 18 Mission: Spacecraft 30 Mission: Science 40 Mission: Landing Site 53 Program & Project Management 55 Appendix: Mars Cube One Tech Demo 56 Appendix: Gallery 60 Appendix: Science Objectives, Quantified 62 Appendix: Historical Mars Missions 63 Appendix: NASA’s Discovery Program 65 3 Introduction Mars InSight Launch Press Kit Introduction NASA’s next mission to Mars -- InSight -- will launch from Vandenberg Air Force Base in California as early as May 5, 2018. It is expected to land on the Red Planet on Nov. 26, 2018. InSight is a mission to Mars, but it is more than a Mars mission. It will help scientists understand the formation and early evolution of all rocky planets, including Earth. A technology demonstration called Mars Cube One (MarCO) will share the launch with InSight and fly separately to Mars. Six Ways InSight Is Different NASA has a long and successful track record at Mars. Since 1965, it has flown by, orbited, landed and roved across the surface of the Red Planet. None of that has been easy. Only about 40 percent of the missions ever sent to Mars by any space agency have been successful. The planet’s thin atmosphere makes landing a challenge; its extreme temperature swings make it difficult to operate on the surface. But if a spacecraft survives the trip, there’s a bounty of science to be collected.