Nine Examples of Project-Based Innovation by Australian Contractors ‰Contents
Total Page:16
File Type:pdf, Size:1020Kb
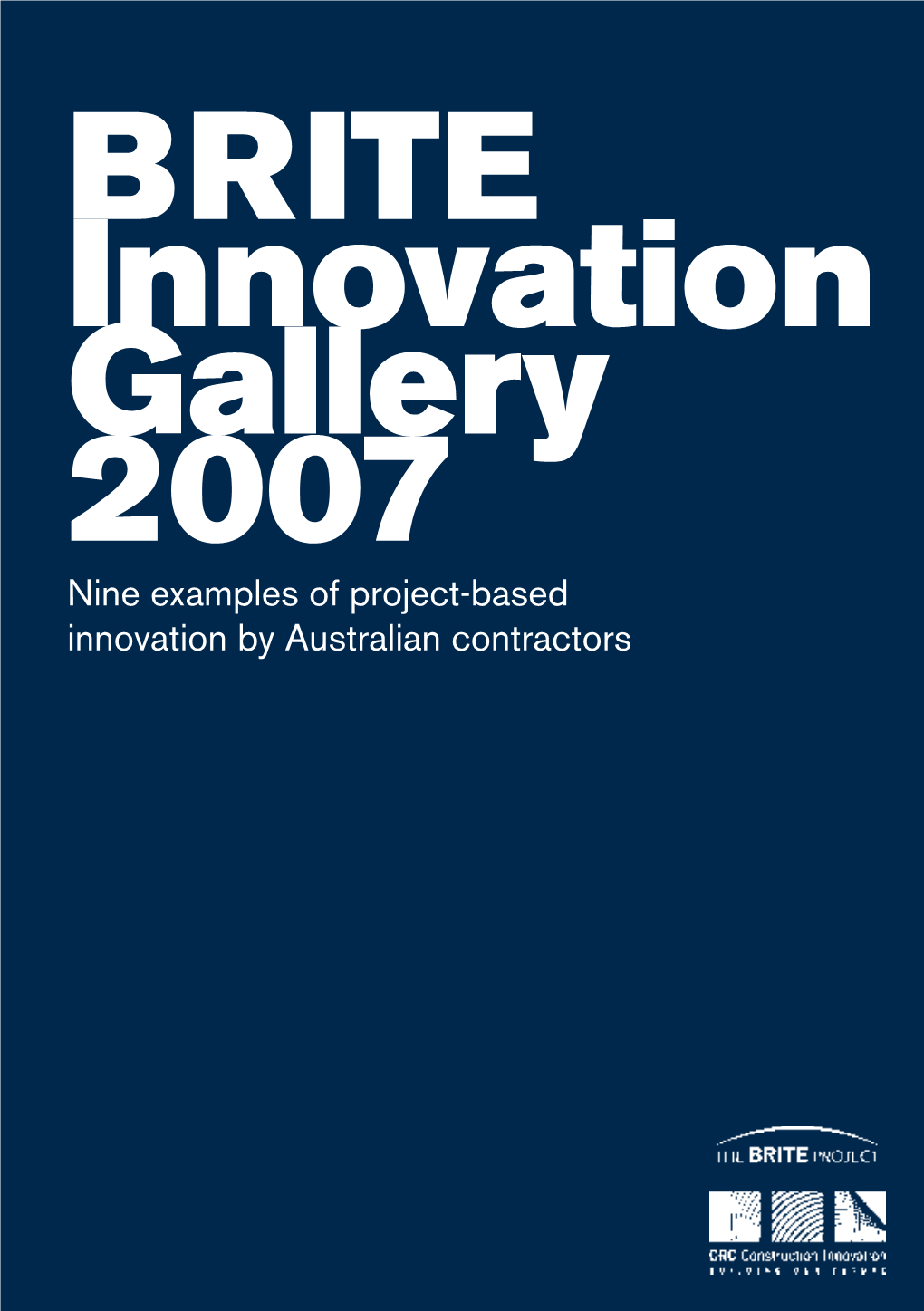
Load more
Recommended publications
-
Study Tours at UOW College UOW COLLEGE STUDY TOURS Study Tour Programs Wollongong
Study Tours at UOW College UOW COLLEGE STUDY TOURS Study Tour Programs Wollongong UOW College Study Tours are a great way to improve your English through Wollongong is a culturally diverse city that has a vibrant and welcoming community where visitors come from all over the world to live, work intercultural exchange and to experience the Australian culture firsthand. and study. Located on the coast just 80 kilometres south of Sydney, Wollongong is the third largest city in New South Wales, Australia. Positioned between the foothills of the Illawarra Escarpment and the Pacific Ocean, it has an abundance of outdoor recreational activities. Our tailored itineraries allow students to: The city is large enough to offer all the facilities, entertainment, • Practice English language skills through lively restaurants and conveniences of a major city, yet small enough to and interactive lessons retain the friendly, relaxed atmosphere of a coastal community. • Enjoy the Australian way of life • Visit local schools and make new friends • Learn outside the class room through cultural activities, industry visits and volunteer opportunities • Experience nature and meet our local wildlife • Stay with local families We are experienced in designing and delivering tailored English language training for specific cohorts through group programs. These tailored programs combine discipline-specific English language training with cultural activities to provide a contextual learning experience. ATTRACTIONS Patrolled beaches • Sea Cliff Bridge and Grand Pacific Drive • Skydive the beach • Illawarra Escarpment bushwalks • Coastal cycleway and walking Component of the Study Tour Program tracks • Botanic Gardens • Science Centre and Planetarium • Steelworks tours • 11 national parks within 50km • Free Wollongong city shuttle bus 1. -
Guide to Cycling in the Illawarra
The Illawarra Bicycle Users Group’s Guide to cycling in the Illawarra Compiled by Werner Steyer First edition September 2006 4th revision August 2011 Copyright Notice: © W. Steyer 2010 You are welcome to reproduce the material that appears in the Tour De Illawarra cycling guide for personal, in-house or non-commercial use without formal permission or charge. All other rights are reserved. If you wish to reproduce, alter, store or transmit material appearing in the Tour De Illawarra cycling guide for any other purpose, request for formal permission should be directed to W. Steyer 68 Lake Entrance Road Oak Flats NSW 2529 Introduction This cycling ride guide and associated maps have been produced by the Illawarra Bicycle Users Group incorporated (iBUG) to promote cycling in the Illawarra. The ride guides and associated maps are intended to assist cyclists in planning self- guided outings in the Illawarra area. All persons using this guide accept sole responsibility for any losses or injuries uncured as a result of misinterpretations or errors within this guide Cyclist and users of this Guide are responsible for their own actions and no warranty or liability is implied. Should you require any further information, find any errors or have suggestions for additional rides please contact us at www.ibug,org.com Updated ride information is available form the iBUG website at www.ibug.org.au As the conditions may change due to road and cycleway alteration by Councils and the RTA and weather conditions cyclists must be prepared to change their plans and riding style to suit the conditions encountered. -
Grand Pacific Drive
SOUTH COAST Right: Tigers by the pool at Symbio Wildlife Park. reptiles, which are sure to captivate visitors of all ages. Also from Stanwell Tops it’s a downhill swoop to Sea Cliff Bridge, a highlight of the Grand Pacifi c Drive. This $52 million cantilever bridge was completed in 2005, after subsidence forced the existing road to close. In its place is a 665-metre-long engineering Wollongong’s best beaches. Austinmer, of prawns at one of Wollongong’s feat that curves around the cliffs or “Austi” to locals, is the pick of the waterfront eateries. 50 metres out to sea. It’s fun to drive, area’s beaches. Framed by pines, it’s The Grand Pacifi c Drive continues but even better to get out and walk an iconic slice of Australia: a perfectly its beachy way south to Nowra, but the purpose-built pedestrian sidewalk, curved beach, crystal clear rockpool and to really appreciate the drive south it’s Left: Aerial view of the Sea Cliff Bridge, part of the Grand Pacifi c Drive. Photo: Dee Kramer Photography/Tourism Wollongong. with parking provided at either end. the salty smell of fi sh and chips. best to spend a few nights. Above: View from Stanwell Tops overlooking beach and coastline. Back in the car again, you are now Keep following the big brown signs If it’s time to turn back, you can Photo: Hamilton Lund/Destination NSW. in Scarborough, a charming old coal of the Grand Pacifi c Drive, which artfully retrace your steps or else take the mining village, the pride of which is the sticks to the lesser-traffi cked coast freeway back to Sydney. -
Great Drives in New South Wales
GREAT DRIVES IN NSW Enjoy the sheer pleasure of the journey on inspirational drives in NSW. Visitors will discover views, wildlife, national parks full of natural wonders, beaches that are the envy of world and quiet country towns with stories to tell. Essential lifestyle ingredients such as wineries, great regional dining and fantastic places to spend the night cap it all off. Take your time and discover a State that is full of adventures. Discover more road trip inspiration with the Destination NSW trip and itinerary planner at: www.visitnsw.com/roadtrips The Legendary Pacific Coast Fast facts A scenic coastal drive north from Sydney to Brisbane Alternatively, fly to Newcastle, Ballina Byron or the Gold Coast and hire a car Drive length: 940km. Toowoon Bay, Central Coast Why drive it? This scenic drive takes you through some of the most striking landscapes in NSW, an almost continuous line of surf beaches, national parks and a hinterland of rolling green hills and friendly villages. The Legendary Pacific Coast has many possible themed itineraries: Coastal and Aquatic Trail Culture, Arts and Heritage Trail Food and Wine and Farmers’ Gate Journey Legendary Kids Trail National Parks and State Forests Nature Trail Legendary Surfing Safari Backpacker and Working Holiday Trail Whale-watching Trail. What can visitors do along the way? On the Central Coast, drop into a wildlife or reptile park to meet Newcastle Ocean Baths, Newcastle Australia’s native animals Stop off at Hunter Valley for cellar door wine tastings and award-winning -
This Is Who We Are This Is Who We Are at UOW, We Believe in the Power of Connecting People, Ideas and Places to Change Things for the Better
this is who we are this is who we are At UOW, we believe in the power of connecting people, ideas and places to change things for the better. CONTENTS 1 OUR ACHIEVEMENTS / 6 OUR HOME: WOLLONGONG 28 KEY FACILITIES AT A GLANCE & THE ILLAWARRA REGION 33 GLOBAL PARTNERSHIPS 3 A MESSAGE FROM THE 10 PRINCIPAL OFFICERS 38 COMMUNITY VICE-CHANCELLOR 11 OUR FACULTIES PARTNERSHIPS 4 OUR HOME: THE 17 OUR CAMPUSES 40 THE STUDENT UNIVERSITY WE BUILT 22 RESEARCH & IMPACT EXPERIENCE OUR ACHIEVEMENTS GLOBALLY TOP 2% OF GLOBALLY RATED TOP 2% FOR RANKED AS ONE UNIVERSITIES IN A FIVE-STAR RESEARCH QUALITY OF AUSTRALIA’S THE WORLD UNIVERSITY § 314th in the world for BEST MODERN § 276th in the world – § 5 Star rating – QS World research quality – 2014 UNIVERSITIES QS World University University Rankings Leiden Ranking § 22nd in the world – Rankings 2013/2014 2012/2013 QS Top 50 Under 50 § 276–300 band – Times § 1st in Australia for Rankings 2014 Higher Education World Educational Experience § 33rd in the world – University Rankings and Graduate Outcomes Times Higher Education 2013/2014 – Australian Good Universities Guide 2013 Top 100 Under 50 § 352nd in the world – Rankings 2014 Academic Ranking of World Universities (ARWU) 2013 AT A GLANCE 30,038 112,302 1,874 85km total student enrolment UOW Alumni subjects to Sydney Opera House (53 miles) 11,631 213 94.6% 27°C International students enrolled academic and research of students indicated that they average summer temperature in Australia and abroad collaborations globally would recommend UOW (80.6°F) 134 476 2,091 292,500 nationalities at UOW degrees on offer UOW staff population of Illawarra area THIS IS WHO WE ARE 1 2 UNIVERSITY OF WOLLONGONG A SHORT, SHARP CLIMB TO THE TOP As you will see in these pages, we are many things. -
Walks, Paddles and Bike Rides in the Illawarra and Environs
WALKS, PADDLES AND BIKE RIDES IN THE ILLAWARRA AND ENVIRONS Mt Carrialoo (Photo by P. Bique) December 2012 CONTENTS Activity Area Page Walks Wollongong and Illawarra Escarpment …………………………………… 5 Macquarie Pass National Park ……………………………………………. 9 Barren Grounds, Budderoo Plateau, Carrington Falls ………………….. 9 Shoalhaven Area…..……………………………………………………….. 9 Bungonia National Park …………………………………………………….. 10 Morton National Park ……………………………………………………….. 11 Budawang National Park …………………………………………………… 12 Royal National Park ………………………………………………………… 12 Heathcote National Park …………………………………………………… 15 Southern Highlands …………………………………………………………. 16 Blue Mountains ……………………………………………………………… 17 Sydney and Campbelltown ………………………………………………… 18 Paddles …………………………………………………………………………………. 22 Bike Rides …………………………………………………………………………………. 25 Note This booklet is a compilation of walks, paddles, bike rides and holidays organised by the WEA Illawarra Ramblers Club over the last several years. The activities are only briefly described. More detailed information can be sourced through the NSW National Parks & Wildlife Service, various Councils, books, pamphlets, maps and the Internet. WEA Illawarra Ramblers Club 2 October 2012 WEA ILLAWARRA RAMBLERS CLUB Summary of Information for Members (For a complete copy of the “Information for Members” booklet, please contact the Secretary ) Participation in Activities If you wish to participate in an activity indicated as “Registration Essential”, contact the leader at least two days prior. If you find that you are unable to attend please advise the leader immediately as another member may be able to take your place. Before inviting a friend to accompany you, you must obtain the leader’s permission. Arrive at the meeting place at least 10 minutes before the starting time so that you can sign the Activity Register and be advised of any special instructions, hazards or difficulties. Leaders will not delay the start for latecomers. -
New South Wales from 1810 to 1821
Attraction information Sydney..................................................................................................................................................................................2 Sydney - St. Mary’s Cathedral ..............................................................................................................................................3 Sydney - Mrs Macquarie’s Chair ..........................................................................................................................................4 Sydney - Hyde Park ..............................................................................................................................................................5 Sydney - Darling Harbour .....................................................................................................................................................7 Sydney - Opera House .........................................................................................................................................................8 Sydney - Botanic Gardens ................................................................................................................................................. 10 Sydney - Sydney Harbour Bridge ...................................................................................................................................... 11 Sydney - The Rocks .......................................................................................................................................................... -
The Chris Diment Memorial Congress Illawarra Bridge Association 2, 3
The Chris Diment Memorial Congress Illawarra Bridge Association Figtree Community Hall, 11 Princes Highway, Figtree 2, 3, 4th June 2017 Friday Welcome Pairs, Saturday Pairs, Sunday Teams Director: Jeff Carberry Convenor: Jill MacRae Information: [email protected] or 0414 900 239 Online entry: www.nswba.com.au/tourn/calendar.asp Conducted under the auspice of the NSWBA The ABF has approved the issue of red masterpoints at level B4 Registration: 1pm Friday, 9.30 am Saturday, 9am Sunday Entry fee: $35 per player (pairs), $40 per player (teams). Payment is at the table on arrival, lunch included both days. Please make sure you bring your system card. Yellow systems and brown sticker conventions are not permitted. Please note that there will be a limit of 30 tables due to room capacity, so early entry is advisable. Prize money Pairs: 1st $240, 2nd $120, 3rd $60 Best youth pair each player <35yrs $100 Teams: 1st $600, 2nd $400, 3rd $200 Best team each player < 300mps $200 Best team each player <100mp $200 Best youth team each player <35yrs $200 Only one prize per pair/team per event Getting there Wollongong is located around 1 hour south of Sydney at the end of the F6 expressway. The Illawarra Bridge Association (IBA) club room is located in the Figtree Community Hall, 11 Princes Highway, Figtree (opposite McDonald’s). Click on this link to view on Google maps. Coming from the north, approach Wollongong via Picton Rd or the F6, travel down Mt Ousley into Wollongong. Watch out for the speed camera at the bottom. -
SEACLIFF BRIDGE No.8 August 2006
CASE STUDY SEACLIFF BRIDGE No.8 August 2006 INTRODUCTION ʻAfter more than a century of temporary road closures owing to an unstable cliff line along Lawrence Hargrave Drive (LHD), the townships of Clifton and Coalcliff now have a reliable transport corridor link that may rival the Great Ocean Road for the title of Australiaʼs most spectacular seafront drive. After a 19-month construction programme, the 665m long bridge, comprising a balanced cantilever bridge and an incrementally launched bridge, bears testament to how seemingly insurmountable project obstacles can be overcome through engineering innovation, and community and stakeholder involvement.ʼi ALLIANCE ʻJust three months after authorising the road closure, the RTA announced that it had joined with three private sector companies in an alliance to develop a solution that would reconnect Lawrence Hargrave Drive between Clifton and Coalcliff. It is the state of New South Walesʼ first ever alliance agreement for a road construction project. The LHD alliance partners comprised the RTA, Image 1: Aerial View Barclay Mowlem, Coffey Geosciences and Maunsell Australia. The team members selected from each organisation brought an incredible pool of expertise in construction, geotechnical, civil, structural and CONCRETE environmental engineering, as well as community Good quality concrete was essential and several liaison. In total, 34 individuals were represented on options were considered to deliver the optimum the team, and were cross-representative of gender, balance of durability and timely construction. ii age and qualification.ʼ Boral Concrete were chosen to supply the concrete for the project and worked with the alliance to DURABILITY develop appropriate mix designs and all aspects to deliver the sites concrete requirements. -
Cruise Sydney & New South Wales
CRUISE SYDNEY & NEW SOUTH WALES Along the Blue Highway YAMBA AUSTRALIA WELCOME COFFS HARBOUR NSW New South Wales (NSW) is located on the east SYDNEY coast of Australia and is the country’s most TRIAL BAY geographically diverse State, offering a wide range of attractions, both natural and man-made. With nine cruise ports along the destination in Australia and New scenic NSW coastline known as Zealand in the 2018 Cruisers’ Choice the Blue Highway, each offering Destination Awards — an award striking natural beauty and unique based on reviews of passengers to experiences for the visitor, NSW caters Sydney the previous year. to all segments of the cruise market. Sydney is complemented by eight Sydney continues to be Australia’s other beautiful ports along NSW’s NEW SOUTH WALES cruise gateway and one of the world’s spectacular coastline — Eden, most beautiful destinations with Batemans Bay, Kiama, Wollongong, its iconic Sydney Harbour Bridge, Newcastle, Trial Bay, Coffs Harbour Sydney Opera House and pristine and Yamba — providing stunning NEWCASTLE beaches. The city offers a spectacular coastal city and regional areas to blend of art, culture, dining, events explore. The growing popularity and outdoor activities, coupled of cruising in NSW has cemented with contemporary and colonial the State’s place as the premier and architecture. With two ports, unrivalled cruise destination in Sydney was named the best cruise Australia and the South Pacific. SYDNEY For more information: visitnsw.com/cruise WOLLONGONG (PORT KEMBLA) KIAMA BATEMANS BAY Front -
Cadastral Survey for the Sea Cliff Bridge on Lawrence Hargrave Drive by the Roads and Maritime Services
Proceedings of the 17th Association of Public Authority Surveyors Conference (APAS2012) Wollongong, New South Wales, Australia, 19-21 March 2012 Cadastral Survey for the Sea Cliff Bridge on Lawrence Hargrave Drive by the Roads and Maritime Services Stephen Bennett Registered Land Surveyor, Roads and Maritime Services (RMS) [email protected] Jim Ollis Registered Land Surveyor, Roads and Maritime Services (retired) [email protected] ABSTRACT This paper describes the cadastral survey carried out by the Roads and Maritime Services (RMS) to define the new road boundaries to accommodate the Sea Cliff Bridge on Lawrence Hargrave Drive near Clifton, NSW. The survey had to contend with inhospitable terrain and the instability of the geological structure of the Illawarra Escarpment. It is shown how the application of traditional survey techniques, coupled with modern technology, under these difficult conditions, has produced a very comprehensive and rigorous cadastral survey. The paper describes how marks that were over 100 years old were located along the ocean rock shelf, as well as locating rare stone cubes placed as monuments along the old road alignment. The political urgency of reopening the road as quickly as possible meant that design of the property boundaries was left until after completion of the bridge. This required the survey team to liaise with land owners and other stakeholders to determine the optimal final boundaries and extent of the survey. Complicating this was the need to accommodate a bridge suspended over the sea bed, reclamation of the sea bed off the NSW coast and survey requirements to protect sensitive heritage items. -
Capital, Coast & Country Touring Route
CAPITAL, COAST & COUNTRY Touring Route WEDDIN 1 CO Blue Mountains 4 2 COPARRA RANGE National Park RANGE Weddin Mountains Lake River 39 National Park Kanangra - Boyd Waljeers Lake Port Jackson Wyangala Abercrombie National Lake Bungarry Lake Park SYDNEY 85 CAPITAL, COAST AND COUNTRY Bullogal River Barren Box Burrangong Swamp Creek Lake Ryans Burragorang SYDNEY Lake Cocoparra Kowmung AIRPORT TOURING ROUTE LEGEND BOTANY National BAY 87 Park Abercrombie River Cape Banks National Lachlan Bunumburt 94 Capital Drive: Canberra region–SouthernPark Highlands–Inland New South Wales Cape Baily Lake Ita Lake Riverina River Blue Mountains Royal Country Drive:Lachlan Bungendore–Braidwood–Batemans BayNational National Park ParkRoyal 31 SCOTTS MAIN RANGE Southern Highlands National Ganaway River Nattai Lake Coast Drive: Jervis Bay–Kiama–Wollongong National Park Creek Lake NARRANDERA RANGE Park Cataract Murrumbidgee 94 20 Ingalba River Nature Reserve River Bangadilly Murrumbidgee River Lake Lake Lake National Tala Loorica Mittagong Avon CordeauxPRINCES HWYWollongong Lake Tombullen 81 Park Bowral Port Kembla Harbour Storage Tarlo River Robertson Lake National Pejar Dam Park Wingecarribee ILLAWARRAReservoir HWY 20 olraT Lake Illawarra Dry Lake Drain 94 85 Wollondilly Shellharbour Goonerah River Lagoon Fitzroy Robertson Eurolie Fitzroy Bass Point Dam FallsFalls Yanga Outfall Budderoo Jamberoo Lake Murrumbidgee Reservoir 87 FEDERAL HWY National 39 Park Condouple 87 79 Kiama Lake Coleambally Creek Ulandra Goulburn 31 Nature Reserve Kangaroo Lake Gerringong Talbetts