Dynamic Estimation of Electrical Demand in Hot Rolling Mills G
Total Page:16
File Type:pdf, Size:1020Kb
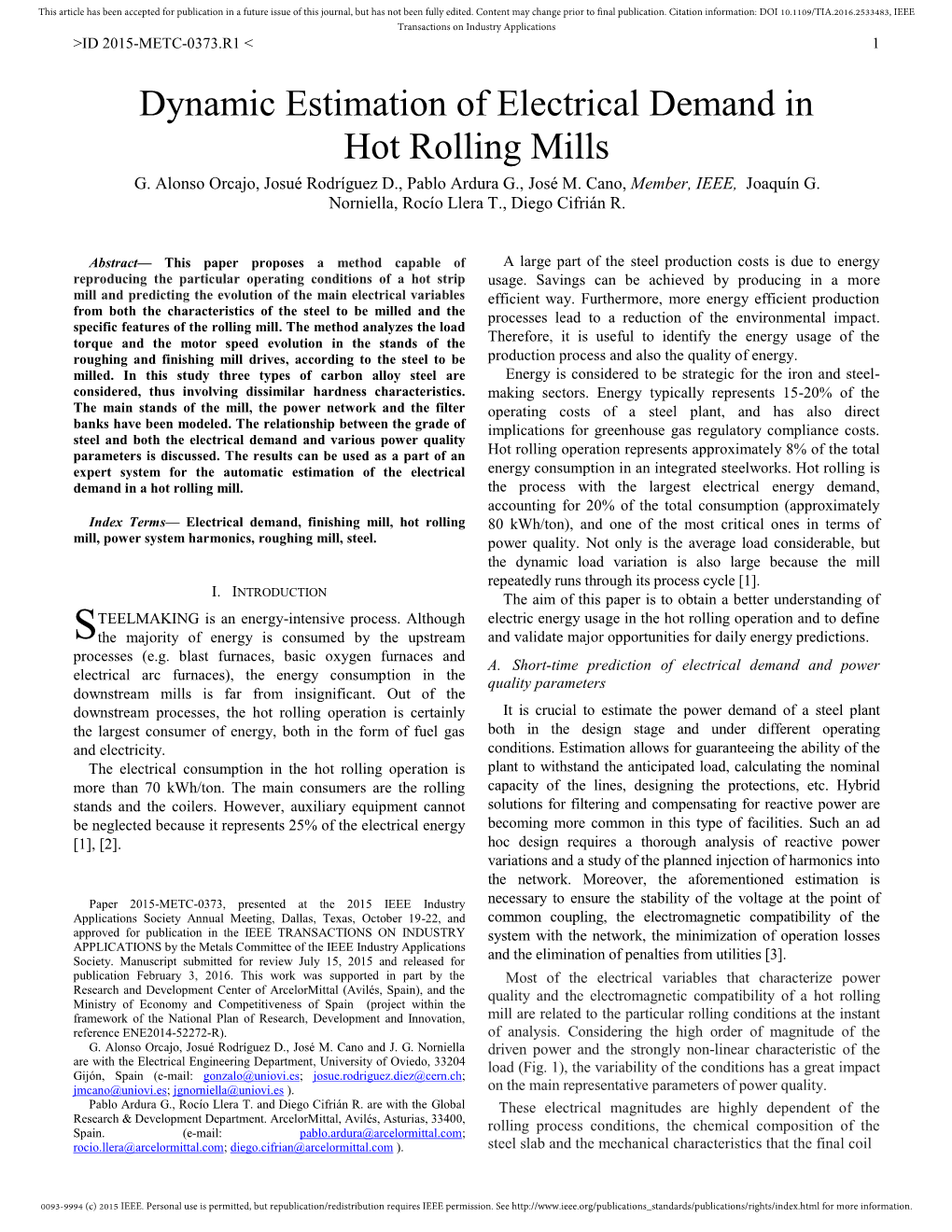
Load more
Recommended publications
-
Power Electronics and Industrial Drives (4 Semesters) Regulations 2010 Sathyabama University Faculty of Electrical Engineering
SATHYABAMA UNIVERSITY (Established under section 3 of UGC Act, 1956) Jeppiaar Nagar, Rajiv Gandhi Salai, Chennai - 119. SYLLABUS MASTER OF ENGINEERING PROGRAMME IN POWER ELECTRONICS AND INDUSTRIAL DRIVES (4 SEMESTERS) REGULATIONS 2010 SATHYABAMA UNIVERSITY FACULTY OF ELECTRICAL ENGINEERING SATHYABAMA UNIVERSITY REGULATIONS – 2010 Effective from the academic year 2010-2011 and applicable to the students admitted to the Master of Engineering / Technology / Architecture /Science (Four Semesters) 1. Structure of Programme 1.1 Every Programme will have a curriculum with syllabi consisting of theory and practical such as: (i) General core courses like Mathematics (ii) Core course of Engineering / Technology/Architecture / Science (iii) Elective course for specialization in related fields (iv) Workshop practice, Computer Practice, laboratory Work, Industrial Training, Seminar Presentation, Project Work, Educational Tours, Camps etc. 1.2 Each semester curriculum shall normally have a blend of lecture course not exceeding 7 and practical course not exceeding 4. 1.3 The medium of instruction, examinations and project report will be English. 2. Duration of the Programme A student is normally expected to complete the M.E/M.Tech./M.Arch/M.Sc Programme in 4 semesters but in any case not more than 8 consecutive semesters from the time of commencement of the course. The Head of the Department shall ensure that every teacher imparts instruction as per the number of hours specified in the syllabus and that the teacher teaches the full content of the specified syllabus for the course being taught. 3. Requirements for Completion of a Semester A candidate who has fulfilled the following conditions shall be deemed to have satisfied the requirement for completion of a semester. -
Français Español English À Simple Effet De Efecto Único Single Acting
Français Español English à simple effet de efecto único single acting abrasif abrasivo Abrasive absorption absorción absorption accélérateur acelerador accelerator accélérateur graphique acelerador gráfico graphics accelerator accélération aceleración ramp-up accéléromètre acelerómetro accelerometer accepteur aceptor Acceptor accès aléatoire acceso aleatorio random access accès séquentiel acceso secuencial serial access accumulateur acumulador accumulator accumulation acumulación accumulation accumulation cryogénique almacenamiento criogénico cryogenic storage acétone acetona acetone acide ácido acid acide acétique ácido acético acetic acid acide bromhydrique ácido bromhídrico hydrobromic acid acide chlorhydrique ácido clorhídrico hydrochloric acid acide fluorhydrique ácido fluorhídrico hydrofluoric acid acide fluorhydrique ácido fluorhídrico buffered hydrofluoric acid tamponné tamponado acide nitrique ácido nítrico nitric acid acide peroxydisulfurique ácido peroxidisulfúrico peroxydisulfuric acid (PDSA) acide phosphorique ácido fosfórico phosphoric acid acide sulfurique ácido sulfúrico sulfuric acid acidose acidosis acidosis actionneur accionador actuator actionneur à fréquence accionador de frecuencia variable frequency driver variable variable actionneur à moteur accionador con motor electric motor actuator électrique eléctrico actionneur électrique accionador eléctrico electric actuator actionneur électrique accionador eléctrico electric driver actionneur électrique accionador eléctrico electrical actuator actionneur électrique accionador -
Remotized Control of Power Electronic Devices Exploiting a Plastic Optical Fiber Photonic Bus
POLITECNICO DI TORINO Collegio di Ingegneria Elettronica, delle Telecomunicazioni e Fisica (ETF) Department of Electronics and Telecommunications (DET) Master of Science in Telecommunications Engineering Master of Science Degree Remotized Control of Power Electronic Devices Exploiting a Plastic Optical Fiber Photonic Bus Candidate: Advisor: Erasmo Vizzaccaro Vittorio Curri (DET) Co-Advisors: Eric Giacomo Armando (DENERG) Gianmario Pellegrino (DENERG) Paolo Savio (ISMB) Academic Year 2017/2018 Erasmo Vizzaccaro: Remotized Control of Power Electronic Devices Ex- ploiting a Plastic Optical Fiber Photonic Bus Telecommunications Engineering, c Politecnico di Torino 2018 advisor: Vittorio Curri To my father and my mother Lovely parents and sources of inspiration in my life I love you A mio padre e mia madre Genitori fantastici e fonti di ispirazione nella mia vita Vi voglio bene ABSTRACT Nowadays, a new energy revolution is in act. This trend can be no- ticed from the explosive growth of portable devices (smartphones, laptops, tablets) industry processes, hybrid cars and many others. Power Electronic assumes a fundamental role in this revolution, since it represents the technique with which the power is transferred from the source to the load. These developments are leading digital control into becoming the enabling technology for many engineering fields and Power Electronic Converters (PECs) into being used in several applications such as computer power supplies, energy conversion and motor drive control, suggesting the possibility of new and better integration of advanced power conversion and ICT services. Therefore, linking the Power Electronic world to the Information and Commu- nication Technologies becomes extremely important and suggestive from the point of view of what we can achieve with this kind of technologies linked together. -
Framework for Quantifying Uncertainty in Electric Ship Design
CHILDREN AND ADOLESCENTS This PDF document was made available from www.rand.org as a public CIVIL JUSTICE service of the RAND Corporation. EDUCATION ENERGY AND ENVIRONMENT Jump down to document HEALTH AND HEALTH CARE 6 INTERNATIONAL AFFAIRS POPULATION AND AGING The RAND Corporation is a nonprofit research PUBLIC SAFETY SCIENCE AND TECHNOLOGY organization providing objective analysis and effective SUBSTANCE ABUSE solutions that address the challenges facing the public TERRORISM AND HOMELAND SECURITY and private sectors around the world. TRANSPORTATION AND INFRASTRUCTURE U.S. NATIONAL SECURITY Support RAND Purchase this document Browse Books & Publications Make a charitable contribution For More Information Visit RAND at www.rand.org Explore the RAND National Defense Research Institute View document details Limited Electronic Distribution Rights This document and trademark(s) contained herein are protected by law as indicated in a notice appearing later in this work. This electronic representation of RAND intellectual property is provided for non-commercial use only. Permission is required from RAND to reproduce, or reuse in another form, any of our research documents for commercial use. This product is part of the RAND Corporation documented briefing series. RAND documented briefings are based on research briefed to a client, sponsor, or targeted au- dience and provide additional information on a specific topic. Although documented briefings have been peer reviewed, they are not expected to be comprehensive and may present preliminary findings. Framework for Quantifying Uncertainty in Electric Ship Design ISAAC PORCHE, HENRY WILLIS, MARTIN RUSZKOWSKI DB-407-ONR March 2004 Prepared for the Office of Naval Research Approved for public release; distribution unlimited The research described in this briefing was sponsored by the Office of Naval Research. -
PDF (Size: 5,09 МБ) "Електричні Машини Та
Білий Леонід Білик Олександр Богаєнко Микола Болюх Володимир Бородій Ірина Адамович Анатолійович Володимирович Федорович Олексіївна Бредун Руслан Васьковський Вишневський Войтецька Таїсія Войтецький Вячеславович Юрій Миколайович Леонід Вікторович Олександрівна Ігор Євгенович Гамалія Ростислав Глазєва Оксана Гребеніков Віктор Джура Олександр Віталійович Володимирівна Володимирович Васильович Дунєв Олексій Єгоров Андрій Заблодський Микола Зарицька Ковальчук Олександрович Володимирович Миколайович Олена Ігорівна Станіслав Ігорович Котлярова Вікторія Красовський Павло Лісевич Світлана Мазуренко Леонід Мандровський Володимирівна Олексійович Петрівна Іванович Максим Юрійович Автори статей Вісник НТУ «ХПІ» 2020, № 3 (1357). Серія: "Електричні машини та електромеханічне перетворення енергії" МІНІСТЕРСТВО ОСВІТИ MINISTRY OF EDUCATION І НАУКИ УКРАЇНИ AND SCIENCE OF UKRAINE Національний технічний університет National Technical University «Харківський політехнічний інститут» "Kharkiv Polytechnic Institute" Вісник НТУ «Харківський Bulletin of the NTU політехнічний інститут». "Kharkiv Polytechnic Institute". Серія: Електричні машини Series: Electrical Machines and та електромеханічне Electromechanical Energy перетворення енергії Conversion № 3 (1357) 2020 No. 3 (1357) 2020 Збірник наукових праць Collection of Scientific papers Видання засноване у 1961 р. The edition was founded in 1961 Харків Kharkiv НТУ «ХПІ», 2020 NTU "KhPI", 2020 Вісник НТУ «Харківський політехнічний інститут». Серія: Електричні машині та електромеханічне пе- ретворення енергії -
AC Motor Control Applications in High-Power Industrial Drives
23 AC Motor Control Applications in High-Power Industrial Drives Ajit K. Chattopadhyay Electrical Engineering Department, Bengal Engineering & Science University, India 23.1 Introduction The power ratings of large medium voltage (2.2–13.8 kV) industrial drives range between few hundred kilowatts to a few tens of megawatts and even 100 MW. The upper limit is decided by the requirements of the applications rather than by the technology of the converters and machines (Stemmler 1994). The available speed range lies from 10 rpm for low-speed machines (e.g. Cement mills), 1500/3000 rpm for normal-speed drives to even 18 000 rpm for very high power high speed drives (e.g., compressors). The limits for the dc motors such as cost, size, commutator problems and inability to operate satisfactorily in a dirty and explosive environment have called for ac motor drives for high power applications. Major technical breakthroughs have occurred both in the power conversion and in control areas of variable voltage variable frequency (VVVF) ac drives to meet the exacting requirements of ac drives using direct ac/ac cycloconverters or ac/dc/ac link inverters that feed either induction motors (IM) or synchronous motors (SM). The machine may be excited by a voltage source inverter (VSI) or a current source inverter (CSI). Synchronous motor drives have the advantages over the induction motor drives in that, with separate field excitation, these can be operated at any power factor-leading, lagging and unity. The operation near unity power factor reduces armature copper loss and permits inverter size reduction with simplicity of commutation (load commutation) with thyristors as switches. -
Electric and Hybrid Vehicle Power Electronics Efficiency, Testing and Reliability
World Electric Vehicle Journal Vol. 6 - ISSN 2032-6653 - © 2013 WEVA Page Page 0719 EVS27 Barcelona, Spain, November 17-20, 2013 Electric and Hybrid Vehicle Power Electronics Efficiency, Testing and Reliability Joe Drobnik1, Praveen Jain2 1Freescale Semiconductor, 2100 E Elliot Rd., Tempe AZ 85207, USA, [email protected] 2Queen’s University, Kingston, Ontario, Canada, [email protected] Abstract System efficiency together with the reliability are the most critical factors in the design, characterization and operation of Electric and Hybrid Vehicles. This paper summarizes those aspects from the system level down to the component details and shows practical methods for evaluation and improvement. This paper concentrates on a small to medium size personal vehicles in electric vehicle (EV) and parallel hybrid (HEV) configuration. Even though the main focus of the paper is the traction inverter, other critical high power EV and HEV building blocks such as a DC/DC and AC/DC on board charger are also characterized and discussed to certain depth. Some test methods for evaluation of the individual units and their components including extreme conditions such as heavy overload, short circuit and overvoltage are explored along with examples of experimental results on the prototype units. Keywords: list: Efficiency, Reliability, traction inverter, EV power electronics, Vehicle power electronics battery and converts it into low voltage required by the vehicle (typically 12V). A low voltage battery 1 Introduction for this system remains a necessity, thought its The inevitable global shift towards the EV & capacity may be reduced. HEV development brought number of challenges that were not applicable to a standard vehicle In most instances at least a small AC/DC converter powered only by an internal combustion engine /On-board charger is also required as a functional (ICE). -
A Five-Level Current-Source Inverter for Grid- Connected Or High-Power Three-Phase Wound-Field Synchronous Motor Drives
Engineering, Technology & Applied Science Research Vol. 6, No. 5, 2016, 1139-1148 1139 A Five-Level Current-Source Inverter for Grid- Connected or High-Power Three-Phase Wound-Field Synchronous Motor Drives Sobhan Mohamadian Mohammad Hosein Khanzade School of Engineering Department of FAVA Engineering Damghan University Imam Hossein Comprehensive University Damghan, Iran Tehran, Iran [email protected] [email protected] Abstract—Simple converter structure, inherent short-circuit harmonics created by the PWM switching. However, this protection and regenerative capability are the most important capacitor bank has some drawbacks such as the possibility of advantages of current-source inverters (CSI’s) which have made the resonance risk between output capacitors and machine them suitable for medium-voltage high-power drives. Usually in magnetizing inductance at the fundamental frequency or grid-connected gas turbine generators or pumped storage hydro machine leakage inductance at higher harmonic orders [4]. power plants, efficient and reliable current-source load- Thus, the capacitor bank must be designed so that the lowest commutated inverters (LCI’s) with thyristor switches are harmonic order of the stator current is much higher than the employed. Also, this type of CSI is widely used in very large resonance frequency. Accordingly, the bank size will typically drives with power ratings of tens of megawatts to supply wound- range between 0.3 per unit (pu) to 0.5 pu for switching field synchronous motors (WFSM’s). However, LCI’s suffer from frequencies of approximately 400 Hz [1]. Furthermore, the some disadvantages such as large torque pulsations, poor power factor, and start-up criticalities. -
Fourth Semester Diploma in Engineering/Technology
TED (15) – 4212 Reg.No. …………………………… (REVISION -2015) Signature ………………………… FOURTH SEMESTER DIPLOMA IN ENGINEERING/TECHNOLOGY INDUSTRIAL ELECTRONICS AND CONTROL DRIVES [Time : 3 hours ] ( Maximum marks : 100 ) PART – A ( Maximum marks : 10 ) Marks I Answer the following questions in one or two sentences. Each questions carries 2 marks. 1.Define the term triggering current. 2.Write four turn on methods of SCR 3.Classify DC electric motors. 4.List four applications of servomotors 5.what is cycloconverter. ( 5x2 = 10) PART – B ( Maximum marks : 30 ) II Answer any five of the following questions. Each questions carries 6 marks. 1. Explain the structure of power diode. 2.Describe the transistor analogy of SCR. 3.Draw the circuit diagram and various voltage and current waveform of single phase mid- point converter with R L load 4.Explain the principle of operation of stepper motor. 5. Describe the working principle of AC tachogenerator. 6. Enlist applications of single phase and three phase dual converter 7. Distinguish between AC and DC drives. PART – C ( Maximum marks : 60 ) (Answer one full questions from each unit. Each full question carries 15 marks ) UNIT - I III (a) Explain the structure of SCR. 8 (b) Explain the method adopted for the protection of SCR against over current. 7 OR IV (a) Describe the static V-I characteristics of SCR. 8 (b) Explain the structure and working principle of a DIAC. 7 UNIT – II V (a) Describe single phase bridge converter with relevant waveform. 7 (b) Explain the working of TRIAC light dimming circuit. 8 OR VI (a) Explain the operation of three phase converter. -
Mark Matthew Flynn
Mark M. Flynn EDUCATION Ph.D., Electrical and Computer Engineering, The University of Texas at Austin 2003 • Dissertation: A Methodology for Evaluating and Reducing Rotor Losses, Heating, and Operational Limitations of High-Speed Flywheel Batteries M.S., Electrical and Computer Engineering, The University of Texas at Austin 1999 • Thesis: Design, Construction, and Operation of a Low Distortion Pulse Width Modulation Inverter for Use in a Harmonic Testing Station B.S. with Honors, Electrical and Computer Engineering, The University of Texas at Austin 1997 RESEARCH EXPERIENCE Applied Research Laboratories, The University of Texas at Austin 2014 – Present Research Associate 2014 – Present • Naval Sea Systems Command – Sonar Development May 2014 – Present Design of power-electronic and magnetic systems for high-performance naval applications including dc-dc converters, inverters, and actuators. Proficient in all aspects of product development including design, testing, and manufacturing support. Center for Electromechanics, The University of Texas at Austin 1999 – 2014 Research Associate 2010 – 2014 Research Engineer V 2008 – 2010 Research Engineer IV 2004 – 2008 Research Engineer III 2001 – 2003 Research Engineer II 1999 – 2001 • U.S. Army Construction Engineering Research Laboratory – Forward Operating Base In- The-Loop Power System Simulator August 2013 – April 2014 Developed a simulator-in-the loop for forward operating bases designed to enhance existing supervisory control and data acquisition (SCADA) systems by automatically and continuously simulating credible contingencies and anticipating system state before the SCADA system commits a system change. The in-the-loop simulator is also capable of suggesting efficiency and reliability improvements by computing numerous system metrics among others such as power loss, line outage distribution factors, energy storage requirements, and historical usage data. -
Cycloconverter Drive for AC Motors
International Journal of Electrical Engineering. ISSN 0974-2158 Volume 6, Number 5 (2013), pp. 569-581 © International Research PublicationHouse http://www.irphouse.com Cycloconverter Drive for AC Motors Manishkumar M. Tayade and S.S. Dhamse Department of Electrical Engineering, Government College of Engineering, Aurangabad. Abstract This paper is going to discuss an efficient technique to control the speed of a single phase induction motor in three steps by using cyclo convertor technique by thyristors. The induction motor is most widely used machine in both industrial and domestic sector, the difficulty of varying its speed by a cost effective device is one of its main disadvantages. As the AC supply frequency cannot be changed, so this paper presents a thyristor controlled cyclo converter which enables the control of speed in steps for an induction motor. The microcontroller used here is from 8051 family, a pair of slide switches is used to select the desired speed range (f, f/2 and f/3) of operation of the induction motor. These switches are interfaced to the microcontroller. The status of the switches enables the microcontroller to deliver the pulses to trigger the SCR’s in a dual bridge. Thus, the speed of the induction motor can be achieved in three steps i.e. (f, f/2 and f/3). Index Terms—cycloconverter, single phase induction motors drives(SPIMDs), silicon controled rectifer(SCR). (key words) INTRODUCTION Induction motors are the most widely used electrical motors. Because motors do not inherently have the capability of variable speed operation. Due to this reason, earlier dc motors were applied in most of the electrical drives. -
Jorhat Engineering College, Jorhat Assam – 785 007
New Course Structure and Syllabus of Dibrugarh University | Electrical Engineering (2016-17) & (2017-2018) Batch Dibrugarh University Jorhat Engineering College, Jorhat Assam – 785 007 COURSE STRCUTURE FOR UG ENGINEERING UNDER DIBRUGARH UNIVERSITY ELECTRICAL ENGINEERING SEMESTER I Sl Course Course Title L T P Contact Credit No. Code hrs/wk 01 HS101 Sociology 2 0 0 2 2 02 HS102 Business Communications 2 0 0 2 2 03 MA101 Mathematics I 3 1 0 4 4 04 PH101 Applied Physics I 3 0 0 3 3 05 PH102 Applied Physics Laboratory I 0 0 2 2 1 06 CH101 Engineering Chemistry I 3 0 0 3 3 07 CH102 Engineering Chemistry Laboratory I 0 0 2 2 1 08 CE101 Engineering Graphics 2 0 2 4 3 09 EE101 Basic Electrical Engineering 3 1 0 4 4 10 EE102 Basic Electrical Engineering Laboratory 0 0 2 2 1 11 ME101 Engineering Workshop I 0 0 2 2 1 TOTAL 30 25 SEMESTER II Sl Course Course Title L T P Contact Credit No. Code hrs/wk 01 HS203 Economics for Engineers 2 0 0 2 2 02 HS204 Presentation Skills 1 0 2 3 2 03 MA202 Mathematics II 3 1 0 4 4 04 PH203 Applied Physics II 3 0 0 3 3 05 PH204 Applied Physics Laboratory II 0 0 2 2 1 06 CH203 Engineering Chemistry II 3 0 0 3 3 07 CH204 Engineering Chemistry Laboratory II 0 0 2 2 1 08 CS201 Computer Programming 3 0 0 3 3 09 CS202 Computer Programming Laboratory 0 0 2 2 1 10 ME202 Engineering Mechanics 3 1 0 4 4 11 ME203 Engineering Mechanics Laboratory 0 0 2 2 1 12 ME204 Engineering Workshop II 0 0 2 2 1 TOTAL 30 25 13 AC201 Environmental studies 3 0 0 3 0 SEMESTER III Sl Course Course Title L T P Contact Credit No.