Design and Create with Natural Dyes
Total Page:16
File Type:pdf, Size:1020Kb
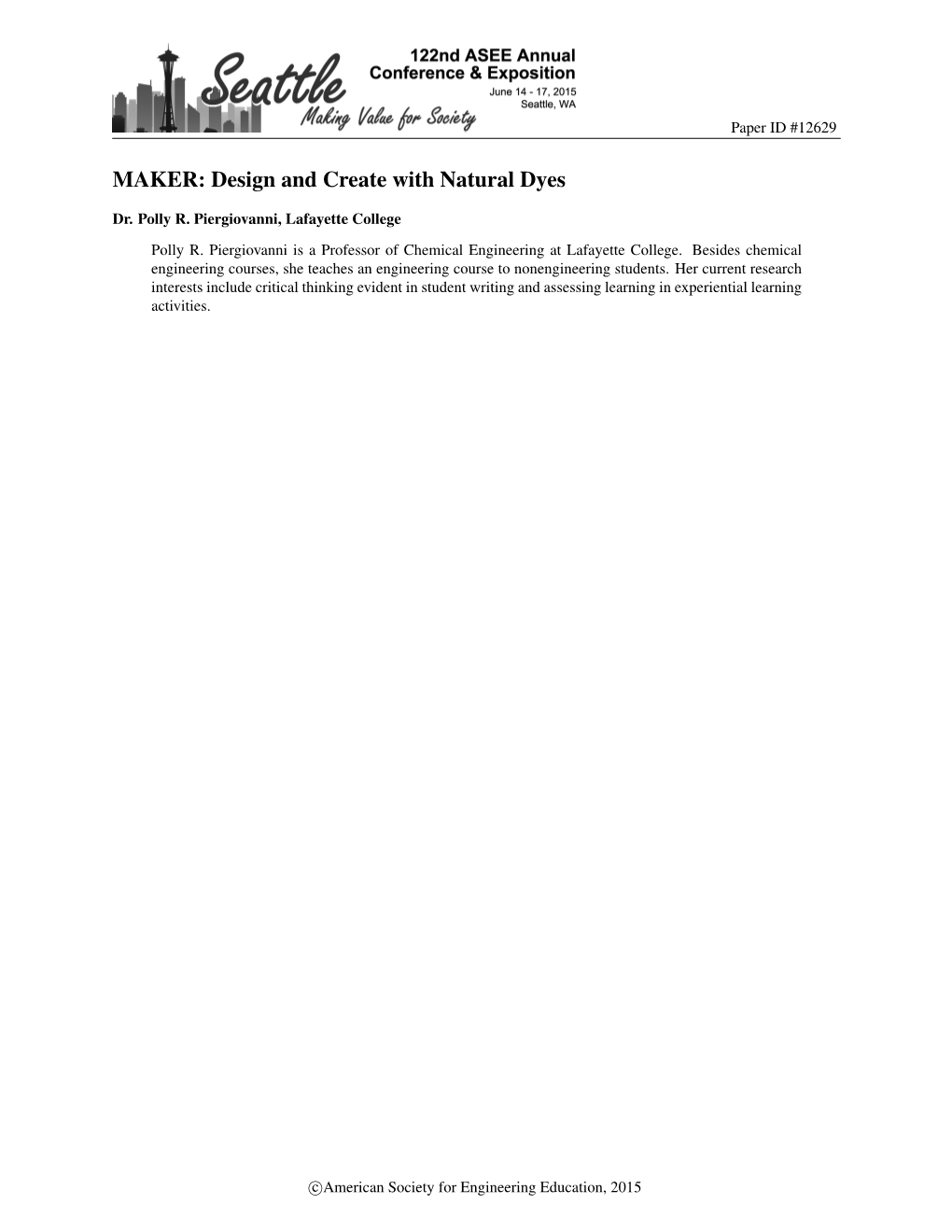
Load more
Recommended publications
-
Natural Colourants with Ancient Concept and Probable Uses
JOURNAL OF ADVANCED BOTANY AND ZOOLOGY Journal homepage: http://scienceq.org/Journals/JABZ.php Review Open Access Natural Colourants With Ancient Concept and Probable Uses Tabassum Khair1, Sujoy Bhusan2, Koushik Choudhury2, Ratna Choudhury3, Manabendra Debnath4 and Biplab De2* 1 Department of Pharmaceutical Sciences, Assam University, Silchar, Assam, India. 2 Regional Institute of Pharmaceutical Science And Technology, Abhoynagar, Agartala, Tripura, India. 3 Rajnagar H. S. School, Agartala, Tripura, India. 4 Department of Human Physiology, Swami Vivekananda Mahavidyalaya, Mohanpur, Tripura, India. *Corresponding author: Biplab De, E-mail: [email protected] Received: February 20, 2017, Accepted: April 15, 2017, Published: April 15, 2017. ABSTRACT: The majority of natural colourants are of vegetable origin from plant sources –roots, berries, barks, leaves, wood and other organic sources such as fungi and lichens. In the medicinal and food products apart from active constituents there are several other ingredients present which are used for either ethical or technical reasons. Colouring agent is one of them, known as excipients. The discovery of man-made synthetic dye in the mid-19th century triggered a long decline in the large-scale market for natural dyes as practiced by the villagers and tribes. The continuous use of synthetic colours in textile and food industry has been found to be detrimental to human health, also leading to environmental degradation. Biocolours are extracted by the villagers and certain tribes from natural herbs, plants as leaves, fruits (rind or seeds), flowers (petals, stamens), bark or roots, minerals such as prussian blue, red ochre & ultramarine blue and are also of insect origin such as lac, cochineal and kermes. -
Tutorial: How to Dye Black with Natural
http://www.aurorasilk.com/ Tutorial: How To Dye Black with Natural Dyes by Cheryl Kolander. Excerpted from TrueFibers. Aurora Silk sells a full selection of natural dyes and mordants. For ideas on which dyes and which mordants to use, view our Natural Dye colour Chart. For more detailed dyeing recipes, read Brilliant Colours! by Cheryl Kolander. After recording the dry weight of your fiber, wet the fiber out in warm or hot water. STEP I: TANNIN 2 oz. tannic acid per pound of fiber (dry weight) OR: 4 oz. tara sawdust per pound of fiber, extracted twice OR: 3 oz Catechu (Cutch) extract per pound of fiber with optional 1/2 oz copper mordant 1. Dissolve tannic acid or catechu extract in hot water. 2. Heat the solution to approximately 200 F. 3. Remove from heat. 4. Enter the silk (or other fiber) that has been thoroughly wet out in warm to hot water. 5. Set to soak for at least 24 hrs, stirring occasionally. STEP II: IRON 1/2 to 1 oz Ferrous Sulphate per pound of fiber Use the lesser amount for fine silk yarn and soft wools. Use the greater amount for wild silk and other fibers. 1. Dissolve the iron in warm water. 2. Soak fiber in a mild soap solution about 15 minutes to neutralize the acid in the tannin (which couters the effect of the iron). This step is not necessary if you used Catechu for STEP I. 3. Add fiber to warm iron solution and soak for about 20 minutes. 4. Remove fiber from iron solution, wring excess solution from fiber, and hang to air 20 minutes to 1 hour. -
The Life and Death of Tamu Rambu Yuliana Princess of Sumba
The Life and Death of Tamu Rambu Yuliana Princess of Sumba 201 Georges Breguet Tamu Rambu Yuliana, Sumba Princess THE LIFE AND DEATH OF TAMU RAMBU YULIANA, 202 PRINCESS OF SUMBA AND CUSTODIAN OF THE ARTS AND TREASURES OF RINDI The Island of Sumba and the Domain of Rindi A fragment formerly detached from the Australian continental plate, the island of Sumba 1 (approximately 11,000 km 2) is situated south of the volcanic arc of the Lesser Sunda Islands, west of Flores. Made up mainly of limestone and sedimentary rocks, Sumba’s topography con - sists of numerous hills and a plateau covered with grassy savannah interspersed with valleys hollowed out by erosion where gallery forests grow. The climate is hot and arid, except during the rainy season that lasts from December to March. With fewer than 600,000 inhabitants, Sumba boasts one of the low - est population densities in Indonesia. The island is divided into two administrative districts, West and East Sumba; the east has greater ethnic, cultural, and linguistic unity than the western part. 2 The town of Waingapu is the administrative center of East Sumba; it is also its Fig. 1. Photo taken in the 1950s from the personal album of the old Raja Umbu Hapu economic center, with its port and airport, the Chinese, Arabic, and Hambandina. On the left is his daughter, Princess Tamu Rambu Yuliana. On the right is Bugis communities, and its many Indonesian civil servants. The villages Princess Tamu Rambu Mirinai Liaba, third wife of the old raja and mother of the present of the major traditional domains are in the countryside surrounding raja , Umbu Kanabundaung. -
Textile Society of America Newsletter 27:2 — Fall 2015 Textile Society of America
University of Nebraska - Lincoln DigitalCommons@University of Nebraska - Lincoln Textile Society of America Newsletters Textile Society of America Fall 2015 Textile Society of America Newsletter 27:2 — Fall 2015 Textile Society of America Follow this and additional works at: https://digitalcommons.unl.edu/tsanews Part of the Art and Design Commons Textile Society of America, "Textile Society of America Newsletter 27:2 — Fall 2015" (2015). Textile Society of America Newsletters. 71. https://digitalcommons.unl.edu/tsanews/71 This Article is brought to you for free and open access by the Textile Society of America at DigitalCommons@University of Nebraska - Lincoln. It has been accepted for inclusion in Textile Society of America Newsletters by an authorized administrator of DigitalCommons@University of Nebraska - Lincoln. VOLUME 27. NUMBER 2. FALL, 2015 Cover Image: Collaborative work by Pat Hickman and David Bacharach, Luminaria, 2015, steel, animal membrane, 17” x 23” x 21”, photo by George Potanovic, Jr. page 27 Fall 2015 1 Newsletter Team BOARD OF DIRECTORS Roxane Shaughnessy Editor-in-Chief: Wendy Weiss (TSA Board Member/Director of External Relations) President Designer and Editor: Tali Weinberg (Executive Director) [email protected] Member News Editor: Ellyane Hutchinson (Website Coordinator) International Report: Dominique Cardon (International Advisor to the Board) Vita Plume Vice President/President Elect Editorial Assistance: Roxane Shaughnessy (TSA President) and Vita Plume (Vice President) [email protected] Elena Phipps Our Mission Past President [email protected] The Textile Society of America is a 501(c)3 nonprofit that provides an international forum for the exchange and dissemination of textile knowledge from artistic, cultural, economic, historic, Maleyne Syracuse political, social, and technical perspectives. -
Batik of Java: Global Inspiration Maria Wronska-Friend the Cairns Institute, James Cook University, [email protected]
University of Nebraska - Lincoln DigitalCommons@University of Nebraska - Lincoln Textile Society of America Symposium Proceedings Textile Society of America 2018 Batik of Java: Global Inspiration Maria Wronska-Friend The Cairns Institute, James Cook University, [email protected] Follow this and additional works at: https://digitalcommons.unl.edu/tsaconf Part of the Art and Materials Conservation Commons, Art Practice Commons, Fashion Design Commons, Fiber, Textile, and Weaving Arts Commons, Fine Arts Commons, and the Museum Studies Commons Wronska-Friend, Maria, "Batik of Java: Global Inspiration" (2018). Textile Society of America Symposium Proceedings. 1080. https://digitalcommons.unl.edu/tsaconf/1080 This Article is brought to you for free and open access by the Textile Society of America at DigitalCommons@University of Nebraska - Lincoln. It has been accepted for inclusion in Textile Society of America Symposium Proceedings by an authorized administrator of DigitalCommons@University of Nebraska - Lincoln. Published in Textile Society of America Symposium Proceedings 2018 Presented at Vancouver, BC, Canada; September 19 – 23, 2018 https://digitalcommons.unl.edu/tsaconf/ Copyright © by the author(s). Batik of Java: Global Inspiration Maria Wronska-Friend [email protected] Batik, the resist-dyeing technique of patterning cloth through the application of wax, has been known since antiquity in several parts of the world, but it reached its highest level of complexity on the island of Java. While deeply embedded in local traditions and associated with the beliefs, philosophy, and social order of Java, during the last two centuries batik has become a powerful cultural intermediary connecting Indonesia with other parts of the world. -
2Bbb2c8a13987b0491d70b96f7
An Atlas of Rare & Familiar Colour THE HARVARD ART MUSEUMS’ FORBES PIGMENT COLLECTION Yoko Ono “If people want to make war they should make a colour war, and paint each others’ cities up in the night in pinks and greens.” Foreword p.6 Introduction p.12 Red p.28 Orange p.54 Yellow p.70 Green p.86 Blue p.108 Purple p.132 Brown p.150 Black p.162 White p.178 Metallic p.190 Appendix p.204 8 AN ATLAS OF RARE & FAMILIAR COLOUR FOREWORD 9 You can see Harvard University’s Forbes Pigment Collection from far below. It shimmers like an art display in its own right, facing in towards Foreword the glass central courtyard in Renzo Piano’s wonderful 2014 extension to the Harvard Art Museums. The collection seems, somehow, suspended within the sky. From the public galleries it is tantalising, almost intoxicating, to see the glass-fronted cases full of their bright bottles up there in the administra- tive area of the museum. The shelves are arranged mostly by hue; the blues are graded in ombre effect from deepest midnight to the fading in- digo of favourite jeans, with startling, pleasing juxtapositions of turquoise (flasks of lightest green malachite; summer sky-coloured copper carbon- ate and swimming pool verdigris) next to navy, next to something that was once blue and is now simply, chalk. A few feet along, the bright alizarin crimsons slake to brownish brazil wood upon one side, and blush to madder pink the other. This curious chromatic ordering makes the whole collection look like an installation exploring the very nature of painting. -
ABSTRACT YI, DING. a Comparison of Mordant and Natural Dyes In
ABSTRACT YI, DING. A Comparison of Mordant and Natural Dyes in Dyeing Cotton Fabrics. (Under the direction of Dr. Harold S. Freeman and Dr. Peter J. Hauser). Mordant dyes constitute a class of synthetic colorants that are applied to textile fibers mainly through the aid of transition metal ions such as Cr3+. The resultant dye-metal complexes are key to the fastness properties produced on wool. In the same way, most natural dyes require the use of a mordant to have coloring power on textiles such as cotton. Unlike mordant dyes on wool, the fastness properties of natural dyes on cotton are generally quite low. Consequently, they have largely been replaced by synthetic dyes that are more cost effective, brighter, and more durable under end-use applications. Interest in green technologies has led to renewed consideration of natural dyes for textile coloration because they are biodegradable and do not involve manufacturing processes requiring genotoxic aromatic amines. Interestingly, such a shift would bring dyeing technology full circle to a family of colorants lacking the vibrancy and technical properties of most synthetic dyes. However, similarities between the dyeing method for mordant and natural dyes brought to mind the potential for reducing the level of synthetic dyes used commercially by combining suitable dyes from these two classes for dyeing textiles. This thesis research was devoted to stage 1 of this idea, namely the evaluation of mordant dyes as colorants for cotton fabric. With this in mind, dyes such as Mordant Blue 13, Mordant Brown 40, Mordant Orange 6 and Mordant Yellow 8 were applied to cotton using various dyeing times, temperatures, dye bath concentrations and mordants. -
Influence of Natural and Artificial Mordants on the Dyeing Performance of Cotton Knit Fabric with Natural Dyes
IOSR Journal of Polymer and Textile Engineering (IOSR-JPTE) e-ISSN: 2348-019X, p-ISSN: 2348-0181, Volume 6, Issue 1 (Jan. - Feb. 2019), PP 01-06 www.iosrjournals.org Influence of Natural and Artificial Mordants on the Dyeing Performance of Cotton Knit Fabric with Natural Dyes Shuvo Brahma1*, Md. Rashedul Islam1, Salima Sultana Shimo2 and Rasheda Begum Dina1 1(Department of Wet Process Engineering, Bangladesh University of Textiles, Dhaka, Bangladesh) 2(Department of Industrial and Production Engineering, Bangladesh University of Textiles, Dhaka, Bangladesh) Corresponding Author: Shuvo Brahma Abstract: This work aims on an effort to determine the effect of some natural and artificial mordants on various natural dyes for cotton fabric dyeing. As natural mordant Eucalyptus Bark, Arjun Bark and Khair was used on cotton knit fabric under the treatment of three natural dyes namely Marigold, Eucalyptus leaf and Henna. As artificial mordants, potash alum and tannic acid were used along with natural mordants for further improvement of color strength. The cotton knit fabrics were scoured & bleached before dyeing. Concentrations of mordants were varied. Color strength and wash fastness properties were evaluated to determine the best mordant for particular dyes. It was observed that both the color strength and wash fastness properties increased with the application of mordants especially artificial mordants. Keywords: Natural dye, Natural Mordant, Artificial Mordant, Color strength, Fastness Properties. ----------------------------------------------------------------------------------------------------------------------------- -
Analysis of Natural Dyes and Metal Threads Used in 16Th
Shibayama et al. Heritage Science (2015) 3:12 DOI 10.1186/s40494-015-0037-2 RESEARCH ARTICLE Open Access Analysis of natural dyes and metal threads used in 16th -18th century Persian/Safavid and Indian/Mughal velvets by HPLC-PDA and SEM-EDS to investigate the system to differentiate velvets of these two cultures Nobuko Shibayama1*, Mark Wypyski1 and Elisa Gagliardi-Mangilli2 Abstract Introduction: Analyses of natural dyes and the metal of the metal-wrapping threads used in 16th -18th century Persian/Safavid and Indian/Mughal period velvets were performed on these textiles in the collection of The Metropolitan Museum of Art. The purpose was to determine whether velvets from the two cultures, which have shown problems in the past with attribution based on historical and iconographical studies, could be more precisely differentiated with the additional evidence from identification of their natural dyes and metals along with information of weaving techniques. Dyes and metal of the metal-wrapped threads from fifteen Persian velvets and six Indian velvets were analyzed by high performance liquid chromatography with photo diode array detector and by scanning electron microscopy with energy dispersive X-ray spectrometry respectively. Results: There seem to be types of dyes which specifically characterize the velvets of each culture, as well as types of dyes commonly found in velvets of both cultures. Dyes typical of Persian velvets are cochineal and yellow larkspur, while lac and turmeric are characteristic of Indian velvets. The dyes commonly found are a combination of yellow larkspur and indigo dye in green, as well as safflower, indigo dye, soluble redwoods, and tannin dye. -
Product Catalog Product Catalog Product
KREMER /// PRODUCT CATALOG www.kremerpigments.com PRODUCT CATALOG Table of Contents Pigments 01 TABLE OF Dyes & Vegetable Color CONTENTS Paints 02 Fillers & Building Materials 03 Mediums, Binders & Glues 04 Solvents, Chemicals & Additives 05 Ready-made Colors & Gilding Materials 3 01 Pigments 06 31 02 Dyes & Vegetable Color Paints Linen, Paper 35 03 Fillers & Building Materials & Foils 41 04 Mediums, Binders & Glues 53 05 Solvents, Chemicals & Additives 07 56 06 Ready-made Colors & Gilding Brushes Materials 66 07 Linen, Paper & Foils 08 69 08 Brushes Tools, Packaging & 74 09 Tools, Packaging & Supplies Supplies 10 82 Books & Color Charts 09 85 11 General Information Books & Color Charts 10 General Information 11 For further information and prices please visit us at www.kremerpigments.com 1 Icon-Legend ICON-LEGEND The following Icons are used in the brochure: Hazardous Item Read the Material Safety Data sheet carefully – you can find all Disclaimer product sheets under www.kremerpigments.com and consult our safe handling procedures – see Chapter 11. Not for home use! To buy this product you have to be over 21 years old. Please send us a copy of your identity card . These products require a Hazardous Item Disclaimer. Please fill out the form on page 116 or at www. kremerpigments. com and submit with your order. Cautionary Products may contain hazardous substances. Label Read the ACMI cautionary label carefully and consult our safe handling procedures – see Chapter 11. For further product-specific information please visit us at www.kremerpigments.com. Approved Products bearing the AP Product Seal of ACMI are certified in a Product program of toxicological evaluation By a medical expert to con- tain no materials in suMcient quantities to be toxic or injurious to humans or cause acute or chronic health problems. -
Eco-Dyeing of Wool with Rubia Cordifolia Root Extract: Assessment
Yusuf et al. Textiles and Clothing Sustainability (2016) 2:10 Textiles and Clothing DOI 10.1186/s40689-016-0021-6 Sustainability RESEARCH Open Access Eco-dyeing of wool with Rubia cordifolia root extract: Assessment of the effect of Acacia catechu as biomordant on color and fastness properties Mohd Yusuf1* , Faqeer Mohammad2, Mohd Shabbir2 and Mohd Ali Khan3 Abstract In the present study, anthraquinone colorants were extracted from powdered Rubia cordifolia roots and applied on wool fiber. Acacia catechu is used as a biomordant, a replacement to metallic mordants, for wool dyeing, and the effect on color characteristics and fastness properties was assessed. Shades on wool of red tones with good to excellent color fastness properties were obtained. Pre-mordanting with A. catechu improved the overall color and fastness parameters, due to the maximum dye uptake. Auxochromic groups responsible for interaction of dye and wool were studied by Fourier transform infrared (FTIR) analysis of R. cordifolia extract. The surface morphology of dyed wool fiber was investigated by scanning electron microscopy (SEM) for any changes on fiber after dyeing. Keywords: Natural dye, Biomordant, Color, Fastness, FTIR, Rubia cordifolia Background green alternative towards synthetic dyes (Yusuf et al. In the present context of eco-preservation, natural dyes 2012; Velmurugan et al. 2009). have acquired tremendous commercial potential as some Low reactivity of natural dyes to wool has been a con- of the synthetic dyes are associated with the release of cern to researchers in the past, and a lot of research has enormous amount of hazardous chemicals into the en- been done to understand the dyeing mechanism of natural vironment (Yusuf et al. -
Toolkit for Sustainable Textile Production
Publisher All India Artisans and Craftworkers Welfare Association (AIACA) Switch Asia- SUSTEX Project Implementing Partner-India, 18, Community Centre, 3rd Floor, East of Kailash New Delhi- 110065 India Phone: +91.11.26416492/93/94 | Fax: +91.11.26416491 www.aiacaonline.org | mail to: [email protected] under European Commission – SWITCH ASIA ‘Sustainable Textiles for Sustainable Development’ Project Research and Preliminary Editing KAARAK Enterprise Development Services Pvt. Ltd. # 3153, Sector A Pocket B & C, Vasant Kunj New Delhi-110070, India AIACA Editorial Team Ravi Kharka, Project Manager, Switch Asia Project Mayank Trivedi, Project Coordinator, Policy Research and Advocacy Printed at Fortune India Printers C-5, Sector-8, Noida (U.P.) www.fortuneprinters.com | mail to: [email protected] © SWITCH-Asia Project Partners and the European Commission Reproduction and dissemination of material in this publication for educational or other non-commercial purposes is authorized without prior written permission from the copyright holders, provided the source is fully acknowledged. This publication has been produced for SWITCH-Asia Programme and the European Commission. The contents of this publication are the sole responsibility of the ‘KAARAK Enterprise Development Services Pvt. Ltd.’ (consultant assigned to develop this manual) under the project being implemented by SUSTEX Project Partners (Traidcraft, AIACA and COTEX) on Sustainable Consumption and Production (SCP) and can in no way be taken to reflect the views of the European Commission. PREFACE The Toolkit for Sustainable Textile Production (TSTP) has been designed to encourage sustainable production practices amongst the textile producers through access to technical, economic and environmental resources from the textile production chain. This toolkit was developed primarily for small and medium enterprises working in the area of textile manufacturing.