Automatic Morphology Control of Liquid Metal Using a Combined Electrochemical and Feedback Control Approach
Total Page:16
File Type:pdf, Size:1020Kb
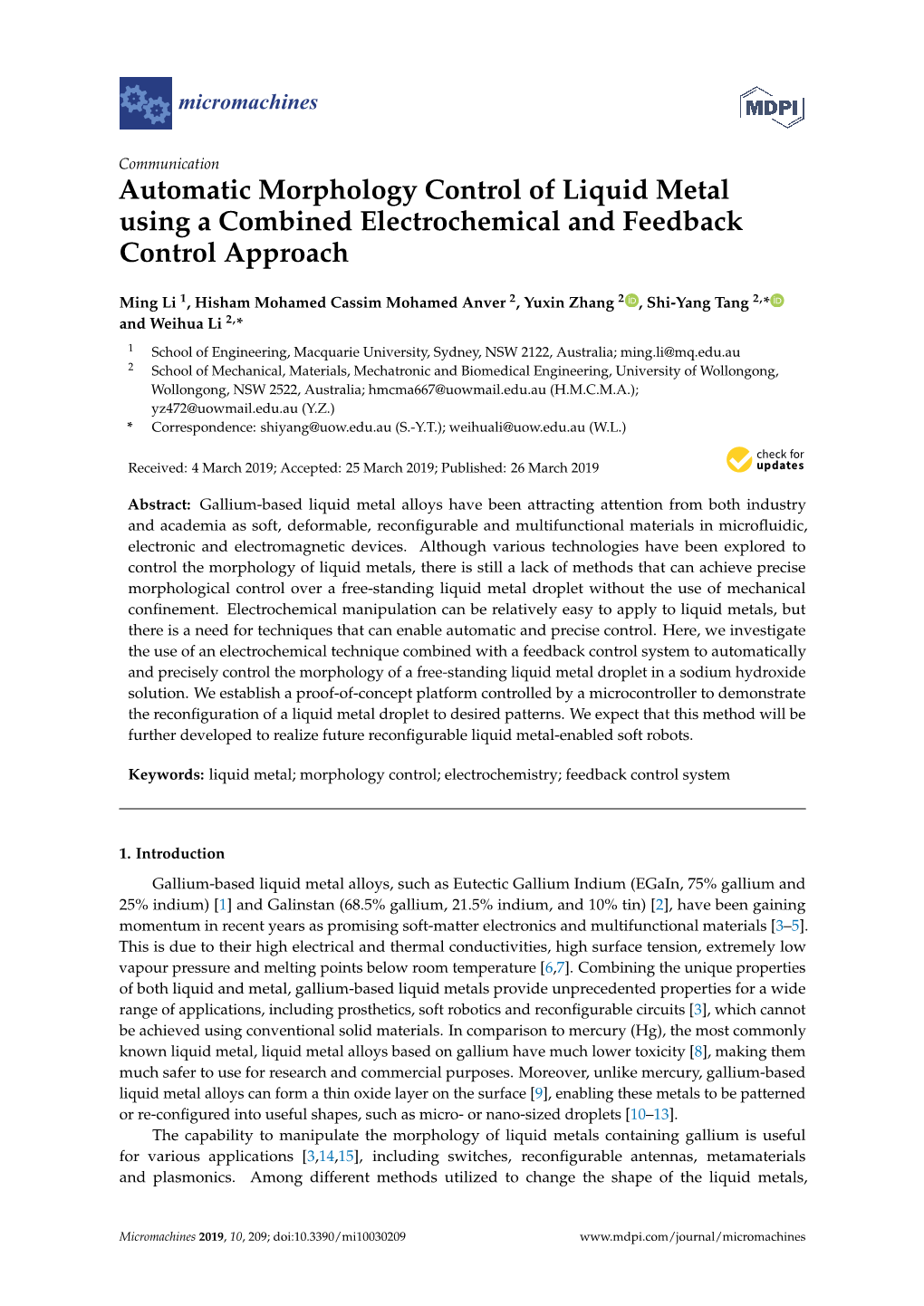
Load more
Recommended publications
-
Design and Experimentation of a Tunably Compliant Robotic Finger
DESIGN AND EXPERIMENTATION OF A TUNABLY COMPLIANT ROBOTIC FINGER USING LOW MELTING POINT METALS by HEON JOO A thesis submitted in partial fulfillment of the requirements for the degree of MASTER OF SCIENCE IN MECHANICAL ENGINEERING WASHINGTON STATE UNIVERSITY Department of Mechanical and Materials Engineering JULY 2017 c Copyright by HEON JOO, 2017 All Rights Reserved c Copyright by HEON JOO, 2017 All Rights Reserved To the Faculty of Washington State University: The members of the Committee appointed to examine the thesis of HEON JOO find it satisfactory and recommend that it be accepted. John Swensen, Ph.D., Chair Arda Gozen, Ph.D. Matthew Taylor, Ph.D. ii ACKNOWLEDGMENTS I would like to thank my advisor, Dr.Swensen who has taught and guided so far for this thesis completion and also thank Dr.Taylor for joining me in his project. During the last two years, my wife sincerely supported me with a lot of courage and hope and my son was another delight that made me endure here to the end. I would like to express my deepest gratitude to all of the families in Korea, especially my grandmother. She is the most appreciated and precious person in my life that made me today. Also, I would like to appreciate many Koreans we have known in Pullman. Lastly, I would like to give my infinite glory and gratitude to God who gave me and my family the strength, courage, and wisdom to overcome any difficulties. iii DESIGN AND EXPERIMENTATION OF A TUNABLY COMPLIANT ROBOTIC FINGER USING LOW MELTING POINT METALS Abstract by Heon Joo, M.S. -
Liquid-Based Reconfigurable Antenna Technology
sensors Review Liquid-Based Reconfigurable Antenna Technology: Recent Developments, Challenges and Future Habshah Abu Bakar 1, Rosemizi Abd Rahim 2,* , Ping Jack Soh 2,3 and Prayoot Akkaraekthalin 4,* 1 Department of Electrical Engineering, Politeknik Sultan Abdul Halim Muadzam Shah, Jitra 06000, Kedah, Malaysia; [email protected] 2 Faculty of Electronic Engineering Technology, Pauh Putra Campus, Universiti Malaysia Perlis, Pauh 02600, Perlis, Malaysia; [email protected] 3 Advanced Communication Engineering (ACE) Centre of Excellence, Universiti Malaysia Perlis, Kangar 01000, Perlis, Malaysia 4 Department of Electrical and Computer Engineering, Faculty of Engineering, King Mongkut’s University of Technology North Bangkok (KMUTNB), 1518 Pracharat 1 Rd., Wongsawang, Bangsue, Bangkok 10800, Thailand * Correspondence: [email protected] (R.A.R.); [email protected] (P.A.) Abstract: Advances in reconfigurable liquid-based reconfigurable antennas are enabling new pos- sibilities to fulfil the requirements of more advanced wireless communication systems. In this review, a comparative analysis of various state-of-the-art concepts and techniques for designing reconfigurable antennas using liquid is presented. First, the electrical properties of different liquids at room temperature commonly used in reconfigurable antennas are identified. This is followed by a discussion of various liquid actuation techniques in enabling high frequency reconfigurability. Next, the liquid-based reconfigurable antennas in literature used to achieve -
A Complete Interfacial System Solution for Liquid Metal Electronics
A Complete Interfacial System Solution for Liquid Metal Electronics A dissertation submitted to the Graduate School of the University of Cincinnati in partial fulfillment of the requirements for the degree of Doctor of Philosophy in the Department of Materials Science & Engineering of the College of Engineering & Applied Science by Sarah E. Holcomb B.S., Rensselaer Polytechnic Institute, 2013 Committee Chair: Jason C. Heikenfeld, Ph.D. Abstract Liquid metal electronic devices have numerous advantages over traditional solid devices such as the ability to be flexed and stretched or reconfigured. Examples of such devices are wires, switches, polarizers, and antennas. Previously, mercury has been used as the room temperature liquid metal of choice but has been recently replaced by gallium liquid metal alloys (GaLMAs) which are non-toxic, have extremely low vapor pressures, and can remain liquid at temperatures as low as -19°C. A key difference in the performance of GaLMAs vs. mercury is the mechanically stabilizing, passivating oxide which forms instantly on the surface of GaLMAs in as little as 1 ppm oxygen environments. This oxide presents a significant challenge for reconfigurable device applications because it “sticks” to most surfaces, preventing reversible shape change, which alters the desired electrical performance. Proposed here are two novel methods of overcoming this challenge. These methods enable new capabilities for reconfigurable electronic devices. The first approach involves removing the oxide in situ as it is continuously formed in all practically achievable device environments. Oxide removal is commonly done through the use of hydrochloric acid (aqueous or vapor), which reacts with the gallium oxide to produce gallium chloride, which is not mechanically stabilizing, and water. -
Gallium-Based Liquid Metals and Their Hybrids As Smart Electronic Materials
University of Wollongong Research Online University of Wollongong Thesis Collection 2017+ University of Wollongong Thesis Collections 2018 Gallium-based liquid metals and their hybrids as smart electronic materials Long Ren University of Wollongong Follow this and additional works at: https://ro.uow.edu.au/theses1 University of Wollongong Copyright Warning You may print or download ONE copy of this document for the purpose of your own research or study. The University does not authorise you to copy, communicate or otherwise make available electronically to any other person any copyright material contained on this site. You are reminded of the following: This work is copyright. Apart from any use permitted under the Copyright Act 1968, no part of this work may be reproduced by any process, nor may any other exclusive right be exercised, without the permission of the author. Copyright owners are entitled to take legal action against persons who infringe their copyright. A reproduction of material that is protected by copyright may be a copyright infringement. A court may impose penalties and award damages in relation to offences and infringements relating to copyright material. Higher penalties may apply, and higher damages may be awarded, for offences and infringements involving the conversion of material into digital or electronic form. Unless otherwise indicated, the views expressed in this thesis are those of the author and do not necessarily represent the views of the University of Wollongong. Recommended Citation Ren, Long, Gallium-based liquid metals and their hybrids as smart electronic materials, Doctor of Philosophy thesis, Institute for Superconducting and Electronic Materials, University of Wollongong, 2018. -
Soft Multifunctional Composites and Emulsions with Liquid Metals
PROGRESS REPORT Soft Materials www.advmat.de Soft Multifunctional Composites and Emulsions with Liquid Metals Navid Kazem, Tess Hellebrekers, and Carmel Majidi* of liquid metal (LM) and low-melting- Binary mixtures of liquid metal (LM) or low-melting-point alloy (LMPA) in point alloys (LMPAs). Referring to an elastomeric or fluidic carrier medium can exhibit unique combinations of Figure 1, LM systems span a wide range electrical, thermal, and mechanical properties. This emerging class of soft of length scales and architectures: mm- [8,9] multifunctional composites have potential applications in wearable com- scale channels embedded in elastomer (Figure 1A,B), traces deposited on a puting, bio-inspired robotics, and shape-programmable architectures. The substrate with a pressurized syringe[10] dispersion phase can range from dilute droplets to connected networks that (Figure 1C), microscale traces printed support electrical conductivity. In contrast to deterministically patterned with soft lithography[11] (Figure 1D), LM LM microfluidics, LMPA- and LM-embedded elastomer (LMEE) composites droplets[12,13] (Figure 1E,F), microscale are statistically homogenous and exhibit effective bulk properties. Eutectic droplets embedded in a polysiloxane[14] Ga-In (EGaIn) and Ga-In-Sn (Galinstan) alloys are typically used due to their (Figure 1G), and LM nanospheres synthe- sized with ultrasonication (Figure 1H).[15] high conductivity, low viscosity, negligible nontoxicity, and ability to wet to Composites composed of droplets sus- nonmetallic materials. Because they are liquid-phase, these alloys can alter pended in a continuous elastic phase the electrical and thermal properties of the composite while preserving the can be tailored to exhibit a unique and mechanics of the surrounding medium. -
Reactivity of Galinstan with Specific Transition Metal Carbides
Examensarbete 15 hp Mars 2014 Reactivity of Galinstan with Specific Transition Metal Carbides Sebastian Lindersson Kandidatprogrammet i Kemi Bachelor Programme in Chemistry Abstract Reactivity of Galinstan with Specific Transition Metal Carbides Sebastian Lindersson This project examines the reactivity of “Galinstan” against specific transition metal carbide (MeCx) films deposited on aluminum (Al) thin films. Galinstan is a non-toxic liquid metal alloy at room temperature, consisting of gallium, indium and tin, and has been studied in order to replace mercury in its’ applications, as well as new applications as microfluidics. However, Galinstan reacts with other conductive materials such as Al, therefore it is interesting to find solutions to prevent this. Thus, MeCx films were tested as barriers between Galinstan and Al. Two approaches of analysis have been performed: X-Ray Diffraction (XRD) was employed to identify potential phase changes of the MeCx films upon Galinstan exposure, and X-ray Photoelectron Spectroscopy (XPS) for determining whether the MeCx films were penetrated by Galinstan or not. It was seen that the MeCx films protected Al from reacting with Galinstan. However, the MeCx films proved to be sensitive to mechanical damages, and so were the Al films. By scratching a MeCx surface with a pipette tip, Galinstan would react with the Al underneath, resulting in crack formation. XPS analysis showed that there were no chemical changes upon scratching the MeCx surface, and the oxide layer remained intact. This lead to the conclusion that mechanical damages was the cause of the reactions between Galinstan and Al. It is believed that scratching the MeCx surface would allow Galinstan to diffuse through and react with the Al underneath. -
Production of Uniformly Sized Gallium-Based Liquid Alloy Nanodroplets Via Ultrasonic Method and Their Li-Ion Storage
materials Article Production of Uniformly Sized Gallium-Based Liquid Alloy Nanodroplets via Ultrasonic Method and Their Li-Ion Storage Chenghao Huang 1 , Junjie Zong 1, Xiaodong Wang 1, Qingpin Cao 1, Dongxian Zhang 1,2 and Jian-Zhong Jiang 1,* 1 International Center for New-Structured Materials (ICNSM), Laboratory of New-Structured Materials, State Key Laboratory of Silicon Materials, School of Materials Science and Engineering, Zhejiang University, Hangzhou 310027, China; [email protected] (C.H.); [email protected] (J.Z.); [email protected] (X.W.); [email protected] (Q.C.); [email protected] (D.Z.) 2 State Key Laboratory of Modern Optical Instrumentation, Zhejiang University, Hangzhou 310027, China * Correspondence: [email protected] Abstract: Gallium-based liquid alloys are attractive due to their unique properties, and they can potentially be applied in the field of flexible electronics as coolant materials for nuclear and liquid batteries, due to the high thermal conductivity and excellent fluid properties of liquid metals. However, it is still challenging to fabricate gallium-based liquid alloy nanodroplets with uniform and small size. Here, we performed a systematical study on the influence of various factors affecting the size of nanodroplets. Liquid metal nanodroplets with an average size of 74 nm and narrow size distribution were successfully fabricated. Li-ion half-cells were assembled with eutectic GaIn (eGaIn) nanodroplets as anode active materials, which showed higher specific capacity than the bulk eGaIn alloy under the same testing conditions. Keywords: Ga-based liquid alloys; nanodroplets; ultrasonic technique; surfactant; centrifugation; Citation: Huang, C.; Zong, J.; Wang, X.; Cao, Q.; Zhang, D.; Jiang, J.Z. -
Buoyancy-Driven Two-Phase Flows of Liquid Metal Contributing to the Generation of Electricity from a Fusion Reactor by Magnetohydrodynamic Energy Conversion
Buoyancy-Driven Two-Phase Flows of Liquid Metal contributing to the Generation of Electricity from a Fusion Reactor by Magnetohydrodynamic Energy Conversion A Thesis Submitted to the University of London for the Degree of Doctor of Philosophy by Charles Edwin Wood School of Engineering and Materials Science Queen Mary University of London Mile End E1 4NS October 2015 Declaration I, Charles Edwin Wood, confirm that the research included within this thesis is my own work or that where it has been carried out in collaboration with, or supported by others, that this is duly acknowledged below and my contribution indicated. I attest that I have exercised reasonable care to ensure that the work is original, and does not to the best of my knowledge break any UK law, infringe any third party’s copyright or other Intellectual Property Right, or contain any confidential material. I accept that the College has the right to use plagiarism detection software to check the electronic version of the thesis. I confirm that this thesis has not been previously submitted for the award of a degree by this or any other university. The copyright of this thesis rests with the author and no quotation from it or information derived from it may be published without the prior written consent of the author. Signature: Charles E. Wood Date: October, 2015 2 Abstract Fusion is desirable for providing the world’s future base-load power capacity due to its lack of greenhouse gas emissions, low environmental and safety risk, and large, secure fuel reserves. Fusion power plants are not expected to deliver electricity commercially until 2050, when it is expected that most fossil-fuelled power plants will have been removed from the global electricity generating mix. -
Supply and Demand of Lithium and Gallium Imprint
Information Center of Ministry of Land and Resources Supply and Demand of Lithium and Gallium Imprint Authors: Cui Rongguo, Guo Juan, Yin Liwen (ICMLR) Dieter Huy, Maren Liedtke (BGR) Contact: Information Center of Ministry of Land and Resources (ICMLR) No. 64, Funeidajie Street 100812 Bejing [email protected] Federal Institute for Geosciences and Natural Resources Stilleweg 2 30655 Hannover [email protected] Layout: Jolante Duba Edition dated: May 2016 ISBN: 978-3-943566-33-8 Titelbild: BGR Supply and Demand of Lithium and Gallium May 2016 Supply and Demand of Lithium and Gallium 5 Content Supply and Demand of Lithium 9 1 Introduction 10 2 Distribution of lithium reserves and resources 10 2.1 Reserves and resources 10 2.2 Changes of reserves and resources 12 2.3 Regional distribution of reserves and resources 13 2.4 Reserves and resources in China 14 3 Lithium production 14 3.1 Changes of lithium production 14 3.2 Regional distribution of lithium production 14 3.3 Major lithium producers 15 3.4 Lithium production in China 16 4 Lithium supply and consumption 17 4.1 Lithium consumption 17 4.2 Lithium consumption markets 17 4.3 Trade 18 4.4 Lithium consumption in China 19 4.5 Lithium price 21 5 Outlook for lithium supply and demand 21 5.1 Outlook for lithium demand 21 5.2 Outlook for lithium supply capacity 24 5.3 China lithium supply capacity 25 6 Conclusions 25 6.1 Lithium reserves and resources abundant across the world 25 6.2 The supply of global lithium highly concentrated 25 6.3 The demand for global lithium strongly in future -
Biomedical Applications of Liquid Metal Nanoparticles: a Critical Review
biosensors Review Biomedical Applications of Liquid Metal Nanoparticles: A Critical Review Haiyue Li 1, Ruirui Qiao 2, Thomas P. Davis 2,* and Shi-Yang Tang 3,* 1 Department of Chemistry and Biochemistry, University of California, San Diego, CA 92093, USA; [email protected] 2 ARC Centre of Excellence in Convergent Bio-Nano Science and Technology and Australian Institute for Bioengineering and Nanotechnology, The University of Queensland, Brisbane, QLD 4072, Australia; [email protected] 3 Department of Electronic, Electrical and Systems Engineering, University of Birmingham, Edgbaston, Birmingham B15 2TT, UK * Correspondence: [email protected] (T.P.D.); [email protected] (S.-Y.T.) Received: 15 October 2020; Accepted: 27 November 2020; Published: 30 November 2020 Abstract: This review is focused on the basic properties, production, functionalization, cytotoxicity, and biomedical applications of liquid metal nanoparticles (LMNPs), with a focus on particles of the size ranging from tens to hundreds of nanometers. Applications, including cancer therapy, medical imaging, and pathogen treatment are discussed. LMNPs share similar properties to other metals, such as photothermal conversion ability and a propensity to form surface oxides. Compared to many other metals, especially mercury, the cytotoxicity of gallium is low and is considered by many reports to be safe when applied in vivo. Recent advances in exploring different grafting molecules are reported herein, as surface functionalization is essential to enhance photothermal therapeutic effects of LMNPs or to facilitate drug delivery. This review also outlines properties of LMNPs that can be exploited in making medical imaging contrast agents, ion channel regulators, and anti-pathogenic agents. -
Gallium-Based Room Temperature Liquid Metals and Its Application To
View metadata, citation and similar papers at core.ac.uk brought to you by CORE provided by ASU Digital Repository Gallium-Based Room Temperature Liquid Metals and its Application to Single Channel Two-Liquid Hyperelastic Capacitive Strain Sensors by Shanliangzi Liu A Thesis Presented in Partial Fulfillment of the Requirements for the Degree Master of Science Approved April 2015 by the Graduate Supervisory Committee: Konrad Rykaczewski, Chair Owen Hildreth Terry Alford Marcus Herrmann ARIZONA STATE UNIVERSITY May 2015 ABSTRACT Gallium-based liquid metals are of interest for a variety of applications including flexible electronics, soft robotics, and biomedical devices. Still, nano- to microscale device fabrication with these materials is challenging because of their strong adhesion to a majority of substrates. This unusual high adhesion is attributed to the formation of a thin oxide shell; however, its role in the adhesion process has not yet been established. In the first part of the thesis, we described a multiscale study aiming at understanding the fundamental mechanisms governing wetting and adhesion of gallium-based liquid metals. In particular, macroscale dynamic contact angle measurements were coupled with Scanning Electron Microscope (SEM) imaging to relate macroscopic drop adhesion to morphology of the liquid metal-surface interface. In addition, room temperature liquid-metal microfluidic devices are also attractive systems for hyperelastic strain sensing. Currently two types of liquid metal-based strain sensors exist for inplane measurements: single-microchannel resistive and two- microchannel capacitive devices. However, with a winding serpentine channel geometry, these sensors typically have a footprint of about a square centimeter, limiting the number of sensors that can be embedded into. -
The Effect of Static Liquid Galinstan on Common Metals and Non-Metals at Temperatures up to 200 °C
Canadian Journal of Chemistry The Effect of Static Liquid Galinstan on Common Metals and Non-Metals at Temperatures up to 200 °C Journal: Canadian Journal of Chemistry Manuscript ID cjc-2020-0227.R1 Manuscript Type: Article Date Submitted by the 19-Jul-2020 Author: Complete List of Authors: Geddis, Philip; Natural Resources Canada, CanmetENERGY-Ottawa Wu, Lijun; Natural Resources Canada, CanmetENERGY-Ottawa McDonald, Andrew; Natural Resources Canada, CanmetENERGY-Ottawa Chen, Steven; Natural Resources Canada, CanmetENERGY-Ottawa Clements, DraftBruce; Natural Resources Canada, CanmetENERGY-Ottawa Is the invited manuscript for consideration in a Special Not applicable (regular submission) Issue? : Galinstan corrosion, Gallium corrosion, liquid metal corrosion, liquid Keyword: metal embrittlement, magnetohydrodynamics https://mc06.manuscriptcentral.com/cjc-pubs Page 1 of 31 Canadian Journal of Chemistry The Effect of Static Liquid Galinstan on Common Metals and Non-Metals at Temperatures up to 200 °C Philip Geddis*, Lijun Wu, Andrew McDonald, Steven Chen, Bruce Clements * [email protected], 613-947-3128 ORCID 0000-0002-5610-9748 CanmetENERGY-Ottawa, Natural Resources Canada, Ottawa, Ontario, K1A 1M1, Canada Draft KEYWORDS Galinstan corrosion, Gallium corrosion, liquid metal embrittlement, liquid metal corrosion, magnetohydrodynamics DECLARATIONS FUNDING This research has been funded by Natural Resources Canada through the Energy Innovation Program (EIP). CONFLICTS OF The authors declare that they have no conflict of interest. INTEREST/COMPETING INTERESTS: AVAILABILITY OF DATA The datasets generated during and/or analyzed during the current study are AND MATERIALS available from the corresponding author on reasonable request. AUTHORS’ CONTRIBUTIONS Study conception and design was carried out by Philip Geddis. Material preparation and data collection were carried out by Philip Geddis, Andrew McDonald, and Steven Chen.