Dewavrin & Souppez 2018
Total Page:16
File Type:pdf, Size:1020Kb
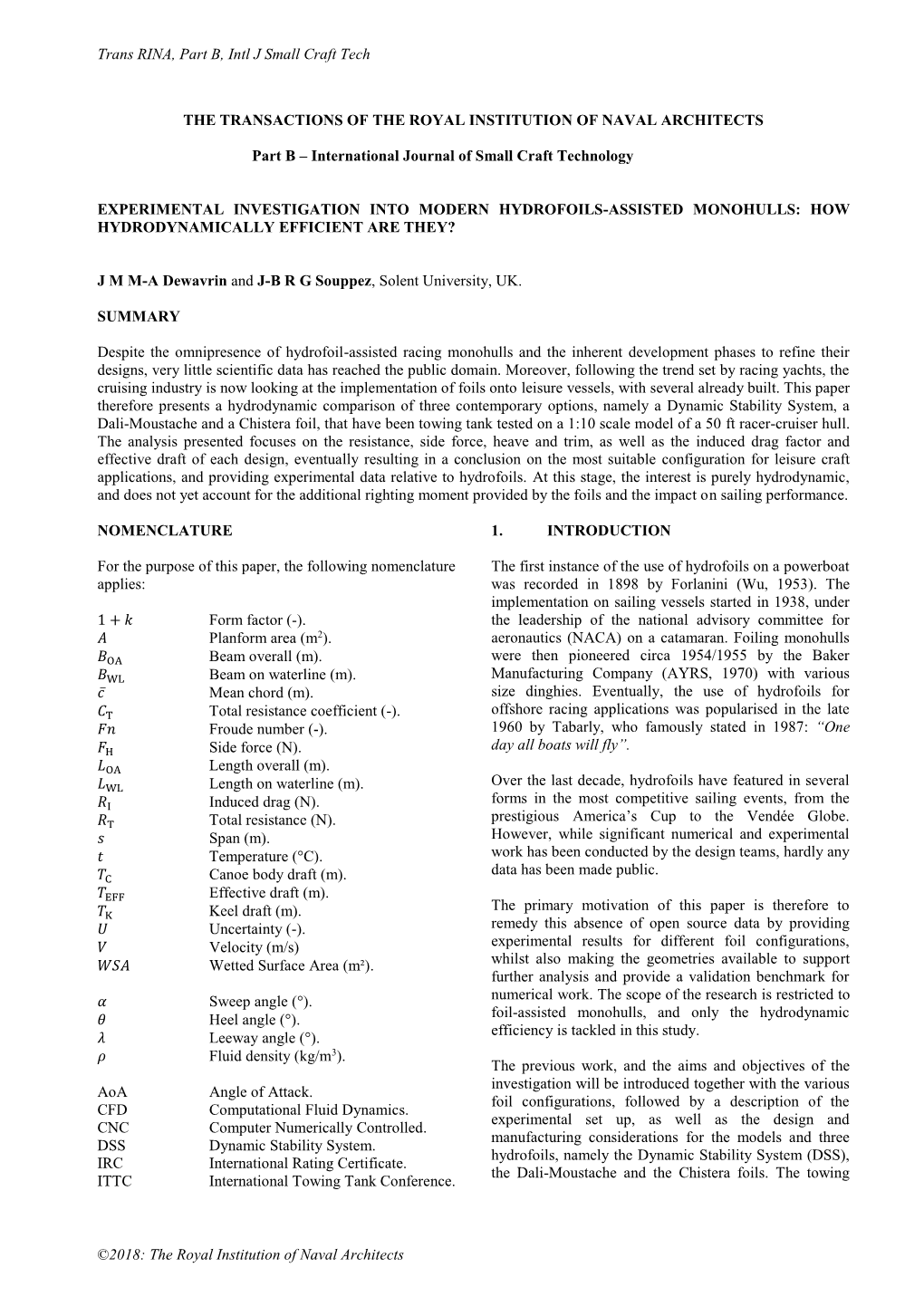
Load more
Recommended publications
-
Épisode 24 Autumn 2019
Yacht Brokerage Épisode 24 Autumn 2019 Kriss, p. 4 Summary w Editorial . .2 w Recent Sales ..................3 w Brokerage News ............4 w Ice Yachts Agent .......... 12 w New Construction ........ 13 w Sales Index .................. 14 w Racing Index ............... 18 w Charter ....................... 19 w Charter Index .............. 30 w Upcoming Events ......... 35 w BGYB Contact .............. 36 Atlantic, p. 7 Exhibited at the BROKERAGE RACING CHARTER Cannes Yachting Festival 2019 Blue Diamond, p. 9 SALE, CHARTER & MANAGEMENT Also specialises in Transoceanic charter www.bernard-gallay.com Yacht Brokerage w EDITORIAL w 135ft Sir Norman Foster Design OCEAN SAPPHIRE, p. 5 Photo Richard Sprang The Yacht Market Overview Bernard Gallay Sales a watchful eye on the many mega sailing yachts and catamarans, 78ft S/CAT TAJ and 58ft Ipanema 58 S/Cat motor yachts which increasingly grace the Balearic ports. ARAOK as well as the luxury high class 100ft S/Y Wally ft GYB’s year was kicked off with the sale of 104 S/Y Elsewhere, the opening of our Port-Napoléon office DARK SHADOW will be available in the region. BSloop OCEAN SEVEN². A particularly nice start to close to Marseille is being commissioned to specifically 2019 on familiar ground, this being the 2nd time in The enduring fashionability of the catamaran in the focus on the “60 feet plus” yacht market, giving the charter sphere was particularly evident this summer recent years that BGYB was chosen to represent OCEAN advantage of long-term dry-docking facilities. SEVEN² during a commercial deal. Shortly after, followed and demand was high for this style of boat in our The Cannes Yachting Festival 2019 will give BGYB the the sale of 121ft S/Y Ed Dubois Sloop DAMAHWIL. -
Yacht Brokerage Épisode 21 Spring 2018
Yacht Brokerage Épisode 21 Spring 2018 Damahwil, p. 11 Summary w Editorial . .2 w Brokerage News ............3 w Brokerage Index .......... 12 w Racing Index ............... 16 w Charter ....................... 17 w Charter Index .............. 26 w Upcoming Events ......... 31 w .............. 32 BGYB Contact Photo © Kristina Strobel RACING CHARTER BROKERAGE The Mercy Boys, p. 18 SALE, CHARTER & MANAGEMENT Also specialises in Transoceanic charter www.bernard-gallay.com Yacht Brokerage w EDITORIAL w Photos © Jesús Renedo 100ft Carbon Sloop “BLUE DIAMOND”, p. 11 Photo Richard Sprang The Yacht Market Overview Bernard Gallay Sales We are very much looking forward to showcasing four the Reichel-Pugh 72 ARAGON, the VOR70 OCEAN of our finest yachts at this year’s Palma Superyacht BREEZE and the fantastic 67ft Open HIGH SPIRIT. For 2017 was BGYB’s best year yet in terms of number Show from April 27th to May 1st 2018. a combination of performance and comfort, the racer- and value of boats sold. Notable sales include: cruiser Yachts SOUTHERN STAR, Mylius 60 SUD, and ft Charter Privilege 615s ETANA and MAEVIE, 78 VPLP Sailing the ICE 62s SUENO and CANTELOUP VIII offer a great Just a few months in, and 2018 has already been an Catamaran CORIOLAN VI, S/Y G75 Garcia ANNKA 1, compromise for keen sailors in need of excitement! Racing Volvo Open 70 GIACOMO, the Swan 82 ALPINA, exciting year in the BGYB Charter Department. Our fleet ft 107ft Large Sailing Yacht ROSINANTE OF NOTIKA, as is growing in size, with 163 M/Y THE MERCY BOYS As for our multihulls, Lagoon 620 MELARNIE is available ft well as Apreamare 65 SATURN. -
Development of a 6-DOF Dynamic Velocity Prediction Program for Offshore Racing Yachts Paul Kerdraon, Boris Horel, Patrick Bot, Adrien Letourneur, David Le Touzé
Development of a 6-DOF Dynamic Velocity Prediction Program for offshore racing yachts Paul Kerdraon, Boris Horel, Patrick Bot, Adrien Letourneur, David Le Touzé To cite this version: Paul Kerdraon, Boris Horel, Patrick Bot, Adrien Letourneur, David Le Touzé. Development of a 6-DOF Dynamic Velocity Prediction Program for offshore racing yachts. Ocean Engineering, Elsevier, 2020, 212, pp.107668. 10.1016/j.oceaneng.2020.107668. hal-02884999 HAL Id: hal-02884999 https://hal.archives-ouvertes.fr/hal-02884999 Submitted on 8 Oct 2020 HAL is a multi-disciplinary open access L’archive ouverte pluridisciplinaire HAL, est archive for the deposit and dissemination of sci- destinée au dépôt et à la diffusion de documents entific research documents, whether they are pub- scientifiques de niveau recherche, publiés ou non, lished or not. The documents may come from émanant des établissements d’enseignement et de teaching and research institutions in France or recherche français ou étrangers, des laboratoires abroad, or from public or private research centers. publics ou privés. Distributed under a Creative Commons Attribution| 4.0 International License Development of a 6-DOF Dynamic Velocity Prediction Program for offshore racing yachts Paul Kerdraon a,b,<, Boris Horel b, Patrick Bot c, Adrien Letourneur a, David Le Touzé b a VPLP Design, 18 Allée Loïc Caradec, 56000 Vannes, France b Ecole Centrale Nantes, LHEEA Lab. (ECN and CNRS), 1 Rue de la Noë, 44300 Nantes, France c Naval Academy Research Institute - IRENAV CC600, 29240 Brest Cedex 9, France Thanks to high lift-to-drag ratios, hydrofoils are of great interest for high-speed vessels. -
Gunboat-72V Brochure.Pdf
ELEVATED SAILING ABOUT GUNBOAT — Gunboat began in 2002 with the vision BORN IN THE USA, INNOVATION AND EVOLUTION. to design and build fast comfortable, MADE IN FRANCE. family-friendly cruising catamarans The elevated experience of a Gunboat is that utilized the latest in race boat Since 2016, Gunboat operations have profound, and exhilarating, throughout technology. At that time, most cruising benefited from a high level of industry the journey and the destination. Speed catamarans were comfortable but knowledge, build expertise and sound and seaworthiness to safely handle the clearly not great performers. On financial backing under the ownership toughest blue water passages. Gliding the other side of the spectrum, the of Grand Large Yachting. Clients receive along faster than the wind. Sinking into performance world had embraced the best of both worlds: the efficiency pure comfort and absorbing the vibe of multihulls with one world record gained by the process-driven culture the yacht during sunsets at anchor. That after another falling to maxi racing and scale of a recognized industry distinctive feeling of intrigue and deep catamarans. player, and the boutique craftsmanship satisfaction is not by chance. We’ve of high-tech, semi-custom yacht gone the extra mile and millimeter too, Through 20 years of head-turning building. Each Gunboat is unique and throughout the design, engineering and designs, enviable cruising speeds, and celebrated by the Gunboat team. build of your new Gunboat. regatta podiums, Gunboat set the We want clients to enjoy the build bar and continues to raise it, applying process too, including their time at our Are you ready to join the fleet? innovation and proven technologies to purpose-built, 3600 sq meter facility in the desires of performance sailing and La Grande-Motte France. -
Oceanwings, Une Contribution À La Décarbonation Du Transport Maritime Par
Séminaire Management de l’innovation n n n Séance du 20 novembre 2019 Oceanwings, une contribution à la décarbonation du transport maritime par n Marc Van Peteghem n Architecte naval, associé fondateur de l’agence VPLP design En bref Marc Van Peteghem est une référence dans la conception des bateaux multicoques tant de croisière que de compétition. Son agence a notamment conçu le trimaran Oracle, vainqueur en 2010 de la Coupe de l’America, gréé avec une voile affalable et automatisée. L’adaptation de ce système aux bateaux à moteur permet de réaliser des économies d’énergie et de réduire les émissions de gaz à effet de serre du transport maritime, qui traite 90 % du commerce international. Sur un plan plus personnel, Marc Van Peteghem a également créé l’ONG Watever pour soutenir la construction navale au Bangladesh, puis cofondé en 2013 The Sustainable Design School, qui place l’homme au centre de solutions innovantes pour un développement durable. Compte rendu rédigé par Florence Berthezène L’Association des Amis de l’École de Paris du management organise des débats et en diffuse les comptes rendus, les idées restant de la seule responsabilité de leurs auteurs. Elle peut également diffuser les commentaires que suscitent ces documents. Séminaire organisé grâce aux parrains de l’École de Paris du management : Algoé 1 • Carewan1 • Chaire Futurs de l’industrie et du travail • Danone • EDF • Else & Bang • ENGIE • Fabernovel • Fondation Roger Godino • Groupe BPCE • Groupe OCP • GRTgaz • IdVectoR2 • IPAG Business School • L’Oréal • La Fabrique de l’industrie • MINES ParisTech • RATP • Renault-Nissan Consulting • Syndicat des entreprises de l’économie numérique et des technologies nouvelles 3 • UIMM • Ylios 1 1. -
Press Trip: 20 – 21 September 2018 Pays De Cornouaille >>> Golfe Du Morbihan – Vannes >>> Lorient PRESS TRIP BRETAGNE SAILING VALLEY 19-20-21 SEPTEMBER
Press Trip: 20 – 21 September 2018 Pays de Cornouaille >>> Golfe du Morbihan – Vannes >>> Lorient PRESS TRIP BRETAGNE SAILING VALLEY 19-20-21 SEPTEMBER Wednesday 19th September 2018 Journalists arrive at Quimper train station (variable arrival times, according to individual travel arrangements) 8pm: Dinner Chez Max – Quimper / Presentation of Bretagne Sailing Valley (Carole Bourlon, mission manager for the Eurolarge Innovation programme at Bretagne Développement Innovation) 10pm: Hôtel Mercure - Quimper Thursday 20th September 2018 Pays de Cornouaille (Finistère) and Golfe du Morbihan – Vannes (Morbihan) 8.30am - 1.30pm: Pays de Cornouaille (Finistère) 8.10am: Leave from the hotel Mercure Quimper by coach: Quimper – Combrit 8.30am - 9.30am: Visit to the POGO STRUCTURES boatyard, Combrit POGO STRUCTURES is a yard employing more than 60 employees mass producing offshore racing yachts, including the Mini 6,50 and Class40. 9.35 - 9.45am: by coach Combrit - Port-la-Forêt 9.50 - 10.15am: reception at PÔLE FINISTERE COURSE AU LARGE, Port-la-Forêt Presentation of the national offshore racing skipper training centre (Figaro, Imoca, Ultim’) and the Bretagne - Crédit Mutuel sector of excellence. 10.15 - 11.15am: meeting with MerConcept, the MACIF race team and holder of the round the world solo record (Trophée Saint-Exupéry, 12/2017) 11.20 - 12.20am: meeting with companies (sailing club, Port-la-Forêt): - AIM 45: navigation data analysis for yacht performance and safety (structure, constraints); - INO ROPE: innovative textile rigging company; - MER AGITEE: innovative project for sail sensors 12.20 - 13.20pm: buffet lunch offered by Quimper Cornouaille Développement (sailing club) 1.30 - 2.55pm: transfer by coach: Port-la-Forêt (Finistère) – Tréffléan (Morbihan) 3pm - 9pm: Golfe du Morbihan – Vannes Agglomération (Morbihan) 3.00 - 4.00pm: visit to HEOL COMPOSITES, Tréffléan Presentation of the manufacturing process of patented hollow carbon parts recognised for their lightweight efficiency. -
TJV Dossierpresse 2019-06
TROPHÉE JULES VERNE, L’EXTRAORDINAIRE RECORD SOMMAIRE PRÉAMBULE P4 LE TROPHÉE JULES VERNE EN CHIFFRES P5 PARCOURS DE L’EXPOSITION P6 1 VOUS AVEZ DIT 80 JOURS ? P7 2 GENÈSE D’UN DÉFI P8-9 3 500 ANS DE CIRCUMNAVIGATION P10 4 HOMMES ET NAVIRES DE L’EXTRÊME P10 5 À BORD P11 6 À L’ASSAUT DU JULES VERNE P11 7 LES RECORDS P12-13 8 PLEIN PHARE SUR LE JULES VERNE P14 9 TOUJOURS PLUS VITE ! P15 LE MUSÉE NATIONAL DE LA MARINE P17 INFORMATIONS PRATIQUES P17 ÉQUIPAGE & CONTACTS PRESSE P18 Groupama 3 et son équipage rentrent victorieux dans la rade de Brest. © Arnaud Pilpré / Groupama 31 Janvier 1993. Départ de Bruno Peyron à Ouessant sur Commodore Explorer pour le premier Trophée Jules Verne. Le spi de 450 m2 est hissé. Peter Blake sur son Enza New Zealand a profité d’une mince fenêtre météo pour partir plus tôt en fin de nuit. © Christian Février 3 TROPHÉE JULES VERNE, L’EXTRAORDINAIRE RECORD PRÉAMBULE TROPHÉE JULES VERNE L’EXTRAORDINAIRE RECORD EXPOSITION DU 28 JUIN 2019 AU 3 JANVIER 2021 Musée national de la Marine, Brest Créé par des marins pour des marins en 1992, le Trophée Jules Verne est un impressionnant défi nautique : le pari d’une circumnavigation à la voile, en moins de 80 jours, d’est en ouest, sans escale et sans assistance. Dans le sillage de Philéas Fogg, le héros du roman de Jules Verne, et sur les traces de Magellan, seules neuf équipes ont soulevé le précieux trophée. Présentée au château-musée de Brest, qui ofre une vue imprenable sur les arrivées et départs de nombreux records et tours du monde en solitaire ou en équipage, l’exposition « Trophée Jules Verne, l’extraordinaire record » rend hommage aux coureurs d’océans et témoigne de la singularité de ce défi et de son trophée symbolique, œuvre d’art signée Thomas Shannon. -
Astus 16.5 Corsair 760 Tricat 30 Easy To
64-71 moins de 40_MM180-US.qxp_essai 10/11/2016 14:08 Page64 MULTIHULLS UP TO 40 FEET Multihulls under 40 feet allow you to envisage some nice cruises – even offshore – or to take advantage of the slightest gust to go and challenge the other boats on the water. Catamarans and trimarans which are easy to sail, and reasonable from both a sailing and maintenance point of view. NEW 2017 CORSAIR 760 ASTUS 16.5 Here is the latest boat from Astus Boats. This brand new trimaran was designed by the VPLP design office. This is the NEW first time the builder has wor- 2017 ked with the famous architects, well-known for their racing and cruising multihulls. The Astus 16.5 is built to the With this brand-new trimaran, Corsair is presenting a boat same standards as the other which will have the heavy burden of taking up the torch from trimarans in the range, with the 700 or so 24-foot Corsairs the builder has already produced! notably floats on telescopic The new Corsair 760 can be folded and transported, and tubes to avoid dismantling offers much more comfort than its predecessors, with a small when storing, and a daggerboard for ease of use. cabin offering a perfect little shelter for coastal camping. But The Astus 16.5 is available in a choice of ‘Leisure’ or the trimaran shows its true colors under sail: boosted by a ‘Sport’ versions (built using infusion), and can be equipped screecher on its bowsprit, runs at over 20 knots become the with a small motor for lovers of coastal ‘raids’. -
AR PR Phase 2 Designers 17 Apr 2014 SWE
ARTEMIS RACING STÄRKER SITT DESIGNTEAM MED NYA TILLÄGG ALAMEDA, April 17, 2014 - Artemis Racing meddelade idag att man tecknat Vincent Lauriot- Prévost, Simon Watin, Juan Garay och Matthew Davis, vilka kommer att ingå i designteamet när Artemis Racing förbereder sig för en eventuell 35: e Americas Cup satsning. Både Vincent Lauriot-Prévost och Simon Watin går från VPLP design, världsledande inom flerskrovsracing och super-yacht design, som grundades 1983. Under den 34: e Americas Cup var deltog de i Americas Cup ledningens design och forskargrupp, inrättade för att skapa ett ursprungligt konstruktionspaket för högteknologiska vingseglade AC72 katamaraner. Vincent Lauriot-Prévost är skeppsarkitekt och en av grundarna till VPLP Design baserade i Frankrike. Under sin karriär har Lauriot-Prévost bidragit till flera av de mest avancerade prototypprojekten inom kappsegling, bland annat utformningen av de sex senaste vinnarna i La Route du Rhum, rekordinnehavare i transatlantiska (New York - Lizard) samt världsomfattande (Jules Verne Trophy) seglingar, samt BMW ORACLE Racings trimaran USA 17 som vann den 33: e Americas Cup. "Vi har alltid varit i framkanten i utvecklingen av snabba flerskrovskonstruktioner med VPLP Design. Var först involverade i Americas Cup-utmaningen 2007, då cupen vände sig till flerskrovsbåtar," sade skeppsarkitekten. "Den här gången är det en fantastisk möjlighet att samarbeta med Artemis Racing på ett folierande katamaranprojekt, då tekniken för Americas Cup sätts på sin fullkomliga spets.” Som specialist på att förutspå prestanda, tog Watin en ingengörsexamen med inriktningen fluidmekanik innan han specialiserade sig inom skeppsbyggnad. Under 2011 gick han med i VPLP Yacht Designs kontor i Frankrike, där han utvecklade fluidmekaniska simuleringar , och var inblandad i maxi-racing trimaran projekt (Prince de Bretagne 80, Sodebo 4 och MACIF 100) samt Open 60 projekt (Safran 2 och Banque Populaire) för 2016 års Vendée Globe Race. -
Breton Companies Involved in the Construction of Racing Boats, in Particular IMOCA
BRETAGNE SAILING VALLEY® PLATFORM MEETING Breton companies involved in the construction of racing boats, in particular IMOCA. Contents Bretagne Sailing Valley®: Technological Innovation Laboratory ........................................................ p.3 Companies in Bretagne Sailing Valley ® .............................................................................................. p.5 Design, Structural Calculations ........................................................................................................... p.5 Composite Parts.................................................................................................................................. p.12 On-board Safety / Equipment ............................................................................................................ p.20 Sails and Rigging ................................................................................................................................. p.26 Digital at the Service of Performance ................................................................................................. p.30 Support and Training Organisations for Competitive Sailing in Brittany............................................ p.41 Bretagne Sailing Valley®: Technological Innovation Laboratory for Competitive Sailing It is no accident that the most talented sailors have come from the four corners of the world to the coasts of Brittany to prepare their future victories. The region offers two major assets: an ideal maritime environment and a -
2500 Teus-Trade Wings 2500 – Approval of Principle from BV
PRESS RELEASE Paris, 17th of May 2021, 9h00 - Beijing, 17th of May 2021, 15h00 Innovative 2,500 TEU Container Vessel “Trade Wings 2,500” from VPLP Design, Alwena Shipping, SDARI and AYRO receives Approval in Principle from Bureau Veritas The “Trade Wings 2,500”: an innovative container ship with a capacity of 2,500 TEU (Twenty-Foot Equivalent Unit), designed jointly by VPLP Design (France), Alwena Shipping (France), SDARI (China) and AYRO (France) has received Approval in Principle from Bureau Veritas. With an overall length of 197m and a breadth of 32m, the vessel offers a deadweight of 32 500 m tons. It fosters the combination of a wind-assisted propulsion with six Oceanwings® with an LNG-electric propulsion with pods. The wingsails are installed on a vertical sliding mechanism to retract them partially while the vessel is in port, thus minimizing the impact on cargo operations. The LNG storage tank is based on GTT’ Mark III containment system and the LNG power plant is designed with pure gas 4-strokes gensets only. This architecture is a flexible platform offering possible upgrade to decarbonated fuels in the future such as Ammonia or Hydrogen. Suitable to short sea shipping operations or feedering in Europe, Central America, Caribbean Islands and China, the Trade Wings 2,500 can also operate on transatlantic trades. The design minimizes time in port operations, as maneuverability is increased with the Pods, and the hatch coverless design further speeds up cargo operations. On a typical transatlantic route of 4,000 Nm, the Trade Wings 2,500 will save on average 35% CO2- equivalent emissions compared to a conventional design, with a 2-stroke engine, single shaft and without wingsails, at the same speed. -
Vendée Globe 2020, Le Défi Technologique Se Prépare Au Cœur De La Bretagne Sailing Valley
Vendée Globe 2020, le défi technologique se prépare au cœur de la Bretagne Sailing Valley Sommaire Communiqué de synthèse : Vendée Globe 2020, le défi technologique se prépare au cœur de la Bretagne Sailing Valley® ...................................................................................................................p.3 Bretagne Sailing Valley® : le laboratoire de l’innovation technologique de la voile de compétition ▪ La Bretagne Sailing Valley®, une marque pour un endroit unique au monde : Interview Carole Bourlon .....p.5 ▪ Le poids économique de la voile de compétition en Bretagne .......................................................................p.6 Les bateaux au départ du Vendée Globe : la Bretagne sur le pont .........................................................................p.7 Galerie de portraits : natifs ou d’adoption, ces coureurs qui s’entraînent en Bretagne… et qui gagnent..............p.9 Les entreprises de la Bretagne Sailing Valley® au cœur du 9e Vendée Globe ▪ Conception, calcul de structures .....................................................................................................................p.10 ▪ Pièces composites ...........................................................................................................................................p.18 ▪ Sécurité à bord / équipement .........................................................................................................................p.26 ▪ Voiles et gréements ........................................................................................................................................p.33