Oregon State University 30K Rocketry Team 2019–2020 Technical Report
Total Page:16
File Type:pdf, Size:1020Kb
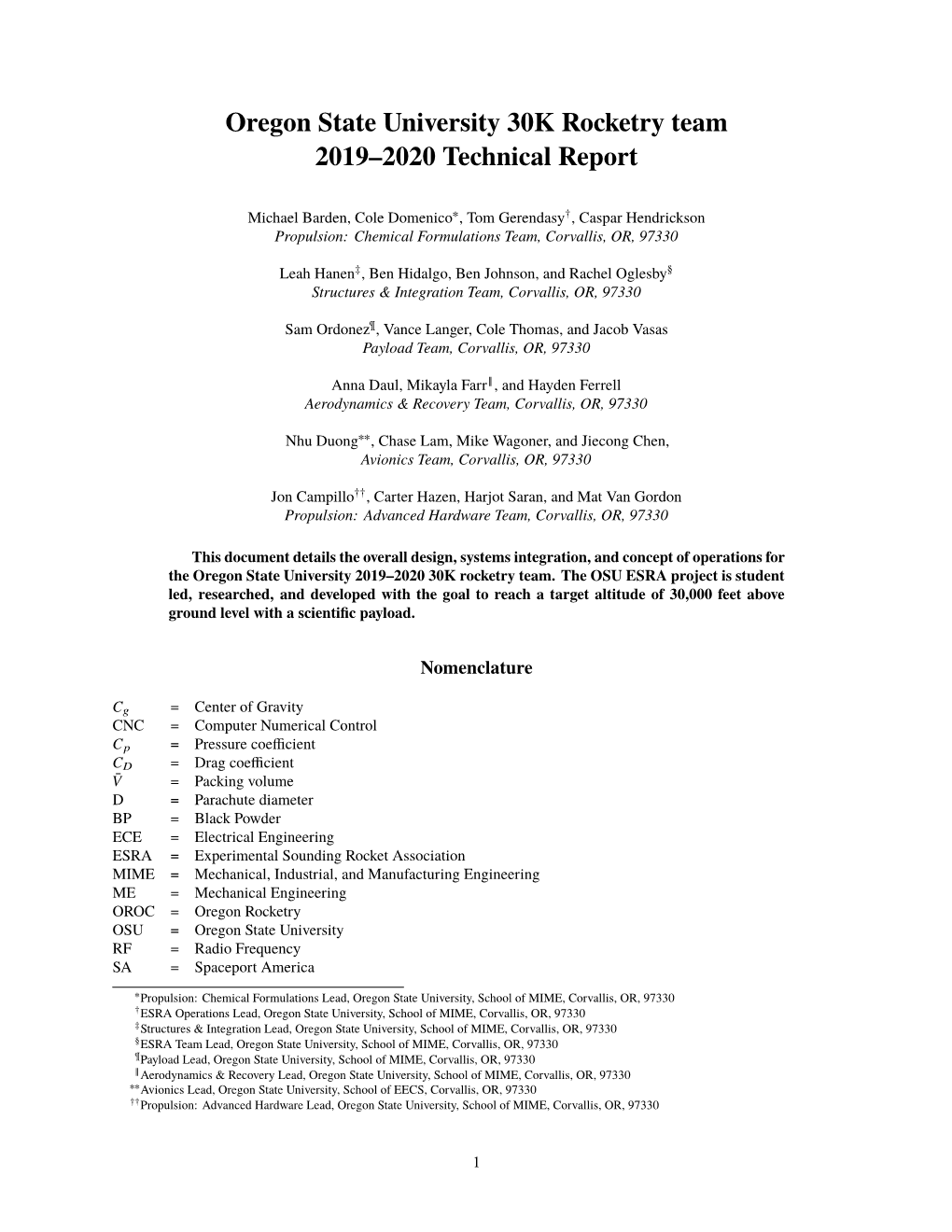
Load more
Recommended publications
-
Space Launch System (Sls) Motors
Propulsion Products Catalog SPACE LAUNCH SYSTEM (SLS) MOTORS For NASA’s Space Launch System (SLS), Northrop Grumman manufactures the five-segment SLS heavy- lift boosters, the booster separation motors (BSM), and the Launch Abort System’s (LAS) launch abort motor and attitude control motor. The SLS five-segment booster is the largest solid rocket motor ever built for flight. The SLS booster shares some design heritage with flight-proven four-segment space shuttle reusable solid rocket motors (RSRM), but generates 20 percent greater average thrust and 24 percent greater total impulse. While space shuttle RSRM production has ended, sustained booster production for SLS helps provide cost savings and access to reliable material sources. Designed to push the spent RSRMs safely away from the space shuttle, Northrop Grumman BSMs were rigorously qualified for human space flight and successfully used on the last fifteen space shuttle missions. These same motors are a critical part of NASA’s SLS. Four BSMs are installed in the forward frustum of each five-segment booster and four are installed in the aft skirt, for a total of 16 BSMs per launch. The launch abort motor is an integral part of NASA’s LAS. The LAS is designed to safely pull the Orion crew module away from the SLS launch vehicle in the event of an emergency on the launch pad or during ascent. Northrop Grumman is on contract to Lockheed Martin to build the abort motor and attitude control motor—Lockheed is the prime contractor for building the Orion Multi-Purpose Crew Vehicle designed for use on NASA’s SLS. -
The SKYLON Spaceplane
The SKYLON Spaceplane Borg K.⇤ and Matula E.⇤ University of Colorado, Boulder, CO, 80309, USA This report outlines the major technical aspects of the SKYLON spaceplane as a final project for the ASEN 5053 class. The SKYLON spaceplane is designed as a single stage to orbit vehicle capable of lifting 15 mT to LEO from a 5.5 km runway and returning to land at the same location. It is powered by a unique engine design that combines an air- breathing and rocket mode into a single engine. This is achieved through the use of a novel lightweight heat exchanger that has been demonstrated on a reduced scale. The program has received funding from the UK government and ESA to build a full scale prototype of the engine as it’s next step. The project is technically feasible but will need to overcome some manufacturing issues and high start-up costs. This report is not intended for publication or commercial use. Nomenclature SSTO Single Stage To Orbit REL Reaction Engines Ltd UK United Kingdom LEO Low Earth Orbit SABRE Synergetic Air-Breathing Rocket Engine SOMA SKYLON Orbital Maneuvering Assembly HOTOL Horizontal Take-O↵and Landing NASP National Aerospace Program GT OW Gross Take-O↵Weight MECO Main Engine Cut-O↵ LACE Liquid Air Cooled Engine RCS Reaction Control System MLI Multi-Layer Insulation mT Tonne I. Introduction The SKYLON spaceplane is a single stage to orbit concept vehicle being developed by Reaction Engines Ltd in the United Kingdom. It is designed to take o↵and land on a runway delivering 15 mT of payload into LEO, in the current D-1 configuration. -
A Pictorial History of Rockets
he mighty space rockets of today are the result A Pictorial Tof more than 2,000 years of invention, experi- mentation, and discovery. First by observation and inspiration and then by methodical research, the History of foundations for modern rocketry were laid. Rockets Building upon the experience of two millennia, new rockets will expand human presence in space back to the Moon and Mars. These new rockets will be versatile. They will support Earth orbital missions, such as the International Space Station, and off- world missions millions of kilometers from home. Already, travel to the stars is possible. Robotic spacecraft are on their way into interstellar space as you read this. Someday, they will be followed by human explorers. Often lost in the shadows of time, early rocket pioneers “pushed the envelope” by creating rocket- propelled devices for land, sea, air, and space. When the scientific principles governing motion were discovered, rockets graduated from toys and novelties to serious devices for commerce, war, travel, and research. This work led to many of the most amazing discoveries of our time. The vignettes that follow provide a small sampling of stories from the history of rockets. They form a rocket time line that includes critical developments and interesting sidelines. In some cases, one story leads to another, and in others, the stories are inter- esting diversions from the path. They portray the inspirations that ultimately led to us taking our first steps into outer space. NASA’s new Space Launch System (SLS), commercial launch systems, and the rockets that follow owe much of their success to the accomplishments presented here. -
+ Part 17: Acronyms and Abbreviations (265 Kb PDF)
17. Acronyms and Abbreviations °C . Degrees.Celsius °F. Degrees.Fahrenheit °R . Degrees.Rankine 24/7. 24.Hours/day,.7.days/week 2–D. Two-Dimensional 3C. Command,.Control,.and.Checkout 3–D. Three-Dimensional 3–DOF . Three-Degrees.of.Freedom 6-DOF. Six-Degrees.of.Freedom A&E. Architectural.and.Engineering ACEIT. Automated.Cost-Estimating.Integrated.Tools ACES . Acceptance.and.Checkout.Evaluation.System ACP. Analytical.Consistency.Plan ACRN. Assured.Crew.Return.Vehicle ACRV. Assured.Crew.Return.Vehicle AD. Analog.to.Digital ADBS. Advanced.Docking.Berthing.System ADRA. Atlantic.Downrange.Recovery.Area AEDC. Arnold.Engineering.Development.Center AEG . Apollo.Entry.Guidance AETB. Alumina.Enhanced.Thermal.Barrier AFB .. .. .. .. .. .. .. Air.Force.Base AFE. Aero-assist.Flight.Experiment AFPG. Apollo.Final.Phase.Guidance AFRSI. Advanced.Flexible.Reusable.Surface.Insulation AFV . Anti-Flood.Valve AIAA . American.Institute.of.Aeronautics.and.Astronautics AL. Aluminum ALARA . As.Low.As.Reasonably.Achievable 17. Acronyms and Abbreviations 731 AL-Li . Aluminum-Lithium ALS. Advanced.Launch.System ALTV. Approach.and.Landing.Test.Vehicle AMS. Alpha.Magnetic.Spectrometer AMSAA. Army.Material.System.Analysis.Activity AOA . Analysis.of.Alternatives AOD. Aircraft.Operations.Division APAS . Androgynous.Peripheral.Attachment.System APS. Auxiliary.Propulsion.System APU . Auxiliary.Power.Unit APU . Auxiliary.Propulsion.Unit AR&D. Automated.Rendezvous.and.Docking. ARC . Ames.Research.Center ARF . Assembly/Remanufacturing.Facility ASE. Airborne.Support.Equipment ASI . Augmented.Space.Igniter ASTWG . Advanced.Spaceport.Technology.Working.Group ASTP. Advanced.Space.Transportation.Program AT. Alternate.Turbopump ATCO. Ambient.Temperature.Catalytic.Oxidation ATCS . Active.Thermal.Control.System ATO . Abort-To-Orbit ATP. Authority.to.Proceed ATS. Access.to.Space ATV . Automated.Transfer.Vehicles ATV . -
Torontech Tab Density Tester1
ARCoptix FT-IR Rocket Mid-IR Fourier-transform spectrometer (2-6 or 2-12 μm) If you are looking for high performance & compact Mid-IR spectrometer, that can operate both free-space or with IR optical fibers, the ARCoptix FT-IR Rocket is the instrument that you need. Thanks to its permanently aligned interferometer and solid-state reference laser, the FT- MIR Rocket offers excellent stability in both intensity and wavelength scales. Two spectral ranges are available, depending on your needs for high sensitivity or broad spectral range. Benefits Two detector choices: 2-6μm or 2-12μm Very good sensitivity (2-stage cooled MCT detector) High resolution of 4cm-1 Excellent stability in intensity and wavelength Removable fiber coupler for operation with fibers or free-space IR beams Applications Mid-IR Optical Spectrum Analyzer (OSA) for MIR Lasers & LEDs Liquid, thin-film or gas measurement Material identification and quantification in various fields such as geology, food and beverage industry, … Characteristics: FT-MIR 2-6 FT-IR 2-12 Models Beam-splitter material CaF2 ZnSe Spectral Range [cm-1] 5000 - 1700 5000 - 830 Spectral Range [μm] 2-6 2-12 Detector Type MCT (2-TE cooled) MCT (2-TE cooled) Detector D* [cm >1x1011 >1.5x109 Hz1/2W-1] SNR > 1:5'000i > 1:2'000ii Recommended fiber CIR (chalcogenide) fibers PIR (polycrystalline) (1-6μm) fibers (3-18μm) Interferometer type Permanently aligned, double retro-reflector design Resolution (unapodized) [cm-1 ] 4 Wavenumber repeatability <10PPM Scan frequency 1 spectrum / second Control laser -
Download Sponsorship Packet
Sponsorship Packet 2020-2021 masa.engin.umich.edu MASA Rockets 2603 Draper Dr. Ann Arbor, MI, 48109 masa.engin.umich.edu [email protected] MASA is launching to 400,000 ft from Spaceport America We’re a student engineering team launching to space in 2021 as we compete for a $1M prize in the Base 11 Space Challenge. We’re building and testing a 3D-printed, regen-cooled liquid rocket engine, welded aluminum propellant tanks, and advanced hardware. It's all part of Tangerine Space Machine - the 1,400 lb. rocket that will take Michigan to space. 2021 2017 2018 MASA’s mission is to design, build, and fly sounding rockets while teaching students about the basics of rocketry. We provide valuable hands-on engineering experience to both students at the University of Michigan and to aspiring engineers, through our outreach projects. Laika, an experimental liquid-fueled rocket, undergoes final checks at Spaceport America Cup 2018 MASA is an interdisciplinary team comprised of students from seven different majors. It is made up of different subteams, including aerodynamics & recovery, propulsion, assembly, test & launch operations (ATLO) , avionics, structures, business, and production. MASA remains one of only five teams in the world to have launched and recovered a liquid-propellant rocket and was the first to do so, at Spaceport America Cup 2018. Blueshift, a solid-fuel rocket, sits on the launchpad at IREC 2017 MASA’s sustained innovation is made possible by our corporate and private sponsors. Join us and become part of a growing legacy of partners that help keep MASA at the forefront of student rocketry, year after year. -
A Conceptual Analysis of Spacecraft Air Launch Methods
A Conceptual Analysis of Spacecraft Air Launch Methods Rebecca A. Mitchell1 Department of Aerospace Engineering Sciences, University of Colorado, Boulder, CO 80303 Air launch spacecraft have numerous advantages over traditional vertical launch configurations. There are five categories of air launch configurations: captive on top, captive on bottom, towed, aerial refueled, and internally carried. Numerous vehicles have been designed within these five groups, although not all are feasible with current technology. An analysis of mass savings shows that air launch systems can significantly reduce required liftoff mass as compared to vertical launch systems. Nomenclature Δv = change in velocity (m/s) µ = gravitational parameter (km3/s2) CG = Center of Gravity CP = Center of Pressure 2 g0 = standard gravity (m/s ) h = altitude (m) Isp = specific impulse (s) ISS = International Space Station LEO = Low Earth Orbit mf = final vehicle mass (kg) mi = initial vehicle mass (kg) mprop = propellant mass (kg) MR = mass ratio NASA = National Aeronautics and Space Administration r = orbital radius (km) 1 M.S. Student in Bioastronautics, [email protected] 1 T/W = thrust-to-weight ratio v = velocity (m/s) vc = carrier aircraft velocity (m/s) I. Introduction T HE cost of launching into space is often measured by the change in velocity required to reach the destination orbit, known as delta-v or Δv. The change in velocity is related to the required propellant mass by the ideal rocket equation: 푚푖 훥푣 = 퐼푠푝 ∗ 0 ∗ ln ( ) (1) 푚푓 where Isp is the specific impulse, g0 is standard gravity, mi initial mass, and mf is final mass. Specific impulse, measured in seconds, is the amount of time that a unit weight of a propellant can produce a unit weight of thrust. -
A Race to the Stars and Beyond: How the Soviet Union's Success in The
Volume 18 Article 5 May 2019 A Race to the Stars and Beyond: How the Soviet Union’s Success in the Space Race Helped Serve as a Projection of Communist Power Jack H. Lashendock Gettysburg College Class of 2020 Follow this and additional works at: https://cupola.gettysburg.edu/ghj Part of the History Commons Share feedback about the accessibility of this item. Lashendock, Jack H. (2019) "A Race to the Stars and Beyond: How the Soviet Union’s Success in the Space Race Helped Serve as a Projection of Communist Power," The Gettysburg Historical Journal: Vol. 18 , Article 5. Available at: https://cupola.gettysburg.edu/ghj/vol18/iss1/5 This open access article is brought to you by The uC pola: Scholarship at Gettysburg College. It has been accepted for inclusion by an authorized administrator of The uC pola. For more information, please contact [email protected]. A Race to the Stars and Beyond: How the Soviet Union’s Success in the Space Race Helped Serve as a Projection of Communist Power Abstract In the modern era, the notion of space travel is generally one of greater acceptance and ease than in times previously. Moreover, a greater number of nations (and now even private entities) have the technological capabilities to launch manned and unmanned missions into Earth’s Orbit and beyond. 70 years ago, this ability did not exist and humanity was simply an imprisoned species on this planet. The ourc se of humanity’s then- present and the collective future was forever altered when, in 1957, the Soviet Union successfully launched the world’s first satellite into space, setting off a decades-long completion with the United States to cosmically outperform the other. -
National Spaceport Network Development Plan
SPfciCEPORT ALLIANCE National Spaceport Network Development Plan Prepared by the Global Spaceport Alliance for the Office of Spaceports Office of Commercial Space Transportation Federal Aviation Administration June 1, 2020 EXECUTIVE SUMMARY Space has become an indispensable part of everyday life in the 21st century, supporting not only our nation's military and intelligence capabilities, but also communications, navigation, weather forecasting, agriculture, financial transactions, disaster response, and even entertainment. The Eastern Range, located at Cape Canaveral Air Force Station, Florida, and the Western Range, located at Vandenberg Air Force Base, California, have served as the military's primary launch sites for space launches and missile tests for more than 60 years. Many NASA and commercial space missions have also been conducted from those locations. Recently however, a number of commercial spaceports have been established by state and local governments, or by private companies, based on a desire to take advantage of the growing space economy, to minimize the federal regulatory burden, and to provide additional launch opportunities for civil and commercial space missions. The development of a National Spaceport Network, consisting of current and prospective commercial spaceports, government-owned-and-operated launch & landing sites, and privately- owned-and-operated launch & landing sites, offers an opportunity to increase the safety, capacity, efficiency, and resiliency of the nation's space operations. Such a network could provide the framework for formal or informal public-private partnerships between federal, state, and local governments; the aerospace industry; and academia. A key component of the operation of a successful network of spaceports is federal funding for infrastructure development. -
Space Race Knowledge Organiser.Docx
Burlington Junior School - History Year 5 What was the Space Race? Why was it important? Background Information The Space Race was a competition of space exploration between the Soviet Union (now Russia) and the United States, which lasted from 1955 to 1969. The Space Race began after the Soviet launch of Sputnik 1 on 4 October 1957. The term "Space Race" started as a comparison to the arms race. The Space Race became an important part of the rivalry between the United States and the Soviet Union during the Cold War. Space technology became an extra important area in this rivalry, because of possible military uses. In this unit the children will: - Learn about Space and the Solar System - Explore the movement of the Sun, Earth and other planets. - Find out about the early years of space exploration from 1940 to 1970. - Learn about different astronauts. - Think about extra-terrestrial life. Historical Skills and Concepts: - Chronology – key events in world history. - Questioning – develop their historical questioning skills. - Sources – use a range of sources to explore our knowledge of the past. Key People: Timeline of Key Events: John F Kennedy - American President who made 4 October 1957 - The world's first artificial promise to reach the moon by 1970. satellite. Alan Shepherd - First American in Space. 28 May 1959 - First creatures to return Yuri Gargarin – First person to orbit Earth. alive from space. Neil Armstrong – One of 3 American’s on Apollo 12 April 1961 - The first man in space. 11. 16 June 1963 - The first woman in space. Buzz Aldrin - One of 3 American’s on Apollo 11. -
How Does Spaceflight Affect the Human Body?
The Science Journal of the Lander College of Arts and Sciences Volume 8 Number 1 Fall 2014 - 1-1-2014 How Does Spaceflight Affect the Human Body? Sara Dina Feinzeig Touro College Follow this and additional works at: https://touroscholar.touro.edu/sjlcas Part of the Biology Commons Recommended Citation Feinzeig, S. D. (2014). How Does Spaceflight Affect the Human Body?. The Science Journal of the Lander College of Arts and Sciences, 8(1). Retrieved from https://touroscholar.touro.edu/sjlcas/vol8/iss1/5 This Article is brought to you for free and open access by the Lander College of Arts and Sciences at Touro Scholar. It has been accepted for inclusion in The Science Journal of the Lander College of Arts and Sciences by an authorized editor of Touro Scholar. For more information, please contact [email protected]. How Does Spaceflight Affect the Human Body? By: Sara Dina Feinzeig Sara graduated in June 2014 with a B.S. in biology. Sara has been accepted into the Touro Winthrop Physician Assistant Program. Abstract Spaceflight can impact just about every organ of the human body. The launch into space increases gravitational forces, which may decrease consciousness. Once subjected to the microgravity of outer space, the constant mechanical stress exerted on the body from Earth’s gravity decreases enormously, causing bone degeneration to occur. Calcium, a major component of bone is excreted in very high amounts, often leading to the formation of calcium kidney stones. Astronauts perform weight bearing exercise, take osteoporosis drugs and calcium and vitamin D supplements in order to combat bone loss. -
A Two-Stage-To-Orbit Spaceplane Concept with Growth Potential
NASA/TM-2001-209620 A Two-Stage-to-Orbit Spaceplane Concept with Growth Potential Unmeel B. Mehta and Jeffrey V. Bowles February2001 The NASA STI Program Office... in Profile Since its founding, NASA has been dedicated to the CONFERENCE PUBLICATION. Collected advancement of aeronautics and space science. The papers from scientific and technical confer- NASA Scientific and Technical Information (STI) ences, symposia, seminars, or other meetings Program Office plays a key part in helping NASA sponsored or cosponsored by NASA. maintain this important role. • SPECIAL PUBLICATION. Scientific, technical, The NASA STI Program Office is operated by or historical information from NASA programs, Langley Research Center, the Lead Center for projects, and missions, often concerned with NASA's scientific and technical information. The subjects having substantial public interest. NASA STI Program Office provides access to the NASA STI Database, the largest collection of • TECHNICAL TRANSLATION. English- aeronautical and space science STI in the world. language translations of foreign scientific and The Program Office is also NASA's institutional technical material pertinent to NASA's mission. mechanism for disseminating the results of its research and development activities. These results Specialized services that complement the STI are published by NASA in the NASA STI Report Program Office's diverse offerings include creating Series, which includes the following report types: custom thesauri, building customized databases, organizing and publishing research results.., even TECHNICAL PUBLICATION. Reports of providing videos. completed research or a major significant phase of research that present the results of NASA For more information about the NASA STI programs and include extensive data or theoreti- Program Office, see the following: cal analysis.