Washington County Conditional Use Permit Reissuance Application
Total Page:16
File Type:pdf, Size:1020Kb
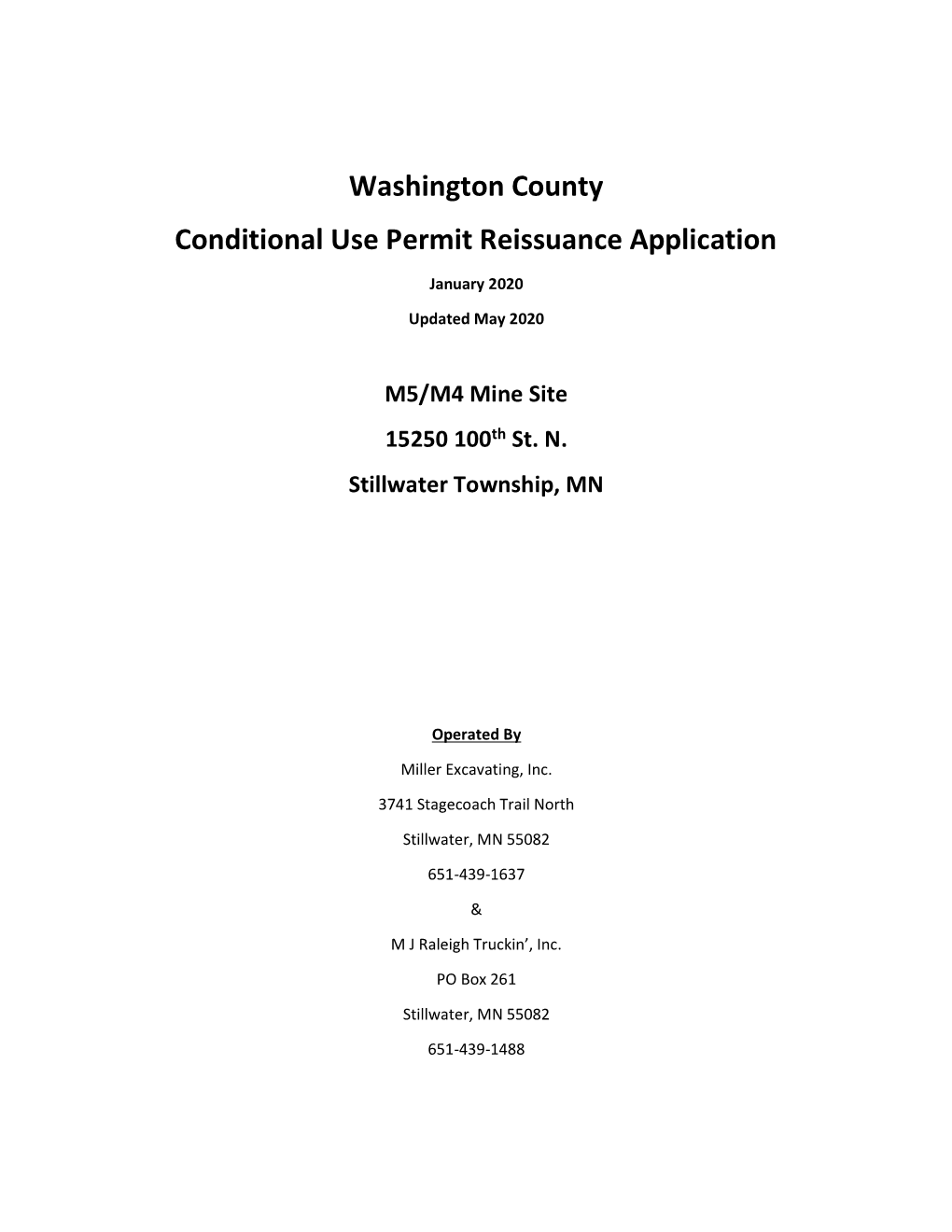
Load more
Recommended publications
-
Gravel Pit Solar
July 31, 2020 Gravel Pit Solar and Public Need Compatibility of Environmental Certificate for Application Pit Solar Gravel Application for Certificate of Environmental Compatibility and Public Need SUBMITTED TO Connecticut Siting Council APPLICANT Gravel Pit Solar, LLC Gravel Pit Solar II, LLC Gravel Pit Solar III, LLC Gravel PIt Solar IV, LLC PREPARED IN ASSOCIATION WITH Pullman & Comley, LLC Vanasse Hangen Brustlin, Inc. 22,May 2020 Heritage Consultants, LLC Environmental Design & Research D.P.C Exponent Engineering and Scientific Consulting APPLICATION FOR CERTIFICATE OF ENVIRONMENTAL COMPATIBILITY AND PUBLIC NEED Gravel Pit Solar 120 MW Solar Photovoltaic Energy Generation Project in East Windsor, Connecticut PREPARED FOR Gravel Pit Solar, LLC Gravel Pit Solar II, LLC Gravel Pit Solar III, LLC Gravel Pit Solar IV, LLC 1166 Avenue of the Americas, 9th Floor New York, NY 10036 PREPARED BY 100 Great Meadow Road Suite 200 Wethersfield, CT 06109 JULY 31, 2020 i APPLICATION OF GRAVEL PIT SOLAR APPLICATION FOR A CERTIFICATE OF ENVIRONMENTAL COMPATIBILITY AND PUBLIC NEED FOR THE CONSTRUCTION, OPERATION AND MAINTENANCE OF A 120 MW-AC SOLAR PHOTOVOLTAIC PROJECT NEAR APOTHECARIES HALL ROAD, PLANTATION ROAD, WAPPING ROAD, AND WINDSORVILLE ROAD IN EAST WINDSOR, CONNECTICUT JULY 31, 2020 Application for a Certificate of Environmental Compatibility and Public Need Table of Contents 1 Introduction ................................................................................................................. 1 2 Applicant ..................................................................................................................... -
Oil Shale Provisions of Epact Hearing
S. HRG. 109–602 OIL SHALE PROVISIONS OF EPACT HEARING BEFORE THE COMMITTEE ON ENERGY AND NATURAL RESOURCES UNITED STATES SENATE ONE HUNDRED NINTH CONGRESS SECOND SESSION ON THE IMPLEMENTATION OF THE OIL SHALE PROVISIONS OF THE ENERGY POLICY ACT OF 2005 GRAND JUNCTION, CO, JUNE 1, 2006 ( Printed for the use of the Committee on Energy and Natural Resources U.S. GOVERNMENT PRINTING OFFICE 30–202 PDF WASHINGTON : 2006 For sale by the Superintendent of Documents, U.S. Government Printing Office Internet: bookstore.gpo.gov Phone: toll free (866) 512–1800; DC area (202) 512–1800 Fax: (202) 512–2250 Mail: Stop SSOP, Washington, DC 20402–0001 VerDate 0ct 09 2002 10:51 Oct 20, 2006 Jkt 109602 PO 30202 Frm 00001 Fmt 5011 Sfmt 5011 P:\DOCS\30202.TXT SENERGY2 PsN: PAULM COMMITTEE ON ENERGY AND NATURAL RESOURCES PETE V. DOMENICI, New Mexico, Chairman LARRY E. CRAIG, Idaho JEFF BINGAMAN, New Mexico CRAIG THOMAS, Wyoming DANIEL K. AKAKA, Hawaii LAMAR ALEXANDER, Tennessee BYRON L. DORGAN, North Dakota LISA MURKOWSKI, Alaska RON WYDEN, Oregon RICHARD M. BURR, North Carolina, TIM JOHNSON, South Dakota MEL MARTINEZ, Florida MARY L. LANDRIEU, Louisiana JAMES M. TALENT, Missouri DIANNE FEINSTEIN, California CONRAD BURNS, Montana MARIA CANTWELL, Washington GEORGE ALLEN, Virginia KEN SALAZAR, Colorado GORDON SMITH, Oregon ROBERT MENENDEZ, New Jersey JIM BUNNING, Kentucky BRUCE M. EVANS, Staff Director JUDITH K. PENSABENE, Chief Counsel BOB SIMON, Democratic Staff Director SAM FOWLER, Democratic Chief Counsel DICK BOUTS, Professional Staff Member PATTY BENEKE, Democratic Senior Counsel (II) VerDate 0ct 09 2002 10:51 Oct 20, 2006 Jkt 109602 PO 30202 Frm 00002 Fmt 5904 Sfmt 5904 P:\DOCS\30202.TXT SENERGY2 PsN: PAULM C O N T E N T S STATEMENTS Page Baardson, John, CEO, Baard Energy, LLC, Vancouver, WA .............................. -
Mapping Sand and Gravel Mining Within the Presumpscot River Watershed, Maine, Using Remote Sensing and Other Digital Data in a G.I.S
MAPPING SAND AND GRAVEL MINING WITHIN THE PRESUMPSCOT RIVER WATERSHED, MAINE, USING REMOTE SENSING AND OTHER DIGITAL DATA IN A G.I.S. ENVIRONMENT Chris Jones, Justin Rich, Irwin D. Novak Department of Geosciences University of Southern Maine Gorham, Maine August, 2006 ABSTRACT The growth of gravel mining sites from 1998 to 2001 within the Presumpscot River watershed of southern Maine has been documented using ArcGIS software, Ortho- rectified Digital Images (ODIs) and digital surface water, road, watershed, town boundary and tax map data. Maine Department of Environmental Protection licensed site locations of 5 acres or more were added as a geo-referenced layer to aid in tracing and interpreting gravel pit boundaries. The growth of the pits was calculated by hand digitizing the outlines of areas in which the surface soils have been disturbed in order to expose extractable materials as shown on 1998 ODIs. These areas were compared with the pit outlines shown on the 2001 ODIs and satellite images (2004). The total area of all licensed and non-licensed pits within the watershed was 461.49 acres in 1998 and grew to 653.24 acres in 2004, a 47% increase. There was an increase of 49 acres, from 117.49 acres to 161.29 acres for the 34 licensed sites from 1998 to 2004 a 37% increase. The average growth was 3.8 acres per pit. More detailed analysis in the Town of Gorham, Maine, reveals that 18% of the watershed falls within Gorham and that there are 21 licensed mines. This is the second largest area of coverage after Windham, Maine, which has 22% of the watershed within its boundaries, but only 13 pits. -
Gravel Roads Construction and Maintenance Guide Table of Contents Subject Page
Errata Replaces page 137 Reconstruction Using a Detour When the reconstruction and resulting berm are significant, the work space takes all or most of the road surface, leaving no room for traffic to negotiate past the work activities. An agency may need to reconstruct the unpaved roadway by correcting the drainage and/or adding surface materials. With this type of work, additional equipment may be used and a large amount of material may create a large berm (12 inches or more across). This will present significant hazards for the traveling public. To improve safety for mo torists and workers, a detour may be the best TTC. Not all road users will be familiar with the local road system and some may be confused by the road closure, so signing should be used to assist users negotiating the detour. Reconstruction work space. (Source: Greg Vavra, SDLTAP). Notes: 1. Not all local agencies use route makers for their system. MUTCD Section 6F.59 states “A Street Name sign should be placed above, or the street name should be incorporated into, a DETOUR (M49) sign to indicate the name of the street being detoured.” 2. With an increase in traffic at the intersections where the detour begins and ends, a review of the usage of the STOP and YIELD signs should be completed. 3. Flashing warning lights and/or flags may be used to call attention to advance warning signs. 4. Flashing warning lights may be used on the Type 3 Barricades, which should be installed at the point where the road is closed. -
Gravel Mining Bibliography
SEDIMENT REMOVAL BIBLIOGRAPHY Compiled by Janine Castro, US Fish and Wildlife Service, Portland, Oregon, March 1, 2006 Alexander, G.R. and E.A. Hansen. 1983. Sand sediment in a Michigan trout stream, Part II. Effects of reducing bedload on a trout population. North American Journal of Fisheries Management 3:365-372. American Fisheries Society. 2002. Position paper on instream sand and gravel mining activities in North Carolina, February 6, 2002. North Carolina Chapter of the American Fisheries Society. American River Management Society. 1996. ARMS News. Summer 1996, Vol 9, No. 2. Annandale and Gilpin. 1992. Engineering risk analysis of sand and gravel operations. In: Van Zyl, Dirk, Koval, Marshall, and Li (Eds.), Risk Assessment/Management Issues in the Environmental Planning of Mines. Andrews, J. and D. Kinsman. 1990. Gravel pit restoration for wildlife: a practical manual. Sandy, Bedfordshire, Royal Society for Protection of Birds. Anonymous. 1985. Attacks on the Otaki – gravel or grants? Soil and Water Magazine, National Water and Soil Conservation Authority, Wellington, New Zealand, 21(2):2-6. Anonymous. 1986. Rocks from the rivers – a report on gravel extraction in NZ’s lower North Island. Soil and Water Magazine, National Water and Soil Conservation Authority, Wellington, New Zealand, 22(4):2-14. Anonymous. 2000. A review of options for improving the regulation of aggregate, a diminishing pulic resource. Internal Government of British Columbia Document. 7 pp. & appendices. Arnold, L.R., W.H. Langer, and S.S. Paschke. 2003. Analytic and numerical simulation of the steady-state hydrologic effects of mining aggregate in hypothetical sand-and-gravel and fractured crystalline-rock aquifers. -
Docket No. 492 (Gravel Pit Solar/East Windsor)
DOCKET NO. 492 - Gravel Pit Solar application for a Certificate of } Connecticut Environmental Compatibility and Public Need for the construction, maintenance, and operation of a 120-megawatt-AC solar photovoltaic } Siting electric generating facility on eight parcels generally located to the east and west of the Amtrak and Connecticut Rail Line, south of } Council Apothecaries Hall Road and north of the South Windsor town boundary in East Windsor, Connecticut and associated electrical February 19, 2021 interconnection. DRAFT Findings of Fact Introduction 1. Gravel Pit Solar, LLC, Gravel Pit Solar II, LLC, Gravel Pit Solar III, LLC, and Gravel Pit Solar IV, LLC (collectively, GPS or Applicant), in accordance with the provisions of Connecticut General Statutes (C.G.S.) §16-50g et seq., applied to the Connecticut Siting Council (Council) on July 31, 2020 for a Certificate of Environmental Compatibility and Public Need (Certificate) for the construction, maintenance, and operation of a 120-megawatt-AC solar photovoltaic electric generating facility on eight parcels generally located to the east and west of the Amtrak and Connecticut Rail Line, south of Apothecaries Hall Road and north of the South Windsor town boundary in East Windsor, Connecticut. (Applicant 1, p. 1) 2. Gravel Pit Solar, LLC, Gravel Pit Solar II, LLC, Gravel Pit Solar III, LLC, and Gravel Pit Solar IV, LLC are affiliates of D.E. Shaw Renewable Investments, LLC (DESRI) and are Delaware limited liability companies headquartered at 1166 Avenue of the Americas, 9th Floor, New York, New York. (Applicant 1, p. 3) 3. DESRI, through its affiliates, is a developer, owner, and operator of renewable energy projects in North America, including two commercial solar projects in Connecticut: 26.4 MW Tobacco Valley Solar in Simsbury and 20 MW Fusion Solar in Sprague. -
A Review of the Effect of Floodplain Gravel Mining on River Stability
7th Australian Stream Management Conference - Full Paper A review of the effect of floodplain gravel mining on river stability 1 2 Anthony R. Ladson , Dean A. Judd 1. Moroka Pty Ltd, P.O. Box 1245 Fitzroy North, Vic 3068. Email: [email protected] 2. Goulburn Broken Catchment Management Authority, P.O. Box 1752, Shepparton Vic 3630. Email: [email protected] Key Points • A large amount of aggregate is used in advanced economies such as Australia; 6 to 12 tonnes per person per year. Some of this aggregate is supplied from floodplain mining • Floodplain gravel mining is seen to be safer than direct extraction of gravel from rivers but there remain substantial threats to river stability • A literature review found 37 examples where rivers had broken into gravel mines and the resulting river response had led to bed and bank erosion and threats to infrastructure. • Appropriate locations for, and active management of, floodplain gravel mines is required to reduce threats to acceptable levels and ensure the sustainability of mines Abstract Floodplain gravel mining can cause change in the riverine environment, both locally and distant to the mining site, and in the short and long term. Immediate effects of mining include loss of land and vegetation and other impacts such as noise, dust and vibration. Gravel mining may affect flood hydraulics. During floods, gravel pits provide an area of increased conveyance to flow and often a shortened flow path for floodwaters. This can result in high velocities and scour. Erosional processes associated with floodplain pits can result in river channel changes where the river diverts into, and through, gravel mines. -
Ace Concrete Gravel Pit
NORTHWESTNORTHWEST MONDAY, January 18, 2021 MARTIN LUTHER KING JR. DAY 2021 More than 4,500 still without power Avista: All service should be restored sometime Monday By Emma Epperly THE SPOKESMAN-REVIEW Crews worked around the clock for the fifth day straight Sunday to restore electricity to the Inland Northwest after a windstorm last Wednesday left tens of thousands without power and toppled hundreds of trees. As of 5 p.m., a little more than 4,500 Avista Corp. cus- tomers were still without power, according to the util- DAN PELLE/THE SPOKESMAN-REVIEW ity’s website. That was down Kiantha Duncan, recently elected president of the Spokane chapter of the NAACP, stands in her hallway with paintings by Sam The Artist. from 7,300 customers late Sunday morning, and down from the storm’s peak outage of 70,000 customers without power. NEW NAACP PRESIDENT’S Shortly after the storm, more than 100,000 house- holds in the Inland North- west were without power. An estimated 133 trees fell in city parks, with more potentially MLK DAY IS FULL OF HOPE hazardous leaning trees. Initial assessments from Avista the day after the storm suggested power might not be Kiantha Duncan draws inspiration from King’s dedication to all of humankind returned to some South Hill neighborhoods until Sunday By Maggie Quinlan that he focus on issues at home, Time maga- “If America’s soul becomes totally poi- evening. In a statement Sun- THE SPOKESMAN-REVIEW zine reported. soned,” King said, “part of the autopsy must day, the utility said some cus- In his 1967 speech “Beyond Vietnam,” he read Vietnam.” tomers would need to wait Kiantha Duncan, president of the Spokane pointed out a “cruel irony,” that soldiers were Duncan, inspired by King’s dedication to until Monday for service to be chapter of the NAACP, said she believes in fighting for justice in Southeast Asia that all of humankind, international and domestic, restored. -
H. M-1 Industrial/Manufacturing*
8-3-6: ZONING DISTRICT DESCRIPTIONS: H. M-1 INDUSTRIAL/MANUFACTURING*: H-1. Purpose: The purpose of this district is to provide distinct zones encouraging the establishment and grouping together of industrial and manufacturing uses, that are capable of being operated under such standards as to location and appearance of buildings and structures, and treatment of the land, which are not obtrusive and detrimental to the adjacent zoning districts and land uses. H-2. Uses: Use of this district is allowed only within the city areas of impact. BASE ZONING REGULATIONS 8-4-1: ZONING RESTRICTIONS AND LAND USE TABLE: Land use, height, setback, lot size, off-street parking and sign schedules are described in this chapter and Chapter 5 of this title. Permitted land uses are outlined in the following Land Use Matrix (Table 1), land use schedule for the zoning districts. No other uses shall be permitted without being added to the schedule. P = Permitted Use C = Conditional Use PC=Permitted with Conditions = Not Permitted (May be allowed) (Blank) Zoning Classification Title 8, Section 8-4-1 Permitted by Right P Table 1 Land Use Matrix Permitted with Conditions PC Conditional Use CU Retail/Services/Office M-1 Agriculture M-1 Animal Grooming / Training CU Agriculture, Commercial P Appliance/Electronic Repair Service/Shop P Beekeeping CU Composting Facility CU Blacksmith CU Construction Materials Sales and Services PC Plant Nursery / Greenhouse CU Heavy Equipment Sales Lot PC Riding Academy PC Kennel/ Boarding /Pet Daycare CU Riding / Training Stable PC LP Gas or Fuel Oil Sales CU Plumbing/ Heating Equipment Shop P Recreation Facility CU Recreation, Motorized CU Sexually Oriented Business CU Storage Units PC Vehicle Repair Shop PC Vehicle Sales Lot PC Vehicle Wash PC Veterinary Clinic CU Waste Material Resale Store PC Title 8, Rev. -
Hydraulic Impacts of Quarries and Gravel Pits
Hydraulic Impacts of Quarries and Gravel Pits Prepared by J.A. Green, J.A. Pavlish, R.G. Merritt, and J.L. Leete Minnesota Department of Natural Resources, Division of Waters for the Legislative Commission on Minnesota Resources funded by the Minnesota Environment and Natural Resources Trust Fund 2005 Hydraulic Impacts of Quarries and Gravel Pits Executive Summary 1 2 EXECUTIVE SUMMARY Natural aggregate (crushed stone, sand, and gravel) is a vital part of our economic infrastructure in Minnesota. Aggregate is used for road and bridge construction and in a variety of building materials. In 2003, the value of construction sand and gravel and crushed stone in Minnesota was approximately $245,000,000. As Minnesota’s economy continues to expand, the demand for aggregate will continue to grow. Sand and gravel pits are located in every county in Minnesota. In 1990, the Minnesota Department of Natural Resources, Division of Minerals (DNR Minerals), estimated the number of active and inactive operations at 1500 with the view that this number was likely too low (Dennis Martin, pers. comm.). Quarries for mining limestone, dolomite, sandstone, and hard rock (granite and quartzite) are found in 34 counties. A 1990 DNR Minerals inventory found 165 active operations, 88% of which were limestone quarries (Nelson and others, 1990). That same inventory counted 1,367 inactive operations, 70% of which were limestone quarries. Aggregate mining is an extractive use of resources: mining alters the landscape and its natural hydrologic system. When a new pit or quarry is proposed or when an existing operation needs to expand, local governments and citizens typically have many questions about the impacts mining might have. -
Active Mines and Mineral Plants in Michigan
Active Mines and Mineral Plants in Michigan Data downloaded from Active mines and mineral plants in the US (http://mrdata.usgs.gov/mineral-resources/active-mines.html) PLANT or COMMODITY SITE NAME COMPANY NAME COUNTY LATITUDE LONGITUDE MINE Sand and Gravel R. Smith & Sons, Inc. R. Smith & Sons, Inc. Allegan 42.44223 -85.77682 M/P Aggregate Industries, Sand and Gravel Smith-Belden #8 Allegan 42.45280 -85.67110 M/P Inc. Aggregate Industries, Sand and Gravel P. E. P. Plant Allegan 42.45280 -85.67110 M/P Inc. Aggregate Industries, Sand and Gravel Allis Chalmers Plant #1 Allegan 42.45739 -85.67140 M/P Inc. Aggregate Industries, Sand and Gravel Allis Chalmers Plant #2 Allegan 42.45739 -85.67140 M/P Inc. Aggregate Industries, Sand and Gravel Allis Chalmers Plant #3 Allegan 42.45739 -85.67140 M/P Inc. Aggregate Industries, Sand and Gravel Nb #1 Allegan 42.45739 -85.67140 M/P Inc. Sand and Gravel Chicora Pit Southwest Gravel, Inc. Allegan 42.48433 -85.98750 M/P Sand and Gravel Reed Pit R. Smith & Sons, Inc. Allegan 42.61460 -86.10270 M/P Sand and Gravel Telsmith Gravel Plant South Kent Gravel, Inc. Allegan 42.69680 -85.54520 M/P Sand and Gravel Patterson Pit & Wash Plant South Kent Gravel, Inc. Allegan 42.69708 -85.54596 M/P Aggregate Industries, Sand and Gravel Wayland Plant Allegan 42.70310 -85.55520 M/P Inc. Bob-O-Link Associates, Sand and Gravel Sand & Gravel Operations Allegan 42.75858 -85.56651 M/P Llc. PLANT or COMMODITY SITE NAME COMPANY NAME COUNTY LATITUDE LONGITUDE MINE Cement Alpena Plant Lafarge Corp Alpena 45.06500 -83.44200 P Lafarge North America, Crushed Stone Alpena Plant Great Lakes Alpena 45.08470 -83.39860 M/P Inc. -
Gravel Pit Study
2011 Municipal District of Peace No. 135 Mackenzie Municipal Services Agency GRAVEL PIT STUDY MARCH 8, 2011 Table of Contents INTRODUCTION ........................................................................................................................... 3 OBJECTIVES ................................................................................................................................. 5 DEFINITIONS ................................................................................................................................ 6 GRAVEL PIT OPERATIONS ....................................................................................................... 8 Existing Gravel Pit Operations ................................................................................................ 9 Impact of Gravel Pit Operations ............................................................................................ 13 Guidelines and Standards for Controlling Future Gravel Pit Operations ........................ 17 Location of Potential Future Gravel Pit Operations ........................................................... 23 LAND USE REGULATIONS ...................................................................................................... 26 CONCLUSION/RECOMMENDATIONS .................................................................................. 27 REFERENCES ............................................................................................................................ 29 APPENDIX A – DRAFT GRIMSHAW GRAVELS