Electrochemical Double Layered Capacitor Development and Implementation System
Total Page:16
File Type:pdf, Size:1020Kb
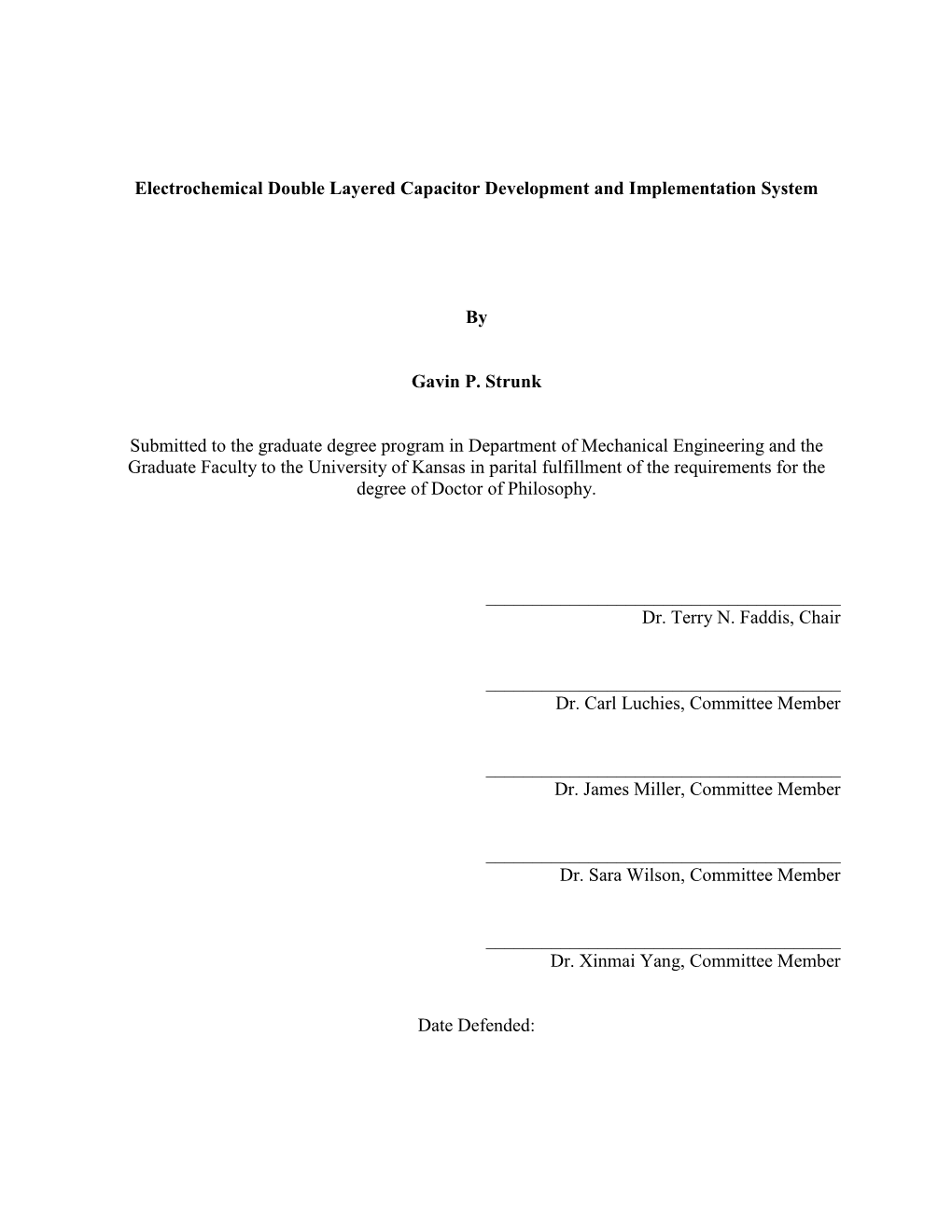
Load more
Recommended publications
-
Short Range Object Detection and Avoidance
Short Range Object Detection and Avoidance N.F. Jansen CST 2010.068 Traineeship report Coach(es): dr. E. García Canseco, TU/e dr. ing. S. Lichiardopol, TU/e ing. R. Niesten, Wingz BV Supervisor: prof.dr.ir. M. Steinbuch Eindhoven University of Technology Department of Mechanical Engineering Control Systems Technology Eindhoven, November, 2010 Abstract The scope of this internship is to investigate, model, simulate and experiment with a sensor for close range object detection for the purpose of the Tele-Service Robot (TSR) robot. The TSR robot will be implemented in care institutions for the care of elderly and/or disabled. The sensor system should have a supporting role in navigation and mapping of the environment of the robot. Several sensors are investigated, whereas the sonar system is the optimal solution for this application. It’s cost, wide field-of-view, sufficient minimal and maximal distance and networking capabilities of the Devantech SRF-08 sonar sensor is decisive to ultimately choose this sensor system. The positioning, orientation and tilting of the sonar devices is calculated and simulations are made to obtain knowledge about the behavior and characteristics of the sensors working in a ring. Issues surrounding the sensors are mainly erroneous ranging results due to specular reflection, cross-talk and incorrect mounting. Cross- talk can be suppressed by operating in groups, but induces the decrease of refresh rate of the entire robot’s surroundings. Experiments are carried out to investigate the accuracy and sensitivity to ranging errors and cross-talk. Eventually, due to the existing cross-talk, experiments should be carried out to decrease the range and timing to increase the refresh rate because the sensors cannot be fired more than only two at a time. -
Architecture of 8051 & Their Pin Details
SESHASAYEE INSTITUTE OF TECHNOLOGY ARIYAMANGALAM , TRICHY – 620 010 ARCHITECTURE OF 8051 & THEIR PIN DETAILS UNIT I WELCOME ARCHITECTURE OF 8051 & THEIR PIN DETAILS U1.1 : Introduction to microprocessor & microcontroller : Architecture of 8085 -Functions of each block. Comparison of Microprocessor & Microcontroller - Features of microcontroller -Advantages of microcontroller -Applications Of microcontroller -Manufactures of microcontroller. U1.2 : Architecture of 8051 : Block diagram of Microcontroller – Functions of each block. Pin details of 8051 -Oscillator and Clock -Clock Cycle -State - Machine Cycle -Instruction cycle –Reset - Power on Reset - Special function registers :Program Counter -PSW register -Stack - I/O Ports . U1.3 : Memory Organisation & I/O port configuration: ROM RAM - Memory Organization of 8051,Interfacing external memory to 8051 Microcontroller vs. Microprocessors 1. CPU for Computers 1. A smaller computer 2. No RAM, ROM, I/O on CPU chip 2. On-chip RAM, ROM, I/O itself ports... 3. Example:Intel’s x86, Motorola’s 3. Example:Motorola’s 6811, 680x0 Intel’s 8051, Zilog’s Z8 and PIC Microcontroller vs. Microprocessors Microprocessor Microcontroller 1. CPU is stand-alone, RAM, ROM, I/O, timer are separate 1. CPU, RAM, ROM, I/O and timer are all on a single 2. designer can decide on the chip amount of ROM, RAM and I/O ports. 2. fix amount of on-chip ROM, RAM, I/O ports 3. expansive 3. for applications in which 4. versatility cost, power and space are 5. general-purpose critical 4. single-purpose uP vs. uC – cont. Applications – uCs are suitable to control of I/O devices in designs requiring a minimum component – uPs are suitable to processing information in computer systems. -
SERVO MAGAZINE TEAM DARE’S ROBOT BAND • RADIO for ROBOTS • BUILDING MAXWELL June 2012 Full Page Full Page.Qxd 5/7/2012 6:41 PM Page 2
0 0 06 . 7 4 $ A D A N A C 0 5 . 5 $ 71486 02422 . $5.50US $7.00CAN S . 0 U CoverNews_Layout 1 5/9/2012 3:21 PM Page 1 Vol. 10 No. 6 SERVO MAGAZINE TEAM DARE’S ROBOT BAND • RADIO FOR ROBOTS • BUILDING MAXWELL June 2012 Full Page_Full Page.qxd 5/7/2012 6:41 PM Page 2 HS-430BH HS-5585MH HS-5685MH HS-7245MH DELUXE BALL BEARING HV CORELESS METAL GEAR HIGH TORQUE HIGH TORQUE CORELESS MINI 6.0 Volts 7.4 Volts 6.0 Volts 7.4 Volts 6.0 Volts 7.4 Volts 6.0 Volts 7.4 Volts Torque: 57 oz-in 69 oz-in Torque: 194 oz-in 236 oz-in Torque: 157 oz-in 179 oz-in Torque: 72 oz-in 89 oz-in Speed: 0.16 sec/60° 0.14 sec/60° Speed: 0.17 sec/60° 0.14 sec/60° Speed: 0.20 sec/60° 0.17 sec/60° Speed: 0.13 sec/60° 0.11 sec/60° HS-7950THHS-7950TH HS-7955TG HS-M7990TH HS-5646WP ULTRA TORQUE CORELESS HIGH TORQUE CORELESS MEGA TORQUE HV MAGNETIC ENCODER WATERPROOF HIGH TORQUE 6.0 Volts 7.4 Volts 4.8 Volts 6.0 Volts 6.0 Volts 7.4 Volts 6.0 Volts 7.4 Volts Torque: 403 oz-in 486 oz-in Torque: 250 oz-in 333 oz-in Torque: 500 oz-in 611 oz-in Torque: 157 oz-in 179 oz-in Speed: 0.17 sec/60° 0.14 sec/60° Speed: 0.19 sec/60° 0.15 sec/60° Speed: 0.21 sec/60° 0.17 sec/60° Speed: 0.20 sec/60° 0.18 sec/60° DIY Projects: Programmable Controllers: Wild Thumper-Based Robot Wixel and Wixel Shield #1702: Premium Jumper #1336: Wixel programmable Wire Assortment M-M 6" microcontroller module with #1372: Pololu Simple Motor integrated USB and a 2.4 Controller 18v7 GHz radio. -
Programming and Customizing the Multicore Propeller
PROGRAMMING AND CUSTOMIZING THE MULTICORE PROPELLERTM MICROCONTROLLER This page intentionally left blank PROGRAMMING AND CUSTOMIZING THE MULTICORE PROPELLERTM MICROCONTROLLER THE OFFICIAL GUIDE PARALLAX INC. Shane Avery Chip Gracey Vern Graner Martin Hebel Joshua Hintze André LaMothe Andy Lindsay Jeff Martin Hanno Sander New York Chicago San Francisco Lisbon London Madrid Mexico City Milan New Delhi San Juan Seoul Singapore Sydney Toronto Copyright © 2010 by The McGraw-Hill Companies, Inc. All rights reserved. Except as permitted under the United States Copyright Act of 1976, no part of this publication may be reproduced or distributed in any form or by any means, or stored in a database or retrieval system, without the prior written permission of the publisher. ISBN: 978-0-07-166451-6 MHID: 0-07-166451-3 The material in this eBook also appears in the print version of this title: ISBN: 978-0-07-166450-9, MHID: 0-07-166450-5. All trademarks are trademarks of their respective owners. Rather than put a trademark symbol after every occurrence of a trademarked name, we use names in an editorial fashion only, and to the benefit of the trademark owner, with no intention of infringement of the trademark. Where such designations appear in this book, they have been printed with initial caps. McGraw-Hill eBooks are available at special quantity discounts to use as premiums and sales promotions, or for use in corporate training programs. To contact a representative please e-mail us at [email protected]. Information contained in this work has been obtained by The McGraw-Hill Companies, Inc. -
Propeller Manual, Propeller Datasheet, Propeller Forum, and Propeller Object Exchange, As Well As Examples of Using These Resources
Propeller Education Kit Labs Fundamentals Version 1.2 (web release 2) By Andy Lindsay WARRANTY Parallax Inc. warrants its products against defects in materials and workmanship for a period of 90 days from receipt of product. If you discover a defect, Parallax Inc. will, at its option, repair or replace the merchandise, or refund the purchase price. Before returning the product to Parallax, call for a Return Merchandise Authorization (RMA) number. Write the RMA number on the outside of the box used to return the merchandise to Parallax. Please enclose the following along with the returned merchandise: your name, telephone number, shipping address, and a description of the problem. Parallax will return your product or its replacement using the same shipping method used to ship the product to Parallax. 14-DAY MONEY BACK GUARANTEE If, within 14 days of having received your product, you find that it does not suit your needs, you may return it for a full refund. Parallax Inc. will refund the purchase price of the product, excluding shipping/handling costs. This guarantee is void if the product has been altered or damaged. See the Warranty section above for instructions on returning a product to Parallax. COPYRIGHTS AND TRADEMARKS This documentation is copyright © 2006-2010 by Parallax Inc. By downloading or obtaining a printed copy of this documentation or software you agree that it is to be used exclusively with Parallax products. Any other uses are not permitted and may represent a violation of Parallax copyrights, legally punishable according to Federal copyright or intellectual property laws. Any duplication of this documentation for commercial uses is expressly prohibited by Parallax Inc. -
Using the Parallax Propeller for Mechatronics Education
Paper ID #7393 Using the Parallax Propeller for Mechatronics Education Dr. Hugh Jack, Grand Valley State University Hugh Jack is a Professor of Product Design and Manufacturing Engineering at Grand Valley State Uni- versity in Grand Rapids, Michigan. His interests include manufacturing education, design, project man- agement, automation, and control systems. c American Society for Engineering Education, 2013 Using the Parallax Propeller for Mechatronics Education Abstract Microcontrollers have become a mainstay of mechatronics laboratories. For example, the Arduino boards, and shields, are low cost flexible hardware that can provide substantial capabilities. At Grand Valley State University all engineering students learn to program microcontrollers using Atmel ATMega processors, the same processors used on the Arduino boards. In the mechatronics course, EGR 345 - Dynamic System Modeling and Control, the students use Parallax Propeller based hardware. The alternate, Parallax Propeller, hardware platform broadens the students’ knowledge and gives them access to a multiprocessing environment. The paper objectively outlines the hardware/software platform and how it can be used in a mechatronics course for Manufacturing Engineering students. The supported topics include data collection, feedback control, various sensors, networking, and human interfaces. Educational activities include laboratory work and small projects. Introduction A computation platform is the backbone of any introductory course focused on mechatronics and/or modern controls. The number of available platforms easily reaches into the thousands. However for the purposes of education there are a few wise alternatives. The typical selection criteria for these systems are: • Cost for hardware and software; • Programming knowledge and student prerequisites; • Capabilities; • Electronic interfacing complexity and options; • Built in capabilities and functions; and • Adoption by industry. -
Lecture #3 PIC Microcontrollers
Integrated Technical Education Cluster Banna - At AlAmeeria © Ahmad © Ahmad El E-626-A Real-Time Embedded Systems (RTES) Lecture #3 PIC Microcontrollers Instructor: 2015 SPRING Dr. Ahmad El-Banna Banna Agenda - What’s a Microcontroller? © Ahmad El Types of Microcontrollers Features and Internal structure of PIC 16F877A RTES, Lec#3 , Spring Lec#3 , 2015 RTES, Instruction Execution 2 Banna What is a microcontroller? - • A microcontroller (sometimes abbreviated µC, uC or MCU) is a small computer on a single integrated circuit © Ahmad El containing a processor core, memory, and programmable input/output peripherals. • It can only perform simple/specific tasks. • A microcontroller is often described as a ‘computer-on-a- chip’. RTES, Lec#3 , Spring Lec#3 , 2015 RTES, 3 Microcomputer system and Microcontroller Banna based system - © Ahmad © Ahmad El RTES, Lec#3 , Spring Lec#3 , 2015 RTES, 4 Banna Microcontrollers.. - • Microcontrollers are purchased ‘blank’ and then programmed with a specific control program. © Ahmad El • Once programmed the microcontroller is build into a product to make the product more intelligent and easier to use. • A designer will use a Microcontroller to: • Gather input from various sensors • Process this input into a set of actions • Use the output mechanisms on the microcontroller to do something useful. RTES, Lec#3 , Spring Lec#3 , 2015 RTES, 5 Banna Types of Microcontrollers - • Parallax Propeller • Freescale 68HC11 (8-bit) • Intel 8051 © Ahmad El • Silicon Laboratories Pipelined 8051 Microcontrollers • ARM processors (from many vendors) using ARM7 or Cortex-M3 cores are generally microcontrollers • STMicroelectronics STM8 (8-bit), ST10 (16-bit) and STM32 (32-bit) • Atmel AVR (8-bit), AVR32 (32-bit), and AT91SAM (32-bit) • Freescale ColdFire (32-bit) and S08 (8-bit) • Hitachi H8, Hitachi SuperH (32-bit) • Hyperstone E1/E2 (32-bit, First full integration of RISC and DSP on one processor core [1996]) • Infineon Microcontroller: 8, 16, 32 Bit microcontrollers for Spring Lec#3 , 2015 RTES, automotive and industrial applications. -
45% of Members Believe Mo Lybdenite O R Grapheme Will Replace Silico N As the Co Nducto R O F Choice
ja, … goedkope) en onbeperkte (nou ja… bijna) hardware bijna) ja… (nou onbeperkte en goedkope) … ja, (nou gratis over gaat toekomst De komt. op aan er het als 32-bits MCU’s of en 8-bit microcontrollers, elektronica discrete Vergeet toekomst. de heeft Platform-denken 89% of members work on MCU- based projects in their spare time. Il vero sacro calice della progettazione con FPGA è passare da un qual- che modello ad alto liv- ello direttamente al co- dice FPGA. Solo in questo modo è possibile proget- tare un sistema utilizzan- THE CIR do del codice C, simulare l’intero sistema sul pro- prio computer e scaricare con estrema facilità il co- C dice nella FPGA. Ebbene, UI questa tecnologia esiste T ed è disponibile in varie CELLAR 25 . 60% of members solder almost daily. Si vous avez des signaux HF dans la partie analogique d’un par les lignes ce signal HF rayonnera forcément circuit, sûr : une ligne d’alimentationd’alimentation. Un seul remède séparée pour chaque section analogique ou numérique de avec un découplage systématique de chacun, circuit, votre eux. d’alimentation et entre aussi bien par rapport à la source forme già da diversi anni A MICROCONTROLLER IS A SPECIALIZED, INTE- GRATED CHIP THAT PERFORMS SIMILAR FUNC- TIONS TO A PC. ITS OPERATION, HOWEVER, IS TAILORED FOR A SINGLE DEDICATED TASK COMPARED TO A PC TYPICALLY USED FOR MANY T H GENERAL-PURPOSE TASKS. MICROCONTROLLER A PERFORMANCE IS LIMITED TO THE ON CHIP NNIVERSARY PHYSICAL RESOURCES. THE PC, IN CONTRAST, IS COMPOSED OF MANY HIGH-PERFORMANCE INTEGRATED CIRCUITS AND IS BETTER SUITED FOR GENERAL-PURPOSE TASKS. -
Propeller Quick Reference Guide
Propeller Chip Quick Reference Spin Language Command Returns Description Value ABORT 〈Value〉 9 Exit from PUB/PRI method using abort status with optional return value. BYTE Symbol 〈[Count]〉 Declare byte-sized symbol in VAR block. 〈Symbol〉 BYTE Data 〈[Count]〉 Declare byte-aligned and/or byte-sized data in DAT block. BYTE [BaseAddress] 〈[Offset]〉 9 Read/write byte of main memory. Symbol.BYTE 〈[Offset]〉 9 Read/write byte-sized component of word/long-sized variable. BYTEFILL (StartAddress, Value, Count) Fill bytes of main memory with a value. BYTEMOVE (DestAddress, SrcAddress, Count) Copy bytes from one region to another in main memory. CASE CaseExpression MatchExpression : Statement(s) Compare expression against matching expression(s), execute code block if match found. 〈 MatchExpression : MatchExpression can contain a single expression or multiple comma-delimited expressions. Statement (s)〉 Expressions can be a single value (ex: 10) or a range of values (ex: 10..15). 〈 OTHER : Statement(s)〉 CHIPVER 9 Version number of the Propeller chip. CLKFREQ 9 Current System Clock frequency, in Hz. CLKMODE 9 Current clock mode setting. CLKSET (Mode, Frequency) Set both clock mode and System Clock frequency at run time. CNT 9 Current 32-bit System Counter value. COGID 9 Current cog’s ID number; 0-7. COGINIT (CogID, SpinMethod 〈(ParameterList)〉, StackPointer) Start or restart cog by ID to run Spin code. COGINIT (CogID, AsmAddress, Parameter) Start or restart cog by ID to run Propeller Assembly code. COGNEW (SpinMethod 〈(ParameterList)〉, StackPointer) 9 Start new cog for Spin code and get cog ID; 0-7 = succeeded, -1 = failed. COGNEW (AsmAddress, Parameter) 9 Start new cog for Propeller Assembly code and get cog ID; 0-7 = succeeded, -1 = failed. -
Controlling Home Appliances Using Internet
CONTROLLING HOME APPLIANCES USING INTERNET Project Report submitted in partial fulfillment of the requirement for the degree of Bachelor of Technology In Information Technology Under the Supervision of Mr. Amol Vasudeva Assistant Professor By ANIRUDH KAUSHIK (111478) Jaypee University of Information and Technology Waknaghat, Solan– 173234, Himachal Pradesh i Certificate This is to certify that project report entitled “Controlling Home Appliances Using Internet”, submitted by Anirudh Kaushik in partial fulfillment for the award of degree of Bachelor of Technology in Information Technology in Jaypee University of Information Technology, Waknaghat, Solan has been carried out under my supervision. This work has not been submitted partially or fully to any other University or Institute for the award of this or any other degree or diploma. Date: 8th May 2015 Mr. Amol Vasudeva (Assistant Professor) ii Acknowledgement No venture can be completed without the blessings of the Almighty. I consider it my bounded duty to bow to Almighty whose kindness has always inspired me on the right path. I would like to take the opportunity to thank all the people who helped us in any form in the completion of my project “Controlling Home Appliances using Internet”. It would not have been possible to see through the project without the guidance and constant support of my project guide Mr. Amol Vasudeva. For his coherent guidance, careful supervision, critical suggestions and encouragement I feel fortunate to be taught by him. I would like to express my gratitude towards Brig. (Retd) Balbir Singh, Director JUIT, for having trust in me. I owe my heartiest thanks to Prof. -
Propeller Manual Version 1.01 WARRANTY Parallax Inc
Propeller Manual Version 1.01 WARRANTY Parallax Inc. warrants its products against defects in materials and workmanship for a period of 90 days from receipt of product. If you discover a defect, Parallax Inc. will, at its option, repair or replace the merchandise, or refund the purchase price. Before returning the product to Parallax, call for a Return Merchandise Authorization (RMA) number. Write the RMA number on the outside of the box used to return the merchandise to Parallax. Please enclose the following along with the returned merchandise: your name, telephone number, shipping address, and a description of the problem. Parallax will return your product or its replacement using the same shipping method used to ship the product to Parallax. 14-DAY MONEY BACK GUARANTEE If, within 14 days of having received your product, you find that it does not suit your needs, you may return it for a full refund. Parallax Inc. will refund the purchase price of the product, excluding shipping/handling costs. This guarantee is void if the product has been altered or damaged. See the Warranty section above for instructions on returning a product to Parallax. COPYRIGHTS AND TRADEMARKS This documentation is copyright © 2006 by Parallax Inc. By downloading or obtaining a printed copy of this documentation or software you agree that it is to be used exclusively with Parallax products. Any other uses are not permitted and may represent a violation of Parallax copyrights, legally punishable according to Federal copyright or intellectual property laws. Any duplication of this documentation for commercial uses is expressly prohibited by Parallax Inc. -
Least Power Point Tracking Method for Photovoltaic Differential Power Processing Systems
International Journal for Modern Trends in Science and Technology Volume: 03, Issue No: 05, May 2017 ISSN: 2455-3778 http://www.ijmtst.com Least Power Point Tracking Method for Photovoltaic Differential Power Processing Systems S.Sathish Kumar1 | S.Sri Priya2 1PG Scholar, Department of EEE, Roever Engineering College, Perambalur, Tamilnadu, India. 2Assistant Professor, Department of EEE, Roever Engineering College, Perambalur, Tamilnadu, India. To Cite this Article S.Sathish Kumar and S.Sri Priya, “Least Power Point Tracking Method for Photovoltaic Differential Power Processing Systems”, International Journal for Modern Trends in Science and Technology, Vol. 03, Issue 05, May 2017, pp. 38-43. ABSTRACT Differential power processing (DPP)systems are a promising architecture for future photovoltaic (PV) power systems that achieve high system efficiency through processing a faction of thefull PV power, while achieving distributed local maximum power point tracking (MPPT). In the PVto-bus DPP architecture, the power processed through the DPP converters depends on the string current, which must be controlled to minimize thepower processed through the DPP converters. A realtimeleast power point tracking (LPPT) method is proposed to minimize power stress on PV DPPconverters. Mathematical analysis shows theuniqueness of the least power point for the total power processed through the system. The perturband observe LPPT method is presented that enablesthe DPP converters to maintain optimal operatingconditions, while reducing the total power loss andconverter stress. This work validates throughsimulation and experimentation that LPPT in thestring-level converter successfully operates withMPPT in the DPP converters to maximize outputpower for the PV to- bus architecture. Hardware prototypes were developed and tested at 140 W and300 W, and the LPPT control algorithm showedeffective operation under steady-state operation andan irradiance step change.