Oxidation of Sodium Thiocyanate (Nascn) in High Ionic-Strength Process Aqueous Liquor
Total Page:16
File Type:pdf, Size:1020Kb
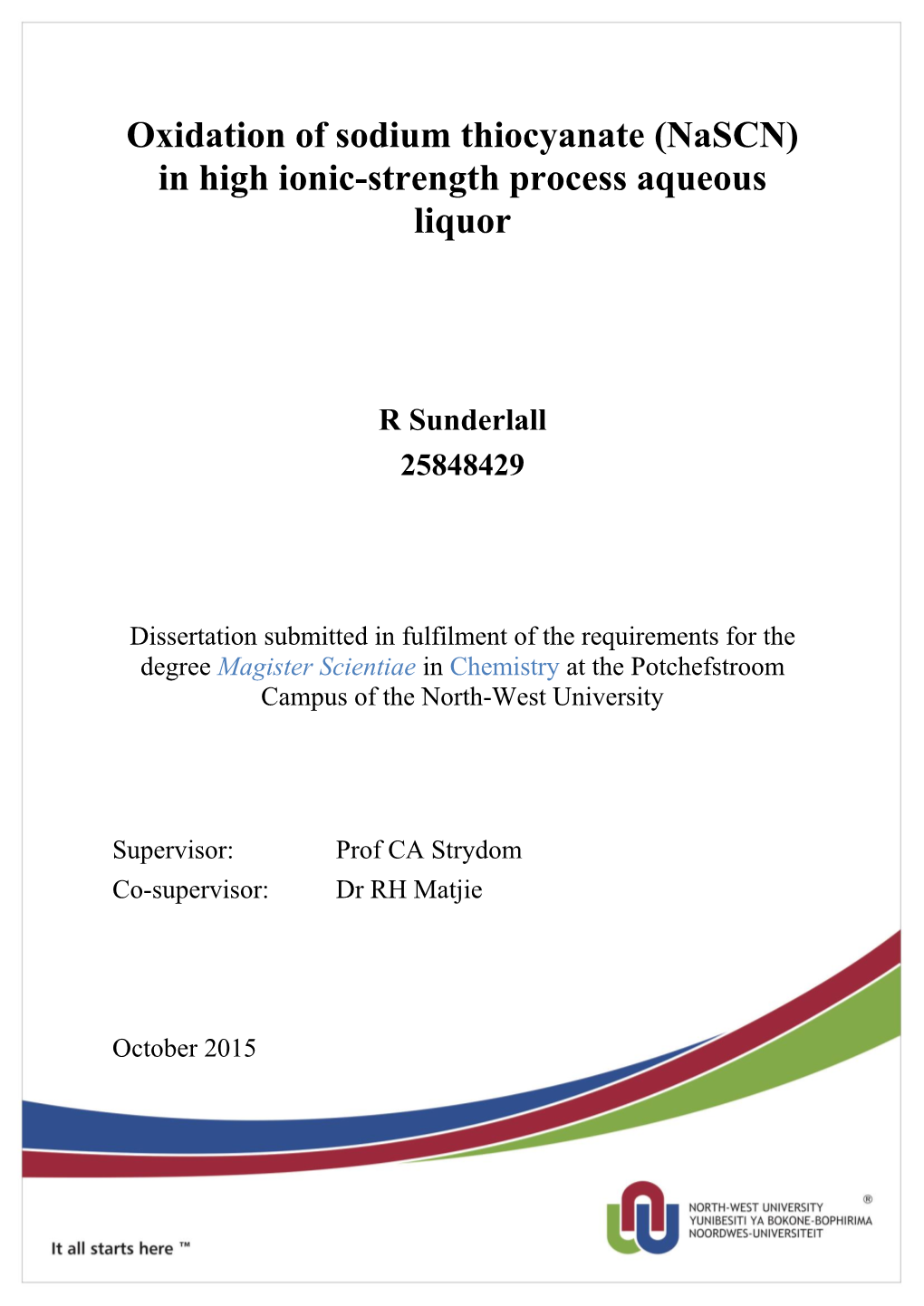
Load more
Recommended publications
-
Product Information Sodium Thiocyanate
Product Information Sodium Thiocyanate 98% Product Description: Sodium thiocyanate 98% is an odorless, white solid. Produced from cyanide with sulfur. It is one of the main sources of the thiocyanate ion making it useful as a precursor to a lot of specialty chemicals. Applications: Sodium thiocyanate is used as a concrete hardener accelerator and can be used with other accelerators. It is used as a corrosion inhibitor, in synthetic fibre production, electroplating and pesticide. Chemical Formula: NaSCN CAS No. : 540-72-7 Specifications: Parameters (units) Specifications Sodium thiocyanate (%) ≥ 98 Chloride (%) ≤ 0.06 Sulfate (%) ≤ 0.2 Iron (%) ≤ 0.0005 Heavy metals (%) ≤ 0.001 Insolubles (%) ≤ 0.006 Moisture content (%) ≤ 1.0 pH 6.0 - 8.0 Bisley International LLC 1790 Hughes Landing Boulevard Suite 400 The Woodlands 77380 TX USA Phone number: +1 (281) 506 046 Emergency telephone number: +1 855 237 5573 bisleyinternational.com Copyright 2021 Bisley & Co. Pty Ltd. All rights reserved Packaging: Material is available in 25 kg bags and 950 kg bulk bags. Further packaging options may be available upon enquiry. Storage: Product should be stored in a dry place away from direct sunlight in sealed, original packaging. Safety: For further safety information refer to product SDS available from your Bisley International contact. Disclaimer: This document is for information purposes only. Customers are responsible for testing and confirming the suitability of this product in their application. To the extent permitted by law, no warranty as to merchantability or fitness of purpose, expressed or implied, is made. Global Headquarters Regional offices Sydney, Australia Jakarta, Indonesia Bangkok, Thailand Bisley & Company PT Bisindo Kencana Bisley Asia (Thailand) Co. -
Microemulsion and Oil Soluble Gassing System
Europaisches Patentamt (19) European Patent Office Office europeeneen des brevets £P 0 775 681 A1 (12) EUROPEAN PATENT APPLICATION (43) Date of publication: (51) intci.6: C06B 23/00, C06B 47/14 28.05.1997 Bulletin 1997/22 (21) Application number: 96308223.5 (22) Date of filing: 14.11.1996 (84) Designated Contracting States: (72) Inventor: Chattopadhyay, Arun Kumar DE FR GB SE Quebec J4Z 3E6 (CA) (30) Priority: 24.11.1995 CA 2163682 (74) Representative: Ede, Eric Fitzpatricks, (71) Applicant: ICI Canada Inc. 4 West Regent Street North York Ontario M2N 6H2 (CA) Glasgow G2 1 RS, Scotland (GB) (54) Microemulsion and oil soluble gassing system (57) The present invention relates to a process for microemulsions of the present invention provides more preparing an emulsion explosive which has been sensi- complete mixing of the gas precursor with the constitu- tized by the in-situ gassing of a chemical gassing agent, ents of the emulsion explosives. The process thus pro- wherein the gassing agent is contained in a microemul- vides a more controllable reaction for the in-situ, chem- sion. The invention also relates to the microemulsions ical gassing of emulsions, and for the production of utilized in the practise of this process. The use of the chemically gassed emulsion explosives at lower tem- perature. FIGURE Density (g/cc) i 1.3 1.2 1.1 h 1.0 00 CO 30 Time (mins) lO Is- Is- o a. LU Printed by Jouve, 75001 PARIS (FR) EP 0 775 681 A1 Description Field of the Invention 5 This invention relates to an improved process for preparing an emulsion explosive and incorporation of a dispersed gaseous phase within the emulsion. -
ISOPROPYL THIOCYANATE [Thiocyanic Acid, Isopropyl Ester]
A Publication of Reliable Methods for the Preparation of Organic Compounds Working with Hazardous Chemicals The procedures in Organic Syntheses are intended for use only by persons with proper training in experimental organic chemistry. All hazardous materials should be handled using the standard procedures for work with chemicals described in references such as "Prudent Practices in the Laboratory" (The National Academies Press, Washington, D.C., 2011; the full text can be accessed free of charge at http://www.nap.edu/catalog.php?record_id=12654). All chemical waste should be disposed of in accordance with local regulations. For general guidelines for the management of chemical waste, see Chapter 8 of Prudent Practices. In some articles in Organic Syntheses, chemical-specific hazards are highlighted in red “Caution Notes” within a procedure. It is important to recognize that the absence of a caution note does not imply that no significant hazards are associated with the chemicals involved in that procedure. Prior to performing a reaction, a thorough risk assessment should be carried out that includes a review of the potential hazards associated with each chemical and experimental operation on the scale that is planned for the procedure. Guidelines for carrying out a risk assessment and for analyzing the hazards associated with chemicals can be found in Chapter 4 of Prudent Practices. The procedures described in Organic Syntheses are provided as published and are conducted at one's own risk. Organic Syntheses, Inc., its Editors, and its Board of Directors do not warrant or guarantee the safety of individuals using these procedures and hereby disclaim any liability for any injuries or damages claimed to have resulted from or related in any way to the procedures herein. -
1 Abietic Acid R Abrasive Silica for Polishing DR Acenaphthene M (LC
1 abietic acid R abrasive silica for polishing DR acenaphthene M (LC) acenaphthene quinone R acenaphthylene R acetal (see 1,1-diethoxyethane) acetaldehyde M (FC) acetaldehyde-d (CH3CDO) R acetaldehyde dimethyl acetal CH acetaldoxime R acetamide M (LC) acetamidinium chloride R acetamidoacrylic acid 2- NB acetamidobenzaldehyde p- R acetamidobenzenesulfonyl chloride 4- R acetamidodeoxythioglucopyranose triacetate 2- -2- -1- -β-D- 3,4,6- AB acetamidomethylthiazole 2- -4- PB acetanilide M (LC) acetazolamide R acetdimethylamide see dimethylacetamide, N,N- acethydrazide R acetic acid M (solv) acetic anhydride M (FC) acetmethylamide see methylacetamide, N- acetoacetamide R acetoacetanilide R acetoacetic acid, lithium salt R acetobromoglucose -α-D- NB acetohydroxamic acid R acetoin R acetol (hydroxyacetone) R acetonaphthalide (α)R acetone M (solv) acetone ,A.R. M (solv) acetone-d6 RM acetone cyanohydrin R acetonedicarboxylic acid ,dimethyl ester R acetonedicarboxylic acid -1,3- R acetone dimethyl acetal see dimethoxypropane 2,2- acetonitrile M (solv) acetonitrile-d3 RM acetonylacetone see hexanedione 2,5- acetonylbenzylhydroxycoumarin (3-(α- -4- R acetophenone M (LC) acetophenone oxime R acetophenone trimethylsilyl enol ether see phenyltrimethylsilyl... acetoxyacetone (oxopropyl acetate 2-) R acetoxybenzoic acid 4- DS acetoxynaphthoic acid 6- -2- R 2 acetylacetaldehyde dimethylacetal R acetylacetone (pentanedione -2,4-) M (C) acetylbenzonitrile p- R acetylbiphenyl 4- see phenylacetophenone, p- acetyl bromide M (FC) acetylbromothiophene 2- -5- -
Determination of Tetrathionate, Thiosulfate, Sulfite and Trithionate in Their Mixtures by Spectrophotometry
ANALYTICAL SCIENCES FEBRUARY 1989, VOL. 5 79 Determination of Tetrathionate, Thiosulfate, Sulfite and Trithionate in Their Mixtures by Spectrophotometry Tomozo KOH, Yasuyuki MIURA, Masahiro IsHIMORI and Norihito YAMAMURO Department of Chemistry, Faculty of Science, Tokai University, Hiratsuka, Kanagawa 259-12, Japan The proposed method consists of four procedures; excess iodine for reactions with thiosulfate and/or sulfite under Procedures I, II and III, and the thiocyanate formed under Procedure IV are measured spectrophotometrically after proper chemical treatments. The absorbance obtained by Procedure I corresponds to the sum of the amount of tetrathionate and that of thiosulfate in the mixture. The absorbance obtained by Procedure II corresponds only to the amount of thiosulfate in the mixture. The absorbance obtained by Procedure III corresponds to the sum of the amount of thiosulfate and twice that of sulfite in the mixture. The absorbance obtained by Procedure IV corresponds to the sum of the amount of both thiosulfate and trithionate and twice that of tetrathionate in the mixture. The proposed method was applied to the determination of tetrathionate, thiosulfate, sulfite and trithionate mixed in various ratios in amounts of more than 0.05 µmol with an error below ±0.02 µmol. Keywords Polythionates determination, tetrathionate sulfitolysis, trithionate cyanolysis, tetrathionate-trithionate- thiosulfate-sulfite mixture, spectrophotometry The determination of various sulfur anion species in of four sulfur species of tetrathionate, thiosulfate, their mixtures is desirable for interpreting their redox sulfite and trithionate in a mixture. chemistry in aqueous solution systems. However, this is difficult owing to similarities in their chemical and physical properties. Spectrophotometric methods"2 for Experimental the determination of trithionate, thiosulfate and tetra- thionate in a mixture, based on the formation of Reagents and apparatus thiocyanate by their cyanolysis, have been proposed. -
United States Patent Office Patented Apr
3,509,255 United States Patent Office Patented Apr. 28, 1970 1. 2 biotics Annual, 1953-1954, pages 191-194, Medical En 3,509,255 cyclopedia, Inc., New York, N.Y. PROCESS FOR THE RECRYSTALLIZATION The recovery of nystatin by isopropanol extraction of OF NYSTATIN Harold Mendelsohn, Nanuet, N.Y., assignor to American the whole broth resulting from the fermentation of the Cyanamid Company, Stamford, Conn., a corporation of nystatin producing Streptomyces noursei is described in Maine U.S. Patent No. 2,786,781 to Vandeputte et al. The par No Drawing. Filed July 2, 1968, Ser. No. 741,912 tially purified product obtained by the Vandeputte et al. Int. Cl. A61k 21/00 process is a therapeutically useful product of about 65 U.S. C. 424-123 10 Claims 70% purity. At best, however it is only partially crystal line and for the most part is substantially non-crystalline or amorphous in character. The purification of nystatin ABSTRACT OF THE DISCLOSURE employing methanolic-calcium chloride is also described This disclosure describes a process for preparing highly in U.S. Patent No. 2,832,719 to Vandeputte and in U.S. purified crystalline nystatin by extracting crude nystatin Patent No. 2,865,807 to Dutcher et al. The product ob with acetone which is saturated with sodium iodide, 15 tained by the Vandeputte and Dutcher et al. processes is Sodium thiocyanate, potassium thiocyanate or ammonium a therapeutically useful highly refined product substan thiocyanate; and precipitating highly purified crystalline tially crystalline in character. nystatin from the extract by displacement of the acetone The processes described above produce crystalline ny with water. -
Life Cycle Assessment of Process Strategies for Value Recovery and Environmental Mitigation of Mining Waste
Life cycle assessment of process strategies for value recovery and environmental mitigation of mining waste by Kieran Hillmar Cairncross Thesis presented in partial fulfilment of the requirements for the Degree of MASTER OF ENGINEERING (CHEMICAL ENGINEERING) in the Faculty of Engineering at Stellenbosch University The financial assistance of the National Research Foundation (NRF) towards this research is hereby acknowledged. Opinions expressed and conclusions arrived at, are those of the author and are not necessarily to be attributed to the NRF. Supervisor Dr Margreth Tadie December 2020 Stellenbosch University https://scholar.sun.ac.za Declaration By submitting this thesis electronically, I declare that the entirety of the work contained therein is my own, original work, that I am the sole author thereof (save to the extent explicitly otherwise stated), that reproduction and publication thereof by Stellenbosch University will not infringe any third party rights and that I have not previously in its entirety or in part submitted it for obtaining any qualification. Date: 11 September 2020 Copyright © 2020 Stellenbosch University All rights reserved i Stellenbosch University https://scholar.sun.ac.za Abstract By 2031, South African primary ore gold grades are forecasted to decline to the gold grades expected in mine tailings resources. Furthermore, the reprocessing of mine tailings does not require the costly excavation and size reduction unit operations necessary for primary ore resources. Mine tailings can therefore be viewed as a secondary gold resource. Hazardous pollutants and acid mine drainage (AMD) emanating from Witwatersrand stockpiled tailings dams affect human and ecosystem health. Potential exists to valorise mine tailings to the circular economy as construction raw materials and mine backfill. -
Experiment 4
Experiment Chemical Equilibrium 4 A reversible reaction is the type of reaction where a certain chemical process is able to proceed in a forward or reverse direction depending on experimental conditions. The chemical equation, which represents this, is written with double arrows as follows: aA + bB ⇄ cC + dD In an equation as above, the chemical symbols (capitol letters) represent not only moles of the substances involved in the process but also moles per liter of the substances. The lower case letters are the stoichiometric coefficients. At equilibrium, the rate of the forward reaction is equal to the rate of the reverse reaction. The equilibrium constant is expressed as the concentrations of the products over the concentrations of the reactants. [C]c[D]d K [A]a[B]b In a reversible system, the species involved (on both sides of the double arrows) will be at a dynamic equilibrium with each other, so that a small disturbance of this balance affecting either side of the equation will involve all the species. The formal way of stating this is called Le Chatlier’s Principle - If stress is placed on a system at equilibrium, the equilibrium will shift in a direction in order to overcome the stress. The stress could be a change of concentration of one or more of the chemical species, change of pressure, change of temperature and etc. Shift means the direction of change of the concentration of certain species opposing the stress. Examples of reversible systems at equilibrium are the following: 1. Weak acids or bases 2. Saturated solutions of salts 3. -
United States Patent (19) 11 Patent Number: 5,212,098 Hoffmann Et Al
III USOO5212098A United States Patent (19) 11 Patent Number: 5,212,098 Hoffmann et al. (45) Date of Patent: May 18, 1993 54 BROMIDE ION DETERMINATION Determinative of Alkali Metal Bromides and Thiocya 75 Inventors: Andrew F. Hoffmann, Walworth; nates in Mixtures', Anal. Chem. 40(13), Nov. 1968, pp. Richard W. Bauer, Jr., Rochester, 2052-2053. both of N.Y. Kolesnikova, T. A. and R. A. Etinger, "Determination of Bromide and Thiocyanate in Developer Solutions', 73) Assignee: Eastman Kodak Company, Tekh. Kino Telev. 12(2) 33-34, 1968, English Abstract Rochester, N.Y. Only. 21 Appl. No.: 766,944 Chemical Reviews, "Adsorption Indicators', I. M. Kolthoff, vol. 16, 87 (1935). 22 Filed: Sep. 27, 1991 New Methods of Volumetric Analysis, Part VII, "Adsorp tion Indicators for Precipitation Titrations', K. Fajans, Related U.S. Application Data D. Van Norstrand Company, Inc., New York (1938). 63 Continuation-in-part of Ser. No. 761,181, Sep. 17, 1991, abandoned. Primary Examiner-James C. Housel Assistant Examiner-Jan M. Ludlow 51) int. Cl. ............................................. G01N 33/00 Attorney, Agent, or Firm-L. George Legg 52 U.S. C. .................................... 436/125; 436/124; 436/163; 436/175; 436/178; 430/399 57 ABSTRACT 58 Field of Search ............... 436/124, 125, 163, 164, Bromide ion content in a photographic developer is an 436/175, 178; 430/399 important variable to be controlled by photoprocessors 56 References Cited who process color reversal material or color negative film. The bromide content of such developers can be U.S. PATENT DOCUMENTS determined by titration with silver ion, using tetraiodo 3,329,468 7/1967 Rupe .................................. -
Chemical Names and CAS Numbers Final
Chemical Abstract Chemical Formula Chemical Name Service (CAS) Number C3H8O 1‐propanol C4H7BrO2 2‐bromobutyric acid 80‐58‐0 GeH3COOH 2‐germaacetic acid C4H10 2‐methylpropane 75‐28‐5 C3H8O 2‐propanol 67‐63‐0 C6H10O3 4‐acetylbutyric acid 448671 C4H7BrO2 4‐bromobutyric acid 2623‐87‐2 CH3CHO acetaldehyde CH3CONH2 acetamide C8H9NO2 acetaminophen 103‐90‐2 − C2H3O2 acetate ion − CH3COO acetate ion C2H4O2 acetic acid 64‐19‐7 CH3COOH acetic acid (CH3)2CO acetone CH3COCl acetyl chloride C2H2 acetylene 74‐86‐2 HCCH acetylene C9H8O4 acetylsalicylic acid 50‐78‐2 H2C(CH)CN acrylonitrile C3H7NO2 Ala C3H7NO2 alanine 56‐41‐7 NaAlSi3O3 albite AlSb aluminium antimonide 25152‐52‐7 AlAs aluminium arsenide 22831‐42‐1 AlBO2 aluminium borate 61279‐70‐7 AlBO aluminium boron oxide 12041‐48‐4 AlBr3 aluminium bromide 7727‐15‐3 AlBr3•6H2O aluminium bromide hexahydrate 2149397 AlCl4Cs aluminium caesium tetrachloride 17992‐03‐9 AlCl3 aluminium chloride (anhydrous) 7446‐70‐0 AlCl3•6H2O aluminium chloride hexahydrate 7784‐13‐6 AlClO aluminium chloride oxide 13596‐11‐7 AlB2 aluminium diboride 12041‐50‐8 AlF2 aluminium difluoride 13569‐23‐8 AlF2O aluminium difluoride oxide 38344‐66‐0 AlB12 aluminium dodecaboride 12041‐54‐2 Al2F6 aluminium fluoride 17949‐86‐9 AlF3 aluminium fluoride 7784‐18‐1 Al(CHO2)3 aluminium formate 7360‐53‐4 1 of 75 Chemical Abstract Chemical Formula Chemical Name Service (CAS) Number Al(OH)3 aluminium hydroxide 21645‐51‐2 Al2I6 aluminium iodide 18898‐35‐6 AlI3 aluminium iodide 7784‐23‐8 AlBr aluminium monobromide 22359‐97‐3 AlCl aluminium monochloride -
Recent Developments on the Origin and Nature of Reductive Sulfurous Off-Odours in Wine
fermentation Review Recent Developments on the Origin and Nature of Reductive Sulfurous Off-Odours in Wine Nikolaus Müller 1,* and Doris Rauhut 2 1 Silvanerweg 9, 55595 Wallhausen, Germany 2 Department of Microbiology and Biochemistry, Hochschule Geisenheim University, Von-Lade-Straße 1, 65366 Geisenheim, Germany; [email protected] * Correspondence: [email protected]; Tel.: +49-6706-913103 Received: 9 July 2018; Accepted: 3 August 2018; Published: 8 August 2018 Abstract: Reductive sulfurous off-odors are still one of the main reasons for rejecting wines by consumers. In 2008 at the International Wine Challenge in London, approximately 6% of the more than 10,000 wines presented were described as faulty. Twenty-eight percent were described as faulty because they presented “reduced characters” similar to those presented by “cork taint” and in nearly the same portion. Reductive off-odors are caused by low volatile sulfurous compounds. Their origin may be traced back to the metabolism of the microorganisms (yeasts and lactic acid bacteria) involved in the fermentation steps during wine making, often followed by chemical conversions. The main source of volatile sulfur compounds (VSCs) are precursors from the sulfate assimilation pathway (SAP, sometimes named as the “sulfate reduction pathway” SRP), used by yeast to assimilate sulfur from the environment and incorporate it into the essential sulfur-containing amino acids methionine and cysteine. Reductive off-odors became of increasing interest within the last few years, and the method to remove them by treatment with copper (II) salts (sulfate or citrate) is more and more questioned: The effectiveness is doubted, and after prolonged bottle storage, they reappear quite often. -
EPA's Hazardous Waste Listing
Hazardous Waste Listings A User-Friendly Reference Document September 2012 Table of Contents Introduction ..................................................................................................................................... 3 Overview of the Hazardous Waste Identification Process .............................................................. 5 Lists of Hazardous Wastes .............................................................................................................. 5 Summary Chart ............................................................................................................................... 8 General Hazardous Waste Listing Resources ................................................................................. 9 § 261.11 Criteria for listing hazardous waste. .............................................................................. 11 Subpart D-List of Hazardous Wastes ............................................................................................ 12 § 261.31 Hazardous wastes from non-specific sources. ............................................................... 13 Spent solvent wastes (F001 – F005) ......................................................................................... 13 Wastes from electroplating and other metal finishing operations (F006 - F012, and F019) ... 18 Dioxin bearing wastes (F020 - F023, and F026 – F028) .......................................................... 22 Wastes from production of certain chlorinated aliphatic hydrocarbons (F024