Textile Institute
Total Page:16
File Type:pdf, Size:1020Kb
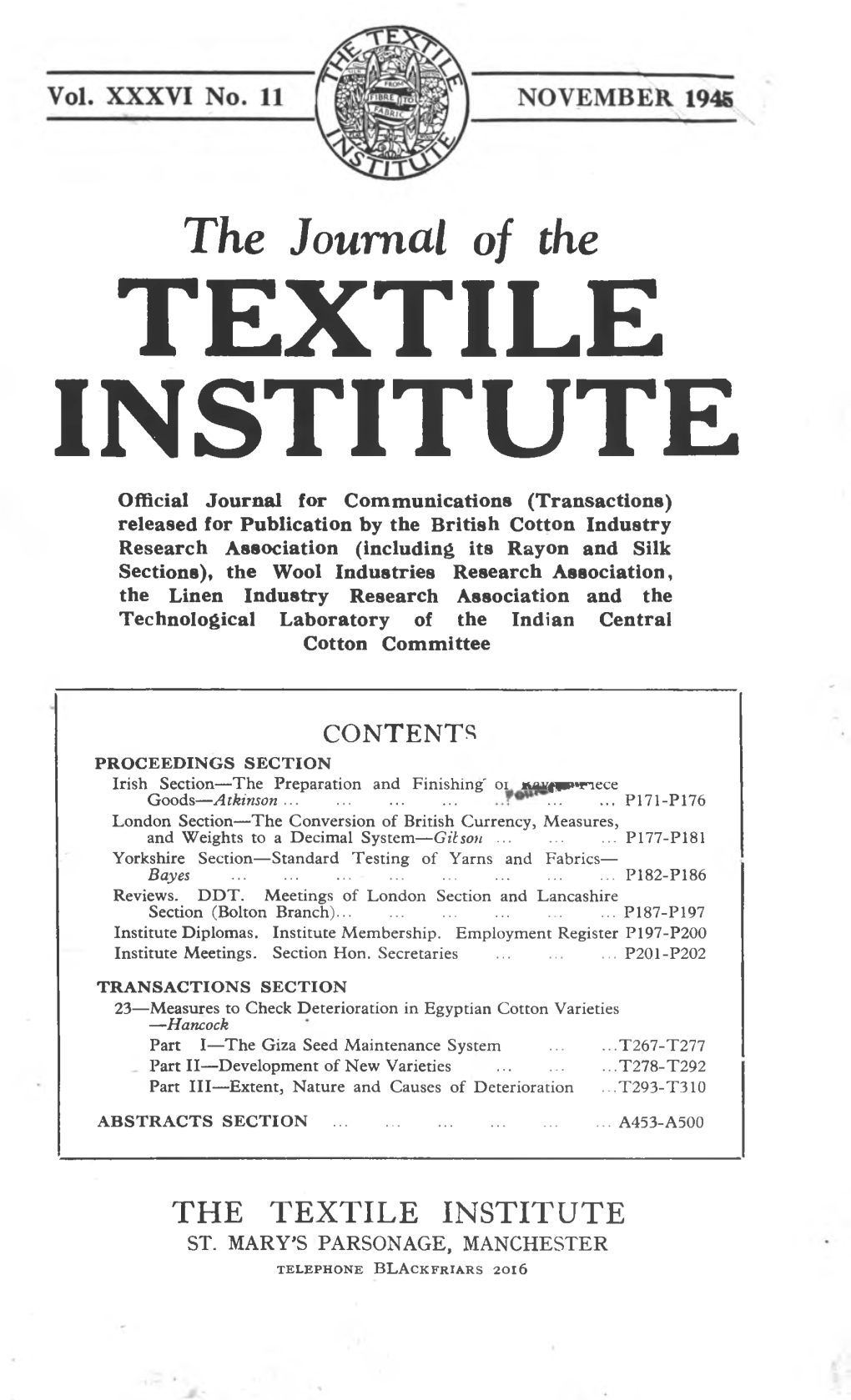
Load more
Recommended publications
-
CURRICULUM(CBCS) TEXTILE ENGINEERING (3 to 8 Semester)
Himachal Pradesh Technical University, Hamirpur (H.P.) CURRICULUM(CBCS) TEXTILE ENGINEERING rd th (3 to 8 Semester) Teaching and Examination Scheme 1 HIMACHAL PRADESH TECHNICAL UNIVERSITY, HAMIRPUR CURRICULUM OF B.TECH TEXTILE ENGINEERING 1. Credit System: A system enabling quantification of course work, with one credit being assigned to each unit after a student completes its teaching-learning process, followed by passing in both Continuous Internal Assessment CIA & Semester End Examination (SEE); Further, Choice Based Credit System (CBCS) to be helpful in customizing the course work for a student, through Core &Electives. 2. Credit Courses: All Courses registered by a student in a Semester is to earn credits. In a widely accepted definition, students to earn One Credit by registering and passing: One hour/week/Semester for Theory/Lecture (L) Courses; and, Two hours/week/Semester for Laboratory/Practical (P) Courses or Tutorials (T). NOTE: Other student activities not demanding intellectual work or enabling proper assessment like, practical training, study tour and guest lecture not to carry Credits. 3. Credit Representation: Credit values for different courses is as given in Table 1: Lectures Tutorials Practical Work Credits Total (hrs./wk./Sem.) (hrs./wk./Sem.) (hrs./wk./Sem.) (L: T: P/D) Credits 3 0 0 3:0:0 3 2 2 0 2:1:0 3 2 0 2 2:0:1 3 2 2 2 2:1:1 4 0 0 6 0:0:3 3 4.Course Load: Every student to register for a set of Courses in each Semester, with the total number of their Credits being limited by considering the permissible weeklyContactHours (typically: 30/Week); For this, an average Course Load of 24Credits/Semester (e.g., 6-7 Courses) is generally acceptable. -
Spinning and Winding Taro Nishimura
The_Textile_Machinery_Society_of_Japan_Textile_College_2-Day_Course_on_Cloth_Making_Introduction_to_Spinning_2014_05_22 Spinning and Winding Taro Nishimura 1. Introduction Since several thousand years ago, humans have been manufacturing linen, wool, cotton, and silk to be used as fibrous materials for clothing. In 繊維 (sen’i ), which is the word for “fiber,” the Chinese character 繊 (sen ) is a unit for decimal fractions of one ten-millionth (equal to approximately 30 Ǻ), while 維 (i) means “long and thin.” Usually, fibers are several dozen µ thick, and can range from around one centimeter long to nigh infinite length. All natural materials, with the exception of raw silk, are between several to several dozen centimeters long and are categorized as staple fibers. Most synthetic fibers are spun into filaments. Figure 1 shows how a variety of textile product forms are interrelated. Short fibers are spun into cotton (spun) yarns, whereas filaments are used just as they are, or as textured yarns by being twisted or stretched. Fabric cloths that are processed into two-dimensional forms using cotton (spun) yarns and filament yarns include woven fabrics, knit fabrics, nets, and laces. Non-woven fabrics are another type of two-dimensional form, in which staple fibers and filaments are directly processed into cloths without being twisted into yarns. Yet another two-dimensional form is that of films, which are not fiber products and are made from synthetic materials. Three-dimensional fabrics and braids are categorized as three-dimensional forms. This paper discusses spinning, or the process of making staple fibers into yarns, and winding, which prepares fibers for weaving. One-dimensional Two-dimensional Three-dimensional Natural Staple fibers Spun yarns Woven fabrics Three-dimensional materials Filaments Filament yarns Knit fabrics fabrics Synthetic Nets Braids materials Laces Non-woven fabrics Films Fig. -
Paper 2: the Woollen Cloth Industry in the Lim Valley © Richard Bull & Lyme Regis Museum Revised with Extra Images July 2015
Industrial Lyme - Paper 2: The Woollen Cloth Industry in the Lim Valley © Richard Bull & Lyme Regis Museum Revised with extra images July 2015 Like all research, this is on-going. If you know more, or are descended from any of the families involved, please get in touch with the author via Lyme Regis Museum. Summary Woollen cloth has been made in the Lim Valley from at least medieval times, but this paper is more about the factories in Lyme Regis and Uplyme that made high-quality West of England coat cloths. The factories in Lyme were bankrupt in 1847, leaving the Uplyme factory to soldier on against Yorkshire competition until it was destroyed by fire in 1866, whilst being modernised. In Lyme the factories were started up again in the 1850s to make silk thread and hemp twine, but only for a short period; these are the subjects of other papers in this series. This paper contains: the background to the trade, the history of the factories and a walking trail to see the mills. Cloth making – the essential process in a nutshell Sheep fleeces are packed on the farm into big canvas bags called woolsacks. At the factory the fleeces are scoured (washed) to remove lanolin (wool- grease), dirt and adhering vegetable material. Then the fleeces are scribbled (torn up into pieces), combed and carded to produce rovings, long strips of wool ready for spinning. Washed and combed fleece being fed into a carding machine at Coldharbour Mill, Uffculme, Devon Industrial Lyme Paper 2 – The Woollen Cloth Industry © R Bull & Lyme Regis Museum 1 Spinning means to draw out and twist - and by this process the scales of the individual wool fibres lock together to produce a thread known as a single. -
SOCIAL COUNCIL Mtniiiimhiuhhmtiimiiitniiiimiriiuniiitriiiiiiiftihiu ECONOMIC COMMISSION Î0R LATIN AMERICA
UNITED NATI ONS GENERAL E/CN.I2/9I9 ECONOMIC September 1971 ENGLISH AND ORIGINAL: PORTUGUESE SOCIAL COUNCIL MtniiiimHiuHHmtiimiiitniiiimiriiuniiitriiiiiiiftiHiu ECONOMIC COMMISSION Î0R LATIN AMERICA THE TRAÍAS PER OF TECHNICAL KNOW-HOW IN THE TEXTILE AND CLOTHING INDUSTRIES IN BRAZIL prepared by Luigi Spreafico, Consultant J Note; This report foms part of a study undertaken ty the Economic Commission for Latin America (ECLA), the Interamerican Development Bank (IDB) and the Division of Public Finance and Financial Institutions of the United Nations Department of Economic and Social Affairs on the problems of the transfer of industrial technology in Brazil. I - iii - TABLE OF CONTENTS Page Chapter I. PRODUCTION IN THE TEXTILE INDUSTRY AND THE ACCUMULATION OF TECHNICAL KNOW-HOW OVER TIME 1 A. INTRODUCTION 1 B. THE ACCUMULATION OF TECHNICAL KNOW-HOW IN THE TEXTILE INDUSTRY 5 C. CHARACTERISTICS OF THE PRODUCTION PROCESS IN THE TEXTILE INDUSTRY 10 1. Basic concepts ........................... 10 2. Prospects of a radical change in the production processes of the textile industry 13 3i Classification of processes by type of fibre used 21 Chapter II. DIFFERENT WAYS OF TRANSFERRING KNOW-HOW IN THE TEXTILE INDUSTRY 26 A. BACKGROUND 26 1. The establishment of the textile industry in Latin America 26 2. Current trends 28 B. TRANSFER OF KNOW-HOW NEEDED TO ESTABLISH NEW MILLS 28 C. TRANSFER OF KNOW-HOW NEEDED FOR RE-STRUCTURING AND MODERNIZING OUT-OF-DATE FACTORIES 35 D. THE WAYS OF TRANSFERRING KNOW-HOW ON THE USE OF SPECIAL PROCESSES AND SYNTHETIC RAW MATERIALS 40 A. Use of - iV - Page 1. Use of synthetic raw materials .......... -
Textile Institute
NOVEMBER 1944 P 1 2 1 THE JOURNAL OF THE TEXTILE INSTITUTE THE BLEACHING OF JUTE FOR TEXTILE PURPOSES B y B . P . R i d g e and A . H . L i t t l e . SUMMARY Details are given of methods that have been found satisfactory for bleaching jute materials to different degrees without undue loss of weight or strength. For mild bleaching, treatment is suggested with cold or warm hypochlorite solutions that are maintained in an alkaline condition. Cold alkaline permanganate fol lowed by a bisulphite clearing process, and hot sodium chlorite under slightly acid conditions also give reasonable results. For better shades a hot peroxide bleach may be given after an alkaline hypochlorite treatment, but for uniformity it is best first to scour the material under mild conditions with a soda ash solution at 65° to 750 C., using about 7-5 per cent, of ash on the weight of jute, whilst still further improvement in shade is obtained if the scouring bath contains a small proportion of peroxide. Other methods that may be used are the ordinary peroxide bleach without previous hypochlorite treatment as normally used for cotton goods, or alternate steepings first in a dilute alkaline hypochlorite and then in a hot solution of sodium hydrosulphite or bisulphite. White or nearly white jute can be obtained only if substantially all the lignin is removed, when the wet strength is seriously reduced. Information is recorded on the bleaching of yarn in package form and on the processing of mixtures of jute with cotton, linen, wool and rayon. -
The Industrial Revolution - Making Cloth: the Start of the Industrial Revolution
The Industrial Revolution - Making Cloth: The Start of the Industrial Revolution The Industrial Revolution - Making Cloth: The Start of the Industrial Revolution by ReadWorks The Industrial Revolution got its start in the textile industry. Before the Industrial Revolution, making cloth was a very slow process. Cotton from cotton plants is puffy and full of seeds. First, the seeds had to be taken out, by hand. Next, the cotton had to be spun and stretched into thread, by hand. Finally, the thread was woven into cloth, by hand. Every step along the way required the full concentration of one person. Making cloth took a long time. In 1764, the process of turning cotton into cloth began to change. The three main steps stayed the same. But people began to use machines instead of doing everything manually. The machines did each step faster and faster. Some of the machines were huge. They couldn't fit into a person's home. The first factories were built to house machines and the workers needed to run them. Look at the timeline below. It describes the most important textile machines that were invented. Use it to answer the questions that follow. 1764: The spinning jenny was invented by James Hargreaves. This machine made it easier to make thread. 1769: Sir Richard Arkwright invented the water frame. Now weavers could keep up with all the thread that was being made. After the invention of the water frame, one weaver could weave the yarn from four spinners! The water frame was too big for homes. It only fit in factories. -
ARCHAEOLOGICAL REMAINS ALONG the MANCHESTER AIRPORT RELIEF ROAD Wessex 9 781911 137207 £5.00 Archaeology Acknowledgments
The construction of the Manchester Airport relief road provided an opportunity for archaeologists to Greater investigate the historic landscape on the southern Manchester’s fringes of Greater Manchester. The earliest remains Past Revealed were a Middle Bronze Age (1600–1100 BC) pit containing cremated human bone lying alongside an • 26 • enigmatic ring-shaped monument, found between Bramhall and Poynton. The majority of the discoveries, however, dated to the post-medieval and Industrial periods, and include a former corn mill, a turnpike toll house and a possible medieval moated manor, all near Norbury. This well-illustrated booklet, generously funded by roadbuilders Carillion Morgan Sindall Joint Venture, presents a summary of the most significant sites and their broader context in the local landscape. It also provides an insight into archaeological methods, along with the experiences of some of those who carried out the fieldwork. © Wessex Archaeology 2019 ISBN 978-1-911137-20-7 Front: Yard area near site of Norbury toll house Life on MARR Rear: Post-medieval land drainage ditches near Moss Nook Rear: The Bramhall ring ditch ARCHAEOLOGICAL REMAINS ALONG THE MANCHESTER AIRPORT RELIEF ROAD wessex 9 781911 137207 £5.00 archaeology Acknowledgments Wessex Archaeology would like to thank Carillion Morgan Sindall Joint Venture, for commissioning the archaeological investigations, particularly Steve Atkinson, Rory Daines, Molly Guirdham and Irish Sea Stuart Williams for their communication and assistance throughout. Special thanks are due to Norman Redhead, Heritage Management Director (Archaeology) at GMAAS, who advised upon and monitored the archaeological response to the road construction on behalf of Stockport Greater Manchester Metropolitan Borough Council and Manchester City Council, and also to Mark Leah who carried out the same role at Cheshire East Council. -
DEPARTMENT of TEXTILE TECHNOLOGY Vision
DEPARTMENT OF TEXTILE TECHNOLOGY Vision: The Vision of the Department of Textile Technology, Anna University is to be recognized as a leader in textile and apparel technology education, research and application of knowledge and skills to benefit the society. Mission: The mission of the Department of Textile Technology, Anna University is To deliver the highest quality textile and apparel technologists with societal values. To carryout cutting-edge research and develop innovative technology for the benefit of society at national and international level. To inculcate a sense of highest ethical and professional standards among the students. ANNA UNIVERSITY, CHENNAI: 600 025 UNIVERSITY DEPARTMENTS M.TECH. TEXTILE TECHNOLOGY REGULATIONS – 2019 CHOICE BASED CREDIT SYSTEM 1. PROGRAM EDUCATIONAL OBJECTIVES(PEOs): Master of Textile Technology curriculum is designed to prepare the graduates to 1. Have attitude and knowledge for the successful professional and technical career 2. Design and conduct experiments and interpret the results, Design new process and product for textile industry 3. Manage research and development activities in textile industry and research organizations and 4. Enhance their skills for managing textile manufacturing industry 2. PROGRAM OUTCOMES(POs): The Textile Technology Post Graduates will have the ability to 1. Apply the knowledge gained through the post graduate programme to effectively teach the students at the undergraduate level 2. Effectively carryout fundamental and applied research 3. Develop new process or product at the textile industry 4. Develop new process or product at the textile research organizations 5. Apply the knowledge of textile technology to effectively manage textile industry 6. Effectively function as individual or as a part of a team to accomplish a stated goal. -
Britannia Rules the Waves
Working Paper No. 66/01 Britannia Ruled the Waves Timothy Leunig © Timothy Leunig Department of Economic History London School of Economics October 2001 Department of Economic History London School of Economics Houghton Street London, WC2A 2AE Tel: +44 (0)20 7955 7857 Fax: +44 (0)20 7955 7730 Additional copies of this working paper are available at a cost of £2.50. Cheques should be made payable to ‘Department of Economic History, LSE’ and sent to the Economic History Department Secretary. LSE, Houghton Street, London WC2A 2AE, UK. 2 Britannia Ruled the Waves1 Timothy Leunig2 Abstract This paper uses new micro-level US data to re-examine productivity leadership in cotton spinning c. 1900. We find that output aggregation problems make the Census unreliable in this industry, and that Lancashire, not New England was the productivity leader for almost every type of yarn. This is true both for the operation of a given machinery type, and when comparing machinery typical in each country. Higher capital and labour productivity rates imply that Lancashire’s combination of a more favourable climate, external economies of scale and more experienced workers dominated the advantages that New England firms derived from greater scale. Keywords COTTON ¦ ECONOMIES OF SCALE ¦ LANCASHIRE ¦ MULES ¦ NEW ENGLAND ¦ PRODUCTIVITY ¦ RINGS ¦ SPINNING 1 This paper is based on work in my doctoral dissertation. I thank my supervisor, James Foreman-Peck for his advice. An earlier version of this paper was given at the 1996 Cliometrics meeting. I would like to thank participants there, especially Steve Broadberry and Greg Clark. I thank the Royal Economic Society, Nuffield College Oxford, and Oxford University’s Sir John Hicks Fund for financial support. -
Samuel Crompton (3 Dec 1753 - 26 Jun 1827)
Samuel Crompton (3 Dec 1753 - 26 Jun 1827) British inventor who contributed to the Industrial Revolution with his invention of the “spinning mule” to produce continuous, strong, fine yarn. (source) Samuel Crompton Crompton was born at Firwood Fold, near Bolton, England. He was 15 when he started working on a spinning jenny in the Hall'i'th'Wood1 mill, Bolton. The yarn then in use was soft, and broke frequently. He realized that an improved machine was needed. By 1774, at age 21, he began working on that project in his spare time, and continued for five years. He later wrote2 that he was in a “continual endeavour to realise a more perfect principle of spinning; and though often baffled, I as often renewed the attempt, and at length succeeded to my utmost desire, at the expense of every shilling I had in the world.” During this time, he supplemented his income from weaving, when the Bolton theatre was open, by earning eighteen pence a night as a violinist in the orchestra. Samuel Crompton (source) Drawing of the Spinning Mule Because of the machine-wrecking Luddites active during the Industrial Revolution, he worked as best he (1823) (source) could in secret while developing the machine. At one point, he kept it hidden in the roof of his house. (Luddites were handloom workers who violently rejected the changes produced by the Industrial Revolution, and destroyed mechanised looms, in their attempt to protect their livelihoods during harsh economic conditions.) In 1779, his invention was finished - the spinning mule. It was able to spin a continuous, strong, fine yarn by combining ideas from the spinning jenny of Richard Arkwright and the water frame of James Hargreaves. -
Lecture Outline Processing Fiber Into Yarn I
LECTURE OUTLINE PROCESSING FIBER INTO YARN I. The History of Fiber Processing 11. Material Opening and Cleaning A. Preparing the bale lay-down 1. Selection of bales 2. Bale arrangement for blending 3. Removal of bands and bagging B. Opening and cleaning equipment 1. Weigh-pan feeders 2. Magnetic and electronic cleaners 3. Dust removers 4. Beater type cleaners 5. Positive-fed saw-type cleaners 111. Carding A. Opening of fiber B. Cleaning as a hction C. Reducing or drafting D. Packaging of stock IV. Drawing A. Drafting and fiber orientation B. Blending and uniformity V. Combing A. Combing preparation 1. Drawing for Iapper 2. Lapping B. Principles of combing operation I. Feeding of laps 2. Nipping of fiber 3. Circular combing 4. Detaching 5. Top combing V. Combing (continued) C. Primary functions 1. Removal of short fiber (noils) 2. Removal of trash D. Secondary functions 1. Reducing and drafting 2. Blending and packaging VI. Roving A. Definition and description of machine B. Description of product C. Purpose of roving machine 1. Drafting 2. Twisting 3. Packaging a. laying b. winding c. building VII. Types of Spinning A. Intermittent spinning 1. Hand Spinning 2. Saxony Wheel-Spinning Jenny B. Continuous spinning 1. Cap spinning 2. Centrifugal spinning 3. Flyer spinning 4. Ring spinning a. definition and description of process 1. drafting of fibers 2. twisting of yarn 3. packagmg of yarn aa. laying bb. winding cc. package building b. other ring spinning factors 1. ring and traveler 2. speeds and rpms C. Open-end spinning 1. Definition and methods a. -
B.Tech Textile Technology –
Department of Textile Technology Vision Department of Textile Technology aspires to be a centre of excellence in textile education, manifesting excellence, inspiring confidence, and engaging society. Mission ➢ Develop industry relevant curriculum, infrastructure, innovative teaching methods and hands on training in textile education that enables students to be efficient professionals. ➢ Motivate Faculty to update their knowledge and skills through their higher education and providing opportunities to participate in short- term programme, workshops, conferences, seminars and specific industry based training.etc., ➢ Provide holistic student development by creating opportunities to participate in Inter-Intra college events, soft skills trainings, competitive exams training etc., to develop their technical and team building competencies for lifelong learning and to develop entrepreneurship skills. ➢ Undertake inter-disciplinary research and development/Consultancy in the field of Textile Technology to support the industry and society. 1 Signature of BOS chairman, TXT Programme Educational Objectives (PEO’s) PEO:1 Graduates of B.Tech Textile Technology programme will have increasing responsibilities/advancement in positions in Textile and related segments such as product development, production, technical services, quality assurance and marketing. PEO:2 Graduates of B.Tech Textile Technology programme will become successful entrepreneur / business partners in Textile and related field, by starting new ventures/expansion of existing family