Inkjet Printing of Conductive Inks with High Lateral Resolution on Omniphobic “R F Paper” for Paper- Based Electronics and MEMS
Total Page:16
File Type:pdf, Size:1020Kb
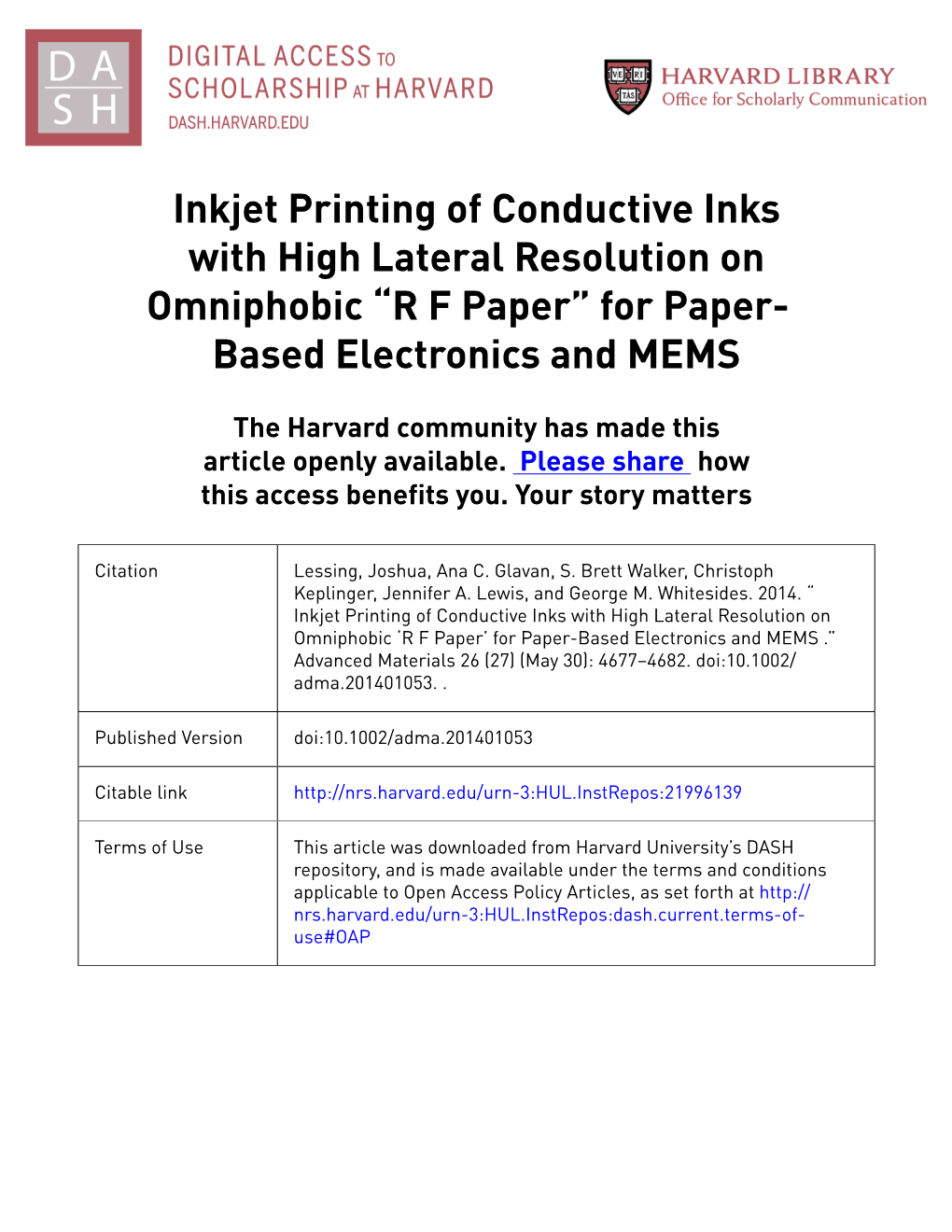
Load more
Recommended publications
-
Dry Film Photoresist Tips and Tricks
Updated October 2017 Hints and Tips For Use First a couple of notes What is Dry Film. Dry Film is a photo-resist, when strong UV light hits it, where the light hits, it hardens and this hardened form resists etching solutions. The film is comprised of three parts, the blue layer is in the middle, this is the polymer which hardens with UV, on each side of this polymer is a protective transparent film. How do you use it? In very brief summary, one protective layer (the inside of curl generally) is removed, the now uncovered polymer side is attached to the PCB, the PCB is exposed to UV through a 'mask' which has transparent traces to allow UV to harden the “”traces image , the remaining protective layer is removed and the PCB is developed in a solution of washing soda (Sodium Carbonate), then the PCB is etched. The rest of this document gives you all the steps, tips and tricks which I have learned in using Dry Film! Be sure to read it, save yourself lots of experimenting! Practice, Practice, Practice. I advise cutting some small squares of film a couple of cm squared and using these to get the hang of affixing it to a board and developing, use some moderately dense small (section of) artwork with the finest traces you want to do, with the narrowest spaces you want to do etc. You might want to practice 5 or 10 times before doing it for real. If you mess one up, just clean it off, and start again. -
Tensile Properties of Paper and Paperboard (Using Constant Rate of Elongation Apparatus) (Revision of T 494 Om-01)
WI 050808.09 T 494 DRAFT NO. 2 DATE June 13, 2006 TAPPI WORKING GROUP CHAIRMAN D Muchorski SUBJECT CATEGORY Physical Properties RELATED METHODS See “Additional Information” CAUTION: This Test Method may include safety precautions which are believed to be appropriate at the time of publication of the method. The intent of these is to alert the user of the method to safety issues related to such use. The user is responsible for determining that the safety precautions are complete and are appropriate to their use of the method, and for ensuring that suitable safety practices have not changed since publication of the method. This method may require the use, disposal, or both, of chemicals which may present serious health hazards to humans. Procedures for the handling of such substances are set forth on Material Safety Data Sheets which must be developed by all manufacturers and importers of potentially hazardous chemicals and maintained by all distributors of potentially hazardous chemicals. Prior to the use of this method, the user must determine whether any of the chemicals to be used or disposed of are potentially hazardous and, if so, must follow strictly the procedures specified by both the manufacturer, as well as local, state, and federal authorities for safe use and disposal of these chemicals. Tensile properties of paper and paperboard (using constant rate of elongation apparatus) (Revision of T 494 om-01) (Underlines indicated changes/corrections since last draft) 1. Scope 1.1 This test method describes the procedure, using constant-rate-of-elongation equipment, for determining four tensile breaking properties of paper and paperboard: tensile strength, stretch, tensile energy absorption, and tensile stiffness. -
How to Make a Collage 4 Free Mixed Media Collage Techniques Presented by Cloth Paper Scissors®
how to make a collage 4 free mixed media collage techniques presented by cloth paper scissors® 1 3 4 2 collage to order: objects of my desire: 1 create with words 3 making sewn paper SUSAN BLACK collage collections JENNY COCHRAN LEE the elements of collage: 2 putting it all together reverse collage painting: NICOLE PAISLEY MARTENSEN 4 a bright spot on a winter day HOLLY CHRISTINE MOODY In “Objects of My Desire: Making Sewn Paper Collage Collections,” Jenny Cochran Lee explores how to How to Make a Collage: turn paper scraps into collage art 4 Free Mixed Media treasures. Collage Techniques presented by Finally, Holly Christine Moody Cloth Paper Scissors® offers an easy collage project that ONLINE EDITOR Cate Prato will help you whittle down your decorative paper stash in a fun CREATIVE SERVICES way. In “Reverse Collage Painting,” DIVISION ART DIRECTOR Larissa Davis PHOTOGRAPHER Larry Stein you make a paper collage on a substrate, apply gel medium, Projects and information are for inspiration and personal use only. Interweave Press is not responsible hat is collage art? A and then paint over it. The magic for any liability arising from errors, omissions, or whole lot of fun! At happens when you swipe away mistakes contained in this eBook, and readers should proceed cautiously, especially with respect to technical the most basic level, some of the paint to reveal the information. wyou can make a collage with paper, collage designs below. © F+W Media, Inc. All rights reserved. F+W Media glue, and a substrate like a canvas grants permission for any or all pages in this eBook to With How to Make a Collage: 4 Free or watercolor paper. -
Conservation of Coated and Specialty Papers
RELACT HISTORY, TECHNOLOGY, AND TREATMENT OF SPECIALTY PAPERS FOUND IN ARCHIVES, LIBRARIES AND MUSEUMS: TRACING AND PIGMENT-COATED PAPERS By Dianne van der Reyden (Revised from the following publications: Pigment-coated papers I & II: history and technology / van der Reyden, Dianne; Mosier, Erika; Baker, Mary , In: Triennial meeting (10th), Washington, DC, 22-27 August 1993: preprints / Paris: ICOM , 1993, and Effects of aging and solvent treatments on some properties of contemporary tracing papers / van der Reyden, Dianne; Hofmann, Christa; Baker, Mary, In: Journal of the American Institute for Conservation, 1993) ABSTRACT Museums, libraries, and archives contain large collections of pigment-coated and tracing papers. These papers are produced by specially formulated compositions and manufacturing procedures that make them particularly vulnerable to damage as well as reactive to solvents used in conservation treatments. In order to evaluate the effects of solvents on such papers, several research projects were designed to consider the variables of paper composition, properties, and aging, as well as type of solvent and technique of solvent application. This paper summarizes findings for materials characterization, degradative effects of aging, and some effects of solvents used for stain reduction, and humidification and flattening, of pigment-coated and modern tracing papers. Pigment-coated papers have been used, virtually since the beginning of papermaking history, for their special properties of gloss and brightness. These properties, however, may render coated papers more susceptible to certain types of damage (surface marring, embedded grime, and stains) and more reactive to certain conservation treatments. Several research projects have been undertaken to characterize paper coating compositions (by SEM/EDS and FTIR) and appearance properties (by SEM imaging of surface structure and quantitative measurements of color and gloss) in order to evaluate changes that might occur following application of solvents used in conservation treatments. -
Transferring Computer Designs to Materials
FOCUS ON TEXTILES Many students now have easy access to design is drawn with a resistant material such computer drawing packages and having drawn as wax and then sprayed or painted with paint a design on computer, they need to find a or dye (see Figures 2a and 2b). suitable method for transferring their design to For more complex patterns, the designs can be the material. (I use the term 'material' because copied in encaustic art. The design is drawn although students will often be transferring with wax crayons on a heat-retaining card. The designs to textiles, materials such as wood or use of heat can allow the pattern to be altered paper may be the destination for the design.) and the finished design can be left to coolon The problem is the same as it has always been the card or be transferred to fabric using a hot with designs that are drawn on paper, but iron (see Figure 3). because of the modern attitudes to designing and making, teachers need to be much more aware of the wide range of methods. • Carbon paper Transferring With this method, carbon paper is laid between computer One of the first points students need to be a print-out of your design and the fabric and aware of is that when transfer methods result in the outline is traced using a stylus. This method designs to a mirror image of the design, it is important to is suitable for light coloured textiles, wood and materials have a print-out which is a mirror image of the plastic and is suitable for activities such as design. -
Hints and Tips for Use There Are Many Methods for Attaching the Film
Hints and Tips For Use There are many methods for attaching the film to the blank board, Google is your friend. A good attachment without bubbles and wrinkles is the key to success. The film needs moderate heat and pressure to properly adhere enough to resist. Presented in this document are methods for application using a Laminator, and using a Clothes Iron. The Laminator method is very reliable, but requires a little preparation in making a “”carrier from some cardboard. The Clothes Iron method is also very reliable once you've done it a couple times to “”tune in your iron's temperature and your technique - it's far FAR easier than toner transfer! This method however is limited by the size of your iron of course. Laminator Method This is the recommended method, if you have a laminator. Step 1, Clean the PCB surface thoroughly, this is my way... - Sand with fine sand paper. - Wipe with solvent (acetone). - Dunk/wipe in tarnish remover (“ Ceraclen Silver Dip” from supermarkets works well http://www.ceraclen.co.nz/products.aspx ) - Dry and ensure surface is dust free. Step 2, Laminate the film: Place PCB on a carrier and attach a piece film cut to about 5mm larger on each side than you need to the top end-stop, with “”tail attached to film (see next page for diagrams of my carrier setup). It is better to cut 5mm larger on each side than you need, but if you do use right up to the cut edge of a piece of film have a careful look at the edge, sometimes there is a visible “”border of lighter colouring (more transparent) running down an edge (as it comes off the roll), if visibly different this border should be avoided as it's performance may be degraded a bit. -
1965 – Postage
1965 POSTAGE DUE LABELS Issued 17th June, 1965 The bulletin issued by the Ministry of Post in early 1965 advised of the issue of three sets stamps (ITU Centenary, Water Conservation and Postage Due Labels). The bulletin advised that the labels would be issued on 17th June 1965 and would continue in use for an indefinite period. “These are not true postage stamps, as they are used only in bringing to account surcharges arising from deficient postage, etc.”1 The design of the labels was the same as that used for the Federal Postage Due Labels issued in 1961, save that the country name was changed from “Rhodesia & Nyasaland” to “Rhodesia”. The Federal Postage Due labels could be said to be the first stamps printed in the country. In 2001 Cecil Russell exchanged correspondence with Eugene William “Bill” Jones in New Zealand. Bill’s letter of 19th December 2001, confirmed that he was employed by the Government of Southern Rhodesia in the Department of Printing & Stationery. “I was a draughtsman with little or no artistic talent, and when told to design a stamp chose something simple to draw like a post- horn or the garter. The two designs were roughed out in pencil in tracing paper and were handed to my boss and I have no idea how they were selected. Had the selection been left to myself I would have chosen the garter style. There was no competition, and as far as I was concerned it was just another job.”2 Bill took with him two rough sketches of the designs he had produced in tracing paper when he returned to New Zealand. -
Ink Transfers on Clay by Doug Gray
Ceramic Arts Daily Lesson Plan Ink Transfers on Clay by Doug Gray Goals pensive inkjet printer. If you prefer to work without • Learn to roll out slabs of clay to create tiles. a computer, see sidebar (page 4). • Draw or create simple line drawings using water The two main advantages to using this process soluble ink or using Adobe Photoshop to alter are that the image is water based and can be eas- existing images to make self portraits. ily removed with a damp sponge and repositioned, • Learn to transfer designs to soft clay tiles using or you can just burn it off in the bisque fire if you inkjet printouts of line drawings or simple im- don’t like it. Second, any surface design technique ages. Trace these lines to create a relief outline. works in combination with this transfer process— Put multiple tiles together for larger images. carving, slip trailing, water etching, underglazes, • Add color to the bisqued tile using underglazes. terra sig, glazes, etc. Background One significant pitfall is that the ink can’t with- Years ago, in an attempt to incorporate digital pho- stand the heat of firing, so this technique is basi- tography into my clay work, I began experimenting cally just a design transfer. This is where the other with image transfer processes. I began working with surface design processes come into play. In this Xerox transfers and decals with some degree of example, I used a carving process. Try the surface success. But one day I accidentally stumbled across design process you currently use and enjoy. -
*AFA-Front Matterfnl PDF.Mech
Gather Your Supplies and Materials Once you have an idea of your theme and color scheme, you’re ready to gather supplies and materials. One of the great things about scrapbooking is that it doesn’t take a lot of money! Here are the items you will need: • A photo album or scrapbook; if you’re creating a handmade album, make sure that you use acid-free paper • Pre-selected photographs for at least one or two pages, to help you get started • Decorative papers • Sharp scissors – to trim photos and cut out other paper designs and shapes • Adhesives – removable tape, acid-free and photo-safe glue stick, liquid glue, and photo corners • Acid-free pens and markers – with permanent, fade-proof, waterproof ink; make sure that you use pens that clearly state they can be used for archival scrapbooking purposes • pH testing pen – to test paper for acid content • Pencil and kneaded eraser – for marking ARCHIVAL IMPORTANCE and erasing layouts While scrapbooking is primarily fun, you also want to make • Folders or acid-free sheet protectors – for sure that your family’s precious photographs and keep- organizing groupings and protecting pages sakes will last for generations to come. Use only acid-free, • (Optional) Craft or utility knife with blades, archival-quality products and apply a lot of TLC (Tender Loving Care)! Look in our Resources section for a descrip- a steel ruler with a cork bottom, and a tive list of archival products and where to find them. self-healing cutting mat – for paper and mat cutting (Note: Keep the knife away from children – it’s razor sharp!) 14 Although they are not necessary, part of the fun of scrapbooking is to use some of the handy gadgets available at most hobby and scrapbook shops. -
Transferring I Strongly Suggest Drawing on a Good Quality Tracing
Transferring I strongly suggest drawing on a good quality tracing paper rather than directly on the watercolor paper. Watercolor paper does not take erasing well, the surface is easily abraded. The eraser lifts the fibers and some of the sizing, changing the texture of the surface dramatically. Paint will not flow in the usual manner over the abraded surface, settle quicker and more deeply into the paper wicking out making tidy edges very difficult to create. When drawing on tracing paper composition does not interfere with the drawing process, that comes when the tracing is placed on the watercolor paper, an image can be resized, even be reversed, small angle adjustments are easily made. Once the image is drawn to your satisfaction, be sure the drawing is understandable. Imagine the drawing will be passed on to another artist, that artist should be able to transfer your image with complete understanding of every line and nuance of detail. Redraw any lines or areas that are not clear. Check, and re-check your drawing, a bad drawing never gets better when painted it just becomes a really bad painting. It is helpful to think of every stage your process to be complete in and of it itself, for instance if you go no further than this step – the drawing on tracing paper - would the image be complete, stand on its own, fully understood? I know the thought of transferring seems an utter waste of time, but think of it as another chance to check the drawing, go at the process with a peaceful heart, do it slowly, thoughtfully, and NEVER loose sight of what the image is. -
Transferring Your Pattern to Fabric
. Transferring your Pattern To Fabric This is one of the most commonly asked questions and there are lots of answers and methods How do you get the design from the paper to your fabric? The problem seems insurmountable. Well, unless you have a specially printed iron-on transfer then I’m not telling you it will be easy – but it will most definitely be worth it. There are many different ways of tackling this task and it seems that every stitcher has their own favourite way. What I’ll do here is describe some of the most popular methods I’ve heard of, plus how to make your design larger or smaller if you don’t have access to printer or photocopier … © Bustle & Sew 2012 www.bustleandsew.com Changing the size of your design This is easy to do if you have access to a photocopier or to a computer and printer. Many printed designs that need to be enlarged will advise the size of enlargement. But do remember, if you are increasing or decreasing the size of the design by more than the stated amount, the quantity of floss you require and also its thickness may change and indeed, you may need to use a different stitch to the one suggested. If you don’t have access to modern technology you might want to resort to the time honoured Grid Method: Draw a small grid with equal squares over a tracing or copy of your design. Then draw an extended diagonal line through the corners of the grid to create an enlarged rectangle or square with the same proportions. -
Surecolor T-Series User's Guide
SureColor T-Series User’s Guide Epson SureColor T-Series User’s Guide Copyrights and Trademarks Systems Incorporated in the United States and/or other countries. Copyrights and HP-GL/2® and HP RTL® are registered trademarks of Hewlett-Packard Trademarks Corporation. Android is a trademark of Google Inc. No part of this publication may be reproduced, stored in a retrieval system, or transmitted in any form or by any means, electronic, mechanical, photocopying, recording, or otherwise, without the prior written permission of Seiko Epson Corporation. The information General Notice: Other product names used herein are for identification contained herein is designed only for use with this Epson printer. Epson purposes only and may be trademarks of their respective owners. Epson is not responsible for any use of this information as applied to other disclaims any and all rights in those marks. printers. © 2016 Epson America, Inc. Neither Seiko Epson Corporation nor its affiliates shall be liable to the 2/16 purchaser of this product or third parties for damages, losses, costs, or expenses incurred by the purchaser or third parties as a result of CPD-41582R1 accident, misuse, or abuse of this product or unauthorized modifications, repairs, or alterations to this product, or (excluding the U.S.) failure to strictly comply with Seiko Epson Corporation’s operating and maintenance instructions. Seiko Epson Corporation shall not be liable for any damages or problems arising from the use of any options or any consumable products other than those designated as Original Epson Products or Epson Approved Products by Seiko Epson Corporation.