A Review of Hybrid Rockets: Present Status and Future Potential
Total Page:16
File Type:pdf, Size:1020Kb
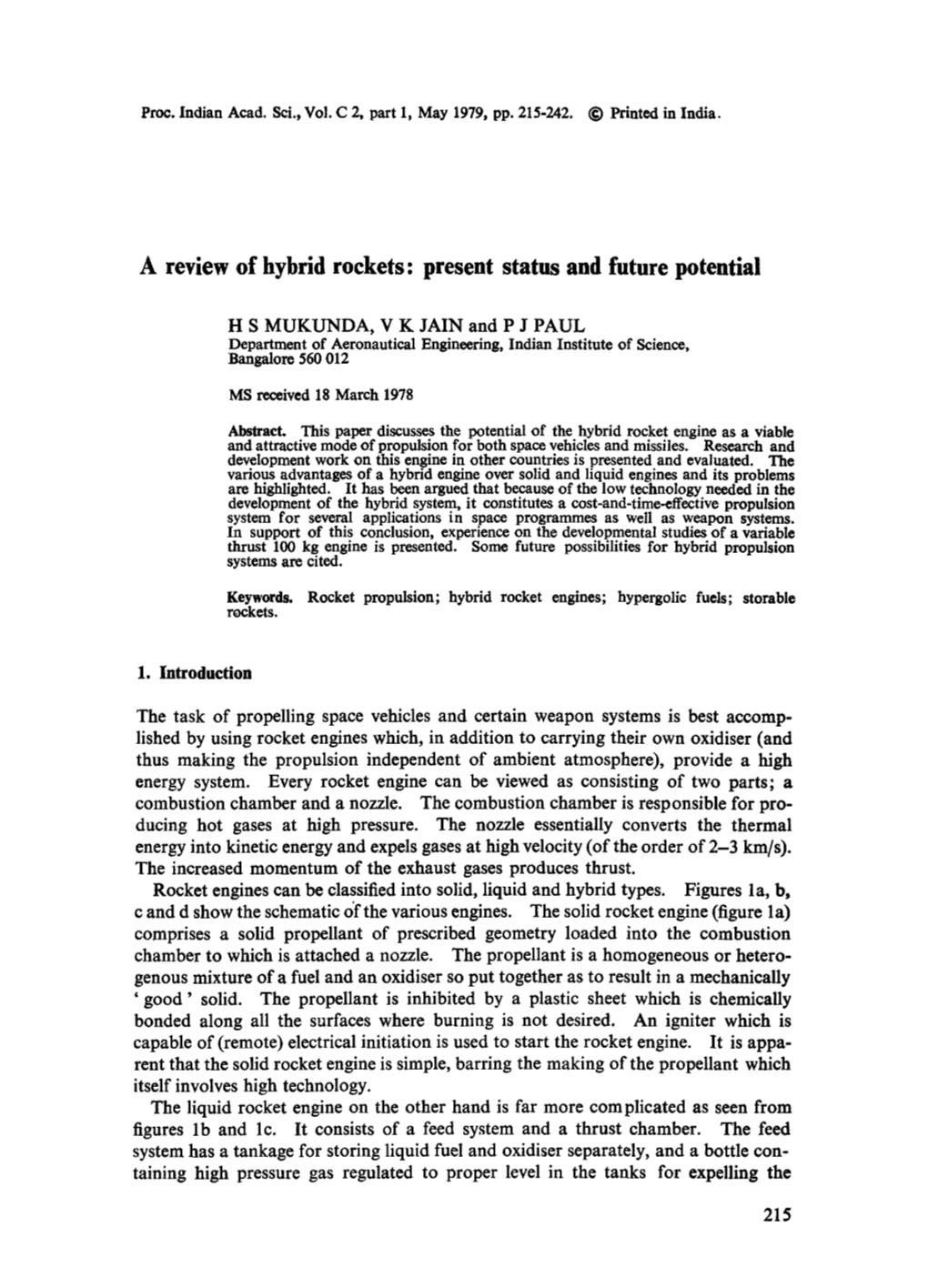
Load more
Recommended publications
-
Investigation of Condensed and Early Stage Gas Phase Hypergolic Reactions Jacob Daniel Dennis Purdue University
Purdue University Purdue e-Pubs Open Access Dissertations Theses and Dissertations Fall 2014 Investigation of condensed and early stage gas phase hypergolic reactions Jacob Daniel Dennis Purdue University Follow this and additional works at: https://docs.lib.purdue.edu/open_access_dissertations Part of the Propulsion and Power Commons Recommended Citation Dennis, Jacob Daniel, "Investigation of condensed and early stage gas phase hypergolic reactions" (2014). Open Access Dissertations. 256. https://docs.lib.purdue.edu/open_access_dissertations/256 This document has been made available through Purdue e-Pubs, a service of the Purdue University Libraries. Please contact [email protected] for additional information. i INVESTIGATION OF CONDENSED AND EARLY STAGE GAS PHASE HYPERGOLIC REACTIONS A Dissertation Submitted to the Faculty of Purdue University by Jacob Daniel Dennis In Partial Fulfillment of the Requirements for the Degree of Doctor of Philosophy December 2014 Purdue University West Lafayette, Indiana ii To my parents, Jay and Susan Dennis, who have always pushed me to be the person they know I am capable of being. Also to my wife, Claresta Dennis, who not only tolerated me but suffered along with me throughout graduate school. I love you and am so proud of you! iii ACKNOWLEDGEMENTS I would like to express my sincere gratitude to my advisor, Dr. Timothée Pourpoint, for guiding me over the past four years and helping me become the researcher that I am today. In addition I would like to thank the rest of my PhD Committee for the insight and guidance. I would also like to acknowledge the help provided by my fellow graduate students who spent time with me in the lab: Travis Kubal, Yair Solomon, Robb Janesheski, Jordan Forness, Jonathan Chrzanowski, Jared Willits, and Jason Gabl. -
Rocket Propulsion Fundamentals 2
https://ntrs.nasa.gov/search.jsp?R=20140002716 2019-08-29T14:36:45+00:00Z Liquid Propulsion Systems – Evolution & Advancements Launch Vehicle Propulsion & Systems LPTC Liquid Propulsion Technical Committee Rick Ballard Liquid Engine Systems Lead SLS Liquid Engines Office NASA / MSFC All rights reserved. No part of this publication may be reproduced, distributed, or transmitted, unless for course participation and to a paid course student, in any form or by any means, or stored in a database or retrieval system, without the prior written permission of AIAA and/or course instructor. Contact the American Institute of Aeronautics and Astronautics, Professional Development Program, Suite 500, 1801 Alexander Bell Drive, Reston, VA 20191-4344 Modules 1. Rocket Propulsion Fundamentals 2. LRE Applications 3. Liquid Propellants 4. Engine Power Cycles 5. Engine Components Module 1: Rocket Propulsion TOPICS Fundamentals • Thrust • Specific Impulse • Mixture Ratio • Isp vs. MR • Density vs. Isp • Propellant Mass vs. Volume Warning: Contents deal with math, • Area Ratio physics and thermodynamics. Be afraid…be very afraid… Terms A Area a Acceleration F Force (thrust) g Gravity constant (32.2 ft/sec2) I Impulse m Mass P Pressure Subscripts t Time a Ambient T Temperature c Chamber e Exit V Velocity o Initial state r Reaction ∆ Delta / Difference s Stagnation sp Specific ε Area Ratio t Throat or Total γ Ratio of specific heats Thrust (1/3) Rocket thrust can be explained using Newton’s 2nd and 3rd laws of motion. 2nd Law: a force applied to a body is equal to the mass of the body and its acceleration in the direction of the force. -
Orbital Fueling Architectures Leveraging Commercial Launch Vehicles for More Affordable Human Exploration
ORBITAL FUELING ARCHITECTURES LEVERAGING COMMERCIAL LAUNCH VEHICLES FOR MORE AFFORDABLE HUMAN EXPLORATION by DANIEL J TIFFIN Submitted in partial fulfillment of the requirements for the degree of: Master of Science Department of Mechanical and Aerospace Engineering CASE WESTERN RESERVE UNIVERSITY January, 2020 CASE WESTERN RESERVE UNIVERSITY SCHOOL OF GRADUATE STUDIES We hereby approve the thesis of DANIEL JOSEPH TIFFIN Candidate for the degree of Master of Science*. Committee Chair Paul Barnhart, PhD Committee Member Sunniva Collins, PhD Committee Member Yasuhiro Kamotani, PhD Date of Defense 21 November, 2019 *We also certify that written approval has been obtained for any proprietary material contained therein. 2 Table of Contents List of Tables................................................................................................................... 5 List of Figures ................................................................................................................. 6 List of Abbreviations ....................................................................................................... 8 1. Introduction and Background.................................................................................. 14 1.1 Human Exploration Campaigns ....................................................................... 21 1.1.1. Previous Mars Architectures ..................................................................... 21 1.1.2. Latest Mars Architecture ......................................................................... -
Fuel and Oxidizer Feed Systems
Fuel and Oxidizer Feed Systems Zachary Hein, Den Donahou, Andrew Doornink, Mack Bailey, John Fieler 1 1 Design Selection Recap Fuel Selection Fuel: Ethanol C2H5OH -Potential Biofuel -Low mixture ratio with LOX -Good specific impulse -Easy to get Oxidizer: Liquid Oxygen LOX -Smaller tank needed (Compared to gaseous O2) -Can be pressurized -Lowest oxidizer mixture ratio -Provides Highest specific impulse 2 Design Selection Recap Thrust Chamber Thrust Chamber Selections ● Injector: Like Impinging Doublet ● Cooling System: Regenerative Cooling ● Thrust Chamber Material: Haynes 230 3 Design Selection Recap Thrust Chamber Thrust Chamber Selections ● Injector: Like Impinging Doublet ● Cooling System: Regenerative Cooling ● Thrust Chamber Material: Haynes 230 Huzel, Dieter, and David Huang. "Introduction." Modern Engineering for Design of Liquid-Propellant Rocket Engines. Vol. 147. Washington D.C.: AIAA, 1992. 7-22. Print. 4 Design Selection Recap Thrust Chamber Thrust Chamber Selections ● Injector: Like Impinging Doublet ● Cooling System: Regenerative Cooling ● Thrust Chamber Material: Haynes 230 Huzel, Dieter, and David Huang. "Introduction." Modern Engineering for Design of Liquid-Propellant Rocket Engines. Vol. 147. Washington D.C.: AIAA, 1992. 7-22. Print. http://www.k-makris.gr/RocketTechnology/ThrustChamber/Thrust_Chamber.htm 5 Design Selection Recap Thrust Chamber Thrust Chamber Selections ● Injector: Like Impinging Doublet ● Cooling System: Regenerative Cooling ● Thrust Chamber Material: Haynes 230 Huzel, Dieter, and David Huang. "Introduction." Modern Engineering for Design of Liquid-Propellant Rocket Engines. Vol. 147. Washington D.C.: AIAA, 1992. 7-22. Print. http://www.k-makris.gr/RocketTechnology/ThrustChamber/Thrust_Chamber.htm http://www.alibaba.com/product-detail/haynes-seamless-pipe_1715659362.html 6 Turbo Pump Basics Turbo Pumps provide pressurization to gaseous fuel components to required pressures and mixture ratios. -
Experimental Study of the Combustion Efficiency in Multi-Element Gas
energies Article Experimental Study of the Combustion Efficiency in Multi-Element Gas-Centered Swirl Coaxial Injectors Seongphil Woo 1,* , Jungho Lee 1,2, Yeoungmin Han 2 and Youngbin Yoon 1,3 1 Department of Aerospace Engineering, Seoul National University, Seoul 08826, Korea; [email protected] (J.L.); [email protected] (Y.Y.) 2 Korea Aerospace Research Institute, Daejeon 34133, Korea; [email protected] 3 Institute of Advanced Aerospace Technology, Seoul National University, Seoul 08826, Korea * Correspondence: [email protected] Received: 27 October 2020; Accepted: 16 November 2020; Published: 19 November 2020 Abstract: The effects of the momentum-flux ratio of propellant upon the combustion efficiency of a gas-centered-swirl-coaxial (GCSC) injector used in the combustion chamber of a full-scale 9-tonf staged-combustion-cycle engine were studied experimentally. In the combustion experiment, liquid oxygen was used as an oxidizer, and kerosene was used as fuel. The liquid oxygen and kerosene burned in the preburner drive the turbine of the turbopump under the oxidizer-rich hot-gas condition before flowing into the GCSC injector of the combustion chamber. The oxidizer-rich hot gas is mixed with liquid kerosene passed through combustion chamber’s cooling channel at the injector outlet. This mixture has a dimensionless momentum-flux ratio that depends upon the dispensing speed of the two fluids. Combustion tests were performed under varying mixture ratios and combustion pressures for different injector shapes and numbers of injectors, and the characteristic velocities and performance efficiencies of the combustion were compared. It was found that, for 61 gas-centered swirl-coaxial injectors, as the moment flux ratio increased from 9 to 23, the combustion-characteristic velocity increased linearly and the performance efficiency increased from 0.904 to 0.938. -
Materials for Liquid Propulsion Systems
CHAPTER 12 Materials for Liquid Propulsion Systems John A. Halchak Consultant, Los Angeles, California James L. Cannon NASA Marshall Space Flight Center, Huntsville, Alabama Corey Brown Aerojet-Rocketdyne, West Palm Beach, Florida 12.1 Introduction Earth to orbit launch vehicles are propelled by rocket engines and motors, both liquid and solid. This chapter will discuss liquid engines. The heart of a launch vehicle is its engine. The remainder of the vehicle (with the notable exceptions of the payload and guidance system) is an aero structure to support the propellant tanks which provide the fuel and oxidizer to feed the engine or engines. The basic principle behind a rocket engine is straightforward. The engine is a means to convert potential thermochemical energy of one or more propellants into exhaust jet kinetic energy. Fuel and oxidizer are burned in a combustion chamber where they create hot gases under high pressure. These hot gases are allowed to expand through a nozzle. The molecules of hot gas are first constricted by the throat of the nozzle (de-Laval nozzle) which forces them to accelerate; then as the nozzle flares outwards, they expand and further accelerate. It is the mass of the combustion gases times their velocity, reacting against the walls of the combustion chamber and nozzle, which produce thrust according to Newton’s third law: for every action there is an equal and opposite reaction. [1] Solid rocket motors are cheaper to manufacture and offer good values for their cost. Liquid propellant engines offer higher performance, that is, they deliver greater thrust per unit weight of propellant burned. -
Advances in Hypergolic Propellants: Ignition, Hydrazine, and Hydrogen Peroxide Research
Hindawi Publishing Corporation Advances in Aerospace Engineering Volume 2014, Article ID 729313, 9 pages http://dx.doi.org/10.1155/2014/729313 Review Article Advances in Hypergolic Propellants: Ignition, Hydrazine, and Hydrogen Peroxide Research Stephen M. Davis and Nadir Yilmaz Department of Mechanical Engineering, New Mexico Institute of Mining and Technology, Socorro, NM 87801, USA Correspondence should be addressed to Nadir Yilmaz; [email protected] Received 6 June 2014; Accepted 27 August 2014; Published 15 September 2014 Academic Editor: Kazhikathra Kailasanath Copyright © 2014 S. M. Davis and N. Yilmaz. This is an open access article distributed under the Creative Commons Attribution License, which permits unrestricted use, distribution, and reproduction in any medium, provided the original work is properly cited. A review of the literature pertaining to hypergolic fuel systems, particularly using hydrazine or its derivatives and hydrogen peroxide, has been conducted. It has been shown that a large effort has been made towards minimizing the risks involved with the use of a toxic propellant such as the hydrazine. Substitution of hydrazines for nontoxic propellant formulations such as the use of highpurityhydrogenperoxidewithvarioustypesoffuelsisoneofthemajorareasofstudyforfuturehypergolicpropellants.Aseries of criteria for future hypergolic propellants has been recommended, including low toxicity, wide temperature range applicability, short ignition delay, high specific impulse or density specific impulse, and storability at room temperature. 1. Introduction the onset of vaporization and ignition is utilized as defined in [3, 4]. In [5, 6] these delay times are used, in part, to In typical combustion systems an ignition source such as a describe the preignition behavior of hypergolic propellants. spark is needed to begin the combustion reaction [1]. -
Solid Amine-Boranes As High Performance Hypergolic Hybrid Rocket Fuels Mark A
Purdue University Purdue e-Pubs Open Access Dissertations Theses and Dissertations Fall 2014 Solid amine-boranes as high performance hypergolic hybrid rocket fuels Mark A. Pfeil Purdue University Follow this and additional works at: https://docs.lib.purdue.edu/open_access_dissertations Part of the Aerospace Engineering Commons Recommended Citation Pfeil, Mark A., "Solid amine-boranes as high performance hypergolic hybrid rocket fuels" (2014). Open Access Dissertations. 347. https://docs.lib.purdue.edu/open_access_dissertations/347 This document has been made available through Purdue e-Pubs, a service of the Purdue University Libraries. Please contact [email protected] for additional information. PURDUE UNIVERSITY GRADUATE SCHOOL Thesis/Dissertation Acceptance . . To the best of my knowledge and as understood by the student in the Thesis/Dissertation Agreement, Publication Delay, and Certification/Disclaimer (Graduate School Form 32), this thesis/dissertation adheres to the provisions of Purdue University’s “Policy on Integrity in Research” and the use of copyrighted material. i SOLID AMINE-BORANES AS HIGH PERFORMANCE HYPERGOLIC HYBRID ROCKET FUELS A Dissertation Submitted to the Faculty of Purdue University by Mark A. Pfeil In Partial Fulfillment of the Requirements for the Degree of Doctor of Philosophy i December 2014 Purdue University West Lafayette, Indiana ii To my dear children. ii iii ACKNOWLEDGEMENTS I would first like to thank my advisors Professor Stephen Heister and Professor Steven Son. I am forever thankful for their willingness to take me on and spend time and effort to help me develop professionally. I very much enjoy the rocket/energetics field, and because of their efforts, I will be able to enjoy a long and fruitful career in this area. -
Astrotech.Pdf
1-1 1-2 1-3 1-4 1-5 1-6 1-7 1-8 1-9 1-10 1.0 INTRODUCTION This report has been jointly prepared by the Office of Commercial Space Transportation (OCST) of the Department of Transportation (DOT) and the U.S. Environmental Protection Agency (EPA). This joint effort provides an evaluation of the buildings, equipment, operations and procedures employed at a commercial payload processing facility owned and operated by Astrotech Space Operations (Astrotech), Limited Partnership, in Titusville, Florida. Astrotech's corporate management gave its full cooperation to the evaluation. This report provides an overview of the operations, procedures and methods employed by Astrotech to protect public health and safety, the environment, and public and private property in the Titusville area and presents a summary of the OCST/EPA evaluation team's findings regarding operating procedures, safety policies, and emergency planning and preparedness. However, the safety evaluation team did not examine operations from the standpoint of worker safety, which is regulated by the Occupational Health and Safety Administration (OSHA), nor did they perform a detailed analysis of transportation operations, which are regulated by the Research and Special Programs Administration (RSPA) of DOT. This report can also serve as a general model and guide for the evaluation of similar issues at other existing or proposed facilities that would support the commercial space launch industry. Payloads (also called spacecraft) are satellites that are launched into space to be used in communications systems, for remote sensing, in weather systems, for planetary exploration and as scientific experiments. Before launch on an expendable launch vehicle (ELV) like the Titan, Delta, or Atlas, or on the Space Shuttle, a payload must be prepared for its mission. -
Self-Igniting Fuel-Oxidizer Systems and Hybrid Rockets
Journal of Scientific & Industrial Research Vol. 62, April 2003, pp 293-3 10 Self-igniting Fuel-oxidizer Systems and Hybrid Rockets S R Jain Department of Aerospace Engineering, Indian Institute of Science, Bangalore 560 012 Fuel-oxidizer combinations capable of self-igniting simply on coming into mutual contact have been extensively used in bi-liquid rockets. In hybrid (solid fuel-liquid oxidizer) rockets too the self-igniting (hypergolic) propellant could be suited ideally. The relative non-existence of the hybrid rockets has been partly because of the paucity of suitable hypergolic solid fuels. The development of such fuelsis hampered because of the lack of understanding of the chemical reactions occurring between the fuel and the oxidizer leading to ignition. The chemistry of these highly exothermic reactions occurring in sub milliseconds in the pre-ignition stage is being studied for the past several years, in an effort to evolve suitable self-igniting systems. A major aspect of this work relates to,the solid N-N-bonded derivatives of hydrazines, which have been conceived as self-igniting fuels fo r the first time. Many of these compounds ignite readily, with short ignition delays on coming into contact with liquid oxidizers, like HN03 and N204. Polymeric resins having N-N bonds and reactive end-groups have been evolved to serve as fuel-binders for self-igniting compositions. This review narrates briefly the main highlights of the work carried out on hypergolic systems. A report Oil the hybrid rockets and their current status is also included. Introduction propellant rockets based on kerosene or 'alcohol Combustion of a fuel-oxidizer combination has liquid oxygen (LOX), e.g., the fuel and oxidizer are • been the main source of energy world over. -
Feasibility Study for Multiply Reusable Space Launch System
Feasibility Study For Multiply Reusable Space Launch System. Mikhail V. Shubov University of MA Lowell One University Ave, Lowell, MA 01854 E-mail: [email protected] Contents 1 Introduction 3 2 State of Art and Proposed Orbital Delivery Systems 5 2.1 HistoricalLaunchCosts. ..... 5 2.2 LaunchCostReduction . .. .. .. .. .. .. .. ... 6 2.3 SingleStagetoOrbit(SSTO)Concept . ....... 7 2.4 Non-RocketSpaceLaunch . ... 7 3 Multiply Reusable Launch System – Purpose and Concept 9 3.1 EarlyStagesofSolarSystemColonization . .......... 9 3.2 The Concept of Multiply Reusable Launch System Consistingof MPDS and MPTO 10 4 Rocket Motion and Propulsion 11 4.1 RocketFlightPhysics.. .. .. .. .. .. .. .. .... 11 4.1.1 RocketMotion ................................ 12 4.1.2 Lossesof v ................................. 15 △ 4.2 LiquidRocketEngines ............................. ... 16 4.2.1 Enginespecifications . .. 16 4.2.2 Combustionchambertemperature . .... 17 4.3 LiquidRocketFuelsandOxidizers . ....... 18 arXiv:2107.13513v1 [physics.soc-ph] 19 Apr 2021 4.3.1 CryogenicPropellantforMPDSEngines . ..... 18 4.3.2 HypergolicPropellantforMPTOEngines . ...... 19 4.4 PropellantCost .................................. .. 21 4.4.1 MPDSPropellant–$188PerTonAverage. .... 21 4.4.2 MPTOPropellant–$2,000PerTonAverage . .... 23 1 4.4.3 OrbitalLaunchFuelBill . .. 24 5 Rocket Parameters and Performance 25 5.1 MidpointDeliverySystem(MPDS) . ..... 25 5.1.1 MainparametersofMPDSstages . .. 26 5.1.2 PerformanceandtimetableofMPDSstages . ...... 27 5.2 MidpointtoOrbitDeliverySystem(MPTO) -
A Summary of NASA and USAF Hypergolic Propellant Related Spills and Fires
https://ntrs.nasa.gov/search.jsp?R=20100038321 2019-08-30T12:26:05+00:00Z A Summary of NASA and USAF Hypergolic Propellant Related Spills and Fires B. Nufer System Engineer NASA Kennedy Space Center, Engineering Directorate, Fluids Division, Hypergolic and Hydraulic Systems Branch Mail Stop: NE-F5 Kennedy Space Center, FL 32899 Several unintentional hypergolic fluid related spills, fires, and explosions from the Apollo Program, the Space Shuttle Program, the Titan Program, and a few others have occurred over the past several decades. Spill sites include the following government facilities: Kennedy Space Center (KSC), Johnson Space Center (JSC), White Sands Test Facility (WSTF), Vandenberg Air Force Base (VAFB), Cape Canaveral Air Force Station (CCAFS), Edwards Air Force Base (EAFB), Little Rock AFB, and McConnell AFB. Until now, the only method of capturing the lessons learned from these incidents has been "word of mouth" or by studying each individual incident report. Through studying several dozen of these incidents, certain root cause themes are apparent. Scrutinizing these themes could prove to be highly beneficial to future hypergolic system test, checkout, and operational use. I. Introduction Hypergolic fluids are toxic liquids that react spontaneously and violently when they contact each other. These fluids are used in many different rocket and aircraft systems for propulsion and hydraulic power including: orbiting satellites, manned spacecraft, military aircraft, and deep space probes. Hypergolic fuels include hydrazine (N2H4) and its derivatives including: monomethylhydrazine (MMH), unsymmetrical di-methylhydrazine (UDMH), and Aerozine 50 (A-50), which is an equal mixture of N2114 and UDMH. The oxidizer used with these fuels is usually nitrogen tetroxide (N2O4), also known as dinitrogen tetroxide or NTO, and various blends of N2O4 with nitric oxide (NO).