Driving Pockels Cells Using Avalanche Transistor Pulsers
Total Page:16
File Type:pdf, Size:1020Kb
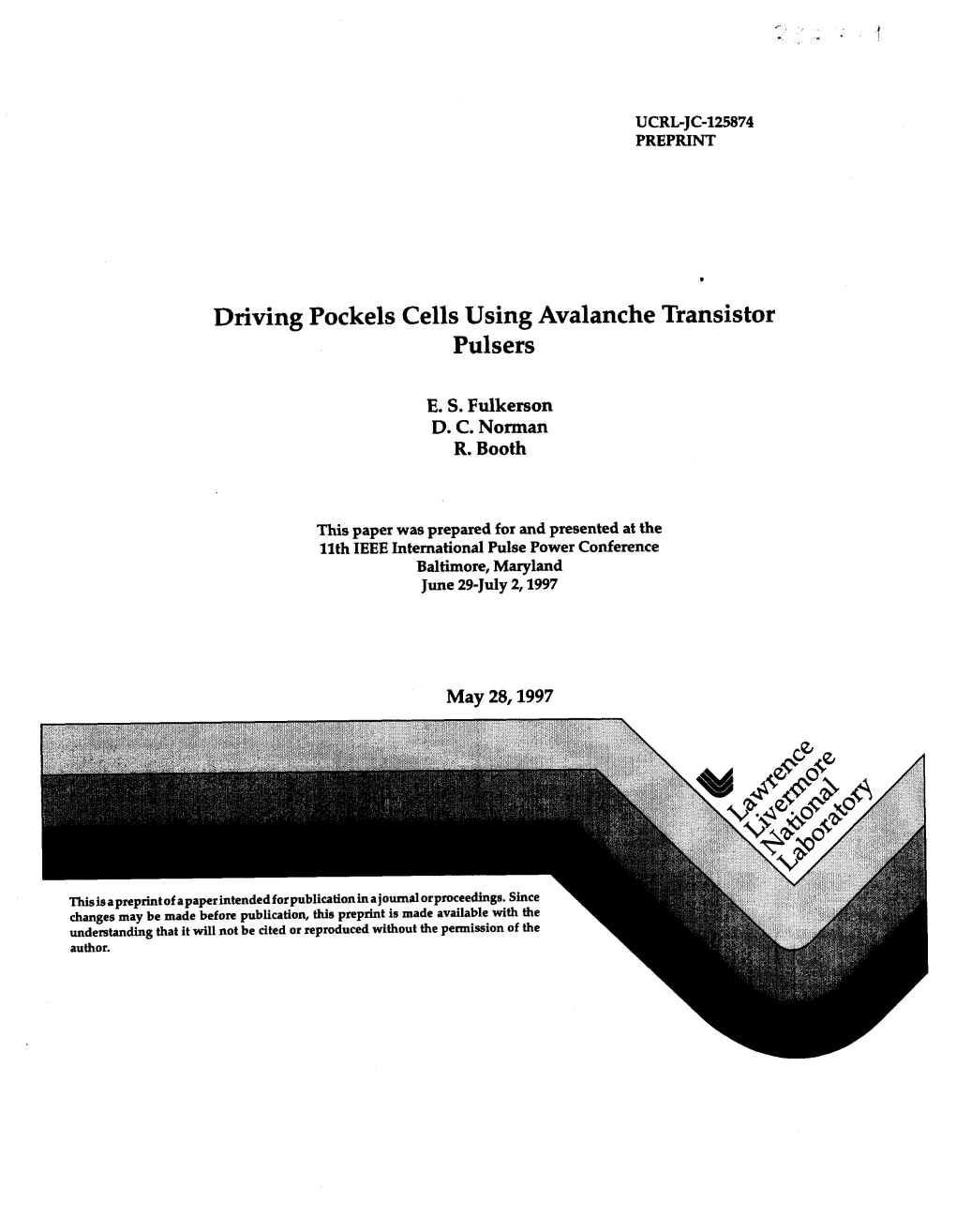
Load more
Recommended publications
-
Timing of Load Switches
Application Report SLVA883–April 2017 Timing of Load Switches Nicholas Carley........................................................................................................... Power Switches ABSTRACT Timing of load switches can vary depending on the operating conditions of the system and feature set of the device. At a glance, these variations can seem complex; but, when broken down, each operating condition and feature has a correlation to a change in timing. This application note goes into detail on how each condition or feature can alter the timing of a load switch so that the variations can be prepared for. Contents 1 Overview and Main Questions ............................................................................................. 2 1.1 Definition of Timing Parameters .................................................................................. 2 1.2 Alternative Timing Methods ....................................................................................... 2 1.3 Why is My Rise Time Different than Expected? ................................................................ 3 1.4 Why is My Fall Time Different than Expected? ................................................................. 3 1.5 Why Do NMOS and PMOS Pass FETs Affect Timing Differently?........................................... 3 2 Effect of System Operating Specifications on Timing................................................................... 5 2.1 Temperature........................................................................................................ -
System Step and Impulse Response Lab 04 Bruce A
ROSE-HULMAN INSTITUTE OF TECHNOLOGY Department of Electrical and Computer Engineering ECE 300 Signals and Systems Spring 2009 System Step and Impulse Response Lab 04 Bruce A. Ferguson, Bob Throne In this laboratory, you will investigate basic system behavior by determining the step and impulse response of a simple RC circuit. You will also determine the time constant of the circuit and determine its rise time, two common figures of merit (FOMs) for circuit building blocks. Objectives 1. Design an experiment by specifying a test setup, choosing circuit component values, and specifying test waveform details to investigate the step and impulse response. 2. Measure the step response of the circuit and determine the rise time, validating your theoretical calculations. 3. Measure the impulse response of the circuit and determine the time constant, validating your theoretical calculations. Prelab Find and bring a circuit board to the lab so you can build the RC circuit. Background As we introduce the study of systems, it will be good to keep the discussion well grounded in the circuit theory you have spent so much of your energy learning. An important problem in modern high speed digital and wideband analog systems is the response limitations of basic circuit elements in high speed integrated circuits. As simple as it may seem, the lowly RC lowpass filter accurately models many of the systems for which speed problems are so severe. There is a basic need to be able to characterize a circuit independent of its circuit design and layout in order to predict its behavior. Consider the now-overly-familiar RC lowpass filter shown in Figure 1. -
The ZTX415 Avalanche Mode Transistor an Introduction to Characteristics, Performance and Applications
Application Note 8 Issue 2 January 1996 The ZTX415 Avalanche Mode Transistor An Introduction to Characteristics, Performance and Applications Neil Chadderton Introduction Avalanche mode devices can provide a few application circuit examples. extremely high switching speeds and (Please refer to Appendix A for a list of are capable of producing current outputs reference material). far in excess of that obtained from conventional circuits. These attributes lend themselves to many applications, including; laser diode drivers for ranging, measurement, and collision avoidance systems, Pockel cell drivers for laser Q switches, SAW device exciters, streak cameras and fast high voltage/ high current pulse generators. The Zetex Semiconductors ZTX415 is an avalanche transistor that ideally suits Figure 1 this mode of operation and application. Transistor Characteristics in the The device is available in the proven Avalanche Region. silicone E-Line package that assures excellent thermal properties to complement the high performance What Is An Avalanche avalanche characteristics. It is also Transistor? available in the SOT-23 surface mount Avalanche transistors are characterised package (as FMMT415) to enable very by a negative resistance region in their low inductance designs. V-I breakdown curve (usually called secondary breakdown) as illustrated in This Application Note outlines the Figure 1. This region permits controlled principle of avalanche mode operation, switching of very high currents in gives details on important parameter nanoseconds when appropriate external and operating conditions, and suggests AN 8 - 1 Application Note 8 Issue 2 January 1996 circuitry is employed. The output pulse reliability work. For example, devices on generated is limited by the primary a life test have produced current pulses breakdown BVCBO , the transistor’s ‘On- of 60A peak and 10ns pulse width for state’ voltage and the mean dissipation over 4 x 1011 times without failure. -
Speed of Light with Nanosecond Pulsed 650 Nm Diode Laser M
Speed of Light with Nanosecond Pulsed 650 nm Diode Laser M. Gallant May 23, 2008 The speed of light has been measured many different ways using many ingenious methods. The following note describes a method which is conceptually very easy to understand and fairly easy to implement. The technique is the simple time-of-flight optical pulse delay method using a fairly short (nanosecond) optical pulse and an oscilloscope with bandwidth between 50 - 100 MHz. THE LASER Common low power laser pointers, typically emit at a wavelength of 650 nm and operate from two to four 1.5 V button cells. Many of these lasers can be easily extracted from the pointer assembly and pulse-modulated to several hundred megahertz. The laser used here was removed from a low power (< 5mW) laser pointer assembly from a popular retail outlet. GENERATION OF SHORT OPTICAL PULSES The laser is prebiased below threshold, at 5 - 10 mA current (threshold current for the laser used here is 24 mA) using an inductor as a bias insertion element. A short (< 5 ns) electrical pulse modulates the laser. Since a very low duty cycle is used for pulsing the laser, fairly high current pulses are possible without degrading the laser. The actual forward current and voltage achieved during the drive pulse are dependent on the details of the I-V characteristic of the specific laser used, but are typically in the range of 50 - 100 mA and 6 - 10 V respectively. The short electrical pulse is generated using a simple avalanche transistor circuit. Due to the high frequency content of the short pulse, the actual shape of the current pulse driving the laser will depend on the circuit components (series resistors etc.) and parasitic electrical effects (series inductance of connection wires etc.) The circuit has been described by Jim Williams in a Linear Technology Measurement and Control Circuit Collection and has many other uses. -
Chapter 4 HW Solution
ME 380 Chapter 4 HW February 27, 2012 Chapter 4 HW Solution Review Questions. 1. Name the performance specification for first order systems. Time constant τ. 2. What does the performance specification for a first order system tell us? How fast the system responds. 5. The imaginary part of a pole generates what part of the response? The un-decaying sinusoidal part. 6. The real part of a pole generates what part of the response? The decay envelope. 8. If a pole is moved with a constant imaginary part, what will the responses have in common? Oscillation frequency. 9. If a pole is moved with a constant real part, what will the responses have in common? Decay envelope. 10. If a pole is moved along a radial line extending from the origin, what will the responses have in common? Damping ratio (and % overshoot). 13. What pole locations characterize (1) the underdamped system, (2) the overdamped system, and (3) the critically damped system? 1. Complex conjugate pole locations. 2. Real (and separate) pole locations. 3. Real identical pole locations. 14. Name two conditions under which the response generated by a pole can be neglected. 1. The pole is \far" to the left in the s-plane compared with the other poles. 2. There is a zero very near to the pole. Problems. Problem 2(a). This is a 1st order system with a time constant of 1/5 second (or 0.2 second). It also has a DC gain of 1 (just let s = 0 in the transfer function). The input shown is a unit step; if we let the transfer function be called G(s), the output is input × transfer function. -
Effect of Source Inductance on MOSFET Rise and Fall Times
Effect of Source Inductance on MOSFET Rise and Fall Times Alan Elbanhawy Power industry consultant, email: [email protected] Abstract The need for advanced MOSFETs for DC-DC converters applications is growing as is the push for applications miniaturization going hand in hand with increased power consumption. These advanced new designs should theoretically translate into doubling the average switching frequency of the commercially available MOSFETs while maintaining the same high or even higher efficiency. MOSFETs packaged in SO8, DPAK, D2PAK and IPAK have source inductance between 1.5 nH to 7 nH (nanoHenry) depending on the specific package, in addition to between 5 and 10 nH of printed circuit board (PCB) trace inductance. In a synchronous buck converter, laboratory tests and simulation show that during the turn on and off of the high side MOSFET the source inductance will develop a negative voltage across it, forcing the MOSFET to continue to conduct even after the gate has been fully switched off. In this paper we will show that this has the following effects: • The drain current rise and fall times are proportional to the total source inductance (package lead + PCB trace) • The rise and fall times arealso proportional to the magnitude of the drain current, making the switching losses nonlinearly proportional to the drain current and not linearly proportional as has been the common wisdom • It follows from the above two points that the current switch on/off is predominantly controlled by the traditional package's parasitic -
AN79 F01 Cost While Saving Power
Application Note 79 September 1999 30 Nanosecond Settling Time Measurement for a Precision Wideband Amplifier Quantifying Prompt Certainty Jim Williams Introduction SETTLING TIME INPUT Instrumentation, waveform generation, data acquisition, feedback control systems and other application areas RING TIME utilize wideband amplifiers. New components (see page 2 “A Precision Wideband Dual Amplifier with 30ns Settling ALLOWABLE OUTPUT Time”) have introduced precision while maintaining high ERROR BAND speed operation. The amplifier’s DC and AC specifications SLEW OUTPUT approach or equal previous devices at significantly lower TIME DELAY TIME AN79 F01 cost while saving power. Figure 1. Settling Time Components Include Delay, Slew and Settling Time Defined Ring Times. Fast Amplifiers Reduce Slew Time, Although Amplifier DC specifications are relatively easy to verify. Longer Ring Time Usually Results. Delay Time is Normally a Small Term Measurement techniques are well understood, albeit often tedious. AC specifications require more sophisticated approaches to produce reliable information. In particular, pensation. Additionally, the architecture of very fast ampli- amplifier settling time is extraordinarily difficult to deter- fiers usually dictates trade-offs which degrade DC error mine. Settling time is the elapsed time from input applica- terms.1 tion until the output arrives at and remains within a Measuring anything at any speed requires care. Dynamic specified error band around the final value. It is usually measurement is particularly challenging. Reliable nano- specified for a full-scale transition. Figure 1 shows that second region settling time measurement constitutes a settling time has three distinct components. The delay high order difficulty problem requiring exceptional care time is small and is almost entirely due to amplifier in approach and experimental technique.2 propagation delay. -
Fmmt415, Fmmt417
FMMT415 FMMT417 NPN AVALANCHE TRANSISTOR IN SOT23 Features Mechanical Data Avalanche Transistor Case: SOT23 60A Peak Avalanche Current (Pulse width = 20ns) Case Material: Molded Plastic. “Green” Molding Compound. BVCES > 260V (415) & 320V (417) UL Flammability Classification Rating 94V-0 BVCEO > 100V Moisture Sensitivity: Level 1 per J-STD-020 Specifically designed for Avalanche mode operation Terminals: Finish – Matte Tin Plated Leads. Totally Lead-Free & Fully RoHS Compliant (Notes 1 & 2) Solderable per MIL-STD-202, Method 208 e3 Halogen and Antimony Free. “Green” Device (Note 3) Weight: 0.008 grams (Approximate) Qualified to AEC-Q101 Standards for High Reliability Description Applications The FMMT415/417 are NPN silicon planar bipolar transistors Laser Diode Drivers for Ranging and Measurement (LIDAR) designed for operating in avalanche mode. Tight process control and Radar Systems low inductance packaging combine to produce high-current pulses Fast Edge Switch Generator with fast edges. High Speed Pulse Generators SOT23 C E B C B E Top View Device Symbol Top View Pin-Out Ordering Information (Note 4) Product Compliance Marking Reel size (inches) Tape width (mm) Quantity per reel FMMT415TD AEC-Q101 415 7 8 500 FMMT417TD AEC-Q101 417 7 8 500 Notes: 1. No purposely added lead. Fully EU Directive 2002/95/EC (RoHS) & 2011/65/EU (RoHS 2) compliant. 2. See http://www.diodes.com/quality/lead_free.html for more information about Diodes Incorporated’s definitions of Halogen- and Antimony-free, “Green” and Lead-free. 3. Halogen- and Antimony-free “Green” products are defined as those which contain <900ppm bromine, <900ppm chlorine (<1500ppm total Br + Cl) and <1000ppm antimony compounds. -
A Fiber-Optically Triggered Avalanche Transistor Matic Test Equipment Involving Ac Bridges [8[
IEEE TRA~"SACTlO0:S ON INSTRU:vIEl\TATlON AND MEASUREMENT. VOL. 40. NO.3. JUl\E 1'191 25 Input signal ; 500 jJV 20 Amplifier gain ~ A Simulation result continuous curves Measured error points x x x A ; 200 o ::J 10 '"0 A 400 (f) ClJ 750 D:::: o 20 40 60 80 100 120 140 160 180 Phase difference <r (deg) Fig. 6. Extent of pha.'c compensation as a function of amplifier gain A. effcct [7 J. The schemc can also be successfully employed in auto A Fiber-Optically Triggered Avalanche Transistor matic test equipment involving ac bridges [8[. R. Jacob Baker, Gregory T. Perryman. and Phillip W. Watts Y. CONCLUSION It has been demonstrated that using feedback technique for phase Abstract-A silicon bipolar transistor operating in the avalanche re compensation in a PSD, the amplitudc of thc measurand can bc got gion is optically triggered into secondary breakdown, This transistor has been given the name fiber-optically triggered avalanche transistor directly without the need for a post-processing of the in-pha,e and (FOTAT), The FOTAT acts as an optical power discriminator. That quadrature components. Experimental results presented serve to is, secondar) breakdown occurs when the triggering optical power ex establish the easy applicability of the method to obtain a high de ceeds tbe triggering tbreshold of tbe FOT AT, This secondary break gree of phase compensation coupled with a fine resolution. Quan down is seen as a negative resistance between the collector and emitter. High voltage (> 100 V) nanosecond transition duration pulses arc gen titative comparison of the extent of compensation obtained exper erated using this negative resistance, imentally with that estimated by PC-simulation indicates good agreement. -
Introduction to Amplifiers
ORTEC ® Introduction to Amplifiers Choosing the Right Amplifier for the Application The amplifier is one of the most important components in a pulse processing system for applications in counting, timing, or pulse- amplitude (energy) spectroscopy. Normally, it is the amplifier that provides the pulse-shaping controls needed to optimize the performance of the analog electronics. Figure 1 shows typical amplifier usage in the various categories of pulse processing. When the best resolution is needed in energy or pulse-height spectroscopy, a linear pulse-shaping amplifier is the right solution, as illustrated in Fig. 1(a). Such systems can acquire spectra at data rates up to 7,000 counts/s with no loss of resolution, or up to 86,000 counts/s with some compromise in resolution. The linear pulse-shaping amplifier can also be used in simple pulse-counting applications, as depicted in Fig. 1(b). Amplifier output pulse widths range from 3 to 70 µs, depending on the selected shaping time constant. This width sets the dead time for counting events when utilizing an SCA, counter, and timer. To maintain dead time losses <10%, the counting rate is typically limited to <33,000 counts/s for the 3-µs pulse widths and proportionately lower if longer pulse widths have been selected. Some detectors, such as photomultiplier tubes, produce a large enough output signal that the system shown in Fig. 1(d) can be used to count at a much higher rate. The pulse at the output of the fast timing amplifier usually has a width less than 20 ns. -
A Compact, Short-Pulse Laser for Near-Field, Range-Gated Imaging Fred J Zutavem, Wesley D
A Compact, Short-pulse Laser for Near-field, Range-gated Imaging Fred J Zutavem, Wesley D. Helgeson, and Guillermo M. Loubnel Sandia National Laboratories, Albuquerque, New Mexico, 87185-1 153 (505) 845-9128, FAX 845-3651, Email: [email protected] George J. Yates, Robert A. Gallegos, and Thomas E. McDonald Los Alamos National Laboratory, Los Alamos, New Mexico 87545 (505) 667-7529, FAX 665-4121, Email: [email protected] ABSTRACT This paper describes a compact laser, which produces high power, wide-angle emission for a near-field, range-gated, imaging system. The optical pulses are produced by a 100 element laser diode array (LDA) which is pulsed with a GaAs, photoconductive semiconductor switch (PCSS). The LDA generates 100 ps long, gain-switched, optical pulses at 904 nm when it is driven with 3 ns, 400 A, electrical pulses from a high gain PCSS. Gain switching is facilitated with this many lasers by using a low impedance circuit to drive an array of lasers, which are connected electrically in series. The total optical energy produced per pulse is 10 microjoules corresponding to a total peak power of 100 kW. The entire laser system, including prime power (a nine volt battery), pulse charging, PCSS, and LDA, is the size of a small, hand-held flashlight. System lifetime, which is presently limited by the high gain PCSS, is an active area of research and development. Present limitations and potential improvements will be discussed. The complete range-gated imaging system is based on complementary technologies: high speed optical gating with intensified charge coupled devices (ICCD) developed at Los Alamos National Laboratory (LANL)and high gain, PCSS-driven LDAs developed at Sandia National Laboratories (SNL). -
Avalanche Impedance Avalanche Transistor Avalanche Voltage Average Current
AVERAGE CURRENT 29 Avalanche breakdown in a particular diode might occur The exact value of the avalanche impedance for alternating with just a few volts of reverse bias, or it might take hundreds of current is the value of resistor that would be necessary to allow volts. Rectifier diodes do not undergo avalanche breakdown the same flow of reverse current. The average ZA for alternating until the voltage becomes quite large (see AVALANCHE current differs from the instantaneous value, which fluctuates VOLTAGE). A special type of diode, called the zener diode (see as the voltage rises and falls. Avalanche is usually undesirable ZENER DIODE), is designed to have a fairly low, and very pre- in alternating-current applications. cise, avalanche breakdown voltage. Such diodes are used as voltage regulators. Zener diodes are sometimes called avalanche diodes because of their low avalanche voltages. AVALANCHE TRANSISTOR The illustration shows graphically the current flow through An avalanche transistor is an npn or pnp transistor that is de- a diode as a function of reverse voltage. The current is so small, signed to operate with a high level of reverse bias at the emitter- for small reverse voltages, that it might be considered to be zero base junction. Normally, transistors are forward-biased at the for practical purposes. When the reverse voltage becomes suffi- emitter-base junction except when cutoff conditions are de- cient to cause avalanche breakdown, however, the current rises sired when there is no signal input. rapidly. Avalanche transistors are seen in some switching applica- tions. The emitter-base junction is reverse-biased almost to the point where avalanche breakdown occurs.