DIY Robotic Sky Tracking Astrophotography Mount with Circuitpython Created by Dylan Herrada
Total Page:16
File Type:pdf, Size:1020Kb
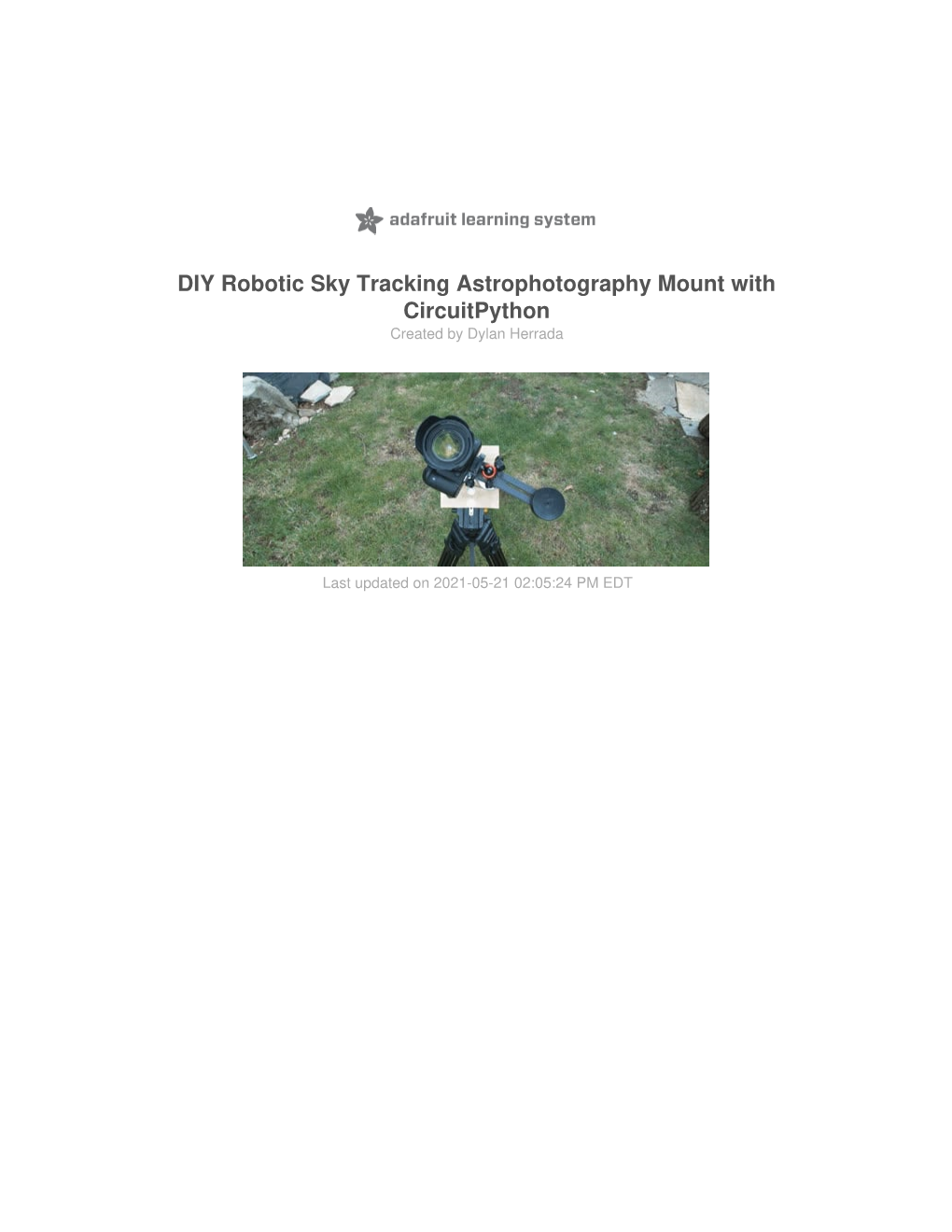
Load more
Recommended publications
-
The Toastboard: Ubiquitous Instrumentation and Automated Checking of Breadboarded Circuits
The Toastboard: Ubiquitous Instrumentation and Automated Checking of Breadboarded Circuits Daniel Drew†, Julie L. Newcomb‡, William McGrath?, Filip Maksimovic†, David Mellis†, Bjoern Hartmann† †: UC Berkeley EECS, ‡: University of Washington PLSE, ? : Stanford University HCI Group ddrew73,fil,mellis,[email protected], [email protected], [email protected] ABSTRACT The recent proliferation of easy to use electronic components and toolkits has introduced a large number of novices to de- signing and building electronic projects. Nevertheless, debug- ging circuits remains a difficult and time-consuming task. This paper presents a novel debugging tool for electronic design projects, the Toastboard, that aims to reduce debugging time by improving upon the standard paradigm of point-wise circuit measurements. Ubiquitous instrumentation allows for imme- diate visualization of an entire breadboard’s state, meaning users can diagnose problems based on a wealth of data instead Figure 1. The Toastboard device and accompanying software. (1) LED bars indicate power, ground, or other voltage. (2) A push button triggers of having to form a single hypothesis and plan before taking a scan. (3) Quantitative voltage data is displayed in the accompanying a measurement. Basic connectivity information is displayed software. (4) Components are associated with testers that run on every visually on the circuit itself and quantitative data is displayed scan. (5) The voltage at a selected row can be viewed over time as a on the accompanying web interface. Software-based testing graph. functions further lower the expertise threshold for efficient debugging by diagnosing classes of circuit errors automati- cally. In an informal study, participants found the detailed, frustrating, and time-consuming to debug. -
A Freecad Manual
Table of Contents Introduction 1.1 Discovering FreeCAD 1.2 What is FreeCAD? 1.2.1 Installing 1.2.2 Installing on Windows 1.2.2.1 Installing on Linux 1.2.2.2 Installing on Mac OS 1.2.2.3 Uninstalling 1.2.2.4 Setting basic preferences 1.2.2.5 Installing additional content 1.2.2.6 The FreeCAD interface 1.2.3 Workbenches 1.2.3.1 The interface 1.2.3.2 Customizing the interface 1.2.3.3 Navigating in the 3D view 1.2.4 A word about the 3D space 1.2.4.1 The FreeCAD 3D view 1.2.4.2 Selecting objects 1.2.4.3 The FreeCAD document 1.2.5 Parametric objects 1.2.6 Import and export to other filetypes 1.2.7 Working with FreeCAD 1.3 All workbenches at a glance 1.3.1 Traditional modeling, the CSG way 1.3.2 Traditional 2D drafting 1.3.3 Modeling for product design 1.3.4 Preparing models for 3D printing 1.3.5 Exporting to slicers 1.3.5.1 Converting objects to meshes 1.3.5.2 Using Slic3r 1.3.5.3 2 Using the Cura addon 1.3.5.4 Generating G-code 1.3.5.5 Generating 2D drawings 1.3.6 BIM modeling 1.3.7 Using spreadsheets 1.3.8 Reading properties 1.3.8.1 Writing properties 1.3.8.2 Creating FEM analyses 1.3.9 Creating renderings 1.3.10 Python scripting 1.4 A gentle introduction 1.4.1 Writing Python code 1.4.1.1 Manipulating FreeCAD objects 1.4.1.2 Vectors and Placements 1.4.1.3 Creating and manipulating geometry 1.4.2 Creating parametric objects 1.4.3 Creating interface tools 1.4.4 The community 1.5 3 Introduction A FreeCAD manual Introduction FreeCAD is a free, open-source parametric 3D modeling application. -
Electronic and Electromechanical Prototyping
Electronic and electromechanical prototyping Introduction - ECAD Corso LM ‘Materiali Intelligenti e Biomimetici’ – Prof. A. Ahluwalia 4/05/2017 [email protected] After Breadboards: Matrix Boards We use breadboards for quick construction, Matrix Boards for laying out a project so it can be copied to make a Printed Circuit Board. This is a prototyping board, with copper pads in a matrix layout. You solder the components in place, and then simply cut pieces of wire, and solder them to make the circuit Printed Circuit Board The PCB is the physical board that holds and connects all of the electronic components. The circuits are formed by a thin layer of conducting material deposited, or "printed," on the surface of an insulating board known as the substrate. Individual electronic components are placed on the surface of the substrate and soldered to the interconnecting circuits. ECAD Electronic computer-aided design (ECAD) or Electronic design automation (EDA) is a category of software tools for designing electronic systems such as integrated circuits and printed circuit boards. The tools work together in a design flow that chip designers use to design and analyze entire semiconductor chips. Before EDA, integrated circuits were designed by hand and manually laid out. By the mid-1970s, developers started to automate the design along with the drafting. The first placement and routing tools were developed. Printed Circuit Board Design PCB ECAD Software (Ex. Eagle): PCB design in EAGLE is a two-step process. First you design your schematic, then you lay out a PCB based on that schematic. PCB Design (2) Your circuit design software will allow you to output the PCB layout in a format called Gerber with one file for each PCB layer (copper layers, solder mask, legend or silk) to allow manufacturing. -
Metadefender Core V4.12.2
MetaDefender Core v4.12.2 © 2018 OPSWAT, Inc. All rights reserved. OPSWAT®, MetadefenderTM and the OPSWAT logo are trademarks of OPSWAT, Inc. All other trademarks, trade names, service marks, service names, and images mentioned and/or used herein belong to their respective owners. Table of Contents About This Guide 13 Key Features of Metadefender Core 14 1. Quick Start with Metadefender Core 15 1.1. Installation 15 Operating system invariant initial steps 15 Basic setup 16 1.1.1. Configuration wizard 16 1.2. License Activation 21 1.3. Scan Files with Metadefender Core 21 2. Installing or Upgrading Metadefender Core 22 2.1. Recommended System Requirements 22 System Requirements For Server 22 Browser Requirements for the Metadefender Core Management Console 24 2.2. Installing Metadefender 25 Installation 25 Installation notes 25 2.2.1. Installing Metadefender Core using command line 26 2.2.2. Installing Metadefender Core using the Install Wizard 27 2.3. Upgrading MetaDefender Core 27 Upgrading from MetaDefender Core 3.x 27 Upgrading from MetaDefender Core 4.x 28 2.4. Metadefender Core Licensing 28 2.4.1. Activating Metadefender Licenses 28 2.4.2. Checking Your Metadefender Core License 35 2.5. Performance and Load Estimation 36 What to know before reading the results: Some factors that affect performance 36 How test results are calculated 37 Test Reports 37 Performance Report - Multi-Scanning On Linux 37 Performance Report - Multi-Scanning On Windows 41 2.6. Special installation options 46 Use RAMDISK for the tempdirectory 46 3. Configuring Metadefender Core 50 3.1. Management Console 50 3.2. -
IDF Exporter IDF Exporter Ii
IDF Exporter IDF Exporter ii April 27, 2021 IDF Exporter iii Contents 1 Introduction to the IDFv3 exporter 2 2 Specifying component models for use by the exporter 2 3 Creating a component outline file 4 4 Guidelines for creating outlines 6 4.1 Package naming ................................................ 6 4.2 Comments .................................................... 6 4.3 Geometry and Part Number entries ...................................... 7 4.4 Pin orientation and positioning ........................................ 7 4.5 Tips on dimensions ............................................... 8 5 IDF Component Outline Tools 8 5.1 idfcyl ....................................................... 9 5.2 idfrect ...................................................... 10 5.3 dxf2idf ...................................................... 11 6 idf2vrml 12 IDF Exporter 1 / 12 Reference manual Copyright This document is Copyright © 2014-2015 by it’s contributors as listed below. You may distribute it and/or modify it under the terms of either the GNU General Public License (http://www.gnu.org/licenses/gpl.html), version 3 or later, or the Creative Commons Attribution License (http://creativecommons.org/licenses/by/3.0/), version 3.0 or later. All trademarks within this guide belong to their legitimate owners. Contributors Cirilo Bernardo Feedback Please direct any bug reports, suggestions or new versions to here: • About KiCad document: https://gitlab.com/kicad/services/kicad-doc/issues • About KiCad software: https://gitlab.com/kicad/code/kicad/issues • About KiCad software i18n: https://gitlab.com/kicad/code/kicad-i18n/issues Publication date and software version Published on January 26, 2014. IDF Exporter 2 / 12 1 Introduction to the IDFv3 exporter The IDF exporter exports an IDFv3 1 compliant board (.emn) and library (.emp) file for communicating mechanical dimensions to a mechanical CAD package. -
A Credit Card Sized Ethernet Arduino Compatable Controller Board by Drj113 on July 4, 2010
Home Sign Up! Browse Community Submit All Art Craft Food Games Green Home Kids Life Music Offbeat Outdoors Pets Photo Ride Science Tech A credit card sized Ethernet Arduino compatable controller board by drj113 on July 4, 2010 Table of Contents A credit card sized Ethernet Arduino compatable controller board . 1 Intro: A credit card sized Ethernet Arduino compatable controller board . 2 Step 1: Here is the Schematic Diagram . 2 File Downloads . 3 Step 2: The PCB Layout . 3 File Downloads . 3 Step 3: Soldering the Components . 4 Step 4: Programming the Firmware . 5 File Downloads . 5 Step 5: But what does it do???? . 6 Step 6: Parts LIst . 6 Step 7: KiCad Files . 7 File Downloads . 7 Related Instructables . 7 Comments . 7 http://www.instructables.com/id/A-credit-card-sized-Ethernet-Arduino-compatable-co/ Author:drj113 I have a background in digital electronics, and am very interested in computers. I love things that blink, and am in awe of the physics associated with making blue LEDs. Intro: A credit card sized Ethernet Arduino compatable controller board I love the Arduino as a simple and accessible controller platform for many varied projects. A few months ago, a purchased an Ethernet shield for my Arduino controller to work on some projects with a mate of mine - it was a massive hit - for the first time, I could control my projects remotely using simple software. That got me thinking - The Arduino costs about $30AUD, and the Ethernet board cost about $30AUD as well. That is a lot of money - Could I make a simple, dedicated remote controller for much cheaper? Why Yes I could. -
Programming Resume
Thomas John Hastings Programming Resume Introduction: I am a highly motivated self-starter with a passion for problem solving. As the owner of a thriving entertainment agency, Big Top Entertainment, I used coding as a way to automate and improve our business processes. I also designed, built and programmed my own unique performance equipment. Since the pandemic and recurring lockdowns have put live entertainment on hold, I have repurposed my passion for programming into a full time focus. I am looking for a challenge, to be involved in building something, learning new technology and sharing the knowledge I have gained from my own projects. Programming – languages and frameworks: Processing I have extensive knowledge of this Java-based creative programming language. The great thing about Processing is the way you can deploy to Desktop, Mobile, and Cloud with only a few modifications to the same code base. Android (Java) I have seven Android apps published to the Google Play Store, five of which are written in Java. I have developed many more for personal use, including the most recent, CoronaVirusSA, an open source app which graphs reliable stats on the COVID-19 outbreak in South Africa. JavaScript Anyone developing for the web needs to know JavaScript. I am familiar with the Flask back end with Jinja, Bootstrap, JQuery, as well as the excellent Tabulator library for tables. Currently (2020/21) my free time is spent on a couple of entertainment related side projects using this stack. Linux I have been using Ubuntu as my main computing system for over 10 years, both in the cloud (DigitalOcean) and on my Laptop. -
Beyond Schematic Capture Meaningful Abstractions for Better Electronics Design Tools
Beyond Schematic Capture Meaningful Abstractions for Better Electronics Design Tools Richard Lin, Rohit Ramesh, Antonio Iannopollo, Alberto Sangiovanni Vincentelli, Prabal Dutta, Elad Alon, Björn Hartmann University of California, Berkeley {richard.lin,rkr,antonio,alberto,prabal,elad,bjoern}@berkeley.edu Physical Device Parts Selection Ideas and ATmega Part Number Size Vf +3.3v Iteration Requirements System Architecture OVLFY3C7 5mm 2 V D0 APG1005SYC-T 0402 2.05 V Button J1 Design Micro- D1 5988140107F 0805 2 V D1 controller - or - ... SW1 Part Number Core LED Flow R1 U1 R2 ATmega32u4 AVR GND Micro- controller LPC1549 ARM CM3 Final FE310-G000 RV32IMAC Hand-built Schematic Prototype PCB Prototypes Capture PCB Tools paper, drawing software breadboards EDA suites: Altium, EAGLE, KiCAD parts libraries, catalogs, spreadsheets Used more abstract, high-level more concrete, low-level Design user stories implementation exploration documentation verification cost, manufacturability cost Concerns functional specification verification supporting circuitry system integration component availability and sourcing Figure 1: The electronics design flow, as described by our participants. Users start with an idea, refine that intoasystem architecture, and then iterate physical prototypes. Parts selection happens throughout the process. While certain steps require linear progression, iteration and revision of earlier stages also happen. Overall, EDA tools only support a small part of this process, and moving between steps was a major source of friction. ABSTRACT on clickthrough mockups of design flows through an exam- Printed Circuit Board (PCB) design tools are critical in help- ple project. We close with our observation on opportunities ing users build non-trivial electronics devices. While recent for improving board design tools and discuss generalizability work recognizes deficiencies with current tools and explores of our findings beyond the electronics domain. -
Kustannustehokkaat Cad, Fem Ja Cam -Ohjelmat Tutkimus Saatavilla Olevista Ohjelmista Tammikuussa 2018
OULUN YLIOPISTON KERTTU SAALASTI INSTITUUTIN JULKAISUJA 6/2018 Kustannustehokkaat Cad, Fem ja Cam -ohjelmat Tutkimus saatavilla olevista ohjelmista tammikuussa 2018 Terho Iso-Junno Tulevaisuuden tuotantoteknologiat FMT-tutkimusryhmä Terho Iso-Junno KUSTANNUSTEHOKKAAT CAD, FEM JA CAM -OHJELMAT Tutkimus saatavilla olevista ohjelmista tammikuussa 2018 OULUN YLIOPISTO Kerttu Saalasti Instituutin julkaisuja Tulevaisuuden tuotantoteknologiat (FMT) -tutkimusryhmä ISBN 978-952-62-2018-5 (painettu) ISBN 978-952-62-2019-2 (elektroninen) ISSN 2489-3501 (painettu) Terho Iso-Junno Kustannustehokkaat CAD, FEM ja CAM -ohjelmat. Tutkimus saatavilla olevista ohjelmista tammikuussa 2018. Oulun yliopiston Kerttu Saalasti Instituutti, Tulevaisuuden tuotantoteknologiat (FMT) -tutkimusryhmä Oulun yliopiston Kerttu Saalasti Instituutin julkaisuja 6/2018 Nivala Tiivistelmä Nykyaikaisessa tuotteen suunnittelussa ja valmistuksessa tietokoneohjelmat ovat avainasemassa olevia työkaluja. Kaupallisten ohjelmien lisenssihinnat voivat nousta korkeiksi ja olla hankinnan esteenä etenkin aloittelevilla yrityksillä. Tässä tutkimuk- sessa on kartoitettu kustannuksiltaan edullisia CAD, FEM ja CAM -ohjelmia, joita voisi käyttää yritystoiminnassa. CAD-ohjelmien puolella perinteisille 2D CAD-ohjelmille löytyy useita hyviä vaih- toehtoja. LibreCAD ja QCAD ovat helppokäyttöisiä ohjelmia perustason piirtämiseen. Solid Edge 2D Drafting on erittäin monipuolinen täysiverinen 2D CAD, joka perustuu parametriseen piirtämiseen. 3D CAD-ohjelmien puolella tarjonta on tasoltaan vaihtelevaa. -
Ecebuntu - an Innovative and Multi-Purpose Educational Operating System for Electrical and Computer Engineering Undergraduate Courses
RESEARCH ARTICLE Electrica 2018; 18(2): 210-217 ECEbuntu - An Innovative and Multi-Purpose Educational Operating System for Electrical and Computer Engineering Undergraduate Courses Bilal Wajid1 , Ali Rıza Ekti2 , Mustafa Kamal AlShawaqfeh3 1Department of Electrical Engineering, University of Engineering and Technology, Lahore, Pakistan 2Department of Electrical-Electronics Engineering, Balıkesir University School of Engineering, Balıkesir, Turkey 3School of Electrical Engineering and Information Technology, German Jordanian University, Amman, Jordan Cite this article as: B. Wajid, A. R. Ekti, M. K. AlShawaqfeh, “ECEbuntu - An Innovative and Multi-Purpose Educational Operating System for Electrical and Computer Engineering Undergraduate Courses”, Electrica, vol. 18, no: 2, pp. 210-217, 2018. ABSTRACT ECEbuntu is a free, easily distributable, customized operating system based on Ubuntu 12.04 long term support (LTS) designed for electrical/electronic and computer engineering (ECE) students. ECEbuntu is aimed at universities and students as it represents a cohesive environment integrating more than 30 pre-installed software and packages all catering to undergraduate coursework offered in ECE and Computer Science (CS) programs. ECEbuntu supports a wide range of tools for programming, circuit analysis, printed circuit board design, mathematical and numerical analysis, network analysis, and RF and microwave transmitter design. ECEbuntu is free and effective alternative to the existing costly and copyrighted software packages. ECEbuntu attempts -
Open-Source Software for Documenting Prototypes, Learning Interactive Electronics and PCB Production
Open-source software for documenting prototypes, learning interactive electronics and PCB production www.fritzing.org Supporting the tinkerer through all steps from breadboard prototype to a professional PCB production Fritzing is developed by the Fritzing community and researchers of the Interaction Design Lab at the University of Applied Sciences, Potsdam with support from the Ministry of Science, Research and Culture in the state of Brandenburg, Germany Index 1. Abstract: What is Fritzing? 3.4 Publishers 1.1 Democratization of Technology 3.4.1 Books 3.4.2 Magazines 2. What is Fritzing for? 3.4.3 Blogs 2.1 Documenting 2.1.1 From a breadboard sketch to a professional file format 4. Fritzing: Development Model and Feature Set 2.2 Sharing and Open-source 4.1 Arduino, Processing and Fritzing 2.2.1 Sharing is Caring 4.2 Why Open-Source 2.2.3 The community 4.3. Three views of Fritzing 2.2.4 The Fritzing.org Website 4.3.1 Breadboard view 2.3 Teaching and Learning 4.3.2 Schematics view 2.3.1 Why teaching electronics is important 4.3.3 PCB view 2.3.2 Teaching at schools 4.4. Parts Editor 2.3.3 Women on the forefront 4.4.1 Personalizing Fritzing 2.3.4 The Fritzing Starter Kit 4.4.2 Making parts simple 2.3.5 How Fritzing overcomes classical teaching difficulties 2.4 Manufacturing 5. Fritzing Quality 3. Who uses Fritzing and how 5.1 Real size 3.1 Teachers 5.2 Flexibility 3.1.1 Academic 5.3 Trustworthiness 3.1.2 School 5.4 Workshops and continuous research 3.1.3 Workshop 3.2 Manufacturers 6. -
Freecad a Manual.Pdf
Table of Contents Introduction 1.1 Discovering FreeCAD 1.2 What is FreeCAD? 1.2.1 Installing 1.2.2 Installing on Windows 1.2.2.1 Installing on Linux 1.2.2.2 Installing on Mac OS 1.2.2.3 Uninstalling 1.2.2.4 Setting basic preferences 1.2.2.5 Installing additional content 1.2.2.6 The FreeCAD interface 1.2.3 Workbenches 1.2.3.1 The interface 1.2.3.2 Customizing the interface 1.2.3.3 Navigating in the 3D view 1.2.4 A word about the 3D space 1.2.4.1 The FreeCAD 3D view 1.2.4.2 Selecting objects 1.2.4.3 The FreeCAD document 1.2.5 Parametric objects 1.2.6 Import and export to other filetypes 1.2.7 Working with FreeCAD 1.3 All workbenches at a glance 1.3.1 Traditional modeling, the CSG way 1.3.2 Traditional 2D drafting 1.3.3 Modeling for product design 1.3.4 Preparing models for 3D printing 1.3.5 Exporting to slicers 1.3.5.1 Converting objects to meshes 1.3.5.2 Using Slic3r 1.3.5.3 2 Using the Cura addon 1.3.5.4 Generating G-code 1.3.5.5 Generating 2D drawings 1.3.6 BIM modeling 1.3.7 Using spreadsheets 1.3.8 Reading properties 1.3.8.1 Writing properties 1.3.8.2 Creating FEM analyses 1.3.9 Creating renderings 1.3.10 Python scripting 1.4 A gentle introduction 1.4.1 Writing Python code 1.4.1.1 Manipulating FreeCAD objects 1.4.1.2 Vectors and Placements 1.4.1.3 Creating and manipulating geometry 1.4.2 Creating parametric objects 1.4.3 Creating interface tools 1.4.4 The community 1.5 3 Introduction A FreeCAD manual Note: The manual has been moved to the official FreeCAD wiki which is now its new home.