Design of a Miniaturized Imaging System for As-Built Performance
Total Page:16
File Type:pdf, Size:1020Kb
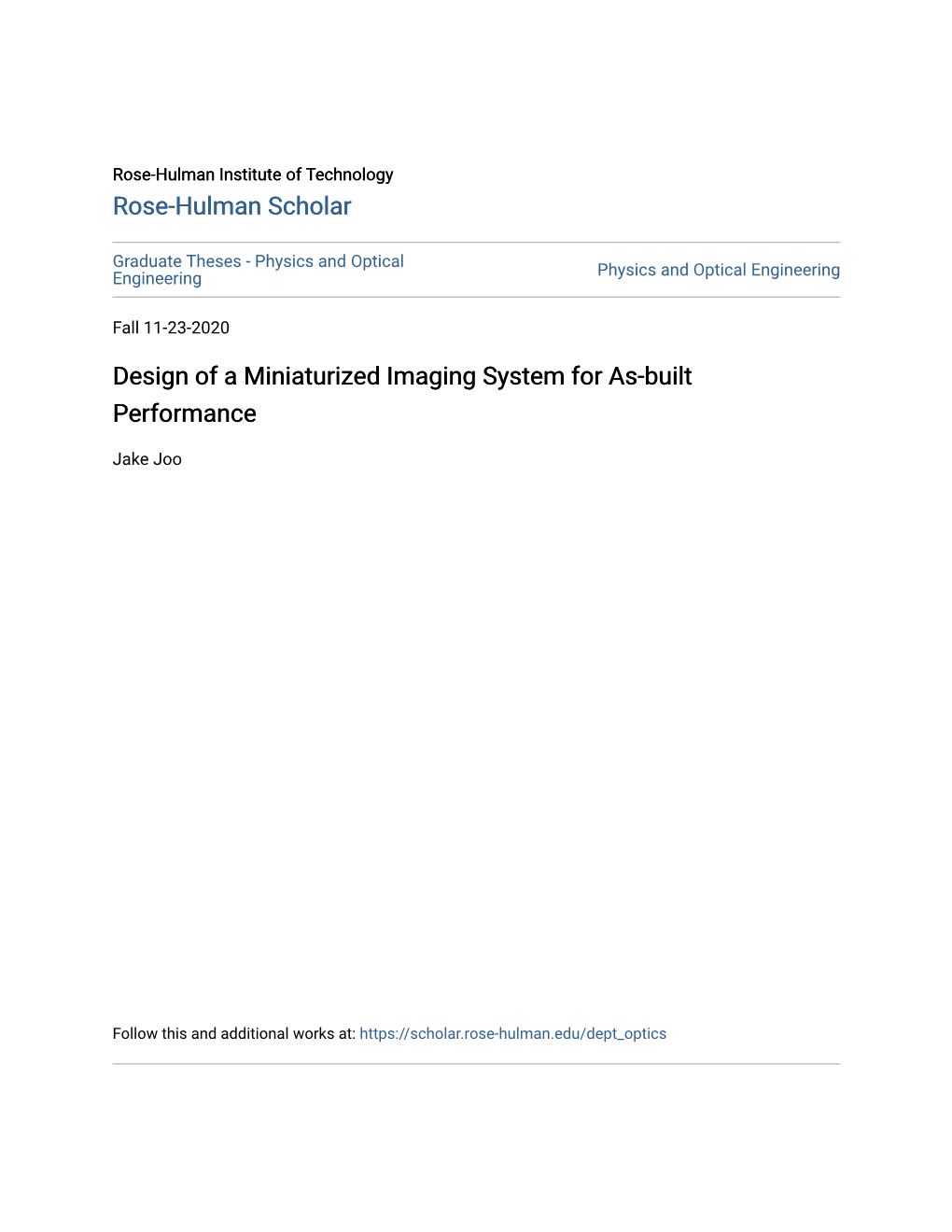
Load more
Recommended publications
-
Nokia 7650 Provides Various Functions, Which Are Very Handy for Daily Use, Such As Camera, Clock, Alarm Clock, Calculator, and Calendar
User’s Guide 9353238 Issue 4 EN Electronic user’s guide released subject to "Nokia User’s Guides Terms and Conditions, 7th June, 1998" DECLARATION OF CONFORMITY We, NOKIA CORPORATION declare under our sole responsibility that the product NHL-2NA is in conformity with the provisions of the following Council Directive: 1999/5/EC. A copy of the Declaration of Conformity can be found from http://www.nokia.com/phones/declaration_of_conformity/ Copyright © 2002 Nokia. All rights reserved. Reproduction, transfer, distribution or storage of part or all of the contents in this document in any form without the prior written permission of Nokia is prohibited. Nokia and Nokia Connecting People are registered trademarks of Nokia Corporation. Other product and company names mentioned herein may be trademarks or tradenames of their respective owners. Nokia tune is a trademark of Nokia Corporation. This product includes software licensed from Symbian Ltd © 1998-2002 © 1998-2002 Symbian Ltd. All rights reserved. Symbian and Symbian OS are trademarks of Symbian Ltd. All rights reserved. Java™ and all Java-based marks are trademarks or registered trademarks of Sun Microsystems, Inc. Stac ®, LZS ®, ©1996, Stac, Inc., ©1994-1996 Microsoft Corporation. Includes one or more U.S. Patents: No. 4701745, 5016009, 5126739, 5146221, and 5414425. Other patents pending. Hi/fn ®, LZS ®,©1988-98, Hi/fn. Includes one or more U.S. Patents: No. 4701745, 5016009, 5126739, 5146221, and 5414425. Other patents pending. Part of the software in this product is © Copyright ANT Ltd. 1998. All rights reserved. m-Router Connectivity Components © 2000-2002 Intuwave Limited. All rights reserved. (www.intuwave.com) US Patent No 5818437 and other pending patents. -
(12) Patent Application Publication (10) Pub. No.: US 2015/0055085A1 Fonte Et Al
US 2015.0055085A1 (19) United States (12) Patent Application Publication (10) Pub. No.: US 2015/0055085A1 Fonte et al. (43) Pub. Date: Feb. 26, 2015 (54) METHOD AND SYSTEM TO CREATE (52) U.S. Cl. PRODUCTS CPC .......... G02C 13/001 (2013.01); G06F 19/3456 (2013.01); G06F 17/50 (2013.01) (71) Applicant: Bespoke, Inc., San Francisco, CA (US) USPC ............................................. 351/178; 700/98 (72) Inventors: Timothy A. Fonte, San Francisco, CA (57) ABSTRACT (US); Eric J. Varady, San Francisco, CA Systems and methods for creating fully custom products from (US) scratch without exclusive use of off-the-shelfor pre-specified components. A system for creating custom products includes (21) Appl. No.: 14/466,615 an image capture device for capturing image data and/or measurement data of a user. A computer is communicatively (22) Filed: Aug. 22, 2014 coupled with the image capture device and configured to constructananatomic model of the user based on the captured O O image data and/or measurement data. The computer provides Related U.S. Application Data a configurable product model and enables preview and auto (60) Provisional application No. 61/869,051, filed on Aug. matic or user-guided customization of the product model. A 22, 2013, provisional application No. 62/002,738, display is communicatively coupled with the computer and filed on May 23, 2014. displays the custom product model Superimposed on the ana tomic model or image data of the user. The computeris further Publication Classification configured to provide the customized product model to a manufacturer for manufacturing eyewear for the user in (51) Int. -
SAMPLE – Apple Iphone Review - Article (Copyrighted Content – Not for Re-Use)
Godot Content Services Website: content.godotmedia.com Email: [email protected] SAMPLE – Apple iPhone Review - Article (Copyrighted Content – Not for Re-use) Apple iPhone 3GS Overview The ‘S’ in Apple’s 3GS iPhone denotes better speed and performance, which comes from the higher RAM and a faster processor. The 3GS undoubtedly gives a better performance than its predecessors. It also comes with video recording, voice control, copy-paste and MMS features. Its biggest weakness however is with regard to USB transfers and it is time Apple did something about it. Design The design of the iPhone 3GS is almost identical to the 3G version, measuring 4.5 x 2.4 x 0.48 inches. It comes in black and white colors. It is slightly heavier though, at 135 grams. The 3GS has a 3.5-inch widescreen display with a 480×320 resolution. The display is brighter than the 3G phone. To reduce the effects of fingerprint smudges, it features an oleophobic glaze on the display screen. Camera iPhone 3GS comes with an improved 3 megapixel camera but still falls short of the Nokia N95’s 5 megapixel camera. It now has autofocus, a feature that adjusts the color, balance, and contrast of the subject being photographed with just a tap on the display. It also comes with better low light sensitivity. But Apple has yet again decided against flash and digital zoom, which will disappoint many users. The image quality is decent. The device comes with a new video recording feature in VGA resolution at 30fps. Another great feature is video editing, where the video is displayed in different frames and you can change the clip in several ways. -
Nokia Phones: from a Total Success to a Total Fiasco
Portland State University PDXScholar Engineering and Technology Management Faculty Publications and Presentations Engineering and Technology Management 10-8-2018 Nokia Phones: From a Total Success to a Total Fiasco Ahmed Alibage Portland State University Charles Weber Portland State University, [email protected] Follow this and additional works at: https://pdxscholar.library.pdx.edu/etm_fac Part of the Engineering Commons Let us know how access to this document benefits ou.y Citation Details A. Alibage and C. Weber, "Nokia Phones: From a Total Success to a Total Fiasco: A Study on Why Nokia Eventually Failed to Connect People, and an Analysis of What the New Home of Nokia Phones Must Do to Succeed," 2018 Portland International Conference on Management of Engineering and Technology (PICMET), Honolulu, HI, 2018, pp. 1-15. This Article is brought to you for free and open access. It has been accepted for inclusion in Engineering and Technology Management Faculty Publications and Presentations by an authorized administrator of PDXScholar. Please contact us if we can make this document more accessible: [email protected]. 2018 Proceedings of PICMET '18: Technology Management for Interconnected World Nokia Phones: From a Total Success to a Total Fiasco A Study on Why Nokia Eventually Failed to Connect People, and an Analysis of What the New Home of Nokia Phones Must Do to Succeed Ahmed Alibage, Charles Weber Dept. of Engineering and Technology Management, Portland State University, Portland, Oregon, USA Abstract—This research intensively reviews and analyzes the management made various strategic changes to take the strategic management of technology at Nokia Corporation. Using company back into its leading position, or at least into a traditional narrative literature review and secondary sources, we position that compensates or reduces the losses incurred since reviewed and analyzed the historical transformation of Nokia’s then. -
Nokia and Symbian OS White Paper
White Paper Nokia and Symbian OS White Paper Contents Nokia and Symbian – the history – extracts from Nokia announcements 3 What is Symbian 4 Symbian OS and Nokia products 5 Commercial benefi ts for both operators and developers 5 Symbian OS – fundamental customer requirements 6 Symbian OS – architecture 6 An open operating system 8 Symbian product releases – launching new technology 8 Writing applications for Symbian OS 8 2 White Paper Symbian is key to the future of the telecommunications industry. Nokia is basing its future smartphones on Symbian OS and it forms the basis of the recently launched Series 60 platform. Nokia is a founding member and shareholder of the Symbian alliance. This paper provides a basic understanding of why Nokia is strongly committed to Symbian – from both a commercial and a technical perspective. Additionally, some of the technical qualities of Symbian OS are examined in some detail – this section is aimed at the more technically minded reader. Nokia and Symbian – the history – extracts from Nokia announcements 24.6.1998 21.5.2001 13.11.2001 “It was announced today that Ericsson, “Nokia expects 50% of its 3G phones Open Mobile Architecture alliance Nokia and Psion have conditionally to use the Symbian Operating System launched – AT&T Wireless, Cingular agreed to form a new joint venture by 2004.” Jorma Ollila, CEO Nokia. Wireless, MM02, NTT DoCoMo, called Symbian. Nokia’s investment is Telefonica Moviles, Vodafone, Fujitsu, approx. USD 50 million. This agreement 5.6.2001 Matsushita, Mitsubishi Electric, is further strengthened by the support The Nokia 9290 Communicator (for US) Motorola, NEC, Nokia, Samsung, Sharp, of Motorola who have signed a launched – “The 9290 Communicator Siemens, Sony Ericsson, Toshiba and Memorandum of Understanding to join demonstrates Nokia’s commitment to Symbian to commit to products Symbian.“ not only provide unique, innovative and services based on open mobile products for our customers, but to do architecture enablers. -
Mobile Learning for HIV/AIDS Healthcare Worker
Zolfo et al. AIDS Research and Therapy 2010, 7:35 http://www.aidsrestherapy.com/content/7/1/35 RESEARCH Open Access Mobile learning for HIV/AIDS healthcare worker training in resource-limited settings Maria Zolfo1*, David Iglesias2, Carlos Kiyan1, Juan Echevarria2, Luis Fucay2, Ellar Llacsahuanga2, Inge de Waard1, Victor Suàrez3, Walter Castillo Llaque2, Lutgarde Lynen1 Abstract Background: We present an innovative approach to healthcare worker (HCW) training using mobile phones as a personal learning environment. Twenty physicians used individual Smartphones (Nokia N95 and iPhone), each equipped with a portable solar char- ger. Doctors worked in urban and peri-urban HIV/AIDS clinics in Peru, where almost 70% of the nation’s HIV patients in need are on treatment. A set of 3D learning scenarios simulating interactive clinical cases was devel- oped and adapted to the Smartphones for a continuing medical education program lasting 3 months. A mobile educational platform supporting learning events tracked participant learning progress. A discussion forum accessi- ble via mobile connected participants to a group of HIV specialists available for back-up of the medical informa- tion. Learning outcomes were verified through mobile quizzes using multiple choice questions at the end of each module. Methods: In December 2009, a mid-term evaluation was conducted, targeting both technical feasibility and user satisfaction. It also highlighted user perception of the program and the technical challenges encountered using mobile devices for lifelong learning. Results: With a response rate of 90% (18/20 questionnaires returned), the overall satisfaction of using mobile tools was generally greater for the iPhone. Access to Skype and Facebook, screen/keyboard size, and image quality were cited as more troublesome for the Nokia N95 compared to the iPhone. -
Design and Analysis of Optical Layouts for Free Space Optical Switching
Edith Cowan University Research Online Theses: Doctorates and Masters Theses 2002 Design and analysis of optical layouts for free space optical switching Kung-meng Lo Edith Cowan University Follow this and additional works at: https://ro.ecu.edu.au/theses Part of the Electrical and Computer Engineering Commons Recommended Citation Lo, K. (2002). Design and analysis of optical layouts for free space optical switching. https://ro.ecu.edu.au/theses/1645 This Thesis is posted at Research Online. https://ro.ecu.edu.au/theses/1645 Edith Cowan University Copyright Warning You may print or download ONE copy of this document for the purpose of your own research or study. The University does not authorize you to copy, communicate or otherwise make available electronically to any other person any copyright material contained on this site. You are reminded of the following: Copyright owners are entitled to take legal action against persons who infringe their copyright. A reproduction of material that is protected by copyright may be a copyright infringement. Where the reproduction of such material is done without attribution of authorship, with false attribution of authorship or the authorship is treated in a derogatory manner, this may be a breach of the author’s moral rights contained in Part IX of the Copyright Act 1968 (Cth). Courts have the power to impose a wide range of civil and criminal sanctions for infringement of copyright, infringement of moral rights and other offences under the Copyright Act 1968 (Cth). Higher penalties may apply, and higher damages may be awarded, for offences and infringements involving the conversion of material into digital or electronic form. -
Smartphone-Based Vehicle Telematics — a Ten-Year Anniversary Johan Wahlstrom,¨ Isaac Skog, Member, IEEE, and Peter Handel,¨ Senior Member, IEEE
Internet of Things Telematics Vehicle Telematics Smartphone-based Vehicle Telematics Smartphone-based Vehicle Telematics — A Ten-Year Anniversary Johan Wahlstrom,¨ Isaac Skog, Member, IEEE, and Peter Handel,¨ Senior Member, IEEE Abstract—Just like it has irrevocably reshaped social life, Estimated market value: the fast growth of smartphone ownership is now beginning to revolutionize the driving experience and change how we think 263 about automotive insurance, vehicle safety systems, and traffic Internet of Things research. This paper summarizes the first ten years of research in smartphone-based vehicle telematics, with a focus on user- 138 friendly implementations and the challenges that arise due to Telematics the mobility of the smartphone. Notable academic and industrial projects are reviewed, and system aspects related to sensors, Vehicle Telematics 45 energy consumption, cloud computing, vehicular ad hoc net- [Billion dollars] works, and human-machine interfaces are examined. Moreover, we highlight the differences between traditional and smartphone- Smartphone-based based automotive navigation, and survey the state-of-the-art Vehicle Telematics By 2020 By 2019 in smartphone-based transportation mode classification, driver classification, and road condition monitoring. Future advances are expected to be driven by improvements in sensor technology, evidence of the societal benefits of current implementations, and the establishment of industry standards for sensor fusion and Fig. 1. A Venn diagram illustrating the relation between the internet of things, telematics, vehicle telematics, and smartphone-based vehicle telemat- driver assessment. ics. Predicted market values are $263 billion (internet of things, by 2020) [2], Index Terms—Smartphones, internet-of-things, telematics, ve- $138 billion (telematics, by 2020) [7], and $45 billion (vehicle telematics, by hicle navigation, usage-based-insurance, driver classification. -
Design for Manufacturability and Optical Performance Trade-Offs Using Precision Glass Molded Aspheric Lenses
Invited Paper Design for Manufacturability and Optical Performance Trade-offs using Precision Glass Molded Aspheric Lenses Alan Symmons, Jeremy Huddleston and Dennis Knowles LightPath Technologies, Inc., 2603 Challenger Tech Ct, Ste 100, Orlando, FL, USA 32826 ABSTRACT Precision glass molding (PGM) enables high-performance, low-cost lens designs through aspheric shapes and a broad array of moldable glass types. While these benefits bring a high potential value, the design of PGM lenses must be skillfully approached to balance manufacturability and cost considerations. Different types of mold tooling and processes used by PGM suppliers can also lead to confusion regarding the manufacturing parameters and design rules that should be considered. The authors discuss the various factors that can affect manufacturability and cost of lenses made to PGM standards, and present a case study to demonstrate the trade-offs in performance. Keywords: Precision glass molding, asphere, optical lens, design rules, manufacturability 1. INTRODUCTION Precision glass molding is a compression molding process (as opposed to the popularized injection molding of plastic) capable of transferring high-quality aspheric shapes from a precision mold set into the optical lens being formed. This technology has the distinct advantage of enabling low cost optical lenses for high volume applications, while maintaining the high quality of aspheric optical surface profiles and utilizing the inherent advantages of glass materials [1]. Modern PGM technology was pioneered in the late 1970’s to early 1980’s by companies such as Corning Glass Works and Eastman Kodak, who then transferred these complex capabilities to PGM manufacturers such as Geltech (acquired by LightPath Technologies in 2000) [2]. -
'Inferior' Iphone 9 January 2017, by Nigel Linge
Nokia had the world's best smartphone – then came the 'inferior' iPhone 9 January 2017, by Nigel Linge device as a phone first and a computer second. That's not too surprising given its history and evolution, starting out as a basic telephone and slowly but surely acquiring more computing features. But a new entrant can turn thinking on its head, and that's precisely what Apple did by viewing the handset as primarily a computer that just happened to include a phone capability. This was clearly reflected in its appearance, where the physical keyboard was eliminated and replaced by a single button and large touch screen. In Credit: Sami Keinänen/Flickr, CC BY-SA contrast, the Nokia N95 had a range of buttons and a slide feature that revealed a conventional phone keypad. Ten years ago, anyone who wanted the latest and Even more important were the key differences best smartphone was excited about the Nokia N95. between the software that controlled the two Launched at the Nokia Open Studio in September phones. Nokia was locked into the cumbersome 2006, it was trumpeted as the all-in-one multimedia Symbian operating system and its complex user computer and went on to achieve sales of a million interface, whereas Apple iOS was centred on the handsets within the UK in its first year. touch screen with gesture controls and had a fully functioning web browser and, of course, apps. On paper, it had everything a gadget-lover could desire, including a 2.6-inch LCD screen, a Several reviewers at the time were rather lukewarm 5-megapixel camera with Carl Zeiss optics and towards the iPhone, concerned about its technical video recorder, up to 8GB of storage, 3G and WiFi inadequacies and especially its lack of 3G. -
Iphone: Surviving the Shakeout
iPhone: Surviving The Shakeout Robin Abraham, Daniel Alvarez, Brent Goldman, and Craig Vieregg BEM 106 – Competitive Strategy, Spring Term June 4, 2008 iPhone: Surviving the Shakeout 1 Table of Contents 1 Executive Summary............................................................................................................. 3 2 History ..................................................................................................................................... 3 3 Six Forces Analysis .............................................................................................................. 4 3.1 Competition .....................................................................................................................................4 3.2 New Entrants...................................................................................................................................5 3.3 Buyer Bargaining Power ............................................................................................................5 3.4 Supplier Bargaining Power .......................................................................................................5 3.5 Substitute Products ......................................................................................................................6 3.6 Complements/Synergies............................................................................................................6 4 SWOT Analysis ..................................................................................................................... -
Anssi Cebit Final
Nokia Mobile Phones – The next phase Nokia Investor seminar CeBIT 2002 Anssi Vanjoki Executive Vice President Nokia Mobile Phones 1 © NOKIA 2000 Outline • Nokia’s new product launches • Nokia 3410 • Nokia 3510 • Nokia 6310i • Nokia 9210i • Nokia 7210 • Mobile Device technology evolution • Convergence in Mobility • Summary 2 © NOKIA 2000 New Product Launches 3 © NOKIA 2000 • RealOne Player for streaming video • Flash Player allowing playback of Macromedia flash content • Considerably faster data processing • New web browser for JavaScripts support and HTML 4.01 compatibility • Enhanced security with Nokia VPN Client • Nokia GPS module for route assistance 4 © NOKIA 2000 Nokia and RealNetworks alliance • RealOne player to be included in Nokia’s Symbian based handsets • RealOne player to be licensed in Nokia Series 60 platform • RealSystem Streaming Server Software included in Nokia’s infrastructure solutions for mobile operators 5 © NOKIA 2000 • JavaTM 2 Micro Edition (J2ME TM) • Picture editor • 3D graphics engine • WAP 1.1 with push funtionality • 5 games: Link5, Space impact, Bantumi, Snake II, Bumper 6 © NOKIA 2000 • GPRS • Polyphonic (MIDI) sounds • Value added services (VAS) over Multimedia messaging (MMS) receive • Fun gaming concept • sounds, multiple keypress, vibra 7 © NOKIA 2000 FUNctional Accessory Covers 8 © NOKIA 2000 FILENAMEs.PPT/ DATE / NN • Tri-band GSM, GPRS, HSCSD • Multimedia messaging (MMS) • Java 2 Micro Edition (J2ME) • Series 40 user interface • High quality color display • Polyphonic (MIDI) sounds • Stereo FM radio • Integrated handsfree speaker Lord of the Clouds: Sumea ® 9 © NOKIA 2000 • Tri-band GSM, GPRS, HSCSD • Multimedia messaging (MMS) • Java 2 Micro Edition (J2ME) • Series 40 user interface • High quality color display • Polyphonic (MIDI) sounds • Stereo FM radio • Integrated handsfree speaker 10 © NOKIA 2000 • Tri-band GSM, GPRS, HSCSD • Java 2 Micro Edition (J2ME) • Bluetooth, infrared, cable • Wallet with WIM 11 © NOKIA 2000 Leadership in Product Portfolio 22 mobile phones announced in 2001.