High Purity Polycrystalline Silicon Growth and Characterization Uda Hashim* [A], Abang A
Total Page:16
File Type:pdf, Size:1020Kb
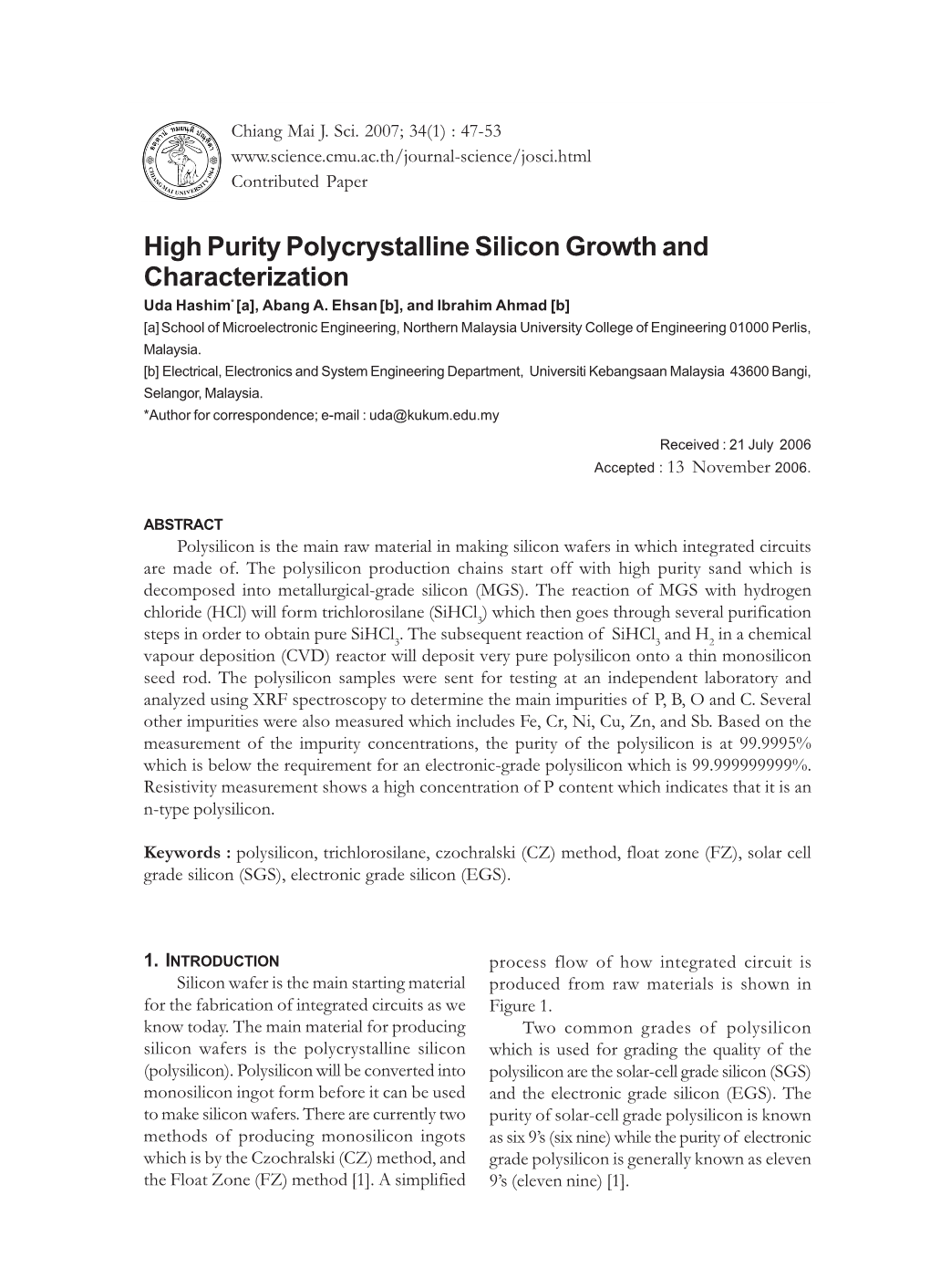
Load more
Recommended publications
-
Channel Structures Formed in Copper Ingots Upon Melting and Evaporation by a High-Power Electron Beam
Metals 2015, 5, 428-438; doi:10.3390/met5010428 OPEN ACCESS metals ISSN 2075-4701 www.mdpi.com/journal/metals/ Communication Channel Structures Formed in Copper Ingots upon Melting and Evaporation by a High-Power Electron Beam Sergey Bardakhanov 1,2,5, Andrey Nomoev 2,3,*, Makoto Schreiber 2, Alexander Radnaev 2, Rustam Salimov 4, Konstantin Zobov 1,5, Alexey Zavjalov 1,5 and Erzhena Khartaeva 2,3 1 Khristianovich Institute of Applied and Theoretical Mechanics, Siberian Branch of the Russian Academy of Sciences, Institutskaya str., 4/1, Novosibirsk 630090, Russia; E-Mails: [email protected] (S.B.); [email protected] (K.Z.); [email protected] (A.Z.) 2 Department of Physics and Engineering, Buryat State University, Smolina str., 24a, Ulan-Ude 670000, Russia; E-Mails: [email protected] (M.S.); [email protected] (A.R.); [email protected] (E.K.) 3 Institute of Physical Materials, Siberian Branch of the Russian Academy of Sciences, Sakhyanovoy str., 6, Ulan-Ude 670047, Russia 4 Budker Institute of Nuclear Physics, Siberian Branch of the Russian Academy of Sciences, Lavrenteva str., 11, Novosibirsk 630090, Russia; E-Mail: [email protected] 5 Department of Physics, Novosibirsk State University, Pirogova str., 20, Novosibirsk 630090, Russia * Author to whom correspondence should be addressed; E-Mail: [email protected]; Tel.: +8-902-564-24-62. Academic Editor: Hugo F. Lopez Received: 5 November 2014 / Accepted: 5 March 2015 / Published: 12 March 2015 Abstract: A new phenomenon is described in this paper: the formation of macroscopic channel structures on the bottom of copper ingots which were used as the target for the synthesis of copper nanoparticles by high-power electron beam evaporation and condensation. -
Conventional Steel Making Vs Powder Metallurgy
Conventional Steelmaking vs. Powder Metallurgy Steelmaking Conventional steelmaking begins by melting steel in a large electric arc furnace. The initial melting of the steel is usually followed by a secondary ladle refining process such as Argon Oxygen Decarburization (AOD) or Vacuum Oxygen Decarburization (VOD). After refining, the molten metal is cast into ingots. Ladle Refining Cast Ingots Conventional Steelmaking - Ingot Structure Cast steel is very homogeneous in the molten state but as it slowly solidifies in the ingot molds, the alloying elements segregate producing a non-uniform as-cast structure. In high speed steels and high alloy steels, carbides precipitate and form coarse networks that must be broken up by hot working of the ingots. The hot processing will improve the structure but the segregation effects are never fully eliminated. Cast Ingot And Internal Structure Powder Metallurgy Steelmaking using Hot Isostatic Pressing (HIP) Making tool steels using Hot Isostatic Pressing begins with an initial melt furnace similar to a conventional melting process but on a much smaller scale. Instead of pouring and casting the melt, the molten metal is poured through a small nozzle where high pressure gas atomizes the liquid stream. The droplets fall and rapidly solidify into powder which is collected in the atomization chamber. Each powder particle is essentially a micro ingot with minimal segregation and fine carbides. The fine carbide size is retained through the mill processing. After atomization the powder is collected, screened to specific mesh requirements, and blended. The powder is loaded into steel containers, evacuated of air, then sealed. The steel containers full of powder are then loaded into an autoclave and Hot Isostatically Pressed at pressures and temperatures approximately the same as used for forging. -
Crystalline Silicon Photovoltaic Module Manufacturing
Crystalline Silicon Photovoltaic Module Manufacturing Costs and Sustainable Pricing: 1H 2018 Benchmark and Cost Reduction Road Map Michael Woodhouse, Brittany Smith, Ashwin Ramdas, and Robert Margolis National Renewable Energy Laboratory NREL is a national laboratory of the U.S. Department of Energy Technical Report Office of Energy Efficiency & Renewable Energy NREL/TP-6A20-72134 Operated by the Alliance for Sustainable Energy, LLC Revised February 2020 This report is available at no cost from the National Renewable Energy Laboratory (NREL) at www.nrel.gov/publications. Contract No. DE-AC36-08GO28308 Crystalline Silicon Photovoltaic Module Manufacturing Costs and Sustainable Pricing: 1H 2018 Benchmark and Cost Reduction Road Map Michael Woodhouse, Brittany Smith, Ashwin Ramdas, and Robert Margolis National Renewable Energy Laboratory Suggested Citation Woodhouse, Michael. Brittany Smith, Ashwin Ramdas, and Robert Margolis. 2019. Crystalline Silicon Photovoltaic Module Manufacturing Costs and Sustainable Pricing: 1H 2018 Benchmark and Cost Reduction Roadmap. Golden, CO: National Renewable Energy Laboratory. https://www.nrel.gov/docs/fy19osti/72134.pdf. NREL is a national laboratory of the U.S. Department of Energy Technical Report Office of Energy Efficiency & Renewable Energy NREL/TP-6A20-72134 Operated by the Alliance for Sustainable Energy, LLC Revised February 2020 This report is available at no cost from the National Renewable Energy National Renewable Energy Laboratory Laboratory (NREL) at www.nrel.gov/publications. 15013 Denver West Parkway Golden, CO 80401 Contract No. DE-AC36-08GO28308 303-275-3000 • www.nrel.gov NOTICE This work was authored by the National Renewable Energy Laboratory, operated by Alliance for Sustainable Energy, LLC, for the U.S. Department of Energy (DOE) under Contract No. -
Copper Oxhide Ingot Marks
COPPER OXHIDE INGOT MARKS: A DATABASE AND COMPARATIVE ANALYSIS A Thesis Presented to the Faculty of the Graduate School of Cornell University In Partial Fulfillment of the Requirements for the Degree of Master of Archaeology by Alaina M. Kaiser May 2013 © 2013 Alaina M. Kaiser All Rights Reserved. ABSTRACT COPPER OXHIDE INGOT MARKS: A CATALOGUE AND COMPARATIVE ANALYSIS Alaina Kaiser, M.A. Cornell University, 2013 Many objects of international trade from the Late Bronze Age eastern Mediterranean are marked with symbols of undetermined meaning. Of these, copper oxhide ingots have been of particular interest to archaeologists for decades. As the meaning of these marks is currently unknown, my work attempts to analyze patterns of them that are distinguishable through a study of the marked ingots’ contextual and geographic distribution. My research resulted in a database composed of all retrievable information regarding the discovery, contextual information, and physical characteristics of all copper oxhide ingot remains and marks. The purpose of this database and distribution analysis is to contribute to the ongoing efforts to understand these artifacts so ubiquitous in Late Bronze Age settlements in the eastern Mediterranean. ii BIOGRAPHICAL SKETCH Alaina Kaiser was graduated from Boston University in 2009 with a Bachelors of Arts degree in Archaeology and a minor in Classical Civilizations. After obtaining her degree, Ms. Kaiser held a research assistant position at the Massachusetts Board of Underwater Archaeological Resources and worked as a field technician in CRM at Public Archaeology Laboratory. While interning with the National Park Service at the Historic Kingsley Plantation in 2010, Ms. Kaiser volunteered with the University of Florida’s archaeological field school led by Dr. -
Defects Introduced Into Metals During Fabrication and Service - A.J.Wilby and D.P
MATERIALS SCIENCE AND ENGINEERING – Vol. III – Defects Introduced into Metals During Fabrication and Service - A.J.Wilby and D.P. Neale DEFECTS INTRODUCED INTO METALS DURING FABRICATION AND SERVICE A.J.Wilby and D.P. Neale British Energy Ltd., Gloucester, UK Keywords: Defects, metals, service, failure, casting, cracks, forging, fabrication, welding, metallurgical, heat-treatment, embrittlement, fatigue, creep, oxidation, wear, cavitation, tribosystem Contents 1. Introduction 2. Primary Production Defects 2.1. Casting Defects 2.1.1. Pipe and Shrinkage 2.1.2. Inclusions 2.1.3. Segregation 2.1.4. Porosity 2.1.5. Surface Defects 2.1.6. Other Defects 2.2. Forming Defects 2.2.1. Cracks, Laps and Seams 2.2.2. Surface Defects 3. Defects Introduced During Fabrication 3.1. Defects Resulting From Cutting 3.2. Joining Methods 3.2.1. Design Related Defects 3.2.2. Procedure and Process Defects 3.2.3. Metallurgical Factors 3.3. Heat Treatment 3.3.1. Stress relief of machined or welded components 3.3.2. Hardening and quench cracking 3.3.3. Embrittlement 4. Defects IntroducedUNESCO in Service – EOLSS 4.1. Fatigue 4.2. High Temperature Defects 4.2.1. Mechanical property degradation and creep 4.2.2. EnvironmentalSAMPLE interaction CHAPTERS 4.2.3. Microstructural Changes 4.3. Wear 4.3.1. Abrasive Wear 4.3.2. Adhesive Wear 4.3.3. Fretting 4.3.4. Erosion 4.3.5. Rolling Contact Wear 4.4. Embrittlement 5. The significance of defects entering service ©Encyclopedia of Life Support Systems (EOLSS) MATERIALS SCIENCE AND ENGINEERING – Vol. III – Defects Introduced into Metals During Fabrication and Service - A.J.Wilby and D.P. -
SILICON INGOT PRODUCTION PROCESS for WAFERS the Element Silicon Has Been the Leading Semiconductor Material for Microelectronic Circuits for Decades
Basics of Microstructuring 01 Chapter MicroChemicals® – Fundamentals of Microstructuring www.microchemicals.com/downloads/application_notes.html SILICON INGOT PRODUCTION PROCESS FOR WAFERS The element silicon has been the leading semiconductor material for microelectronic circuits for decades. It can be produced in an extremely pure mono-crystalline form and doped with foreign materials in a targeted manner allowing for the modulation of the electrical conductivity over approx. six orders of magnitude. A great advantage of silicon compared to other semiconductor materials such as germanium or gallium arsenide is the possibility of generating a chemically stable electrical insulator with high breakdown fi eld strength from the substrate itself using selective thermal oxidation to SiO2. As a substrate for microelectronic circuits, silicon must be mono-crystalline in its purest form as described in this chapter. From Quartz to High-Purity Silicon Origin and Occurrence of Silicon Universe: 0.1 % Si Silicon fuses in the interior of massive suns at temperatures above 109 K from oxygen cores and is fl ung into the uni- Nuclear Fusion: Crust: 28 % Si verse at the end of the star’s life during 2 16O 28Si + 4He supernova explosions. Hydrogen and Earth: 17 % Si helium dominate the visible matter of the universe; silicon makes up less than 0.1% of the total mass (Fig. 1). Core: 7 % Si In our solar system formed from the "ashes" of earlier star explosions, silicon has been enriched, especially in the in- ner planets which have lost most of the volatile elements due to their proxim- ity to the central sun. The entire plan- et Earth contains approx. -
Aluminum Foundry Products
ASM Handbook, Volume 2: Properties and Selection: Nonferrous Alloys and Special-Purpose Materials Copyright © 1990 ASM International® ASM Handbook Committee, p 123-151 All rights reserved. DOI: 10.1361/asmhba0001061 www.asminternational.org Aluminum Foundry Products Revised by A. Kearney, Avery Kearney & Company Elwin L. Rooy, Aluminum Company of America ALUMINUM CASTING ALLOYS are wrought alloys. Aluminum casting alloys cast aluminum alloys are grouped according the most versatile of all common foundry must contain, in addition to strengthening to composition limits registered with the alloys and generally have the highest cast- elements, sufficient amounts of eutectic- Aluminum Association (see Table 3 in the ability ratings. As casting materials, alumi- forming elements (usually silicon) in order article "Alloy and Temper Designation Sys- num alloys have the following favorable to have adequate fluidity to feed the shrink- tems for Aluminum and Aluminum Al- characteristics: age that occurs in all but the simplest cast- loys"). Comprehensive listings are also • Good fluidity for filling thin sections ings. maintained by general procurement specifi- The phase behavior of aluminum-silicon • Low melting point relative to those re- cations issued through government agencies compositions (Fig. 1) provides a simple quired for many other metals (federal, military, and so on) and by techni- • Rapid heat transfer from the molten alu- eutectic-forming system, which makes pos- cal societies such as the American Society sible the commercial viability of most high- minum to the mold, providing shorter for Testing and Materials and the Society of casting cycles volume aluminum casting. Silicon contents, Automotive Engineers (see Table 1 for ex- • Hydrogen is the only gas with apprecia- ranging from about 4% to the eutectic level amples). -
Metal Forming Process
METAL FORMING PROCESS Unit 1:Introduction and concepts Manufacturing Processes can be classified as i) Casting ii) Welding iii) Machining iv)Mechanical working v) Powder Metallurgy vi)Plastic Technology etc., In Mechanical working Process the raw material is converted to a given shape by the application of external force. The metal is subjected to stress.It is a process of changing the shape and size of the material under the influence of external force or stress.Plastic Deformation occurs. Classification of Metal Working Processes 1. General classification i. Rolling ii. Forging iii. Extrusion iv. Wire Drawing v. Sheet Metal Forming 2. Based on Temperature of Working i. Hot Working ii. Cold Working iii. Warm Working 3. Based on the applied stress i. Direct Compressive Stress ii. Indirect Compressive Stress iii. Tensile Stress iv. Bending Stress v. Shear Stress Classification of Metal Working based on temperature. Hot working: It is defined as the mechanical working of metal at an elevated (higher) temperature above a particular temperature. This temperature is referred to RCT(Re Crystallization Temperature). Cold Working: It is defined as the mechanical working of metal below RCT. Warm Working: It is defined as the mechanical working of metal at a temperature between that of Hot working and Cold Working. Ingot is the starting raw metal for all metal working process. Molten metal from the furnace is taken and poured into metallic moulds and allowed to cool or solidify. The cooled solid metal mass is then taken out of the mould. This solid metal is referred to as Ingot.This Ingot is later on converted to other forms by mechanical working. -
Control in Semiconductor Wafer Manufacturing
Control in Semiconductor Wafer Manufacturing Abbas Emami-Naeini and Dick de Roover have turned to single-wafer processes which require precise Abstract: A semiconductor wafer undergoes a wide range of processes before it is transformed from a bare silicon wafer to one control. Interestingly, the processes that make the chip are populated with millions of transistor circuits. Such processes now beginning to use controllers which require the include Physical or Chemical Vapor Deposition, (PVD, CVD), computational power of the chips being fabricated. Another Chemical-Mechanical Planarization (CMP), Plasma Etch, Rapid trend is to conduct several related steps in a “cluster” Thermal Processing (RTP), and photolithography. As feature sizes comprising of several chambers integrated into a single keep shrinking, process control plays an increasingly important machine. role in each of these processes. A model-based control approach is an effective means of designing commercial controllers for The processes that deal with producing the integrated advanced semiconductor equipment. We will give an overview of circuit (IC) on the wafer are commonly referred to as “front- the applications of advanced control in the semiconductor industry. end” processes, whereas “back-end” processes deal with It is our experience that the best models for control design borrow wire bonding and packaging the IC. In this paper, we will heavily from the physics of the process. The manner in which focus on the “front-end” processes that produce the IC on these models are used for a specific control application depends on the silicon wafer, and the increasingly important role of the performance goals. In some cases such as RTP and lithography, the closed-loop control depends entirely on having control. -
Optimization of Mixed Casting Processes Considering Discrete
Journal of Mechanical Science and Technology Journal of Mechanical Science and Technology 23 (2009) 1899~1910 www.springerlink.com/content/1738-494x DOI 10.1007/s12206-009-0428-y Optimization of mixed casting processes considering discrete ingot sizes† Yong Kuk Park1,* and Jung-Min Yang2 1School of Mechanical and Automotive Engineering, Catholic University of Daegu, Hayang-Eup, Gyeongsan-si, Gyeongbuk, 712-702, Korea 2Department of Electrical Engineering, Catholic University of Daegu, Hayang-Eup, Gyeongsan-si, Gyeongbuk, 712-702, Korea (Manuscript Received September 18, 2008; Revised March 23, 2009; Accepted March 26, 2009) -------------------------------------------------------------------------------------------------------------------------------------------------------------------------------------------------------------------------------------------------------- Abstract Using linear programming (LP), this research devises a simple and comprehensive scheduling methodology for a complicated, yet typical, production situation in real foundries: a combination of expendable-mold casting, permanent- mold casting and automated casting for large-quantity castings. This scheduling technique to determine an optimal casting sequence is successfully applied to the most general case, in which various types of castings with different al- loys and masses are simultaneously produced by dissimilar casting processes within a predetermined period. The methodology proves to generate accurate scheduling results that maximize furnace or ingot efficiency. -
GAG Guidance Document 001
Global Advisory Group GAG - Guidance GAG Guidance Document 001 Terms and Definitions Edition 2009-01 March 2009 Global Advisory Group GAG – Guidance "Terms and Definitions" – 2009-01 Contents Introduction..................................................................................................................................................3 1. Scope .................................................................................................................................................3 2. Aluminium products.........................................................................................................................4 2.1. Aluminium ...........................................................................................................................................4 2.2. Alloys, alloying elements and impurities.............................................................................................4 2.3. Materials and products .......................................................................................................................5 2.4. Unwrought products, excepting castings............................................................................................6 2.5. Castings..............................................................................................................................................6 2.6. Sheet and plate...................................................................................................................................7 2.7. Foil ......................................................................................................................................................9 -
Environmentally Benign Silicon Solar Cell Manufacturing
July 1998 ! NREL/CP-590-23902 Environmentally Benign Silicon Solar Cell Manufacturing Y.S. Tsuo, J.M. Gee, P. Menna, D.S. Strebkov, A. Pinov, and V. Zadde Presented at the 2nd World Conference and Exhibition on Photovoltaic Solar Energy Conversion; 6-10 July 1998; Vienna, Austria National Renewable Energy Laboratory 1617 Cole Boulevard Golden, Colorado 80401-3393 A national laboratory of the U.S. Department of Energy Managed by the Midwest Research Institute For the U.S. Department of Energy Under Contract No. DE-AC36-83CH10093 ENVIRONMENTALLY BENIGN SILICON SOLAR CELL MANUFACTURING Y.S. Tsuo National Renewable Energy Laboratory, Golden, CO 80401, USA Phone: 303-384-6433, Fax: 303-384-6531, E-mail: [email protected] J.M. Gee Sandia National Laboratories, Albuquerque, NM 87185, USA Phone: 505-844-7812, Fax: 505-844-6541, E-mail: [email protected] P. Menna National Agency for New Technologies Energy & Environment, I-80055 Portici, Italy Phone: 39-81-772-3205, Fax: 772-3299, E-mail: [email protected] D.S. Strebkov, A. Pinov, and V. Zadde Intersolarcenter, Moscow 109456, Russia Phone: 7-095-171-1920, Fax: 7-095-170-5101, E-mail: [email protected] ABSTRACT: The manufacturing of silicon devices - from polysilicon production, crystal growth, ingot slicing, wafer cleaning, device processing, to encapsulation - requires many steps that are energy intensive and use large amounts of water and toxic chemicals. In the past two years, the silicon integrated-circuit (IC) industry has initiated several programs to promote environmentally benign manufacturing, i.e., manufacturing practices that recover, recycle, and reuse materials resources with a minimal consumption of energy.