A Critical Review on Special Forming Processes and Associated Research for Lightweight Components Based on Sheet and Tube Materials
Total Page:16
File Type:pdf, Size:1020Kb
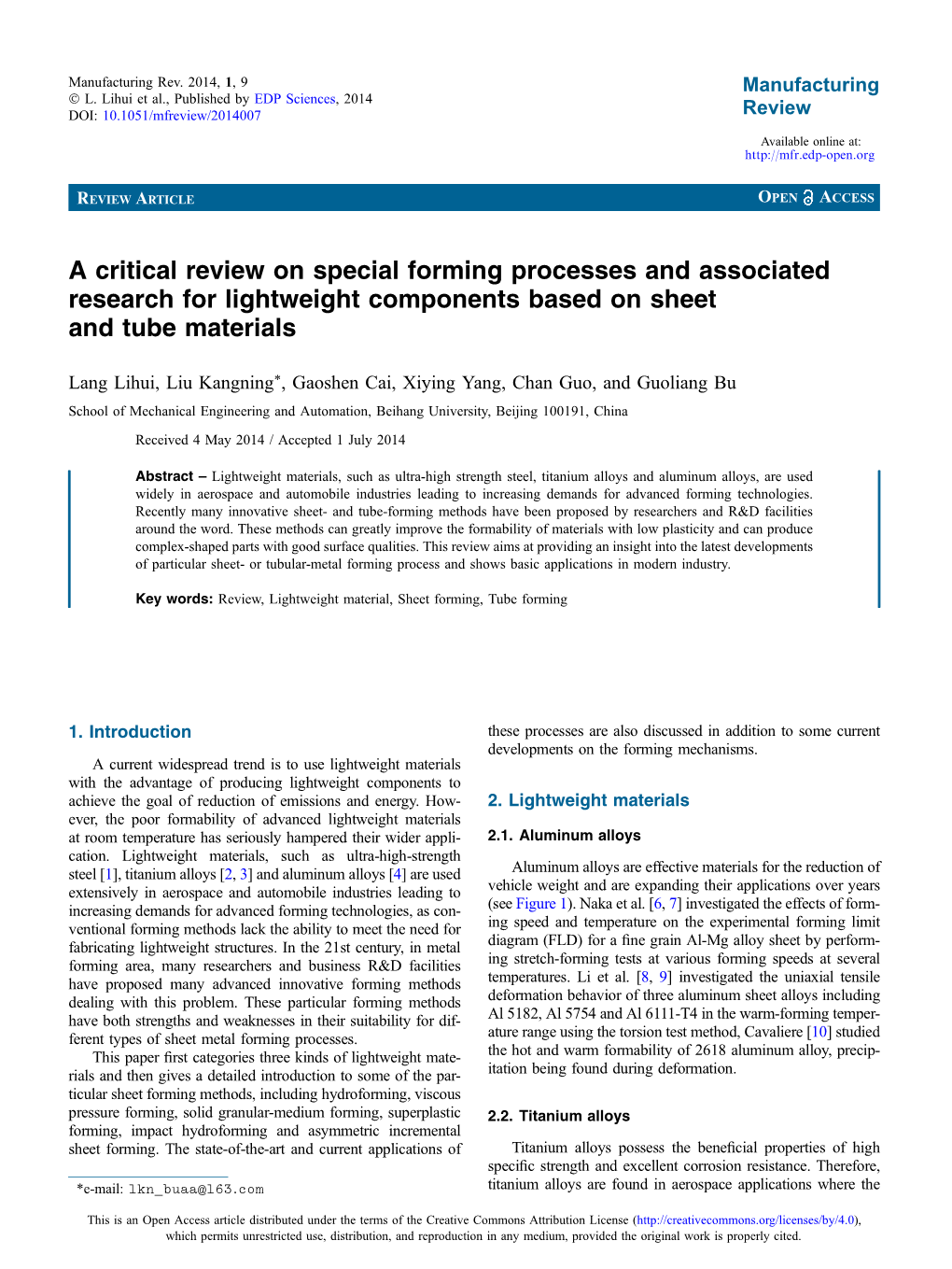
Load more
Recommended publications
-
Simulation of Tube Hydroforming Process Using Bidimensional Finite Element Analysis with Hyperworks
IJISET - International Journal of Innovative Science, Engineering & Technology, Vol. 3 Issue 5, May 2016. www.ijiset.com ISSN 2348 – 7968 Simulation of tube hydroforming process using bidimensional finite element analysis with HyperWorks Juan Carlos Cisneros1, Isaías Angel2 1 Engineering Department, UPAEP/ Electronic Faculty, Puebla, Puebla, 72410, Mexico 2 AgDesign, Inc., 2491 Simpson St. Kingsburg, CA 93631, USA Abstract the action of a pressurized fluid, that usually is water mixed with anticorrosive additives. In this process Nowadays, an intense competition exists among the many tools are required, like: a vise to hold raw manufacturing enterprises that try to bring to the market material, a pressure supply system, pistons for the products with a better quality, the least cost and as fast as supply of axial feeding (in case of tube hydroforming) possible. Because of this, particularly the automotive ones and a process control system. are looking for alternatives that will improve their production processes. The hydroforming process for The industry with more benefits by the tubular parts had benefited manufacturing industries, hydroforming and specially by the tube hydroforming especially the automotive industry. This because by this is the process it is possible to obtain complex geometry pieces, lighter, more resistant, made with fewer steps and at the automotive one, that has implemented this technique lowest price, which would have been harder with other in their products for reducing the parts fabrication methods. In this work, the simulation of tubes’ steps, obtaining a greater component’s resistance, hydroforming process is presented into a virtual minimizing the cost of tools, achieving more tight environment of Finite Element Analysis, this to obtain the tolerances compared to the stamping process and appropriate hydroforming parameters for the Elbow Pipe piece that takes part of the exhaust system of an automobile above all lower manufacturing costs [2]. -
Under the Direction of Dr. Gracious Ngaile)
ABSTRACT LOWRIE, JAMES BALLANFONTE. Development of a Micro-Tube Hydroforming System. (Under the direction of Dr. Gracious Ngaile). The rising demand for small parts with complex shapes for micro-electrical mechanical systems (MEMS) and medical applications has caused researchers to focus on metal forming as a possible way to mass produce miniature components. Studies into the miniaturization of macro-scale metal forming processes have mainly been focused in the sheet metal and extrusion fields and only a few researchers have attempted to take on the problem of miniaturizing the tube hydroforming process. The research that has been done into micro- tube hydroforming has been limited to simple expansion studies and no researchers have yet been able to combine axial feeding of the ends of the micro-tubular blank with simultaneous expansion of the tube. This has significantly reduced the complexity of the micro-parts which can be created using the tube hydroforming system. Combining material feed and expansion must be accomplished in order to create a micro-tube hydroforming process which is capable of producing metallic components with complex tubular geometries. The major objective of the research presented in this thesis is the development of a micro- tube hydroforming system which is capable supplying both axial feed and expansion to the tube simultaneously. This was accomplished by first breaking down the concepts of the conventional hydroforming tooling so that they could be analyzed for problems when being scaled down. Once the problems with the conventional tooling and the basic needs of the hydroforming system were established, the information was used to develop a new form a hydroforming tooling, called floating die tooling, which could apply both material feed and expansion to tubular blanks. -
Superplastic Forming, Electromagnetic Forming, Age Forming, Warm Forming, and Hydroforming
ANL-07/31 Innovative Forming and Fabrication Technologies: New Opportunities Final Report Energy Systems Division About Argonne National Laboratory Argonne is a U.S. Department of Energy laboratory managed by UChicago Argonne, LLC under contract DE-AC02-06CH11357. The Laboratory’s main facility is outside Chicago, at 9700 South Cass Avenue, Argonne, Illinois 60439. For information about Argonne, see www.anl.gov. Availability of This Report This report is available, at no cost, at http://www.osti.gov/bridge. It is also available on paper to the U.S. Department of Energy and its contractors, for a processing fee, from: U.S. Department of Energy Office of Scientific and Technical Information P.O. Box 62 Oak Ridge, TN 37831-0062 phone (865) 576-8401 fax (865) 576-5728 [email protected] Disclaimer This report was prepared as an account of work sponsored by an agency of the United States Government. Neither the United States Government nor any agency thereof, nor UChicago Argonne, LLC, nor any of their employees or officers, makes any warranty, express or implied, or assumes any legal liability or responsibility for the accuracy, completeness, or usefulness of any information, apparatus, product, or process disclosed, or represents that its use would not infringe privately owned rights. Reference herein to any specific commercial product, process, or service by trade name, trademark, manufacturer, or otherwise, does not necessarily constitute or imply its endorsement, recommendation, or favoring by the United States Government or any agency thereof. The views and opinions of document authors expressed herein do not necessarily state or reflect those of the United States Government or any agency thereof, Argonne National Laboratory, or UChicago Argonne, LLC. -
Magnesium Casting Technology for Structural Applications
Available online at www.sciencedirect.com Journal of Magnesium and Alloys 1 (2013) 2e22 www.elsevier.com/journals/journal-of-magnesium-and-alloys/2213-9567 Full length article Magnesium casting technology for structural applications Alan A. Luo a,b,* a Department of Materials Science and Engineering, The Ohio State University, Columbus, OH, USA b Department of Integrated Systems Engineering, The Ohio State University, Columbus, OH, USA Abstract This paper summarizes the melting and casting processes for magnesium alloys. It also reviews the historical development of magnesium castings and their structural uses in the western world since 1921 when Dow began producing magnesium pistons. Magnesium casting technology was well developed during and after World War II, both in gravity sand and permanent mold casting as well as high-pressure die casting, for aerospace, defense and automotive applications. In the last 20 years, most of the development has been focused on thin-wall die casting ap- plications in the automotive industry, taking advantages of the excellent castability of modern magnesium alloys. Recently, the continued expansion of magnesium casting applications into automotive, defense, aerospace, electronics and power tools has led to the diversification of casting processes into vacuum die casting, low-pressure die casting, squeeze casting, lost foam casting, ablation casting as well as semi-solid casting. This paper will also review the historical, current and potential structural use of magnesium with a focus on automotive applications. The technical challenges of magnesium structural applications are also discussed. Increasing worldwide energy demand, environment protection and government regulations will stimulate more applications of lightweight magnesium castings in the next few decades. -
Determination of Process Parameters for Stamping and Sheet Hydroforming of Sheet Metal Parts Using Finite Element Method
DETERMINATION OF PROCESS PARAMETERS FOR STAMPING AND SHEET HYDROFORMING OF SHEET METAL PARTS USING FINITE ELEMENT METHOD DISSERTATION Presented in Partial Fulfillment of the Requirements for the Degree Doctor of Philosophy in the Graduate School of The Ohio State University By Hariharasudhan Palaniswamy, M.S. * * * * * The Ohio State University 2007 Dissertation Committee: Approved by Professor. Taylan Altan, Adviser __________________________ Professor. Gary L. Kinzel Adviser Professor. Henry R. Busby Graduate program in Mechanical Engineering Professor. Jerald R. Brevick Copyright by Hariharasudhan Palaniswamy 2007 ABSTRACT Increase in the complexity of the parts and emphasis on the low formability and expensive lightweight materials require the use of multipoint cushion systems in modern presses and optimal blank shapes. Thus, better control of metal flow can be achieved for increasing the drawability and reducing the scrap rate and manufacturing cost in sheet metal forming. The blank holder force (BHF) / cushion pin force /cylinder force required to program the multipoint cushion system for forming a part is difficult and costly to estimate by trial and error FE simulation and die tryouts as there more than one variable to change. Hence, multipoint cushion system available in a modern press is hardly used in practice. Estimation of BHF to program the multipoint cushion system could be best done through structured FE simulations in process design stage so that its advantages can be incorporated in process design and carried forward to die tryout and production to realize its potential. Successful application of FE simulations in stamping process design depends on the accuracy of the input parameters. Conventionally, properties of sheet materials obtained from tensile test are used in FE simulation. -
Manufacturing Technology I Unit I Metal Casting
MANUFACTURING TECHNOLOGY I UNIT I METAL CASTING PROCESSES Sand casting – Sand moulds - Type of patterns – Pattern materials – Pattern allowances – Types of Moulding sand – Properties – Core making – Methods of Sand testing – Moulding machines – Types of moulding machines - Melting furnaces – Working principle of Special casting processes – Shell – investment casting – Ceramic mould – Lost Wax process – Pressure die casting – Centrifugal casting – CO2 process – Sand Casting defects. UNIT II JOINING PROCESSES Fusion welding processes – Types of Gas welding – Equipments used – Flame characteristics – Filler and Flux materials - Arc welding equipments - Electrodes – Coating and specifications – Principles of Resistance welding – Spot/butt – Seam – Projection welding – Percusion welding – GS metal arc welding – Flux cored – Submerged arc welding – Electro slag welding – TIG welding – Principle and application of special welding processes – Plasma arc welding – Thermit welding – Electron beam welding – Friction welding – Diffusion welding – Weld defects – Brazing – Soldering process – Methods and process capabilities – Filler materials and fluxes – Types of Adhesive bonding. UNIT III BULK DEFORMATION PROCESSES Hot working and cold working of metals – Forging processes – Open impression and closed die forging – Characteristics of the process – Types of Forging Machines – Typical forging operations – Rolling of metals – Types of Rolling mills – Flat strip rolling – Shape rolling operations – Defects in rolled parts – Principle of rod and wire drawing – Tube drawing – Principles of Extrusion – Types of Extrusion – Hot and Cold extrusion – Equipments used. UNIT IV SHEET METAL PROCESSES Sheet metal characteristics – Typical shearing operations – Bending – Drawing operations – Stretch forming operations –– Formability of sheet metal – Test methods – Working principle and application of special forming processes – Hydro forming – Rubber pad forming – Metal spinning – Introduction to Explosive forming – Magnetic pulse forming – Peen forming – Super plastic forming. -
Module 3 Selection of Manufacturing Processes
Module 3 Selection of Manufacturing Processes Lecture 4 Design for Sheet Metal Forming Processes Instructional objectives By the end of this lecture, the student will learn the principles of several sheet metal forming processes and measures to be taken during these process to avoid various defects. Sheet Metal Forming Processes Sheet metals are widely used for industrial and consumer parts because of its capacity for being bent and formed into intricate shapes. Sheet metal parts comprise a large fraction of automotive, agricultural machinery, and aircraft components as well as consumer appliances. Successful sheet metal forming operation depends on the selection of a material with adequate formability, appropriate tooling and design of part, the surface condition of the sheet material, proper lubricants, and the process conditions such as the speed of the forming operation, forces to be applied, etc. A numbers of sheet metal forming processes such as shearing, bending, stretch forming, deep drawing, stretch drawing, press forming, hydroforming etc. are available till date. Each process is used for specific purpose and the requisite shape of the final product. Shearing Irrespective of the size of the part to be produced, the first step involves cutting the sheet into appropriate shape by the process called shearing. Shearing is a generic term which includes stamping, blanking, punching etc. Figure 3.4.1 shows a schematic diagram of shearing. When a long strip is cut into narrower widths between rotary blades, it is called slitting. Blanking is the process where a contoured part is cut between a punch and die in a press. The same process is also used to remove the unwanted part of a sheet, but then the process is referred to punching. -
Role of Hydraulic Fluid Pressure in Sheet Metal Forming
International Journal of Emerging Technologies in Engineering Research (IJETER) Volume 5, Issue 9, September (2017) www.ijeter.everscience.org Role of Hydraulic Fluid Pressure in Sheet Metal Forming Dr.R.Uday Kumar Associate Professor, Dept. Of Mechanical Engineering, Mahatma Gandhi Institute of Technology, Gandipet, Hyderabad – 500075, India. Abstract – The stamping of parts from sheet metal is a During forming, a combination of increasing internal fluid straightforward operation in which the metal is shaped or cut pressure and a simultaneous axial pressing on the tube ends by through deformation by shearing, punching, drawing, stretching, the sealing punches cause the tubular material to flow into the bending, coining, etc. Production rates are high and secondary contours of the die. Tubular hydro forming is generally divided machining is generally not required to produce finished parts into three operating techniques: Low-Pressure Hydro forming within tolerances. This versatile process lends itself to low costs, since complex parts can be made in a few operations at high uses fluid pressures of 12,000 PSI/828 BAR or less. Cycle time production rates. Sheet metal has a high strength-to-weight is less than with other hydroforming methods, but components factor, enabling production of parts that are lightweight and must be designed carefully to form properly using the lower strong. Hydroforming process is divided into two main groups; fluid pressures (3-6). sheet hydroforming and tube hydroforming. Tube HydroForming (THF) is a process of forming hollow parts with different cross High-Pressure hydroforming uses fluid pressures ranging from sections by applying simultaneously an internal hydraulic 20,000 to 100,000 PSI/1,379 to 6,895 BAR. -
Sheet Metalworking Terminology Sheet-Metal Characteristics • Elongation – the Capability of the Sheet Metal to Stretch Without Necking and Failure
ME477 Fall 2004 Introduction SHEET • Cutting and forming thin sheets of metal usually performed as cold working METALWORKING • Sheet metal = 0.4 (1/64) to 6 mm (1/4in) thick 1. Cutting Operation • Plate stock > 6 mm thick 2. Bending Operation • Advantage - High strength, good dimensional 3. Drawing accuracy, good surface finish, economical mass 4. Other Sheet-metal Forming production (low cost). 5. Dies and Presses • Cutting, bending, drawing γ 6. Sheet-metal Operation ε1 Localized necking 7. Bending of Tube Stock θ=55° Because ν=0.5 in plasticity, ε =-2ε =-2ε ε3,ε2 ε1 ε ε2 1 2 3 2θ 1 2 Sheet Metalworking Terminology Sheet-metal Characteristics • Elongation – the capability of the sheet metal to stretch without necking and failure. • “Punch-and-die” • Yield-point elongation – Lüeder’s bands on Low-carbon steels and Al-Mg alloys. – Tooling to perform cutting, bending, and Lüder’s bands can be eliminated by cold-rolling the drawing thickness by 0.5-1.5%. Yupper • “Stamping press” Ylower – Machine tool that performs most sheet metal • Anisotropy operations – Crystallographic and mechanical fibering anisotropy • Grain Size effect on mechanical properties • “Stampings” • Residual Stress, Springback and Wrinkling – Sheet metal products • Testing method – Cupping test – Forming Limit Diagram 3 4 1. Cutting Operation Cutting Operation • Cutting operation – Plastic deformation Punch – Penetration (1/3 thickness) t –Fracture • Shearing using a machine called power Die shear or square shear. c • Blanking – shearing a closed outline Rollover part (desired part called blank) Burnish • Punching – sheared part is slag (or scrap) and remaining stock is a desired part Fracture zone Burr 5 6 part Kwon 1 ME477 Fall 2004 Analysis Die, blank and punch size • Clearance - 4-8% but sometime 1% of thickness For a round blank, – Too small – fracture does not occur requiring more force. -
Design of Roll Forming Mill
SSRG International Journal of Mechanical Engineering Volume 8 Issue 4, 1-19, April 2021 ISSN: 2348 – 8360 /doi:10.14445/23488360/IJME-V8I4P101 ©2021 Seventh Sense Research Group® Design of Roll Forming Mill Kondusamy V#1, Jegatheeswaran D#2, Vivek S#3, Vidhuran D#4, Harishragavendra A#5 1Faculty Advisor, Karpagam College of Engineering, Coimbatore 2Research Scholar, Karpagam College of Engineering, Coimbatore 3Research Scholar, Karpagam College of Engineering, Coimbatore 4Research Scholar, Karpagam College of Engineering, Coimbatore 5Research Scholar, Karpagam College of Engineering, Coimbatore Received Date: 01 March 2021 Revised Date: 15 April 2021 Accepted Date: 17 April 2021 Abstract - Sheet metal forming is widely used by the industries in the current scenario. Bending, Spinning, Deep drawing, Stretch forming & Roll forming is the major sheet metal forming processes. In this, roll forming is a unique continuous forming process, where 2D sheet metal is formed into various profiles like Rooftops, Window frames, Storage columns, etc., by using series of mated rollers. This project focuses on design considerations of roll forming tools and process parameters for a roll forming line. This design consideration discusses certain issues in the design of the roll forming tool, which includes Unfold length calculation, Figure 1.1: (a) Kitchen sinks (b) Storage columns Flower pattern design, and Roller design by using an analytical solution. The constant bend allowance (arc) (c) Exhaust systems method of flower patterning was used to find the dimensions for the 2D die design. This dimension includes web length, II. DIFFERENT SHEET METAL PROCESSES AND flange length, and radius at each bend for both upper and PRODUCTS In the present scenario, demand for sheet metal products is lower roller. -
2. Technology Metal Forming
2. Technology Metal Forming Technology: Metal Forming • Metal forming includes a large group of manufacturing processes in which plastic deformation is used to change the shape of metal work pieces • Plastic deformation: a permanent change of shape, i.e., the stress in materials is larger than its yield strength • Usually a die is needed to force deformed metal into the shape of the die Metal Forming • Metal with low yield strength and high ductility is in favor of metal forming • One difference between plastic forming and metal forming is Plastic: solids are heated up to be polymer melt Metal: solid state remains in the whole process 4 groups of forming techniques: • Rolling, • Forging & extrussion, • Wire drawing, • Deep drawing. Bars shaping vs. Sheets shaping Rolling Flat (plates) rolling Cross rolling slant rolling (for tubes production) Forging & extrussion Macroetched structure of a hot forged hook (a) Relative forgability for different metals and alloys. This information can be directly used for open die forgings. (b) Ease of die filling as a function of relative forability and flow stress/forging pressure – applicable to closed die forging Wire drawing In and conventional wire drawing process, the diameter of a rod or wire is reduced by pulling it through a conical die Illustration of some drawing operations: (a) conventional wire drawing with circular cross-section; (b) wire drawing with rectangular cross-section, using so-called ‘Turk’s’ head; (c) drawing using a floating mandrel. Sheet metal forming Equi-biaxial streching using a clamped sheet and a hemispherical punch (left) and a schematic of an industrial strech-forming operation (right). -
Use of Resin Tooling with Sheet Metal Hydroforming for the Manufacture of Aluminum Alloy Cases
Proceedings of the 12th International Conference on 2069 Aluminium Alloys, SeptemberSeptember 5-9, 2010, Yokohama, Japan ©2010©2010 The Japan Institute of Light Metals pp. 2069-2074 Use of Resin Tooling with Sheet Metal Hydroforming for the Manufacture of Aluminum Alloy Cases Ching-Tsai Wu1,2, Ming-Fu Li1, Chun-Chieh Wang1, Kai-Shen Wang3 and Wan-Wen Zheng3 1 Metal Industries Research & Development Centre, 1001 Kaonan Highway, Kaohsiung, Taiwan. 2Mechanical Engineering Department, Cheng Kung University, No.1, University Road, Tainan, Taiwan. 3Hua-Chuang Automobile Information Technical Center, 2F., No.3, Sec. 3, Zhongxing Rd., Xindian City, Taipei County 231, Taiwan Taiwan. Products are continuously undergoing evolution according to changes in trends, and the need for a high surface quality, complicated shapes, and special materials make this kind of product more and more difficult to fabricate. A product of complex geometry with detailed features is not suitable for production by a conventional forming process, but the Sheet Metal Hydroforming (SHF) process can be employed to produce very detailed features. In this study, we integrated the SHF process with a resin tooling method for the rapid manufacture of products of minimal variety in low quantities, resulting in the reduction of both cost and time. We manufactured a freeform house with a small radius fillet using SHF with resin tooling in a unique and novel process. The process involved the forming of twenty pieces using Al 5052 and SUS 304 sheet plates, and the number of items fabricated, dimensional accuracy, and endurance to wear and tear of the tools was then used to evaluate the applicability of the method in a real manufacturing process.