Modeling a Hydraulic Hybrid Drivetrain: Efficiency
Total Page:16
File Type:pdf, Size:1020Kb
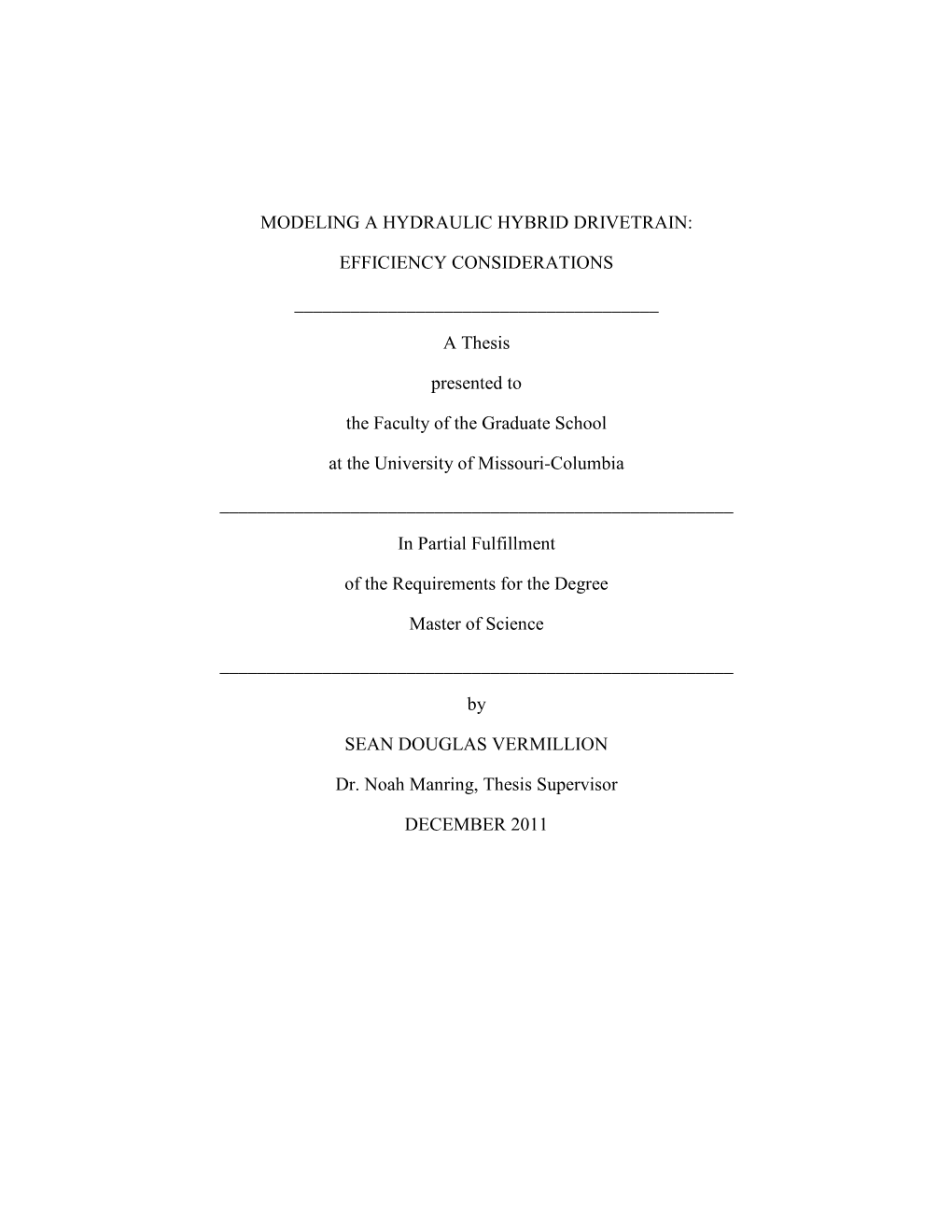
Load more
Recommended publications
-
RC Baja: Drivetrain Nick Paulay [email protected]
Central Washington University ScholarWorks@CWU All Undergraduate Projects Undergraduate Student Projects Winter 2019 RC Baja: DriveTrain Nick Paulay [email protected] Follow this and additional works at: https://digitalcommons.cwu.edu/undergradproj Part of the Mechanical Engineering Commons Recommended Citation Paulay, Nick, "RC Baja: DriveTrain" (2019). All Undergraduate Projects. 79. https://digitalcommons.cwu.edu/undergradproj/79 This Undergraduate Project is brought to you for free and open access by the Undergraduate Student Projects at ScholarWorks@CWU. It has been accepted for inclusion in All Undergraduate Projects by an authorized administrator of ScholarWorks@CWU. For more information, please contact [email protected]. Central Washington University MET Senior Capstone Projects RC Baja: Drivetrain By Nick Paulay (Partner: Hunter Jacobson-RC Baja Suspension & Steering) 1 Table of Contents Introduction Description Motivation Function Statement Requirements Engineering Merit Scope of Effort Success Criteria Design and Analyses Approach: Proposed Solution Design Description Benchmark Performance Predictions Description of Analyses Scope of Testing and Evaluation Analyses Tolerances, Kinematics, Ergonomics, etc. Technical Risk Analysis Methods and Construction Construction Description Drawing Tree Parts list Manufacturing issues Testing Methods Introduction Method/Approach/Procedure description Deliverables Budget/Schedule/Project Management Proposed Budget Proposed Schedule Project Management Discussion Conclusion Acknowledgements References Appendix A – Analyses Appendix B – Drawings Appendix C – Parts List Appendix D – Budget Appendix E – Schedule Appendix F - Expertise and Resources 2 Appendix G –Testing Data Appendix H – Evaluation Sheet Appendix I – Testing Report Appendix J – Resume 3 Abstract The American Society of Mechanical Engineers (ASME) annually hosts an RC Baja challenge, testing a RC car in three events: slalom, acceleration and Baja. -
Hybrid Electric Vehicles: a Review of Existing Configurations and Thermodynamic Cycles
Review Hybrid Electric Vehicles: A Review of Existing Configurations and Thermodynamic Cycles Rogelio León , Christian Montaleza , José Luis Maldonado , Marcos Tostado-Véliz * and Francisco Jurado Department of Electrical Engineering, University of Jaén, EPS Linares, 23700 Jaén, Spain; [email protected] (R.L.); [email protected] (C.M.); [email protected] (J.L.M.); [email protected] (F.J.) * Correspondence: [email protected]; Tel.: +34-953-648580 Abstract: The mobility industry has experienced a fast evolution towards electric-based transport in recent years. Recently, hybrid electric vehicles, which combine electric and conventional combustion systems, have become the most popular alternative by far. This is due to longer autonomy and more extended refueling networks in comparison with the recharging points system, which is still quite limited in some countries. This paper aims to conduct a literature review on thermodynamic models of heat engines used in hybrid electric vehicles and their respective configurations for series, parallel and mixed powertrain. It will discuss the most important models of thermal energy in combustion engines such as the Otto, Atkinson and Miller cycles which are widely used in commercial hybrid electric vehicle models. In short, this work aims at serving as an illustrative but descriptive document, which may be valuable for multiple research and academic purposes. Keywords: hybrid electric vehicle; ignition engines; thermodynamic models; autonomy; hybrid configuration series-parallel-mixed; hybridization; micro-hybrid; mild-hybrid; full-hybrid Citation: León, R.; Montaleza, C.; Maldonado, J.L.; Tostado-Véliz, M.; Jurado, F. Hybrid Electric Vehicles: A Review of Existing Configurations 1. Introduction and Thermodynamic Cycles. -
ICOM North American LLC Comments
DOCKETED Docket 16-ALT-02 Number: Project Title: 2017-2018 Investment Plan Update for the Alternative and Renewable Fuel and Vehicle Technology Program TN #: 214418 Document Title: ICOM North American LLC Comments: alt-fuel near zero engines and alt- fuel hybrids Description: N/A Filer: System Organization: ICOM North American LLC Submitter Role: Public Submission 11/7/2016 4:47:41 PM Date: Docketed Date: 11/7/2016 Comment Received From: jon vanbogart Submitted On: 11/7/2016 Docket Number: 16-ALT-02 alt-fuel near zero engines and alt-fuel hybrids Additional submitted attachment is included below. November 7, 2016 California Energy Commission 1516 Ninth Street Sacramento, CA 95814 Re: Comments on the 2017-2018 Investment Plan Update for the Alternative and Renewable Fuel and Vehicle Technology Program Dear California Energy Commissioners and Staff, ICOM North America LLC values the opportunity to provide comments on the 2017-2018 Investment Plan Update for the Alternative and Renewable Fuel and Vehicle Technology Program (ARFVTP). While we support the Energy Commission goals and investment in advanced transportation technologies to advance petroleum reduction goals and reduce emission for the State’s climate change initiatives. Near Zero – Lower NOx Engines and Alternative Fuel Hybrid Technology ICOM has provided sustainable fleets solutions for Propane-Autogas since 2004 with over 150 EPA certification covering more than 1000 vehicle platforms. As part of our 2017 strategy and beyond, ICOM will be offering CARB Certified Near Zero - Lower NOx engine technology for both Propane-AutoGas and CNG at or near the 0.02 NOx level for vehicle platforms above 14001 GVWR for both the Ford 6.8L and GM 6.0L engines. -
The Hybrid Vehicle and Alternative Fuel Report September 30, 2016
ISSN 1946-1011 The Hybrid Vehicle and Alternative Fuel Report September 30, 2016 The fine print: This report is a summary of articles appearing in popular, business, and technical media referring to the impact of fuel costs and fuel efficiency on vehicle technology, development, and markets. At the end of the report is a list of all articles summarized, with hyperlinks to internet sources where available. Some articles may require free registration or paid subscriptions to access. The Hybrid Vehicle and Alternative Fuel Report (ISSN: 1946-1011) is compiled, written, and edited by Thomas L. R. Smith, Ph. D. (hereinafter referred to as “The Editor”), Economic Analysis Branch of the Budget and Financial Analysis Division, Washington State Department of Transportation. Contact The Hybrid Vehicle and Alternative Fuel Report’s editor at [email protected] or (360) 705-7941. Contributions of news items, original articles, cookies, and positive comments about The Report are welcome. TABLE OF CONTENTS HYBRIDS .......................................................................................................................................................................... 1 ELECTRIC VEHICLES ...................................................................................................................................................... 1 ALTERNATIVE FUELS ..................................................................................................................................................... 4 COMING TO A LOCATION NEAR YOU -
EPRI Journal--Driving the Solution: the Plug-In Hybrid Vehicle
DRIVING THE SOLUTION THE PLUG-IN HYBRID VEHICLE by Lucy Sanna The Story in Brief As automakers gear up to satisfy a growing market for fuel-efficient hybrid electric vehicles, the next- generation hybrid is already cruis- ing city streets, and it can literally run on empty. The plug-in hybrid charges directly from the electricity grid, but unlike its electric vehicle brethren, it sports a liquid fuel tank for unlimited driving range. The technology is here, the electricity infrastructure is in place, and the plug-in hybrid offers a key to replacing foreign oil with domestic resources for energy indepen- dence, reduced CO2 emissions, and lower fuel costs. DRIVING THE SOLUTION THE PLUG-IN HYBRID VEHICLE by Lucy Sanna n November 2005, the first few proto vide a variety of battery options tailored 2004, more than half of which came from Itype plugin hybrid electric vehicles to specific applications—vehicles that can imports. (PHEVs) will roll onto the streets of New run 20, 30, or even more electric miles.” With growing global demand, particu York City, Kansas City, and Los Angeles Until recently, however, even those larly from China and India, the price of a to demonstrate plugin hybrid technology automakers engaged in conventional barrel of oil is climbing at an unprece in varied environments. Like hybrid vehi hybrid technology have been reluctant to dented rate. The added cost and vulnera cles on the market today, the plugin embrace the PHEV, despite growing rec bility of relying on a strategic energy hybrid uses battery power to supplement ognition of the vehicle’s potential. -
A Review of Range Extenders in Battery Electric Vehicles: Current Progress and Future Perspectives
Review A Review of Range Extenders in Battery Electric Vehicles: Current Progress and Future Perspectives Manh-Kien Tran 1,* , Asad Bhatti 2, Reid Vrolyk 1, Derek Wong 1 , Satyam Panchal 2 , Michael Fowler 1 and Roydon Fraser 2 1 Department of Chemical Engineering, University of Waterloo, 200 University Avenue West, Waterloo, ON N2L3G1, Canada; [email protected] (R.V.); [email protected] (D.W.); [email protected] (M.F.) 2 Department of Mechanical and Mechatronics Engineering, University of Waterloo, 200 University Avenue West, Waterloo, ON N2L3G1, Canada; [email protected] (A.B.); [email protected] (S.P.); [email protected] (R.F.) * Correspondence: [email protected]; Tel.: +1-519-880-6108 Abstract: Emissions from the transportation sector are significant contributors to climate change and health problems because of the common use of gasoline vehicles. Countries in the world are attempting to transition away from gasoline vehicles and to electric vehicles (EVs), in order to reduce emissions. However, there are several practical limitations with EVs, one of which is the “range anxiety” issue, due to the lack of charging infrastructure, the high cost of long-ranged EVs, and the limited range of affordable EVs. One potential solution to the range anxiety problem is the use of range extenders, to extend the driving range of EVs while optimizing the costs and performance of the vehicles. This paper provides a comprehensive review of different types of EV range extending technologies, including internal combustion engines, free-piston linear generators, fuel cells, micro Citation: Tran, M.-K.; Bhatti, A.; gas turbines, and zinc-air batteries, outlining their definitions, working mechanisms, and some recent Vrolyk, R.; Wong, D.; Panchal, S.; Fowler, M.; Fraser, R. -
A Comparative Analysis of Well-To-Wheel Primary Energy
Journal of Power Sources 249 (2014) 333e348 Contents lists available at ScienceDirect Journal of Power Sources journal homepage: www.elsevier.com/locate/jpowsour A comparative analysis of well-to-wheel primary energy demand and greenhouse gas emissions for the operation of alternative and conventional vehicles in Switzerland, considering various energy carrier production pathways Mashael Yazdanie*, Fabrizio Noembrini, Lionel Dossetto, Konstantinos Boulouchos Aerothermochemistry and Combustion Systems Laboratory, Institute of Energy Technology, Department of Mechanical and Process Engineering, Swiss Federal Institute of Technology Zurich, ML J41.3, Sonneggstrasse 3, 8092 Zurich, Switzerland highlights Operational GHG emissions and energy demand are found for alternative drivetrains. Well-to-wheel results are compared for several H2/electricity production pathways. Pluggable electric cars (PECs) yield the lowest WTW GHG emissions and energy demand. Fuel cell car WTW results are on par with PECs for direct chemical H2 production. ICE and hybrid cars using biogas and CNG also yield some of the lowest WTW results. article info abstract Article history: This study provides a comprehensive analysis of well-to-wheel (WTW) primary energy demand and Received 4 June 2013 greenhouse gas (GHG) emissions for the operation of conventional and alternative passenger vehicle Received in revised form drivetrains. Results are determined based on a reference vehicle, drivetrain/production process effi- 9 September 2013 ciencies, and lifecycle inventory data specific to Switzerland. WTW performance is compared to a gas- Accepted 12 October 2013 oline internal combustion engine vehicle (ICEV). Both industrialized and novel hydrogen and electricity Available online 21 October 2013 production pathways are evaluated. A strong case is presented for pluggable electric vehicles (PEVs) due to their high drivetrain efficiency. -
Prospects for Bi-Fuel and Flex-Fuel Light Duty Vehicles
Prospects for Bi-Fuel and Flex-Fuel Light-Duty Vehicles An MIT Energy Initiative Symposium April 19, 2012 MIT Energy Initiative Symposium on Prospects for Bi-Fuel and Flex-Fuel Light-Duty Vehicles | April 19, 2012 C Prospects for Bi-Fuel and Flex-Fuel Light-Duty Vehicles An MIT Energy Initiative Symposium April 19, 2012 ABOUT THE REPORT Summary for Policy Makers The April 19, 2012, MIT Energy Initiative Symposium addressed Prospects for Bi-Fuel and Flex-Fuel Light-Duty Vehicles. The symposium focused on natural gas, biofuels, and motor gasoline as fuels for light-duty vehicles (LDVs) with a time horizon of the next two to three decades. The important transportation alternatives of electric and hybrid vehicles (this was the subject of the 2010 MITEi Symposium1) and hydrogen/fuel-cell vehicles, a longer-term alternative, were not considered. There are three motivations for examining alternative transportation fuels for LDVs: (1) lower life cycle cost of transportation for the consumer, (2) reduction in the greenhouse gas (GHG) footprint of the transportation sector (an important contributor to total US GHG emissions), and (3) improved energy security resulting from greater use of domestic fuels and reduced liquid fuel imports. An underlying question is whether a flex-fuel/bi-fuel mandate for new LDVs would drive development of a robust alternative fuels market and infrastructure versus alternative fuel use requirements. Symposium participants agreed on these motivations. However, in this symposium in contrast to past symposiums, there was a striking lack of agreement about the direction to which the market might evolve, about the most promising technologies, and about desirable government action. -
Analysis of the Fuel Economy Benefit of Drivetrain Hybridization
NREL/CP-540-22309 ● UC Category: 1500 ● DE97000091 Analysis of the Fuel Economy Benefit of Drivetrain Hybridization Matthew R. Cuddy Keith B. Wipke Prepared for SAE International Congress & Exposition February 24—27, 1997 Detroit, Michigan National Renewable Energy Laboratory 1617 Cole Boulevard Golden, Colorado 80401-3393 A national laboratory of the U.S. Department of Energy Managed by Midwest Research Institute for the U.S. Department of Energy under contract No. DE-AC36-83CH10093 Work performed under Task No. HV716010 January 1997 NOTICE This report was prepared as an account of work sponsored by an agency of the United States government. Neither the United States government nor any agency thereof, nor any of their employees, makes any warranty, express or implied, or assumes any legal liability or responsibility for the accuracy, completeness, or usefulness of any information, apparatus, product, or process disclosed, or represents that its use would not infringe privately owned rights. Reference herein to any specific commercial product, process, or service by trade name, trademark, manufacturer, or otherwise does not necessarily constitute or imply its endorsement, recommendation, or favoring by the United States government or any agency thereof. The views and opinions of authors expressed herein do not necessarily state or reflect those of the United States government or any agency thereof. Available to DOE and DOE contractors from: Office of Scientific and Technical Information (OSTI) P.O. Box 62 Oak Ridge, TN 37831 Prices available by calling 423-576-8401 Available to the public from: National Technical Information Service (NTIS) U.S. Department of Commerce 5285 Port Royal Road Springfield, VA 22161 703-605-6000 or 800-553-6847 or DOE Information Bridge http://www.doe.gov/bridge/home.html Printed on paper containing at least 50% wastepaper, including 10% postconsumer waste 970289 Analysis of the Fuel Economy Benefit of Drivetrain Hybridization Matthew R. -
Drive Train Selection
Selecting the best drivetrains for your fleet vehicles Drivetrain Basics FWD RWD AWD 4WD Front-wheel drive Rear-wheel drive All-wheel drive (AWD) 4WD generally (FWD) is the most (RWD) is regaining vehicles drive all four requires manually common form of popularity due to wheels. AWD is used switching between engine/transmission consumer demand to market vehicles two-wheel drive for layout; the engine for performance; the that switch from two streets and a drives only the front engine drives only drive wheels to four four-wheel drive for wheels. the rear wheels. as needed. low traction areas. Two-wheel drive (2WD) is used to describe vehicles able to power two wheels at most. For vehicles with part-time four-wheel drive (4WD), the term refers to the mode when 4WD is deactivated and power is applied to only two wheels. Sedans | Minivans | Crossovers Pickups | Full-Size Vans | SUVs Generally FWD, RWD and AWD Generally 2WD and 4WD Element Fleet Management ® Acquisition Cost FWD RWD AWD 2WD 4WD FWD less expensive RWD can be more AWD generally most due to fewer expensive due to more expensive due to more 4WD is more expensive than 2WD due to components and more components and parts than FWD and heavier-duty components efficient manufacturing additional time to RWD assemble Select vehicles based on intended function and operating environment rather than acquisition cost, as these factors largely dictate operating costs Operating Expenses: Fuel Efficiency FWD RWD AWD 2WD 4WD FWD more efficient More parts for RWD More parts for AWD 2WD gets better -
Joining Forces an Electric Motor/Generator and Batter- Ies
HYBRID TECHNOLOGY Eaton’s parallel electric hybrid system. The vehicle’s diesel engine is coupled with Joining forces an electric motor/generator and batter- ies. It maintains a conventional drive- train architecture, such as Eaton’s Fuller UltraShift automated transmission, while A look at the work being done by OEMs and adding the ability to augment engine component suppliers to bring hydraulic and torque with electrical torque (Eaton photo). electric hybrid technology to on-highway trucks. are an inevitable by-product of burning by Michelle EauClaire hydrocarbon fuel. s a consumer, you can make fuel prices for nearly all of the vehicles used changes to your daily lifestyle in these applications is to improve their Electric and hydraulic Ain order to counteract the efficiency, and the best technology avail- There are two different kinds of effects of the rising fuel prices. Those able to do that today is hybrid technology. hybrids, electric and hydraulic. Electric options, however, don’t suit the obli- A hybrid powertrain system reduces hybrids more easily support other on- gations of commercial vehicle users. fuel consumption by blending the power board electronics and have a high energy Refuse has to be picked up, parcels generated by the internal combustion density — best suited to applications that need to be delivered, and the whole engine with power from other stored have a lot of cruising time because they scope of other services still need to be sources of energy on board. And of course, can support longer engine-off operation. provided, regardless of fuel prices. when you reduce fuel consumption, you Electric power is generated by the die- The only practical response to rising also reduce the polluting emissions that sel engine and through regenerative brak- 40 ■ OEM Off-Highway ■ March 2008 ing, which recovers power which would Glenn R. -
Energy Efficiency Comparison Between Hydraulic Hybrid and Hybrid Electric Vehicles
Energies 2015, 8, 4697-4723; doi:10.3390/en8064697 OPEN ACCESS energies ISSN 1996-1073 www.mdpi.com/journal/energies Article Energy Efficiency Comparison between Hydraulic Hybrid and Hybrid Electric Vehicles Jia-Shiun Chen Department of Vehicle Engineering, National Taipei University of Technology, 1, Sec. 3, Zhongxiao E. Road, Taipei 10608, Taiwan; E-Mail: [email protected]; Tel.: +886-2-2771-2171 (ext. 3626); Fax: +886-2-2731-4990 Academic Editor: Joeri Van Mierlo Received: 4 March 2015 / Accepted: 18 May 2015 / Published: 26 May 2015 Abstract: Conventional vehicles tend to consume considerable amounts of fuel, which generates exhaust gases and environmental pollution during intermittent driving cycles. Therefore, prospective vehicle designs favor improved exhaust emissions and energy consumption without compromising vehicle performance. Although pure electric vehicles feature high performance and low pollution characteristics, their limitations are their short driving range and high battery costs. Hybrid electric vehicles (HEVs) are comparatively environmentally friendly and energy efficient, but cost substantially more compared with conventional vehicles. Hydraulic hybrid vehicles (HHVs) are mainly operated using engines, or using alternate combinations of engine and hydraulic power sources while vehicles accelerate. When the hydraulic system accumulator is depleted, the conventional engine reengages; concurrently, brake-regenerated power is recycled and reused by employing hydraulic motor–pump modules in circulation patterns to conserve fuel and recycle brake energy. This study adopted MATLAB Simulink to construct complete HHV and HEV models for backward simulations. New European Driving Cycles were used to determine the changes in fuel economy. The output of power components and the state-of-charge of energy could be retrieved.