Three-Dimensional Fabrication for Microfluidics by Conventional
Total Page:16
File Type:pdf, Size:1020Kb
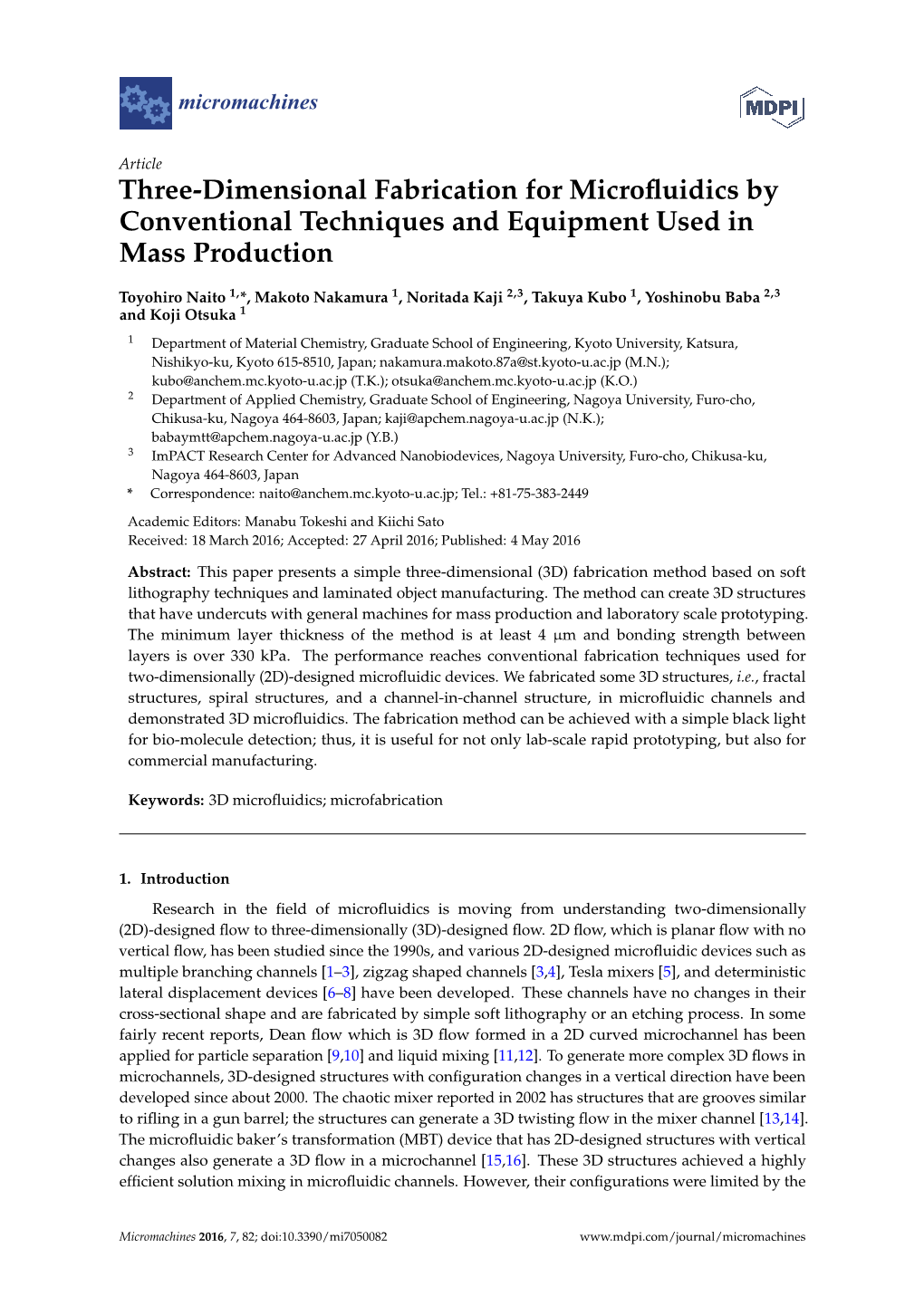
Load more
Recommended publications
-
Accepted Article Preview
ACCEPTED ARTICLE PREVIEW Accepted Article Preview: Published ahead of advance online publication Multi-material multi-photon 3D laser micro- and nanoprinting Liang Yang, Frederik Mayer, Uwe H. F. Bunz, Eva Blasco and Martin Wegener Cite this article as: Liang Yang, Frederik Mayer, Uwe H. F. Bunz, Eva Blasco and Martin Wegener. Multi-material multi-photon 3D laser micro- and nanoprinting. Light: Advanced Manufacturing accepted article preview 29 May 2021; doi: 10.37188/lam.2021.017 This is a PDF file of an unedited peer-reviewed manuscript that has been accepted for publication. LAM are providing this early version of the manuscript as a service to our customers. The manuscript will undergo copyediting, typesetting and a proof review before it is published in its final form. Please note that during the production process errors may be discovered which could affect the content, and all legal disclaimers apply. Received 11 February 2021; revised 26 May 2021; accepted 26 May 2021; Accepted article preview online 29 May 2021 Multi-material multi-photonACCEPTED 3D laser ARTICLE micro- and nanoprinting PREVIEW Liang Yang 1, Frederik Mayer 1,2, Uwe H. F. Bunz 3,4, Eva Blasco 1,3,4 and Martin Wegener 1,2 1Institute of Nanotechnology, Karlsruhe Institute of Technology (KIT), 76128 Karlsruhe, Germany 2Institute of Applied Physics, Karlsruhe Institute of Technology (KIT), 76128 Karlsruhe, Germany 3Institut für Organische Chemie, Ruprecht-Karls-Universität Heidelberg, Im Neuenheimer Feld 270, 69120 Heidelberg, Germany 4Centre for Advanced Materials (CAM), Ruprecht-Karls-Universität Heidelberg, Im Neuenheimer Feld 225 and 270, 69120 Heidelberg, Germany Correspondence: Professor Martin Wegener, Institute of Applied Physics, Karlsruhe Institute of Technology (KIT), 76128 Karlsruhe, Germany E-mail: [email protected] Abstract: Three-dimensional (3D) laser micro- and nanoprinting based upon multi-photon absorption has made its way from early scientific discovery to industrial manufacturing processes, e.g., for advanced microoptical components. -
All-Printed Smart Structures: a Viable Option? John O’Donnella, Farzad Ahmadkhanloub, Hwan-Sik Yoon*A, Gregory Washingtonb Adept
All-printed smart structures: a viable option? John O’Donnella, Farzad Ahmadkhanloub, Hwan-Sik Yoon*a, Gregory Washingtonb aDept. of Mechanical Engineering, The University of Alabama, Box 870276, Tuscaloosa, AL, USA 35487-0276; bDept. of Mechanical and Aerospace Engineering, University of California Irvine, Irvine, CA, USA 92697-3975 ABSTRACT The last two decades have seen evolution of smart materials and structures technologies from theoretical concepts to physical realization in many engineering fields. These include smart sensors and actuators, active damping and vibration control, biomimetics, and structural health monitoring. Recently, additive manufacturing technologies such as 3D printing and printed electronics have received attention as methods to produce 3D objects or electronic components for prototyping or distributed manufacturing purposes. In this paper, the viability of manufacturing all-printed smart structures, with embedded sensors and actuators, will be investigated. To this end, the current 3D printing and printed electronics technologies will be reviewed first. Then, the plausibility of combining these two different additive manufacturing technologies to create all-printed smart structures will be discussed. Potential applications for this type of all-printed smart structures include most of the traditional smart structures where sensors and actuators are embedded or bonded to the structures to measure structural response and cause desired static and dynamic changes in the structure. Keywords: printed smart structures, 3D printing, printed electronics, printed strain sensor 1. INTRODUCTION Decades of research and development have seen the progression of a variety of different additive manufacturing processes [1]. From basic Fused Deposition modeling to the more intricate Energy Beam methods, the ability to print a diverse selection of structures, both complex and simple, on demand with accuracy and precision has become a reality. -
Call for Papers | 2022 MRS Spring Meeting
Symposium CH01: Frontiers of In Situ Materials Characterization—From New Instrumentation and Method to Imaging Aided Materials Design Advancement in synchrotron X-ray techniques, microscopy and spectroscopy has extended the characterization capability to study the structure, phonon, spin, and electromagnetic field of materials with improved temporal and spatial resolution. This symposium will cover recent advances of in situ imaging techniques and highlight progress in materials design, synthesis, and engineering in catalysts and devices aided by insights gained from the state-of-the-art real-time materials characterization. This program will bring together works with an emphasis on developing and applying new methods in X-ray or electron diffraction, scanning probe microscopy, and other techniques to in situ studies of the dynamics in materials, such as the structural and chemical evolution of energy materials and catalysts, and the electronic structure of semiconductor and functional oxides. Additionally, this symposium will focus on works in designing, synthesizing new materials and optimizing materials properties by utilizing the insights on mechanisms of materials processes at different length or time scales revealed by in situ techniques. Emerging big data analysis approaches and method development presenting opportunities to aid materials design are welcomed. Discussion on experimental strategies, data analysis, and conceptual works showcasing how new in situ tools can probe exotic and critical processes in materials, such as charge and heat transfer, bonding, transport of molecule and ions, are encouraged. The symposium will identify new directions of in situ research, facilitate the application of new techniques to in situ liquid and gas phase microscopy and spectroscopy, and bridge mechanistic study with practical synthesis and engineering for materials with a broad range of applications. -
Engineered 3D Polymer and Hydrogel Microenvironments for Cell Culture Applications
bioengineering Review Engineered 3D Polymer and Hydrogel Microenvironments for Cell Culture Applications Daniel Fan , Urs Staufer and Angelo Accardo * Department of Precision and Microsystems Engineering, Delft University of Technology, Mekelweg 2, 2628 CD Delft, The Netherlands; [email protected] (D.F.); [email protected] (U.S.) * Correspondence: [email protected]; Tel.: +31-(0)15-27-81610 Received: 14 October 2019; Accepted: 6 December 2019; Published: 13 December 2019 Abstract: The realization of biomimetic microenvironments for cell biology applications such as organ-on-chip, in vitro drug screening, and tissue engineering is one of the most fascinating research areas in the field of bioengineering. The continuous evolution of additive manufacturing techniques provides the tools to engineer these architectures at different scales. Moreover, it is now possible to tailor their biomechanical and topological properties while taking inspiration from the characteristics of the extracellular matrix, the three-dimensional scaffold in which cells proliferate, migrate, and differentiate. In such context, there is therefore a continuous quest for synthetic and nature-derived composite materials that must hold biocompatible, biodegradable, bioactive features and also be compatible with the envisioned fabrication strategy. The structure of the current review is intended to provide to both micro-engineers and cell biologists a comparative overview of the characteristics, advantages, and drawbacks of the major 3D printing techniques, the most -
High-Precision and Innovative Additive Manufacturing Solutions Based on Photopolymerization Technology
materials Review A New Approach to Micromachining: High-Precision and Innovative Additive Manufacturing Solutions Based on Photopolymerization Technology Paweł Fiedor 1 and Joanna Ortyl 1,2,* 1 Faculty of Chemical Engineering and Technology, Cracow University of Technology, Warszawska 24, 31-155 Cracow, Poland; pawel.fi[email protected] 2 Photo HiTech Ltd., Bobrzy´nskiego14, 30-348 Cracow, Poland * Correspondence: [email protected] Received: 9 June 2020; Accepted: 29 June 2020; Published: 1 July 2020 Abstract: The following article introduces technologies that build three dimensional (3D) objects by adding layer-upon-layer of material, also called additive manufacturing technologies. Furthermore, most important features supporting the conscious choice of 3D printing methods for applications in micro and nanomanufacturing are covered. The micromanufacturing method covers photopolymerization-based methods such as stereolithography (SLA), digital light processing (DLP), the liquid crystal display–DLP coupled method, two-photon polymerization (TPP), and inkjet-based methods. Functional photocurable materials, with magnetic, conductive, or specific optical applications in the 3D printing processes are also reviewed. Keywords: 3D printing; high-resolution; additive manufacturing; photopolymerization; industry 4.0; stereolithography; two-photon polymerization 1. Introduction Three dimensional (3D) printing is currently an extremely important branch of Research and Development (R&D) departments. This is because of its rapid prototyping, swift elimination of design errors, and improvements of the product at the prototyping stage. This approach significantly accelerates the implementation of new solutions without incurring significant production costs and eliminating in-production testing of underdeveloped models. Thanks to 3D printing techniques, making a prototype with complex geometry has become possible in a short time with unprecedented precision [1]. -
Lightweight, Flaw-Tolerant, and Ultrastrong Nanoarchitected Carbon
Lightweight, flaw-tolerant, and ultrastrong nanoarchitected carbon Xuan Zhanga, Andrey Vyatskikhb, Huajian Gaoc,1, Julia R. Greerb,1, and Xiaoyan Lia,d,1 aCenter for Advanced Mechanics and Materials, Applied Mechanics Laboratory, Department of Engineering Mechanics, Tsinghua University, 100084 Beijing, China; bDivision of Engineering and Applied Science, California Institute of Technology, Pasadena, CA 91125; cSchool of Engineering, Brown University, Providence, RI 02912; and dCenter for X-Mechanics, Zhejiang University, 310027 Hangzhou, China Contributed by Huajian Gao, February 9, 2019 (sent for review October 8, 2018; reviewed by Yonggang Huang and Christopher M. Spadaccini) It has been a long-standing challenge in modern material design to Most work on micro/nanoarchitected materials to date has create low-density, lightweight materials that are simultaneously been focused on hollow-beam-based architectures, which offer robust against defects and can withstand extreme thermomechan- exceptionally light weight with a concomitant high compliance ical environments, as these properties are often mutually exclusive: [e.g., nickel-based hollow-tube microlattices with a Young’s The lower the density, the weaker and more fragile the material. modulus of 529 kPa and a compressive strength of ∼10 kPa at a Here, we develop a process to create nanoarchitected carbon that density of ∼0.010 g/cm3 (7) and ceramic hollow-tube nanolattices can attain specific strength (strength-to-density ratio) up to one to with Young’s moduli of 0.003 to 1.4 GPa and compressive three orders of magnitude above that of existing micro- and strengths of 0.07 to 30 MPa at densities of 0.006 to 0.25 g/cm3 nanoarchitected materials. -
Two-Photon Polymerization: Functionalized Microstructures, Micro-Resonators, and Bio-Scaffolds
polymers Review Two-Photon Polymerization: Functionalized Microstructures, Micro-Resonators, and Bio-Scaffolds Adriano J. G. Otuka 1,*,†, Nathália B. Tomazio 1,2,†, Kelly T. Paula 1 and Cleber R. Mendonça 1,* 1 Photonics Group, São Carlos Institute of Physics, University of São Paulo, São Carlos 13566-590, SP, Brazil; [email protected] (N.B.T.); [email protected] (K.T.P.) 2 Device Research Laboratory, “Gleb Wataghin” Institute of Physics, University of Campinas, Campinas 13083-859, SP, Brazil * Correspondence: [email protected] (A.J.G.O.); [email protected] (C.R.M.) † Contributed equally to this work as the first author. Abstract: The direct laser writing technique based on two-photon polymerization (TPP) has evolved considerably over the past two decades. Its remarkable characteristics, such as 3D capability, sub- diffraction resolution, material flexibility, and gentle processing conditions, have made it suitable for several applications in photonics and biosciences. In this review, we present an overview of the progress of TPP towards the fabrication of functionalized microstructures, whispering gallery mode (WGM) microresonators, and microenvironments for culturing microorganisms. We also describe the key physical-chemical fundamentals underlying the technique, the typical experimental setups, and the different materials employed for TPP. Keywords: direct laser writing; ultrashort laser pulses; two-photon polymerization; functional microdevices; whispering gallery mode microresonators; scaffolds for biological applications Citation: Otuka, A.J.G.; Tomazio, N.B.; Paula, K.T.; Mendonça, C.R. Two-Photon Polymerization: 1. Introduction Functionalized Microstructures, Micro-Resonators, and Bio-Scaffolds. The processing of materials by ultrashort lasers, which allows high precision-patterning Polymers 2021, 13, 1994. -
Habilitationsschrift 3D-Techniques in Materials Science
Habilitationsschrift 3D-techniques in Materials Science Eingereicht von Dipl.-Ing. Dr.mont. Jur¨ gen Stampfl and der Fakultat¨ fur¨ Maschinenbau der TU Wien zum Zwecke der Erlangung der Lehrbefugnis fur¨ das Fach Werkstoffwissenschaften Wien, im Marz¨ 2004 2 Contents 1 Preface 1 1.1 Contributions of the author . 1 1.2 Achievements of the habilitation . 2 I Introduction 5 2 3D-scanning 7 2.1 Stereoscopic electron microscopy . 7 2.1.1 Principle . 7 2.1.2 Image processing . 8 2.2 3D scanning in fracture mechanics . 10 2.3 Orientation image microscopy . 11 2.4 References . 11 3 3D-shaping 15 3.1 Stereolithography . 15 3.1.1 Stereolithography for microsystems . 18 3.1.1.1 Systems based on pixel arrays (DLP - digital light processing) . 19 3.1.1.2 Miniaturized SLA systems . 21 3.1.1.3 Two-photon processes . 22 3.1.2 Materials for stereolithography . 23 3.1.3 Objet Quadra . 25 i CONTENTS 3.2 Selective Laser Sintering (SLS) . 25 3.3 3D Printing . 30 3.4 Systems based on the deposition of thermoplastics . 31 3.4.1 Fused Deposition Modeling (FDM) . 31 3.4.2 ModelMaker Series . 32 3.4.3 MultiJet Modeling . 33 3.5 CNC Machining, Shape deposition Manufacturing . 33 3.6 Laminated Object Manufacturing (LOM) . 36 3.7 System selection . 37 3.8 References . 41 4 RP of cellular solids 47 4.1 Cellular structures for photonic crystals . 47 4.2 Cellular materials for biomedical applications . 48 4.2.1 Requirements for RP processes . 48 4.2.2 Applications . 52 4.3 References . -
3D and 4D Lithography of Untethered Microrobots
Progress in Materials Science 120 (2021) 100808 Contents lists available at ScienceDirect Progress in Materials Science journal homepage: www.elsevier.com/locate/pmatsci 3D and 4D lithography of untethered microrobots Fatemeh Rajabasadi a, Lukas Schwarz a, Mariana Medina-Sanchez´ a,*, Oliver G. Schmidt a,b,c a Institute for Integrative Nanosciences, Leibniz IFW Dresden, Helmholtzstrasse 20, 01069 Dresden, Germany b Research Center for Materials, Architectures and Integration of Nanomembranes (MAIN), Rosenbergstraße 6, TU Chemnitz, 09126 Chemnitz, Germany c School of Science, TU Dresden, 01062 Dresden, Germany ARTICLE INFO ABSTRACT Keywords: In the last decades, additive manufacturing (AM), also called three-dimensional (3D) printing, has Micromotors advanced micro/nano-fabrication technologies, especially in applications like lightweight engi Microrobots neering, optics, energy, and biomedicine. Among these 3D printing technologies, two-photon Two-photon polymerization polymerization (TPP) offers the highest resolution (even at the nanometric scale), reproduc 3D Laser Lithography ibility and the possibility to create monolithically 3D complex structures with a variety of ma 4D Soft Robotics terials (e.g. organic and inorganic, passive and active). Such active materials change their shape Smart Materials upon an applied stimulus or degrade over time at certain conditions making them dynamic and Stimuli-responsive reconfigurable (also called 4D printing). This is particularly interesting in the field of medical microrobotics as complex functions such as gentle interactions with biological samples, adapt ability when moving in small capillaries, controlled cargo-release profiles, and protection of the encapsulated cargoes, are required. Here we review the physics, chemistry and engineering principles of TPP, with some innovations that include the use of micromolding and microfluidics, and explain how this fabrication schemes provide the microrobots with additional features and application opportunities. -
3D PRINTING Introduction Additive Manufacturing Or 3D Printing Is a Process of Making Three Dimensional Solid Objects from a Digital Model
3D PRINTING Introduction Additive manufacturing or 3D printing is a process of making three dimensional solid objects from a digital model. 3D printing is achieved using additive processes, where an object is created by laying down successive layers of material. 3D printing is considered distinct from traditional machining techniques (subtractive processes) which mostly rely on the removal of material by drilling, cutting etc. A 3D Printer A hyperboloid object print (made of PLA) using a RepRap “Prusa Mendel” 3D printer for molten polymer deposition. 3D printing is usually performed by a materials printer using digital technology. Since the start of the twenty-first century there has been a large growth in the sales of these machines, and their price dropped substantially. The technology is used in the fields of jewellery, footwear, industrial design, architecture, engineering and construction (AEC), automotive, aerospace, dental and medical industries, education, geographic information systems, civil engineering, and many others. History Early examples of 3D printing occurred in the 1980s, though the printers then were large, expensive and highly limited in what they could produce. • The term "3D printing" was coined at MIT in 1995 when then graduate students Jim Bredt and Tim Anderson modified an inkjet printer to extrude a binding solution onto a bed of powder, rather than ink onto paper. The ensuing patent led to the creation of modern 3D printing companies Z Corporation (founded by Bredt and Anderson) and ExOne. • SLS was developed and patented by Dr. Carl Deckard at the University of Texas at Austin in the mid-1980s, under sponsorship of DARPA. -
A Review on 3D Micro-Additive Manufacturing Technologies
Int J Adv Manuf Technol (2013) 67:1721–1754 DOI 10.1007/s00170-012-4605-2 ORIGINAL ARTICLE A review on 3D micro-additive manufacturing technologies Mohammad Vaezi & Hermann Seitz & Shoufeng Yang Received: 27 June 2011 /Accepted: 30 October 2012 /Published online: 25 November 2012 # Springer-Verlag London 2012 Abstract New microproducts need the utilization of a di- 1 Introduction versity of materials and have complicated three-dimensional (3D) microstructures with high aspect ratios. To date, many Nowadays, there is an enormous variety in microproducts, micromanufacturing processes have been developed but the major kinds being microelectromechanical systems specific class of such processes are applicable for fabrication (MEMS), micro-opto-electro-mechanical systems of functional and true 3D microcomponents/assemblies. The (MOEMS), and microelectronic products and micro-optical aptitude to process a broad range of materials and the ability electronics systems (MOES) depending on the mixtures of to fabricate functional and geometrically complicated 3D product usefulness and operation fundamentals [197]. Due microstructures provides the additive manufacturing (AM) to the present tendency towards miniaturization of products processes some profits over traditional methods, such as in many industries comprising medical, automotive, optics, lithography-based or micromachining approaches investi- electronics, and biotechnology sectors [4], there is a demand gated widely in the past. In this paper, 3D micro-AM pro- for improvements in micro- and nanofabrication technolo- cesses have been classified into three main groups, gies and merging them in new manufacturing platforms. including scalable micro-AM systems, 3D direct writing, A broad range of microfabrication technologies have been and hybrid processes, and the key processes have been developed which have different applications and capabilities reviewed comprehensively. -
Three-Dimensional Stretchable Microelectronics by Projection
www.acsami.org Research Article Three-Dimensional Stretchable Microelectronics by Projection Microstereolithography (PμSL) Yuejiao Wang, Xiang Li, Sufeng Fan, Xiaobin Feng, Ke Cao, Qi Ge,* Libo Gao,* and Yang Lu* Cite This: https://dx.doi.org/10.1021/acsami.0c20162 Read Online ACCESS Metrics & More Article Recommendations *sı Supporting Information ABSTRACT: Stretchable and flexible electronics conformal to human skin or implanted into biological tissues has attracted considerable interest for emerging applications in health monitoring and medical treatment. Although various stretchable materials and structures have been designed and manufactured, most are limited to two-dimensional (2D) layouts for interconnects and active components. Here, by using projection microstereolithography (PμSL)-based three-dimensional (3D) printing, we introduce a versatile microfabrication process to push the manufacturing limit and achieve previously inaccessible 3D geometries at a high resolution of 2 μm. After coating the printed microstructures with thin Au films, the 3D conductive structures offer exceptional stretchability (∼130%), conformability, and stable electrical conductivity (<5% resistance change at 100% tensile strain). This fabrication process can be further applied to directly create complicated 3D interconnect networks of sophisticated active components, as demonstrated with a stretchable capacitive pressure sensor array here. The proposed scheme allows a simple, facile, and scalable manufacturing route for complex, integrated 3D flexible electronic