Hull Protection for Ice-Going Vessels Part I: Introduction Part I
Total Page:16
File Type:pdf, Size:1020Kb
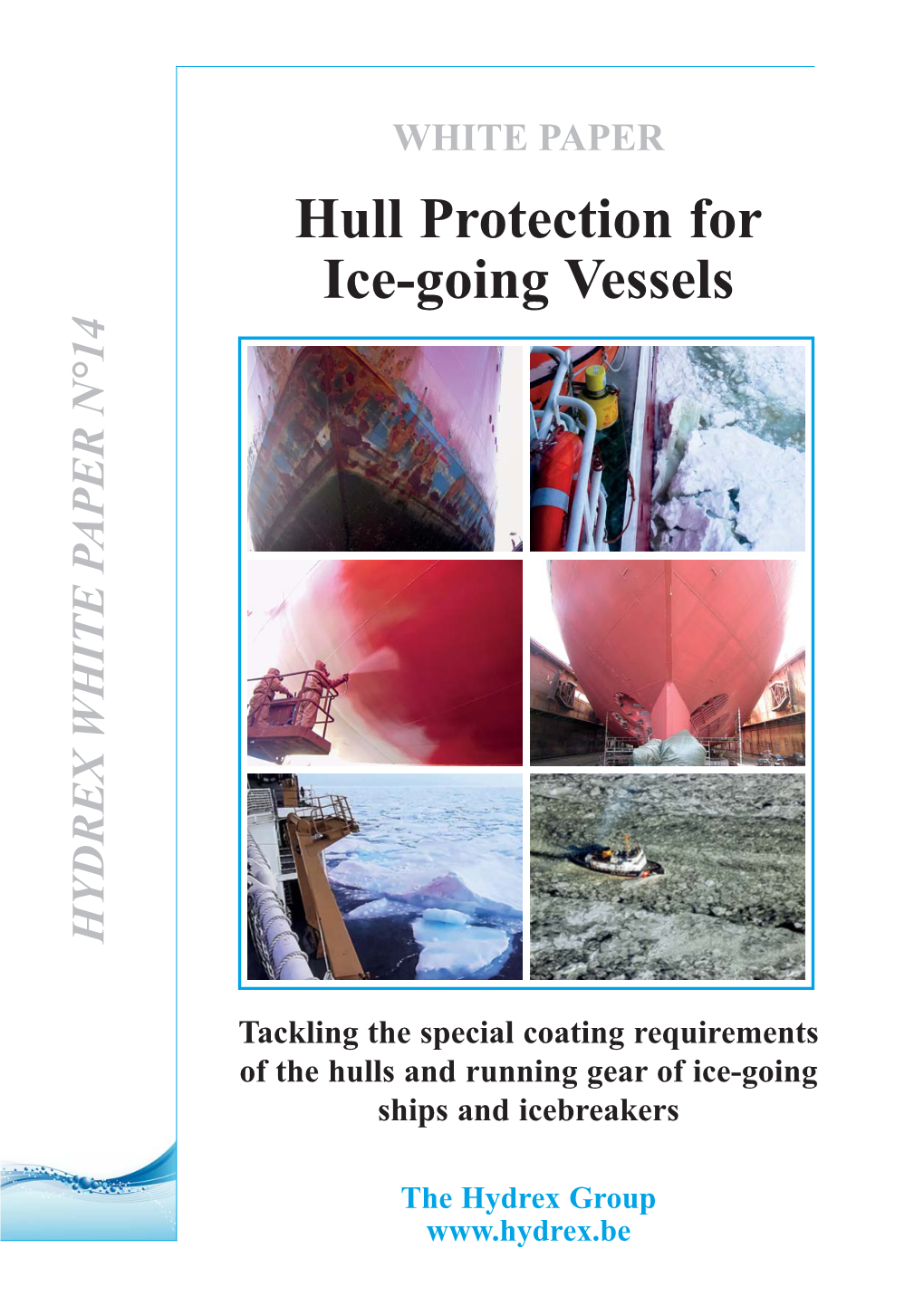
Load more
Recommended publications
-
Northern Sea Route Cargo Flows and Infrastructure- Present State And
Northern Sea Route Cargo Flows and Infrastructure – Present State and Future Potential By Claes Lykke Ragner FNI Report 13/2000 FRIDTJOF NANSENS INSTITUTT THE FRIDTJOF NANSEN INSTITUTE Tittel/Title Sider/Pages Northern Sea Route Cargo Flows and Infrastructure – Present 124 State and Future Potential Publikasjonstype/Publication Type Nummer/Number FNI Report 13/2000 Forfatter(e)/Author(s) ISBN Claes Lykke Ragner 82-7613-400-9 Program/Programme ISSN 0801-2431 Prosjekt/Project Sammendrag/Abstract The report assesses the Northern Sea Route’s commercial potential and economic importance, both as a transit route between Europe and Asia, and as an export route for oil, gas and other natural resources in the Russian Arctic. First, it conducts a survey of past and present Northern Sea Route (NSR) cargo flows. Then follow discussions of the route’s commercial potential as a transit route, as well as of its economic importance and relevance for each of the Russian Arctic regions. These discussions are summarized by estimates of what types and volumes of NSR cargoes that can realistically be expected in the period 2000-2015. This is then followed by a survey of the status quo of the NSR infrastructure (above all the ice-breakers, ice-class cargo vessels and ports), with estimates of its future capacity. Based on the estimated future NSR cargo potential, future NSR infrastructure requirements are calculated and compared with the estimated capacity in order to identify the main, future infrastructure bottlenecks for NSR operations. The information presented in the report is mainly compiled from data and research results that were published through the International Northern Sea Route Programme (INSROP) 1993-99, but considerable updates have been made using recent information, statistics and analyses from various sources. -
Ice Navigation Training
Training for maritime operations in polar waters-fulfillment of the Polar code Sergey Aysinov, MBA, PhD, Director of Professional development programmes Institute Head of Makarov training centre Historical Background Number of Students (2015/2016 academic year) Full time training 5168 Distance learning (all Faculties) 2712 Maritime College (all forms of education) 1376 3317 Teaching Staff (Higher Education) Professors, PH.D. Full time 431 Part time 154 Assistant Professors 221 Branches 72 International Maritime Activity The University experts participate in Russian Federation Delegations as well as IALA, ITF delegations to the regulatory organizations: International Maritime Organization (IMO) and International Labour Organization (ILO) University is a member of: . Executive Committee of International Association of Maritime Universities (IAMU); . International Maritime Lecturers Association (IMLA); . International Sail Training Association (ISTA); . International Maritime Simulator Forum (IMSF); . STENA Association of Maritime Institutions (STAMI) acting under the patronage of shipping company STENA (Sweden) Technological and Personnel resourses Makarov Training Centre: . 46 Modern training simulators, . More than 200 highly professional Engineers, Instructors, Managers, Experts, . More than 170 training programs, . 20+ years of operation, . Approval from Russian Ministry of Transport, Federal Marine and River Transport Agency, other Flag state Administrations, Certification Association “Russian Register”, Russian Maritime Register of Shipping, The Nautical Institute, and others. MTC provides professional simulator training to more than 15 000 trainees from 23+ countries annually without any boundaries. MAKAROV TRAINING CENTRE ICE NAVIGATION TRAINING Start May, 2003 Main Sailing Areas – the Baltics: - St. Petersburg - Primorsk - Vysotsk - Ust’-Luga Number of trainees: 900 + Unicom (Cyprus) – the first partner 2003-2016. What have been changed ? Regulatory base – Polar code, SOLAS and STCW amendments. -
Structural Challenges Faced by Arctic Ships
NTIS # PB2011- SSC-461 STRUCTURAL CHALLENGES FACED BY ARCTIC SHIPS This document has been approved For public release and sale; its Distribution is unlimited SHIP STRUCTURE COMMITTEE 2011 Ship Structure Committee RADM P.F. Zukunft RDML Thomas Eccles U. S. Coast Guard Assistant Commandant, Chief Engineer and Deputy Commander Assistant Commandant for Marine Safety, Security For Naval Systems Engineering (SEA05) and Stewardship Co-Chair, Ship Structure Committee Co-Chair, Ship Structure Committee Mr. H. Paul Cojeen Dr. Roger Basu Society of Naval Architects and Marine Engineers Senior Vice President American Bureau of Shipping Mr. Christopher McMahon Mr. Victor Santos Pedro Director, Office of Ship Construction Director Design, Equipment and Boating Safety, Maritime Administration Marine Safety, Transport Canada Mr. Kevin Baetsen Dr. Neil Pegg Director of Engineering Group Leader - Structural Mechanics Military Sealift Command Defence Research & Development Canada - Atlantic Mr. Jeffrey Lantz, Mr. Edward Godfrey Commercial Regulations and Standards for the Director, Structural Integrity and Performance Division Assistant Commandant for Marine Safety, Security and Stewardship Dr. John Pazik Mr. Jeffery Orner Director, Ship Systems and Engineering Research Deputy Assistant Commandant for Engineering and Division Logistics SHIP STRUCTURE SUB-COMMITTEE AMERICAN BUREAU OF SHIPPING (ABS) DEFENCE RESEARCH & DEVELOPMENT CANADA ATLANTIC Mr. Craig Bone Dr. David Stredulinsky Mr. Phil Rynn Mr. John Porter Mr. Tom Ingram MARITIME ADMINISTRATION (MARAD) MILITARY SEALIFT COMMAND (MSC) Mr. Chao Lin Mr. Michael W. Touma Mr. Richard Sonnenschein Mr. Jitesh Kerai NAVY/ONR / NAVSEA/ NSWCCD TRANSPORT CANADA Mr. David Qualley / Dr. Paul Hess Natasa Kozarski Mr. Erik Rasmussen / Dr. Roshdy Barsoum Luc Tremblay Mr. Nat Nappi, Jr. Mr. -
Ice Trials in Antarctica • New Rules on the Northern Sea Route • Processing Barge to the Arctic • Equipment for the Navy in This Issue
Arctic Passion News No. 1 | 2020 | issue 19 • Ice trials in Antarctica • New rules on the Northern Sea Route • Processing barge to the Arctic • Equipment for the Navy In this issue Page 4 Page 8 Page 11 Page 16 New rules on the Northern Xue Long 2 in Equipment for the Navy Barge for mining project Sea Route ice trials Table of contents From the Managing Director.................................. 3 Front cover New regime and regulations on the NSR...............4 Sami Saarinen spent six weeks travelling to Antarctica Xue Long 2 in successful ice trials.......................... 8 and back, onboard both of China’s icebreakers Xue Equipment for Navy corvettes.......................... ….11 Long and Xue Long 2. Read about his voyage and Safe and reliable shipping of crude oil................. 12 Xue Long 2’s ice trials on page 8. Feasibility study for Qilak LNG.........................….14 Aalto Ice Tank opens.............................................15 Contact details Pavlovskoe mining project.....................................16 AKER ARCTIC TECHNOLOGY INC Reducing ice friction since 1969 ...........................18 Merenkulkijankatu 6, FI-00980 HELSINKI Active Heeling systems.........................................20 Tel.: +358 10 323 6300 News in brief.........................................................21 www.akerarctic.fi Announcements....................................................23 Study tour to Gothenburg.....................................24 Join our subscription list Our services Please send your message to www.akerarctic.fi -
Modern Day Pioneering and Its Safety in the Floating Ice Offshore
Modern Day Pioneering and its Safety in the Floating Ice Offshore Arno J. Keinonen AKAC INC. Victoria, B.C. Canada [email protected] Evan H. Martin AKAC INC. Victoria, B.C. Canada [email protected] ABSTRACT al. (2006a), Keinonen et al. (2006b), Keinonen et al. (2000), Pilkington et al. (2006a), Pilkington et al. (2006b), Reed (2006), Tambovsky et al. Floating ice offshore pioneering has been performed since the mid (2006), Wright (1999), and Wright (2000). 1970s. This paper presents the key lessons learned from 5 such operations of wide geographic as well as operational range. The intent FLOATING STATIONARY OPERATIONS IN PACK ICE is to present the safety related lessons from these operations for the OFFSHORE benefit of the future safety of similar operations. Beaufort Sea Drillships KEY WORDS: ice offshore operations; station keeping in ice; ice management; safety in ice. When four open water drillships, upgraded to an ice class and winterized, entered the Beaufort Sea mid seventies, together with INTRODUCTION several ice class supply vessels, the operators had an expectation of having an open water season of a few months each year to be able to Several early pioneers going to the Arctic went all out, all thinking that explore for oil and gas (Keinonen and Martin, 2010). The operation they were well prepared, yet some were clearly not prepared for what itself was expected to be a seasonal summer operation only and not to could happen. Some became heroes while others left their names on interact with ice. pages of history books for not completing their missions, at times paying the ultimate price, losing their lives, equipment and leaving The first pioneering lesson was that the so-called summer season had behind a low level, local pollution to the environment. -
Coatings and Cold Hard Truths | International Paint
Ice Class Vessels Coatings and cold hard truths The sophisticated ships destined to recover hard to reach resources under ice-covered polar seas have required new thinking on design and construction. No matter how profound that thinking has been, however, owner preference for the protective coating Intershield® 163 Inerta 160 has remained a constant. Despite the challenges posed the Arctic Circle promises to yield around 22% of the world’s oil and gas still known to be available. hile the wider harshest of environments. natural gas liquids. newbuilding market Despite the challenges posed by their More than a fifth of Russian territory for ships may only now recovery, the Arctic Circle promises to lies north of the polar circle. The W be showing any signs of yield around 22% of the world’s oil and nation’s Arctic and sub-Arctic regions recovery, few can doubt that sustained gas still known to be available, in the account for 90% of its gas reserves and high oil and gas prices dictate the shape of up to an estimated 90 billion over 20% of its crude oil. Accordingly, future need for increasing numbers barrels of oil, 1,670 trillion cubic feet Russian gas giant Gazprom, for of vessels capable of operating in the of natural gas, and 44 billion barrels of example, has gone on record as saying 1 Ice Class Vessels that field development offshore Russia to 2020 alone will drive orders for over 10 production platforms, over 50 ice class tankers and other specialised ships, and at least 23 liquefied natural gas carriers. -
Role of Classification Society in Arctic Shipping
ROLE OF CLASSIFICATION SOCIETY IN ARCTIC SHIPPING Seppo Liukkonen, Station Manager, DNVGL Station Helsinki Abstract The core mission of a classification society is “to protect human lives, property and the environment”. In first place the classification societies are fulfilling this function in marine environment, because the classification business in its current form started within sea transportation and shipping. Since then the function of the classification societies has widened to comprise shipbuilding, different kinds of off- shore activities and also some on-shore activities. When fulfilling their function the classification societies are using their own classification rules as their main, own tool. Additionally, the classification societies are often fulfilling their above-mentioned function by working together with and on behalf of the flag state administrations. Here the so-called IMO instruments such as the SOLAS and MARPOL conventions, for instance, are the main basis of the work. Also, international standards, such as the EN-ISO and IEC standards, for instance, and other national and international regulations, such as the Finnish-Swedish Ice Class Rules and Canadian Arctic Pollution Prevention Regulations, for instance, are used by the classification societies. Basically, the work of the classification societies is to ensure that the object in question, e.g., a ship, an off-shore structure, a quality management system, etc., is in compliance with the above-mentioned relevant rules and regulations. In practice this can be done, e.g., with plan approvals, supervision of manufacturing, surveys, inspections and audits. This presentation gives an overview about the role of the classification societies in ensuring and developing the safe Arctic shipping. -
Towards an Automatic Ice Navigation Support System in the Arctic Sea
International Journal of Geo-Information Article Towards an Automatic Ice Navigation Support System in the Arctic Sea Xintao Liu, Shahram Sattar and Songnian Li * Department of Civil Engineering, Ryerson University, 350 Victoria Street, Toronto, ON M5B 2K3, Canada; [email protected] (X.L.); [email protected] (S.S.) * Correspondence: [email protected]; Tel.: +1-416-979-5000 Academic Editors: Suzana Dragicevic, Xiaohua Tong and Wolfgang Kainz Received: 18 January 2016; Accepted: 8 March 2016; Published: 14 March 2016 Abstract: Conventional ice navigation in the sea is manually operated by well-trained navigators, whose experiences are heavily relied upon to guarantee the ship’s safety. Despite the increasingly available ice data and information, little has been done to develop an automatic ice navigation support system to better guide ships in the sea. In this study, using the vector-formatted ice data and navigation codes in northern regions, we calculate ice numeral and divide sea area into two parts: continuous navigable area and the counterpart numerous separate unnavigable area. We generate Voronoi Diagrams for the obstacle areas and build a road network-like graph for connections in the sea. Based on such a network, we design and develop a geographic information system (GIS) package to automatically compute the safest-and-shortest routes for different types of ships between origin and destination (OD) pairs. A visibility tool, Isovist, is also implemented to help automatically identify safe navigable areas in emergency situations. The developed GIS package is shared online as an open source project called NavSpace, available for validation and extension, e.g., indoor navigation service. -
Ice Navigation in Canadian Waters
Ice Navigation in Canadian Waters Published by: Icebreaking Program, Maritime Services Canadian Coast Guard Fisheries and Oceans Canada Ottawa, Ontario K1A 0E6 Cat. No. Fs154-31/2012E-PDF ISBN 978-1-100-20610-3 Revised August 2012 ©Minister of Fisheries and Oceans Canada 2012 Important Notice – For Copyright and Permission to Reproduce, please refer to: http://www.dfo-mpo.gc.ca/notices-avis-eng.htm Note : Cette publication est aussi disponible en français. Cover photo: CCGS Henry Larsen in Petermann Fjord, Greenland, by ice island in August 2012. Canadian Coast Guard Ice Navigation in Canadian Waters Record of Amendments RECORD OF AMENDMENTS TO ICE NAVIGATION IN CANADIAN WATERS (2012 VERSION) FROM MONTHLY NOTICES TO MARINERS NOTICES TO INSERTED DATE SUBJECT MARINERS # BY Note: Any inquiries as to the contents of this publication or reports of errors or omissions should be directed to [email protected] Revised August 2012 Page i of 153 Canadian Coast Guard Ice Navigation in Canadian Waters Foreword FOREWORD Ice Navigation in Canadian Waters is published by the Canadian Coast Guard in collaboration with Transport Canada Marine Safety, the Canadian Ice Service of Environment Canada and the Canadian Hydrographic Service of Fisheries and Oceans Canada. The publication is intended to assist ships operating in ice in all Canadian waters, including the Arctic. This document will provide Masters and watchkeeping crew of vessels transiting Canadian ice-covered waters with the necessary understanding of the regulations, shipping support services, hazards and navigation techniques in ice. Chapter 1, Icebreaking and Shipping Support Services, pertains to operational considerations, such as communications and reporting requirements as well as ice advisories and icebreaker support within Canadian waters. -
Ice Class Strengthening of Existing Reefer Vessels Trading in the Baltic Sea - a Comparative Study of Ice Classifications 1D and 1C
Kungliga Tekniska Högskolan Centre for Naval Architecture Bachelor Thesis in Mechanical Engineering SA118X Ice Class Strengthening of Existing Reefer Vessels Trading in the Baltic Sea - A comparative study of ice classifications 1D and 1C Authors Dennis Bremberg ([email protected]) Sara Högdahl ([email protected]) Supervisor Ivan Stenius Date 2016-05-02 Abstract This bachelor thesis strives to perspicuously answer what an ice strengthening of two different existing reefer vessels might mean for operations in the Baltic Sea and illustrate what factors a shipping company needs to consider when initiating such a project. The main purpose is to provide an information basis facilitating the communication between different parties in the shipping industry. The existing specialized reefer fleet is old and few new ships are being built or commissioned. At the same time, there is an increasing demand of shipping perishables to St. Petersburg, inciting the strengthening of existing ships to meet market demands. The methodology used in this report is a compilation of selective literature research (primarily providing qualitative, secondary data) and a comparative study in which the secondary data is applied on the reefer classes Crown and Family. While other classification societies are mentioned, this report focuses on Lloyd’s Register and the ice classes 1D and 1C, suitable for very light and light ice conditions and sailing in convoy with icebreaker assistance. Although ice class 1C is designated for tougher ice conditions than 1D, they share many strengthening requirements. Most substantially, the requirements for 1C concerning the forward region and steering arrangements, stipulated by the Swedish Maritime Administration (Swedish: Sjöfartsverket), are also applicable to 1D. -
7 Information About Navigation in Ice
Notices to Mariners 1 to 46 Section A – Aids to Navigation and Marine Safety 7 Information about Navigation in Ice Ice Navigation in Canadian Waters is published by the Canadian Coast Guard in collaboration with Transport Canada Marine Safety, the Canadian Ice Service of Environment Canada and the Canadian Hydrographic Service of Fisheries and Oceans Canada. The publication is intended to assist ships operating in ice in all Canadian waters, including the Arctic. This document will provide Masters and watchkeeping crew of vessels transiting Canadian ice-covered waters with the necessary understanding of the regulations, shipping support services, hazards, and navigation techniques in ice. The nautical publication is available for download, free-of-charge, from https://www.ccg-gcc.gc.ca/publications/icebreaking-deglacage/ice-navigation-glaces/page01-eng.html (It is important to note that the paper version of the document is no longer available.) 7.1 General Ice is an obstacle to any ship, even an icebreaker, and the inexperienced Navigation Officer is advised to develop a healthy respect for the latent power and strength of ice in all its forms. However, it is quite possible, and continues to be proven so, for well-found ships in capable hands to navigate successfully through ice-covered waters. The first principle of successful ice navigation is to maintain freedom of manoeuvre. Once a ship becomes trapped, the vessel goes wherever the ice goes. Ice navigation requires great patience and can be a tiring business with or without icebreaker escort. The open water long way round a difficult ice area whose limits are known is often the fastest and safest way to port, or to the open sea when leaving a port. -
Lloyd's Register – Written Evidence (ARC0048)
Lloyd’s Register – Written evidence (ARC0048) 1. Summary The objectives of this submission of evidence to the Select Committee on the Arctic are: To offer supporting data and insights on transit and destination shipping in the Arctic and, in addition, the characteristics of the UK registered Arctic shipping fleet. To contribute evidence on the technological challenges for future Arctic shipping activities To contribute evidence on the regulatory framework that will govern Arctic shipping To contribute advice, and views, on Arctic shipping to support consideration of the “UK dimension” by the Select Committee Considering each objective in turn: Key points on supporting data and insights on transit and destination shipping in the Arctic: 1. Very small numbers of ships use Arctic transits for voyages between ocean basins (i.e. Pacific and Atlantic basins) as an alternative shipping route to transits through the Panama or Suez canal 2. Shipping in the Russian Arctic is likely to increase, but will be mainly export shipping for dedicated natural resources projects. Transit of commercial ships through the Russian Arctic is likely to occur during the summer season only 3. The UK registered ice-classed fleet is small, with 119 ice classed ships, and just 8 ships potentially suitable for transiting the Russian Northern Sea Route independently in an average summer season Figure 1.1 % of Ice Classed UK Fleet Figure 1.2 Ice Classes assigned to UK flagged ships 1 Key points on the technological challenges for future Arctic shipping activities: 1. Technological challenges remain for efficient Arctic shipping with a significant build and operating cost premium associated with current generation of Arctic capable ships 2.