The Measure of Success Military Flight Testing at Nlr Who We Are
Total Page:16
File Type:pdf, Size:1020Kb
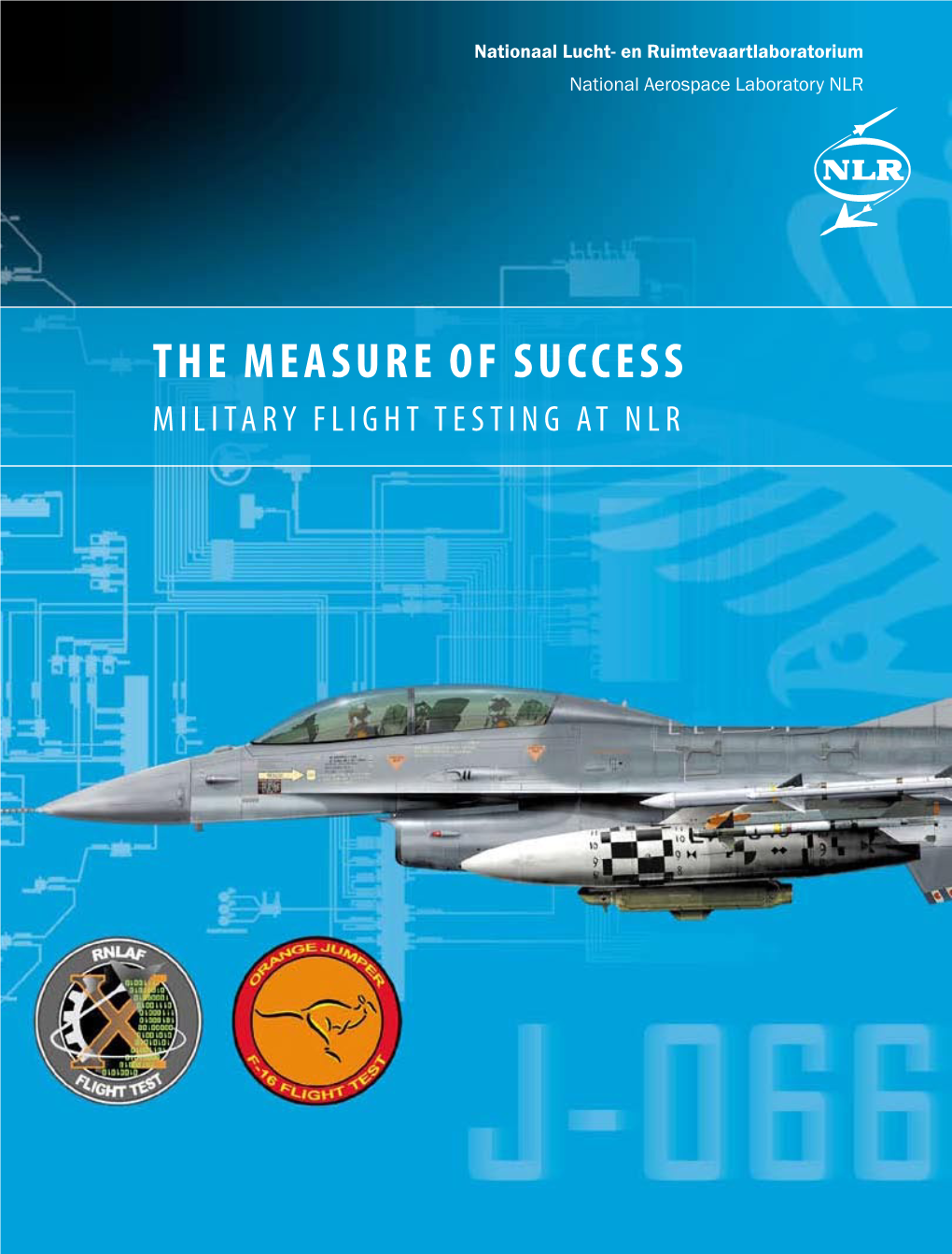
Load more
Recommended publications
-
2018 Annual Report Our Leadership Team (From Left to Right): Frank A
FINANCIAL HIGHLIGHTS In millions, except per share data 2018 2017 2016 Net Sales $53,762 $49,960 $47,290 Segment Operating Profit 5,877 5,092 4,982 Consolidated Operating Profit 7,334 6,744 5,888 Net Earnings From Continuing Operations 5,046 1,890 3,661 Net Earnings 5,046 1,963 5,173 Diluted Earnings Per Common Share Continuing Operations 17.59 6.50 12.08 Net Earnings 17.59 6.75 17.07 Cash Dividends Per Common Share 8.20 7.46 6.77 Average Diluted Common Shares Outstanding 287 291 303 Cash and Cash Equivalents $772$ 2,861 $ 1,837 Total Assets 44,876 46,620 47,560 Total Debt, net 14,104 14,263 14,282 Total Equity (Deficit) 1,449 (776) 1,477 Common Shares Outstanding at Year-End 281 284 289 Net Cash Provided by Operating Activities $3,138 $ 6,476 $ 5,189 NOTE: For additional information regarding the amounts presented above, see the Form 10-K portion of this Annual Report. A reconciliation of Segment Operating Profit to Consolidated Operating Profit is included on the page preceding the back cover of this Annual Report. On the Cover: F-35B Lightning II On September 29, 2018, the first F-35B Lightning II stealth fighters landed on the flight deck of HMS Queen Elizabeth, as Britain’s newest Royal Navy aircraft carrier conducted trials off the Eastern Seaboard of the United States. These developmental trials included more than 500 take-offs and landings from the warship over an 11-week period. The F-35B is one of three variants of the world’s most advanced supersonic fifth-generation fighter jet. -
Aerospace-Facts-And-Figures-1988
Facts and Figures 8 8 8 9 Key Technologies Legacy for the 21st Century Aerospace Industries Association of America, Inc. $16.95 Compiled by Economic Data Service Aerospace Research Center Aerospace Industries Association of America, Inc. 1250 Eye Street, N.W., Washington , D.C. 20005 (202) 371 -8400 Director , Research Center: Virginia C. Lopez Manager, Economic Data Servi ce: Carl M. P ~ s ale Ed itorial onsultant: Jam s 1. Hagg rty De~ign : wen Hoelscher and Associates Published by Aviation Week 1221 Avenue of the Americas New York, N.Y. 10020 1-800-433-0880 Copyright © 19tl!l by Aerospace Industries A ss ociution u f i\mericu. Inc . Library o f Congre ss utalog N<> . 46-25 007 Ackno-wledgments Air Transport Association of America Battelle Memorial Institute Council of Economic Advisers Export-Import Bank of the United States Exxon International Company General Aviation Manufacturers Association Helicopter Association International International Air Transport Association International Civil Aviation Organization McGraw-Hill Publications Company National Aeronautics and Space Administration National Science Foundation Office of Management and Budget Price Waterhouse U.S. Departments of Commerce (Bureau of the Census, Bureau of Economic Analysis, International Trade Administration) Defense (Comptroller; Directorate for Information, Operations and Reports: Army, Navy, Air Force) Labor (Bureau of Labor Statistics) Transportation (Federal Aviation Administration) Focused development of key "enabling" technologies will determine the U.S. aerosp~ce. industry's technological and market leadership mto the next century. These technologies will help ensure U.S. defense superiority and will also provide endless possibilities for a range of products to revolutionize the way we live-from fully-automated factories to crash-resistant, ultra safe automobiles to greatly improved medical diagnostic equipment. -
Downloaded April 22, 2006
SIX DECADES OF GUIDED MUNITIONS AND BATTLE NETWORKS: PROGRESS AND PROSPECTS Barry D. Watts Thinking Center for Strategic Smarter and Budgetary Assessments About Defense www.csbaonline.org Six Decades of Guided Munitions and Battle Networks: Progress and Prospects by Barry D. Watts Center for Strategic and Budgetary Assessments March 2007 ABOUT THE CENTER FOR STRATEGIC AND BUDGETARY ASSESSMENTS The Center for Strategic and Budgetary Assessments (CSBA) is an independent, nonprofit, public policy research institute established to make clear the inextricable link between near-term and long- range military planning and defense investment strategies. CSBA is directed by Dr. Andrew F. Krepinevich and funded by foundations, corporations, government, and individual grants and contributions. This report is one in a series of CSBA analyses on the emerging military revolution. Previous reports in this series include The Military-Technical Revolution: A Preliminary Assessment (2002), Meeting the Anti-Access and Area-Denial Challenge (2003), and The Revolution in War (2004). The first of these, on the military-technical revolution, reproduces the 1992 Pentagon assessment that precipitated the 1990s debate in the United States and abroad over revolutions in military affairs. Many friends and professional colleagues, both within CSBA and outside the Center, have contributed to this report. Those who made the most substantial improvements to the final manuscript are acknowledged below. However, the analysis and findings are solely the responsibility of the author and CSBA. 1667 K Street, NW, Suite 900 Washington, DC 20036 (202) 331-7990 CONTENTS ACKNOWLEGEMENTS .................................................. v SUMMARY ............................................................... ix GLOSSARY ………………………………………………………xix I. INTRODUCTION ..................................................... 1 Guided Munitions: Origins in the 1940s............. 3 Cold War Developments and Prospects ............ -
Table of Contents
Table of Contents March 2021 User’s Guide User’s Guide Index Index (System Type) ................................................................................................................................March 2021 Market Overviews Airborne AESA Fighter Radars: Northrop Grumman (#1) ............................................................... November 2020 Airborne AESA Fighter Radars: Raytheon (#2) ......................................................................................... July 2020 Airborne DIRCM Systems & Missile Warning Systems (MWS) ............................................................... May 2020 Airborne Large SAR/GMTI Radar Market ........................................................................................... August 2021 Airborne SOF TF/TA Radars ............................................................................................................ November 2020 Air Defense/BMD Radars: Fixed/Transportable Ground Systems ........................................................ August 2020 Ballistic Missile Defense (BMD): Mobile Ground Systems ............................................................. November 2020 F-16 Electronic Warfare (EW) Systems ..................................................................................................... July 2020 Naval Electronic Warfare (EW) Systems ............................................................................................. October 2020 USAF Legacy Bomber Electronics Programs ............................................................................................ -
Usafalmanac ■ Gallery of USAF Weapons
USAFAlmanac ■ Gallery of USAF Weapons By Susan H.H. Young The B-1B’s conventional capability is being significantly enhanced by the ongoing Conventional Mission Upgrade Program (CMUP). This gives the B-1B greater lethality and survivability through the integration of precision and standoff weapons and a robust ECM suite. CMUP will include GPS receivers, a MIL-STD-1760 weapon interface, secure radios, and improved computers to support precision weapons, initially the JDAM, followed by the Joint Standoff Weapon (JSOW) and the Joint Air to Surface Standoff Missile (JASSM). The Defensive System Upgrade Program will improve aircrew situational awareness and jamming capability. B-2 Spirit Brief: Stealthy, long-range, multirole bomber that can deliver conventional and nuclear munitions anywhere on the globe by flying through previously impenetrable defenses. Function: Long-range heavy bomber. Operator: ACC. First Flight: July 17, 1989. Delivered: Dec. 17, 1993–present. B-1B Lancer (Ted Carlson) IOC: April 1997, Whiteman AFB, Mo. Production: 21 planned. Inventory: 21. Unit Location: Whiteman AFB, Mo. Contractor: Northrop Grumman, with Boeing, LTV, and General Electric as principal subcontractors. Bombers Power Plant: four General Electric F118-GE-100 turbo fans, each 17,300 lb thrust. B-1 Lancer Accommodation: two, mission commander and pilot, Brief: A long-range multirole bomber capable of flying on zero/zero ejection seats. missions over intercontinental range without refueling, Dimensions: span 172 ft, length 69 ft, height 17 ft. then penetrating enemy defenses with a heavy load Weight: empty 150,000–160,000 lb, gross 350,000 lb. of ordnance. Ceiling: 50,000 ft. Function: Long-range conventional bomber. -
The F-16'S Evolution from a Lightweight Day Fighter to a Deep
© Cem DOĞUT The F-16’s Evolution from a Lightweight Day Fighter to a Deep Strike Aircraft In 1968, the United States Thus, it could easily change Indo-Pakistan conflicts, started a new aircraft its speed, altitude, and the USAF requested a fast project following the direction. Also, it would be and high maneuverable by Cem DOĞUT development of the high- difficult to detect the light aircraft that weighs 20 pylons was increased performance interceptor and, therefore, the small tons and is optimized for from two to three. The Mig-25 by the Soviet plane. It would also be combat at Mach 0.6 - 1.6 radar requirements were Union. The requirements cheap to manufacture and at an altitude of 30,000 - also changed, and the of the F-X project were operate. Later, Boyd and 40,000 feet. In May 1972, Westinghouse APG-66 40,000 lb. MTOW, a his team received funding the proposals of General multi-mode mission radar maximum speed of 2.5 from Northrop and General Dynamics and Northrop was selected. Mach, and a high thrust- Dynamics to develop these were selected, and the YF- to-weight ratio. In 1969, concepts. The Air Force did 16 and YF-17 prototypes On June 13, 1975, the U.S. McDonnell-Douglas's F-15 not support these efforts, were manufactured. The Air Force announced that was selected, leading the as it would undermine prototypes made their it had chosen the YF-16. In way to the birth of the the F-15 (Project F-X). maiden flights on February this choice, the P&W F100 fighter that would replace Finally, they realized that 2, 1974, and June 9, 1974, turbofan engines used in the F-4 Phantom II. -
Simulation Programs Using Concurrent Computer Systems
SIMULATION PROGRAMS USING CONCURRENT COMPUTER SYSTEMS US AIR FORCE PROGRAMS US NAVY PROGRAMS OTHER GOVERNMENT PROGRAMS JAPAN FIGHTER AIRCRAFT Coast Guard HH-60 Jayhawk Active Phased Array Radar FIGHTER AIRCRAFT F-117A Nighthawk AH-1S Cobra F-14B/A Tomcat NASA Space Shuttle SMS F-15 Eagle C-1 Trader F/A-18 Hornet NASA X-29 US101 Helicopter C-130 Hercules BOMBER AIRCRAFT ATTACK AIRCRAFT F-15J WST INTERNATIONAL MILITARY PROGRAMS B-1B Lancer ERS A-6E Intruder FS-X/F-2 Avionics Development B-2 Spirit ATD Crew Trainer AUSTRALIA JSDF Anti-aircraft Artillery ELECTRONIC WARFARE B-52 Stratofortress WST Collins-class Submarine CCS OH-1 Ninja EA-6B Prowler F-111 Aardvark Avionics Development P-3C Orion NEWTS Patriot Missile Defense ATTACK AIRCRAFT CZECKOSLOVAKIA P-3C Orion SH-60K Sea Hawk A-10 Thunderbolt L-159 ALCA S-3 Viking T-4 Trainer AC-130U Gunship FRANCE Agusta 129 Helicopter T-5 Trainer RESEARCH T-90 Tank MISSILES LEAP Program Airbus A400M CALCM Cruise E-2C Hawkeye TC-90 Trainer U-125A Peace Krypton HELICOPTERS Eurocopter US-1A Kai CARGO AIRCRAFT CH-46 Sea Knight Exocet Missile KOREA C-12F Huron CH-53 Sea Stallion Mirage 2000 Fighter F-16K Avionics Development C-130 Hercules MH-60R LAMPS Mistral Missile Hawk 60 Trainer C-17 Globemaster III SURFACE/SUBSURFACE Rafale Fighter KC-135 Stratotanker NETHERLANDS AGSS class sub GERMANY F-16 Eagle AGG2 Gepard Tank Tomahawk ACM Missile SAUDI ARABIA ELECTRONIC WARFARE C-160 Transall E-2C AWACS F-5 Tiger GENERAL TRAINERS CH-53G Helicopter EC-135 Looking Glass SINGAPORE 20F16 Tactical Command E-3A AWACS -
Weapons Pack
Weapons Pack for Strike Fighters: Project 1 Wings Over Vietnam Wings Over Europe 03 Jul 2006 ________________________________________________________________________ Rob "Bunyap" McCray [email protected] www.bunyap2w1.com Overview This project is designed to provide a hassle free way of obtaining every 3rd party released weapon and gun. It will be updated after every aircraft release to include the newly created ordnance, gun types, and fuel tanks. All data is checked and verified by experts to provide the most realistic weapons effects and performance possible. The Weapons Pack is compatible with Strike Fighters: Project 1, Wings Over Vietnam, and Wings Over Europe. This version of the Weapons Pack has been re-designed with a far superior system for nation and date assignments than previous versions. Modified aircraft data must be used to take advantage of this. Instructions for installing this data and modifying aircraft that are not included are provided. Some other enhancements include functional targeting pods, guidance for laser, EO, IIR, and GPS guided bombs, better missile guidance, functional EO/IR guided missiles, and functional weapon availability dates. Effects created by Deuces or based on his work are included covering the range of weapons currently available. These include: Bomb explosion effects of various sizes. Cluster Bomb explosion effects. Rocket Launcher effects. Missile and Rocket motor effects. Smoke trails. White Phosphorus explosion effects. Colored smoke effects for WP rockets. Leaflet bomb effects. Chaff and flare effects. White Phosphorus smoke for Anti-radiation missiles. Inert bomb and rocket effects. Spotting charge effects for practice bombs. Rocket sub-munition effects. Illumination flare effects. Napalm explosion effects. -
Gallery of USAF Weapons Note: Inventory Numbers Are Total Active Inventory Figures As of Sept
Gallery of USAF Weapons Note: Inventory numbers are total active inventory figures as of Sept. 30, 2015. By Aaron M. U. Church, Senior Editor ■ 2016 USAF Almanac BOMBER AIRCRAFT B-1 Lancer Brief: Long-range bomber capable of penetrating enemy defenses and de- livering the largest weapon load of any aircraft in the inventory. COMMENTARY The B-1A was initially proposed as replacement for the B-52, and four proto- types were developed and tested before program cancellation in 1977. The program was revived in 1981 as B-1B. The vastly upgraded aircraft added 74,000 lb of usable payload, improved radar, and reduced radar cross section, but cut maximum speed to Mach 1.2. The B-1B first saw combat in Iraq during Desert Fox in December 1998. Its three internal weapons bays accommodate a substantial payload of weapons, including a mix of different weapons in each bay. Lancer production totaled 100 aircraft. The bomber’s blended wing/ body configuration, variable-geometry design, and turbofan engines provide long range and loiter time. The B-1B has been upgraded with GPS, smart weapons, and mission systems. Offensive avionics include SAR for tracking, B-2A Spirit (SSgt. Jeremy M. Wilson) targeting, and engaging moving vehicles and terrain following. GPS-aided INS lets aircrews autonomously navigate without ground-based navigation aids Dimensions: Span 137 ft (spread forward) to 79 ft (swept aft), length 146 and precisely engage targets. Sniper pod was added in 2008. The ongoing ft, height 34 ft. integrated battle station modifications is the most comprehensive refresh in Weight: Max T-O 477,000 lb. -
Appendix: Delivery Systems and Munitions
Appendix Delivery Systems and Munitions Two major areas of development are of par- gets by placing a human observer on the scene. ticular interest for the follow-on forces attack Short-range missiles can incorporate relatively (FOFA) concept: reconnaissance, surveillance, simple guidance systems that offer substantial im- target acquisition, and data handling; and muni- provements in accuracy over free-fall munitions; tions and delivery systems. Little can be said but at longer ranges, providing high accuracy be- about the former in an unclassified report. This comes a complex engineering challenge. appendix provides information on munitions and delivery systems. Munitions for follow-on forces attack can be as simple as conventional high-explosive bombs. A weapon system is a combination of a deliv- But improvements in two general areas can sig- ery system and a munition. The delivery system— nificantly increase the usefulness of a munition an aircraft, a missile, or an aircraft launching a in follow-on forces attack: missile—needs to have several general capabil- ities if it is to be of use in follow-on forces attack: ● kill radius: a conventional 500-lb high-ex- plosive bomb must land within a meter of ● range: FOFA targets will be located any- a tank to put it out of action; a munition with where from 30 km back to as far as the a greater area of effect need not be delivered Polish-Soviet border, some 800 km from the so accurately and may in addition be able inter-German border; to engage multiple targets; and ● accuracy: depending -
Gallery of USAF Weapons Note: Inventory Numbers Are Total Active Inventory Figures As of Sept
Gallery of USAF Weapons Note: Inventory numbers are total active inventory figures as of Sept. 30, 2009. By Susan H. H. Young ■ 2010 USAF Almanac Bombers B-1 Lancer Brief: A long-range, air refuelable multirole bomber capable of flying intercontinental missions and penetrating enemy defenses with the largest payload of guided and unguided weapons in the Air Force inventory. Function: Long-range conventional bomber. Operator: ACC, AFMC. First Flight: Dec. 23, 1974 (B-1A); Oct. 18, 1984 (B-1B). Delivered: June 1985-May 1988. IOC: Oct. 1, 1986, Dyess AFB, Tex. (B-1B). Production: 104. Inventory: 66. Aircraft Location: Dyess AFB, Tex., Edwards AFB, Calif., Eglin AFB, Fla., Ellsworth AFB, S.D. Contractor: Boeing; AIL Systems; General Electric. Power Plant: four General Electric F101-GE-102 turbo- fans, each 30,780 lb thrust. Accommodation: four, pilot, copilot, and two systems officers (offensive and defensive), on zero/zero ACES II B-1B Lancer (Clive Bennett) ejection seats. Dimensions: span spread 137 ft, swept aft 79 ft, length 146 ft, height 34 ft. towed decoy complement its low radar cross section to First Flight: July 17, 1989. Weight: empty 192,000 lb, max operating weight form an integrated, robust onboard defense system that Delivered: Dec. 20, 1993-2002. 477,000 lb. supports penetration of hostile airspace. IOC: April 1997, Whiteman AFB, Mo. Ceiling: more than 30,000 ft. B-1A. USAF initially sought this new bomber as a replace- Production: 21. Performance: max speed at low level high subsonic, ment for the B-52, developing and testing four prototypes Inventory: 20. -
Operation Iraqi Freedom Saw the Baathist Regime of Air Support Due to Its Modest Spalling* Radius
TECHNOLOGY EXPLAINED – IRAQI FREEDOM by Carlo Kopp Guided Munitions Operation Iraqi Freedom saw the Baathist regime of air support due to its modest spalling* radius. The ‘en- Iraq collapse after just three weeks of sustained and hanced’ GPS and inertial guidance equipped EGBU-22 and concentrated air attacks by coalition aircraft, sup- EGBU-24 supplemented stocks of baseline GBU-22/B and ported by ground forces which aided in flushing out GBU-24G/B, while the EGBU-27/B supplemented the targets for air attack. It was by any measure an excep- baseline GBU-27 Paveway III carried by the F-117A – the tional achievement, reflecting the maturity and so- latter the specific weapon claimed to have been used in phistication of modern airpower. the initial bunker strike. With GPS/inertial capability and a While a good proportion of the combat effect achieved in Mil-Std-1760 interface, the ‘enhanced’ Paveway bombs re- Iraq can be attributed to clever deployment and use of air vert to autonomous GPS aided inertial guidance should assets, the technology of the systems and munitions used the laser lock be lost, upon which they behave not unlike played a no less important role. Airpower is the sum of the much cheaper JDAM – an important consideration dur- technique and technology, and this has never been as appar- ing urban strikes where collateral damage does matter. ent as in Operation Iraqi Freedom. The heavyweight in the Paveway III family is the 5000lb GBU-28/BLU-113/B bunker buster, often dubbed ‘Deep Laser Guided Munitions Throat’. Originally carried by the F-111F and first used in The laser guided bomb was one of the pillars of the air Iraq in 1991, this weapon continues to be carried by the campaign, especially the battlefield interdiction effort and F-15E.