Fluid Catalytic Cracking Unit
Total Page:16
File Type:pdf, Size:1020Kb
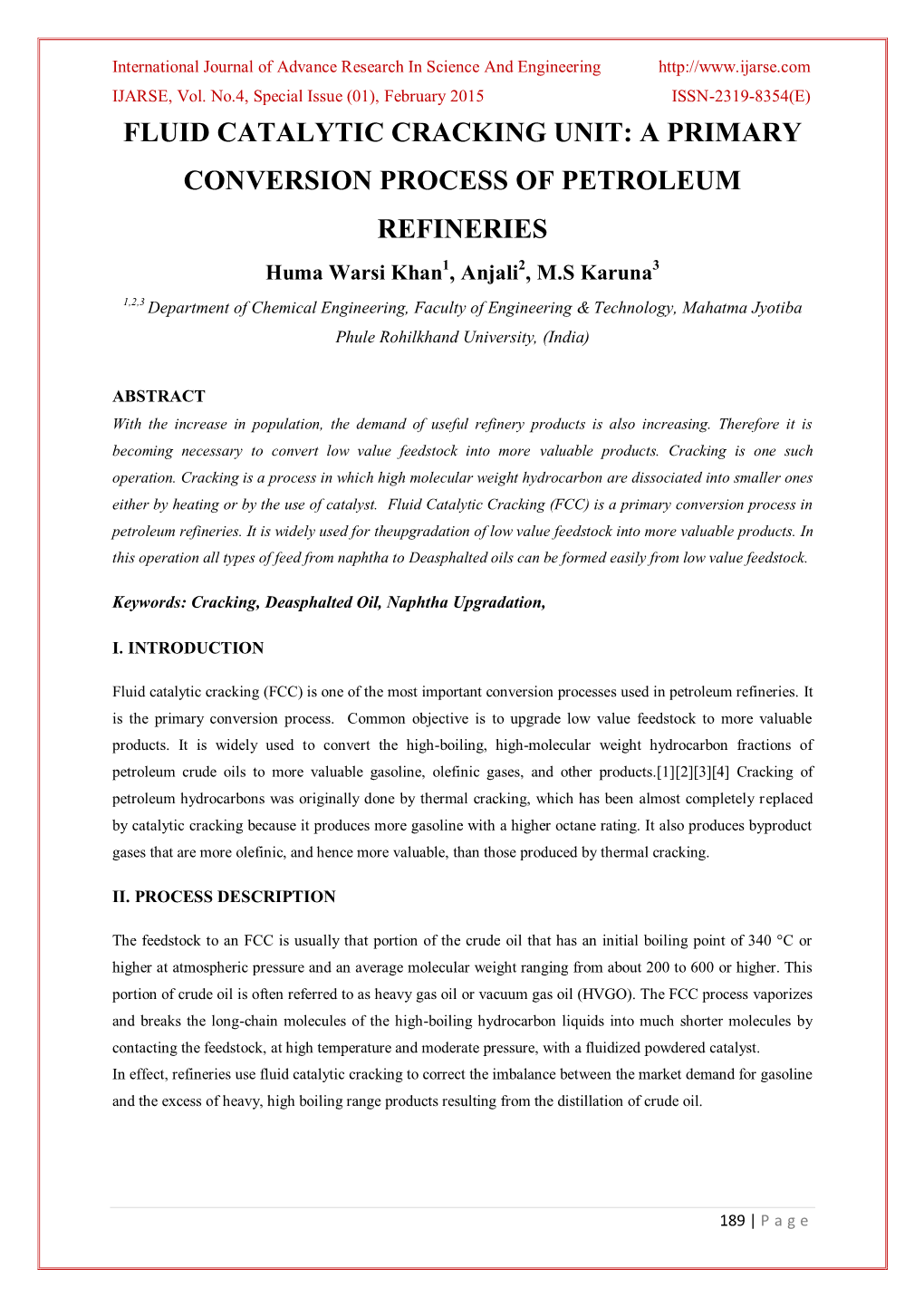
Load more
Recommended publications
-
The Chemistry of Sulfur in Fluid Catalytic Cracking
Catalytic Reduction of Sulfur in Fluid Catalytic Cracking Rick Wormsbecher Collaborators Grace Davison Laboratoire Catalyse et Spectrochimie, CNRS, Université de Caen Ruizhong Hu Michael Ziebarth Fabian Can Wu-Cheng Cheng Francoise Maugé Robert H. Harding Arnaud Travert Xinjin Zhao Terry Roberie Ranjit Kumar Thomas Albro Robert Gatte Outline • Review of fluid catalytic cracking. • Sulfur balance and sulfur cracking chemistry. • Catalytic reduction of sulfur by Zn aluminate/alumina. Fluid Catalytic Cracking • Refinery process that “cracks” high molecular weight hydrocarbons to lower molecular weight. • Refinery process that provides ~50 % of all transportation fuels indirectly. • Provides ~35 % of total gasoline pool directly from FCC produced naphtha. • ~80 % of the sulfur in gasolines comes from the FCC naphtha. Sulfur in Gasoline • Sulfur compounds reversibly poison the auto emission catalysts, increasing NOx and hydrocarbon emission. SOx emissions as well. • World-wide regulations to limit the sulfur content of transportation fuels. – 10 - 30 ppm gasoline. • Sulfur can be removed by hydrogenation chemistry. – Expensive. – Lowers fuel quality. Fluid Catalytic Cracking Unit Products Riser Flue Gas Reactor (~500 ºC) Regenerator (~725 ºC) Reaction is endothermic. 400 tons Catalyst circulates from catalyst Riser to Regenerator. inventory 50, 000 Air Feedstock barrels/day Carbon Distribution H2 ~0.05 % Flare C1 ~1.0 % Flare Petrochem Feed C2-C4 ~14-18 % Naphtha MW ~330 g/mole C5-C11 ~50 % C12-C22 ~15-25 % LCO C22+ ~5-15 % HCO Coke ~3-10 % -
Exxonmobil Torrance Refinery Electrostatic Precipitator Explosion Torrance, California
InvestigationInvestigation Report Report ExxonMobil Torrance Refinery Electrostatic Precipitator Explosion Torrance, California Incident Date: February 18, 2015 On-Site Property Damage, Catalyst Particles Released to Community, Near Miss in MHF Alkylation Unit No. 2015-02-I-CA KEY ISSUES: • Lack of Safe Operating Limits and Operating Procedure • Safeguard Effectiveness • Operating Equipment Beyond Safe Operating Life • Re-use of Previous Procedure Variance Without Sufficient Hazard Analysis Published May 2017 CSB · ExxonMobil Torrance Refinery Investigation Report The U.S. Chemical Safety and Hazard Investigation Board (CSB) is an independent Federal agency whose mission is to drive chemical safety change through independent investigations to protect people and the environment. The CSB is a scientific investigative organization; it is not an enforcement or regulatory body. Established by the Clean Air Act Amendments of 1990, the CSB is responsible for determining accident causes, issuing safety recommendations, studying chemical safety issues, and evaluating the effectiveness of other government agencies involved in chemical safety. More information about the CSB is available at www.csb.gov. The CSB makes public its actions and decisions through investigative publications, all of which may include safety recommendations when appropriate. Examples of the types of publications include: CSB Investigation Reports: formal, detailed reports on significant chemical accidents and include key findings, root causes, and safety recommendations. CSB Investigation Digests: plain-language summaries of Investigation Reports. CSB Case Studies: examines fewer issues than a full investigative report, case studies present investigative information from specific accidents and include a discussion of relevant prevention practices. CSB Safety Bulletins: short, general-interest publications that provide new or timely information intended to facilitate the prevention of chemical accidents. -
ADVANCES in FLUID CATALYTIC CRACKING (November 2005)
Abstract Process Economics Program Report 195A ADVANCES IN FLUID CATALYTIC CRACKING (November 2005) Recent emphasis in fluid catalytic cracking is on maximum light olefins production, gasoline sulfur reduction and compliance with FCCU NOx and SOx emissions requirements. New cracking catalysts and additives for the reduction of NOx, SOx and gasoline sulfur continue to significantly improve FCCU operation. New hardware designs offer improved unit operation and efficiency. Areas of recent new hardware design improvements include the standpipe inlet, third stage cyclones, spent catalyst distributor and catalyst stripping. Wet gas scrubbers or selective catalytic reduction may now be required in some cases to meet emissions requirements. This report provides an overview of FCC developments in catalyst, process and hardware technologies since PEP Report 195, Advances in Fluid Catalytic Cracking, issued in 1991. The report then develops process economics for cracking the most common type of FCC feedstock, vacuum gas oil. PEP Report 228, Refinery Residue Upgrading, issued in 2000 reviews the special issues and technology of Residual Fluid Catalytic Cracking (RFCC) and develops process economics for cracking a residual feedstock. Since the refinery production of light olefins such as propylene offers refiners in some regions, especially Asia and Western Europe, an opportunity for profit, the process economics of maximum light olefins FCC from VGO are developed. Air emissions (SOX, NOX) from FCCUs and the reduction of FCC gasoline sulfur are major environmental issues discussed. Professionals and managers involved in the energy industry who manage, research, develop, plan, operate, design plants or manage investments in the petroleum refining and allied industries could benefit from the information contained in this report. -
THE H-OIL PROCESS: a Worldwxide LEADER in VACUUM RESIDUE HYDROPROCESSING” \ ^
—t&CR I'd, D 3 YJj TT-097 CONEXPO ARPEL '96 . i ' 1 "THE H-OIL PROCESS: A WORLDWXiDE LEADER IN VACUUM RESIDUE HYDROPROCESSING” \ ^ J.J. Colyar1 L.I. Wisdom2 A. Koskas3 SUMMARY With the uncertainty of market trends, refiners will need to hedge their investment strategies in the future by adding processing units that provide them with flexibility to meet the changing market. The various process configurations involving the H-Oil® Process described in this paper have been tested commercially and provide the refiner with the latest state of the art technology. ABSTRACT The H-Oil® Process is a catalytic hydrocracking process, invented by HRI, Inc., a division of IFP Enterprises, Inc. which is used to convert and upgrade petroleum residua and heavy oils. Today the H-Oil Process accounts for more than 50 percent of the worldwide vacuum residue hydroprocessing market due to its unique flexibility to handle a wide variety of heavy crudes 'while producing clean transportation fuels. The process is also flexible in terms of changes in yield selectivity and product quality. The unconverted vacuum residue from the process can be utilized for fuel oil production, blended into asphalt, routed to resid catalytic cracking, directly combusted or gasified to produce hydrogen. This paper will discuss additional background information on the H-Oil Process, some of the key advances made to the process and applications for the Latin America market. The paper will also discuss the status of recent commercial plants which are in operation or which are under design or construction and which utilize these new advances. -
Visbreaking: a Technology of the Past and the Future
View metadata, citation and similar papers at core.ac.uk brought to you by CORE provided by Elsevier - Publisher Connector Scientia Iranica C (2012) 19 (3), 569–573 Sharif University of Technology Scientia Iranica Transactions C: Chemistry and Chemical Engineering www.sciencedirect.com Visbreaking: A technology of the past and the future J.G. Speight ∗ CD&W Inc., 2476 Overland Road, Laramie, WY 82070, USA Received 18 August 2011; revised 1 December 2011; accepted 28 December 2011 KEYWORDS Abstract Because of their relative simplicity of design and straightforward thermal approach, visbreaking Petroleum refining; processes will not be ignored or absent from the refinery of the future. However, new and improved Visbreaking; approaches are important for the production of petroleum products. These will include advances in current Fouling. methods, minimization of process energy losses, and improved conversion efficiency. In addition, the use of additives to encourage the preliminary deposition of coke-forming constituents is also an option. Depending upon the additive, disposal of the process sediment can be achieved by a choice of methods. ' 2012 Sharif University of Technology. Production and hosting by Elsevier B.V. Open access under CC BY-NC-ND license. 1. Introduction variables are (1) feedstock type, (2) temperature, (3) pressure, and residence time, which need to be considered to control the extent of cracking. Balancing product yield and market demand, without the manufacture of large quantities of fractions having low com- 2. The visbreaking process mercial value, has long required processes for the conversion of hydrocarbons of one molecular weight range and/or struc- Visbreaking (viscosity reduction, viscosity breaking), a mild ture into some other molecular weight ranges and/or struc- form of thermal cracking, insofar as thermal reactions are tures. -
5.1 Petroleum Refining1
5.1 Petroleum Refining1 5.1.1 General Description The petroleum refining industry converts crude oil into more than 2500 refined products, including liquefied petroleum gas, gasoline, kerosene, aviation fuel, diesel fuel, fuel oils, lubricating oils, and feedstocks for the petrochemical industry. Petroleum refinery activities start with receipt of crude for storage at the refinery, include all petroleum handling and refining operations and terminate with storage preparatory to shipping the refined products from the refinery. The petroleum refining industry employs a wide variety of processes. A refinery's processing flow scheme is largely determined by the composition of the crude oil feedstock and the chosen slate of petroleum products. The example refinery flow scheme presented in Figure 5.1-1 shows the general processing arrangement used by refineries in the United States for major refinery processes. The arrangement of these processes will vary among refineries, and few, if any, employ all of these processes. Petroleum refining processes having direct emission sources are presented on the figure in bold-line boxes. Listed below are 5 categories of general refinery processes and associated operations: 1. Separation processes a. Atmospheric distillation b. Vacuum distillation c. Light ends recovery (gas processing) 2. Petroleum conversion processes a. Cracking (thermal and catalytic) b. Reforming c. Alkylation d. Polymerization e. Isomerization f. Coking g. Visbreaking 3.Petroleum treating processes a. Hydrodesulfurization b. Hydrotreating c. Chemical sweetening d. Acid gas removal e. Deasphalting 4.Feedstock and product handling a. Storage b. Blending c. Loading d. Unloading 5.Auxiliary facilities a. Boilers b. Waste water treatment c. Hydrogen production d. -
The Role of Fluid Catalytic Cracking in Process Optimisation for Petroleum Refineries Chinwendu R
World Academy of Science, Engineering and Technology International Journal of Chemical and Molecular Engineering Vol:13, No:7, 2019 The Role of Fluid Catalytic Cracking in Process Optimisation for Petroleum Refineries Chinwendu R. Nnabalu, Gioia Falcone, Imma Bortone relative to its backup height for sustaining catalyst loads. Abstract—Petroleum refining is a chemical process in which the Increase in capacity and, subsequently, an increase in pressure raw material (crude oil) is converted to finished commercial products drop leads to dipleg plugging with catalysts, and on reaching for end users. The fluid catalytic cracking (FCC) unit is a key asset in the cyclone’s bottom, catalysts losses may occur due to it refineries, requiring optimised processes in the context of engineering being carried over. The inadequate performance of the unit design. Following the first stage of separation of crude oil in a distillation tower, an additional 40 per cent quantity is attainable in would lead to significant catalyst losses, operation at reduced the gasoline pool with further conversion of the downgraded product capacity intake, and reduced process performance in achieving of crude oil (residue from the distillation tower) using a catalyst in specified product yields and emission limits. FCC separation the FCC process. Effective removal of sulphur oxides, nitrogen systems are installed in a variety of ways such as single, two- oxides, carbon and heavy metals from FCC gasoline requires greater stage, third-stage separation (TSS) and fourth-stage separation separation efficiency and involves an enormous environmental (FSS) [2]-[4]. According to the Climate and Clean Air significance. The FCC unit is primarily a reactor and regeneration system which employs cyclone systems for separation. -
Waste Edible Oil Fluid Catalytic Cracking in a Downer Reactor
Refereed Proceedings The 12th International Conference on Fluidization - New Horizons in Fluidization Engineering Engineering Conferences International Year 2007 Waste Edible Oil Fluid Catalytic Cracking in a Downer Reactor Xiaoping Tang∗ Fei Weiy ∗Tsinghua University, [email protected] yTsinghua University This paper is posted at ECI Digital Archives. http://dc.engconfintl.org/fluidization xii/77 FLUIDIZATION XII 631 Tang and Wei: Waste Edible Oil Fluid Catalytic Cracking in a Downer Reactor WASTE EDIBLE OIL FLUID CATALYTIC CRACKING IN A DOWNER REACTOR Xiaoping Tang, Fei Wei, Yong Jin Department of Chemical Engineering, Tsinghua University, Beijing, China ABSTRACT The waste edible oil used as feedstock of a downer fluid catalytic cracking process (FCC), an environment friendly process to produce clean fuel and high-value chemical materials, was studied in a small hot model of downer reactor. The process has the similar product distribution to petroleum-based fuel fluid catalytic cracking process. And the desired products with trace sulfur contents have the similar molecular weight and chemical structure to the gasoline and diesel from petroleum- based fuel. Therefore, the waste edible oil fluid catalytic cracking is a promising process, with both economic and environmental benefit. INTRODUCTION The waste edible oil which is mainly from the catering trade is a kind of fluid with high viscosity and acid value. The annual generation of waste edible oil in US is about 4.54~11.35 Million tons(1); in Japan is 0.4 MT(2); in the European Union is 0.71MT(3); in China is more than 1.2 MT(4).Thus, how to treat the waste edible oil becomes one of the focuses to academic community, government and public. -
Effects of Catalyst Properties on Hydrodesulfurization of Fluid
The Pennsylvania State University The Graduate School Department of Energy and Mineral Engineering EFFECTS OF CATALYST PROPERTIES ON HYDRODESULFURIZATION OF FLUID CATALYTIC CRACKING DECANT OILS AS FEEDSTOCK FOR NEEDLE COKE A Thesis in Energy and Mineral Engineering by Joseph P. Abrahamson © 2015 Joseph P. Abrahamson Submitted in Partial Fulfillment of the Requirements for the Degree of Master of Science May 2015 The thesis of Joseph P. Abrahamson was reviewed and approved* by the following: Semih Eser Professor of Energy and Geo-Environmental Engineering Thesis Advisor Jonathan P. Mathews Associate Professor of Energy and Mineral Engineering Caroline Burgess Clifford Senior Research Associate Luis F. Ayala H. Associate Professor of Petroleum and Natural Gas Engineering Associate Department Head for Graduate Education *Signatures are on file in the Graduate School ii ABSTRACT This thesis investigates hydrodesulfurization of fluid catalytic cracking decant oils and its impact on carbonaceous mesophase development during carbonization. Delayed Coking of decant oils leads to the development of carbonaceous mesophase, a liquid crystalline phase, that is responsible for the structural anisotropy of needle coke. Because of its anisotropic microstructure, needle coke is used as the filler along with a coal tar pitch binder for manufacturing graphite electrodes for electric-arc furnaces. When sulfur content of the filler needle coke is high (>0.8 wt. %) an irreversible volume expansion (puffing) takes place when extruded electrodes are subjected to graphitization heat treatment. Puffing in needle coke results primarily from the evolution of sulfur in the form of CS2 and H2S. Puffing causes the formation of mico-cracks reducing the quality of electrodes. -
BP Whiting Refinery
National Environmental & Safety Conference April 23-24, 2002 New Orleans Hilton Riverside New Orleans, LA ENV-03-128 Selective Catalytic Reduction of NOx From Fluid Catalytic Cracking Case Study: BP Whiting Refinery Presented By: Gerald Bouziden BP K. Gentile Mitsubishi Power Systems, Inc. R.G. Kunz Cormtech, Inc. National Petrochemical & Refiners Association 1899 L Street, NW 202.457.0480 voice Suite 1000 202.429.7726 fax Washington, DC www.npra.org 20036.3896 This paper has been reproduced for the author or authors as a courtesy by the National Petrochemical & Refiners Association. Publication of this paper does not signify that the contents necessarily reflect the opinions of the NPRA, its officers, directors, members, or staff. Requests for authorization to quote or use the contents should be addressed directly to the author(s) Selective Catalytic Reduction of NOx from Fluid Catalytic Cracking - Case Study: BP Whiting Refinery G.D. Bouziden BP Whiting Business Unit Whiting, Indiana J.K. Gentile Mitsubishi Power Systems, Inc. (MPS) Newport Beach, California R.G. Kunz Cormetech, Inc. Environmental Technologies Durham, North Carolina ABSTRACT One of the newest examples of selective catalytic reduction (SCR) in service on a fluid catalytic cracking unit (FCCU) is scheduled to begin operation in October 2003 at the BP Products North America Inc. (BP) refinery in Whiting, Indiana. This application is a step beyond the typical refinery boiler/heater/furnace case since treatment of nitrogen oxides (NOx) in the regenerator flue gas must account for the other atmospheric contaminants generated simultaneously in the FCCU process. Such conditions typically include a high particulate loading. -
Olefins Recovery CRYO-PLUS(PDF 4.0
02 REFINING & PETROCHEMICAL EXPERIENCE Linde Process Plants, Inc. (LPP) has constructed more than twenty (20) CRYO-PLUS™ units since 1984. Proprietary Technology Higher Recovery with Less Energy Refinery Configuration Designed to be used in low-pressure hydrogen-bearing Some of the principal crude oil conversion processes are off-gas applications, the patented CRYO-PLUS™ process fluid catalytic cracking and catalytic reforming. Both recovers approximately 98% of the propylene and heavier processes convert crude products (naphtha and gas oils) components with less energy required than traditional into high-octane unleaded gasoline blending components liquid recovery processes. (reformate and FCC gasoline). Cracking and reforming processes produce large quantities of both saturated and unsaturated gases. Higher Product Yields The resulting incremental recovery of the olefins such as propylene and butylene by the CRYO-PLUS™ process means Excess Fuel Gas in Refineries that more feedstock is available for alkylation and polym- The additional gas that is produced overloads refinery erization. The result is an overall increase in production of gas recovery processes. As a result, large quantities of high-octane, zero sulfur, gasoline. propylene and propane (C3’s), and butylenes and butanes (C4’s) are being lost to the fuel system. Many refineries produce more fuel gas than they use and flaring of the excess gas is all too frequently the result. Our Advanced Design for Ethylene Recovery The CRYO-PLUS C2=™ technology was specifically designed to recover ethylene and heavier hydrocarbons from low-pressure hydrogen-bearing refinery off-gas streams. Our patented design has eliminated many of the problems associated with technologies that predate the CRYO-PLUS C2=™ technology. -
BY ELECTRONIC MAIL 17 June 2019 Jack Broadbent, Air Pollution
350 Bay Area Alameda Interfaith Climate Action Network Benicians for a Safe and Health Community Citizen Air Monitoring Network Communities for a Better Environment Crockett-Rodeo United to Defend the Environment Good Neighbor Steering Committee — Benicia BY ELECTRONIC MAIL Greenaction for Health and Environmental Justice Idle No More SF Bay 17 June 2019 Interfaith Climate Action Network of Contra Costa County Richmond Progressive Alliance Jack Broadbent, Air Pollution Control Officer Rodeo Citizens Association Bay Area Air Quality Management District Sierra Club San Francisco Bay Chapter 375 Beale Street, Suite 600 Stand.Earth San Francisco, CA 94105 Sunflower Alliance West Marin Standing Together Request for Action Now to Prepare Environmental Health and Justice-critical Petroleum Refinery PM2.5 Emission Reduction Protections for Adoption As Soon As Practicable Dear Mr. Broadbent, On behalf of 16 organizations we request that you publish a schedule specifying public emission control rule development activities by the Bay Area Air Quality Management District (BAAQMD) to begin forth- with for each of these long-promised protections from deadly oil refinery PM2.5 emissions: Fluid Catalytic Cracking Unit (FCCU) wet scrubbing; Rule 6-5, delayed since 2015. Fuel gas hydrotreating; Rule 9-1, delayed since 2015. Refinery fuel combustion reduction strategy; Rule 13-XX, delayed since 2017. Cross-basin PM2.5 pollution trading ban; Rule 2-XX, delayed since 2017 (when BAAQMD deferred consideration of PM2.5 emission caps originally proposed as part of proposed Rule 12-16). Each of these protections was identified by BAAQMD, planned by BAAQMD for implementation 2–4 years ago, and found by BAAQMD staff at that time to be capable of cutting refinery emissions significantly based on refinery retrofit and/or operational measures which were demonstrated in practice.