Heavy Construction Equipment Noise Study Using Dosimetry and Time-Motion Studies
Total Page:16
File Type:pdf, Size:1020Kb
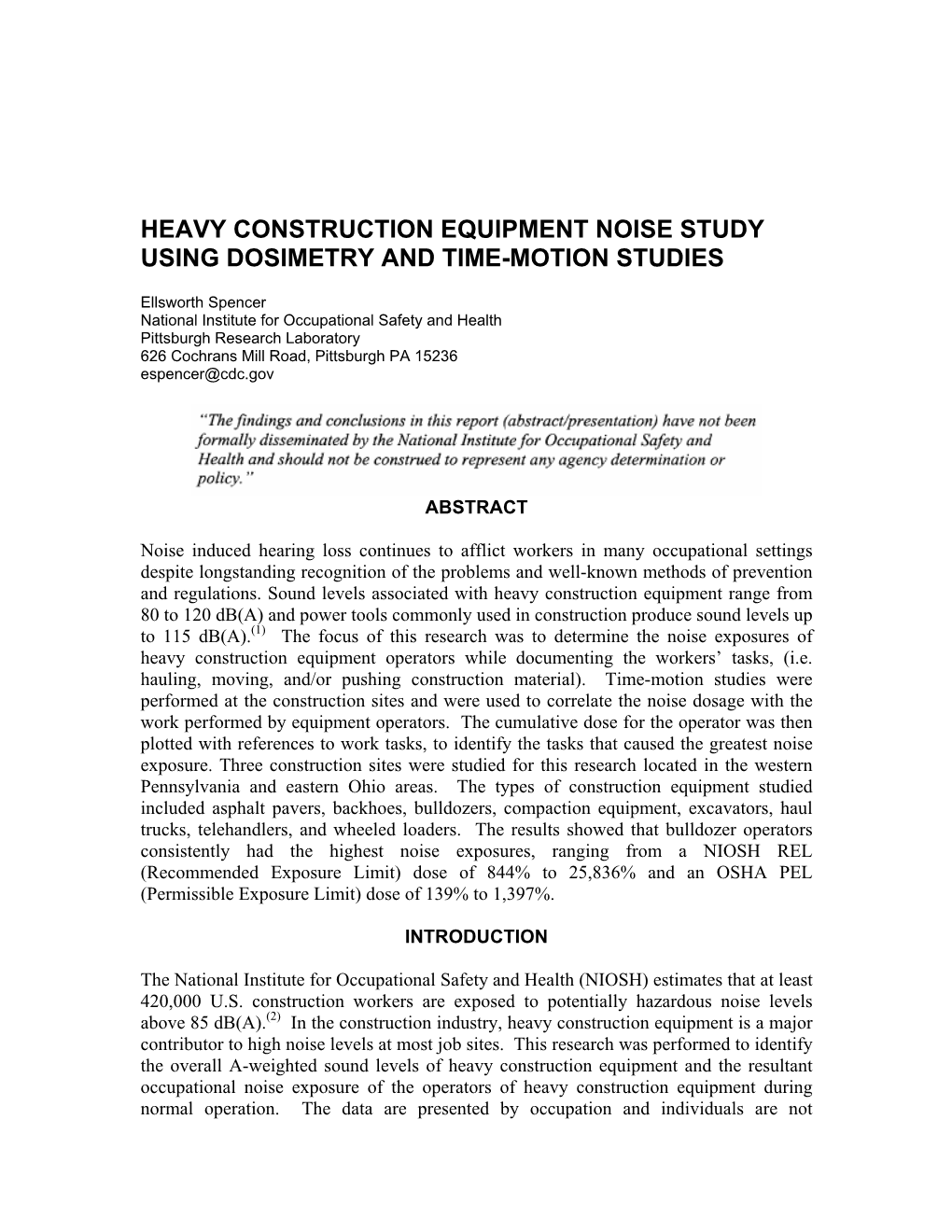
Load more
Recommended publications
-
Sloping and Benching Systems
Trenching and Excavation Operations SLOPING AND BENCHING SYSTEMS OBJECTIVES Upon the completion of this section, the participant should be able to: 1. Describe the difference between maximum allowable slope and actual slope. 2. Observe how the angle of various sloped systems varies with soil type. 3. Evaluate layered systems to determine the proper trench slope. 4. Illustrate how shield systems and sloping systems interface in combination systems. ©HMTRI 2000 Page 42 Trenching REV1 Trenching and Excavation Operations SLOPING SYSTEMS If enough surface room is available, sloping or benching the trench walls will offer excellent protection without any additional equipment. Cutting the slope of the excavation back to its prescribed angle will allow the forces of cohesion (if present) and internal friction to hold the soil together and keep it from flowing downs the face of the trench. The soil type primarily determines the excavation angle. Sloping a method of protecting employees from caveins by excavating to form sides of an excavation that are inclined away from the excavations so as to prevent caveins. In practice, it may be difficult to accurately determine these sloping angles. Most of the time, the depth of the trench is known or can easily be determined. Based on the vertical depth, the amount of cutback on each side of the trench can be calculated. A formula to calculate these cutback distances will be included with each slope diagram. NOTE: Remember, the beginning of the cutback distance begins at the toe of the slope, not the center of the trench. Accordingly, the cutback distance will be the same regardless of how wide the trench is at the bottom. -
DAO Level 3 Certificate in Military Engineering (Armoured) Titan and Trojan Crew Supervision
Qualification Handbook DAO Level 3 Certificate in Military Engineering (Armoured) Titan and Trojan crew supervision QN: 603/3232/3 The Qualification Overall Objective for the Qualifications This handbook relates to the following qualification: DAO Level 3 Certificate in Military Engineering (Armoured) Titan and Trojan crew supervision Pre-entry Requirements Learners are required to have completed the Class ME (Armd) Class 0-2 course, must be fully qualified AFV crewman and hold full category H driving licence Unit Content and Rules of Combination This qualification is made up of a total of 6 mandatory units and no optional units. To be awarded this qualification the candidate must achieve a total of 13 credits as shown in the table below. Unit Unit of assessment Level GLH TQT Credit number value L/617/0309 Supervise Titan Operation and 3 25 30 3 associated Equipment L/617/0312 Supervise Titan Crew 3 16 19 2 R/617/0313 Supervise Trojan Operation and 3 26 30 3 associated Equipment D/617/0315 Supervise Trojan Crew 3 16 19 2 H/617/0316 Supervise Trojan and Titan AFV 3 10 19 2 maintenance tasks K/617/0317 Carry out emergency procedures and 3 7 11 1 communication for Trojan and Titan AFV Totals 100 128 13 Age Restriction This qualification is available to learners aged 18 years and over. Opportunities for Progression This qualification creates a number of opportunities for progression through career development and promotion. Exemption No exemptions have been identified. 2 Credit Transfer Credits from identical RQF units that have already been achieved by the learner may be transferred. -
Earthwork Design and Construction
Technical Fundamentals for Design and Construction April 6, 2020 Earthwork Design and Construction Key Points • The primary objectives of earthwork operations are: (1) to increase soil bearing capacity; (2) control shrinkage and swelling; and (3) reduce permeability. • Particle shape is a critical physical soil property influencing engineering modification of a soil. • Proper water content is essential to economically achieve specified soil density. Purpose and Scope of Earthwork The purpose and scope of earth construction differ for various types of constructed facilities. The major types of earthwork projects include: • Transportation projects, which require embankments, roadways, and bridge approaches. • Water control, which usually involves dams, levies, and canals. • Landfill closures, which need impervious caps. • Building foundations, which must support loads and limit soil movement by shrinkage and swelling. Properly modified soils are the most economical solution for many constructed facilities. To meet structural support requirements, soils at some project sites may require treatment such as the addition of water, lime, or cement. 1 Technical Fundamentals for Earthwork Design, Materials, and Resources The physical chemical properties of project site soils have a major influence on the design of earthen structures and on the resources and operations needed to properly modify a soil. The fundamental properties of a soil include: granularity, course to fine; water content; specific gravity; and particle size distribution. Other properties include permeability, shear strength, and bearing capacity. The engineering design of a soil seeks to provide sufficient bearing capacity, settlement control, and either limit, in the case of dams and landfill caps, the movement of water or facilitate the movement of water in the case of drains, such as behind retaining walls. -
NSIAD-88-77 Army Disposal
United States General Accounting Office Report to the Chairman, Subcommittee on GAO>; Oversight and Investigations, Committee on Energy and Commerce, House of Representatives September 1988 ARMYDISPOSAL Construction Equipment Prematurely Disposed of in Europe RESTRKTED-Not to be released outside the Gend Accounting Office except on the basis of the specifk 8~4 by the Of&e of CongressionalRelations. United States General Accounting Office GAO Washington, D.C. 20548 National Security and International Affairs Division B-229358 September 20,1988 The Honorable John Dingell Chairman, Subcommittee on Oversight and Investigations Committee on Energy and Commerce House of Representatives Dear Mr. Chairman: The Army, having decided that its fleet of construction vehicles was becoming too costly to keep in repair, directed European units in 1985 to dispose of commercially available combat engineer construction vehi- cles. The Army purchased 850 replacement vehicles for Europe costing about $79 million. The purchase was part of a worldwide replacement program totaling about $470 million through fiscal year 1987. As you requested, we reviewed the Army’s replacement of construction vehicles in Europe. Our objective was to determine the basis for replac- ing these vehicles. We agree with the Army’s goal to replace worn-out vehicles with stan- dardized ones, but question its decision to dispose of usable vehicles without showing that it was cost-effective to do so. Army officials stated that old construction vehicles were difficult to support and that high repair costs made replacing the entire fleet -regardless of condi- tion-cost-effective. We found no analyses to support the Army’s position. -
Failure of Slopes and Embankments Under Static and Seismic Loading
American Scientific Research Journal for Engineering, Technology, and Sciences (ASRJETS) ISSN (Print) 2313-4410, ISSN (Online) 2313-4402 © Global Society of Scientific Research and Researchers http://asrjetsjournal.org/ Failure of Slopes and Embankments Under Static and Seismic Loading Nicolaos Alamanis* Lecturer, Dept. of Civil Engineering, Technological Educational Institute of Thessaly, Larissa, Greece, Civil engineer (National Technical University of Athens, D.E.A Ecole Centrale Paris) Email: [email protected] Summary The stability of slopes and embankments under the influence of static and seismic loads has been the subject of study for many researchers. This paper presents the mechanisms and causes of landslides as well as the forms of failure of slopes and embankments under static and seismic loading, with examples of failures from both Greek and international space. There is also mention to measures to protect and stabilize landslides, categories of slope stability analysis, and methods of seismic impact analysis. What follows is the determination of tolerable movements based on the caused damage on natural slopes, dams and embankments and an attempt is made to connect them with the vulnerability curves that are one of the key elements of stochastic seismic hazard. Particular importance is given to the statistical parameters of the mechanical characteristics of the sloping soil mass and to the simulation of random fields necessary for solving complex geotechnical works. Finally, we compare the simulation and description of random fields and the L.A.S. method is observed to be the most accurate of all simulation methods. The L.A.S. algorithm in conjunction with finite difference models can demonstrate the large fluctuations in the factor of safety values and the permanent seismic displacements of the slopes under the effect of seismic charges whose time histories are known. -
Construction Equipment
CONSTRUCTION EQUIPMENT U.S. PRICE LIST COMPACT EXCAVATORS PL-200 MX SAP REVISION 11 EFFECTIVE JULY 1, 2014 THIS IS AN ELECTRONIC COPY ONLY – HARD COPIES WILL NOT BE DISTRIBUTED. This price list is intended for dealers with the Compact Excavators (MX) contract only. The prices included in this revision supersede any prices established prior to the effective date shown unless specifically identified in a price bulletin as superseding this price list. Below is a list of Family(s) and Model(s) that are included in this price list. Crawler Excavator (Mini) CX17B CX27B CX31B T4 FINAL CX36B T4 FINAL CX55B T4 FINAL PLEASE NOTE: Retain the price book pages of the discontinued series for your records. Copyright 2014 By CNH Industrial America LLC Page 1 of 44 (This page intentionally left blank) Page 2 of 44 General Information Prices shown herein are suggested prices only and in no way are they to be construed as limiting or restricting the dealer in his determination of the ultimate retail selling price. It is understood that the dealers are free to determine their selling price. Subject to any Federal, State or local laws. Where shown herein liquid capacities are U.S. measure unless otherwise noted. ADVANCE FREIGHT Advance freight will be added to the machinery invoice as a separate net charge for machinery shipped from field locations or from other than specified Ex Works locations. PRICES Prices are Ex Works factory, where the goods are manufactured, except where noted. For detailed information concerning prices, please refer to your OPERATING GUIDE. Prices and specifications are subject to change without notice. -
Payandan Shareholders
PAYANDAN PAYANDAN 1. Company Background Creative Path to Growth Payandan Shareholders PAYANDAN Payandan’s shares belong to Mostazafan Foundation of Islamic Revolution. • Mostazafan Foundation owns 49% • Sina Energy Development Company owns 51% Mostazafan Foundation of Islamic Revolution Sina Energy Development Company PAYANDAN Mostazafan Foundation of Islamic Revolution PAYANDAN SEDCO Sina Financial Paya Saman Pars (Oil & Gas) & Investment Co (Road & Building) Sina Food Industries Iran Housing Group Saba Paya Sanat Sina (Power & Electricity) (Tire, Tiles, Glasswork, Textile, Etc) Ferdos Pars Sina ICT Group (Agriculture) Parsian Tourism Kaveh Pars & Transport Group (Mining) Alavi Foundation Alavi Civil (Charitable) Engineering Group Sina Energy Development Holding Company PAYANDAN SEDCO as one of subsidiaries of The Mostazafan Foundation of Islamic Revolution is considered one of pioneer holding companies in area of oil & gas which aims on huge projects in whole chains of oil and gas. Payandan (Oil & Gas General Contractor) North Drilling (Offshore Drilling) Pedex (Onshore Drilling) Behran (Oil Refinery Co) Dr Bagheri SEDCO Managing Director Coke Waste Water Refining Co Payandan in Numbers PAYANDAN +40 1974 Years ESTABLISHED +1400 +4000 EMPLOYEES CONTRACTOR +200,000,000 $ ANNUAL TURNOVER 75 COMPLETED PROJECTS Company Background PAYANDAN • 48” Zanjan-Mianeh Pipeline • 56” Saveh-Loushan • South Pars – SP No. 14 Pipeline (190KM) • South Pars – SP No. 13 • 56" Dezfoul- Kouhdasht Pipeline (160KM) 1974 1996 2003 2005 2007 2009 2011 2013 2015 2017 • Nargesi Gas • F & G Lavan • 56” Asaluyeh Gathering & • South Pars – SP Pipeline Injection No. 17 & 18 • 30” Iran- Payandan is • South Pars – SP No. 22,23,24 Armenia established (oil and • 48” Iraq Pipeline Naftkhane- Pipeline gas contractor) Baghdad (63KM) (113KM) • 56” Naeen-Tehran Gas Pipeline (133KM) • Parsian Gas Refinery • 56” Loushan-Rasht Gas Pipeline (81KM) • Pars Petrochemical Port • Arak Shazand Refinery • Kangan Gas Compressor Station • South Pars – SP No. -
Construction Sector Technical Education and Skills
TRAINING REGULATIONS Heavy Equipment Operation (Bulldozer) NC II CONSTRUCTION SECTOR TECHNICAL EDUCATION AND SKILLS DEVELOPMENT AUTHOR ITY East Service Road, South Superhighway, Taguig City, Metro Manila BULLDOZER TR HEAVY - EQUIPMENT OPERATION (Bulldozer) Promulgated July 2007 TABLE OF CONTENTS CONSTRUCTION - HEAVY EQUIPMENT SUB - SECTOR HEAVY EQUIPMENT OPERATION (BULLDOZER) NC II SECTION 1 HEAVY EQUIPMENT OPERATION QUALIFICATION SECTION 2 COMPETENCY STANDARDS SECTION 3 TRAINING STANDARDS 3.1 Curriculum Design 3. 2 Training Delivery 3.3 Trainee Entry Requirements 3.4 List of Tools, Equipment and Materials 3.5 Training Facilities 3.6 Trainers' Qualifications SECTION 4 ASSESSMENT AND CERTIFICATION ARRANGEMENT COMPETENCY MAP DEFINITION OF TERMS ACKNOWLEDGEMEN TS TR HEAVY - EQUIPMENT OPERATION (Bulldozer) Promulgated July 2007 TRAINING REGULATIONS FOR HEAVY EQUIPMENT OPERATION - BULLDOZER SECTION 1 HEAVY EQUIPMENT OPERATION - BULLDOZER The HEAVY EQUIPMENT OPERATION (BULLDOZER) NC II qualification consists of competencies that workers must achieve to enable them to perform tasks such as excavating, dozing, ripping, winching, and clearing of earth materials in construction sites or other locations. This qualification is packaged from the competency map of Construction - Heavy Equipment sub - sector as shown in Annex A. The units of competency comprising this qualification include the following: CODE NO. BASIC COMPETENCIES Units of Competency 500311105 Participate in workplace communication 500311106 Work in a team environment 500311107 Practice career professionalism 500311108 Practice occupational health and safety procedures CODE NO. COMMON COMPETENCIES Units of Competency CON931201 Prepare construction materials and tools CON311201 Observe procedures, specifications and manuals of inst ruction CON311202 Interpret technical drawings and plans CON311203 Perform mensurations and calculations CON311204 Maintain tools and equipment CODE NO. -
Grader Operators' Handbook
1 Schedule “A” Policy 3204 GRADER OPERATORS’ HANDBOOK 2 Athabasca County Grader Operator Hand Book Table of Contents Page I. SAFETY A. Accident Prevention 3 B. Planning Ahead 3 C. Accident Checklist 4 D. Working Alone 4 - 5 II. GRADER OPERATION A. Prestart Checks 5 B. Start-Up 6 C. Operating Safety Tips 7 D. Service & Repair 8 E. Parking & Disabled Grader 9 III. MAINTAINENCE STANDARDS A. Hazards / Unsafe Conditions 1. Responsibility 10 2. Types 10 B. Gravel Surface Maintenance 1. Regular Roadway Summer Maintenance 11-12 2. Intersections 12 3. Pulling Shoulders 12-13 4. Regravelling 13-14 5. Winter Maintenance 14-15 6. Dust Control 15 7. Railway Crossing 16 8. Bridges 16 3 I. SAFETY A. ACCIDENT PREVENTION: 1. Stop Accidents Before They Stop You i. Even the best and safest grader must still be operated with care and knowledge of its capabilities. Common sense, observance of safety rules and alertness on the job will result in “ACCIDENT FREE” days. ii. Accidents don’t just happen – they are caused by human error. So the person who has the ultimate responsibility is the grader operator – YOU! B. PLANNING AHEAD: 1. Records show that a majority of accidents are caused by a disregard for Safety Rules – OBEY THEM! 2. If you have questions don’t be afraid to ask your maintenance foreman. 3. Dress Properly For The Job – Find out what items are required and wear them. (Safety shoes, hearing protection, safety vests, etc.) 4. Understand Your Grader – Read the Operators Manual and know your machines limitations. 5. Use All the Safety Equipment your grader is equipped with. -
Guideline on Landslide Treatment and Mitigation
Guideline on Landslide Treatment and Mitigation Department of Soil Conservation and Watershed Management Department of Soil Conservation and Watershed Management G.P.O. BOX 4719, Babar Mahal, Kathmandu, Nepal Kathmandu, June 2016 T: 977-1-4220828/4220857 | F: 977-1-4221067 E: [email protected]/[email protected] (Asar 2073) W: www.dscwm.gov.np Guideline on Landslide Treatment and Mitigation Department of Soil Conservation and Watershed Management Kathmandu, June 2016 (Asar 2073) Publisher Department of Soil Conservation and Watershed Management, Ministry of Forests and Soil Conservation, Babar Mahal, Kathmandu, Nepal Cover photo credit Landslide in Rasuwa©Mr. Jagannath Joshi Credits © Department of soil Conservation and Watershed Management (DSCWM) Kathmandu, Nepal Landslide Treatment and Mitigation Sub-Group Coordinator: Mr. KesharMan Sthapit (FAO Nepal Office) Members: Mr. GehendraKeshariUpadhyaya (DSCWM) Dr. Jagannath Joshi (DSCWM) Mr. Deepak Bhardwaj (DSCWM) Mr. Shanmukhesh Chandra Amatya (Department of Water Induced Disaster Management) Ms. Laxmi Thagunna (Department of Environment) Ms. Racchya Shah (IUCN Nepal) Mr. Bhawani Shankar Dongol (WWF Nepal) Mr. Sanjay Devkota (Forum for Energy and Environment Development) Mr. Deo Raj Gurung (ICIMOD) Advisor: Mr. Purna Chandra Lal Rajbhandari (UNEP) Citation DSCWM (2016), Guideline on Landslide Treatment and Mitigation.Department of soil Conservation and Watershed Management, Kathmandu, Nepal. We are very thankful to USAID funded Hariyo Ban Program, WWF Nepal for providing support to edit, format and print this guideline. ii | Guideline on Landslide Treatment and Mitigation Guideline on Landslide Treatment and Mitigation | iii iv | Guideline on Landslide Treatment and Mitigation Preface The working group on “Landslide Treatment and Mitigation” was established following the recommendations of the consultative workshop on “Landslide Inventory, Risk Assessment, and Mitigation” organized by the Department of Soil Conservation and Watershed Management (DSCWM) from 28-29 September 2015 at Kathmandu. -
Control and Inspection of Earthwork Construction
PDHonline Course C284 (8 PDH) Control and Inspection of Earthwork Construction Instructor: George E. Thomas, PE 2012 PDH Online | PDH Center 5272 Meadow Estates Drive Fairfax, VA 22030-6658 Phone & Fax: 703-988-0088 www.PDHonline.org www.PDHcenter.com An Approved Continuing Education Provider www.PDHcenter.com PDH Course C284 www.PDHonline.org Control and Inspection of Structural Earthwork Construction George E. Thomas, PE A. Principles of Construction Control 1. General. In many types of engineering work, structural materials are manufactured to obtain certain characteristics; their use is prescribed by building codes, handbooks, and codes of practice established by various engineering organizations. However, for earth construction, the common practice is to use material that is available locally rather than specifying that a particular type of material of specific properties be secured. A variety of procedures exists by which earth materials may be satisfactorily incorporated into a structure. When earth is the construction material, personnel in charge of construction control must become familiar with design requirements and must verify that the finished product meets the requirements. Design of earth structures must allow for an inherent range of earth material properties. For maximum economy, tolerance ranges will vary according to available materials, conditions of use, and anticipated methods of construction. A closer relationship is required among the operations of inspection, design, and construction for earthwork than is needed in other engineering disciplines. Construction control of earth structures involves not only practices similar to those normally required for structures using manufactured materials, but also the supervision and inspection normally performed at the manufacturing plant. -
New Holland Attachments
ATTACHMENTS SKID STEER & COMPACT TRACK LOADERS LOADER BACKHOES | WHEEL LOADERS | TELEHANDLERS U.S. PRICING PM-17734 ATTACHMENTS SKID STEER & COMPACT TRACK LOADERS LOADER BACKHOES | WHEEL LOADERS | TELEHANDLERS TABLE OF CONTENTS General Information ..................................................................... GI-1 Skid Steer Loaders/Compact Track Loaders .............................. SS-1 Loader Backhoes ....................................................................... LBH-1 Compact Wheel Loaders .......................................................... CWL-1 Wheel Loaders ........................................................................... WL-1 Compact Excavators .................................................................. CEX-1 Telehandlers .............................................................................. TLH-1 Manufacturer’s Warranties ....................................................... MW-1 GENERAL INFORMATION SKID STEER LOADERS/ COMPACT TRACK LOADERS INDEX SKID STEER LOADERS/COMPACT TRACK LOADERS LS120, L120/LS125, L125 Attachments ....... SS-2-6 Mulcher ............................................................. SS-48 Adapter Plate ..................................................... SS-7 Pallet Fork .................................................. SS-49-50 Auger ............................................................ SS-8-10 Pallet Fork - Hydraulic Positioning ................. SS-51 Auto Rake ......................................................... SS-11 Post Driver ......................................................