Closer to the Store Closer to the Customer
Total Page:16
File Type:pdf, Size:1020Kb
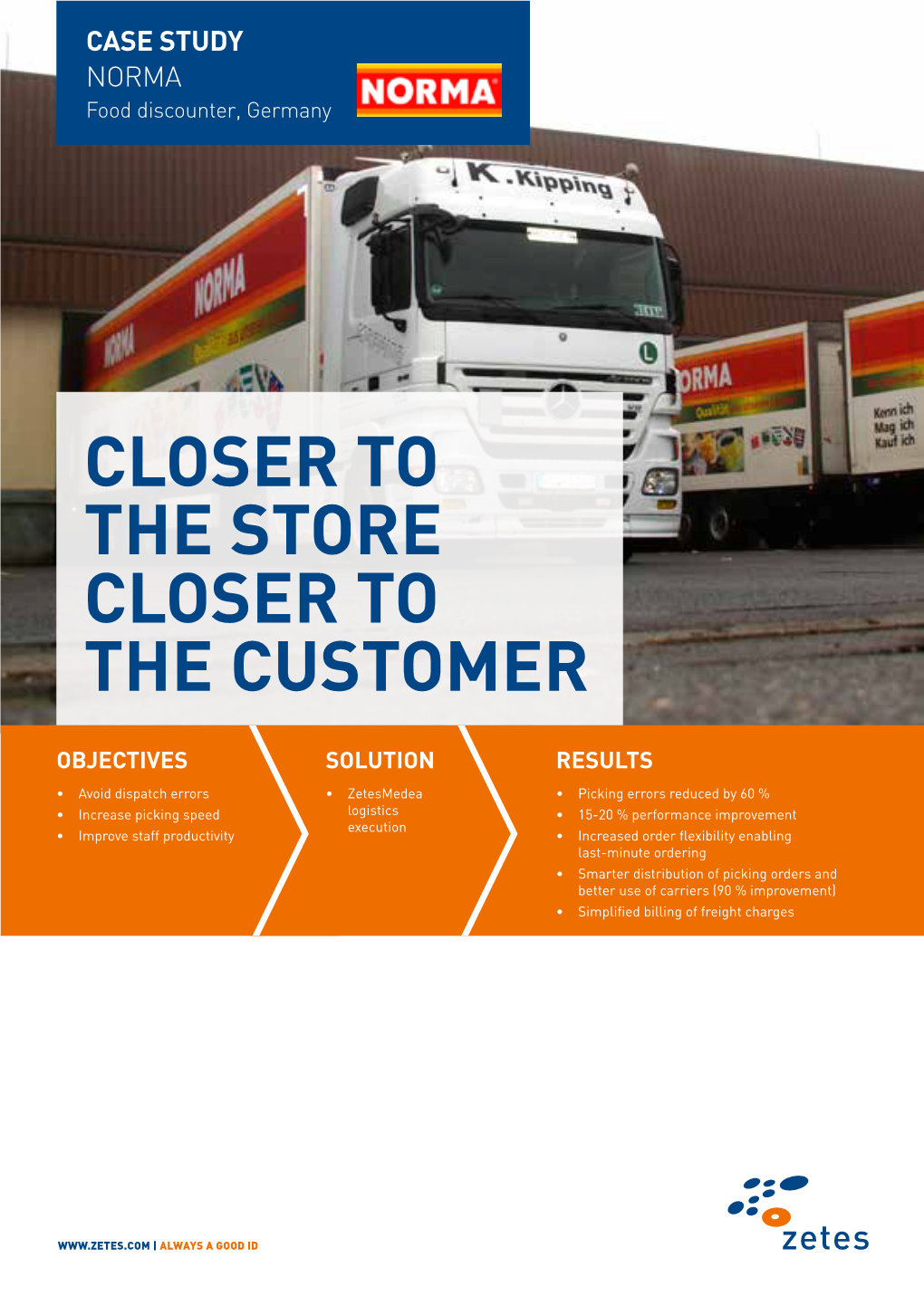
Load more
Recommended publications
-
Aiding Surveillance an Exploration of How Development and Humanitarian Aid Initiatives Are Enabling Surveillance in Developing Countries
Privacy International Aiding Surveillance An exploration of how development and humanitarian aid initiatives are enabling surveillance in developing countries Gus Hosein and Carly Nyst 01 October 2013 www.privacyinternational.org Aiding Surveillance — Privacy International Contents Executive Summary 04 Section 1 Introduction 05 Section 2 Methodology 15 Section 3 Management Information Systems 17 and electronic transfers Section 4 Digital identity registration and biometrics 28 Section 5 Mobile phones and data 42 Section 6 Border surveillance and security 50 Section 7 Development at the expense of human rights? 56 The case for caution Endnotes 59 03/80 Aiding Surveillance — Privacy International Executive Summary Information technology transfer is increasingly a crucial element of development and humanitarian aid initiatives. Social protection programmes are incorporating digitised Management Information Systems and electronic transfers, registration and electoral systems are deploying biometric technologies, the proliferation of mobile phones is facilitating access to increased amounts of data, and technologies are being transferred to support security and rule of law efforts. Many of these programmes and technologies involve the surveillance of individuals, groups, and entire populations. The collection and use of personal information in these development and aid initiatives is without precedent, and subject to few legal safeguards. In this report we show that as development and humanitarian donors and agencies rush to adopt new technologies that facilitate surveillance, they may be creating and supporting systems that pose serious threats to individuals’ human rights, particularly their right to privacy. 04/80 Section 1 Aiding Surveillance — Privacy International Introduction 1.0 It is hard to imagine a current public policy arena that does not incorporate new technologies in some way, whether in the planning, development, deployment, or evaluation phases. -
SEACHILL (UK) Ltd. CASE STUDY
SEACHILL (UK) Ltd CASE STUDY • Zero shipping errors • Complete supply chain visibility • Visual guidance for corrective actions • Rapid, automated handling of fresh fish products • Negligible tag costs • Fast deployment & ROI SEACHILL (UK) Ltd. VISIDOT CHOSEN FOR HIGHLY EFFECTIVE AUTOMATION AND 100% SHIPPING ACCURACY Seachill, now part of the Icelandic Group, was outbound products – became a bottleneck that formed in 1998 to become one of the UK’s could potentially limit throughput on large product leading fresh fish processors. Seachill sup- volumes. plies fresh fish to Tesco, the UK’s foremost food retailer. The company has demonstrated “Dispatch was having a hard time handling the strong and rapid growth, coinciding with both influx of data during shipping peaks,making it the development of the fresh fish market and very clear that we needed to research potential Tesco’s increasing share of that market. scanning and shipping automation solutions.” Seachill presently employs more than 600 employees at its Grimsby production plant, A number of options were considered, including which ships and delivers hundreds of fresh RFID. However, the prohibitive cost of RFID fish pallets a week. tags, especially in the context of high volumes of relatively low-cost products, and concern In early 2006, increasing customer demand for re- over RFID’s potential sensitivity to the cold and duced lead time and faster shipping turnaround damp conditions dominating the dispatch area prompted Seachill to seek a solution that would deemed the technology impractical for Seachill’s enable it to automate its dispatch area and speed needs. “After taking all of our requirements into up its shipping and dispatching processes. -
Katoen Natie Opts for a Zetes Print & Apply Solution
Katoen Natie opts for a Zetes Print & Apply solution 11/02/2009 The Spanish subsidiary of the Belgian group Katoen Natie is automating its labelling and dispatch control process with a P&A solution developedby MD, the Barcelona-based Zetes division specialising in this segment. This solution covers the needs of the Katoen Natie packaging and order preparation departments in line with the two objectives of eliminating labelling errors and boosting the productivity of the logistics centre. Barcelona, 11th of February 2009 - Zetes (Euronext Brussels: ZTS), the leading European integrator of solutions for the automatic identification of goods and people, has successfully completed the installation of a made-to- measure solution for the Spanish logistics centre of Katoen Natie, situated in Azuqueca de Henares (Guadalajara).Katoen Natie is therefore today working with a labelling and dispatch control system based on an automatic labelling solution (P&A) developed by Zetes. Katoen Natie is a company specialising in logistics for the petro-chemical, industrial, consumer goods and port operations sectors. The logistical centre that is hosting the solution includes 3000 square metres of warehouses occupied by an audiovisual company. Thousands of DVDs are sent from Azuqueca de Henares every day. Zetes’ brief was to develop a tailor-made solution that met three basic functions: the printing and application of labels showing the price of each DVD on an automated packing line; the application, on these same DVDs, of the pre-printed labels (also on an automated packing line) and finally, the subsequent control of each product to ensure the compliance of the labelling. -
Pioneering Digital Identity in Belgium
Pioneering Digital Identity in Belgium 1 2 3 The relevance Belgium as the Trends and of identity pioneer of eID international standardization A centralised register since decades and electronic IDs An official identity is what ICAO and ISO are developing for the entire population since make a person a citizen and standards for mobile driving 2003 put make the Belgian provides full participation to license and digital travel federal government a pioneer society. credentials. in identity management at a national scale. v1 Identity Why identity matters The lack of an official identity make a person invisible and hinders a person access to education, financial services, welfare, ownership and the right to vote. Sustainable Development Goals Significantly reduce all forms of violence and related death rates everywhere End abuse, exploitation, trafficking and all forms of violence against and torture of children Promote the rule of law at the national and international levels and ensure equal access to justice for all By 2030, significantly reduce illicit financial and arms flows, strengthen the recovery and return of stolen assets and combat all forms of organized crime Substantially reduce corruption and bribery in all their forms Develop effective, accountable and transparent institutions at all levels Ensure responsive, inclusive, participatory and representative decision-making at all levels Broaden and strengthen the participation of developing countries in the institutions of global governance By 2030, provide legal identity for all, -
Edit Master Title Style Welcome to the World Bank & Countries Delegation
27th March 20153 Welcome to the World Bank & Countries Delegation FromClick Zetes : to edit Master title style R. DepoortereClick to edit Master title style J. Mignon J-M Joiret & team Agenda until lunch 1. Welcome - Zetes at a glance 2. The Belgian e-ID & e-passport processes 3. Factory Visit 4. Q & A Cold Buffet lunch around 13h00 2 Our core competence: Linking the physical with the digital world 3 Facts & Figures Countries Served Direct Presence Close to 30 years of growth Direct presence in 20 countries in EMEA + 1100 FTE 4 Zetes Milestones Uganda Biometric Registration ID 5 Solid Financial Results In € ‘000 Operating 2012 2013 2014 situation Sales 214 126 211 472 245 270 Gross margin 93 699 91 446 103 579 6 Goods ID Value chain Traceability ? Right ID? Right carrier? Right Parent-child? Right products? vehicle? Right shelf? Right Right stop? Right info? goods? Right time? Right Complete carrier? order? Traceability solutions improving Meting the needs of Efficiency Consumers Quality Industry SC managers Visibility Society 7 Goods ID Customers References in Manufacturing References in Warehousing 8 Goods ID Customers References in Transport & Logistics References in Retail 9 Our core People ID competences • Experienced System Integrator for turn-key ID solutions • More than 30 active large-scale contracts implemented • More than 75 Mi citizens successfully biometrically registered • No bias towards any vendor or vendor specific technology 10 People ID – Enrolment Application – online or offline Live enrolment – the key to secure document -
Slavery and Human Trafficking Statement 2020
Slavery and Human Trafficking Statement 2020 Modern slavery can occur in various forms including servitude, forced, compulsory labour and human trafficking, all of which include the deprivation of a person’s (an adult or child’s) liberty by another (collectively “modern slavery”). The following sets out the procedures Panasonic has put in place that aim to prevent modern slavery from occurring within our business or supply chain. Panasonic is committed to a work environment that is free from modern slavery, in accordance with the laws and regulations of the respective countries in which we operate. We have a zero-tolerance approach to modern slavery and we are committed to acting ethically and with integrity in all our business dealings and relationships. We are committed to implement and enforce effective systems and controls to ensure modern slavery is not taking place anywhere in our own business or in any of our supply chains. We will not knowingly use modern slavery in any of our products and/or services supplied. Additionally, we use guidelines and Standard Purchase Agreements with suppliers to require that they not utilise slave labour. ZETES is committed to make efforts to confront Modern Slavery at its sites and along its entire supply chain, in accordance with Section 54 of the Modern Slavery Act 2015. In the following statement, ‘we’, ‘us’ or ‘our’ refers to the Panasonic Group. Scope of Reporting - Fiscal 2020 (1st April, 2019 to 31st March, 2020) 1 ZETES published its first Slavery and Human Trafficking Statement in 2018. This third statement demonstrates its concern and continuous intentions to encourage the implementation of Sustainable Development Goals (SDGs). -
Full and Reliable Traceability Across Logistics Processes
CASE STUDY CERP ROUEN Pharmaceutical wholesale-dispatcher, France FULL AND RELIABLE TRACEABILITY ACROSS LOGISTICS PROCESSES OBJECTIVES SOLUTION RESULTS • ZetesMedea Voice • Greater working efficiency • Comply with the new powered by MCL Voice for 1,000 operators in 40 locations requirements for medicine traceability • Multimodal, multi-customer • Less than 0.07% picking errors voice picking • Maintain existing productivity • Full traceability of medicines levels • Motorola WT4090 terminal • Reduced number of stages required • Ensure very short delivery • Motorola RS507 ring scanner for preparation and inventory lead times • Headsets for voice terminals • Permanent reliable inventory maintained WWW.ZETES.COM | ALWAYS A GOOD ID Pharmaceutical distributor CERP Towards 100% traceability Rouen optimises logistics processes In 2008, the company installed two 2D readers to deal with veterinary items marked with the Datamatrix code and to with ZetesMedea optimise the receipt and storage of medicines on a FIFO/FEFO basis. This reorganisation of logistics processes was prompted The wholesaler distributor CERP Rouen (Astera Cooperative by a number of factors: the introduction of Datamatrix codes; Group) has reorganised its order picking and permanent inventory logistics processes to comply with new medicine mandatory medicine traceability standards introduced to the traceability standards, without compromising the productivity pharmaceutical sector in 2011; and an increasing number of required to ensure very short delivery times. Medicine items with compliant markings. traceability is fully guaranteed using the ZetesMedea logistics execution solution with its multimodal capability combining Until then, with the exception of a few automated sites in Belgium voice and product scanning. where voice picking had been introduced for order preparation, inventory and picking processes were paper-based. -
Panasonic Acquires an Initial 50.95 Percent Stake in Zetes, an Industry Leader Specialised in Identification and Mobility Soluti
Regulated Information – Inside Information Press Release issued pursuant to Article 8, §1 of the Belgian Royal Decree of 27 April 2007 on public takeover bids 22 December 2016 Panasonic acquires an initial 50.95 percent stake in Zetes, an industry leader specialised in identification and mobility solutions – This transaction will be followed by a mandatory tender offer by Panasonic for the remaining shares of Zetes at a price of EUR 54.50 per share Panasonic Corporation (Tokyo Stock Exchange: 6752) (“Panasonic”), a global leader in the development of diverse electronics technologies and solutions for customers in the consumer electronics, housing, automotive, enterprise solutions and device industries, headquartered in Osaka, Japan, and Zetes Industries SA (Euronext Brussels: ZTS.BR) (“Zetes”), a European market leader of goods and people identification and mobility solutions headquartered in Brussels, Belgium, today announced that Panasonic has reached agreements to acquire all of the outstanding shares of Zephir Corporation SA, a holding company that owns 23.70% of the issued shares of Zetes, a further 24.67% of the issued shares from Cobepa SA and additional issued shares from certain other individual shareholders, including Zetes’ management, representing a total of 50.95% of the issued shares in Zetes for a total consideration of EUR 149.6 million (the “Acquisition”). The purchase price per share payable by Panasonic for the Zetes shares is EUR 54.50, representing a premium of 19.1% to the 30-day average share price and a premium of 27.7% to the three-month average closing share price of Zetes. The price will be payable by Panasonic in cash and takes into account the amount of the interim dividend of EUR 0.80 paid on 21 December 2016. -
Supply Chain to Value Chain Together Adding Value
21 - 22 MARCH 2018 THE OAKLEY COURT, WINDSOR, UK SUPPLY CHAIN TO VALUE CHAIN TOGETHER ADDING VALUE CO-ORGANISED BY GIRP AND HDA UK SUPPLY CHAIN TO VALUE CHAIN WINDSOR, UK TOGETHER ADDING VALUE 21 – 22 MARCH 2018 CONFERENCE PROGRAMME CONFERENCE OBJECTIVES • Present the latest state-of-the-art technologies in temperature-controlled transportation • Demonstrate how collaboration can move the supply chain towards a true pharmaceutical value chain • Further the dialogue between supply chain actors and GMDP inspectors • Engage participants in further reflections on how to harness the additional benefits from the serialisation project in Europe • Explore new options for value creation within the healthcare ecosystem • Explore the impact of Brexit on the British and European pharmaceutical value chains TOPICS TO BE ADRESSED • Handling temperature sensitive products • Temperature controlled storage, monitoring and transportation • Experiences from GMDP inspections • Medicines batch tracking requirements • Electronic delivery notes • Responsibilities of responsible person • Implementation of the Falsified Medicines Directive 5 KEY TAKE-AWAYS • Deep and concrete insight on how to secure an end-to-end temperature-controlled supply chain • Clear understanding of GMDP inspectors’ expectations • How to further advance with GDP implementation at national level • How to improve business processes with serialisation • How to collaborate with your value chain partners Rue de la Loi 26, Box 14 T +32 (0)2 777 99 77 E [email protected] 1040 Brussels, Belgium F +32 (0)2 770 36 01 W www.girp.eu SUPPLY CHAIN TO VALUE CHAIN WINDSOR, UK TOGETHER ADDING VALUE 21 – 22 MARCH 2018 CONFERENCE DAY 1 – WEDNESDAY 21 MARCH 2018 12:30 Welcome Lunch 14:00 Opening & Welcome Address • Mr René Jenny, President, European Healthcare Distribution Association (GIRP) • Mr Martin Sawer, Executive Director, Healthcare Distribution Association, United Kingdom (HDA UK) 14:15 Session 1: Seamless handling of temperature sensitive products from production to patient Keynote address • Dr. -
The State of Identification Systems in Africa: Country Briefs
THE STATE OF IDENTIFICATION SYSTEMS IN AFRICA Country Briefs THE STATE OF IDENTIFICATION SYSTEMS IN AFRICA Country Briefs © 2017 International Bank for Reconstruction and Development / The World Bank 1818 H Street, NW Washington, DC 20433 Telephone: 202-473-1000 Internet: www.worldbank.org This work is a product of the staff of The World Bank with external contributions. The findings, interpretations, and conclu- sions expressed in this work do not necessarily reflect the views of The World Bank, its Board of Executive Directors, or the governments they represent. The World Bank does not guarantee the accuracy of the data included in this work. The boundaries, colors, denominations, and other information shown on any map in this work do not imply any judgment on the part of The World Bank concerning the legal status of any territory or the endorsement or acceptance of such boundaries. Rights and Permissions The material in this work is subject to copyright. Because The World Bank encourages dissemination of its knowledge, this work may be reproduced, in whole or in part, for noncommercial purposes as long as full attribution to this work is given. Any queries on rights and licenses, including subsidiary rights, should be addressed to World Bank Publications, The World Bank Group, 1818 H Street NW, Washington, DC 20433, USA; fax: 202-522-2625; e-mail: [email protected]. Currency conversions are as of May 2017 (http://www.google.com/intl/en/googlefinance/disclaimer/). Cover photo: Hope, painting by Antonio Nshimiyimana (Rwanda), 2015. Interior photos (left to right): World Bank; World Bank; Open Society © Liu Chan/Redux; World Bank; UNICEF. -
ZETES CASE STUDY |Kellogg Manufacturing
ZETES CASE STUDY |Kellogg Manufacturing Kellogg Manufacturing entrusts its traceability project to Zetes Kellogg is an American multinational and market leader for breakfast foods, cereals and biscuits. Its head office is based in Battle Creek, Michigan, in the United States. Founded in 1906 by Will Keith Kellogg, his initial aim was to improve the health of the patients in the centre in which he was working. The result was so good that it didn’t take long for the orders to come in and then multiply, and today, the company is the world’s leading producer of breakfast cereals. Kellogg has been operating in Spain since 1978, producing a wide range of breakfast cereals and bars. Many of its products are manufactured in the Valls production plant (Tarragona) which has been running since 1980, producing cereals for Spain, Portugal, Italy and France. Project overview It is at the Valls plant that Zetes introduced a “turnkey” solution for the automatic labelling of finished goods pallets.. The aim of this project was to guarantee traceability through the double sided printing of all the pallet labels in line with standard GS1-128 (the former EAN), as required by supermarkets and the European food traceability Standard. A solution to meet the needs of Kellogg Manufacturing The project involved the installation of LabelPack real time label printers and applicators, manufactured by MD, a Zetes brand, to identify the pallets on the front and on the side in line with standard GS1-128. The Zetes Professional Services department developed a software application to meet the needs of Kellogg, which managed the labelling of the manufacturing equipment and included Kellogg’s own Maewin®, software, authorised by Aecoc (Spanish commercial coding association) for standardised label design and printing. -
Mergers & Acquisitions
Mergers & Acquisitions 201 Seventh Edition 8 Editors: Michael E. Hatchard & Scott V. Simpson GLOBAL LEGAL INSIGHTS – MERGERS & ACQUISITIONS 2018, SEVENTH EDITION Editors Michael E. Hatchard (Retired Partner), Skadden, Arps, Slate, Meagher & Flom (UK) LLP Scott V. Simpson, Skadden, Arps, Slate, Meagher & Flom (UK) LLP Production Editor Andrew Schofi eld Senior Editors Suzie Levy Caroline Collingwood Group Consulting Editor Alan Falach Publisher Rory Smith We are extremely grateful for all contributions to this edition. Special thanks are reserved for Michael E. Hatchard & Scott V. Simpson for all of their assistance. Published by Global Legal Group Ltd. 59 Tanner Street, London SE1 3PL, United Kingdom Tel: +44 207 367 0720 / URL: www.glgroup.co.uk Copyright © 2018 Global Legal Group Ltd. All rights reserved No photocopying ISBN 978-1-912509-10-2 ISSN 2048-6839 This publication is for general information purposes only. It does not purport to provide comprehensive full legal or other advice. Global Legal Group Ltd. and the contributors accept no responsibility for losses that may arise from reliance upon information contained in this publication. This publication is intended to give an indication of legal issues upon which you may need advice. Full legal advice should be taken from a qualifi ed professional when dealing with specifi c situations. The information contained herein is accurate as of the date of publication. Printed and bound by CPI Group (UK) Ltd, Croydon, CR0 4YY May 2018 CONTENTS Preface Michael E. Hatchard & Scott V. Simpson Austria Hartwig Kienast, Horst Ebhardt & Jiayan Zhu, Wolf Theiss Rechtsanwälte GmbH & Co KG 1 Belgium Christel Van den Eynden & Wim Dedecker Liedekerke Wolters Waelbroeck Kirkpatrick 7 Bolivia Jorge Luis Inchauste & José Carlos Bernal, Guevara & Gutiérrez S.C.