Design, Comparison and Experimental Evaluation of Non-Overlap Winding Radial Flux Permanent Magnet Hub Drives for Electric Vehicles
Total Page:16
File Type:pdf, Size:1020Kb
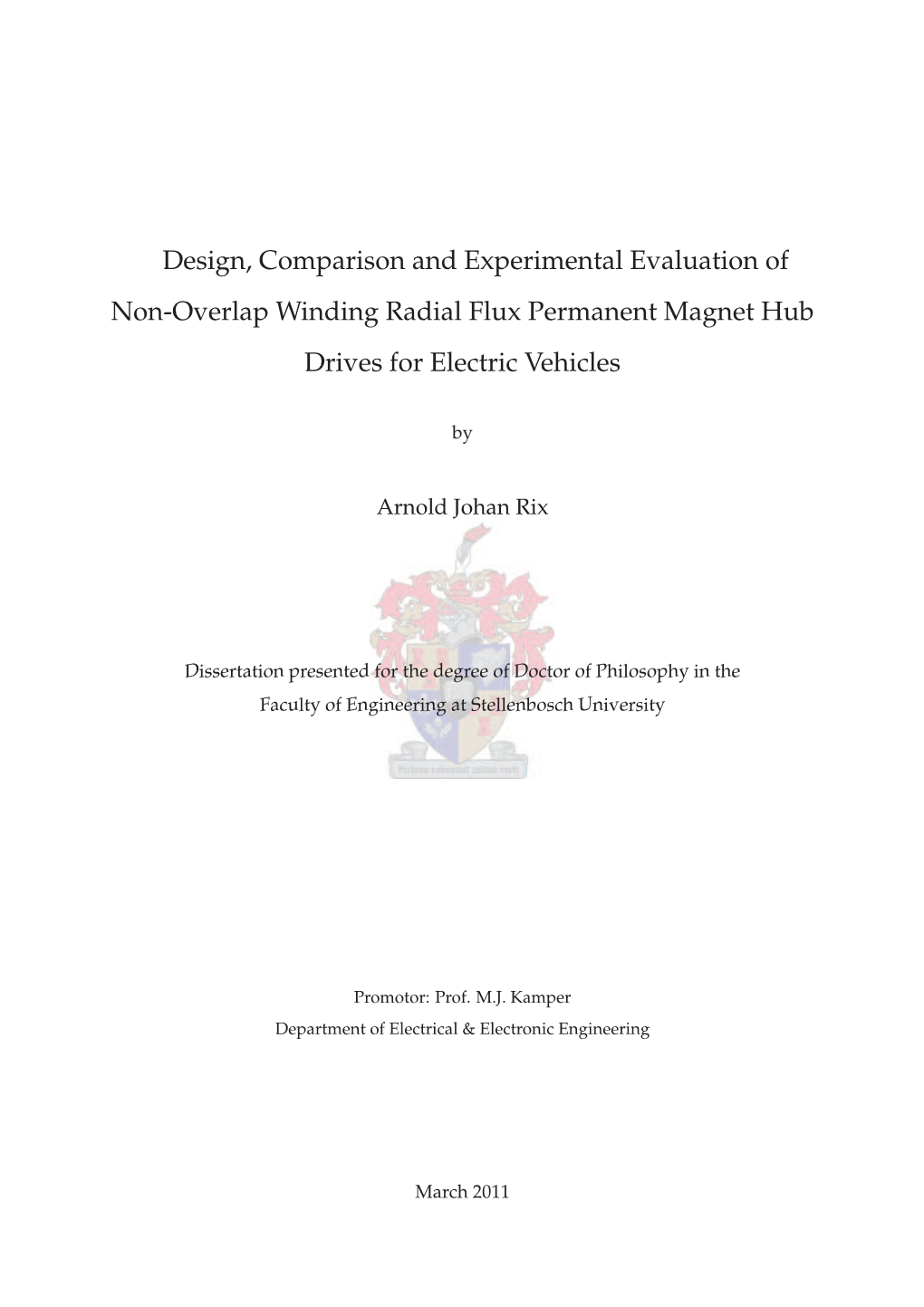
Load more
Recommended publications
-
Design and Fabrication of Self Charging Electric Vehicle M.Sathya Prakash International Journal of Power Control Signal and Computation(IJPCSC) Vol 8
Design And Fabrication Of Self Charging Electric Vehicle M.Sathya Prakash International Journal of Power Control Signal and Computation(IJPCSC) Vol 8. No.1 – Jan-March 2016 Pp. 51-55 ©gopalax Journals, Singapore available at : www.ijcns.com ISSN: 0976-268X DESIGN AND FABRICATION OF SELF CHARGING ELECTRIC VEHICLE M.Sathya Prakash Department of Thermal Engineering Pannai College of Engineering & Technology Sivagangai, India Abstract—Now days the automobile industry batteries, relays, battery chargers and provided to become more competitive the vehicles can get the you. Components including chassis, energy from petrol or diesel engine for its transmissions, wheels and brakes are presented. drive .the recent years e-bike became more Information will be basics for design of the attractive and less maintenance cost. But only drawback of e-bike is requires frequent charging conversion .electrical hazards of batteries, and form EB supply. In this paper is based charging high ampere and high voltage wiring will be arrangement on the e-bike. The motor is use the presented. These e-bikes are differing from type electric energy from battery and battery can of battery used and these e -bikes are designed receive electric energy from dynamo .this energy based on the power of the motor and weight is stored in battery. Market available e-bike motor power rating. E-bikes use 3-4 no’ s of 12V batteries are designed to spent 6-8 hours/charge battery for different power of motors. These by using EB supply. This e-bikes running cost is very low, when compare to other sources of batteries are connected in series, so voltage built energy. -
From the Intelligent Wheel Bearing to the Robot Wheel: Schaeffler
29 Robot Wheel 29 Robot Wheel Robot Wheel 29 From the intelligent wheel bearing to the “robot wheel” Bernd Gombert 29 378 Schaeffl er SYMPOSIUM 2010 Schaeffl er SYMPOSIUM 2010 379 29 Robot Wheel Robot Wheel 29 ered as well. Mechanical steering and braking ele- The increasing ments are being replaced by mechatronic compo- nents thereby leading to higher functi onality with requirements placed increased safety. When referring to the further developments in on motor vehicles safety, the vision of “zero accidents” (autonomous and accident-free driving) has to be menti oned. Why is the trend heading Aft er slip control braking and driving stability sys- towards electromobility? tems, driver assistance systems known as ADAS (Advanced Driver Assistance Systems) are now be- Environmentally-friendly electrical mobility is the ing created as a further requirement for making expected trend and will become a real alternati ve this vision a reality. Figure 2 The fi rst electric vehicle, built in 1835 [1] Figure 4 Lohner-Porsche with four wheel hub motors to the current state of the art. Innovati ve technolo- By-wire technology, amongst others, is one of the in 1900 [1] gies, high oil prices and the increasing ecological nate the transmission and drive shaft since the prerequisites for the implementati on of ADAS. It awareness of many people are reasons, why elec- wheel rotated as the rotor of the direct current In order to compensate for the lack of range, of- monitors the current traffi c situati on and acti vely tromobility is increasingly gaining worldwide ac- motor around the stator, that was fixed to the fered by a vehicle only powered by electricity, supports the driver. -
Active Suspension Control of Electric Vehicle with In-Wheel Motors
University of Wollongong Research Online University of Wollongong Thesis Collection 2017+ University of Wollongong Thesis Collections 2018 Active suspension control of electric vehicle with in-wheel motors Xinxin Shao University of Wollongong Follow this and additional works at: https://ro.uow.edu.au/theses1 University of Wollongong Copyright Warning You may print or download ONE copy of this document for the purpose of your own research or study. The University does not authorise you to copy, communicate or otherwise make available electronically to any other person any copyright material contained on this site. You are reminded of the following: This work is copyright. Apart from any use permitted under the Copyright Act 1968, no part of this work may be reproduced by any process, nor may any other exclusive right be exercised, without the permission of the author. Copyright owners are entitled to take legal action against persons who infringe their copyright. A reproduction of material that is protected by copyright may be a copyright infringement. A court may impose penalties and award damages in relation to offences and infringements relating to copyright material. Higher penalties may apply, and higher damages may be awarded, for offences and infringements involving the conversion of material into digital or electronic form. Unless otherwise indicated, the views expressed in this thesis are those of the author and do not necessarily represent the views of the University of Wollongong. Recommended Citation Shao, Xinxin, Active suspension control of electric vehicle with in-wheel motors, Doctor of Philosophy thesis, School of Electrical, Computer and Telecommunications Engineering, University of Wollongong, 2018. -
Analysis of Wheel Hub Motor Drive Application in Electric Vehicles
100 MATEC Web of Conferences , 01004 (2017)DOI: 10.1051/matecconf/201 710001004 GCMM 2016 Analysis of Wheel Hub Motor Drive Application in Electric Vehicles Yuechao Sun*, Man Li and Cong Liao Mechanical and Electrical Engineering Department, Lingnan Normal University, Zhanjiang 524048 , China Corresponding Email: [email protected] Abstract. Based on the comparative analysis of the performance characteristics of centralized and distributed drive electric vehicles, we found that the wheel hub motor drive mode of the electric vehicles with distributed drive have compact structure, high utilization ratio of interior vehicle space, lower center of vehicle gravity, good driving stability, easy intelligent control and many other advantages, hence in line with the new requirements for the development of drive performance of electric vehicles, and distributed drive will be the ultimate mode of electric vehicles in the future. Keywords Electric Vehicle, Drive Mode, Wheel Hub Motor, Development Analysis. 1 Foreword Compared with conventional vehicles, electric vehicles have the advantages of high efficiency of energy conversion, low noise, zero emission, etc., and the load-carrying property and wide range speed control characteristics of motors can remove the mechanical devices such as clutch and gearbox, simplifying the structure and facilitating maintenance [1, 2]. Driven by the dual pressures of energy and environment nowadays, the world’s major automobile producing countries are developing electric vehicle industry with unprecedented efforts. Electric vehicles are creating a new pattern of the automobile industry, which will sure lead the main direction of the automobile industry development. As the core component of an electric vehicle, the quality of driving motor has a great influence on the power, economical efficiency and safety of the electric vehicle. -
Introduction to Electric Vehicle Transmissions Dr
technical Introduction to Electric Vehicle Transmissions Dr. Hermann J. Stadtfeld Transmissions in Automobiles The vehicle would first jerk and then the that the torque converter output torque is with Internal Combustion Engines engine would die. The torque characteris- amplified enough to accelerate the vehicle Traditional automotive transmissions are tics of a combustion engine and an electric from zero speed to a moving condition. designed to adjust the engine speed to motor (Fig. 1) show the low-torque avail- Shortly after that, when the vehicle is the speed of the driving wheels, required ability of a combustion engine at idle speed. driving between 10 and 20 km/h (6.25 in order to achieve the desired driving Even if a compliant element like a and 12.5 mph), the transmission shifts speed. The engine speed of a modern torque converter between engine and into a higher gear because the engine internal combustion engine has a range wheels is used, it would not be possible rpm would have to double when the for optimal efficiency between 1,000 and to control acceleration, speed and decel- vehicle speed is 30 km/h (18.75 mph) and 2,500 rpm. eration the way it is expected for safe be about 6 times higher (=9,000 rpm) A midsize sedan with an outer tire driving. Besides all of these obstacles, the when the vehicle reaches the desired diameter of 600mm has to rotate with a fuel consumption of a vehicle without a 88 km/h (55 mph). Such a high engine speed of 778 rpm in order to achieve a transmission would be several times that speed would be undesirable in many vehicle speed of 88km/h or 55mph, of a vehicle today that is equipped with a ways. -
Development of Wheel Hub Motor Drive Application in Electric Vehicles
Sabancı University Program for Undergraduate Research (PURE) Summer 2017-2018 DEVELOPMENT OF WHEEL HUB MOTOR DRIVE APPLICATION IN ELECTRIC VEHICLES Melike - Cezayirlioğlu [email protected] Undeclared, Sophomore Murat – Büyük Mechanical Engineering Abstract At most 100-word summary of the problem and the findings. In order to choose the optimum type of electric motor for Formula Student type race car applications, literature review has been conducted. Electric motor types such as AC Induction Motor (ACIM), Brushless DC (BLDC) Motor, Permanent Magnet Synchronous Motor (PMSM) and Stepper Motor & Switched Reluctance (SR) motors are compared. Results have shown that Permanent Magnet Synchronous Motor is the best option with its 95 percent efficiency. Further research has done comparing sub categories of PMSMs which are Interior Permanent Magnet motor (IPM) and surface mounted PM machines (SPM) in which IPM motors are selected as the best candidate for traction applications with their higher capacity of torque production. Finally, SolidWorks design of wheel assembly parts comprising planetary, upright and motor has been done using design parameters and dimensions. Keywords: Hub motor, FSAE, Permanent Magnet Synchronous Motor, Interior Permanent Magnet Synchronous Motor. 1 Introduction Electric motor concept revolutionized the industry by their extensive advantages over the internal combustion engines (IC) by means of low environmental effect and efficiency (Çakır, 2004, p.1). As an alternative solution to non-renewable fossil fuels, electric vehicles gained popularity in the automotive industry (Kucinski, Liang, Davis, &Masucci, 2017, p.10). The electric motor under this project was designed for the Formula SAE competition which is an international university student design competition (Carraro, Degano, Morandin & Bianchi, 2013). -
Faults and Their Influence on the Dynamic Behaviour of Electric Vehicles
KTH Engineering Sciences Controlling over-actuated road vehicles during failure conditions Daniel Wanner Doctoral Thesis Stockholm, Sweden 2015 Typeset in LATEX TRITA-AVE 2015:23 KTH School of Engineering Sciences ISSN 1651-7660 SE-100 44 Stockholm ISBN 978-91-7595-597-1 Sweden Akademisk avhandling som med tillst˚andav Kungliga Tekniska h¨ogskolan framl¨agges till offentlig granskning f¨or avl¨aggande av teknologie doktorsexamen i fordonsteknik fredagen den 5:e juni 2015 klockan 9.00 i Kollegiesalen, Kungliga Tekniska H¨ogskolan, Brinellv¨agen8, Stockholm. c Daniel Wanner, 2015 Tryck: E-print AB Acknowledgements The work presented in this thesis was carried out at KTH Vehicle Dynamics at the Department of Aeronautical and Vehicle Engineering, School of Engineering Sciences, Kungliga Tekniska H¨ogskolan (KTH) in Sweden. Funding was provided by the Swedish Hybrid Vehicle Centre (SHC), and the European Commission and VINNOVA through the research program EVERSAFE (ERA-NET Electromobility+). The financial sup- port is gratefully acknowledged. I would like to express my gratitude to all people involved, especially my academic supervisors Annika Stensson Trigell and Lars Drugge for their constant support and excellent guidance as well as their encouragement and patience provided during the course of this project. I am grateful for all the fruitful discussions and stimulating advice from my industrial advisor Mats Jonasson at Volvo Cars. Further, I would like to thank Oskar Wallmark at KTH Electrical Energy Conversion for the excellent collaboration on all topics related to electrical engineering. I would like to express my gratitude to the SHC steering group committee involved for constructive feedback. -
BLDC Wheel Hub Motor and Motor Controller Performance Test of a Concept Electric Robotic Vehicle in HIL According to Real Driving Characteristics
BLDC wheel hub motor and motor controller performance test of a concept electric robotic vehicle in HIL according to real driving characteristics Mehmed Yuksel¨ 1, Stefan Losch¨ 3, Sven Kroffke1, Michael Rohn1 and Frank Kirchner1;2 1 German Research Center for Artificial Intelligence (DFKI) Robotics Innovation Center (RIC) [email protected], [email protected], [email protected], [email protected] 2 Department of Mathematics and Computer Science, University of Bremen 1 ; 2 Robert-Hooke-Str. 1 - 28359 Bremen, Germany 3 Fraunhofer Institute for Manufacturing Technology and Advanced Materials (IFAM), Wiener Str. 12, 28359 Bremen, Germany [email protected] Abstract Model Region Electric Mobility Bremen/Oldenburg in Bremen. In this paper we are presenting a method, which is devel- Within the Model Region projects we evaluate electric mobility oped as a part of our framework for designing complex through data logging and its analysis [4]. robotic vehicle systems, to test a power train of a robotic concept car according to the real driving characteristic from In our earlier work the communication and control of the telemetry data gathered from a subset of a pilot electric ve- BLDC motorcontroller and the BLDC motor as a subsystem hicle fleet in northern Germany in Hardware-in-the-Loop. of the vehicle control model in Simulink were developed in Our aim is to investigate the driving performance of our Software-in-the-loop (SIL) [5] and tested in our low torque modified BLDC wheel hub motor and its motorcontroller motor test bench (torque controlled up to 120Nm based on under urban area traffic conditions. -
Design of Easy Walker (E-Walker) Er
SSRG International Journal of Mechanical Engineering ( SSRG – IJME ) – Volume 3 Issue 4 – April 2016 Design of Easy Walker (E-Walker) Er. Sailesh K S#, Manu P Nair*, Noel Joseph Karukayil*, Kiran John*, Tom Thomas* #Assistant professor, Mechanical Engineering ,SAINTGITS College of Engineering Kottayam, Kerala State, India *Final year B.Tech, Mechanical Engineering , SAINTGITS College of Engineering Kottayam, Kerala State, India Abstract We have use an automated walker which one place to another easier and thereby make using electric wheels as the base and the them less tired. handicapped peoples are still able to gain their balance as the walker gives them grip to hold on to. II. LITRATURE REVIEW The directions are control by the driver through easy access keys and speed is kept at minimum always. One of the first patents of electrical bikes Rubber wheels are used for the grip and the direction was registered almost 120 years ago by Ogden Bolton changes are pointed out in the front panel. The use of Jr. (Bolton, 1895). The concept Bolton Jr. patented is automated walker reduces the effort required by similar to the E-bikes of today. An E-bike is handicapped people as they can reduces the effect narrowed down to its basics a regular bicycle required by handicapped people as they can relax equipped with an electrical motor, a battery and some their arm muscles and not get fatigue by the machine. electronics and switches that controls power levels. Since it is powered by two energy sources, pedalling Keywords—Electric wheels, access key, automated and electricity, it can be classified 4. -
Electric Wheel Hub Motor with High Recuperative Brake Performance in Automotive Design
World Electric Vehicle Journal Vol. 5 - ISSN 2032-6653 - © 2012 WEVA Page 0510 EVS26 Los Angeles, California, May 6-9, 2012 Electric wheel hub motor with high recuperative brake performance in automotive design Dr.-Ing. Gunter Freitag 1, Dr.-Ing. Marco Schramm 2 1Siemens AG, Otto-Hahn-Ring 6, 81739 München, [email protected] 2 Siemens AG, Günther-Scharowsky-Str. 1, 91050 Erlangen, [email protected] Abstract The entire drive integration in the wheels of electric cars enables completely new vehicle drive train concepts and liberties with the interior design. Central motor, external gearing, differentials, axels and drive-shafts are no longer required, which leads to an enormous gaining of free space for the passenger compartment or other car components. Fully new car concepts and designs will become feasible. As well it can help to reduce weight and costs and increases the efficiency of the whole drive system. In addition wearout and maintenance expenditure are reduced to a minimum. Decentralized electric drives also enable new functionalities mainly concerning vehicle dynamics. This aspect counts especially for wheel hub motors because of the direct access to the wheels without any component in between. Another significant advantage is that direct drives in general are not prone to oscillations during load changes comparing to central drives with transmission gear, coupling and drive-shaft. In this article a review on the development of a wheel hub motor is given that is designed to substitute the friction brake on the rear axle. This demand special thought towards a system that accelerates and decelerates. High torque and power densities are achieved. -
Eguts FS5 DIY E-Vehicle Conversion
Electric, Electronic and Green Urban Transport Systems – eGUTS Code DTP1-454-3.1-eGUTS D4.2.5 DYI Conversion provides step-by-step instructions Responsible Partner Transport Research Centre - CDVB Version 2.0 August 2017 Dissemination level Public Component and Phase D 4. 2. 5 Coordinating partner Transport Research centre (CDBV) Editor(s) Libor Špička, Eva Gelová Contributors Constantin Dan Dumitrescu, Ionela Țișcă, Iosif Hulka, Matei Tămășilă (UPT) Christian Horvath (TOB) Daniel Amariei, Johannes Bachler (CERE) Šime Erlić, Ruđer Bošković, Ivan Šimić (ZADAR) Libor Špička, Eva Gelová, Jaromír Marušinec (CDV) Emese Tass-Aranyos, Emőke Hölbling (DDTG) Alina-Georgiana Birau, Vlad Stanciu, Olga Amariei (ROSENC) Gabriela Jánošíková (VUD) Gregor Srpčič, Sebastijan Seme, Katja Hanžić (UM) Milanko Damjanovic (ULCINJ) Dejan Jegdić (REDASP) Due date of deliverable 01/08/2017 Actual date of deliverable 01/08/2017 Status (F: final, D: draft) F File name eGUTS FS5 DIY e-vehicle conversion August 2017 eGUTS Project Local and Regional eMobility Policy Support Page 2 10 highlights of the study . DIY plans exist in different forms (book, other "paper" formats, electronic, online). Apart from assembly plans of conversion kits manufacturers, DIY plans are not usually comprehensive. There are plenty of universal conversion kits available on the market, especially for bicycles, but also for other two-wheeled vehicles. Their conversion is simple. The conversion of passenger cars and light commercial vehicles (M1 and N1 categories) already requires expert knowledge and practical experience. Conversion kit offer exists for a few selected models (mostly historical). DIY rebuilding of modern cars is not recommended due to their more complex construction and complicated electronic systems. -
Electric Traction for Automobiles – Comparison of Different Wheel-Hub Drives
ELECTRIC TRACTION FOR AUTOMOBILES – COMPARISON OF DIFFERENT WHEEL-HUB DRIVES DIETER GERLING Prof. Dr.-Ing. Dieter Gerling, University of Federal Defense Munich Werner-Heisenberg-Weg 39, 85579 Neubiberg, Germany phone: +49 89 6004 3708, fax: +49 89 6004 3718 [email protected] , http://www.unibw.de/EAA GURAKUQ DAJAKU Dr.-Ing. Gurakuq Dajaku, FEAAM GmbH Werner-Heisenberg-Weg 39, 85579 Neubiberg, Germany phone: +49 89 6004 4120, fax: +49 89 6004 3718 [email protected] , http://www.unibw.de/EAA BENNO LANGE Dr.-Ing. Benno Lange, University of Federal Defense Munich Werner-Heisenberg-Weg 39, 85579 Neubiberg, Germany phone: +49 89 6004 3709, fax: +49 89 6004 3718 [email protected] , http://www.unibw.de/EAA Abstract In this paper, a comparison concerning electric traction drives for passenger cars is given. Electric traction drives presently available on the market are analyzed and future developments are described. Two main classes of such drives are presented: centre drives (like presently known from hybrid cars) and wheel-hub drives (which are still in the research and development phase). The wheel-hub drives are investigated in detail. Two different concepts are regarded: High-speed drive with gear-box and low-speed direct drive. The advantages and disadvantages of both concepts are shown, resulting in the fact that most probably the low-speed direct drive performs better. Keywords: Electric traction drive, wheel-hub drive, low-speed direct drive, permanent magnet motor 1. Introduction The present discussion on the CO2 emissions of passenger cars gives a new stimulus to electric traction drives. At least for city travel the fuel consumption and consequently the CO2 emissions can be reduced by applying a concept containing electric traction.