Comparison of Elastic Moduli of Porous Cordierite by Flexure and Dynamic Test Methods R
Total Page:16
File Type:pdf, Size:1020Kb
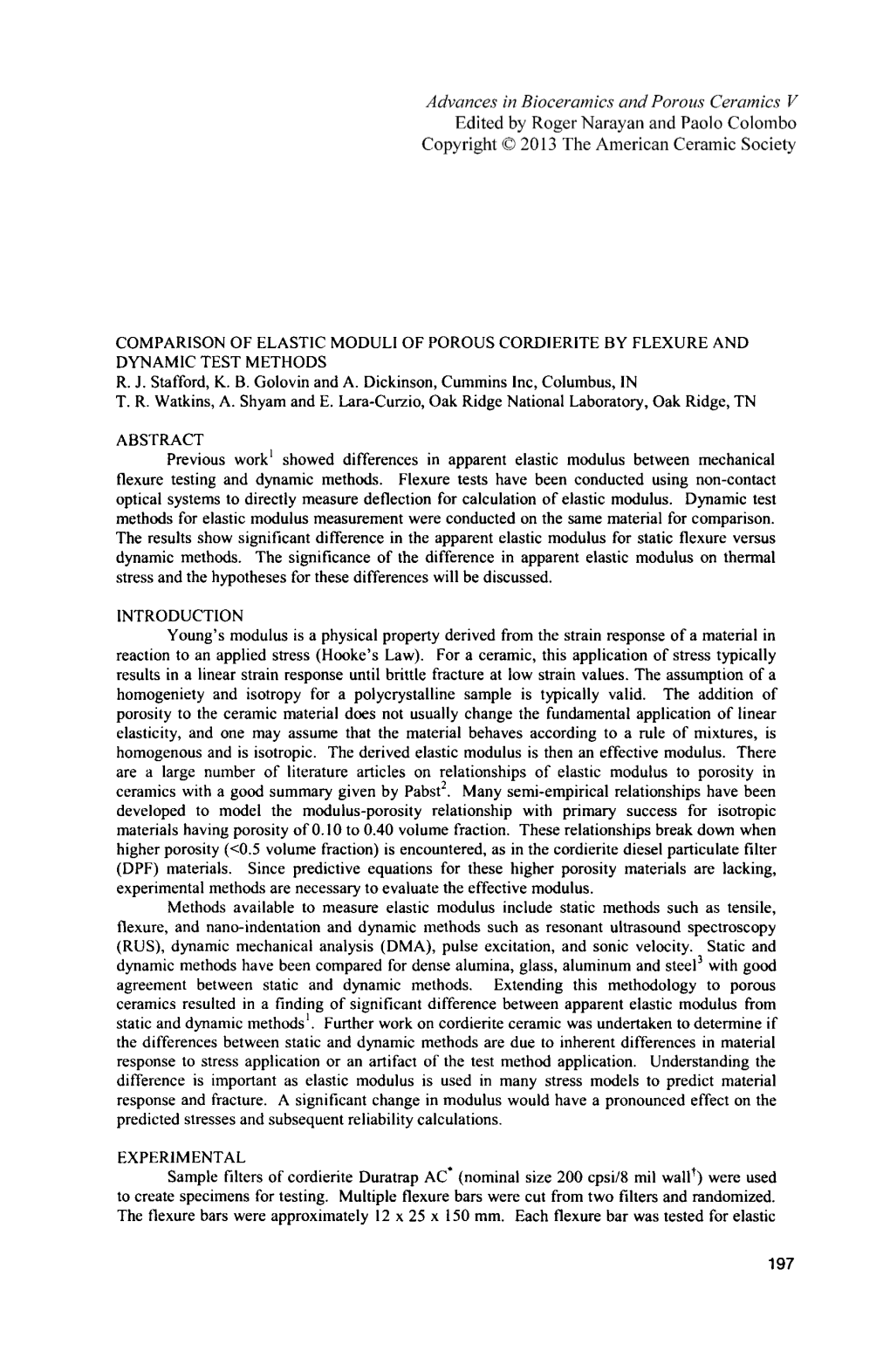
Load more
Recommended publications
-
Elastic Properties of Fe−C and Fe−N Martensites
Elastic properties of Fe−C and Fe−N martensites SOUISSI Maaouia a, b and NUMAKURA Hiroshi a, b * a Department of Materials Science, Osaka Prefecture University, Naka-ku, Sakai 599-8531, Japan b JST-CREST, Gobancho 7, Chiyoda-ku, Tokyo 102-0076, Japan * Corresponding author. E-mail: [email protected] Postal address: Department of Materials Science, Graduate School of Engineering, Osaka Prefecture University, Gakuen-cho 1-1, Naka-ku, Sakai 599-8531, Japan Telephone: +81 72 254 9310 Fax: +81 72 254 9912 1 / 40 SYNOPSIS Single-crystal elastic constants of bcc iron and bct Fe–C and Fe–N alloys (martensites) have been evaluated by ab initio calculations based on the density-functional theory. The energy of a strained crystal has been computed using the supercell method at several values of the strain intensity, and the stiffness coefficient has been determined from the slope of the energy versus square-of-strain relation. Some of the third-order elastic constants have also been evaluated. The absolute magnitudes of the calculated values for bcc iron are in fair agreement with experiment, including the third-order constants, although the computed elastic anisotropy is much weaker than measured. The tetragonally distorted dilute Fe–C and Fe–N alloys exhibit lower stiffness than bcc iron, particularly in the tensor component C33, while the elastic anisotropy is virtually the same. Average values of elastic moduli for polycrystalline aggregates are also computed. Young’s modulus and the rigidity modulus, as well as the bulk modulus, are decreased by about 10 % by the addition of C or N to 3.7 atomic per cent, which agrees with the experimental data for Fe–C martensite. -
Chapter 7 – Geomechanics
Chapter 7 GEOMECHANICS GEOTECHNICAL DESIGN MANUAL January 2019 Geotechnical Design Manual GEOMECHANICS Table of Contents Section Page 7.1 Introduction ....................................................................................................... 7-1 7.2 Geotechnical Design Approach......................................................................... 7-1 7.3 Geotechnical Engineering Quality Control ........................................................ 7-2 7.4 Development Of Subsurface Profiles ................................................................ 7-2 7.5 Site Variability ................................................................................................... 7-2 7.6 Preliminary Geotechnical Subsurface Exploration............................................. 7-3 7.7 Final Geotechnical Subsurface Exploration ...................................................... 7-4 7.8 Field Data Corrections and Normalization ......................................................... 7-4 7.8.1 SPT Corrections .................................................................................... 7-4 7.8.2 CPTu Corrections .................................................................................. 7-7 7.8.3 Correlations for Relative Density From SPT and CPTu ....................... 7-10 7.8.4 Dilatometer Correlation Parameters .................................................... 7-11 7.9 Soil Loading Conditions And Soil Shear Strength Selection ............................ 7-12 7.9.1 Soil Loading ....................................................................................... -
Chapter 14 Solids and Fluids Matter Is Usually Classified Into One of Four States Or Phases: Solid, Liquid, Gas, Or Plasma
Chapter 14 Solids and Fluids Matter is usually classified into one of four states or phases: solid, liquid, gas, or plasma. Shape: A solid has a fixed shape, whereas fluids (liquid and gas) have no fixed shape. Compressibility: The atoms in a solid or a liquid are quite closely packed, which makes them almost incompressible. On the other hand, atoms or molecules in gas are far apart, thus gases are compressible in general. The distinction between these states is not always clear-cut. Such complicated behaviors called phase transition will be discussed later on. 1 14.1 Density At some time in the third century B.C., Archimedes was asked to find a way of determining whether or not the gold had been mixed with silver, which led him to discover a useful concept, density. m ρ = V The specific gravity of a substance is the ratio of its density to that of water at 4oC, which is 1000 kg/m3=1 g/cm3. Specific gravity is a dimensionless quantity. 2 14.2 Elastic Moduli A force applied to an object can change its shape. The response of a material to a given type of deforming force is characterized by an elastic modulus, Stress Elastic modulus = Strain Stress: force per unit area in general Strain: fractional change in dimension or volume. Three elastic moduli will be discussed: Young’s modulus for solids, the shear modulus for solids, and the bulk modulus for solids and fluids. 3 Young’s Modulus Young’s modulus is a measure of the resistance of a solid to a change in its length when a force is applied perpendicular to a face. -
Evaluating High Temperature Elastic Modulus of Ceramic Coatings by Relative Method Guanglin NIE, Yiwang BAO*, Detian WAN, Yuan TIAN
Journal of Advanced Ceramics 2017, 6(4): 288–303 ISSN 2226-4108 https://doi.org/10.1007/s40145-017-0241-5 CN 10-1154/TQ Research Article Evaluating high temperature elastic modulus of ceramic coatings by relative method Guanglin NIE, Yiwang BAO*, Detian WAN, Yuan TIAN State Key Laboratory of Green Building Materials, China Building Materials Academy, Beijing 100024, China Received: June 16, 2017; Revised: August 07, 2017; Accepted: August 09, 2017 © The Author(s) 2017. This article is published with open access at Springerlink.com Abstract: The accurate evaluation of the elastic modulus of ceramic coatings at high temperature (HT) is of high significance for industrial application, yet it is not easy to get the practical modulus at HT due to the difficulty of the deformation measurement and coating separation from the composite samples. This work presented a simple approach in which relative method was used twice to solve this problem indirectly. Given a single-face or double-face coated beam sample, the relative method was firstly used to determine the real mid-span deflection of the three-point bending piece at HT, and secondly to derive the analytical relation among the HT moduli of the coating, the coated and uncoated samples. Thus the HT modulus of the coatings on beam samples is determined uniquely via the measured HT moduli of the samples with and without coatings. For a ring sample (from tube with outer-side, inner-side, and double-side coating), the relative method was used firstly to determine the real compression deformation of a split ring sample at HT, secondly to derive the relationship among the slope of load-deformation curve of the coated ring, the HT modulus of the coating and substrate. -
Glossary of Materials Engineering Terminology
Glossary of Materials Engineering Terminology Adapted from: Callister, W. D.; Rethwisch, D. G. Materials Science and Engineering: An Introduction, 8th ed.; John Wiley & Sons, Inc.: Hoboken, NJ, 2010. McCrum, N. G.; Buckley, C. P.; Bucknall, C. B. Principles of Polymer Engineering, 2nd ed.; Oxford University Press: New York, NY, 1997. Brittle fracture: fracture that occurs by rapid crack formation and propagation through the material, without any appreciable deformation prior to failure. Crazing: a common response of plastics to an applied load, typically involving the formation of an opaque banded region within transparent plastic; at the microscale, the craze region is a collection of nanoscale, stress-induced voids and load-bearing fibrils within the material’s structure; craze regions commonly occur at or near a propagating crack in the material. Ductile fracture: a mode of material failure that is accompanied by extensive permanent deformation of the material. Ductility: a measure of a material’s ability to undergo appreciable permanent deformation before fracture; ductile materials (including many metals and plastics) typically display a greater amount of strain or total elongation before fracture compared to non-ductile materials (such as most ceramics). Elastic modulus: a measure of a material’s stiffness; quantified as a ratio of stress to strain prior to the yield point and reported in units of Pascals (Pa); for a material deformed in tension, this is referred to as a Young’s modulus. Engineering strain: the change in gauge length of a specimen in the direction of the applied load divided by its original gauge length; strain is typically unit-less and frequently reported as a percentage. -
Rheology – Theory and Application to Biomaterials
Chapter 17 Rheology – Theory and Application to Biomaterials Hiroshi Murata Additional information is available at the end of the chapter http://dx.doi.org/10.5772/48393 1. Introduction Rheology is science which treats the deformation and flow of materials. The science of rheology is applied to the physics, chemistry, engineering, medicine, dentistry, pharmacy, biology and so on. Classical theory of elasticity treats the elastic solid which is accordant to Hooke’s law [1]. The stress is directly proportional to strain in deformations and is not dependent of the rate of strain. On the other hand, that of hydrodynamics treats the viscous liquid which is accordant to Newton’s law [1]. The stress is directly proportional to rate of strain and is not dependent of the strain. However, most of materials have both of elasticity and viscosity, that is, viscoelastic properties. Mainly viscoelastic properties of the polymers are analyzed in rheology. Rheology would have two purposes scientifically. One is to determine relationship among deformation, stress and time, and the other is to determine structure of molecule and relationship between viscoelastic properties and structure of the materials. 2. Theory of rheology in polymeric materials A strong dependence on time and temperature of the properties of polymers exists compared with those of other materials such as metals and ceramics. This strong dependence is due to the viscoelastic nature of polymers. Generally, polymers behave in a more elastic fashion in response to a rapidly applied force and in a more viscous fashion in response to a slowly applied force. Viscoelasticity means behavior similar to both purely elastic solids in which the deformation is proportional to the applied force and to viscous liquids in which the rate of deformation is proportional to the applied force. -
On the Relationship Between Indenation Hardness and Modulus, and the Damage Resistance of Biological Materials
bioRxiv preprint doi: https://doi.org/10.1101/107284; this version posted February 9, 2017. The copyright holder for this preprint (which was not certified by peer review) is the author/funder, who has granted bioRxiv a license to display the preprint in perpetuity. It is made available under aCC-BY 4.0 International license. On the relationship between indenation hardness and modulus, and the damage resistance of biological materials. David Labontea,∗, Anne-Kristin Lenzb, Michelle L. Oyena aThe NanoScience Centre, Department of Engineering, Cambridge, UK bUniversity of Applied Sciences, Bremen, Germany Abstract The remarkable mechanical performance of biological materials is based on intricate structure-function relation- ships. Nanoindentation has become the primary tool for characterising biological materials, as it allows to relate structural changes to variations in mechanical properties on small scales. However, the respective theoretical back- ground and associated interpretation of the parameters measured via indentation derives largely from research on ‘traditional’ engineering materials such as metals or ceramics. Here, we discuss the functional relevance of inden- tation hardness in biological materials by presenting a meta-analysis of its relationship with indentation modulus. Across seven orders of magnitude, indentation hardness was directly proportional to indentation modulus, illus- trating that hardness is not an independent material property. Using a lumped parameter model to deconvolute indentation hardness into components arising from reversible and irreversible deformation, we establish crite- ria which allow to interpret differences in indentation hardness across or within biological materials. The ratio between hardness and modulus arises as a key parameter, which is a proxy for the ratio between irreversible and reversible deformation during indentation, and the material’s yield strength. -
The Mechanical Properties and Elastic Anisotropies of Cubic Ni3al from First Principles Calculations
crystals Article The Mechanical Properties and Elastic Anisotropies of Cubic Ni3Al from First Principles Calculations Xinghe Luan 1,2, Hongbo Qin 1,2,* ID , Fengmei Liu 1,*, Zongbei Dai 1, Yaoyong Yi 1 and Qi Li 1 1 Guangdong Provincial Key Laboratory of Advanced Welding Technology, Guangdong Welding Institute (China-Ukraine E.O. Paton Institute of Welding), Guangzhou 541630, China; [email protected] (X.L.); [email protected] (Z.D.); [email protected] (Y.Y.); [email protected] (Q.L.) 2 Key Laboratory of Guangxi Manufacturing System and Advanced Manufacturing Technology, Guilin University of Electronic Technology, Guilin 541004, China * Correspondence: [email protected] (H.Q.); [email protected] (F.L.) Received: 21 June 2018; Accepted: 22 July 2018; Published: 25 July 2018 Abstract: Ni3Al-based superalloys have excellent mechanical properties which have been widely used in civilian and military fields. In this study, the mechanical properties of the face-centred cubic structure Ni3Al were investigated by a first principles study based on density functional theory (DFT), and the generalized gradient approximation (GGA) was used as the exchange-correlation function. The bulk modulus, Young’s modulus, shear modulus and Poisson’s ratio of Ni3Al polycrystal were calculated by Voigt-Reuss approximation method, which are in good agreement with the existing experimental values. Moreover, directional dependences of bulk modulus, Young’s modulus, shear modulus and Poisson’s ratio of Ni3Al single crystal were explored. In addition, the thermodynamic properties (e.g., Debye temperature) of Ni3Al were investigated based on the calculated elastic constants, indicating an improved accuracy in this study, verified with a small deviation from the previous experimental value. -
Elastic Modulus Basics and Significance
T R Anantharaman –Education and Research Foundation www.tra-erf.org Elastic modulus Basics and significance P Rama Rao and V Chandrasekaran ARCI, Hyderabad We claim no originality for the material presented. We have compiled such technical information as we considered useful in our effort to communicate to you the basics, significance and applications of elasticity. Recognizing the importance of quantitative measurement in order to have a feel for the stiffness of a given material, we will demonstrate one known method of measurement of Young’s modulus of steel. I was like a boy playing on the seashore, and diverting myself now and then finding a smoother pebble or a prettier shell than ordinary, whilst the great ocean of truth lay all undiscovered before me. Sir Isaac Newton, Letter to Robert Hooke, February 5, 1675 Professor TR Anantharaman (1925 – 2009) was an exceptional teacher. He was the research guide of one of the speakers (P Rama Rao). He built up the country’s leading research school in Materials science and Technology at Banaras Hindu University during 1962 – 1982 with absolutely meager funds. This lecture draws inspiration from him. Outline Definitions and stress-strain curve Atomic basis of elasticity Stiffness and Young’s modulus of elasticity Magnitude of elastic modulus in different materials Extremities in elasticity observed in new materials: (A) graphene, (B) gum metal Computational approach to elasticity 4 Definitions and stress – strain curve Elasticity The atoms of a solid are distributed on a repetitive three dimensional lattice. The springs represent inter-atomic forces. The lattice is remarkably rigid, interatomic springs are extremely stiff. -
Experimental Study on the Physical Properties of Iron Ore Granules Made from Australian Iron Ores
ISIJ International, AdvanceISIJ PublicationInternational, by AdvanceJ-STAGE, Publication DOI: 10.2355/isijinternational.ISIJINT-2018-508 by J-STAGE ISIJ International, J-Stage AdvancedISIJ International,Publication,ISIJ International, DOI: Advance http://dx.doi.org/10.2355/isijinternational.ISIJINT-2015-@@@ Vol. Publication 59 (2019),ISIJ No.by International, J-Stage2 Vol. 59 (2019), No. 2, pp. 1–10 Experimental Study on the Physical Properties of Iron Ore Granules Made from Australian Iron Ores Chengzhi LI,1) Roberto MORENO-ATANASIO,2) Damien O’DEA3) and Tom HONEYANDS1)* 1) Centre for Ironmaking Materials Research, School of Engineering, The University of Newcastle, Callaghan, NSW, 2308 Australia. 2) Chemical Engineering Department, School of Engineering, The University of Newcastle, Callaghan, NSW, 2308 Australia. 3) BHP, 480 Queen St, Brisbane, QLD, 4000 Australia. (Received on July 17, 2018; accepted on October 15, 2018; J-STAGE Advance published date: December 5, 2018) A fundamental experimental study was conducted to measure the physical properties of iron ore gran- ules made from three types of Australian iron ores. In this study, some key physical property parameters, including apparent density, Young’s modulus and the coefficients of static and rolling frictions, of the iron ore granules with varying moisture content were investigated. The effect of granule size on the considered property parameters was also studied for the iron ore granules at the optimal moisture content which was determined by permeability pot packing test. The measurement results showed that both apparent density and Young’s modulus of iron ore granules generally decreased with moisture content due to the growth of adhering layer around the nuclei particles. -
Rock Physics Reservoir Characterization
JD 2008 2. Definitions and Methods 2.1 ROCK PHYSICS DEFINITIONS Volumetrics: Density, Porosity, Saturation 3D volume of sandstone (left) and a sandstone thin section (right). The pore space is blue due to epoxy that impregnated the samples. Equations for density, porosity, and saturation Bulk Density ρBulk = MTotal /VTotal Total Porosity φTotal = VPore /VTotal ≡ φ M is mass Saturation SFluid = VFluid /VPore V is volume SWater + SOil + SGas =1 Bulk Density ρBulk = (1− φ)ρSolid + φρFluid = (1− φ)ρSolid + φ(SWater ρWater + SOil ρOil + SGasρGas ) Porosity strongly depends on the scale of measurement because rock is € heterogeneous at all scales. 1 Porosity .5 0 Radius 2.2 ROCK PHYSICS DEFINITIONS Velocity 2.3 ROCK PHYSICS BASICS Normal Reflection 1200 (ms) 1300 Time A reflection seismogram is a superposition of 1400 Travel signals reflected from interfaces between earth 1500 layers of different elastic properties. 1600 It is useful, therefore, to examine reflection at a single interface between two elastic half-spaces. 1700 1800 1900 2000 Two important elastic parameters that affect reflection are derived from velocity and density. They are the acoustic (or P-) impedance Ip and Poisson’s ratio ν 2 1 (Vp / Vs ) − 2 I p = ρV p ν = 2 (V / V )2 − 1 p s Normal Incidence. The reflection amplitude of a normal-incidence P-wave at the interface between two infinite half-spaces depends on the difference between the impedances of the half-spaces. The same law applies to S-wave reflection. Normal Reflection R I p2 − Ip1 dIp 1 R(0) = = = d ln I p I p2 + I p1 2I p 2 T Zoeppritz (1919) Normal reflection forms a full differential. -
PDF (Chapter 6. Elasticity and Solid-State
Theory of the Earth Don L. Anderson Chapter 6. Elasticity and Solid-state Geophysics Boston: Blackwell Scientific Publications, c1989 Copyright transferred to the author September 2, 1998. You are granted permission for individual, educational, research and noncommercial reproduction, distribution, display and performance of this work in any format. Recommended citation: Anderson, Don L. Theory of the Earth. Boston: Blackwell Scientific Publications, 1989. http://resolver.caltech.edu/CaltechBOOK:1989.001 A scanned image of the entire book may be found at the following persistent URL: http://resolver.caltech.edu/CaltechBook:1989.001 Abstract: The seismic properties of a material depend on composition, crystal structure, temperature, pressure and in some cases defect concentrations. Most of the Earth is made up of crystals. The elastic properties of crystals depend on orientation and frequency. Thus, the interpretation of seismic data, or the extrapolation of laboratory data, requires knowledge of crystal or mineral physics, elasticity and thermodynamics. The physics of fluids is involved in the study of magmas and the outer core. In the previous chapter we concentrated on density and the bulk modulus. In the present chapter we delve into the shear modulus and the seismic velocities. The following chapter deals with transport and nonelastic properties. Later chapters on seismic wave attenuation, anisotropy and mantle mineralogy build on this foundation. Elasticity and Solid-state Geophysics Mark well the various kinds of minerals, note their properties and their mode of origin. -PETRUS SEVERINUS (1571) he seismic properties of a material depend on compo- The interrelations between the elastic constants and wave T sition, crystal structure, temperature, pressure and in velocities are given in Table 6-1.