Fundamentals of Rheology
Total Page:16
File Type:pdf, Size:1020Kb
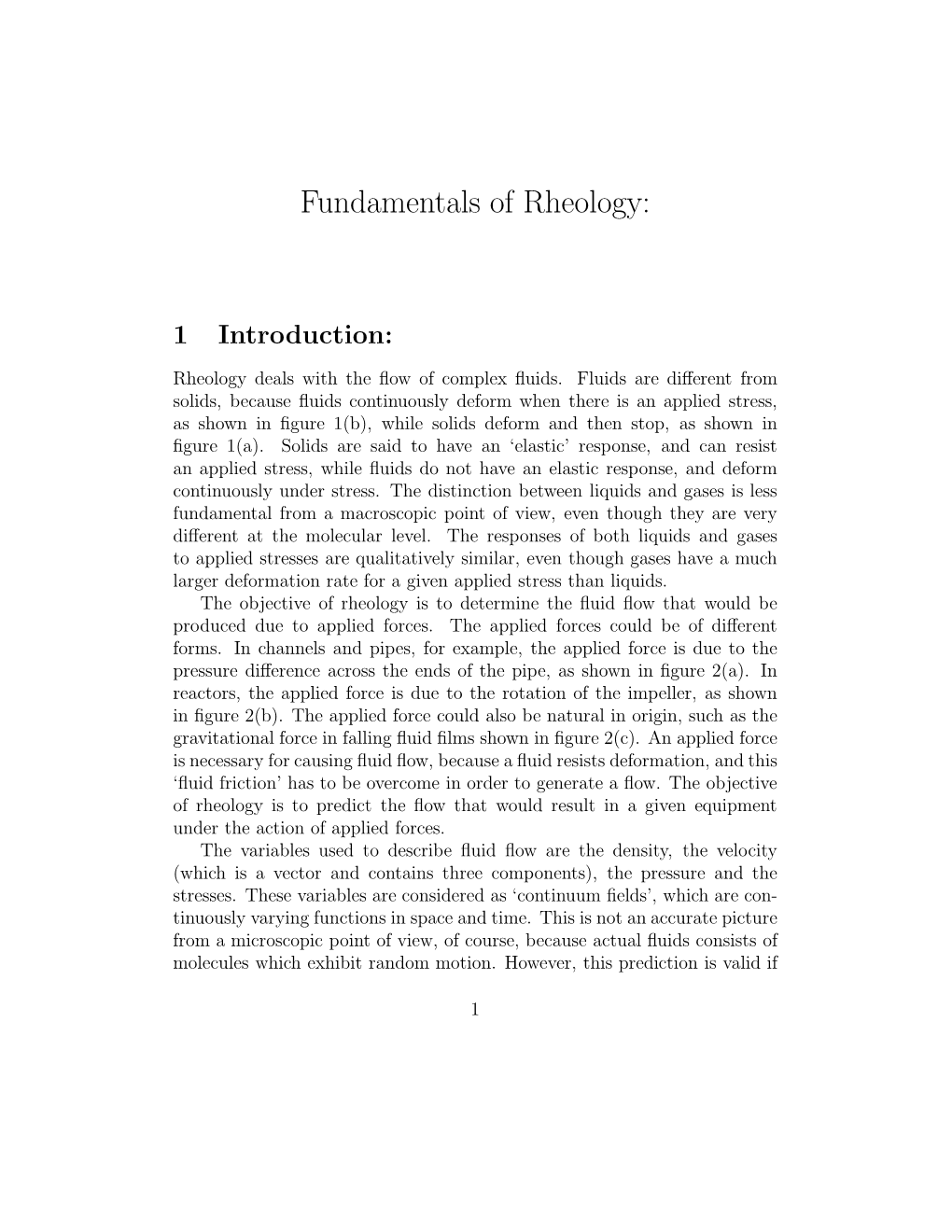
Load more
Recommended publications
-
Equation of State for the Lennard-Jones Fluid
Equation of State for the Lennard-Jones Fluid Monika Thol1*, Gabor Rutkai2, Andreas Köster2, Rolf Lustig3, Roland Span1, Jadran Vrabec2 1Lehrstuhl für Thermodynamik, Ruhr-Universität Bochum, Universitätsstraße 150, 44801 Bochum, Germany 2Lehrstuhl für Thermodynamik und Energietechnik, Universität Paderborn, Warburger Straße 100, 33098 Paderborn, Germany 3Department of Chemical and Biomedical Engineering, Cleveland State University, Cleveland, Ohio 44115, USA Abstract An empirical equation of state correlation is proposed for the Lennard-Jones model fluid. The equation in terms of the Helmholtz energy is based on a large molecular simulation data set and thermal virial coefficients. The underlying data set consists of directly simulated residual Helmholtz energy derivatives with respect to temperature and density in the canonical ensemble. Using these data introduces a new methodology for developing equations of state from molecular simulation data. The correlation is valid for temperatures 0.5 < T/Tc < 7 and pressures up to p/pc = 500. Extensive comparisons to simulation data from the literature are made. The accuracy and extrapolation behavior is better than for existing equations of state. Key words: equation of state, Helmholtz energy, Lennard-Jones model fluid, molecular simulation, thermodynamic properties _____________ *E-mail: [email protected] Content Content ....................................................................................................................................... 2 List of Tables ............................................................................................................................. -
Modeling Conservation of Mass
Modeling Conservation of Mass How is mass conserved (protected from loss)? Imagine an evening campfire. As the wood burns, you notice that the logs have become a small pile of ashes. What happened? Was the wood destroyed by the fire? A scientific principle called the law of conservation of mass states that matter is neither created nor destroyed. So, what happened to the wood? Think back. Did you observe smoke rising from the fire? When wood burns, atoms in the wood combine with oxygen atoms in the air in a chemical reaction called combustion. The products of this burning reaction are ashes as well as the carbon dioxide and water vapor in smoke. The gases escape into the air. We also know from the law of conservation of mass that the mass of the reactants must equal the mass of all the products. How does that work with the campfire? mass – a measure of how much matter is present in a substance law of conservation of mass – states that the mass of all reactants must equal the mass of all products and that matter is neither created nor destroyed If you could measure the mass of the wood and oxygen before you started the fire and then measure the mass of the smoke and ashes after it burned, what would you find? The total mass of matter after the fire would be the same as the total mass of matter before the fire. Therefore, matter was neither created nor destroyed in the campfire; it just changed form. The same atoms that made up the materials before the reaction were simply rearranged to form the materials left after the reaction. -
Derivation of Fluid Flow Equations
TPG4150 Reservoir Recovery Techniques 2017 1 Fluid Flow Equations DERIVATION OF FLUID FLOW EQUATIONS Review of basic steps Generally speaking, flow equations for flow in porous materials are based on a set of mass, momentum and energy conservation equations, and constitutive equations for the fluids and the porous material involved. For simplicity, we will in the following assume isothermal conditions, so that we not have to involve an energy conservation equation. However, in cases of changing reservoir temperature, such as in the case of cold water injection into a warmer reservoir, this may be of importance. Below, equations are initially described for single phase flow in linear, one- dimensional, horizontal systems, but are later on extended to multi-phase flow in two and three dimensions, and to other coordinate systems. Conservation of mass Consider the following one dimensional rod of porous material: Mass conservation may be formulated across a control element of the slab, with one fluid of density ρ is flowing through it at a velocity u: u ρ Δx The mass balance for the control element is then written as: ⎧Mass into the⎫ ⎧Mass out of the ⎫ ⎧ Rate of change of mass⎫ ⎨ ⎬ − ⎨ ⎬ = ⎨ ⎬ , ⎩element at x ⎭ ⎩element at x + Δx⎭ ⎩ inside the element ⎭ or ∂ {uρA} − {uρA} = {φAΔxρ}. x x+ Δx ∂t Dividing by Δx, and taking the limit as Δx approaches zero, we get the conservation of mass, or continuity equation: ∂ ∂ − (Aρu) = (Aφρ). ∂x ∂t For constant cross sectional area, the continuity equation simplifies to: ∂ ∂ − (ρu) = (φρ) . ∂x ∂t Next, we need to replace the velocity term by an equation relating it to pressure gradient and fluid and rock properties, and the density and porosity terms by appropriate pressure dependent functions. -
On Nonlinear Strain Theory for a Viscoelastic Material Model and Its Implications for Calving of Ice Shelves
Journal of Glaciology (2019), 65(250) 212–224 doi: 10.1017/jog.2018.107 © The Author(s) 2019. This is an Open Access article, distributed under the terms of the Creative Commons Attribution-NonCommercial-NoDerivatives licence (http://creativecommons.org/licenses/by-nc-nd/4.0/), which permits non-commercial re-use, distribution, and reproduction in any medium, provided the original work is unaltered and is properly cited. The written permission of Cambridge University Press must be obtained for commercial re- use or in order to create a derivative work. On nonlinear strain theory for a viscoelastic material model and its implications for calving of ice shelves JULIA CHRISTMANN,1,2 RALF MÜLLER,2 ANGELIKA HUMBERT1,3 1Division of Geosciences/Glaciology, Alfred Wegener Institute Helmholtz Centre for Polar and Marine Research, Bremerhaven, Germany 2Institute of Applied Mechanics, University of Kaiserslautern, Kaiserslautern, Germany 3Division of Geosciences, University of Bremen, Bremen, Germany Correspondence: Julia Christmann <[email protected]> ABSTRACT. In the current ice-sheet models calving of ice shelves is based on phenomenological approaches. To obtain physics-based calving criteria, a viscoelastic Maxwell model is required account- ing for short-term elastic and long-term viscous deformation. On timescales of months to years between calving events, as well as on long timescales with several subsequent iceberg break-offs, deformations are no longer small and linearized strain measures cannot be used. We present a finite deformation framework of viscoelasticity and extend this model by a nonlinear Glen-type viscosity. A finite element implementation is used to compute stress and strain states in the vicinity of the ice-shelf calving front. -
Analysis of Deformation
Chapter 7: Constitutive Equations Definition: In the previous chapters we’ve learned about the definition and meaning of the concepts of stress and strain. One is an objective measure of load and the other is an objective measure of deformation. In fluids, one talks about the rate-of-deformation as opposed to simply strain (i.e. deformation alone or by itself). We all know though that deformation is caused by loads (i.e. there must be a relationship between stress and strain). A relationship between stress and strain (or rate-of-deformation tensor) is simply called a “constitutive equation”. Below we will describe how such equations are formulated. Constitutive equations between stress and strain are normally written based on phenomenological (i.e. experimental) observations and some assumption(s) on the physical behavior or response of a material to loading. Such equations can and should always be tested against experimental observations. Although there is almost an infinite amount of different materials, leading one to conclude that there is an equivalently infinite amount of constitutive equations or relations that describe such materials behavior, it turns out that there are really three major equations that cover the behavior of a wide range of materials of applied interest. One equation describes stress and small strain in solids and called “Hooke’s law”. The other two equations describe the behavior of fluidic materials. Hookean Elastic Solid: We will start explaining these equations by considering Hooke’s law first. Hooke’s law simply states that the stress tensor is assumed to be linearly related to the strain tensor. -
1 Fluid Flow Outline Fundamentals of Rheology
Fluid Flow Outline • Fundamentals and applications of rheology • Shear stress and shear rate • Viscosity and types of viscometers • Rheological classification of fluids • Apparent viscosity • Effect of temperature on viscosity • Reynolds number and types of flow • Flow in a pipe • Volumetric and mass flow rate • Friction factor (in straight pipe), friction coefficient (for fittings, expansion, contraction), pressure drop, energy loss • Pumping requirements (overcoming friction, potential energy, kinetic energy, pressure energy differences) 2 Fundamentals of Rheology • Rheology is the science of deformation and flow – The forces involved could be tensile, compressive, shear or bulk (uniform external pressure) • Food rheology is the material science of food – This can involve fluid or semi-solid foods • A rheometer is used to determine rheological properties (how a material flows under different conditions) – Viscometers are a sub-set of rheometers 3 1 Applications of Rheology • Process engineering calculations – Pumping requirements, extrusion, mixing, heat transfer, homogenization, spray coating • Determination of ingredient functionality – Consistency, stickiness etc. • Quality control of ingredients or final product – By measurement of viscosity, compressive strength etc. • Determination of shelf life – By determining changes in texture • Correlations to sensory tests – Mouthfeel 4 Stress and Strain • Stress: Force per unit area (Units: N/m2 or Pa) • Strain: (Change in dimension)/(Original dimension) (Units: None) • Strain rate: Rate -
Law of Conversation of Energy
Law of Conservation of Mass: "In any kind of physical or chemical process, mass is neither created nor destroyed - the mass before the process equals the mass after the process." - the total mass of the system does not change, the total mass of the products of a chemical reaction is always the same as the total mass of the original materials. "Physics for scientists and engineers," 4th edition, Vol.1, Raymond A. Serway, Saunders College Publishing, 1996. Ex. 1) When wood burns, mass seems to disappear because some of the products of reaction are gases; if the mass of the original wood is added to the mass of the oxygen that combined with it and if the mass of the resulting ash is added to the mass o the gaseous products, the two sums will turn out exactly equal. 2) Iron increases in weight on rusting because it combines with gases from the air, and the increase in weight is exactly equal to the weight of gas consumed. Out of thousands of reactions that have been tested with accurate chemical balances, no deviation from the law has ever been found. Law of Conversation of Energy: The total energy of a closed system is constant. Matter is neither created nor destroyed – total mass of reactants equals total mass of products You can calculate the change of temp by simply understanding that energy and the mass is conserved - it means that we added the two heat quantities together we can calculate the change of temperature by using the law or measure change of temp and show the conservation of energy E1 + E2 = E3 -> E(universe) = E(System) + E(Surroundings) M1 + M2 = M3 Is T1 + T2 = unknown (No, no law of conservation of temperature, so we have to use the concept of conservation of energy) Total amount of thermal energy in beaker of water in absolute terms as opposed to differential terms (reference point is 0 degrees Kelvin) Knowns: M1, M2, T1, T2 (Kelvin) When add the two together, want to know what T3 and M3 are going to be. -
Computational Rheology (4K430)
Computational Rheology (4K430) dr.ir. M.A. Hulsen [email protected] Website: http://www.mate.tue.nl/~hulsen under link ‘Computational Rheology’. – Section Polymer Technology (PT) / Materials Technology (MaTe) – Introduction Computational Rheology important for: B Polymer processing B Rheology & Material science B Turbulent flow (drag reduction phenomena) B Food processing B Biological flows B ... Introduction (Polymer Processing) Analysis of viscoelastic phenomena essential for predicting B Flow induced crystallization kinetics B Flow instabilities during processing B Free surface flows (e.g.extrudate swell) B Secondary flows B Dimensional stability of injection moulded products B Prediction of mechanical and optical properties Introduction (Surface Defects on Injection Molded Parts) Alternating dull bands perpendicular to flow direction with high surface roughness (M. Bulters & A. Schepens, DSM-Research). Introduction (Flow Marks, Two Color Polypropylene) Flow Mark Side view Top view Bottom view M. Bulters & A. Schepens, DSM-Research Introduction (Simulation flow front) 1 0.5 Steady Perturbed H 2y 0 ___ −0.5 −1 0 0.5 1 ___2x H Introduction (Rheology & Material Science) Simulation essential for understanding and predicting material properties: B Polymer blends (morphology, viscosity, normal stresses) B Particle filled viscoelastic fluids (suspensions) B Polymer architecture macroscopic properties (Brownian dynamics (BD), molecular dynamics (MD),⇒ Monte Carlo, . ) Multi-scale. ⇒ Introduction (Solid particles in a viscoelastic fluid) B Microstructure (polymer, particles) B Bulk rheology B Flow induced crystallization Introduction (Multiple particles in a viscoelastic fluid) Introduction (Flow induced crystallization) Introduction (Multi-phase flows) Goal and contents of the course Goal: Introduction of the basic numerical techniques used in Computational Rheology using the Finite Element Method (FEM). -
Chapter 3 Equations of State
Chapter 3 Equations of State The simplest way to derive the Helmholtz function of a fluid is to directly integrate the equation of state with respect to volume (Sadus, 1992a, 1994). An equation of state can be applied to either vapour-liquid or supercritical phenomena without any conceptual difficulties. Therefore, in addition to liquid-liquid and vapour -liquid properties, it is also possible to determine transitions between these phenomena from the same inputs. All of the physical properties of the fluid except ideal gas are also simultaneously calculated. Many equations of state have been proposed in the literature with either an empirical, semi- empirical or theoretical basis. Comprehensive reviews can be found in the works of Martin (1979), Gubbins (1983), Anderko (1990), Sandler (1994), Economou and Donohue (1996), Wei and Sadus (2000) and Sengers et al. (2000). The van der Waals equation of state (1873) was the first equation to predict vapour-liquid coexistence. Later, the Redlich-Kwong equation of state (Redlich and Kwong, 1949) improved the accuracy of the van der Waals equation by proposing a temperature dependence for the attractive term. Soave (1972) and Peng and Robinson (1976) proposed additional modifications of the Redlich-Kwong equation to more accurately predict the vapour pressure, liquid density, and equilibria ratios. Guggenheim (1965) and Carnahan and Starling (1969) modified the repulsive term of van der Waals equation of state and obtained more accurate expressions for hard sphere systems. Christoforakos and Franck (1986) modified both the attractive and repulsive terms of van der Waals equation of state. Boublik (1981) extended the Carnahan-Starling hard sphere term to obtain an accurate equation for hard convex geometries. -
Foundations of Continuum Mechanics
Foundations of Continuum Mechanics • Concerned with material bodies (solids and fluids) which can change shape when loaded, and view is taken that bodies are continuous bodies. • Commonly known that matter is made up of discrete particles, and only known continuum is empty space. • Experience has shown that descriptions based on continuum modeling is useful, provided only that variation of field quantities on the scale of deformation mechanism is small in some sense. Goal of continuum mechanics is to solve BVP. The main steps are 1. Mathematical preliminaries (Tensor theory) 2. Kinematics 3. Balance laws and field equations 4. Constitutive laws (models) Mathematical structure adopted to ensure that results are coordinate invariant and observer invariant and are consistent with material symmetries. Vector and Tensor Theory Most tensors of interest in continuum mechanics are one of the following type: 1. Symmetric – have 3 real eigenvalues and orthogonal eigenvectors (eg. Stress) 2. Skew-Symmetric – is like a vector, has an associated axial vector (eg. Spin) 3. Orthogonal – describes a transformation of basis (eg. Rotation matrix) → 3 3 3 u = ∑uiei = uiei T = ∑∑Tijei ⊗ e j = Tijei ⊗ e j i=1 ~ ij==1 1 When the basis ei is changed, the components of tensors and vectors transform in a specific way. Certain quantities remain invariant – eg. trace, determinant. Gradient of an nth order tensor is a tensor of order n+1 and divergence of an nth order tensor is a tensor of order n-1. ∂ui ∂ui ∂Tij ∇ ⋅u = ∇ ⊗ u = ei ⊗ e j ∇ ⋅ T = e j ∂xi ∂x j ∂xi Integral (divergence) Theorems: T ∫∫RR∇ ⋅u dv = ∂ u⋅n da ∫∫RR∇ ⊗ u dv = ∂ u ⊗ n da ∫∫RR∇ ⋅ T dv = ∂ T n da Kinematics The tensor that plays the most important role in kinematics is the Deformation Gradient x(X) = X + u(X) F = ∇X ⊗ x(X) = I + ∇X ⊗ u(X) F can be used to determine 1. -
Fluid Inertia and End Effects in Rheometer Flows
FLUID INERTIA AND END EFFECTS IN RHEOMETER FLOWS by JASON PETER HUGHES B.Sc. (Hons) A thesis submitted to the University of Plymouth in partial fulfilment for the degree of DOCTOR OF PHILOSOPHY School of Mathematics and Statistics Faculty of Technology University of Plymouth April 1998 REFERENCE ONLY ItorriNe. 9oo365d39i Data 2 h SEP 1998 Class No.- Corrtl.No. 90 0365439 1 ACKNOWLEDGEMENTS I would like to thank my supervisors Dr. J.M. Davies, Prof. T.E.R. Jones and Dr. K. Golden for their continued support and guidance throughout the course of my studies. I also gratefully acknowledge the receipt of a H.E.F.C.E research studentship during the period of my research. AUTHORS DECLARATION At no time during the registration for the degree of Doctor of Philosophy has the author been registered for any other University award. This study was financed with the aid of a H.E.F.C.E studentship and carried out in collaboration with T.A. Instruments Ltd. Publications: 1. J.P. Hughes, T.E.R Jones, J.M. Davies, *End effects in concentric cylinder rheometry', Proc. 12"^ Int. Congress on Rheology, (1996) 391. 2. J.P. Hughes, J.M. Davies, T.E.R. Jones, ^Concentric cylinder end effects and fluid inertia effects in controlled stress rheometry, Part I: Numerical simulation', accepted for publication in J.N.N.F.M. Signed ...^.^Ms>3.\^^. Date Ik.lp.^.m FLUH) INERTIA AND END EFFECTS IN RHEOMETER FLOWS Jason Peter Hughes Abstract This thesis is concerned with the characterisation of the flow behaviour of inelastic and viscoelastic fluids in steady shear and oscillatory shear flows on commercially available rheometers. -
On Exact Solution of Unsteady MHD Flow of a Viscous Fluid in An
Rana et al. Boundary Value Problems 2014, 2014:146 http://www.boundaryvalueproblems.com/content/2014/1/146 R E S E A R C H Open Access On exact solution of unsteady MHD flow of a viscous fluid in an orthogonal rheometer Muhammad Afzal Rana1, Sadia Siddiqa2* and Saima Noor3 *Correspondence: [email protected] Abstract 2Department of Mathematics, COMSATS Institute of Information This paper studies the unsteady MHD flow of a viscous fluid in which each point of Technology, Attock, Pakistan the parallel planes are subject to the non-torsional oscillations in their own planes. Full list of author information is The streamlines at any given time are concentric circles. Exact solutions are obtained available at the end of the article and the loci of the centres of these concentric circles are discussed. It is shown that the motion so obtained gives three infinite sets of exact solutions in the geometry of an orthogonal rheometer in which the above non-torsional oscillations are superposed on the disks. These solutions reduce to a single unique solution when symmetric solutions are looked for. Some interesting special cases are also obtained from these solutions. Keywords: viscous fluid; MHD flow; orthogonal rheometer; eccentric rotation; exact solutions 1 Introduction Berker [] has defined the ‘pseudo plane motions’ of the first kind that: if the streamlines in a plane flow are contained in parallel planes but the velocity components are dependent on the coordinate normal to the planes. Berker [] has obtained a class of exact solutions to the Navier-Stokes equations belonging to the above type of flows.