Book of Abstracts
Total Page:16
File Type:pdf, Size:1020Kb
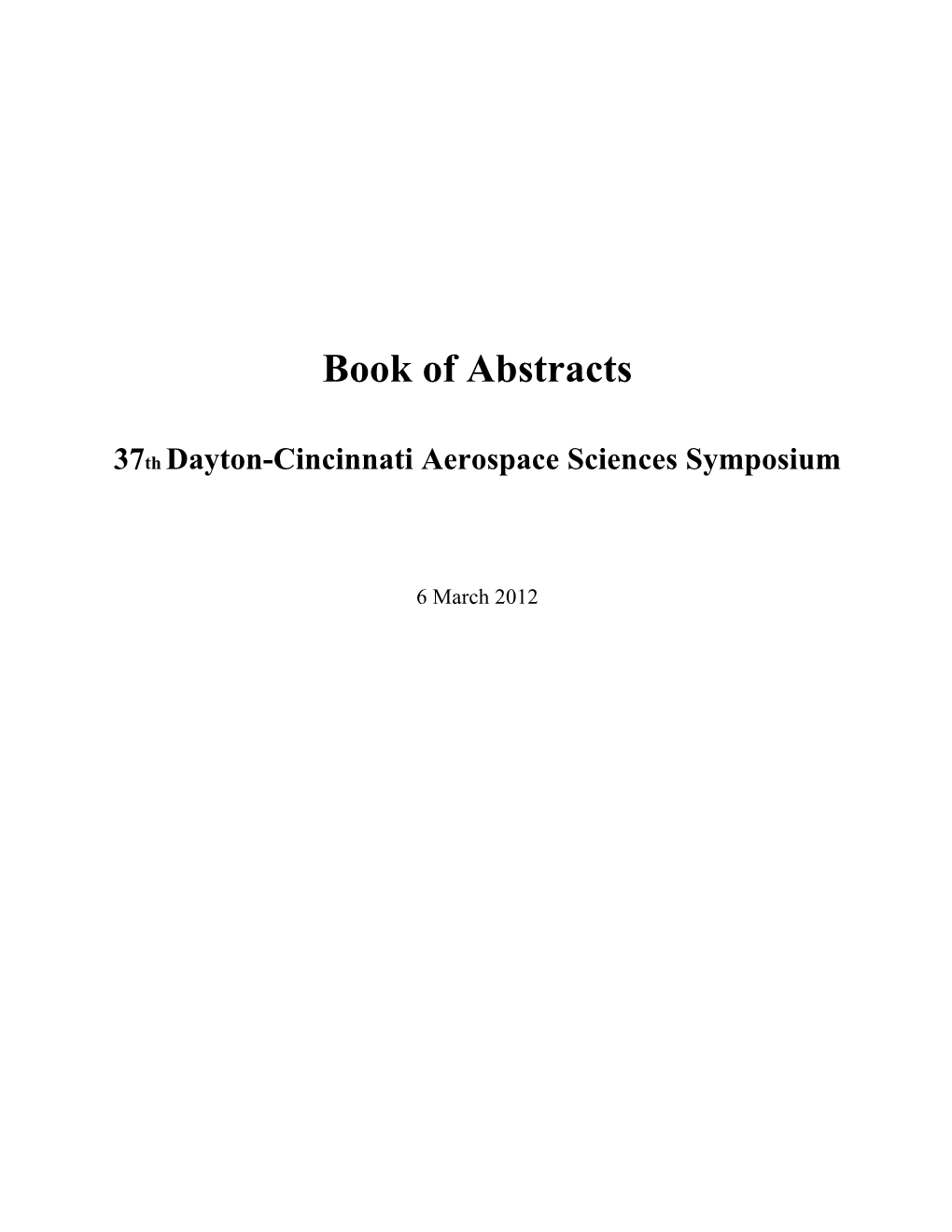
Load more
Recommended publications
-
Penetration Simulation for Uncontained Engine Debris Impact on Fuselage-Like Panels Using LS-DYNA
Finite Elements in Analysis and Design 36 (2000) 99}133 Penetration simulation for uncontained engine debris impact on fuselage-like panels using LS-DYNA Norman F. Knight Jr! *, Navin Jaunky", Robin E. Lawson#, Damodar R. Ambur$ !Veridian MRJ Engineering, Yorktown, VA 23693-2619, USA "Eagle Aeronautics, Inc., Newport News, VA 23606, USA #Newport News Ship Building and Dry Dock Company, Newport News, VA 23607, USA $NASA Langley Research Center, Hampton, VA 23681-0001, USA Abstract Modeling and simulation requirements for uncontained engine debris impact on fuselage skins are proposed and assessed using the tied-nodes-with-failure modeling approach for penetration. A "nite element analysis is used to study the penetration of aluminum plates impacted by titanium impactors in order to simulate the e!ect of such uncontained engine debris impacts on aircraft fuselage-like skin panels. LS-DYNA is used in the simulations to model the impactor, test "xture frame and target barrier plate. The e!ects of mesh re"nement, contact modeling, and impactor initial velocity and orientation are studied using a con"g- uration for which limited test data are available for comparison. ( 2000 Elsevier Science B.V. All rights reserved. Keywords: Impact; Penetration; LS-DYNA; Finite elements 1. Introduction Prediction of the elasto-plastic, large-deformation, transient dynamic behavior involving impact of multiple deformable bodies continues to provide new insights into the response of complex structural systems subjected to extreme loading conditions or exposed to extreme environments (e.g., Refs. [1}3]). Much of the computational mechanics technology necessary for simulating this behavior evolved over decades of research sponsored in part by government laboratories which also have had access to large supercomputer facilities. -
Statistics on Aircraft Gas Turbine Engine Rotor Failures That Occurred
DOT/FAA/CT-89/5 Statistics on Aircraft Gas FAA Techni",,1 Center Atlantic City International Airport Turbine Engine Rotor Failures N.J. 08405 that Occurred in U.S. Commercial Aviation During 1983 R.A. DelUCia J.T. Salvino Naval Air Propulsion Center Trenton, New Jersey March 1989 Final Report This document Is available to the U.S. public through the National Technical Information Service, Springfield, Virginia 22161 . • DOT/FAA us. Depa Ii i e It of Tronspot laro I CT-89/5 Federal AvIaIton Admlnlstratton 00013414 DOT/FAA CT-89/5 Statistics on aircraft g :~rbt ine engine rotor fa~'~res a oCCurred in U.S. ~ommercial aviation during 983. NOTICE This document is disseminated under the sponsorship of the U. S. Department of Transportation in the interest of information exchange. The United States Government assumes no liability for the contents or use thereof. The United States Government does not endorse products or manufacturers. Trade or manufacturers' names appear herein solely because they are considered essential to the objective of this report. Technical Repart Documentatian Page 1. Report No. 2. Go".rn",."t "'cc ••• ion No. 3. R.cipie"t' . Cotolol No . DOT/FAA/CT-89/5 •• Title o"d Subtitle S . Repo,t "ote March 1989 STATISTICS ON AIRCRAFT GAS TURBINE ENGINE ROTOR 6. P.rforming O'.o"ilolion Code FAILURES THAT OCCURRED IN U.S. COMMERCIAL AVIATION DURING 1983 PE32 I . Per'orll'lin g Orooni&etio" Report No . 7. "'ulho,' .) , R. A. Delucia and J. T. Salvino NAPC-PE-184 9. P.rformi". O, • .,i 10110" N_e and "'ddr ••• 10 . -
Engineering and Metallographic Aspects of Gas Turbine Engine Failure Investigation: Identifying the Causes
Engineering and Metallographic Aspects of Gas Turbine Engine Failure Investigation: Identifying the Causes by Robert E. Dundas, Principal Engineer Factory Mutual Engineering & Research Technicians are seldom assigned the provide knowledge of how such responsibility of analyzing the cause failures can be avoided in the future. of a gas turbine engine failure, but it Knowing the features of cracks and is not uncommon for them to be in- fractures in materials used in gas tur- volved in the investigation of a pre- bine engines is important in associat- mature gas turbine engine ing them with failures. malfunction or failure. Table 1 (page 2) lists the most likely As a participant in the tear-down in- initiating failure mechanisms for the spection of the engine and review of major components of gas turbine en- the findings, the technician must un- gines. The list is derived from en- derstand the modes of metallic com- gine case histories and an ponent failures and how each understanding of the design and can be identified during the function of each component. The investigation. mechanisms in boldface represent the most common failures. The purpose of investigating a gas turbine engine failure is to identify a Cracks and fractures in gas turbine definitive cause of the failure to engine parts, both rotating and FLIGHT SAFETY FOUNDATION • AVIATION MECHANICS BULLETIN • JANUARY/FEBRUARY 1994 1 Table 1 Failure Mechanisms of Gas Turbine Components SectionComponents Problem Compressors Disks High-cycle fatigue Low-cycle fatigue Blades High-frequency -
Statistics on Aircraft Gas Turbine Engine Rotor Failures That Occurred
DOT/FAA/CT-88/23 Statistics on Aircraft Gas FAA Technical Center Atlantic City International Airport Turbine Engine Rotor Failures N.J. 08405 that Occurred in U. S. Commercial Aviation During I ! 1982 -- A.A. Delucia J.T. Salvino Naval Air Propulsion Center Trenton, New Jersey AVAH-P.BLE IN July 1988 ELECTRONIC FORMAT Final Report This document is available to the U.S. public through the National Technical Information I• Service, Springfield, Virginia 22161. u.s. Department of Transportation Federal Aviation Administration NOTICE This document is disseminated under the sponsorship of the U. S. Department of Transportation in the interest of information exchange. The United States Government assumes no liability for the contents or use thereof. The United States Government does not endorse products '"( . or manufacturers. Trade or manufacturers' names appear herein solely because they are considered essential to the objective of this report. Technical Report Documentation Page 1. Report No. 2. Government Accession No. 3. Recipient's Catalog No. DOT/FAA/CT-88/23 4. Title and Subtitle 5. Report Date STATISTICS ON AIRCRAFT GAS TURBINE ENGINE ROTOR July 1988 FAILURES THAT OCCURRED IN U.S. COMMERCIAL AVIATION 16-. Perfo'rTllng Organization Code- ------- DURING 1982 Perform,ng ~~~::jZation Report No r---o;-----:-:--------~---------.------ --- IT i 7. Author s) I R. A. Delucia and J. T. Salvino I DOT /FAA/CT-88/23 I >------,----------------- •. ~----- ------1 I 9. Performing OrganizatIon Name and Address i 10. Work Un<f No. ITR,\IS) j COrnDlanding Officer ____________4! Naval Air Propulsion Center l-l. Contract or Grant No. PO Box 7176 DOTiFA71NA AP98 I Trenton, NJ 08628-0176 ~12. -
AEROSPACE July Cover.Indd
THE GREAT BRITISH TAKE-OFF LIGHTNING II HEADS www.aerosociety.com FOR FARNBOROUGH DÉBUT July 2014 UK’S NEW CIVIL AEROSPACE R&D WILD ABOUT THE CAT NASA’S PATH TO MARS His Royal Highness The Prince of Wales is presented with his Honorary Fellowship certifi cate in 1978 by the then-President Prof Lew Crabtree. RAeS (NAL). HRH The Prince of Wales accepts invitation to become Honorary President in 2016 The Royal Aeronautical Society is delighted to announce that His The Chief Executive of the Royal Aeronautical Society, Simon Royal Highness The Prince of Wales has accepted the Society’s Luxmoore said: “We are honoured that The Prince of Wales has invitation to act as its Honorary President for 2016, the 150th graciously accepted our invitation to become our Honorary anniversary year of the establishment of the Society. President during our 150th anniversary year. 2016 will be an His Royal Highness’s Presidency will continue the Royal occasion to celebrate innovation, not only through past Family’s long association with the Royal Aeronautical Society. Her achievements but, more importantly, through looking to the future. Majesty The Queen became the Society’s Patron in 1952, As such, we very much intend to support His Royal Highness’ succeeding her father, King George VI, in this role. Both Their continuing commitment to encouraging youth opportunity. The Royal Highnesses The Prince Philip, Duke of Edinburgh, and The support of our Honorary President in this important area will inspire Prince of Wales are Honorary Fellows, the Society’s highest and the next generation towards even greater innovations in science, most prestigious award. -
Propulsion System Malfunction Plus Inappropriate Crew Response (PSM+ICR)
FLIGHT SAFETY FOUNDATION NOVEMBER–DECEMBER 1999 FLIGHT SAFETY DIGEST SPECIAL DOUBLE ISSUE Propulsion System Malfunction Plus Inappropriate Crew Response (PSM+ICR) Human Factors Report FLIGHT SAFETY FOUNDATION For Everyone Concerned With the Safety of Flight Flight Safety Digest Officers and Staff Vol. 18 No. 11–12 November–December 1999 Stuart Matthews Chairman, President and CEO Board of Governors In This Issue Robert H. Vandel Propulsion System Malfunction Plus Executive Vice President 1 James S. Waugh Jr. Inappropriate Crew Response (PSM+ICR) Treasurer Carl Vogt General Counsel and Secretary Controlled-flight-into-terrain Accidents Board of Governors Decline in First 11 Months of 1999 194 ADMINISTRATIVE Boeing data show one CFIT hull-loss accident involving a Ellen Plaugher large, Western-built commercial jet airplane. Executive Assistant Linda Crowley Horger Manager, Support Services FAA Publishes Guidelines for 196 FINANCIAL Aircraft Data Communications Systems Elizabeth Kirby Advisory circular outlines standards developed Controller in cooperation with international civil aviation authorities. TECHNICAL James Burin Boeing 727 Strikes Runway During Director of Technical Programs 198 Joanne Anderson Missed Approach Technical Assistant Ann Hill Manager of Seminars and Workshops Robert H. Gould Managing Director of Aviation Safety Audits and Internal Evaluation Programs Robert Feeler Manager of Aviation Safety Audits Robert Dodd, Ph.D. Manager, Data Systems and Analysis Darol V. Holsman Safety Audits MEMBERSHIP Carole L. Pammer Director of Marketing and Business Development Ahlam Wahdan Assistant to the Director of Marketing and Business Development PUBLICATIONS Roger Rozelle Director of Publications Mark Lacagnina Senior Editor Wayne Rosenkrans Senior Editor Linda Werfelman Cover image: Copyright © 1999 PhotoDisc Inc. Senior Editor Karen K. -
Experimental Investigations of the Onset of Sand Deposits on Hastelloy-X Between 1000 °C and 1100 °C
Experimental Investigations of the Onset of Sand Deposits on Hastelloy-X between 1000 °C and 1100 °C John Patrick Hutchinson Thesis submitted to the faculty of the Virginia Polytechnic Institute and State University in partial fulfillment of the requirements for the degree of Masters of Science In Mechanical Engineering Wing F. Ng Srinath V. Ekkad Kevin T. Lowe October 10, 2016 Blacksburg, Virginia, USA Keywords: Sand, Microparticle, Arizona Road Dust, Deposition Copyright 2016 Experimental Investigation of the Onset of Sand Deposits on Hastelloy-X between 1000 °C and 1100 °C John Patrick Hutchinson ACADEMIC ABSTRACT In many arid regions, particle ingestion can occur within propulsive gas turbines. The ingested particles can severely impact performance and may damage many primary gas path components through erosion or deposition. Characterizing crystalline deposits on metallic substrates can allow for the prediction of deposition to improve component resilience and develop health monitoring algorithms. This work investigates the effect of temperature and angle on sand deposits and attempts to quantitatively characterize the deposition of Arizona Test Dust (ATD) onto Hastelloy-X. The first study presented in this thesis describes a preliminary investigation of sand deposition at temperatures and velocities similar to those found in the turbine section of propulsive gas turbine engines and presents an equation for predicting deposition as a function of gas path temperature and impact angle. The sand and air mixture maintained a constant flow velocity of approximately 70 m/s, impact angle was varied from 30° to 90°, and the gas path temperature was varied from 1000 °C to 1100 °C. The number of deposits was found to linearly increase with temperature for all coupon angles tested. -
Flight Safety Digest November-December 1999
FLIGHT SAFETY FOUNDATION NOVEMBER–DECEMBER 1999 FLIGHT SAFETY DIGEST SPECIAL DOUBLE ISSUE Propulsion System Malfunction Plus Inappropriate Crew Response (PSM+ICR) Human Factors Report FLIGHT SAFETY FOUNDATION For Everyone Concerned With the Safety of Flight Flight Safety Digest Officers and Staff Vol. 18 No. 11–12 November–December 1999 Stuart Matthews Chairman, President and CEO Board of Governors In This Issue Robert H. Vandel Propulsion System Malfunction Plus Executive Vice President 1 James S. Waugh Jr. Inappropriate Crew Response (PSM+ICR) Treasurer Carl Vogt General Counsel and Secretary Controlled-flight-into-terrain Accidents Board of Governors Decline in First 11 Months of 1999 194 ADMINISTRATIVE Boeing data show one CFIT hull-loss accident involving a Ellen Plaugher large, Western-built commercial jet airplane. Executive Assistant Linda Crowley Horger Manager, Support Services FAA Publishes Guidelines for 196 FINANCIAL Aircraft Data Communications Systems Elizabeth Kirby Advisory circular outlines standards developed Controller in cooperation with international civil aviation authorities. TECHNICAL James Burin Boeing 727 Strikes Runway During Director of Technical Programs 198 Joanne Anderson Missed Approach Technical Assistant Ann Hill Manager of Seminars and Workshops Robert H. Gould Managing Director of Aviation Safety Audits and Internal Evaluation Programs Robert Feeler Manager of Aviation Safety Audits Robert Dodd, Ph.D. Manager, Data Systems and Analysis Darol V. Holsman Safety Audits MEMBERSHIP Carole L. Pammer Director of Marketing and Business Development Ahlam Wahdan Assistant to the Director of Marketing and Business Development PUBLICATIONS Roger Rozelle Director of Publications Mark Lacagnina Senior Editor Wayne Rosenkrans Senior Editor Linda Werfelman Cover image: Copyright © 1999 PhotoDisc Inc. Senior Editor Karen K. -
Aeronautical Engineering
NASA/SP--2000-7037/SU PPL413 March 2000 AERONAUTICAL ENGINEERING A CONTINUING BIBLIOGRAPHY WITH INDEXES National Aeronautics and Space Administration Langley Research Center Scientific and Technical Information Program Office The NASA STI Program Office... in Profile Since its founding, NASA has been dedicated CONFERENCE PUBLICATION. Collected to the advancement of aeronautics and space papers from scientific and technical science. The NASA Scientific and Technical conferences, symposia, seminars, or other Information (STI) Program Office plays a key meetings sponsored or cosponsored by NASA. part in helping NASA maintain this important role. SPECIAL PUBLICATION. Scientific, technical, or historical information from The NASA STI Program Office is operated by NASA programs, projects, and missions, Langley Research Center, the lead center for often concerned with subjects having NASA's scientific and technical information. substantial public interest. The NASA STI Program Office provides access to the NASA STI Database, the largest collection TECHNICAL TRANSLATION. of aeronautical and space science STI in the English-language translations of foreign world. The Program Office is also NASNs scientific and technical material pertinent to institutional mechanism for disseminating the NASA's mission. results of its research and development activities. These results are published by NASA in the Specialized services that complement the STI NASA STI Report Series, which includes the Program Office's diverse offerings include following report types: creating custom thesauri, building customized databases, organizing and publishing research TECHNICAL PUBLICATION. Reports of results.., even providing videos. completed research or a major significant phase of research that present the results of For more information about the NASA STI NASA programs and include extensive data or Program Office, see the following: theoretical analysis. -
Statistics on Aircraft Gas Turbine Engine Rotor Failures That Occurred
DOT/ FAA/CT-8917 Statistics on Aircraft Gas FAA Technical Center Atlantic City International Airport Turbine Engine Rotor Failures N.J. 08405 that Occurred in U. S. Commercial Aviation During 1985 A.A. Delucia Naval Air Propulsion Center J.T. Salvino Trenton, New Jersey B. C. Fenton FAA Technical Center f l DLf(Al AU,! July 1989 l JW - Final Report IlL" ,.Al· , I ~l lANnrJI. tilt This document is available to the U.S. public through the National Technical Information Service, Springfield, Virginia 22161 . us. Depo III iI!fIt 01 TronsporToIIOn DOT/FAA _ AvtatIon Ad...... lratIon CT-89/7 FAA WJH Technical Center 1111111 11111 11111 11111 11111 1111111111 1111111111111 '00020931' DOT/FAA CT-8917 Stat~stics on aircraft gas :~rb,"e engine rotor failures at occurred in U.S . commercial aViation during 1985. NOTICE This document is disseminated under the sponsorship of the U. S. Department of Transportation in the interest of information exchange. The United States Government assumes no liability for the contents or use thereof. The United States Government does not endorse products or manufacturers. Trade or manufacturers' names appear herein solely because they are considered essential to the objective of this report . Technical ~eport Documentation Page 1. R.po" No. 2. Go .... rnm.n' Acc.",on No. 3. A.c,pi.n,· , COlalog No . DOT/FAA/CT-89-7 •. Till. ond S\lb'ill. S. R.porl f)o'. July 1989 STATISTICS ON AIRCRAFT GAS TURBINE ENGINE ROTOR 6. P.,fo""in, Organi lOtion Cod. FAILURES THAT OCCURRED IN U.S. COMMERCIAL AVIATION PE32 DURING 1985 8. -
A Cognitive Approach to Terms in Qantas 32 Investigation Report and Their Translations
Publif@rum 33, 2020 Terminologia e Traduzione Linlin WU, Bo ZHU, Peng GAO Framing the Concepts in Specialized Texts: a Cognitive Approach to Terms in Qantas 32 Investigation Report and Their Translations Nota Il contenuto di questo sito è regolato dalla legge italiana in materia di proprietà intellettuale ed è di proprietà esclusiva dell'editore. Le opere presenti su questo sito possono essere consultate e riprodotte su carta o su supporto digitale, a condizione che siano strettamente riservate per l'utilizzo a fini personali, scientifici o didattici a esclusione di qualsiasi funzione commerciale. La riproduzione deve necessariamente menzionare l'editore, il nome della rivista, l'autore e il documento di riferimento. Qualsiasi altra riproduzione è vietata senza previa autorizzazione dell'editore, tranne nei casi previsti dalla legislazione in vigore in Italia. Farum.it Farum è un gruppo di ricerca dell’Università di Genova Pour citer cet article : Linlin WU, Bo ZHU, Peng GAO, Framing the Concepts in Specialized Texts: a Cognitive Approach to Terms in Qantas 32 Investigation Report and Their Translations, Terminologia e Traduzione, Publifarum, n. 33, pubblicato il 2020, consultato il 25/09/2021, url: http://www.farum.it/publifarum/ezine_pdf.php?id=505 Editore Publifarum (Dipartimento di Lingue e Culture Moderne - Univerità di Genova) http://www.farum.it/publifarum/ http://www.farum.it Documento accessibile in rete su: http://www.farum.it/publifarum/ezine_articles.php?art_id=505 Document généré automatiquement le 25/09/2021. pagina 1 / 15 Framing the Concepts in Specialized Texts: a Cognitive Approach to Terms in Qantas 32 Investigation Report and Their Translations Linlin WU, Bo ZHU, Peng GAO Table 1. -
ME3) in Aerospace Gas Turbine Engines
Vol. 8(6), pp. 46-65, September 2017 DOI: 10.5897/JCEMS2016.0282 Articles Number: 438B1FC66341 Journal of Chemical Engineering and Materials ISSN 2141-6605 Copyright ©2017 Science Author(s) retain the copyright of this article http://www.academicjournals.org/JCEMS Full Length Research Paper Failure of Nickel-based super alloy (ME3) in aerospace gas turbine engines A. Anvari Department of Mechanical and Aerospace Engineering, University of Missouri-Columbia, Columbia, Missouri, U.S.A. Received 28 December, 2016; Accepted 18 July, 2017 The significant goal of this study is to develop a system to determine the margin of safety for ME3 super alloy in aerospace gas turbine engines. This margin of safety can be defined as critical temperature, force stress, exposure time, and cycles. In this research, by applying analytical solutions and using experimental data, equations are obtained to predict the life of a nickel-base super alloy in aerospace gas turbine engines. The experimental data that are applied to obtain the equations are achieved by gas turbine environment simulation experiments. This environment is contained with mechanical cycles at high temperature. The results that are achieved by these solutions are compared with the data from an experiment on a composite material. This comparison has proved that the results of this study seem logical. Ultimately, by employing of convex, concave, and linear equations, many results to predict the life of ME3 are obtained. Main reasons in ME3 failure at gas turbine engine environment is determined by this method. Based on the results of this research, the most important cause of ME3 failure is due to maximum mechanical force at high temperatures close to 763°C.