Surface Characteristics of One-Sided Charred Beech Wood
Total Page:16
File Type:pdf, Size:1020Kb
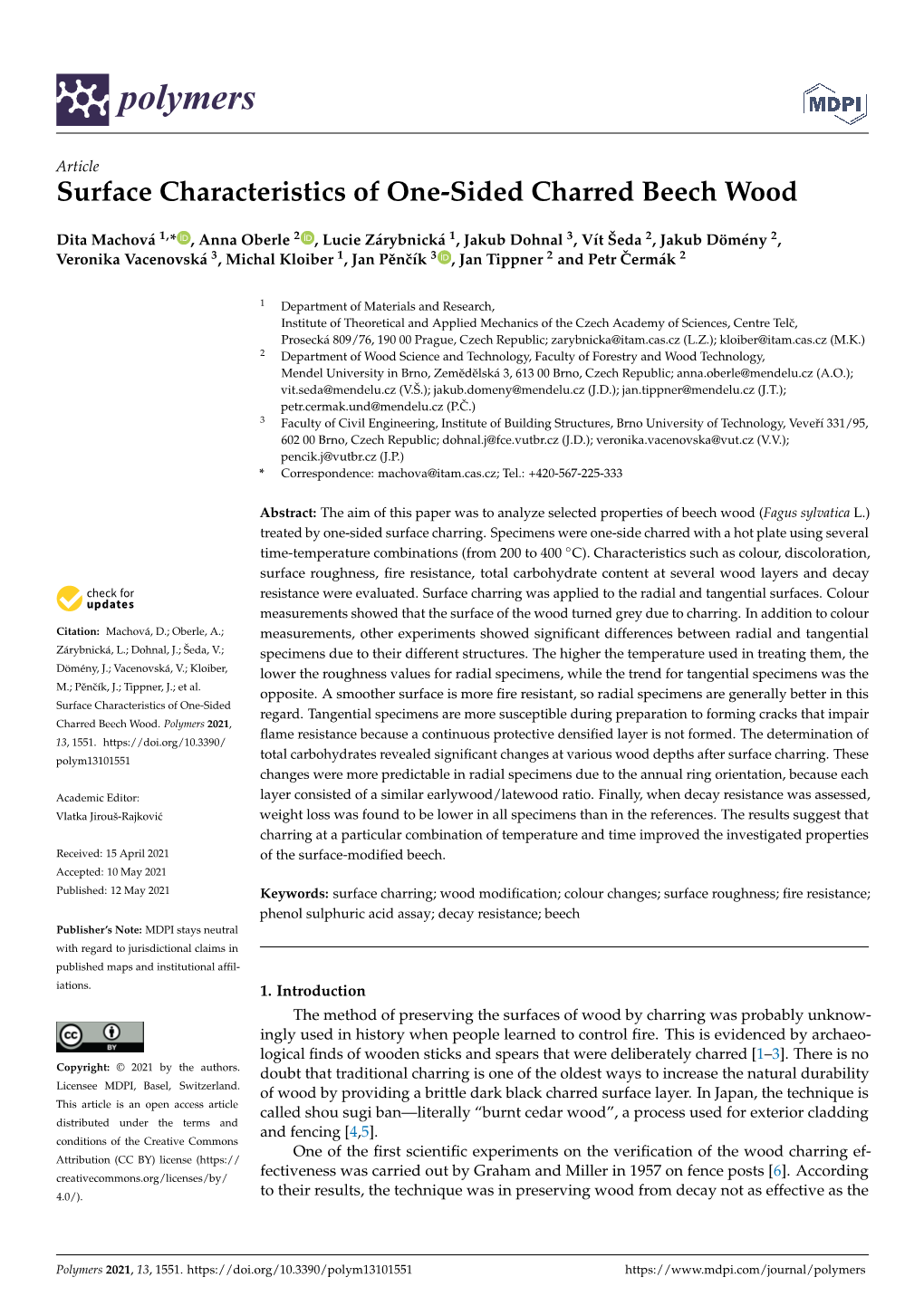
Load more
Recommended publications
-
Simulation of Tree Stem Injury, Air Flow and Heat Dispersion in Forests for Prediction of Fire Effects
SIMULATION OF TREE STEM INJURY, AIR FLOW AND HEAT DISPERSION IN FORESTS FOR PREDICTION OF FIRE EFFECTS DISSERTATION Presented in Partial Fulfillment of the Requirements for the Degree Doctor of Philosophy in the Graduate School of The Ohio State University By Efthalia K. Chatziefstratiou, Dipl. Ing., M.S. Graduate Program in Environmental Sciences The Ohio State University 2015 Dissertation Committee: Gil Bohrer “Advisor” Matthew B. Dickinson Ethan Kubatko Gajan Sivandran Barbara Wyslouzil Copyright by Efthalia Chatziefstratiou 2015 Abstract This work presents two computational tools, Firestem2D and the fire module of Regional Atmospheric Modelling System (RAMS)-based Forest Large Eddy Simulation (RAFLES), which will help to make predictions of fire effects on trees and the atmosphere. FireStem2D is a software tool for predicting tree stem heating and injury in forest fires. It is a physically-based, two-dimensional model of stem thermodynamics that results from heating at the bark surface. It builds on an earlier one-dimensional model (FireStem) and provides improved capabilities for predicting fire-induced mortality and injury before a fire occurs by resolving stem moisture loss, temperatures through the stem, degree of bark charring, and necrotic depth around the stem. The results of numerical parameterization and model evaluation experiments for FireStem2D that simulate laboratory stem-heating experiments of 52 tree sections from 25 trees are presented. A set of virtual sensitivity analysis experiments were also conducted to test the effects of unevenness of heating around the stem and with above ground height using data from two studies: a low-intensity surface fire and a more intense crown fire. -
Iqos: Evidence of Pyrolysis and Release of a Toxicant from Plastic
iQOS: Evidence of Pyrolysis and Release of a Toxicant from Plastic Barbara Davis ([email protected]) a , Monique Williams ([email protected])a , and Prue Talbot ([email protected]) a a Department of Molecular, Cell and Systems Biology, University of California, Riverside, CA 92521, United States Corresponding author: Prue Talbot Address: Department of Molecular, Cell and Systems Biology University of California Riverside, CA 92521 Email: [email protected] Telephone: 951-827-3768 FAX: 951-827-4286 Keywords: new tobacco products, heat-not-burn tobacco products, electronic nicotine delivery devices, ENDS, nicotine, quality control, pyrolysis, char Word Count: 3346 ABSTRACT Objective: To evaluate performance of the iQOS Heat-Not-Burn system as a function of cleaning and puffing topography, investigate the validity of manufacturer’s claims that this device does not burn tobacco, and determine if the polymer-film filter is potentially harmful. Methods: iQOS performance was evaluated using five running conditions incorporating two different cleaning protocols. Heatsticks were visually and stereomicroscopically inspected pre- and post- use to determine the extent of tobacco plug charring (from pyrolysis) and polymer-film filter melting, and to elucidate the effects of cleaning on charring. GC-MS headspace analysis was conducted on unused polymer-film filters to determine if potentially toxic chemicals are emitted from the filter during heating. Results: For all testing protocols, pressure drop decreased as puff number increased. Changes in testing protocols did not affect aerosol density. Charring due to pyrolysis (a form of organic matter thermochemical decomposition) was observed in the tobacco plug after use. When the manufacturers’ cleaning instructions were followed, both charring of the tobacco plug and melting of the polymer-film filter increased. -
Heated Cigarettes: How States Can Avoid Getting Burned
HEATED CIGARETTES: HOW STATES CAN AVOID GETTING BURNED 8/30/18 1 HEATED CIGARETTES HOW STATES CAN AVOID GETTING BURNED 8/30/18 2 THE PUBLIC HEALTH LAW CENTER 8/30/18 3 8/30/18 4 LEGAL TECHNICAL ASSISTANCE Legal Research Policy Development, Implementation, Defense Publications Trainings Direct Representation Lobby 8/30/18 5 HEATED CIGARETTES HOW STATES CAN AVOID GETTING BURNED • Presenters: – Kristy Marynak, MPP, Public Health Analyst, Centers for Disease Control and Prevention – Hudson Kingston, JD, LLM, Staff Attorney, Tobacco Control Legal Consortium at the Public Health Law Center 8/30/18 6 HEATED CIGARETTES HOW STATES CAN AVOID GETTING BURNED • Heated cigarettes on the global market • Distinguishing features 1. Heating at a temperature lower than conventional cigarettes that produce an inhalable aerosol • Heated Cigarettes: 450-700° F (generally) • Conventional cigarettes: 1250 – 1300 °F, • (max: 1500 °F) 2. Processed, commercial tobacco leaf is the nicotine source, flavor source, or both 8/30/18 7 HEATED CIGARETTES HOW STATES CAN AVOID GETTING BURNED Federal Regulation • Pre-Market Review • Modified Risk Tobacco Product Application • Vapeleaf 8/30/18 8 Heated Tobacco Products: Considerations for Public Health Policy and Practice KRISTY MARYNAK, MPP LEAD PUBLIC HEALTH ANALYST CDC OFFICE ON SMOKING AND HEALTH TOBACCO CONTROL LEGAL CONSORTIUM WEBINAR AUGUST 2018 8/30/18 9 What’s the public health importance of this topic? The landscape of tobacco products is continually changing By being proactive and anticipating new products, we can -
Market Development Survey for Continuous Coal Charring Process
Market development survey for continuous coal charring process by Robert A Lengemann A THESIS Submitted to the Graduate Faculty in partial fulfillment of the requirements for the degree of Master of Science in Chemical Engineering Montana State University © Copyright by Robert A Lengemann (1957) Abstract: In recent years, work has been progressing on a new continuous charring process at Montana State College. This work has been sponsored by the Montana State College Engineering Experiment Station with the hope that this process will bolster Montana's lagging coal industry. The work has now reached the point of commercialization and a market for the char needs to be developed. Several tests have been run on the char produced from this char process. Anaconda Company used the char in their Sponge Iron Plant successfully. American Chrome Company has had the char tested and accepts it with the reservation that the sulfur content must be kept below 0.5%. Colorado Fuel and Iron Corporation has used char from this char process with some success. The char used in the Anaconda test and in the American Chrome test was derived from Red Lodge coal as this coal is being used in the first commercial plant at Red Lodge, Montana. Colorado Fuel and Iron Corporation furnished their own coal since this is the coal they intend to use, should they decide to build a char plant for their use. The estimated capacity of the Red Lodge plant is 2000 lb. of char per hour per retort. The by-product yield is 20 gallons per ton of coal. -
Technical Project Lead (TPL) Review: MR0000059-MR0000061
U.S. Food & Drug Administration f"~-,, 11 U.S. FOOD & DRUG 10903 New Hampshire Avenue ~,./- ADM I N I STRATI ON Silver Spring, MD 20993 www.fda.gov Scientific Review of Modified Risk Tobacco Product Application (MRTPA) Under Section 911(d) of the FD&C Act -Technical Project Lead SUBMISSION INFORMATION Applicant Philip Morris Product s S.A. Product Manufacturer Philip Morris Product s S.A. Submission Date November 18, 2016 I FDA Receipt Date I December 5, 2016 Purpose ~ Risk Modificat ion (91l (g)( l )) order ~ Exposure Modification (9ll(g)(2)) order Proposed Modified Risk Modified Risk Claim #1: Claims " AVAILABLE EVIDENCE TO DATE: • The IQOS system heats t obacco but does not burn it. • This significantly reduces the production of harmful and pot entially harmful chemica ls. • Scientific studies have shown that sw itching completely from conventional cigarettes t o the IQOS syst em can reduce the risks of tobacco-related diseases." Modified Risk Claim #2: " AVAILABLE EVIDENCE TO DATE: • Swit ching complet ely to IQOS present s less risk of harm than continuing t o smoke cigarett es." Modified Risk Claim #3: " AVAILABLE EVIDENCE TO DATE: • The IQOS system heats tobacco but does not burn it. • This significant ly reduces the production of harmful and pot entially harmful chemica ls. • Scientific studies have show n that switching completely from conventional cigarettes t o the IQOS syst em significantly reduces your body's exposure t o harmful or pot entially harmful chemicals." PROPOSED MODIFIED RISK TOBACCO PRODUCT (SINGLE PRODUCTS} MR0000059: Marlboro Heatsticks1 Product Category Cigarettes Product Sub-Category Non-Combusted Package Type Box Package Quantity 20 Heat sticks Characterizing Flavor None Length 45 mm Diameter 7.42 mm 1 M ay be sold individually or as a co-packaged product . -
Pyrolysis of Char Forming Solid Fuels: a Critical Review of the Mathematical Modelling Techniques
Proceedings, 5th AOSFST, Newcastle, Australia, 2001 Editors: M.A. Delichatsios, B.Z. Dlugogorski and E.M. Kennedy PYROLYSIS OF CHAR FORMING SOLID FUELS: A CRITICAL REVIEW OF THE MATHEMATICAL MODELLING TECHNIQUES B. Moghtaderi Department of Chemical Engineering, The University of Newcastle AUSTRALIA ABSTRACT Recent advances in mathematical modelling and numerical analysis of the pyrolysis of char forming solid fuels have shed new light on the pyrolytic behaviour of these materials under fire conditions. A review of the pyrolysis models of charring solid fuels developed over the past 30 years is presented in the order of increasing complexity. The models can be broadly categorised into thermal and comprehensive type models. While thermal models predict the conversion of the virgin fuel into products based on a critical pyrolysis criterion and the energy balance, the comprehensive models describe the degradation of the fuel by a chemical kinetic scheme coupled with the conservation equations for the transport of heat and/or mass. A variety of kinetic schemes have been reported in the literature ranging from simple one-step global reactions to semi-global and multi-step reaction mechanisms. There has been much less uniformity in the description of the transport phenomena (i.e. heat and mass) in comprehensive models and different levels of approximation have been used. It is shown that the accuracy of pyrolysis models largely depends on the model parameters. If reliable data are not available, even the most advanced models give poor predictions. Keywords: Pyrolysis, charring solid fuels, mathematical modelling, fires. INTRODUCTION Pyrolysis of solid fuels plays an important role in both the ignition and growth stages of fires. -
Charring of Wood Based Materials
Charring of Wood Based Materials ESKO MIKKOLA VTT-Technical Research Centre of Finland Fire Technology Laboratory SF-02151 Espoo. Finland O:1arring rate of wood is affected by density and rroisture content of wood, external heat flux and oxygen concentration of the surrounding air. A simplified rrodel for charring of wood is presented as v;ell as exper:irra1tal charring rate results for some thennally thick wood species and wood products. The charring rrodel can be used to calculate with ease and comparatively high accuracy relative changes in charring rate when any of the parameters describing the naterial or the surrounding conditions changes. Also the in practice iInportant effect of rroisture is taken into account in the calculations. Results given by the model, are in good agree ment with experimental data. :KEYW:)RDS: charring rate, wood, moisture, cone calorimeter INI'ROI:UCI'ION Wood is quite easily ignitible and a lot of energy is released in wood combustion. 'Ihese properties can be utilized in many ways, but they cause problems in the case of unwanted fire. It is essential that time to ignition, rate of heat release and charring rate are known for fire safety of wood structures. Also, the load bearing capacity of a wooden structural element is dependent on the charring rate, because the load bearing capacity of cross-sections depends on charring depth. '!his study contains results of charring studies made with a cone calorimeter. Experimental charring rate results are compared with the simple charring rrodel, which provides a straight forward means for evaluat ing the influence of different parameters on the charring rate. -
Combustion and Gasification Characteristics of Chars from Raw and Torrefied Biomass E
Combustion and gasification characteristics of chars from raw and torrefied biomass E. M. Fisher, Celine Dupont, L. I. Darvell, Jean-Michel Commandre, A. Saddawi, J. M. Jones, M. Grateau, T. Nocquet, Sylvain Salvador To cite this version: E. M. Fisher, Celine Dupont, L. I. Darvell, Jean-Michel Commandre, A. Saddawi, et al.. Combustion and gasification characteristics of chars from raw and torrefied biomass. Bioresource Technology, Elsevier, 2012, 119, pp.157-165. 10.1016/j.biortech.2012.05.109. hal-01688420 HAL Id: hal-01688420 https://hal.archives-ouvertes.fr/hal-01688420 Submitted on 16 Mar 2018 HAL is a multi-disciplinary open access L’archive ouverte pluridisciplinaire HAL, est archive for the deposit and dissemination of sci- destinée au dépôt et à la diffusion de documents entific research documents, whether they are pub- scientifiques de niveau recherche, publiés ou non, lished or not. The documents may come from émanant des établissements d’enseignement et de teaching and research institutions in France or recherche français ou étrangers, des laboratoires abroad, or from public or private research centers. publics ou privés. Combustion and gasification characteristics of chars from raw and torrefied biomass a, b c d c c b E.M. Fisher ⇑, C. Dupont , L.I. Darvell , J.-M. Commandré , A. Saddawi , J.M. Jones , M. Grateau , T. Nocquet b, S. Salvador e a Sibley School of Mechanical and Aerospace Engineering, Upson Hall, Cornell University, Ithaca, NY 14853, USA b Commissariat à l’Energie Atomique et aux Energies Alternatives, LITEN/DTBH/LTB, Grenoble, France c School of Process, Environmental and Materials Engineering, University of Leeds, Leeds, LS2 9JT, UK d CIRAD, UPR 42 Biomasse Energie, Montpellier, France e Université de Toulouse, MINES ALBI, RAPSODEE, FRE CNRS 3213, Campus Jarlard, route de Teillet, 81013 ALBI CT CEDEX 09, France Keywords: abstract Torrefaction Oxidation Torrefaction is a mild thermal pretreatment (T < 300 °C) that improves biomass milling and storage prop- Gasification Biomass erties. -
Review of Information Related to the Charring Rate of Wood
United States Department of Agriculture Review of Forest Service Forest Information Products Laboratory Related to the Research Note FPL-0145 Issued 1966 Charring Rate of Wood Slightly Revised 1980 SUMMARY Buildings constructed with heavy timber for posts, beak, girders, and flooring have often proven themselves fire resistant because of the slow rate of charring and loss of strength of wood under fire exposure. However, much of the information relating to fire endurance of such construction is empirical in nature. To remain competitive with other construction materials more precise data should be obtained upon which to design and predict fire endur ance of wood assemblies. A long-range program to obtain these data is proposed as part of the fire research studies at the U.S. Forest Products Laboratory. A research program was established in cooperation with the National Forest Products Association to determine the charring rates for wood and the effect of temperature, species, density, moisture content, and grain direction on these rates. The literature review presented here was made as an initial part of that study. Information is summarized on the mechanism of thermal degrada tion of wood, properties affecting rate of char, models and measured rates of char development, and heat liberation during combustion of wood. Related studies on the mechanism of thermal degradation of plastic polymers and analytical degradation models are also summarized. Contents Page Nomenclature . ii Subscripts . iv Introduction . 1 Studies on Degradation of Wood to Char . 2 Mechanism of Degradation to Char . 2 Comparative Char Resistance of Wood Species . 6 Models of Char Development . 6 Measured Rates of Char Development . -
Construction of Charring-Functional Polyheptanazine Towards Improvements in Flame Retardants of Polyurethane
molecules Article Construction of Charring-Functional Polyheptanazine towards Improvements in Flame Retardants of Polyurethane Shaolin Lu, Botao Shen and Xudong Chen * Key Laboratory for Polymeric Composite and Functional Materials of Ministry of Education, School of Chemistry, Sun Yat-sen University, Guangzhou 510275, China; [email protected] (S.L.); [email protected] (B.S.) * Correspondence: [email protected]; Tel.: +86-20-8411-3498 Abstract: Nitrogen-containing flame retardants have been extensively applied due to their low toxic- ity and smoke-suppression properties; however, their poor charring ability restricts their applications. Herein, a representative nitrogen-containing flame retardant, polyheptanazine, was investigated. Two novel, cost-effective phosphorus-doped polyheptazine (PCN) and cobalt-anchored PCN (Co@PCN) flame retardants were synthesized via a thermal condensation method. The X-ray photoelectron spectroscopy (XPS) results indicated effective doping of P into triazine. Then, flame-retardant parti- cles were introduced into thermoplastic polyurethane (TPU) using a melt-blending approach. The introduction of 3 wt% PCN and Co@PCN could remarkably suppress peak heat release rate (pHRR) (48.5% and 40.0%), peak smoke production rate (pSPR) (25.5% and 21.8%), and increasing residues (10.18 wt%!17.04 wt% and 14.08 wt%). Improvements in charring stability and flame retardancy were ascribed to the formation of P–N bonds and P=N bonds in triazine rings, which promoted the retention of P in the condensed phase, which produced additional high-quality residues. Keywords: flame retardants; thermoplastic polyurethane; phosphorous doped; polyheptanazine; thermal decomposition Citation: Lu, S.; Shen, B.; Chen, X. Construction of Charring-Functional Polyheptanazine towards 1. -
Development of Pyrolysis Models for Charring Polymers Jing Li University of New Haven, [email protected]
University of New Haven Digital Commons @ New Haven Fire Science and Professional Studies Faculty Fire Science and Professional Studies Publications 5-2015 Development of Pyrolysis Models for Charring Polymers Jing Li University of New Haven, [email protected] Junhui Gong Nanjing University of Information Science and Technology Stanislav I. Stoliarov University of Maryland - College Park Follow this and additional works at: http://digitalcommons.newhaven.edu/firescience-facpubs Part of the Emergency and Disaster Management Commons Publisher Citation Li, J., J. Gong and S. I. Stoliarov (2015). "Development of pyrolysis models for charring polymers." Polymer Degradation and Stability, Volume 115, May 2015, Pages 138-152. Comments This is the author's accepted version of the article published in Polymer Degradation and Stability. The final version can be accessed via http://dx.doi.org/10.1016/j.polymdegradstab.2015.03.003 Development of Pyrolysis Models for Charring Polymers Jing Lia,b, Junhui Gongc and Stanislav I. Stoliarov*,a aUniversity of Maryland, Department of Fire Protection Engineering, College Park, MD 20742, United States bUniversity of New Haven, Department of Fire Science, West Haven, CT 06516, United States cNanjing University of Technology, College of Urban Construction and Safety Engineering, Nanjing 210009, China Accepted by PDST (http://www.sciencedirect.com/science/article/pii/S0141391015000671) Abstract Controlled atmosphere, radiation-driven gasification experiments were conducted on a series of synthetic polymers including poly(acrylonitrile butadiene styrene), poly(ethylene terephthalate), poly(methyl methacrylate)-poly(vinyl chloride) alloy (Kydex) and polyetherimide. Mass loss rate and non-radiated surface temperature of coupon-sized material samples were measured simultaneously and recorded as a function of time. -
Biochar Characterization and Engineering Catherine Elizabeth Brewer Iowa State University
Iowa State University Capstones, Theses and Graduate Theses and Dissertations Dissertations 2012 Biochar characterization and engineering Catherine Elizabeth Brewer Iowa State University Follow this and additional works at: https://lib.dr.iastate.edu/etd Part of the Analytical Chemistry Commons, Chemical Engineering Commons, and the Soil Science Commons Recommended Citation Brewer, Catherine Elizabeth, "Biochar characterization and engineering" (2012). Graduate Theses and Dissertations. 12284. https://lib.dr.iastate.edu/etd/12284 This Dissertation is brought to you for free and open access by the Iowa State University Capstones, Theses and Dissertations at Iowa State University Digital Repository. It has been accepted for inclusion in Graduate Theses and Dissertations by an authorized administrator of Iowa State University Digital Repository. For more information, please contact [email protected]. Biochar characterization and engineering by Catherine Elizabeth Brewer A dissertation submitted to the graduate faculty in partial fulfillment of the requirements for the degree of DOCTOR OF PHILOSOPHY Co-Majors: Chemical Engineering; Biorenewable Resources and Technology Program of Study Committee: Robert C. Brown, Co-Major Professor David A. Laird, Co-Major Professor Thomas E. Loynachan Klaus Schmidt-Rohr Brent H. Shanks Dennis R. Vigil Iowa State University Ames, Iowa 2012 Copyright © Catherine Elizabeth Brewer, 2012. All rights reserved. ii DEDICATION I dedicate this dissertation in memory of my grandfather, GEORGE JACOB GUMM who received his high school diploma at the age of 75 after dropping out of high school to serve his country during World War II, and in honor of my grandmother, BETTY ANN HEIDEL GUMM who gave up a full scholarship to veterinary school to help take care of her family when her father died.