A Review of Active Noise and Vibration Control in Road Vehicles
Total Page:16
File Type:pdf, Size:1020Kb
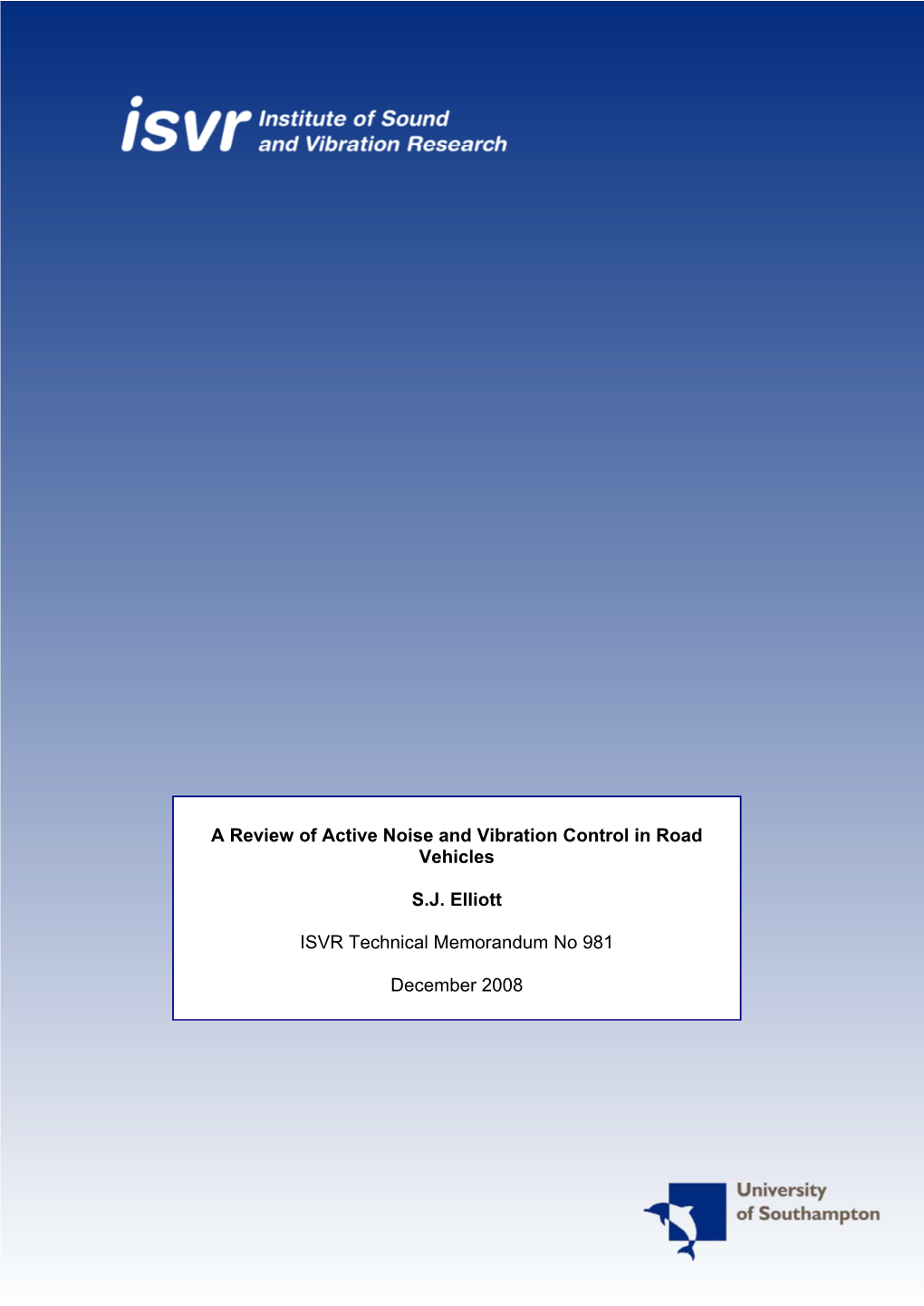
Load more
Recommended publications
-
Active Vibration Isolation Technology
COMPENDIUM Principles of Halcyonics Active Vibration Isolation Technology INTRODUCTION Vibrations accompany us everywhere and, in most cases, these vibrations are undesirable. Such disturbances can be caused by traffic, motors and machine tools, oil and gas platforms, buildings and other construction in seismic zones, undesirable locations of laboratory tables and experimental setups, etc. Modern technologies, e.g. in the area of high-resolution measurements, high-precision manufacturing processes, and super lightweight constructions, require effective anti-vibration solutions to achieve maximum performance. In all these cases, objects require isolation from the sources of vibration. This is particularly true for experiments or processes where the typical amplitudes of the ambient vibration and the dimensions of investigated or manufactured structures fall in the same range. Despite of all the constructional differences, the essence of vibration Figure 1: Comparison of passive and active damping systems. isolation systems is identical. The passive vibration isolation system The comparison reveals the complete absence of resonance in the active damping treatment. consists of a spring and damper (dash-pot). The spring is intended to soften vibrations and disturbances, and the damper has to terminate the oscillation which is amplified within the system. The combination of a mass and the spring is known as a mechanical low-pass. The mechanical response of the spring-mass system decreases significantly for frequencies above the resonance frequency, and the damper reduces the vibration amplitude especially within the resonance range. Because of the low-pass characteristic, passive damping systems are designed with very low resonance frequencies. Since pneumatic springs are characterized by low stiffness and high damping, most anti-vibration mountings available are pneumatic systems. -
Preview Feedforward Control for Active Vibration Damping of a Hybrid Suspension System
Technische Universität München Fakultät für Maschinenwesen Preview Feedforward Control for Active Vibration Damping of a Hybrid Suspension System Johannes N. Strohm Vollständiger Abdruck der von der Fakultät für Maschinenwesen der Technischen Universität München zur Erlangung des akademischen Grades eines Doktor-Ingenieurs genehmigten Dissertation. Vorsitzender: Prof. Dr. phil. Klaus Bengler Prüfer der Dissertation: 1. Prof. Dr.-Ing. habil. Boris Lohmann 2. Prof. Dr.-Ing. Ansgar Trächtler Die Dissertation wurde am 06.04.2020 bei der Technischen Universität München eingereicht und durch die Fakultät für Maschinenwesen am 10.11.2020 angenommen. “So ist die den Akt der Objektivierung abschließende Regelungstechnik die methodis- che Vollendung der Technik.” Denkschrift zur Gründung eines Insitutes für Regelungstechnik, Prof. Dr. Phil. Hermann Schmidt, Deutschlands erster ordentlicher Professor für Regelungstechnik, 1941 Hence, automatic control, which completes the act of objectification, is the methodical perfection of technology. Memorandum on the foundation of an institute for automatic control, Prof. Dr. Phil. Hermann Schmidt, Germany’s first full professor for automatic control, 1941 Abstract The question of how to increase driving comfort in road vehicles was already asked centuries ago. Back then, mechanical and later hydraulic solutions were found. In recent decades semi-active and active suspensions have been introduced, which alter their behavior during the ride. With those arose the need for suitable control laws. In this thesis the focus is set on preview feedforward controllers for vibration damping of a quarter car. Assuming that environmental sensors in autonomous cars can also detect road irregularities, the road profile in front of the vehicle is considered to be known. To exploit this information, various feedforward controllers are proposed. -
Seismic Isolation Strategies for Earthquake-Resistant Construction
Seismic Isolation Strategies for Earthquake-Resistant Construction Seismic Isolation Strategies for Earthquake-Resistant Construction: Emerging Opportunities By Mikayel Melkumyan Seismic Isolation Strategies for Earthquake-Resistant Construction: Emerging Opportunities By Mikayel Melkumyan This book first published 2019 Cambridge Scholars Publishing Lady Stephenson Library, Newcastle upon Tyne, NE6 2PA, UK British Library Cataloguing in Publication Data A catalogue record for this book is available from the British Library Copyright © 2019 by Mikayel Melkumyan All rights for this book reserved. No part of this book may be reproduced, stored in a retrieval system, or transmitted, in any form or by any means, electronic, mechanical, photocopying, recording or otherwise, without the prior permission of the copyright owner. ISBN (10): 1-5275-1802-7 ISBN (13): 978-1-5275-1802-5 TABLE OF CONTENTS Chapter One ................................................................................................. 1 Introduction Chapter Two ................................................................................................ 9 Concepts of Dampers for the Earthquake Protection of Existing Buildings and for Displacement Restraints in Seismically Isolated Buildings 2.1. Study of the Efficiency of Tuned Single and Double Mass Dampers on a Model of a Frame Building under Vibration Tests ................... 9 2.2. Theoretical Background: Linear and Non-Linear Analyses of a Building with and without a TMD ........................................... 20 2.3. Justification of the Transition from the Concept of Flexible Upper Floor to the Concept of Isolated Upper Floor Acting as a TMD ... 31 2.4. Structural Concept of the Series 111 Nine-Storey R/C Frame Apartment Building and the Formation of its Dynamic Design Model ............................................................................................. 34 2.5. Structural Concept of an AIUF and the Non-Linear Seismic Response Analysis of a Building Protected by an AIUF ............... -
Recent Advances in Active Noise and Vibration Control
Recent advances in active noise and vibration control Thilo Bein, Sven Herold, Dirk Mayer Fraunhofer LBF, Division Adaptronics, Darmstadt, Germany. Summary Noise is a serious form of environmental pollution believed to affect the lives of some 100 million European citizens. The cost of the associated damage is estimated at more than ten billion euros per year. Noise leads to serious health problems, limits the capability to learn, and effects the oc- cupants’ comfort and performance in buildings, in vehicles or at work. For instance, the automo- tive industry is more and more facing the problem of reducing the weight of the vehicle but guar- anteeing an equivalent level of comfort in terms of noise, vibration, and harshness (NVH). Im- provement of vehicle noise and vibration without affecting other performances is proving to be ex- tremely difficult if not impossible with state-of-the-art technology. Thus, active or smart concepts are being increasingly considered for the NVH optimization of vehicles besides advanced passive material systems. Within the LOEWE-Center AdRIA (Adaptronics – Research, Innovation, Application), a large in- terdisciplinary research project funded by the German federal state Hessen, and at the Fraunhofer LBF advanced noise and vibration abatement concepts were being developed and demonstrated. Among others, NVH abatement in vehicles and noise abatement in buildings is being considered. As underlying principle for noise reduction concepts, active structural acoustic control (ASAC) is primarily being considered for controlling the structural vibration of the sound radiating structure or by controlling the structure borne sound path. This paper will present an overview of the most recent concepts and results of the LOEWE-Center AdRIA such as active vibration control at en- gine mounts and smart windows. -
Earthquakes: Isolation, Energy Dissipation and Control of Vibrations
IAEA-TECDOC-819 Earthquakes: Isolation, energy dissipation and control vibrationsof structuresof for nuclear industrialand facilities and buildings Overview of lectures and papers of a seminar organized jointly withthe Italian Working Group on Seismic Isolation (GLIS) held Capri,and in Italy, 23-25 August 1993 INTERNATIONAL ATOMIC ENERGY AGENCY The IAEA doe t normallsno y maintain stock f reportsso thin i s series. However, microfiche copies of these reports can be obtained from IN IS Clearinghouse International Atomic Energy Agency Wagramerstrasse 5 0 10 P.Ox Bo . A-1400 Vienna, Austria Orders should be accompanied by prepayment of Austrian Schillings 100,- in the form of a cheque or in the form of IAEA microfiche service coupons orderee whicb y hdma separatel ClearinghouseS y MI froI e mth . The originating Section of this publication in the IAEA was: Nuclear Power Technology Development Section International Atomic Energy Agency Wagramerstrasse 5 P.O. Box 100 A-1400 Vienna, Austria EARTHQUAKES: ISOLATION, ENERGY DISSIPATION AND CONTROL OF VIBRATIONS OF STRUCTURE NUCLEAR SFO INDUSTRIAD RAN L FACILITIE BUILDINGD SAN S IAEA, VIENNA, 1995 IAEA-TECDOC-819 ISSN 1011-4289 © IAEA, 1995 Printe IAEe th AustriAn i y d b a September 1995 FOREWORD Seismic isolation is one of the most significant seismic engineering developments in recent years. Researc developmentd han , together with application experienc especialle— y for numerous isolated civil structures alst existinr bu ,o fo g nuclear reactor facilitiesd san d ha , already shown in past years that this technique is extremely promising for a wide range of uses in the industrial field, in particular for advanced nuclear plants. -
Passive/Active Vibration Control of Flexible Structures
NORTHEASTERN UNIVERSITY Graduate School of Engineering Thesis Title: Passive/Active Vibration Control of Flexible Structures Author: Matthew Jamula Department: Mechanical and Industrial Engineering Approved for Thesis Requirement of the Master of Science Degree ______________________________________________ __________________ Thesis Adviser, Dr. Nader Jalili Date ______________________________________________ __________________ Thesis Reader, Dr. Rifat Sipahi Date ______________________________________________ __________________ Thesis Reader, Dr. Bahram Shafai Date ______________________________________________ __________________ Department Chair, Dr. Jacqueline Isaacs Date Graduate School Notified of Acceptance: ______________________________________________ __________________ Dr. Sara Wadia-Fascetti, Date Associate Dean of the Graduate School of Engineering 1 PASSIVE/ACTIVE VIBRATION CONTROL OF FLEXIBLE STRUCTURES A Thesis Presented by Matthew Thomas Jamula to The Department of Mechanical and Industrial Engineering in partial fulfillment of the requirements for the degree of Master of Science in Mechanical Engineering in the field of Mechanical Engineering Northeastern University Boston, Massachusetts April 2012 2 Abstract More advanced technology and materials in industry lead to the implementation of lightweight components in order for miniaturization and efficiency. Lightweight components and certain materials however, are susceptible to vibrations. The flexible structures that make up these systems pose a great problem for vibration control. The detailed modeling of such systems greatly reduces the complexity of the control law. It is this reason that an analysis of the model as a continuous system was done. The distributed-parameters system was then effectively reduced to an equivalent lumped-parameters model. The use of this discrete system was the basis for controller design of these flexible structures. However, even the best model of a system is not able to overcome the need of an advanced controller for vibration suppression. -
Adaptive Piezoelectric Absorber for Active Vibration Control
actuators Article Adaptive Piezoelectric Absorber for Active Vibration Control Sven Herold * and Dirk Mayer Fraunhofer Institute for Structural Durability and System Reliability LBF, Bartningstr. 47, 64823 Darmstadt, Germany; [email protected] * Correspondence: [email protected]; Tel.: +49-6151-705-259; Fax: +49-6151-705-388 Academic Editor: Kenji Uchino Received: 14 December 2015; Accepted: 15 February 2016; Published: 29 February 2016 Abstract: Passive vibration control solutions are often limited to working reliably at one design point. Especially applied to lightweight structures, which tend to have unwanted vibration, active vibration control approaches can outperform passive solutions. To generate dynamic forces in a narrow frequency band, passive single-degree-of-freedom oscillators are frequently used as vibration absorbers and neutralizers. In order to respond to changes in system properties and/or the frequency of excitation forces, in this work, adaptive vibration compensation by a tunable piezoelectric vibration absorber is investigated. A special design containing piezoelectric stack actuators is used to cover a large tuning range for the natural frequency of the adaptive vibration absorber, while also the utilization as an active dynamic inertial mass actuator for active control concepts is possible, which can help to implement a broadband vibration control system. An analytical model is set up to derive general design rules for the system. An absorber prototype is set up and validated experimentally for both use cases of an adaptive vibration absorber and inertial mass actuator. Finally, the adaptive vibration control system is installed and tested with a basic truss structure in the laboratory, using both the possibility to adjust the properties of the absorber and active control. -
Vibration Control of Mechanical Suspension System Using Active Force Control
CORE Metadata, citation and similar papers at core.ac.uk Provided by Universiti Teknologi Malaysia Institutional Repository Vibration Control of Mechanical Suspension System Using Active Force Control Maziah Mohamad, Musa Mailah, Abdul Halim Muhaimin Department of Applied Mechanics Faculty of Mechanical Engineering Universiti Teknologi Malaysia 81310 Skudai, Johor [email protected], [email protected], [email protected] Abstract: This paper presents the practical implementation of an active force control (AFC) strategy to a laboratory scaled vibration isolator platform. The research was carried out to investigate the performance of vibration suppression capability of feedback controller using AFC. Two types of controller schemes were examined and compared involving the classic proportional- integral-derivative (PID) controller and AFC scheme. The laboratory scaled physical rig was developed using the MATLAB/Simulink with Real Time Workshop (RTW) tool that is interfaced with a suitable data acquisition card via a personal computer (PC) as the main controller. Appropriate vibration source was modelled and applied to the proposed systems to test for the system robustness. Results obtained in this study verified the potential and superiority of the proposed AFC scheme as a robust active vibration suppressor compared to the other schemes considered in the study. Keywords: Vibration, suspension system, active force control, robust, real-time. 1. Introduction Vibration can be pleasant and useful as in massaging and therapeutic application but at the same time it can be unpleasant and harmful too because it can lead to catastrophic failures of components and materials. Unwanted vibration can interfere with our comfort, damage to structures, reduction of equipment performance and machinery noise level. -
MOOC QP Set 1 Principles of Vibration Control (TOTAL = 100 Marks)
Set-1 MOOC QP Set 1 Principles of Vibration Control (TOTAL = 100 marks) Section I : 20 questions x 1 mark/question = 20 marks Section II : 20 questions x 2 marks/question = 40 marks Section III : 8 questions x 5 marks/question = 40 marks Section I [20 Questions] - 1 marks/question 1. A Single degree of freedom system having stiffness 10 N/m and mass 2 kg is subjected to an excitation of 100 Hz, which parameter will be important for vibration control? • Change Elastic modulus of the material • Change stiffness of the material • Mass of the material • Damping of the material • Friction of the system 2. A tuned mass damper is to be designed for a primary system with stiffness 50 N/m and mass 10 kg, the spring attached with the tuned mass has stiffness 1000 N/m and the harmonic excitation force amplitude is 100 N, at perfectly tuned condition, the secondary mass displacement will be? • 0.02m • 2m • 0 • 0.1m • 1m 3. Damping is important for the following application • High Strength of Beams and Plates • Vibration Control of muffler • Fracture toughness of Aircraft Wing • Deflection control of Columns • Reaction Control of Piston Cylinders 4. A vibrating system is dissipating energy at the rate of 0.01 J per ten cycle. Maximum potential energy of the system is 10 J. The loss factor for the system is • 0.001 • 0.1 • 1.01 • 0.011 • 0.0001 Set-1 5. In a hysteretic damping system, the α is 3.14 x 10-2, the excitation frequency is 10 rad/sec the equivalent damping constant will be? • 10-3 • 0.01 • 3.14 • 31.4 • None of these 6. -
Active, Semi-Active and Hybrid Control of Structures
2834 ACTIVE, SEMI-ACTIVE AND HYBRID CONTROL OF STRUCTURES T T SOONG1 And B F SPENCER, JR2 SUMMARY In recent years, considerable attention has been paid to research and development of passive and active structural control devices, with particular emphasis on alleviation of wind and seismic response of buildings and bridges. In both areas, serious efforts have been undertaken to develop the structural control concept into a workable technology, and today we have many such devices installed in a wide variety of structures. The focus of this state-of-the-art paper is on active, semi-active and hybrid structural control with seismic applications. These systems employ controllable force devices integrated with sensors, controllers and real-time information processing. This paper includes a brief historical outline of their development and an assessment of the state-of-the-art and state-of-the-practice of this exciting, and still evolving, technology. Also included in the discussion are their advantages and limitations in the context of seismic design and retrofit of civil engineering structures. INTRODUCTION Active, semi-active and hybrid structural control systems are a natural evolution of passive control technologies such as base isolation and passive energy dissipation. The possible use of active control systems and some combinations of passive and active systems, so called hybrid systems, as a means of structural protection against wind and seismic loads has received considerable attention in recent years. Active/hybrid control systems are force delivery devices integrated with real-time processing evaluators/controllers and sensors within the structure. They act simultaneously with the hazardous excitation to provide enhanced structural behavior for improved service and safety. -
Active Noise Control, Applications of Smart Materials and Structures, As Well As the Modelling of Active Noise and Vibration Reduction Systems
Conference Organizers AGH University of Science and Technology Faculty of Mechanical Engineering and Robotics Department of Process Control Committee on Machine Building of the Polish Academy of Science 13th Conference on Active Noise and Vibration Control Methods MARDiH Proceedings Krakow – Kazimierz Dolny, Poland 12-14 June 2017 This publication contains the abstracts of the papers selected by the Scientific Board of the Conference on Active Noise and Vibration Control Methods Conference. Full papers, however, will be published in indexed scientific journals, after positive review. Editor: Marcin Apostoł - AGH University of Science and Technology Publisher: Department of Process Control AGH University of Science and Technology Printed by: DELTA Jarosław A. Jagła tel. +48 601 68 25 00 ISBN: 978-83-64755-08-8 Program committee: Chairman: Piotr Cupiał Honorary chairman: Janusz Kowal Members Jan Awrejcewicz Wiesław Ostachowicz Jerzy Bajkowski Marek Pawełczyk Stephen P. Banks Stanisław Pietrzko Wojciech Batko Delf Sachau Marian W. Dobry Bogdan Sapiński Stefan Domek Andrzej Seweryn Janusz Gołdasz Zbigniew Starczewski Zdzisław Gosiewski Jacek Snamina Colin Hansen Eugeniusz Świtoński Jan Holnicki-Szulc Ryszard Tadeusiewicz Krzysztof Kaliński Osman Tokhi Marek Książek Jiri Tuma Zi-Qiang Lang Andrzej Tylikowski Lucyna Leniowska Tadeusz Uhl Arkadiusz Mężyk Wiesław Wszołek Józef Nizioł Organizing committee: Chairman: Agata Nawrocka Members: Marcin Apostoł Roman Ornacki Stanisław Flaga Marcin Węgrzynowski Mateusz Kozioł Kamil Zając Preface Ladies and Gentlemen, Following more than 20 years’ tradition, we are meeting again at the Conference on Active Noise and Vibration Control Methods. Our aim is to present the results of recent research work, to exchange ideas and to share experience among the participants from research centres in Poland and abroad. -
Active Noise and Vibration Control - Smart Structures 98-001
" Active Noise and Vibration Control - Smart Structures 98-001 Active Noise and Vibration Control 1. Objectives 2. Background 1. Active Noise Control 2. Active Vibration Control (A VC) 3. Importance 4. Alternatives 5. Maturity and Risk 1. Maturity of Technology 1. Noise Cancellation Headsets (Commercial) 2. Active Muffler or Silencer (prototype) 3. Noise Reduction in Ducts (Commercial) 4. Vehicles (Developmental and Commercial) 5. Turboprop Aircraft (Developmental) 6. Transformers (Commercial) 7. Noise Reduction in Engines (Commercial) 8. Precision Machining (Developmental and Commercial) 9. Active Strut Member (Developmental) 10. Active Suspension (Developmental and Commercial) 11. Airframe Vibration Control (Developmental) 12. Flutter Control (Developmental) 6. Technological Risks 7. Availability 8. Breadth of Application 9. Cost-Benefit Analysis 10. References Page 1 Active Noise and Vibration Control- Smart Structures 98-001 Active Noise and Vibration Control 1. Objectives Active Noise and Vibration Systems have the following objectives: • To improve passenger comfort and crew effectiveness by reducing cabin and cockpit noise and vibration levels. Currently, pilot flying times are limited by exposure to noise and vibrations in turboprop and helicopter aircraft. Future workplace health and safety regulations will establish more rigid standards for exposure to cabin noise. • To increase the performance characteristics of commercial and military aircraft by reducing vibration levels. Operational performance, manoeuvrability and fuel efficiencies are expected to increase with active vibration control of aircraft structures which are exposed to high levels of turbulence and buffet loads creating wing flutter, acoustic resonance in open bomb bays, rotor resonances and fuselage vibrations. • To increase the lifetime of aircraft and improve component life cyclc costs by decreasing fatigue loading which is produced by noise and vibration.