Performance Analysis of a Miniature Joule–Thomson Cryocooler with and Without the Distributed J–T Effect
Total Page:16
File Type:pdf, Size:1020Kb
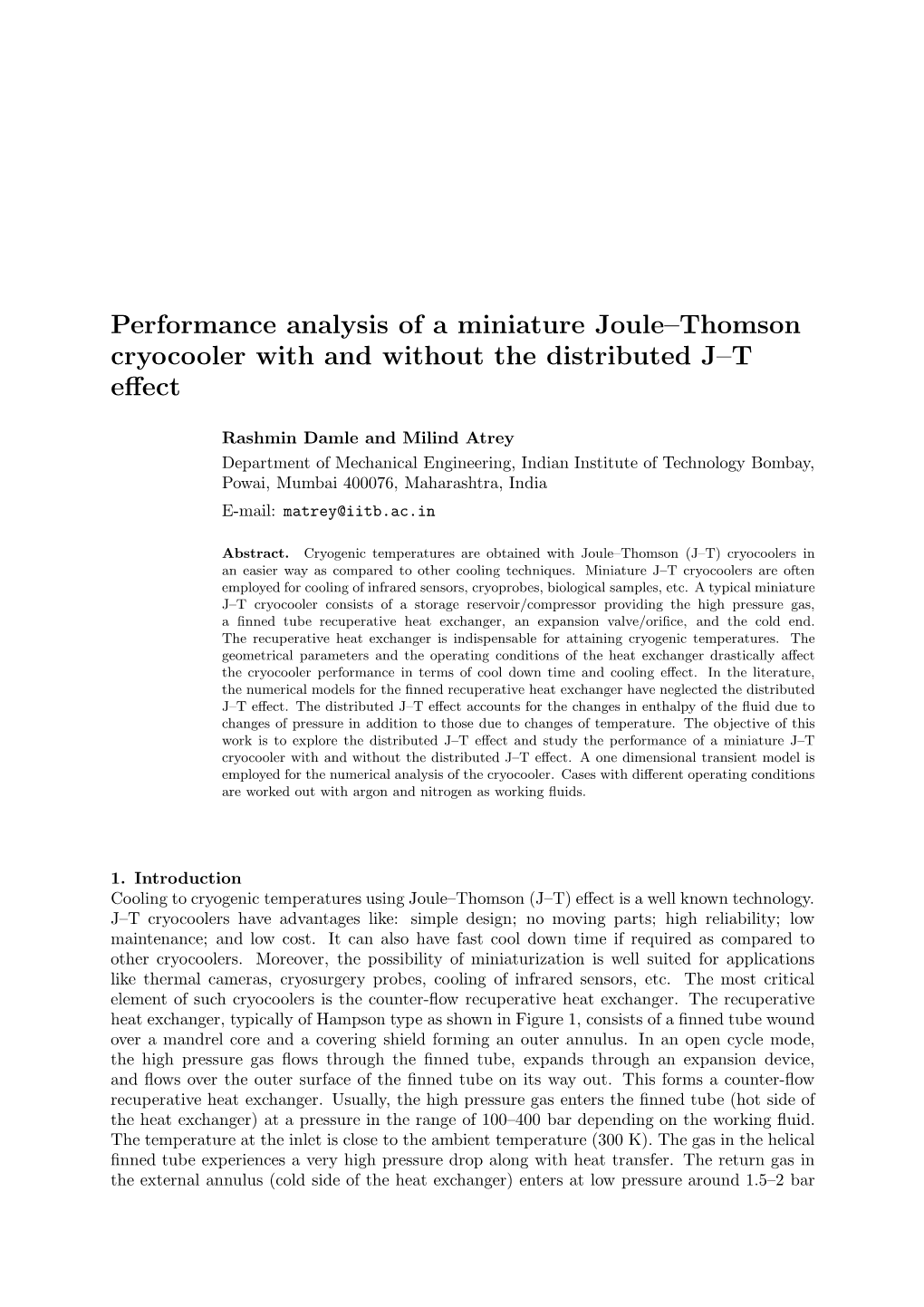
Load more
Recommended publications
-
Che 253M Experiment No. 2 COMPRESSIBLE GAS FLOW
Rev. 8/15 AD/GW ChE 253M Experiment No. 2 COMPRESSIBLE GAS FLOW The objective of this experiment is to familiarize the student with methods for measurement of compressible gas flow and to study gas flow under subsonic and supersonic flow conditions. The experiment is divided into three distinct parts: (1) Calibration and determination of the critical pressure ratio for a critical flow nozzle under supersonic flow conditions (2) Calculation of the discharge coefficient and Reynolds number for an orifice under subsonic (non- choked) flow conditions and (3) Determination of the orifice constants and mass discharge from a pressurized tank in a dynamic bleed down experiment under (choked) flow conditions. The experimental set up consists of a 100 psig air source branched into two manifolds: the first used for parts (1) and (2) and the second for part (3). The first manifold contains a critical flow nozzle, a NIST-calibrated in-line digital mass flow meter, and an orifice meter, all connected in series with copper piping. The second manifold contains a strain-gauge pressure transducer and a stainless steel tank, which can be pressurized and subsequently bled via a number of attached orifices. A number of NIST-calibrated digital hand held manometers are also used for measuring pressure in all 3 parts of this experiment. Assorted pressure regulators, manual valves, and pressure gauges are present on both manifolds and you are expected to familiarize yourself with the process flow, and know how to operate them to carry out the experiment. A process flow diagram plus handouts outlining the theory of operation of these devices are attached. -
Aspects of Flow for Current, Flow Rate Is Directly Proportional to Potential
Vacuum technology Aspects of flow For current, flow rate is directly proportional to potential difference and inversely proportional to resistance. I = V/R or I = V/R For a fluid flow, Q = (P1-P2)/R or P/R Using reciprocal of resistance, called conductance, we have, Q = C (P1-P2) There are two kinds of flow, volumetric flow and mass flow Volume flow rate, S = vA v – the average bulk velocity, A the cross sectional area S = V/t, V is the volume and t is the time. Mass flow rate is S x density. G = vA or V/t Mass flow rate is measured in units of throughput, such as torr.L/s Throughput = volume flow rate x pressure Throughput is equivalent to power. Torr.L/s (g/cm2)cm3/s g.cm/s J/s W It works out that, 1W = 7.5 torr.L/s Types of low 1. Laminar: Occurs when the ratio of mass flow to viscosity (Reynolds number) is low for a given diameter. This happens when Reynolds number is approximately below 2000. Q ~ P12-P22 2. Above 3000, flow becomes turbulent Q ~ (P12-P22)0.5 3. Choked flow occurs when there is a flow restriction between two pressure regions. Assume an orifice and the pressure difference between the two sections, such as 2:1. Assume that the pressure in the inlet chamber is constant. The flow relation is, Q ~ P1 4. Molecular flow: When pressure reduces, MFP becomes larger than the dimensions of the duct, collisions occur between the walls of the vessel. -
Mass Flow Rate and Isolation Characteristics of Injectors for Use with Self-Pressurizing Oxidizers in Hybrid Rockets
49th AIAA/ASME/SAE/ASEE Joint PropulsionConference AIAA 2013-3636 July 14 - 17, 2013, San Jose, CA Mass Flow Rate and Isolation Characteristics of Injectors for Use with Self-Pressurizing Oxidizers in Hybrid Rockets Benjamin S. Waxman*, Jonah E. Zimmerman†, Brian J. Cantwell‡ Stanford University, Stanford, CA 94305 and Gregory G. Zilliac§ NASA Ames Research Center, Moffet Field, CA 94035 Self-pressurizing rocket propellants are currently gaining popularity in the propulsion community, partic- ularly in hybrid rocket applications. Due to their high vapor pressure, these propellants can be driven out of a storage tank without the need for complicated pressurization systems or turbopumps, greatly minimizing the overall system complexity and mass. Nitrous oxide (N2O) is the most commonly used self pressurizing oxidizer in hybrid rockets because it has a vapor pressure of approximately 730 psi (5.03 MPa) at room temperature and is highly storable. However, it can be difficult to model the feed system with these propellants due to the presence of two-phase flow, especially in the injector. An experimental test apparatus was developed in order to study the performance of nitrous oxide injectors over a wide range of operating conditions. Mass flow rate characterization has been performed to determine the effects of injector geometry and propellant sub-cooling (pressurization). It has been shown that rounded and chamfered inlets provide nearly identical mass flow rate improvement in comparison to square edged orifices. A particular emphasis has been placed on identifying the critical flow regime, where the flow rate is independent of backpressure (similar to choking). For a simple orifice style injector, it has been demonstrated that critical flow occurs when the downstream pressure falls sufficiently below the vapor pressure, ensuring bulk vapor formation within the injector element. -
Physics 101: Lecture 18 Fluids II
PhysicsPhysics 101:101: LectureLecture 1818 FluidsFluids IIII Today’s lecture will cover Textbook Chapter 9 Physics 101: Lecture 18, Pg 1 ReviewReview StaticStatic FluidsFluids Pressure is force exerted by molecules “bouncing” off container P = F/A Gravity affects pressure P = P 0 + ρgd Archimedes’ principle: Buoyant force is “weight” of displaced fluid. F = ρ g V Today include moving fluids! A1v1 = A 2 v2 – continuity equation 2 2 P1+ρgy 1 + ½ ρv1 = P 2+ρgy 2 + ½ρv2 – Bernoulli’s equation Physics 101: Lecture 18, Pg 2 08 ArchimedesArchimedes ’’ PrinciplePrinciple Buoyant Force (F B) weight of fluid displaced FB = ρfluid Vdisplaced g Fg = mg = ρobject Vobject g object sinks if ρobject > ρfluid object floats if ρobject < ρfluid If object floats… FB = F g Therefore: ρfluid g Vdispl. = ρobject g Vobject Therefore: Vdispl./ Vobject = ρobject / ρfluid Physics 101: Lecture 18, Pg 3 10 PreflightPreflight 11 Suppose you float a large ice-cube in a glass of water, and that after you place the ice in the glass the level of the water is at the very brim. When the ice melts, the level of the water in the glass will: 1. Go up, causing the water to spill out of the glass. 2. Go down. 3. Stay the same. Physics 101: Lecture 18, Pg 4 12 PreflightPreflight 22 Which weighs more: 1. A large bathtub filled to the brim with water. 2. A large bathtub filled to the brim with water with a battle-ship floating in it. 3. They will weigh the same. Tub of water + ship Tub of water Overflowed water Physics 101: Lecture 18, Pg 5 15 ContinuityContinuity A four-lane highway merges down to a two-lane highway. -
THERMODYNAMICS, HEAT TRANSFER, and FLUID FLOW, Module 3 Fluid Flow Blank Fluid Flow TABLE of CONTENTS
Department of Energy Fundamentals Handbook THERMODYNAMICS, HEAT TRANSFER, AND FLUID FLOW, Module 3 Fluid Flow blank Fluid Flow TABLE OF CONTENTS TABLE OF CONTENTS LIST OF FIGURES .................................................. iv LIST OF TABLES ................................................... v REFERENCES ..................................................... vi OBJECTIVES ..................................................... vii CONTINUITY EQUATION ............................................ 1 Introduction .................................................. 1 Properties of Fluids ............................................. 2 Buoyancy .................................................... 2 Compressibility ................................................ 3 Relationship Between Depth and Pressure ............................. 3 Pascal’s Law .................................................. 7 Control Volume ............................................... 8 Volumetric Flow Rate ........................................... 9 Mass Flow Rate ............................................... 9 Conservation of Mass ........................................... 10 Steady-State Flow ............................................. 10 Continuity Equation ............................................ 11 Summary ................................................... 16 LAMINAR AND TURBULENT FLOW ................................... 17 Flow Regimes ................................................ 17 Laminar Flow ............................................... -
Introduction to Chemical Engineering Processes/Print Version
Introduction to Chemical Engineering Processes/Print Version From Wikibooks, the open-content textbooks collection Contents [hide ] • 1 Chapter 1: Prerequisites o 1.1 Consistency of units 1.1.1 Units of Common Physical Properties 1.1.2 SI (kg-m-s) System 1.1.2.1 Derived units from the SI system 1.1.3 CGS (cm-g-s) system 1.1.4 English system o 1.2 How to convert between units 1.2.1 Finding equivalences 1.2.2 Using the equivalences o 1.3 Dimensional analysis as a check on equations o 1.4 Chapter 1 Practice Problems • 2 Chapter 2: Elementary mass balances o 2.1 The "Black Box" approach to problem-solving 2.1.1 Conservation equations 2.1.2 Common assumptions on the conservation equation o 2.2 Conservation of mass o 2.3 Converting Information into Mass Flows - Introduction o 2.4 Volumetric Flow rates 2.4.1 Why they're useful 2.4.2 Limitations 2.4.3 How to convert volumetric flow rates to mass flow rates o 2.5 Velocities 2.5.1 Why they're useful 2.5.2 Limitations 2.5.3 How to convert velocity into mass flow rate o 2.6 Molar Flow Rates 2.6.1 Why they're useful 2.6.2 Limitations 2.6.3 How to Change from Molar Flow Rate to Mass Flow Rate o 2.7 A Typical Type of Problem o 2.8 Single Component in Multiple Processes: a Steam Process 2.8.1 Step 1: Draw a Flowchart 2.8.2 Step 2: Make sure your units are consistent 2.8.3 Step 3: Relate your variables 2.8.4 So you want to check your guess? Alright then read on. -
Dimensional Analysis and Modeling
cen72367_ch07.qxd 10/29/04 2:27 PM Page 269 CHAPTER DIMENSIONAL ANALYSIS 7 AND MODELING n this chapter, we first review the concepts of dimensions and units. We then review the fundamental principle of dimensional homogeneity, and OBJECTIVES Ishow how it is applied to equations in order to nondimensionalize them When you finish reading this chapter, you and to identify dimensionless groups. We discuss the concept of similarity should be able to between a model and a prototype. We also describe a powerful tool for engi- I Develop a better understanding neers and scientists called dimensional analysis, in which the combination of dimensions, units, and of dimensional variables, nondimensional variables, and dimensional con- dimensional homogeneity of equations stants into nondimensional parameters reduces the number of necessary I Understand the numerous independent parameters in a problem. We present a step-by-step method for benefits of dimensional analysis obtaining these nondimensional parameters, called the method of repeating I Know how to use the method of variables, which is based solely on the dimensions of the variables and con- repeating variables to identify stants. Finally, we apply this technique to several practical problems to illus- nondimensional parameters trate both its utility and its limitations. I Understand the concept of dynamic similarity and how to apply it to experimental modeling 269 cen72367_ch07.qxd 10/29/04 2:27 PM Page 270 270 FLUID MECHANICS Length 7–1 I DIMENSIONS AND UNITS 3.2 cm A dimension is a measure of a physical quantity (without numerical val- ues), while a unit is a way to assign a number to that dimension. -
Module 13: Critical Flow Phenomenon Joseph S. Miller, PE
Fundamentals of Nuclear Engineering Module 13: Critical Flow Phenomenon Joseph S. Miller, P.E. 1 2 Objectives: Previous Lectures described single and two-phase fluid flow in various systems. This lecture: 1. Describe Critical Flow – What is it 2. Describe Single Phase Critical Flow 3. Describe Two-Phase Critical Flow 4. Describe Situations Where Critical Flow is Important 5. Describe origins and use of Some Critical Flow Correlations 6. Describe Some Testing that has been Performed for break flow and system performance 3 Critical Flow Phenomenon 4 1. What is Critical Flow? • Envision 2 volumes at different pressures suddenly connected • Critical flow (“choked flow”) involves situation where fluid moves from higher pressure volume at speed limited only by speed of sound for fluid – such as LOCA • Various models exist to describe this limiting flow rate: • One-phase vapor, one phase liquid, subcooled flashing liquid, saturated flashing liquid, and two-phase conditions 5 2. Critical Single Phase Flow Three Examples will be given 1.Steam Flow 2.Ideal Gas 3.Incompressible Liquid 6 Critical Single Phase Flow - Steam • In single phase flow: sonic velocity a and critical mass flow are directly related: g v(P,T)2 a2 = c dv(P,T) dP S 2 g G = a2 ρ(P,T )2 = c crit dv(P,T ) dP S • Derivative term is total derivative of specific volume evaluated at constant entropy • Tabulated values of critical steam flow can be found in steam tables 7 Example Critical Steam Flow Calculation • Assume 2 in2 steam relief valve opens at 1000 psi • What is steam mass discharge rate? • Assume saturated system with Tsat = 544.61°F • f = 50.3 • Wcrit = f P A =(50.3lb-m/hr)(1000 psi)(2 in2) = 100,600 lb-m/hr = 27.94 lb-m/sec. -
Flow Measurement Using Hot-Film Anemometer
Flow basics Basics of Flow measurement using Hot-film anemometer Version 1.0 1/9 Flow basics Inhaltsverzeichnis: 1. Definitions 1.1. Air Velocity 1.2. Amount (of Gas) 1.3. Flow 1.3.1. Mass flow rate 1.3.2. Volumetric flow rate 1.3.3. Standard volumetric flow rate 2. Flow formulas 3. Flow measurements using E+E Hot-film anemometer Version 1.0 2/9 Flow basics 1. Definitions: 1.1. Air Velocity: Definition: „Air Velocity describes the distance an air molecule is moving during a certain time period “ Units: Name of unit shift Converted to SI - Unit m/s Meter per second m/s 1 m/s Kilometer per hour km/h 0,277778 m/s Centimeter per minute cm/min 1,666667 · 10-4m/s Centimeter per second cm/s 1 · 10-2 m/s Meter per minute m/min 1,66667 · 10-2 m/s Millimeter per minute mm/min 1,666667 · 10-5 m/s Millimeter per second mm/s 1 · 10-3 m/s Foot per hour ft/h, fph 8,466667 · 10-5 m/s Foot per minute ft/min, fpm 5,08 · 10-3 m/s Foot per second ft/s, fps 0,3048 m/s Furlong per fortnight furlong/fortnight 1,66309 · 10-4 m/s Inch per second in/s, ips 2,54000 · 1-2 m/s Knot kn, knot 0,514444 m/s Kyne cm/s 1 · 10-2 m/s Mile per year mpy 8,04327 · 10-13 m/s Mile (stat) per hour mph, mi/h 0,44704 m/s Mile (stat) per hour mi/min 26,8224 m/s Version 1.0 3/9 Flow basics 1.2. -
Momentum and Dimensional Analysis
Performance 5. More Aerodynamic Considerations There is an alternative way of looking at aerodynamic flow problems that is useful for understanding certain phenomena. Rather than tracking a particle of fluid, we can isolate a region of the fluid (called a control volume) and observe the effects of forces (of all kinds) on the fluid that is in that control volume. It should be noted that the fluid in the control volume is changing with time, as some enters and some leaves. (Sometime such problems are called variable mass problems because the mass in the control volume is changing). Again, for the purposes of this course it is convenient to restrict our attention to fluid flow through a stream tube or a duct of some sort, i.e. one-dimensional flow. To start, we will consider flow in a duct and divide it into two overlapping chunks of fluid. The initial chunk of fluid is the fluid that includes regions A and B and is observed at time t1. The second chunk of fluid contains the same fluid particles that have moved to a new position indicated by regions B and C. Hence the region B is common to both. We can now apply Newton’s second law to the same group of fluid particles. At time t1 the particles occupy region AB, and at time t2 the particles occupy region BC. We can write Newton’s laws regarding the change in momentum of the particles from time 1 to time 2: (1) If we designate ( ) my , Eq. (1) becomes: (2) or (3) We now focus on the region B. -
Dimensional Analysis and Modeling
cen72367_ch07.qxd 10/29/04 2:27 PM Page 269 CHAPTER DIMENSIONAL ANALYSIS 7 AND MODELING n this chapter, we first review the concepts of dimensions and units. We then review the fundamental principle of dimensional homogeneity, and OBJECTIVES Ishow how it is applied to equations in order to nondimensionalize them When you finish reading this chapter, you and to identify dimensionless groups. We discuss the concept of similarity should be able to between a model and a prototype. We also describe a powerful tool for engi- ■ Develop a better understanding neers and scientists called dimensional analysis, in which the combination of dimensions, units, and of dimensional variables, nondimensional variables, and dimensional con- dimensional homogeneity of equations stants into nondimensional parameters reduces the number of necessary ■ Understand the numerous independent parameters in a problem. We present a step-by-step method for benefits of dimensional analysis obtaining these nondimensional parameters, called the method of repeating ■ Know how to use the method of variables, which is based solely on the dimensions of the variables and con- repeating variables to identify stants. Finally, we apply this technique to several practical problems to illus- nondimensional parameters trate both its utility and its limitations. ■ Understand the concept of dynamic similarity and how to apply it to experimental modeling 269 cen72367_ch07.qxd 10/29/04 2:27 PM Page 270 270 FLUID MECHANICS Length 7–1 ■ DIMENSIONS AND UNITS 3.2 cm A dimension is a measure of a physical quantity (without numerical val- ues), while a unit is a way to assign a number to that dimension. -
Dimensional Analysis Autumn 2013
TOPIC T3: DIMENSIONAL ANALYSIS AUTUMN 2013 Objectives (1) Be able to determine the dimensions of physical quantities in terms of fundamental dimensions. (2) Understand the Principle of Dimensional Homogeneity and its use in checking equations and reducing physical problems. (3) Be able to carry out a formal dimensional analysis using Buckingham’s Pi Theorem. (4) Understand the requirements of physical modelling and its limitations. 1. What is dimensional analysis? 2. Dimensions 2.1 Dimensions and units 2.2 Primary dimensions 2.3 Dimensions of derived quantities 2.4 Working out dimensions 2.5 Alternative choices for primary dimensions 3. Formal procedure for dimensional analysis 3.1 Dimensional homogeneity 3.2 Buckingham’s Pi theorem 3.3 Applications 4. Physical modelling 4.1 Method 4.2 Incomplete similarity (“scale effects”) 4.3 Froude-number scaling 5. Non-dimensional groups in fluid mechanics References White (2011) – Chapter 5 Hamill (2011) – Chapter 10 Chadwick and Morfett (2013) – Chapter 11 Massey (2011) – Chapter 5 Hydraulics 2 T3-1 David Apsley 1. WHAT IS DIMENSIONAL ANALYSIS? Dimensional analysis is a means of simplifying a physical problem by appealing to dimensional homogeneity to reduce the number of relevant variables. It is particularly useful for: presenting and interpreting experimental data; attacking problems not amenable to a direct theoretical solution; checking equations; establishing the relative importance of particular physical phenomena; physical modelling. Example. The drag force F per unit length on a long smooth cylinder is a function of air speed U, density ρ, diameter D and viscosity μ. However, instead of having to draw hundreds of graphs portraying its variation with all combinations of these parameters, dimensional analysis tells us that the problem can be reduced to a single dimensionless relationship cD f (Re) where cD is the drag coefficient and Re is the Reynolds number.