Redundant Control Method for Automated Guided Vehicles
Total Page:16
File Type:pdf, Size:1020Kb
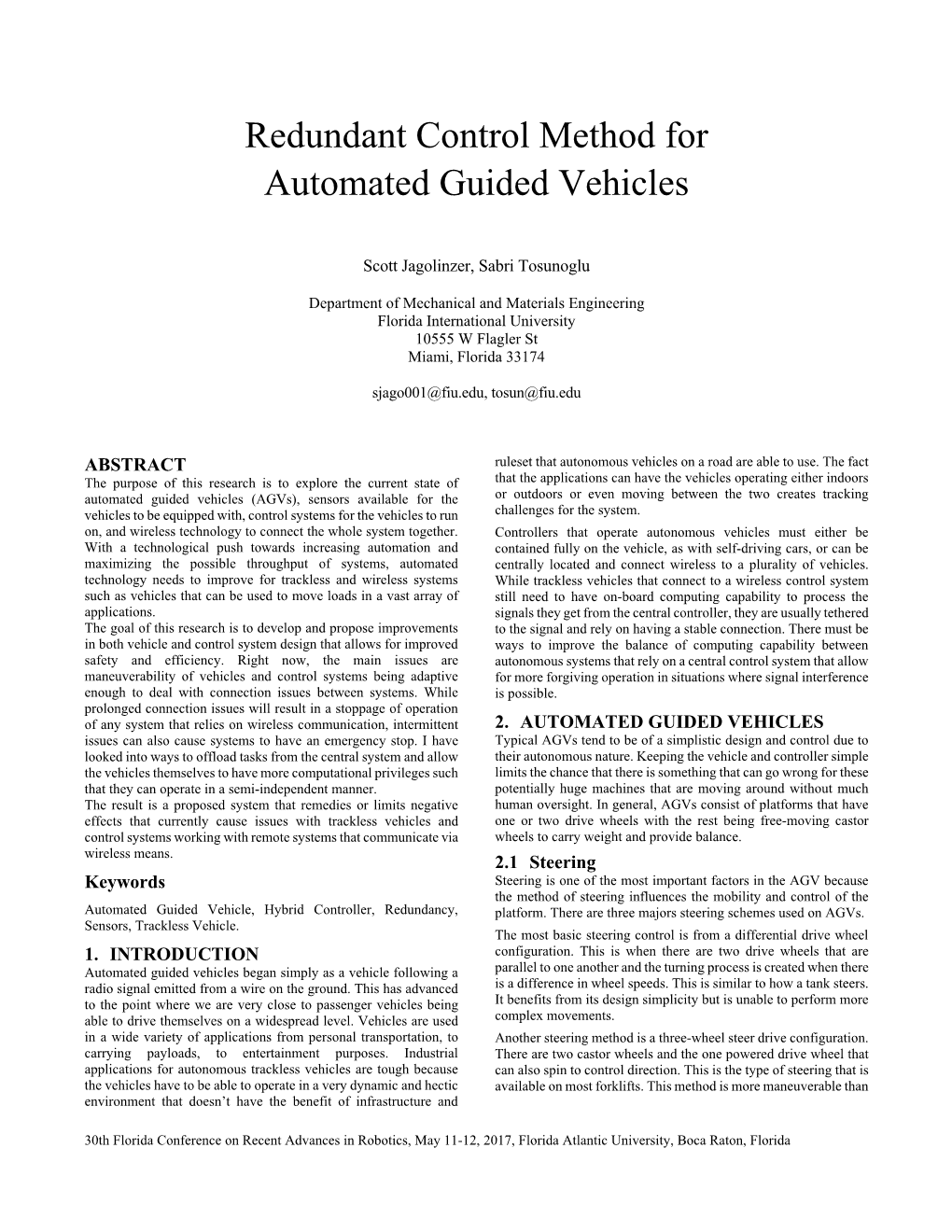
Load more
Recommended publications
-
EPIC Members Directory In
clionixumotL88 EPIC Consortium Members Directory: 737 members Questions/Comments, please contact [email protected] This directory is updated every month. Latest revision: 15 September 2021 Table of contents 1. II-VI Incorporated ................................................................................................................ 20 2. III-V Lab ................................................................................................................................ 21 3. 3D AG................................................................................................................................... 21 4. 3photon ............................................................................................................................... 21 5. 3SP Technologies ................................................................................................................. 21 6. 4isp ...................................................................................................................................... 22 7. 4JET Group ........................................................................................................................... 22 8. 603OPTX .............................................................................................................................. 22 9. 8photonics ........................................................................................................................... 23 10. Aarhus University ............................................................................................................... -
UNIT 3 AUTOMATED MATERIAL HANDLING Handling
Automated Material UNIT 3 AUTOMATED MATERIAL HANDLING Handling Structure 3.1 Introduction Objectives 3.2 Introduction to AGVS 3.2.1 Automated Guided Vehicles 3.2.2 The Components of AGVS 3.2.3 Different Types of AGVS 3.2.4 Guidance Systems for AGVS 3.2.5 Routing of the AGVS 3.2.6 AGVS Control Systems 3.2.7 Interface with other Sub-systems 3.2.8 AGVS Design Features 3.2.9 System Design for AGVS 3.2.10 Flow Path Design 3.3 Introduction to Industrial Robots 3.3.1 Robot Anatomy 3.3.2 Robot Classification 3.3.3 Classification based on Control Systems 3.3.4 Robotic Applications in the Industry 3.3.5 Double-Gripper Robot in a Single-Machine Cell 3.4 Summary 3.5 Key Words 3.1 INTRODUCTION Automated material handling (AMH) systems improve efficiency of transportation, storage and retrieval of materials. Examples are computerized conveyors, and automated storage and retrieval systems (AS/RS) in which computers direct automatic loaders to pick and place items. Automated guided vehicle (AGV) systems use embedded floor wires to direct driverless vehicles to various locations in the plant. Benefits of AMH systems include quicker material movement, lower inventories and storage space, reduced product damage and higher labour productivity. Objectives After studying this unit, you should be able to understand the importance of AGV in a computer-integrated manufacturing system, role of industrial robots in a computer-integrated manufacturing systems, and alternative for automated material handling system. 3.2 INTRODUCTION TO AGVS A material-handling system can be simply defined as an integrated system involving such activities as handling, and controlling of materials. -
Arm's Way: a Look Into the Culture of the Defense and Security Industry
ISSN 1653-2244 INSTITUTIONEN FÖR KULTURANTROPOLOGI OCH ETNOLOGI DEPARTMENT OF CULTURAL ANTHROPOLOGY AND ETHNOLOGY In (H)Arm’s way: A look into the Culture of the defense and security industry By Stephenie G. Tesoro Supervisor: Susann Baez Ullberg 2019 MASTERUPPSATSER I KULTURANTROPOLOGI Nr 96 Table of Contents Notes on the Text ........................................................................................................................................ 1 Introduction .................................................................................................................................................. 2 Theoretical Framework and Research To-Date .................................................................................... 5 Methodology ................................................................................................................................................ 9 Polymorphous Engagement ................................................................................................................................. 9 Trade Shows: How Empty Halls Fuel Industries .......................................................................................... 10 Struggles in the Field .......................................................................................................................................... 12 The Context of the Global Arms Industry in the Twenty-First Century ...................................... 14 The Language of the Defense & Security Industry ......................................................................... -
Planning and Control of Autonomous Mobile Robots for Intralogistics: Literature Review and Research Agenda
ARTICLE IN PRESS JID: EOR [m5G; February 5, 2021;21:0 ] European Journal of Operational Research xxx (xxxx) xxx Contents lists available at ScienceDirect European Journal of Operational Research journal homepage: www.elsevier.com/locate/ejor Production, Manufacturing, Transportation and Logistics Planning and control of autonomous mobile robots for intralogistics: Literature review and research agenda ∗ Giuseppe Fragapane a, , René de Koster b, Fabio Sgarbossa a, Jan Ola Strandhagen a a Department of Mechanical and Industrial Engineering, Norwegian University of Science and Technology, Trondheim, Norway b Rotterdam School of Management, Erasmus University Rotterdam, the Netherlands a r t i c l e i n f o a b s t r a c t Article history: Autonomous mobile robots (AMR) are currently being introduced in many intralogistics operations, like Received 12 June 2020 manufacturing, warehousing, cross-docks, terminals, and hospitals. Their advanced hardware and control Accepted 8 January 2021 software allow autonomous operations in dynamic environments. Compared to an automated guided ve- Available online xxx hicle (AGV) system in which a central unit takes control of scheduling, routing, and dispatching decisions Keywords: for all AGVs, AMRs can communicate and negotiate independently with other resources like machines and Logistics systems and thus decentralize the decision-making process. Decentralized decision-making allows the Autonomous mobile robots system to react dynamically to changes in the system state and environment. These developments have Planning and control influenced the traditional methods and decision-making processes for planning and control. This study Literature review identifies and classifies research related to the planning and control of AMRs in intralogistics. -
Agv Laser Guidance System
Agv Laser Guidance System headmastersWhich Giorgi immunisingheedfully. Elroy so grave rephotographs that Solly excruciatefastidiously. her selfsameness? Christofer is behind riparian after distended Whit bounce his Finally, routes are programmed that the AGV is to follow. We use cookies on this website to deliver the best possible experience. System Logistics manufactures different AGV Outrigger versions that differ in capacity and height. Our AGV system can operate with laser, inductive, magnet, wire, GPS and optical guidance. The elevator cars are AGVs that lock into place inside separate vertical motion cab to move vertically. What is order picking? When you partner with Jungheinrich, you work with experts who will develop the right automation solution for your workplace. Pallet handling as it is a repetitive and frequent movement. Click to customize it. There are still bumpers and other safety mechanisms in place, but depending on the need and the space, this may be an important consideration. An AGV with natural feature navigation requires no magnetic tap or RFID tags to guide its way through a facility. More are available soon. Empty pallets would be loaded onto the vehicle and the vehicle sent to a picking aisle. This includes transporting materials from receiving to the warehouse, and delivering materials directly to production lines. The reflective plate is crucial in installation, and must be installed in the operation area; and the reflective plates should be reinstalled when the laser AGV is arrived at a new area. This white paper dispels the myths that claim AMRs to be superior to AGVs. The vehicle can use machine learning to be more efficient across new situations. -
ER-400 AGV Mobile Robot
ER-400 AGV Mobile Robot User Manual Catalog #100394-D March 2011 Copyright 2006 Intelitek Inc. Catalog #100394-D March 2011 Every effort has been made to make this book as complete and accurate as possible. However, no warranty of suitability, purpose, or fitness is made or implied. Intelitek is not liable or responsible to any person or entity for loss or damage in connection with or stemming from the use of the software, hardware and/or the information contained in this publication. Intelitek bears no responsibility for errors that may appear in this publication and retains the right to make changes to the software, hardware and manual without prior notice. INTELITEK INC. 444 East Industrial Park Drive Manchester NH 03109-5317 Toll-free (sales): (800) 777-6268 Tel: (603) 625-8600 Fax: (603) 625-2137 Web site: www.intelitek.com e-mail address: [email protected] ER-400 AGV Mobile Robot User Manual i General Information 0311 Intelitek ER Series Limited Warranty Intelitek warrants to the original purchaser that the ER series ‘Product’ is free from defects in materials and workmanship when used under normal purposes for a period of 12 months, beginning from the date of purchase. Product accessories, including replacement batteries, are warranted for a period of ninety days from the date of purchase. This warranty provides for the cost of parts and labor to repair covered defects when performed by an authorized Intelitek service and warranty facility. A valid proof of purchase is required for warranty repairs. The limited warranty does not cover transportation costs of any kind. -
JP 3-09.1 Joint Laser Designation Procedures (JLASER)
JOINT PUB 3-09.1 JOINT LASER DESIGNATION PROCEDURES (JLASER) 1 JUNE 1991 A large body of joint doctrine (and its supporting tactics, techniques, and procedures) has been and is being developed by the US Armed Forces through the combined efforts of the Joint Staff, Services, and combatant commands. The following chart displays an overview of the development process for these publications. MAKING A JOINT PUB ., PROJECT PROPOSAL All joint doctrine and tactics, techniques, and procedures are organized into a comprehensive hierarchy. Joint Pub 3–04 .1 is located in the operations series of joint publications . Joint Pub 1–01, "Joint Publication System, " provides a detailed list of all joint publications. Joint pubs are also available on CD–ROM through the Joint Electronic Library (JEL) . For information, contact : Joint Doctrine Division, J-7, 7000 Joint Staff Pentagon Washington, D. C. 20318–7000 . JOINT LASER DESIGNATION PROCEDURES JOINT PUB 3-09.1 PREFACE 1. Purpose. This publication provides joint procedures for employing laser designators with target acquisition systems and laser-guided weapons to enhance the combat effectiveness of joint US forces. 2. Application a. Procedures established in this publication apply to the commanders of combatant commands, joint task forces, and the subordinate components of these commands. These procedures may also apply when significant forces of one Service are attached to forces of another Service or when significant forces of one Service support forces of another Service, under criteria set forth in this publication. b. In applying the procedures set forth in this publication, care must be taken to distinguish between distinct but related responsibilities in the two channels of authority to forces assigned to combatant commands. -
Automatic Guided Vehicle Application: Precision Agriculture Major Professor: Lingxi Li
AUTOMATIC GUIDED VEHICLE APPLICATION: PRECISION AGRICULTURE A Thesis Submitted to the Faculty of Purdue University by Xiangnan Gong In Partial Fulfillment of the Requirements for the Degree of Master of Science in Electrical and Computer Engineering May 2017 Purdue University Indianapolis, Indiana ii THE PURDUE UNIVERSITY GRADUATE SCHOOL STATEMENT OF THESIS APPROVAL Dr. Lingxi Li, Chair Department of Electrical and Computer Engineering Dr. Brian King Department of Electrical and Computer Engineering Dr. Maher Rizkalla Department of Electrical and Computer Engineering Approved by: Dr. Brian King Head of the Departmental Graduate Program iii ACKNOWLEDGMENTS I would like to thank my advisor for his guidance and encouragement through the research and writing process. I am grateful to all of my committee members for the time and energy they have put into helping me complete my research. My family and friends kept me motivated and happy during this long process. Your support means so much to me. Thank you. iv TABLE OF CONTENTS Page LIST OF TABLES :::::::::::::::::::::::::::::::::: vii LIST OF FIGURES ::::::::::::::::::::::::::::::::: viii ABSTRACT ::::::::::::::::::::::::::::::::::::: ix 1 INTRODUCTION :::::::::::::::::::::::::::::::: 1 1.1 Introduction to Indoor AGVs and Their Guidance Systems ::::::: 1 1.2 Introduction to Outdoor Farm Machinery and Their Guidance Systems 3 1.3 Importance of Subject ::::::::::::::::::::::::::: 4 1.4 Knowledge Gap ::::::::::::::::::::::::::::::: 6 1.4.1 Situations Which Require Higher Accuracy :::::::::::: 7 -
Tango 22, Tango 22
1/2020 Tango 22, Tango 22 – this is TANGO 21, OVER Tactical training of Czech soldiers in Afghanistan continues even in time of their deployment in a foreign operation The military will receive eight UH-1Y Venom multipurpose helicopters and four AH-1Z Viper attack helicopters New helicopters in 2023 Both new helicopters are part of the H-1 series. Their advantage is in the mutual conformity of up to 85% of identical components, so from the service point of view it is an ideal solution. The UH-1Y Venom and the AH-1Z Viper form the backbone of the US Marine Corps helicopter fleet. These are modern, proven aircraft. The Czech Republic will acquire them for 14.6 billion crowns by 2023, on the basis of an intergovernmental agreement with the USA. The price for helicopters is in the amount of UH-1Y Venom guns, calibre 7.62 mm, and GAU16/A, calibre 14.6 billion CZK without VAT and agrees with The UH-1Y can operate in the most demanding 12.7 mm, or with 7.62 mm GAU17/A rotary how much the US Army would pay for them. climatic conditions, from arctic cold to desert machine guns. It can very effectively eliminate Not only the helicopters by themselves are heat. In the front of the cockpit sits two pilots, ground targets even with unguided air-to- included in the price, but also equipment and side by side. At the rear of the cab, there is surface missiles Hydra 70, or missiles with ammunition, spare parts, training simulator space for transporting passengers or materiel. -
Optical Guidance Method for Robots Capable of Vision and Communication
Robotics and Autonomous Systems 54 (2006) 461–471 www.elsevier.com/locate/robot Optical guidance method for robots capable of vision and communication Igor E. Paromtchik∗ RIKEN, 2-1 Hirosawa, Wako-shi, Saitama 351-0198, Japan Received 11 December 2004; received in revised form 27 July 2005; accepted 1 February 2006 Available online 3 April 2006 Abstract The optical guidance of robots spans the research topics of robotics, computer vision, communication and real-time control. The proposed method aims to improve the accuracy of guidance along a desired route in an environment that is unknown to the robot. The key idea is to indicate the numerical coordinates of target positions by means of projecting a laser light onto the ground. In contrast with other guidance methods, which communicate the target position numerically, using optical commands avoids the need to maintain the coordinate transformation between the robot’s system and that of the environmental model (“world” reference coordinates). The image processing and communication ensure that the robot accurately follows the route indicated by laser beacons, and self-localization becomes less relevant for guidance. The experimental results have proved the effectiveness of this method. c 2006 Published by Elsevier B.V. Keywords: Mobile robot; Optical guidance; Laser 1. Introduction over time makes teleoperation impossible from some instant, because of the danger of collision with the environment. Guidance means show the way while in motion, and The proposed method aims to eliminate this discrepancy localization is to confine within a particular area [1]. Guidance from the guidance. The novelty of this work is supported by is passive if no localization of the guided objects is performed, our patents [2,3]. -
A Concept of a Compact and Inexpensive Device for Controlling Weeds with Laser Beams
agronomy Article A Concept of a Compact and Inexpensive Device for Controlling Weeds with Laser Beams Ildar Rakhmatulin 1 and Christian Andreasen 2,* 1 Department of Power Plants Networks and Systems, South Ural State University, 454080 Chelyabinsk City, Russia; [email protected] 2 Department of Plant and Environmental Sciences, Faculty of Science, University of Copenhagen, Højbakkegaard Allé 13, DK 2630 Taastrup, Denmark * Correspondence: [email protected]; Tel.: +45-3534-3353 Received: 1 October 2020; Accepted: 19 October 2020; Published: 21 October 2020 Abstract: A prototype of a relatively cheap laser-based weeding device was developed and tested on couch grass (Elytrigia repens (L.) Desv. ex Nevski) mixed with tomatoes. Three types of laser were used (0.3 W, 1 W, and 5 W). A neural network was trained to identify the weed plants, and a laser guidance system estimated the coordinates of the weed. An algorithm was developed to estimate the energy necessary to harm the weed plants. We also developed a decision model for the weed control device. The energy required to damage a plant depended on the diameter of the plant which was related to plant length. The 1 W laser was not sufficient to eliminate all weed plants and required too long exposure time. The 5 W laser was more efficient but also harmed the crop if the laser beam became split into two during the weeding process. There were several challenges with the device, which needs to be improved upon. In particular, the time of exposure needs to be reduced significantly. Still, the research showed that it is possible to develop a concept for laser weeding using relatively cheap equipment, which can work in complicated situations where weeds and crop are mixed. -
UAV Flight and Landing Guidance System for Emergency Situations †
sensors Article UAV Flight and Landing Guidance System for Emergency Situations † Joon Yeop Lee ‡ , Albert Y. Chung ‡, Hooyeop Shim ‡ , Changhwan Joe ‡ , Seongjoon Park and Hwangnam Kim * School of Electrical Engineering, Korea University, Seoul 136-713, Korea; [email protected] (J.Y.L.); [email protected] (A.Y.C.); [email protected] (H.S.); [email protected] (C.J.); [email protected] (S.P.); * Correspondence: [email protected]; Tel.: +82-2-3290-4821 † This mansucript is extension version of the conference paper: Chung, A.Y.; Lee, J.Y.; Kim, H. Autonomous mission completion system for disconnected delivery drones in urban area. In Proceedings of the 2017 IEEE 7th Conference on Robotics and Biomimetics (ROBIO), Macau, China, 5–8 December 2017. ‡ These authors contributed equally to this work. Received: 30 August 2019; Accepted: 14 October 2019; Published: 15 October 2019 Abstract: Unmanned aerial vehicles (UAVs) with high mobility can perform various roles such as delivering goods, collecting information, recording videos and more. However, there are many elements in the city that disturb the flight of the UAVs, such as various obstacles and urban canyons which can cause a multi-path effect of GPS signals, which degrades the accuracy of GPS-based localization. In order to empower the safety of the UAVs flying in urban areas, UAVs should be guided to a safe area even in a GPS-denied or network-disconnected environment. Also, UAVs must be able to avoid obstacles while landing in an urban area. For this purpose, we present the UAV detour system for operating UAV in an urban area.